丰田生产系统14原则.docx
《丰田生产系统14原则.docx》由会员分享,可在线阅读,更多相关《丰田生产系统14原则.docx(18页珍藏版)》请在冰豆网上搜索。
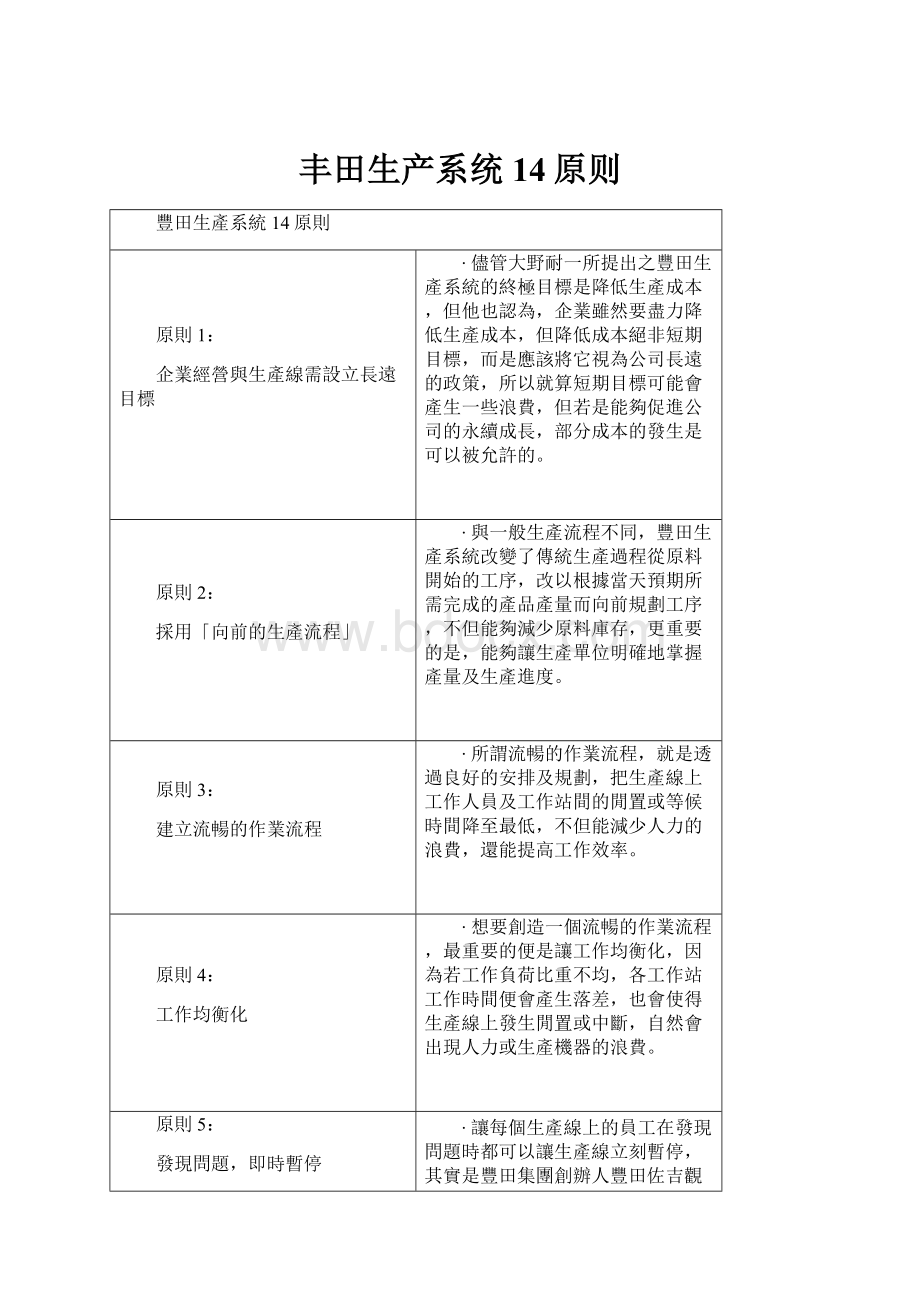
丰田生产系统14原则
豐田生產系統14原則
原則1:
企業經營與生產線需設立長遠目標
∙儘管大野耐一所提出之豐田生產系統的終極目標是降低生產成本,但他也認為,企業雖然要盡力降低生產成本,但降低成本絕非短期目標,而是應該將它視為公司長遠的政策,所以就算短期目標可能會產生一些浪費,但若是能夠促進公司的永續成長,部分成本的發生是可以被允許的。
原則2:
採用「向前的生產流程」
∙與一般生產流程不同,豐田生產系統改變了傳統生產過程從原料開始的工序,改以根據當天預期所需完成的產品產量而向前規劃工序,不但能夠減少原料庫存,更重要的是,能夠讓生產單位明確地掌握產量及生產進度。
原則3:
建立流暢的作業流程
∙所謂流暢的作業流程,就是透過良好的安排及規劃,把生產線上工作人員及工作站間的閒置或等候時間降至最低,不但能減少人力的浪費,還能提高工作效率。
原則4:
工作均衡化
∙想要創造一個流暢的作業流程,最重要的便是讓工作均衡化,因為若工作負荷比重不均,各工作站工作時間便會產生落差,也會使得生產線上發生閒置或中斷,自然會出現人力或生產機器的浪費。
原則5:
發現問題,即時暫停
∙讓每個生產線上的員工在發現問題時都可以讓生產線立刻暫停,其實是豐田集團創辦人豐田佐吉觀察紡織機運作後所留下來的觀念,因為若有一根線斷掉而沒有員工發現的話,紡出來的布匹其實都是瑕疵品,形同浪費。
所以豐田佐吉才發明了「安燈」(andon)制度,當有員工發現生產線異常時,立刻發出訊號、停機,才能減低不良品出現的機會。
∙這項發明後來也被導入Toyota汽車,成為豐田生產系統的主要一環,所以生產線上發生問題時,所有員工都有權立即停止生產線,解決問題,以有效減少因瑕疵品所產生的浪費。
原則6:
工作標準化
∙工作標準化雖然會讓工作內容有點單調,但相反的,工作內容標準化,卻能夠讓員工持續改善工作的方法,並有效減少錯誤產生的機會。
原則7:
借重「看板」
∙儘管電腦普及後,「無紙化」作業已成為許多企業內部的目標,但在豐田集團內,他們卻堅信員工需以看板上所記載的生產內容為依歸,所以在豐田集團的生產線上,到處都有以紙或木板做成的看板在流通,所以一但工作站內的員工發現半完成品與看板上所記載的有所差異,便能夠很快地發現其中的錯誤,並加以除錯,降低瑕疵品產生的機會。
原則8:
採用最適當的生產技術
∙與機器相比,人是較容易發生錯誤的,所以企業應該提供員工經過反覆測試、較不容易出錯,最適當的生產方式,而不是讓員工自己在錯誤中找出適當的生產方式。
。
原則9:
培養真正了解企業文化的員工
