生产能力测定与管理0001.docx
《生产能力测定与管理0001.docx》由会员分享,可在线阅读,更多相关《生产能力测定与管理0001.docx(30页珍藏版)》请在冰豆网上搜索。
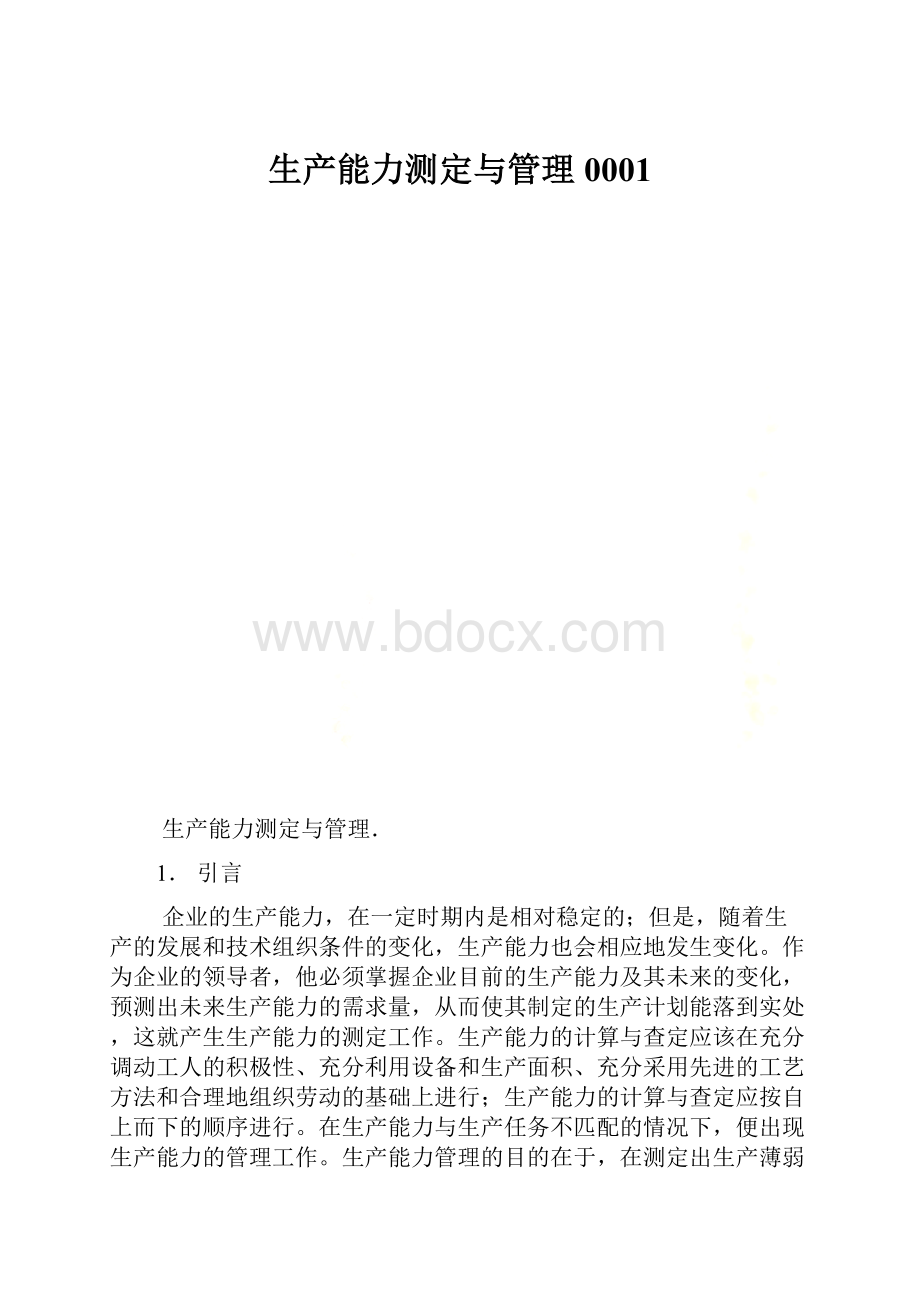
生产能力测定与管理0001
生产能力测定与管理.
