槽钢孔型设计.docx
《槽钢孔型设计.docx》由会员分享,可在线阅读,更多相关《槽钢孔型设计.docx(18页珍藏版)》请在冰豆网上搜索。
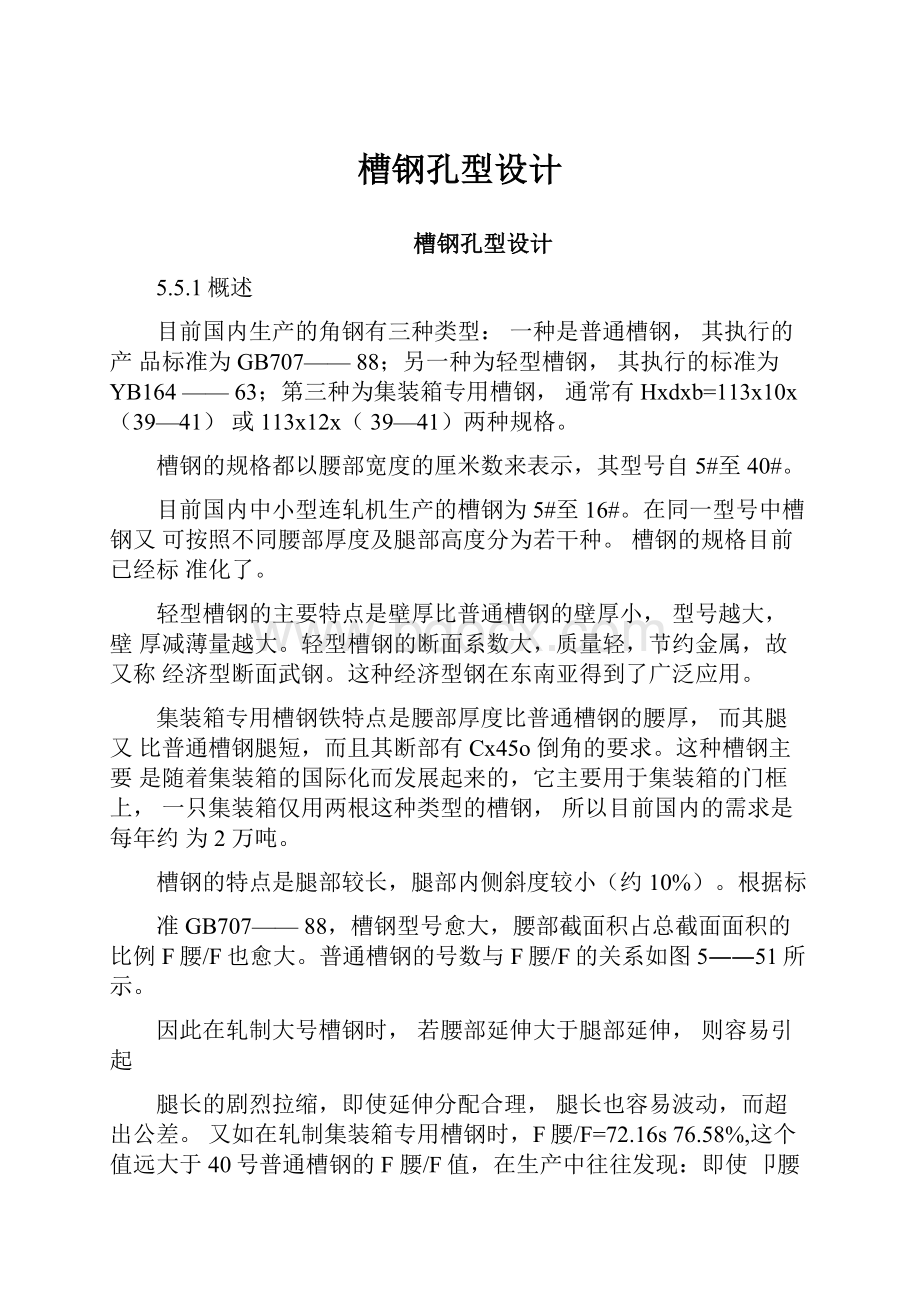
槽钢孔型设计
槽钢孔型设计
5.5.1概述
目前国内生产的角钢有三种类型:
一种是普通槽钢,其执行的产品标准为GB707——88;另一种为轻型槽钢,其执行的标准为YB164——63;第三种为集装箱专用槽钢,通常有Hxdxb=113x10x(39—41)或113x12x(39—41)两种规格。
槽钢的规格都以腰部宽度的厘米数来表示,其型号自5#至40#。
目前国内中小型连轧机生产的槽钢为5#至16#。
在同一型号中槽钢又可按照不同腰部厚度及腿部高度分为若干种。
槽钢的规格目前已经标准化了。
轻型槽钢的主要特点是壁厚比普通槽钢的壁厚小,型号越大,壁厚减薄量越大。
轻型槽钢的断面系数大,质量轻,节约金属,故又称经济型断面武钢。
这种经济型钢在东南亚得到了广泛应用。
集装箱专用槽钢铁特点是腰部厚度比普通槽钢的腰厚,而其腿又比普通槽钢腿短,而且其断部有Cx45o倒角的要求。
这种槽钢主要是随着集装箱的国际化而发展起来的,它主要用于集装箱的门框上,一只集装箱仅用两根这种类型的槽钢,所以目前国内的需求是每年约为2万吨。
槽钢的特点是腿部较长,腿部内侧斜度较小(约10%)。
根据标
准GB707——88,槽钢型号愈大,腰部截面积占总截面面积的比例F腰/F也愈大。
普通槽钢的号数与F腰/F的关系如图5――51所示。
因此在轧制大号槽钢时,若腰部延伸大于腿部延伸,则容易引起
腿长的剧烈拉缩,即使延伸分配合理,腿长也容易波动,而超出公差。
又如在轧制集装箱专用槽钢时,F腰/F=72.16s76.58%,这个值远大于40号普通槽钢的F腰/F值,在生产中往往发现:
即使卩腰大与卩腿相同,但由于轧制过程中腿部的外侧壁磨擦力大于腰部的磨擦力,因此在腿部厚度方向磨损较快,从而产生□腰>卩腿的情况,导致了腰部
拉腿收缩的后果,使腿长往往小于产品标准规定。
5.5.1槽钢孔型系统
轧制槽钢的孔型系统有直轧孔型系统、弯腰式孔型系统、大斜度孔型系统及工字钢轧制系统。
上述孔型系统都不得有切深孔、控制孔、成品孔三种孔型组成。
直轧孔型系统腿部外侧壁斜度较小,一般成品孔为1s1.5%其它孔型为4s10%;而且切槽深,当孔型磨损后重车量大,往往一对轧辊只能使用1s3次。
另外轧件不易脱槽,易造成冲卫板、缠辊等事故。
弯腰式孔型系统可采用较大的腿部外侧斜度,成品孔为5s10%,其它各孔为10s20%孔型磨损后的轧辊重车量小,轧辊使用寿命长;轧件容易脱槽,减少了对卫板的冲击和缠辊事故。
大斜度孔型系统即孔型的侧壁斜度比弯腰式的还要大,其成品孔可达12%,其它各孔的斜度可达30%以上,因而在轧辊的重车次数、轧件易脱槽、减少各类轧制中的生产事故等方面这种孔型系统都优于弯腰式孔型系统。
同时由于其轧辊上的各点的直径差小于上述两种系统的直径差,因此由于速度差而产生的拉缩腿部的现象比上述两种有所改善,所以还可适当减小坯料的高度。
