无损检测监理细则.docx
《无损检测监理细则.docx》由会员分享,可在线阅读,更多相关《无损检测监理细则.docx(14页珍藏版)》请在冰豆网上搜索。
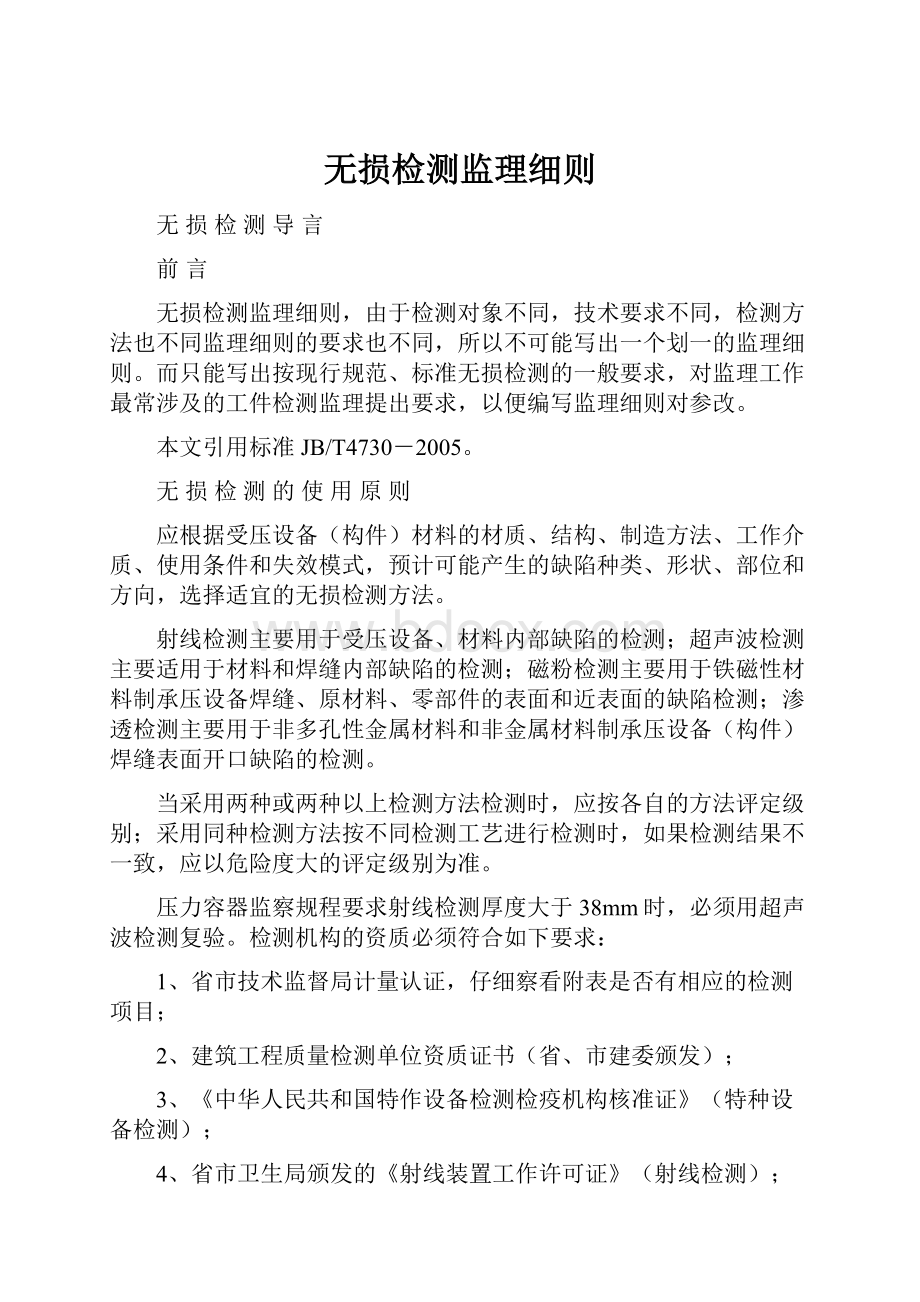
无损检测监理细则
无损检测导言
前言
无损检测监理细则,由于检测对象不同,技术要求不同,检测方法也不同监理细则的要求也不同,所以不可能写出一个划一的监理细则。
而只能写出按现行规范、标准无损检测的一般要求,对监理工作最常涉及的工件检测监理提出要求,以便编写监理细则对参改。
本文引用标准JB/T4730-2005。
无损检测的使用原则
应根据受压设备(构件)材料的材质、结构、制造方法、工作介质、使用条件和失效模式,预计可能产生的缺陷种类、形状、部位和方向,选择适宜的无损检测方法。
射线检测主要用于受压设备、材料内部缺陷的检测;超声波检测主要适用于材料和焊缝内部缺陷的检测;磁粉检测主要用于铁磁性材料制承压设备焊缝、原材料、零部件的表面和近表面的缺陷检测;渗透检测主要用于非多孔性金属材料和非金属材料制承压设备(构件)焊缝表面开口缺陷的检测。
当采用两种或两种以上检测方法检测时,应按各自的方法评定级别;采用同种检测方法按不同检测工艺进行检测时,如果检测结果不一致,应以危险度大的评定级别为准。
压力容器监察规程要求射线检测厚度大于38mm时,必须用超声波检测复验。
检测机构的资质必须符合如下要求:
1、省市技术监督局计量认证,仔细察看附表是否有相应的检测项目;
2、建筑工程质量检测单位资质证书(省、市建委颁发);
3、《中华人民共和国特作设备检测检疫机构核准证》(特种设备检测);
4、省市卫生局颁发的《射线装置工作许可证》(射线检测);
5、省市技术监督局检定的探伤仪必须在检定有效期内。
从事特种设备检测的探伤人员必须获得国家质量监督检验检疫总局颁发的资格证书,且只能从事相应检测技术等级的检测工作。
实施无损检测的人员按无损检测工艺卡进行操作。
无损检测工艺卡应根据产品标准,有关技术文件和设计图的要求编制,一般应包括以下内容:
1、工艺卡编号;
2、产品名称,产品编号,制造、安装或检验编号,承压设备的类别、规格、尺寸、材料牌号、材质、热处理类状态及表面状态;
3、检测设备与器材:
设备种类、型号、规格尺寸、检测附件和检测材料;
4、检测工艺参数:
检测方法、检测比例、检测部位、标准试块或标准试拌(片);
5、检测技术要求:
执行标准和验收级别;
6、检测程序;
7、检测部位示意图;
8、编制和审核人(均需具备相应级别);
9、制定日期。
射线检测
射线检测能确定缺陷平面投影的位置、大小,可获得缺陷平面图象并据此判定缺陷的性质。
射线检测适用于金属材料制承压设备、构件熔化焊接接头的检测。
适用材质有碳素钢、低合金钢、不锈钢、铜
