注塑成型实用实用工艺基本地的知识.docx
《注塑成型实用实用工艺基本地的知识.docx》由会员分享,可在线阅读,更多相关《注塑成型实用实用工艺基本地的知识.docx(11页珍藏版)》请在冰豆网上搜索。
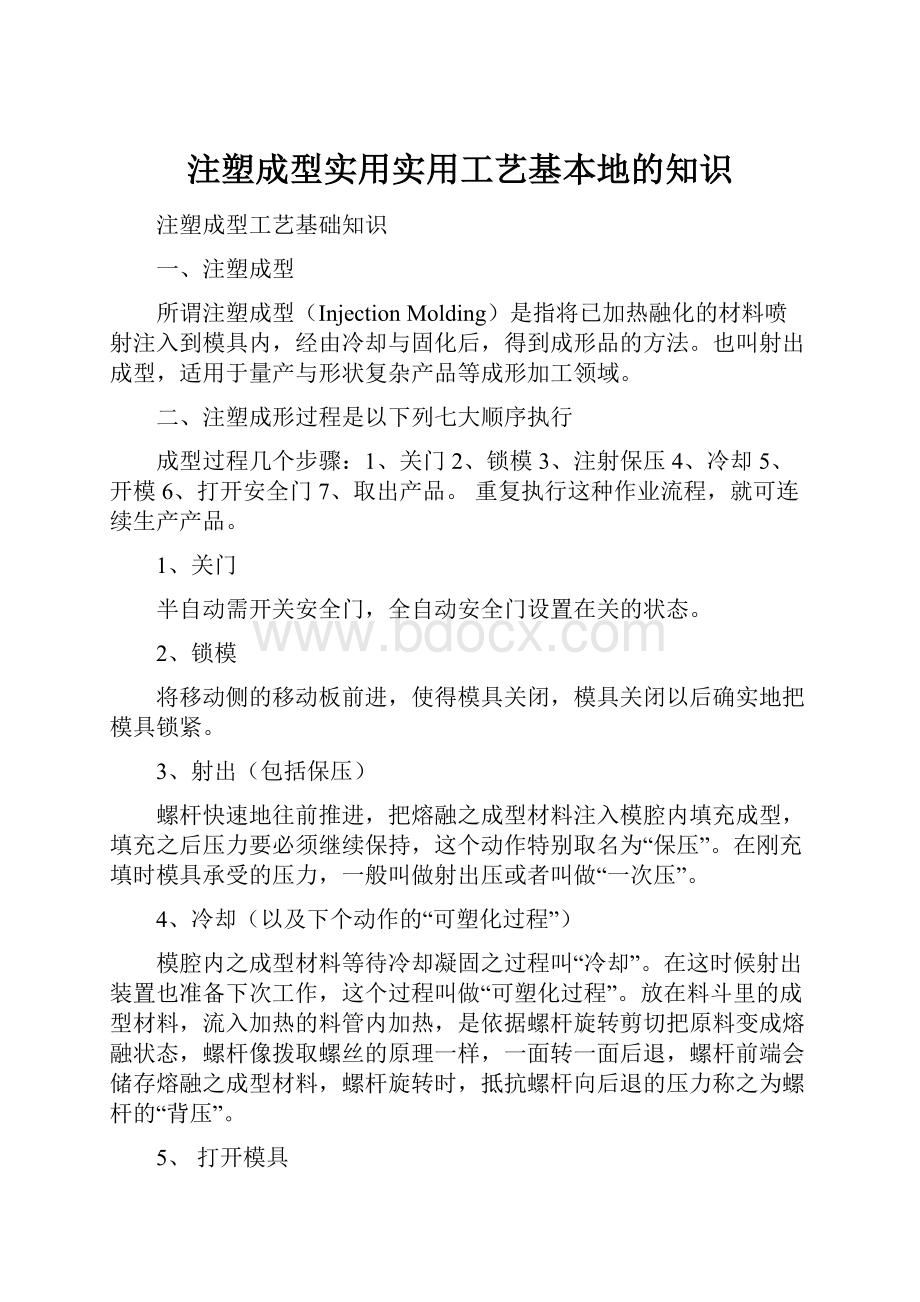
注塑成型实用实用工艺基本地的知识
注塑成型工艺基础知识
一、注塑成型
所谓注塑成型(InjectionMolding)是指将已加热融化的材料喷射注入到模具内,经由冷却与固化后,得到成形品的方法。
也叫射出成型,适用于量产与形状复杂产品等成形加工领域。
二、注塑成形过程是以下列七大顺序执行
成型过程几个步骤:
1、关门2、锁模3、注射保压4、冷却5、开模6、打开安全门7、取出产品。
重复执行这种作业流程,就可连续生产产品。
1、关门
半自动需开关安全门,全自动安全门设置在关的状态。
2、锁模
将移动侧的移动板前进,使得模具关闭,模具关闭以后确实地把模具锁紧。
3、射出(包括保压)
螺杆快速地往前推进,把熔融之成型材料注入模腔内填充成型,填充之后压力要必须继续保持,这个动作特别取名为“保压”。
在刚充填时模具承受的压力,一般叫做射出压或者叫做“一次压”。
4、冷却(以及下个动作的“可塑化过程”)
模腔内之成型材料等待冷却凝固之过程叫“冷却”。
在这时候射出装置也准备下次工作,这个过程叫做“可塑化过程”。
放在料斗里的成型材料,流入加热的料管内加热,是依据螺杆旋转剪切把原料变成熔融状态,螺杆像拨取螺丝的原理一样,一面转一面后退,螺杆前端会储存熔融之成型材料,螺杆旋转时,抵抗螺杆向后退的压力称之为螺杆的“背压”。
5、打开模具
将移动侧的移动板向后退,模具跟着打开。
6、打开安全门
安全门打开,这时成型机处于待机状能。
7、取件
将成品取出,然后检视确认模具内未残留任何物件再关门.
以上整个成型作业叫做一个成型周期。
成品是由模具的形状成型出来。
模具是由母模及公模组合成,公母模模仁之间留有空隙,材料在此流入压缩形成产品。
成型材料要流入公母模之前的通路有主流道(SPRUE)流道(RUNNER)闸门(GATE)等。
三、射出成型机
射出成型机以较大项目来区分,可分为两项,锁模装置和射出装置。
1、锁模装置
将模具关闭不被打开,成型材料在模腔内冷却凝固后,模具才打开然后取出成品等等动作的设备装置之锁模装置。
2、射出装置
将成型材料射出,填充到模腔内的设备装置称之射出装置。
此两个装置组合而成为射出成型机。
注射装置是将树脂予以加热融化后再射入模具内。
此时,要旋转螺杆,并如图所示让投入到料斗的树脂停留在螺杆前端(称之为计量),经过相当于所需树脂量的行程储藏后再进行射出。
当树脂在模具内流动时,则控制螺杆的移动速度(射出速度),并在填充树脂后用压力(保压力)进行控制。