∙豐田生產系統還有一個成功的關鍵,那就是他們不喜歡從外部挖角,「空降」高階主管,而是喜歡從企業體內尋找了解公司內部文化的員工,並栽培他們,如此不但能夠讓員工更有向心力,也能讓企業體內的所有員工都能徹底了解豐田生產系統的文化與精隨,且在做決策時,能夠深刻體會決策是否與公司最高指導原則衝突。
原則10:
強調團隊合作
∙由於豐田集團內部的員工都很了解豐田生產系統,且充分相信這套生產模式,所以員工們都相當團結,且願意執行豐田生產系統。
所以在豐田集團工作的員工,總是都會以身為豐田集團一員為榮,願意無私的團隊合作,以企業成敗為己任,也才能有效地強化生產效率、減少問題的發生。
原則11:
重視合作夥伴
∙豐田集團還會把擁有合作關係的企業體視為集團的延伸,並盡可能地在各方面協助它們成長,幫助他們降低成本、提高效率,甚或指導它們採用豐田生產系統,使集團與協力廠商的生產力皆能共同成長,創造雙贏的局面。
原則12:
親臨現場了解情況
∙如果你不充分了解實際情況,就無法解決問題與作出改善,這意味你必須追溯源頭、親自觀察、深入分析情況,尤其是「現地現物」。
不要只根據別人呈報的資料或電腦螢幕顯示的東西作出推論,遠距離地解決問題。
∙在豐田集團,當生產線出現問題時,管理者第一時間通常就是得親自前往現場,藉由實際觀察問題的產生,研究解決之道;而不是只透過生產線員工口述,便輕易提出問題的解決之道,這樣才能減少二次問題發生的機會,真正徹底解決問題的發生。
原則13:
提出並解決5個W
∙發生問題後,豐田生產系統內就會先針對問題提出5個W:
Why、Who、When、Where與What,再透過集體討論的方式,在團隊內形成共識,再討論問題可能的解決方法。
這樣的解問題方法雖然較花費時間,但卻可以從根本中找出問題,並徹底進行解決。
原則14:
不斷檢討,持續改善
∙就算生產線運作正常、企業體持續成長,但在豐田集團內這樣卻是不夠的,因為豐田生產系統期望每個員工都能透過不斷的學習以持續成長,並時刻反省,甚至在生產過程中找出更適合的作業方法,協助生產線降低生產成本、提高效率,而這也是豐田生產系統的核心價值之一。
豐田式生產管理
豐田式生產管理(ToyotaManagement),或稱豐田生產體系(ToyotaProductionSystem,TPS)由日本豐田汽車公司的副社長大野耐一創建,是豐田公司的一種獨具特色的現代化生產方式。
它順應時代的發展和市場的變化,經歷了20多年的探索和完善,逐漸形成和發展成為今天這樣的包括經營理念、生產組織、物流控制、質量管理、成本控制、庫存管理、現場管理和現場改善等在內的較為完整的生產管理技術與方法體系。
精益生產( LeanProduction)管理是美國麻省理工學院給豐田式生產管理的名稱。
豐田生產方式又稱精細生產方式,或精益生產方式。
豐田式生產管理簡介
美國《商業周刊》2003年第一期評選出世界十五位最傑出經理人,日本首家稅前盈餘超過1兆日元(87.4億美元)的企業———豐田,其社長張富士夫 (FujioCho)名列榜上。
在日本經濟被人形容為“處在黑洞看不見曙光”之際,張富士夫此時能獲選,具有典範的意義與價值。