及铜合金、铝及铝合金、钛及钛合金、镍及镍合金。
射线检测不适合于锻件、管材、棒材的检测。
T型焊接接头、角焊缝以及堆焊层的检
测一般也不采用射线检测。
射线的穿透厚度,由射线能量确定。
见下表:
射线源
透照厚度W(AB级)mm
射线源
透照厚度W(AB级)mm
X射线(300kv)
≤40
Co-60(钴-60)
40~200
X射线(420kv)
≤80
X射线(1Mev~4Mev)
30~200
Se-75(硒-75)
10~40
X射线(4Mev~12Mev)
50~400
Ir-192(铱-192)
20~100
X射线(>12Mev)
≥80
射线检测技术等级分为三级:
A级-低灵敏度技术;AB级-中级灵敏度技术;B级-高灵敏度技术。
如果设计未规定,一律采用AB级检测技术。
射线检测技术等级选择应符合制造、安装、在用等有关标准及设计图样规定。
承压设备、构件对接接头的制造、安装、在用时的射线检测,一般应采用AB级检测技术进行检测。
对重要设备、结构、特殊材料焊接工艺制作的对接焊缝,可采用B级技术进行检测,由于结构、环境条件、射线设备等方面的限制,检测的某些条件不能满足AB级(或B级)射线检测时,经检测方技术负责人批准,在采取有效措施补偿(如造用更高级别的胶片)后,底片的象质灵敏度达到了AB级(或B级)射线检测技术的规定,则可认为按AB级(或B级)射线检测技术进行了检测。
胶片按照GB/T19384.1-2003分为四类,即T1、T2、T3和T4类。
T1为最高级别,T4为最低级别。
A级和AB级射线检测技术应采用T3类或更高类别的胶片,B级射线检测技术应采用T2类或更高类别胶片,采用r射线对裂纹灵敏度性大的材料进行检测时,应采用T2类或更高类别胶片。
对底片质量有如下要求:
1、定位和识别标记影像应显示完整,细丝朝外。
当条件不允许放置在射线源侧时,通过对比试验符合要求时,也可以放在胶片一侧。
其清晰度以该透照厚度应看到的金属丝长度不小于10mm的连续长度为合格。
2、底片评定范围的黑度D符合
A级:
1.5≤D≤4.0;
AB级:
2.0≤D≤4.0;
B级:
2.3≤D≤4.0
3、底片评定范围内不应存在干扰缺陷影像识别的水迹、划痕、斑纹等伪缺陷。
射线检测对焊缝表面、检测时机的要求。
射线检测前,必须对焊缝外观检查合格。
表面的不规则程度以不得掩盖和干扰缺陷影像的辨认,否则应作适当的修整。
对有延迟裂纹倾向的材料,至少应在焊接完成24小时后进行检测。
射线检测报告至少应包括下述内容:
1、委托单位;
2、被检工件:
名称、编号、规格、材质、焊接方法和热处理状况;
3、检测设备:
名称、型号和焦点尺寸;
4、检测标准和验收等级;
5、检测规范:
技术等级、透照布置、胶片、增感屏、射线能量、曝光量、焦距、暗室处理方式和条件等;
6、工件检测部位及布片图;