当达到一定的螺杆位置或一定射出压力时,则从速度控制切换成压力控制。
四、射出成型机技术参数
射出成型机之能力基本上是下述3项规定来区分。
A锁模力
射出时,模具不被打开之最大锁模力,以TON数来表示。
成型品的投影面积,是指以模具开闭方向垂直此方向的投射影子面积(实际也可说模具之面积)。
模具内平均压力加到投影面积就叫做锁模力,锁模力如果是模具的“投影面积×平均压力”大于“锁模力”时模具之公母模就会被推开。
锁模力=投影面积×模具内平均压力
一般而言,模具内平均压力值在20~45MPa,但对于一些薄壁,高精度的制品,模具内平均压力值高达60MPa。
模腔内平均压力值(单位kgf/cm2)
成品、原料一般制品难成型制品小型且精密的成品
PE、PP、PS、ABS300400600
PVC、PC、POM、AS400500800
B、射出量
一次射出之最大重量,一般都是以多少克来表示。
C、可塑化能力
单位时间内能够塑化多少量的树脂,一般都是以多少克来表示。
(以PS树脂为标准)
D、所谓开模行程
就是指成型机的移动板向后退到底时,移动板与固定板之间的距离.模具厚度只能在开模行程之内侧才能安装进出。
锁模装置一般地说,可分为直压式以及曲轴式两种。
五、模具
所谓模具(Mold)是指,为了将材料树脂做成某种形状,而用来承接射出注入树脂的金属制模型。
模具主要的结构部件有模架、模腔、流道。
六、成形品
成形品是由流入融化树脂的浇口、导入模槽的流道与产品部份所构成。
由于一次的成形作业只能作出一个产品,因此效率不高。
若能利用流道连结数个模槽,就可同时成形数个产品。
此时,当各模槽的流道长度不同时,就无法同时填充树脂,而且大部分的模槽尺寸、外观、物性皆不同,因此通常都会将流道设计成相同长度。
七、成形工艺
1成型条件
以PS原料及成型的范例,射出成型的原则为“熔融”、“注射”、“冷却”等三个阶段。
1.1“熔融”的过程
1.1.1料管温度
料管的温度,每一区须设定在多少温度是一般的常识(区分为料管灌嘴,前部、中部、后部)。
成型条件中比较重要的是,螺杆前端停滞原料的温度,成型操作中直接测定是比较困难且无法执行,所以以料管前端的温度当作材料之温度,料管之温度由前端开始设定,如果前端分成2部份时把它当作同样的温度。
材料之温度,首先参考制造商提供的资料以及模具实际情况来决定,这样先决定料管前端之温度,然后再来设定后部之温度。
后部的温度如果太高的话,成型材料立即软化在螺杆上后面的原料就无法被加进去,所以后部须比前部降低20℃之温度。
灌嘴的温度设定,原则上灌嘴的温度应与料管前端的温度一样不可下降,但是如果不下降一点的话,材料会从灌嘴处流漏出来,所以灌嘴的温度比料管前端温度降低10℃。
1.1.2螺杆的回转速度