工字钢轧制系统的实质就是在粗轧孔型系统中采用共同的孔型。
其主要优点是当工字钢和槽钢相互转换时,可减换辊次数,起到提高轧机作业率和减少轧辊储备的作用。
但由于假腿的作用是牵制腰部对腿部的拉缩作用,而粗轧共用孔型就必须大大压缩假腿,从而产生不均匀变形的程度增加,轧槽磨损增加。
上术四种孔型系统中,弯腰式和大斜度的孔型系统比较适合于连轧机组。
但是当矫直能力不足时,就必须采用直轧孔型系统。
5.5.3孔型设计
5.5.3.1面积划分一般把槽钢分为腰部、腿部及假腿三个部分。
5.5.3.2孔型设计槽钢的型设计一般从成品孔开始往前按照逆轧制顺序进行,成品孔为第1孑L,即K1孑L,成品前孔为第二孔,即K2孑L,其他依次类推。
Bn表示第n孔的宽度,Hn-1表示第n—1孔的高度,dn表示第n孔的腰部厚度。
A、成品孔设计
根据GB707—88,由图5—54可知:
Bi=(B—部分负偏差)x(1.01〜1.03)(5—42)
5—43)
0〜部分正偏
5—44)
di=d—(0〜部分负偏差)
m={[H+(0〜部分正偏差)]—〔d+差)〕}x(1.011〜1.013)
式中:
B、d、H――分别为槽钢的腰宽、腰厚及腿长的标准尺寸
计算hi时,应考虑到腰厚di调整到最大正偏差时,腿长H不超出最大正偏差;当腰厚d1调整到最小负偏差时,腿长H不小于最小负偏差。
锁口余量△=5~10mm,且
ti=(0.96〜1)t(5-45)
式中t——腿厚的标准尺寸。
ai=ti—〔(hi/2)x(1/10)〕(5-46a)
bi=b+〔(h1/2)x(1/10)〕(5-46b)
为防止槽孔磨损后腿部太厚,则腿厚a、b可取部分负偏差,但
不能过大,否则在装辊及导卫安装不当、调整不当时,易使一条腿厚超出负偏差。
当腿部斜度®值取得较小时(约1%左右),贝庐生如下问题:
(1)®太小,使接触弧长度增加,金属横向运动加剧,使腿的外侧壁磨损增加,常常造成成品肩角且腰部与腿外侧壁夹角大于90°,或“塌角”。
(2)®太小,使轧件难于脱槽,容易造成缠辊等轧制事故。
(3)®太小,腿部外侧壁磨擦力增加,轧制负荷增加。
某厂在①400连轧机组上轧制GB70—88中的8号槽钢,当9=1%时,其成品机架的轧制电流竟达1000~1200A。
(4)轧槽寿命低,单槽轧制吨位往往只能达到100t左右,
而且重车时不仅难度大,而且只能重车1~2次,辊耗极大。
(5)成品质量较差,由于外侧壁磨擦剧烈,因此腿外部的表
面上有较严重的擦伤和刮伤,而且在槽钢的内圆角处易发生网裂。
(6)®太小,使成品前孔的轧件在进入成品孔时,由于其腿
部的较大,而使轧件经多道次轧制后,进入成品孔的轧件腰部端头呈舌状,即进成品孔时,腰部先咬入、压平,所以对成品前孔的轧件腿外侧斜度有收小作用。
但过大的A®,则产生强烈的收缩,会引起槽钢腿外侧严重擦伤。
在横列式轧机上轧制槽钢(GB707-88)时,一般卩腰=□腿+(0~0.02),即腰部的延伸系数大于腿部的延伸系数,腰部金属拉缩腿部金属,以保证腰部的肩角不产生“塌角”。