7、检测结果及质量分级;
8、检测人员和责任人员签字(其技术资格符合相应规定);
9、检测日期。
射线检测的卫生防护应符合GB18871、GB16357和GB18465的有关规定。
X射线检测时,应按GB16375的规定控制区和管理区、设置警告标志。
检测人员应佩个人剂量计,剂量报警仪。
r射线检测时,应按GB18465的规定划定控制区和监督区,设置警告标志,检测作业人员应佩带个人剂量计,携带剂量报警仪。
警告区须有专人看管。
此外,在透照场不得吸烟、进食,工作完成后须洗手。
室内透照必须设通风设备,保持空气清新。
超声波检测
超声检测能确定缺陷的位置、尺寸。
超声检测适用于板材、复合板材、碳钢和低合金钢锻件、管材、棒材、奥氏体不锈钢锻件等承压设备原材料和零部件的检测;也适用于承压设备对接焊接接头,T型焊接接头、角焊缝以及堆焊层等的检测。
不同检测对象相应的超声检测厚度范围如下表
超声检测对象
适用的厚度范围mm
碳素钢、低合金钢、镍及镍合金
母材为6~250
铝及铝合金、钛合金板材
厚度≥6
碳钢、低合金钢锻
厚度≤1000
不锈钢、钛及钛合金、铝及铝合金、镍及镍合金
基板厚度≥6
碳钢、低合金无缝钢管
外径12~660、壁厚≥2
奥氏体不锈钢无缝钢管
外径12~400、壁厚2~35
碳钢、低合金钢螺栓件
直径>M36
全熔化焊钢对接焊接头
母材厚度为6~400
铝及铝合金制压力容器对接焊接头
母材厚度≥8
碳钢、低合金钢压力管道环焊缝
壁厚≥4.0,外径为32~159或壁厚为4.0~6,外径≥159
钛及钛合金制压力容器对接焊接头
母材厚度≥8
铝及铝合金接管环焊缝
壁厚≥5.0,外径为80~159或壁厚为5.0~8,外径≥159
奥氏体不锈钢对接焊接接头
母材厚度为10~50
耦合剂按如下要求选用:
1、具有良好的透声性能;
2、具有一定的流动性和侵润性;
3、易于清洗,不污染,利于下道工序施工;
4、对人体无害,对工件无腐蚀。
承压设备用板材超声检测按下表选用探头
板厚mm
采用探头
公称频率MHZ
探头晶片直径尺寸
6~20
双晶直探头
5
晶片面积≥150mm2
>20~40
单晶直探头
5
Ф14mm~Ф20mm
>40~250
单晶直探头
2.5
Ф20mm~Ф25mm
标准试块选用遵从:
1、用双晶直探头检测厚度不大于20mm的钢板时,采用CBⅠ标准试块。
如图。
2、用单晶直探头检测厚度大于20mm的钢板时,采用CBⅡ标准试块。
如下图及表。
试块编号
被检钢板厚度mm
检测面到平底的距离Smm
试块厚度Tmm
CBⅡ-1
>20~40
15
≥20
CBⅡ-2
>40~60
30
≥40
CBⅡ-3
>60~100
50
≥65
CBⅡ-4
>100~160
90
≥110
CBⅡ-5
>160~200
140
≥170
CBⅡ-6