張富士夫認為,日本要脫離困境,無論是製造、服務業或者是政府,唯一的良方就是打破傳統產業(部門)藩籬,也就是要改變僵固思維模式,引進“豐田式生產管理”。
通過塑造豐田式生產管理的企業文化,張富士夫領導這家世界第三大的汽車廠,建立全球製造和銷售系統,成績亮麗,創下凈利達46億美元,銷售額比前一年同期增長15.4%為657億美元,並滿懷信心宣示:
“要實現全球年銷售量600萬輛的目標”,“要從現在全球10%占有率提升至15%”。
[編輯]
豐田式生產管理的起源和理念
TPS的靈感來自美國,而不是來自豐田自己的汽車生產過程。
豐田的代表團到美國訪問,研究美國的企業。
他們首先參觀了福特汽車公司位於美國密歇根州的汽車廠。
儘管當時福特汽車是行業的領導者,豐田代表團發現福特使用的很多生產方法,並不是很有效率。
令代表團最為震驚的是大量的庫存,工廠各部門的工作量並不平均。
不過,他們在訪問PigglyWiggly超級市場時,看到PigglyWiggly只會在顧客購買貨品之後,才重新進貨,代表團從而得到啟示。
豐田實踐從PigglyWiggly學習所得──減少存貨.存貨的水平只足夠其雇員使用一小段時間,然後重新訂貨。
這是典型的“即時生產”(JIT)。
而低庫存水平是豐田生產方式的一個關鍵的結果。
TPS背後的理念是杜絕浪費,因而不再需要庫存。
基本原則是“豐田模式”(TheToyotaWay),概述如下:
[編輯]
正確的流程方能產生正確結果
∙建立無間斷的作業流程以使問題浮現
∙使用「後拉式制度」以避免過度生產
∙平準化:
工作負荷平均(工作要像龜兔賽跑中的烏龜,而不是兔子那樣)
∙建立立即暫停以解決問題、一開始就重視品管的文化
∙職務工作的標準化是持續改善與授權員工的基礎
∙使用視覺控管,使問題無從隱藏
∙使用可靠的、已經經過充分測試的技術以支持人員及流程
[編輯]
發展員工與事業伙伴,以為組織創造價值
∙栽培徹底瞭解並擁抱公司理念的員工成為領導者,並使他們能教導其他員工
∙栽培與發展信奉公司理念的傑出人才與團隊
∙重視公司的事業伙伴與供貨商網路,挑戰它們,並幫助它們改善
[編輯]
持續解決根本問題是組織型學習的驅動力
∙現地現物:
親臨現場查看以徹底瞭解情況
∙決策不急躁,要通過協商以共識為基礎,徹底考慮所有可能選擇,快速執行決策
∙透過不斷地省思與持續改善,以變成一個學習型組織
[編輯]
豐田式生產管理:
不降低成本就無法提高利潤
成本中心型
以計算或實際的成本為中心,加上預先設定好的利潤而得出售價,其公式為:
售價=成本+利潤
在供應<銷量時,在壟斷產品時可以如此定價
售價中心型
在供應>銷量時,以售價為中心,當市場售價降低時利潤隨之減少,其公式為:
利潤=售價-成本
缺乏改善意識的企業屬於此類型,市場好時有較高的利潤,市場差時大幅度下降
利潤中心型
在供應>銷量時,以利潤為中心,當市場售價降低時,成本也必須下降以獲得的利潤(目標利潤 )不會減少,其公式為:
成本=售價-利潤
減少浪費--降低成本的主要手段
什麼是浪費?