1.引言
企业的生产能力,在一定时期内是相对稳定的;但是,随着生产的发展和技术组织条件的变化,生产能力也会相应地发生变化。
作为企业的领导者,他必须掌握企业目前的生产能力及其未来的变化,预测出未来生产能力的需求量,从而使其制定的生产计划能落到实处,这就产生生产能力的测定工作。
生产能力的计算与查定应该在充分调动工人的积极性、充分利用设备和生产面积、充分采用先进的工艺方法和合理地组织劳动的基础上进行;生产能力的计算与查定应按自上而下的顺序进行。
在生产能力与生产任务不匹配的情况下,便出现生产能力的管理工作。
生产能力管理的目的在于,在测定出生产薄弱环节的基础上,寻求平衡生产能力和生产任务的措施,制定出变更生产能力的策略以及提高生产能力的途径。
充分掌握企业的生产能力是一项十分重要的工作,它不但为企业制定计划提供了依据,而且还可以了解企业各个生产环节和各类生产设备之间的比例关系是否恰当,从而帮助人们找到其中的薄弱环节,这也正是进行技术革新和技术改造所要解决的关键问题。
众所周知,掌握和确定企业生产能力的意义不仅限于企业的计划要求,也是加速我国四化建设进程的客观要求。
2.生产能力的概念
所谓生产能力,是指企业的固定资产,在一定的时期(年、在先进合理的,季、月等).
组织条件下,经过综合平衡所能生产一定种类产品的最大数量。
企业的生产能力是一种客观的存在,在一定时期内是相对稳定的,但也会随着各方面的变化而变化。
根据核算生产能力时所依据的条件不同,企业的生产能力可以分为设计能力、查定能力和现实能力(计划能力)。
(1)设计能力企业基本建设设计任务书和技术文件中所规定的生产能力。
它是技术装备和各种设照工厂设计中所规定的企业产品方案、计数据计算出来的应该达到的最大产量。
工厂建成投产(即经过一个熟悉和掌握生产技术的后,要经过一段时间过程)方能达到。
指由于产品方案、协作2()查定能力
原有的设计能力不能反关系和技术组织条件发生了变化,查定生映实际情况时,由企业重新调查核实的生产能力。
并考虑到采取各种技术产能力是由现有设备条件为依据,组织措施或者进行技术改造后所能取得的效果。
考虑到年度内)现实能力(计划能力)3(
所计算出来的在计划所能实现的各种技组织措施的效果,年度内可能达到的生产能力。
计划能力又分为年初能力、11年末能力及年平均能力。
年初能力是指按计划年度月年末能力是指企业及各生产环节计划年度日计算的能力;它考虑了拟在计划年度内采取的并在计末时的生产能力,年平均能力是指划期末得以实现的扩大生产能力的措施;标计划年度平均拥有的生产能力。
.
上述三种企业生产能力,各有其不同的用途。
当确定企业的生产规模,编制企业的长期计划,安排企业的基本建设和技术改造时,应当以设计能力或查定能力为依据;当编制企业的年度、季度生产计划及确定生产指标时,应该以企业的计划能力为依据。
国外把企业的生产能力分为以下三种:
(1)潜在能力。
指最高管理部门预期在将来可能具有的生产能力。
(2)现实能力。
在本预算期内可能实现的生产能力。
(3)有效能力。
在本预算期内已经投入使用的生产能力。
一般而言,潜在能力大于现实能力,而现实能力大于或等于有效能力。
有效能近现实能
力,完成生产计划任务愈不容易,就越需要有严密的组织管理。
3.影响生产能力的因素
影响企业生产能力的因素很多,如产品品种;产品结构;产品工艺;质量要求;零部件的标准化和通用性水平;机床设备的数量和性能;工艺方法和通用性水平;机床设备的数量和性能;工艺方法和工艺装备系数;有效生产面积;组织管理的水平及工人的劳动积极性和技术水平等。
从查定生产能力的角度来考虑,可以将这些因素归结为三个基本因素,即生产设备数量(或生产面积数)、设备工作时间(生产面积利用时间)和设备(生产面积)生产率定额。
.