>200~250
190
≥220
检测面可选钢板的任一轧制面。
若检测人员认为需要或设计上有要求,也可以选钢板的上、下两轧制面分别进行检测。
扫查方式的要求如下图。
如合同、技术协议书或图择要求,也可以采用其它的扫查形式。
当板厚超过100mm时,剖口扫查以剖口预定线两侧各一半为准;板厚<100mm时,以各50mm。
钢制承压设备对接焊缝超声检测
JB/T4730-2005规定,适用于母材厚度为8~400mm。
不适用于铸钢对接焊缝、外径小于159mm的钢管环向对接焊缝、内径小于或等于200mm的管座角焊缝的超声检测,也不适用于外径小于250mm或内外径之比小于80%的纵向对接焊缝的检测。
检测技术等级分为A、B、C三个检测级别。
检测技术等级的选择应符合制造、安装、在用等有关规范、标准及设计图纸的规定。
A级仅适用于母材厚度为8~46mm的对接焊缝。
可用一种K值探头采用直射法和一次反射法进行单面单侧检测。
B级检测适用厚度为8~46mm时,用一种K值探头采用直射法和一次反射法进行单面单侧检测。
母材厚度为46~120mm时,用一种K值探头采用直射法进行双面双侧检测。
如受几何条件限制,也可以进行双面单侧或单面双侧采用两种K值探头检测。
母材厚度为120~400mm时,一般用两种K值探头采用直射法双面双侧检测。
两种K值探头的折射角≮10°。
应进行横向缺陷的检测。
检测时,在焊缝两侧边缘使探头与焊缝中心线成10°~20°作两个方向的斜平行线扫查。
C级检测要求将焊缝加强高磨平。
对焊缝两侧斜探头扫查经过的母材区域要用直探头进行检测。
母材厚度为8~46mm时,用两种K值探头采用直射法和一次反射法在焊缝的单面双进行侧检测。
两种探头的折射角相差应不小于10°,其中一个折射角应为45°。
母材为46~400mm时,用两种K值探头采用直射法在焊缝的双面双侧进行检测。
两种探头的K值相差不应小于10°。
进行横向缺陷的检测时,将探头放在焊缝及热影响区上作两个方向的平行扫查。
探伤时机的要求,对于碳素钢,焊接完成冷却到环境温度,而具有延迟裂纹倾向的钢材至少要在焊接完成24小时后才可检测。
探头的移动区域内不得有焊接飞溅、铁屑、油垢及其它杂物,表面粗糙度Ra≤6.3um。
探头移动区(焊缝单侧)不小于1.25P(P等于二倍板厚与K值的积)。
板厚Tmm
K值
6~25
3.0~2.0(72°~60°)
>25~46
2.5~1.5(68°~56°)
>46~120
2.0~1.0(60°~45°)
>120~400
2.0~1.0(60°~45°)
探头K值的选择对焊缝检测结果有决定性的影响。
JB/T4730-2005推荐采用的斜探头K值如下表:
平板对接焊缝扫查方式如下图。
锯齿型扫查是最基本的扫查。
平行扫查是进行C级检测对检测焊缝中的横向缺陷,如裂纹。