不增加價值的活動(如:
生產過程改變零件尺寸、形狀或功能,非價格)是浪費;儘管是增加價值的活動,但所用資源超過了絕對最少的界限,也是浪費
豐田式生產管理目的就是取消那些不增加產品價值的工作,即降低成本。
[編輯]
豐田式生產管理哲理的理論框架
豐田式生產管理哲理的理論框架包含“一個目標”、“兩大支柱”和“一大基礎”。
“一個目標”是低成本、高效率、高質量地進行生產,最大限度地使顧客滿意。
“兩大支柱”是準時化與人員自主化。
準時化(JIT-Justintime)生產。
即以市場為龍頭在合適的時間、生產合適的數量和高質量的產品,JIT需要以拉動生產為基礎,以平準化(LevelingSystem)為條件。
所謂拉動生產是以看板管理為手段,採用“取料制”即後道工序根據“市場”需要進行生產,對本工序在製品短缺的量從前道工序取相同的在製品量,從而形成全過程的拉動控制系統,絕不多生產一件產品。
平準化是指工件的被拉動到生產系統之前要進行人為的按照加工時間、數量、品種進行合理的搭配和排序,使拉動到生產系統中的工件流具有加工工時上的平穩性,保證均衡生產,同時在品種和數量上實現混流加式運動,起到對市場多品種、小批量需要的快速反應和滿足功能。
人員自主化是人員與機械設備的有機配合行為。
生產線上產生質量、數量、品種上的問題機械設備自動停機,並有指示顯示,而任何人發現故障問題都有權立即停止生產線,主動排除故障,解決問題。
同時將質量管理溶入生產過程,變為每一個員工的自主行為,將一切工作變為有效勞動。
“一大基礎”是指改善(Improvement)。
改善是豐田式生產管理的基礎。
這裡的改善是指這樣的含義:
①從局部到整體永遠存在著改進與提高的餘地。
在工作、操作方法、質量、生產結構和管理方式上要不斷地改進與提高。
②消除一切浪費。
豐田式生產管理哲理認為不能提高附加價值的一切工作(包括生產過剩、庫存、等待、搬運、加工中的某些活動,多餘的動作,不良品的返工等)都是浪費。
這些浪費必須經過全員努力不斷消除。
③連續改善(ContinuousImprovement)是當今國際上流行的管理思想。
它是指以消除浪費和改進提高的思想為依托,對生產與管理中的問題,採用由易到難的原則,不斷地改善、鞏固,改善、提高的方法,經過不懈的努力,以求長期的積累,獲得顯著效果。
[編輯]
豐田式生產管理的關鍵原則
豐田式生產管理的關鍵原則歸納如下:
一、建立看板體系(Kanbansystem)。
就是重新改造流程,改變傳統由前端經營者主導生產數量,重視後端顧客需求,後面的工程人員通過看板告訴前一項工程人員需求,比方零件需要多少,何時補貨,亦即是“逆向”去控制生產數量的供應鏈模式,這種方式不僅能節省庫存成本(達到零庫存),更重要是將流程效率化。
二、強調實時存貨(JustInTime)。
依據顧客需求,生產必要的東西,而在必要的時候,生產必要的量,這種豐田獨創的生產管理概念,在80年代即帶給美國企業變革的思維,現已經有很多企業沿用並有成功的案例。
三、標準作業徹底化。
他們對生產每個活動、內容、順序、時間控制和結果等所有工作細節都制定了嚴格的規範,例如裝個輪胎、引擎需要幾分幾秒鐘。
但這並不是說標準是一成不變的,只要工作人員發現更好更有效率的方法,就可以變更標準作業,目的在於促進生產效率。
四、排除浪費、不平及模糊等。
排除浪費任何一絲材料、人力、時間、能量、空間、程式、運搬或其他資源。
即排除生產現場的各種不正常與不必要的工作或動作時間人力的浪費。
這是豐田生產方式最基本的概念。
五、重覆問五次為什麼。