但在连轧机中,由于粗、中轧一般没有活套轧制,实际操作中存在着“微拉”轧制的不良操作。
即使精轧有活套,也存在着起套的间隙时间。
在两架连轧机之间活套没有形成时,一定产生大小不一的拉钢轧制,因此上面三个因素都使腿长发生变化,所以如果继续采用□腰腿的设计方法,则无法保证腿部尺寸。
当轧制F腰/F腿较大的集装箱专用槽钢时,则腿部尺寸不容易控制的情况尤为突出。
因此,连轧机中成品孔的腰部延伸系数希望略小于腿部延伸系数,即
□腰=卩腿一(0.01~0.03)(5—47)
当腿部斜度®取得较大时,一般不小于5%,上述六个不足之处将得到很大改善。
如果车间有矫正能力,则希望采取5%。
倘若矫直能力不足,则建议将腿部斜度由5%以上改为3%较为适宜。
某连轧机组轧制8#槽钢和集装箱专用槽钢时,成品孔腿部斜度在5%
时,经7辊矫直机矫直后的两腿外侧斜度往往为(3〜4%)H,超过GB70—88中2.5%的规定。
当把此腿部斜度由5%改为3%时,则可完全解决此“扒脚”问题。
B切分孔设计
为了获得合格的成品腿长以及防止控制孔出耳子,正确设计切分孔非常重要。
一般切分孔的孔型特征是两腿的内壁在腰部相交,且一般腰厚>20mm以及实际腿根厚度2g>B/2,见图5-55。
a切分孔的形状切分孔有开口式和闭口式两种,这两种的优缺点已在前面介绍了。
但不论开口式或闭口式,其切分孔两腿内侧壁的交角大小对轧制时切分孔型中的充满情况和能量消耗、轧槽磨损都有很大影响。
根据切分孔型中金属不均匀变形的过程可以明显地看到:
当切入楔角度减小时,腿部的充满情况得到改善,轧制时的能量消耗减小,同时切分孔型中的总延伸量也就减小。
设计切分孔型下槽的“楔子”时应注意到:
如“楔子”太钝,则金属的拉缩愈严重,显然对腿长形成不利;若“楔子”太尖,对腿长形成有利,但下槽冷却条件较差,“楔子”容易磨损,当磨损严重时,容易使轧件表面产生沟痕且不易消除,将影响到成品的表面质量。
a切分孔切入孔型的条件
对一般切分孔来讲,切入楔的总高度与腿部高度上的压下量之和大于该机座轧辊直径的20%,则轧件就咬入困难,即
刀f+Ahp=<0.2D
式中刀Hq……上、下切入楔的高度之和即(h上+h下);
△hp—腿部高度上的压下量(见图5-56)
按切入楔顶端计算的相应咬入角为:
a=(180/3.14)〔(△h/R)开平方〕=(180/3.14)〔(0.2D/0.5D)
开平方
若用孔型中的平均压下量计算咬入角则更为正确,这时将(平
均)代入。
△h等于:
△h=H0—F切/B切
式中H0……切分前坯料高度;
F切、B切分别为切分孔的面积和宽度。
将上述公式代入a=(180/3.14)〔(△h/R)开平方〕中,则对于钢辊,平均咬入角为24~25o,由此根据最大压下量按咬入角和磨擦角相等的条件可算出:
△hmax=D-[D/(1+f2)开平方]
式中f磨擦系数。
上式可简化为:
2
△hmax坐0.5Df(5……49)
因此可根据式5—49来计算采用切分孔的数量和形状。