前后、转角、环绕扫查是为了扫查到缺陷的最大反射波高。
左右扫查是对缺陷测长的扫查。
斜平行扫查为了检测焊缝中某些具有方向性的缺陷。
扫查方式的选择原则,是根据焊接方法、工艺、材质,预见不能产生的缺陷种类方向,以及检测技术等级进行的。
目的是尽可能保证缺陷能有效检出,使产品达到设计要求。
管座角焊缝的超声波检测
检测面和探头的选择,应根据各种缺陷产生的可能性,使声束尽可能垂直于该焊缝的主要缺陷。
管座焊一般有如下几种形式,可选择其中一种或几种方式组合实施检测。
检测方式的选择还应依据合同双方的商定,并考虑主要检测对象和几何条件的限制。
直探头可采用频率为2.5MHZ的软保护膜直探头或双晶直探头。
斜探头可采用频率为2.5MHZ,探头于工件接触面尺寸符合下式规定。
a(或b)≤D/2(mm)
式中a——斜探头接触面的长度;
b——斜探头接触面的宽度;
D——探伤面的曲面半径。
即尽可能选择小直径、小体积的探头,以保证有良好的声传播。
超声检测报告至少应包括以下内容:
1、委托单位;
2、被检工件:
名称、编号、规格、材质、坡口形式、焊接方法、表面光洁度和热处理状况;
3、检测设备:
探伤仪、试块;
4、检测规范:
技术等级、探头K值、探头频率、检测面和灵敏度;
5、工件检测部位及缺陷种类、尺寸、位置和分布应在草图上标明及必要的说明;
6、检测标准名称、验收等级和检测结果;
7、检测人员和责任人员签字及其技术资格;
8、检测日期。
磁粉检测
a、预处理。
去除材料或工件表面的油污、铁锈、氧化铍及其它粘附磁粉的物质、划痕、凹陷等防碍磁痕辨别的不规则物;如被检工件表面有残留涂层,应不影响检测结果,且其厚度不均匀不超过0.05mm,经合同各方同意,可以带涂层进行检测。
b、按预先制定的磁化规范对检测物进行磁化;
c、施加磁粉式磁悬液;
d、磁痕观察与记录;
e、缺陷评级;
f、退磁;
g、后处理。
磁粉检测的监理重点要考虑两个问题:
工件的磁化。
磁化规范正确与否,直接对缺陷的检出与否有直接的影响,,所以,必须要求施工单位在工艺卡中提供磁化规范,并实施监督按该规范进行磁化。
检测时机的要求,如是焊缝,应在焊接完成,质检员外观检查合格后进行。
对于有延迟裂纹倾向的材料,磁粉检测应在焊接完成后至少24小时后进行。
对于紧固件和锻件的磁粉检测应安排在最终热处理后进行。
安全防护的要求如下:
1、轴向通电法和触头法检验不得在易燃易爆的场合进行,其它地方也应预防起火燃烧。
2、使用水磁悬液检测时,应防止绝缘不良或短路。
3、使用荧光磁粉检测时,应避免荧光灯直射眼睛。
4、使用干法检测时,注意通风良好、防火。
磁粉检测报告至少应包括以下内容:
1、委托单位;
2、被检工件:
名称、编号、规格、材质、坡口形式、焊接方法、和热处理状况;
3、检测设备:
名称、型号;