要求每個員工在每一項任何的作業環節里,都要重覆的問為什麼(Why),然後想如何做(How),以嚴謹的態度打造完美的製造任務。
六、生產平衡化。
豐田所謂平衡化指的是“取量均值性”。
假如後工程生產作業取量變化大,則前作業工程必須準備最高量因而產生高庫存的浪費。
所以豐田要求各生產工程取量儘可能達到平均值,也就是前後一致,為的是將需求與供應達成平衡,降低庫存與生產浪費。
七、充分運用“活人和活空間”。
在不斷的改善流程下,豐田發現生產量不變,生產空間卻可精簡許多,而這些剩餘的空間,反而可以做靈活的運用;相同人員也是一樣,例如一個生產線原來六個人在組裝抽掉一個人,則那個人的工作空間自動縮小,空間空出來而工作由六個人變成五個人,原來那個人的工作被其他五人取代。
這樣靈活的工作體系,豐田稱呼為“活人、活空間”即鼓勵員工都成為“多能工”以創造最高價值。
八、養成自動化習慣。
這裡的自動化不僅是指機器系統的高品質,還包括人的自動化,也就是養成好的工作習慣,不斷學習創新,這是企業的責任。
這點完全如松下幸之助所說:
“做東西和做人一樣”,通過生產現場教育訓練的不斷改進與激勵,成立學苑讓人員的素質越來越高,反應越快越精確。
九、彈性改變生產方式。
以前是生產線上(line)作業方式,一個步驟接著一個步驟組裝,但現在有時會視情況調整成幾個員工在一作業平臺(Cell)上同時作業生產。
NEC的手機製造工廠,因為需同時生產二十幾種款式手機,所以激活機器人並無法發揮效率,他們就採用上述方式,一桌約三、四個員工作業,來解決現場生產問題。
[編輯]
豐田式生產管理的四大規則
蘊涵在豐田式生產管理之中的隱性知識(TacitKnowledge)可以用四條基本規則來概括。
這些規則指導著每一產品和服務所涉及的每一項作業、每一處銜接和每一條流程路線的設計,實施和改進.這四條規則如下:
規則一:
所有工作的內容、次序、時間和結果都必須明確規定。
規則二:
每一種客戶-供應商關係都必須是直接的,發送要求和得到回應的方式必須明確無誤,非“是”即“否”。
規則三:
每一種產品和服務的流轉路線都必須簡單而直接。
規則四:
所有的改進都必須在老師的指導下,按照科學的方法,在儘可能低的組織層面上進行。
這四條規則要求,企業的各種作業、銜接和流程路線必須能夠進行自我檢測,以自動發出問題警示。
正是由於不斷地對問題做出響應,看似僵化的體系才得以保持柔性,能夠靈活適應不斷變化的環境。
[編輯]
把握TPS的幾個要點
精益生產是TPS的精髓。
早在1996年,美國學者JamesP.Womack和英國學者DanielT.Jones就在《精益思想:
消滅浪費,創造財富》一書中詮釋了TPS就是”精益製造”的先進理念。
其目的是”喚醒仍然堅持舊式大量生產方式的各種機構、管理者、職工和投資者”。
精益生產也是美國麻省理工學院多位國際汽車計劃組織的專家對TPS的贊譽之稱。
精益生產是一種以最大限度地減少企業生產所占用的資源和降低企業管理和運營成本為主要目標的生產方式。
同時,它又是一種理念、一種文化。
實施精益生產就是決心追求完善的學習過程中獲得自我滿足的一種文化境界。
只有精益理念在企業領導和所有員工思想里牢固確立,才能把握與之相關的理念,作為企業持續改進的強有力工具,構築企業的精益系統,TPS才能在企業實施到位。
持續改善是TPS的基礎。
可以說,沒有改善就沒有TPS。
這裡的“改善”包括三個意思:
一是從局部到整體的改善。
在企業發展的道路上,永遠存在著改進與提高的餘地。
在工作、操作方法、質量,生產結構和管理方式上要不斷地改進與提高。