当咬入角过大时,则可采用两个连续的切分孔型来对坯料依次进行逐步切分,并且第一个切分孔一般为开口孔,第二个切分孔大部分取闭口孔。
第一个取开口孔主要是为了便于咬入和增加轧辊强度,第二个切分孔取
闭口孔主要是为了得到较正确的腿部尺寸。
c腰部带侧压的大斜度闭口切分孔
腰部带侧压的大斜度闭口切分孔可对连铸坯或轧制坯直接进行切分,在切出和压薄轧件腰部的同时可减小轧件腰部的宽度,以适应中、精轧弯腰大斜度槽孔宽度的要求。
这种孔型有以下优点。
(1)从图5——57中看到,这种孔型可阻止腿部的金属向腰部流动,因此可以减小切分孔腰部的垂直压缩对轧件腿长的拉缩作用,从而可用相同高度的坯料轧出较长的成品腿。
(2)对轧件的夹持作用大,改善咬入条件,提高轧制稳定性。
(3)宽展量较小,促使轧件腰部的金属向槽钢的两个间角流动,保证肩角充满良好,减少“秃角”、“塌角”缺陷。
(4)脱槽容易,同时减轻对上卫板的负荷,避免发生缠辊事故。
d切分孔的拉缩率
切分孔的拉缩率5表示切分孔来料高度与切分孔尺寸的关系
(见图5——85),即
5=[(H-A)/(H-d)]100%
式中H进入切分孔前的坯料高度;
A——切分孔的高度;
d——切分孔的腰部厚度。
一般拉缩率在25s50%
e切分孔的侧压
当轧件进入切分孔时应给予一定的侧压量,以增加咬入及提高轧件在切分孔中的稳定性。
侧压量太大,则孔型侧壁容易磨损。
侧压量的大小可根据坯料厚度B和孔型宽度b用作图法来确定。
一般用矩形坯时,矩形坯与孔型开始接触时的空隙量x为3s6mm见图5――59。
为提高轧件在切分孔中的稳定性,希望钢坯侧面的斜度和切分孔型的侧壁斜度能基本相同。
表5――13列出某连轧机上采用闭口切分孔时外侧壁斜度®随
规格变化的情况。
表5――13外侧壁斜度随规格变化的情况
规格
5#
6.5#
8#
10#
12#
14#
16#
b/mm
45
54.5
72.5
91.5
95
108.7
128
B/mm
65
76
88.5
103.5
109
126
140
A/mm
51
62
77.5
89
116
124.5
132
2/%
19.6
17.3
10.32
6.74
6.03
6.95
4.55
从表5――13中可以看到®基本上是随着规格的增大而减小。
C切分孔前坯料的设计
切分孔前的坯料对横列式轧机来讲基本上都选择矩形坯。
但在连
轧机上由于切分孔前的的轧件要有较正确的断面,因此只要有可能一
般都不得尽量采用方坯断面。
a钢坯与成品断面的尺寸比
从图5――60和表5――14可看出成品断面尺寸(He、Be)与坯断面尺寸(Ho、Bo)的关系。
b切分孔前坯料与成品断面的尺寸比
切分孔前坯料与成品断面的尺寸关系如表5――15所示。
其中H/为切分孔前断面的高度,B/为切分孔前断面的宽度。
D控制孔的设计
a控制孔配置的数量与位置
一般情况下,轧制槽钢配置两个控制孔,这两个控制孔通常是这样安排的:
第一个控制孔尺可能贴近成品孔,但不能把成品孔作为控
坯料断面/mm2
规格
Ho/He