(1)生产设备数量(生产面积数量)是指企业在计划期内所拥有的全部能够用于生产的机器设备数,包括:
A:
正在运转的机器设备;B:
正在修理、安装或者准备修理、安装的机器设备;C:
因生产任务或其他不正常原因暂时停用的设备。
对已判定不能修复或已决定报废的设备、不配套的设备、企业留用作备用的设备和封存待调的设备,都不应列入企业生产能力的计算范围之列。
辅助车间(如机修车间、工具车间)所拥有的设备,不能参与与企业基本产品能力的计算,而只能用以计算辅助车间的生产能力;只有当辅助车间的设备数量超过规定并用于生产基本产品时,才可以把多余的设备用于计算基本产品的生产能力。
生产面积的数量对于铸造车间、铆焊车间、装配车间的生产能力有十分重要的意义。
在这类车间中,生产面积是指造型、装配等工作地、通道、工作地旁边的零部件存放地及运输设备所占的面积。
(2)设备工作时间(生产面积利用时间)
分为制度工作时间和有效工作时间。
制度工作时间是指在规定的工作制度下,设备可工作(或利用)的时间数;有效工作时间是指在制度工作时间中,扣除设备修理停歇时间后的时间总数。
制度工作时间用于计算生产面积的生产能力,有效工作时间用于计算设备的生产能力。
制度工作时间的计算公式为
FS=(Dr─Dh).f式年制度工作时间;------Fs中
Dr------全年日历日数;
Dh-------全年节假日数;
F每日制度工作小时数。
-------
有效工作时间的计算公式为?
)Fe=Fs.(1─Fe式中,-------设备年有效工作时间;
设备修理停工率。
-------?
就生产率定额(生产面积))(3设备是单台设备(单位生产面积)在单位时间内的产量定额,或者单台设备(单位生产面积)制造单位产品的时间消耗定额。
这两者成倒数关系,即=1/pt式中,t
------单位产品的时间定额
单位时间的产量定额p------
加生产率定额受产品的品种与结构、质量、要求、工工艺、工人技术水平等一系列因素的影响,它是决定生产能力三个基本因素中最易变化而且变化幅度较大的因素。
因此,在计算生产能力时,应当采用平均先进的生产率定额。
根据确定不同生产能力的要求,设备(生产面积)的生产率定额可以分为设计定额、查定定额和
计划定额。
设计定额和查定定额是企业在若干年内应该达到的先进水平定额,计划定额是企业在计划年度应该达到的平均先进定额。
一般而言,计划定额低于设计定额和查定定额。
其中计划定额可以根据现行定额乘计划超额系数(或计划压缩系数)加以确定。
其计算公式为
P1=
a)
(1+P0
)
T1=t0β─(1
P1---------------式中
计划产量定额;P0---------------
现行产量定额a
产量定额计划超额系数---------
t1
--------------计划时间定额t0
--------------现行时间定额β
--------时间定额计划压缩系数4生产能力测定.
41.现有生产能力的查定)生产能力查定的概念1(
所谓的生产能力查定,是指对企业、车间、工段或小组在一定时间内的生产能力进行计算和确定的过程。
其目的在于摸清企业现有生产能力的大小。
为改进技术、改善组织以及克服生产中的薄弱环节而提供依据,以便挖掘潜力和提高生产能力,完成或超额完成任务。
(2)查定生产能力的原始资料
A:
固定资产登记表和技术说明书,其中载有各车间设备的数量、性能、生产率及生产面积等方面的资料。
B:
工艺过程卡或工艺明细表。
C:
查定期内企业、车间、工段、小组的生产大纲,各种产品产量的比例构成资料。
D:
企业的技术改造计划和技术组织措施计划。
E:
机器设备和生产面积工作时间的规定,设备在很大程度上生产面积在时间利用方面的统计分析资料以及设备修理计划。
F:
企业职工认数、各工种人数及技术等级方面的资料。
G:
各项产量定额或时间定额及定额实际完成情况的统计分析资料。
(3)生产能力的计量单位
通常,生产能力是以实物指标作为计量单位的。
生产能力的实物计量单位有具体产品、代表产品和假定产品三种形式。
A:
具体产品。
在计算企业生产能力的生产定额时,是用该具体产品的时间定额或生产该产品的产量定
额。
该计量单位使用于大量生产的企业,如以某种机器产品的台数,某种毛坯、零部件的件数或套数等具体产品来计量单位。
B:
代表产品。
在多种产品生产的企业中,在结构、工艺和劳动量构成相似的产品中选出代表产品,以生产代表产品的时间定额或产量定额来计算生产能力,这种生产能力的计量单位即为代表产品。
该类计量单位使用于批量生产的企业。
代表产品和具体产品之间可以通过换算系数进行换算:
Ki=Ti/T0
式中,Ki----------产品i的换算系数;
Ti----------第
i种产品的时间定;
T0---------------
--代表产品的时间定额。
C:
假定产品。
以生产计划中各种产品的单位劳动量占全部产品劳动量的比重为基础计算出来的劳动量定额加权平均系数,作为单位产品劳动量定额用于计算生产生产能力的一种产品单位。
该计量单位使用于产品品种较多,各种产品的结构、工艺和劳动量构成差别较大的企业。
在单件小批量生产条件下,常常采用产品的某种重要技术参数为计量单位,如发电机的功率(KW))等。
T数,重型机器厂采用的质量单位(.