成型材料是以螺杆回转来使其熔解,回转的速度太快时因磨擦过多产生过热现象,回转速度太慢时拉长—循环成型的时间因而使成本提高,基本上以不产生过热现象转速快一点来设定。
也不要设定太快。
1.1.3螺杆的背压
为了防止螺杆快速的后退,必须给螺杆有个压力,螺杆的背压太低时,因成型材料熔融时,产生的气体会使螺杆后退,那么熔融的成型材料量就不稳定,如果螺杆的背压太高时,螺杆后退的速度慢,因而使一个循环的时间也增长,背压会使材料的混合达到良好之状态,承受背压的螺杆转速如果快一点,会使材料之混合更好,但是回转速不能太快,背压也不能太高,否则螺杆回转太快了,会因磨擦过剧而产生过热现象。
螺杆背压的多少是以压力表的度数来表示。
1.2射出的过程
1.2.1射出量
是以螺杆后退到所定位置来决定射出量,即指成型材料充填到模具内材料的重量,实际上当螺杆后退到一定的位置后仍然会继续向后退一点,就像螺杆向前进到某一位置后也无法完全切断不让材料继续射出一样,这种虽然到达所定位置应切断停止,却无法切断停止而继续动作的位置,我们叫做垫料。
成型品的体积,是垫料量加上螺杆后退到所定位置来决定。
通常垫料量大概为5~10mm程度,例如实际料量需60mm时,应设定为65~70mm,因为垫料量为5~10mm。
1.2.2射出速度
射出速度是由螺杆前进的速度来决定,螺杆前进速度是指根据机台上已设定的程序,使螺杆由一个位置换到另一个位置,开始时射出速度等于螺杆前进速度,也就是以射出速度来称呼,成型的原则是,材料尚未冷却下来前趁早把材料射出去,所以射出速度应愈早愈快愈好,但是因为模具的不同也有无法趁早快速射出的情况,例如射出速度太快时,由闸门射出材料会造成喷痕的不良现象。
1.2.3射出压(一次压)
射出压就是把成型材料在瞬间内充填到模具腔内的压力,在许多成型条件中模具的压力变化是属于重要的一个。
在这里我们说的射出压即为螺杆向前推的油压压力。
对射出成型机来说,射出压与射出速度是有互相关联的,也就是说射出压力不高时,射出速度也无法达到快速的情况。
新作的模具第一次试模时,应以中压中速为益,这是为了避免不小心因射出压太高而使模具损坏。
模具内压力一般为400Kgf/cm2,压力太高除了会产生毛边之外也会使模具受到损害,所以切记压力不可调得太高,但是压力太低了材料无法在模具各角落都充填得到。
1.2.4模具温度
模具温度因模具水路位置不同会有所不同,
模具温度的设定的程序,开始把模具温度控制器的水温设定,然后母模与公模分别使用模具温度控制器,水温之温度设定开始时与模具温度一样,母模及公模开始时一样温度。
模具温度高的时候,成型品冷却慢,但成型材料流动性较好但会使循环时间长,所以模具温度不要太高。
1.3保压的工程
1.3.1保压切换(二次压切换)
为使成型材料于模具内完全地充填,成型机必须于瞬间内给予射出压力,然后保压维持一段时间这样的过程叫做射出成型保压切换过程。