Bo/Be
槽孔总宽展量/mm2
1002
5#
100/38
100/50
—50
1302
6.5#
130/42
130/65
—65
1302
8#
130/45
130/80
—50
1302
10#
130/50
130/100
—30
1302
12#
130/55
130/120
—10
1302
14#
130/60
130/140
+10
1402
16#
140/65
140/160
+20
表5――15某厂连轧机关于切分孔前坯料与成品断面的尺寸关系
规格
标准
H//He
B//Be
槽钢总宽展量/mm
5#
DIN1026—63
61/38
61/50
—11
6.5#
GB707—88
61/40
61/63
+2
8#
GB707—88
79/43
79/80
+1
10#
DIN1026—63
95/50
95/100
+5
12#
DIN1026—63
94/55
122/120
—2
14#
DIN1026—63
108/66
142/140
—2
16#
DIN1026—63
127/65
145/160
+15
制孔,因为若成品孔为控制孔,虽可获得精确的腿部尺寸,但不能获得正确的顶角,顶角在压下量不足时不能够充满,而太下量过大时,则产生孔型过充满出耳子。
因此一般第一控制孔取成品前孔或成品前前孔(K3)较为合适,同时还要考虑到工厂的工艺布置。
安排第一个控制孔的原则是:
必须在控制孔的机后有取样的“剪切机”。
如果
不有通过在线的各种类型剪机正确、迅速地取得控制孔的实样,则此控制孔高的意义就不大了。
第二控制孔最好是放在切分孔后的第一个孔型。
该控制孔的作
用主要是可以控制由于切分前坯料的变化而造成腿高尺寸的变化。
上述两个控制孔中第一控制孔是必须设置的,而第二控制孔则视切分孔而定,倘若切分孔能保证获得精确的腿高尺寸,则可取消第二
控制孔
b控制孔类型
控制孔有闭口和半闭口两种,见图5——47。
目前一般采用半闭口的控制孔,这主要有以下三个原因:
(1)半闭口孔型的腿部斜度可以和相邻的开口孔的腿部斜度方向相同,由此可以消除腿部的弯曲现象,并可以避免进入下一道的困难。
(2)由于半闭口的孔型能消除半腿部弯曲现象,因而可以加大相邻孔型的侧壁斜度,增加轧制吨位,增加轧辊的重车次数。
(3)半闭口孔型切入轧辊较浅,有利于提高轧辊工作辊径强度。
半闭口孔型在腿部高度上压下量的分配形式取决于它本身的形状,见图5——61。
从图5——61可知:
在腿的下部不允许沿腿的厚度上进行压缩,因为这样会引起压缩的金属被除数挤入轧辊的辊缝中而形成耳子。
腿下部离轧辊辊缝愈远,也就是愈接近腿根,则腿部厚度上的压下量可以成比例地增加,这时孔型的开口处不会有出耳子的危险。
c控制孔的设计原则
控制孔的设计必须符合以下原则:
(1)an+1/an>bn+1/bn
(an+1—an)<(bn+1—bn)(5——51)
式中an+i、an分别为n孔、(n+1)孔的腿端尺寸;
bn+1、bn分别为n孔、(n+1)孔的腿根尺寸。