(4)查定生产能力的步骤
A:
确定企业的专业方向和生产大纲(产品的品种和各种产品的数量方案)。
它的依据有企业上级主管部门(工业部、局)的计划规定或决策,用户的需求调查和销售预测,技术预测等。
B:
做好查定准备工作。
首先,要向企业职工宣传查定生产能力的重要性,动员全体职工积极参加查定工作;再次,要组成全厂的和车间的生产能力查定小组,配备一定的技术人员、管理干部和技术工人来具体负责生产能力的查定工作,并制定生产能力查定的目标和计划,明确职责;其次,要收集整理查定生产能力所必须的各种数据资料。
C:
查定小组、工段、车间的生产能力。
首先;计算和确定各生产线、各生产小组的生产能力,然后计算和确定各工段的生产能力,再计算和确定各车间的生产能力。
这种自下而上的程序可以逐级地查找薄弱环节并采取措施,以便逐级提高其上层环节的生产能力。
D:
进行全厂生产能力的综合能力平衡。
即在查定的车间能力之后,在综合平衡的基础上来确定企业的生产能力。
(5)生产能力的计算和查定
生产能力的计算方法因各生产环节的生产类型不同而各异。
在大量生产条件下,流水线、自动线的生产能力往往是根据工厂生产大纲的需要预先规定的,它是根据
生产大纲计算流水线的节拍,然后根据节拍计算设备需要量和负荷,这就决定了按流水线组织大量生产的企业,其生产能力的核算要按每条流水线进行。
在成批生产和单件小批生产条件下,各个生产环节的生产能力通常是按设备组来计算的。
构成设备组的基本条件是,它们在生产上具有的互换性,也就是设备组中的任何设备在大体相同的时间内,可以完成分配给该设备组加工的工艺工序中的任何相同工序,并能够达到规定的质量标准。
不同机床设备有着不同的分组标志,金属切削机床的分组标志有:
机床的用途(工艺工序种类)、机床的规格尺寸(如中心高、工作台尺寸、钻孔直径和深度等)、机床的生产率、机床的精度、机床的运转特点、机床的动力特征和功率等;锻压设备和锻造设备可以按照设备的用途、种类、加工吨位、生产率等标志来分组。
如前所述,生产能力的计算与查定,应从基层开始自下而上来进行,同时还应根据生产能力取决于设备还是生产面积而分别计算。
A:
单台设备生产能力的计算。
计算公式为
P0=Fe/t
式中,P0-------单台设备生产能力,台或件;
Fe-------单台设备;h计划期(年)有效工作时间,
t-------单位产品台时定额。
工序由一台设备承担时,单台设备的生产能力即为工序生产能力;工序由S台设备承担时,工序生产能力为P0?
S;加工流水线(装配流水线亦同)的生产能力,在各道工序的生产能力综合平衡的基础上加以确定。
B:
设备组生产能力的计算。
计算公式为本P
=Fe×S/t
式中,P---------设备组的生产能力,台或件;
Fe---------
单台设备计划期(年)有效工作时间,h;
S-------
设备组的设备数,台;
t----------制造单位产品(具体产品、代表产品或假定产品)所需该种设备的台时数,该台时定额是压缩之后的即计划期内将采用的新定额。
C:
车间(工段)生产能力的计算。
加工车间的生产能力可以在计算设备组生产能力的基础上加以确定。
由于各设备组的生产能力一般是不相等的,因此在确定车间(工段)的生产能力时,要进行综合平衡工作。
综合平衡的依据是主要设备组(即完成劳动量比重最大或贵重而无代用设备的设备组)的生产能力。
生产能力不足的设备组为薄弱环节,要制定消除薄弱环节的措施,
应尽可能利用富裕环节的能力来补偿;薄弱环节。
车间(工
段)生产能力综合平衡的示例如图7.8.1:
在该图所示的机械加工工段中,六个设备组的生产能力是不相等的。
如果将该工段的生产能力定到100台水平,那末钻床组、镗床组和刨床组的生产能力过低而成为薄弱环节,车床组和铣床组的生产能力过剩而成为富裕环节。
若能以铣代刨、以车代镗,便可以使刨床组和镗床组两个薄弱环节得以消除;若对钻床组可以采取技术革新或增加工作班次的措施,则该薄弱环节亦可得以消除。
这样,经过综合平衡和采取措施之后,该机械加工工段的生产能力便可以达到100台的水平。
铸造、锻造、装配车间(工段)生产能力的计算方法与机械加工车间生产能力的计算方法有所不同。
(a)铸造车间生产能力的计算。
对于铸造车间,主要是计算熔炼设备、造型设备和造型面积的生产能力。
熔炼设备生产能力的计算公式为:
M?