二是消除一切浪費。
不能提高附加值的一切工作(包括生產過剩、庫存、等待、搬運、加工中的某些活動,複雜的動作,不良的返工等)都是浪費,都應通過全員行為不斷加以消除。
三是連續改善。
這也是當今世界流行的管理思想。
它是以消除浪費和改進提高的思想為依托,對生產與管理中的問題,採用由易到難的原則,不斷地改善、鞏固、改善、提高,以求長期的結果,獲得預期成效。
全員參與是TPS的保證。
1969年,美國《幸福》雜誌在其“豐田”專輯里曾指出:
“豐田公司高速發展的秘密就在於有一支卓越的管理隊伍和一支高效的職工隊伍”,很顯然,這兩支隊伍的共同組成要素都是人。
TPS的準時化生產、看板管理、全面質量管理、生產的分工與協作以及消除浪費為核心的合理化活動等,所有這一切都離不開人的積极參与,都離不開具有積極性、主動性、創造性的人。
所以,推行TPS,必須尊重人性,調動人的積極性,培養人的責任感和自主精神,促使人們去尋求腳踏實地完成工作的更好方法。
IE(工業工程)是TPS的根基。
日本自20世紀60年代從美國引進了IE技術,根據本國民族文化特色加以發展、應用。
為TPS這一先進的生產管理模式提供了堅實的基礎。
IE解決的主要問題是各類產品生產過程及服務過程中的增值鏈問題。
通俗地講,就是新產品進入生產階段後,運用IE的知識來解決生產的組織與運行問題,如:
如何縮短生產線,如何進行零部件和製成品的全球配送,如何保持生產或服務的質量等等。
美國是IE的發源地,IE奠定了美國成為世界經濟霸主地位。
英國、德國、日本以及亞洲四小龍都成功引進了IE,促進了本國經濟的騰飛,這些發達國家和地區的IE建設與發展經驗,值得導入TPS的國內企業借鑒與效仿。
[編輯]
豐田式生產管理:
工人如何學習規則
如果說豐田式生產管理的規則是隱性的,那麼它們又是怎樣傳播的呢?
豐田的管理者並不具體告訴工人和主管們如何工作,而是採用一種教與學的方法,讓工人們通過解決問題來領悟這些規則。
例如,在教第一條規則時,主管會來到工作現場,向正在工作的工人提出一系列問題:
●你是怎樣做這項工作的?
●你怎樣判斷自己做的方式是正確的?
●你如何知道自己的工作成果沒有瑕疵?
●如果遇到問題,你會怎樣處理?
這一持續發問的過程,使得員工對自己的具體工作領悟得越來越深刻。
在經歷了多次類似的提問之後,這名員工就逐漸學會瞭如何按照規則一來設計各種作業。
所有的規則都是通過蘇格拉底式的反覆提問和解決問題來傳授的。
雖然這是一種非常有效的教學方法,但是員工獲得的知識卻是隱性的,所以,只有當管理者有能力並且願意用這種提問方式來督促工人在實踐中學習時,豐田生產方纔能夠被成功地複製和移植。
[編輯]
推廣和應用豐田生產方式的思考
豐田生產方式是當今國際上最為成功的集約型管理模式之一,歐美各國紛紛對該生產方式進行了研究和推廣,並已取得顯著成效。
我國也有許多企業在研究和借鑒豐田生產方式,下麵對推廣和應用豐田生產方式的一些思考。
1.推行豐田生產方式,最高管理層一定要有堅定不移的決心,一定要給予系統持續的有力的與可見的支持豐田生產方式的建立初期必然頻繁地打破生產系統的正常和平穩,並隨時可能暴露出生產系統中存在著的種種問題和隱患。
如果最高管理層沒有堅定推行的決心,不能經常給予企業中每一個員工實行變革的鼓勵與支持,那麼現場管理人員和f1業人員就不會針對問題積極地提出持續改進的設想和實施,就不可能在問題出現之後很快地予以消除,從而產生畏難情緒和挫折感,動搖推行豐田生產方式的信念。
這樣,使得豐田生產方式的推行必然是虎頭蛇尾,有始無終,有限的努力付諸東流。