(2)当轧件从开口孔进控制孔时腿部尺寸按下式确定:
hn=hn-i+(3s13)mm(552a)
式中,(3s13)mm为控制孔的腿部直压量,其值随规格的增大而增大。
图5――62为轧件进控制孔时确定腿部尺寸的示意图。
(3)当轧件从控制孔或开口孔进开口孔时,轧件腿部按下式确定(见图5――63):
hn=hn-1-(0.5s3)mm(552b)
式中,(0.5s3)mm为腿部经过开口孔侧压后腿部尺寸的增长量(成品孔除外)。
E异型孔的设计
异型孔的设计见图5――64(大斜度变腰变形孔型)。
从图5——64中可知a=0,贝卩
B=2x{[b/2-(R-c)sinq/cosa+[2x3.14(R+d/2)/360]}(5—53)
a=arctg[(B—b)/(2H)]
h=H/cosa-(c+d)
式中B――腰部平均高度;
h――腿高。
a腰部尺寸的确定
根据腰部的压下量△dA确定各孔型的腰厚,根据腰部的宽展量△b确定各孔型的腰宽,即
dn==dn-1+△dn-1
Bn==Bn-l+△bn-1
(5——54)
由于腰部温度较低,特别是成品孔表面质量要求又较高时,压下量不宜取得太大,一般△d可按表5——16参考选取。
表5――16某连轧机轧制5――16#槽钢时的△d
机架
5#
6.3#
8#
10#
12#
14#
16#
K1
0.7
0.8
1.2
0.9
0.9
0.7
0.35
K2
1.9
2.2
1.5
1.6
2
1.4
1.45
K3
2.9
3.5
2.2
2.2
2.5
2
2
K4
5
6
3.5
4.8
3.5
3.3
3.9
K5
8.5
10
6.5
8.4
6
5.5
4.8
K6
12
15.3
6
12
7
K7
14
22
20
7.5
K8
9.5
K9
7.5
从表5——16知,K1sK5孔的△d如下:
K1:
△d=0.35s1.2;&:
△d=1.4s2.2;K3:
△d=2s3.5;K4:
△d=3.3s6.6;K5:
△d=4.8s10。
△b可按表5——17参考设计。
表5——17K1sK5孔的△b
孔型号
K1
K2
K3
K4
K5
△b
1s1.2
0.8s1.2
1s2
2s2.5
3s4
在异型孔的设计中,要依照切分孔前的轧件宽度方向的尺寸与成品断面的宽度尺寸之差来设计切分孔后各道的△b,从而确定是采用负宽展轧制还是宽展轧之。
一般讲,负宽展轧制能使轧件在孔型中较为稳定,但反过来由于腰部侧压的存在,使磨擦力增加,轧槽外侧壁
磨损加剧,同时也增加了主电机负荷,而且使轧件脱槽困难。
所以,一般希望将负宽展轧制尽量放大前面的道次来完成,在接近成品的机架中,尽量不要采用负宽展轧制,以避免轧槽磨损加剧而影响成品质量,以及发生轧件缠辊的事故。
腰部的延伸系数按下式计算:
□n腰=(dn-lXBn-1)/(dnXBn)(555)
腰部的延伸系数也可参照以下公式确定:
粗轧机中:
□腰=卩腿+(0.05
~0.1)
中轧机中:
□腰=卩腿+(0.03
~0.05)
精轧机中:
□腰=□腿+(0.00