=S×
q×Fe×?
1─(а+β+γ)?
式中,M?
----------化铁炉的生产能力,t/а;
S----------化铁炉数量,座;
q----------化铁炉小时产量(它等于熔炼周期除化铁炉容量),t/h
Fe----------化铁炉全年有效工作时间,h;
自然损耗率;-----------а
β-----------浇冒口残头损失率;
γ-----------铸件废品率。
造型设备生产能力的计算方法与金属切削机床设备的生产能力计算方法相同。
造型面积生产能力的计算公式为:
Mα=A×qа
式中,Mα---------造型面积生产能力
A--------造型面2;积,mq---------单位造型面a2.t/m积平均铸件年产量,在计算铸造车间生产能力时,除了以上三者的能力依据之外,还须考虑配砂、型心、烘干、清沙、退火、吊车等各个环节的能力配合情况。
(b)锻造车间生产能力的计算。
锻造车间的生产能力主要按锻锤和水压机的能力配合情况。
锻造设备生产能力的计算公式为:
M=S×Q×Fe
pp式中,M----------锻造设备组生产能力,p
件;
S
----------锻造
设备台数,台;
Q----------单台p锻造设备每小时锻件产量,件/(台·H)
F----------每台锻造设备全年e
。
H有效工作时间,
(c)装配车间生产能力的计算。
装配车间的生产能力一般按生产面积计算,其方法与
面积生产能力的计算方法类似。
在流水生产条件下,装配流水线生产能力的计算公式为:
M=1/rasF=S/tFeiei
式中,M-------装as配流水线生产能力,台;
r----------装配流水线节拍;
S----------装配流水线第I道i
工序的工作地数;
t----------第I道工序的单i
件时间定额;
F----------
装配流水线计划期e
有效工作时间。
(D)企业生产能力的确定。
企业生产能力是在各车间能力综合平衡的基础上加以确定的。
车间生产能力综合平衡的内容主要有两个方面,其一是基本生产车间能力的平衡,其二是基本生产车间与辅助生产车间以及生产服务部门之间能力的平衡。
在平衡各个基本车间的能力时,一般以基本车间生产能力为准,核对辅助车间生产能力的协调配合情况,若两者能力不平衡,就采取措施使之达到平衡。
4.2未来生产能力的预测
生产能力供给预测)1(.
今后某段时期内的生产能力可以用工时递减曲线加以预测。
工时递减曲线又称熟练曲线,是指某一产品随着生产时间或累积平均生产时间将按某一规律逐渐减少,当生产数量超过一定界限时,这种减少的趋势就几乎消失了,这种现象称为工时递减现象。
工时递减除了取决于工人操作水平的提高之外,还有设备性能的改善、产品设计和原材料的改进等多种因素,它常被用来预测在生产设备的性能和产量不变的情况下,未来工时消耗量或新产品的工时定额,从而达到预测生产能力供给的目标。
15100组系列2备设系列150065341202015251010系列2100100857590100系列1生产能力工段生产能力平衡图解
图7.8.1工段生产能力平衡图解
A.工时递减曲线数学模型一般工时简化bx═a×对数线性工时曲线表达式。
即у
其变化规律如图7.8.2所示:
TC
Lg工时
ATC1
Tx
LG台数
对数线性工时递减曲线图AT═在图中,1C
n
X÷
Tx
-xn)÷(1t═n1Tc
(1-n)t.x═1A式中,C
-------------累计平均公工时;t1
生产第一台(件)产品的工时消耗;-------------
x-------------
生产量;n
递减系数;-------------
Tx
个别产品工时;-------------
Tc
-------------累计工时。
递减系数n和递减率ρ之间存在下列关系
n═
lgρ÷lg(1/2)
B.工时递减曲线应用举例设备能力预测。
已知生产某产品的工时递减系数n═0.0665,生产第一件产品的工时消耗t═2.05H,其它数据见1下表7.8.1。