所以,推行豐田生產方式,最高管理層一定要對系統給予熱情的鼓勵和有力的支持,並直接地參與到系統的實施中去,同時要教育中層管理人員照此效法,讓每一個員工感到推行豐田生產方式決無迴旋的餘地。
2.推行豐田生產方式要杜絕一切浪費。
豐田生產方式的基本原則就是“杜絕一切形式的浪費。
因此,“無浪費”就成了豐田生產方式和管理方法的核心。
準時化生產的創始人大野耐一曾經多次指出:
“豐田生產方式及其管理方法的最重要的精神就是杜絕切形式的浪費”。
他認為,提高生產率的最簡單、最迅速,而且不花錢的方法就是杜絕浪費。
為此,豐田公司的生產方式和管理方法始終把“杜絕一切形式的浪費”,徹底降低成本作為基本原則和追求的目標,並以此作為獲得利潤的源泉。
事實上,在我國的一些企業存在各種各樣的浪費,例如長明燈、長流水、聞人過多、庫存過多、在製品過多、無效勞動等等。
然而,一般人對這些浪費往往習以為常,甚至有人會認為這些浪費是必要的、不可避免的。
但是,豐田公司卻認為,這些“正常的浪費、必要的浪費、不可避免的浪費,乃至看不出來的浪費,其實是最可怕的浪費和最大的浪費”。
所以,推行豐田生產方式,一定要把那些在別的企業眼裡視為“正常的、必要的、不可避免的浪費”統統找出來,然後逐步採取措施堅決地予以消除。
3.推行豐田生產方式、必須堅持動態的自我完善。
豐田生產方式不滿足於生產系統的正常和平穩,相反,它總是試圖打破已有的正常和平穩,而進八到更高水平的運行狀態。
當生產系統平穩運行時,他們總是通過減少看板數量而強制性地減少工序之間在製品儲備量(或者壓縮生產前置期、減少作業人數),從而迫使生產系統中存在的問題和隱患在不平穩中暴露出來,如設備保養不善、加工能力不均衡、作業人員技能差異、工序作業銜接不良等等。
當這些問題和隱患暴露出來之後,要求現場管理人員和作業人員針對問題提出改善措施、消除問題,使生產系統達到新水平的穩定。
當一個新水平的穩定達成之時,也就是下一階段改善的開始之日,從而使得改進活動如同大海的波濤,一浪緊隨一浪,把生產系統不斷推向更高水平。
4.推行豐田生產方式,必須尊重人性,調動人的積極性。
1969年,美國的《幸福》雜誌在其豐田”專輯里曾經指出:
“豐田公司高速發展的秘密就在於有一支卓越的管理隊伍和一支高效的職工隊伍”。
很顯然,這兩支隊伍的共同組元都是人,豐田公司的準時化生產、看板管理、全面質量管理、質量管理活動小組、合理化建議制度、生產的分工與協作以及以消除浪費為核心的台理化運動和改善活動等等,所有這一切都離不開人的積极參与,都離不開具有積極性、主動性、創造性和衝天幹勁的人。
豐田公司把“尊重人性”作為人事政策的綱領,它主要體現在對員工良好的教育和培養上,從而為員工個人價值的實現,以及由此而贏得尊重創造了條件。
同時,受到良好教育和培養的員工也為公司勞動生產率的提高,產品質量的提高,生產成本的降低以及向更高程度的合理化邁進奠定了堅實的基礎。
豐田公司正是通過培養人、尊重人的途徑訶動起人的主觀能動性和創造性,從而激勵員工去消除汽車生產經營過程中的各種難以預料的不利因素,從而實現準時化生產,實現生產系統的柔性,以不變應萬變。
所以,推行豐田生產方式,必須尊重人性,調動起人的積極性,培養人的責任感和自主精神,促使人們腳踏實地地去尋求完成工作的更好方法。
5.關於庫存問題的思考。
應該承認,豐田公司獲得巨大成功的背後灑下了不計其數的承包協作企業的汗水和淚水。
豐田所實行的生產方式嚴格地要求其承包協作企業準時地、頻繁地交送其所需要的零部件,所以,豐田公司本身沒有多餘的庫存,因而