4、磁化方法和规范,磁粉种类及磁悬液浓度和施加方法,检测灵敏度试验标准试块、标准试块;
5、磁痕记录及工件草图(示意图);
6、检测标准名称、验收等级和检测结果;
7、检测人员和责任人员签字及其技术资格;
8、检测日期。
渗透检测
渗透检测的基本程序:
1、表面准备工件被检表面不得有影响渗透检测的铁锈、氧化皮、焊接飞溅、铁屑、毛刺以及防护层;工件机加工表面粗糙度Ra≤12.5um,非机加工表面可适当放宽,但不得影响检测结果。
2、预清洗可采用溶剂、洗涤剂等进行。
铝、镁、钛合金和奥氏体钢制零件经机加工的表面,如确有需要,可先进行酸洗或碱洗。
清洗后,检测面上遗留的溶剂和水分等必须干燥,且保证在施加渗透剂前不得污染。
3、施加渗透剂。
4、去除多余的渗透剂。
5、干燥。
6、施加显影剂。
7、观察及评定。
检测时机:
焊接完成,并经外观检查合格后进行。
对有延迟裂纹倾向的材料,至少应在焊接完成24小时后进行。
检测方法的选用:
1、首先满足检测缺陷的类型和灵敏度的要求。
并根据工件表面粗糙度、检测批量大小和现场水源、电源等条件决定。
2、对于表面光洁度且检测灵敏度高的工件,宜采用后乳化型着色型着色法或后乳化型荧光法,也可采用溶剂去除型荧光法。
3、对于现场无水源、电源的检测宜采用溶剂去除型着色法。
4、对于批量大的工件检测,宜采用水洗型着色法或水洗型荧光法。
5、对于大工件的局部检测,宜采用溶剂去除型着色法或溶剂去除型荧光法。
渗透检测剂的质量控制:
1、渗透剂的密度、颜色必须符合制造厂说明书的要求。
2、对在用的渗透剂进行外观检验,如发现明显的混浊或沉淀物、颜色或难以清洗,则应予报废。
3、被检渗透剂与基准渗透剂进行比较试验,当被检渗透剂显示渗透剂显示缺陷的能力低于基准渗透剂时,应予报废。
4、对于干式显影剂如发现粉末凝聚、显著的荧光残留或性能低下时要废弃。
5、湿式显影剂浓度应保持在制造厂规定的范围内。
6、湿式显影剂出现混浊、变色或难以形成薄而均匀的显影层时应予报废。
7、对喷罐式渗透剂,喷罐表面不得有锈蚀、泄漏。
8、对同一被检工件,不能混用不同类型的渗透剂。
9、渗透检测剂必须标明生产厂家、生产日期、有效期、产品合格证和使用说明书。
10、渗透检测剂应对工件无腐蚀和对人体无害。
渗透检测报告至少应包括以下内容:
1、委托单位;
2、被检工件:
名称、编号、规格、材质、坡口形式、焊接方法、和热处理;
3、检测设备:
渗透检测剂名称和牌号;
4、检测规范:
检测比例、检测灵敏度校验及试块名称、预清洗方法、乳化剂施加方法、去除方法、干燥方法、显像剂施加方法、观察方法和后清洗方法、渗透温度、渗透时间、乳化时间、水压及水温、干燥温度和时间、显像时间;
5、渗透显示记录及工件草图;
6、检测标准名称、验收等级和检测结果;
7、检测人员和责任人员签字及其技术资格;
8、检测日期。