在今后12个月生产计划的基础上,预测12个月后设备的生产能力。
生产产品设备需求量
12个月后,单件工时T为x
Tx
nω)-t(1n)÷(x+═1═
0.0665
)120000)÷(30000+2.05×(1-0.0665═
0.86(H/件)
将12个月后的计算结果与现状比较于下表7.8.2:
12个月以后,设备的生产能力将提高(18=16)/18=11%。
表7.8.1生产产品设备需求量
/件生产量每月每截止台设备个月12每月计目前的台时累积计划产量累积定额划产量(产量3))
(1)(4)(120000
30000
1000040
需用设备台数月需用工单件工/)(4(比较对象时(6)=7)=)时(5))(3*(51)(95H/.0现状18台≈179500H.1件86H/.12个月以09158600H
.≈台16后件
比较表7.8.2表)生产能力需求预测(2
短期生产能力的A.短期需求量预测个月的办法来进行预测。
首先,12需求,可以用展望后预计出对本厂不同产品或多或少服务的需求量;然后,再把这些需求量与现有的生产能力进行比较,从而边可预测出短期生产能力的需求。
例如,一个生产两种产品所示的办法预测需求量。
的企业,可以用图7.8.3生产能力的长期B.长期需求量预测
需求量会因市场需求和工艺技术的不定而难以确定,同时,企业在将来会增加一些新的产品而后淘汰一些过时产品,因而,预测为
需求量产品B的月需求量预测
产品A的月需求量预测
月份
短期生产能力预测7.8.3图
年的生产能力需求量是一项冒险而困难的工105年或期作。
预测企业长期生产能力需量的有效方法是应用产品的生命周期原理,即首先按产品类别确定其生命周期曲并合理确定目前的各种产品在计划期内将处于7.8.4,线生命周期的哪个阶段,由此可确定各种产品的生产能力的长期需求量,进而便可以预测出企业生产能力的长期需求量。
酝酿阶段
增长阶段
成熟阶段
饱和阶
需
衰退阶销售量
时间图7.8.4产品生命周期的各个阶段.生产能力的分析5.
生产能力可以按五个步骤进行,即确定瓶颈操作、收集数据、进行性能分析、确定能力指标、撰写能力利用和损失分析报告。
(1)确定瓶颈操作
瓶颈操作的确定依据是每小时的生产率和该项工作每天实际能操作的时间之间的关系。
确定生产总体中的瓶颈部位之后,要将生产总体中每个组成部分按照它们对整体生产能力的限制程度按顺序排列。
(2)收集数据
一旦确定了真正的瓶颈部位并将它们进行排队以后,就能确定潜在的总生产能力(无损失、无干扰),它们通常是以各种单位(件数或组件数)/H、体积(以立方计)/H、质量(KG)/H来表示的。
例如,用手动操作的机器生产,总是将零件的装卸时间算在机器循环中,只将部件的传送时间计入机器循环中;在人工装配中,只将直接装配的工件考虑进去,其他诸如检测、操作工休息或个人需用时间等因素就不考虑了。
第二个要确定的是对总产量的干扰因素,这种干扰分为两种基本类型:
安排好的(计划的和有规律的)和未安排好的(未计划的和无规律的)。
某些干扰因素是不能计算在操作循环中的,如更换工具、搬运原材料和操作工人需要用时间等,把这些因素加上有规律的重复人工劳动因素就形成了工作标准。
有规律的重复人工劳动因素中干扰设备产量的因素,诸如造成机器停机等待的,不在机器操作循环之内的检验和对机器与人之间.
复杂工作的(安排)分派,就餐时间,废料处理,计划内或计划外的设备修理等,这些损失可以分为已安排的和未安排的两种,企业可以任意选选择一种分类方法。
然而,有人建议要确定所谓的可以达到的标准产量,即劳动者工作标准所规定的产量加以对照,来确定通过计划所允许的损失程度。
(3)进行性能分析
“性能分析”这个术语是指有关数据的确定过程,并将它们在某一段时间内对实际产量和潜在产量的重要性予以说明。
(表7.8.3)列出了部门ABC这一个复合产品(E和E')的生产部门,在6个月时间范围内的各种数据。
下表是一张复合产品生产企业某一部门的典型数据表。
它列出了与产品生产中瓶颈因素有关的数据。
用6个月时间收集到的这一系列数据可能代表了真正的工作状态