~0.03)
成品孔:
□
腰=□腿—(0.01~
0.03)
b腿部尺寸的确定
确定腿部孔型面积的原则是:
从粗轧到中轧到精轧到成品孔,各道次的变形不均匀程度由大至小逐步递减,以保证成品尺寸的精度。
一般讲,在K4孔前可采用较大的不均匀变形,而K1~K3孔则力求变形均匀。
当□腰选定后,腿部的面积为:
Fn腿=F(n-1)腿Xn-1)腿(556)
腿部面积确定后,则腿长可按式5—51和式5—52来确定。
c腰、腿部斜度的设计
当成品孔的腿部斜度不大于5%时,一般希望成品前孔腿部斜度
®小于10%其它各孔可仿效增大5%^10%同时希望相邻两个孔型的不宜过大,以防止发生腿端刮伤或鳞层等缺陷。
另外,控制孔前的弯腰孔的腿斜度应比控制孔腿斜度小2%^4%
腰部的斜度®—般等于腿部斜度或略小1%^2%即尽可能保持腰部与腿部基本垂直,以保证成品形状正确。
目前采用弯腰大斜度的孔型后,贝S成品前孔与成品孔的腿部
相差较大。
其原因是在粗、中、精的各道孔型中,其□腰〉□腿,因
此成品前的轧件其腰部头端总是呈舌状,即成品腰部先咬入,然后压
平,这样对成品前轧件腿外侧壁起到收小的作用,所以成品孔的咬入没有发生困难,同时由于腰部与腿部成90o,因此在实际生产中也未见外侧有鳞层和肩角、塌角等缺陷。
表5——18列出某厂5#s16#中K1与K2腿部斜度
表5――18某厂5#s16#中K1与K2的腿部斜度
规格
5#
6.3#
8#
10#
12#
14#
16#
K1
¥1/%
1.29
1.41
1
0.988
0.987
0.987
1.52
K2
¥2/%
30.87
29.38
24
22.73
16.26
15.27
9.15
/%
29.58
27.97
23
21.742
15.273
14.283
7.63
注:
j=¥2—¥1
从表5—18可看出:
随着规格的增大而逐步减小。
其5号槽钢,可达29.58%,而16号槽钢仅为7.63%当K2孔的腿部斜度①2确定后,则以后各孔依照上述原则逐步确定。
在连轧机原轧制中,要保证轧制的稳定性,则希望相邻机架的腿部外侧斜度尽量接近,同时又考虑到进入控制孔前的腿部斜度应小于控制孔的腿部外侧壁斜度,而且在辊道上输送又要力求稳定,因此在某些连轧机的槽钢孔型设计中,其腿部从腰的顶部到腿端有三个斜度
的变化,以适应轧制稳定和避免在控制孔出耳子的机率。
表5――19
和表5――20反映了某厂400连轧机组在轧制8#槽钢时,其孔型外侧壁顶点至腿端斜度的变化,以及进入孔型轧件与孔型外侧壁斜度差。
表5――19某厂/400连轧机8#槽钢孔型外侧壁顶点至腿端斜度的变化
名称
K1
K2
K3
K4
K5
K6
K7
K8
21机架
19机架
12机架
11机架
9机架
8机架
6机架
5机架
¥1/%
1.096
24
27.78
28.26
27.27
21.43
16.176
14.29
¥2/%
52.7
52.63
13.47
39.4
5.75
0
¥3/%
72.92
11.76
-16.33
-10
¥1垂直
投影/