如果射出压不变地保持一段时间,这样会在“入水”附近承受有害的压力以至会有变形及破裂情形发生,也就是射出压力太高。
但是射出压力不高,材料又无法在模具各处充填完全,像这种状况就必须想个办法来解决。
我们以保压切换位置来说明,何时射出压(一次压)转换成保压(二次压),保压切换是设定螺杆前进位置的基本,当螺杆后退到所设定之位置,其与保压切换位置间距即为螺杆前进量,也就是射出量,射出量如果不够的话,射出压是不会上升,当一次压与二次压在转换时,想要求螺杆前进在某预定的位置立即停止将办不到,因为螺杆会继续前进一点,保压切换位置就是一次压完结之后切换掉使螺杆停止,但是螺杆仍然继续走的位置。
二次压完了之后,螺杆位置在垫料的位置上,保压切换位置比垫料大一点,通常比5mm大一点。
1.3.2保压(二次压)
在这里保压首先以射出压之1/2来调整,然后观察产品,再调高直到射出压之80%程度为止。
有的成型机,可以用程序来调整,保压随着时间的延长而渐减,开始时一样的一次压压力,太高时闸门周围因不合理的压力影响会变形以及破裂现象发生,但是压力太低成型品的尺寸每次变化相当大,或者欠肉或者会胶线等成型不良的情形发生。
1.3.3保压时间
保压的原则是,维持成型材料在模具冷却到无法再流动为止,但因闸门有封堵的作用,所以如果闸门冷却凝固后,保压的效果就无作用,维持保压的时间如果太短,压力就放掉,这样保压的效果就会消失,成品会有欠肉缩水等不良情况发生。
1.4冷却的过程
1.4.1冷却时间
冷却时间是指保压时间完了之后到模具打开为止所设定的时间,成型材料在模具内冷却,然后由模具取出必须不变形而且坚固才行,冷却时间如果设定太长会使成型的循环时间变长。
模具的温度低会使冷却时间缩短,如果冷却时间太短了会使模具内取出的成型品变形。
但是实际成型时,在冷却的这段时间内,也正在为下次成型做可塑化过程,也就是螺杆一面回转一面往后退到所设定的位置,这段时间的长短,应可包含在冷却时间内,如果可塑化的时间比冷却时间长的话,成型的冷却时间就会浪费,这时为了要避免此浪费,可以把螺杆之回转以及螺杆的背压调整,也就是回转数提高或者降低背压这样可以缩短可塑化的时间。
冷却时间是成型循环时间中最长的时间,如果能把冷却时间缩短可以降低成本费用。
1.4.2成型循环(CYCLETIME)
成型循环是一个成品生产出来到另外一个成品生产出来的时间,在成型机上可以用“定时”来设定为多少时间,在成型如果安全门打开的时间过长,比所定的循环时间还长时,警报器会叫起来,如果安全门打开的时间很短,但是成型循环所定之时间还未到达,下次成型动作也无法开始,为了使产品的尺寸不会有变化起见,每次成型循环(CYCLE)之时间要一定。
如果依照一般原则,充填时间应该较短较好,充填的时间是可以用射出速度及射出压来调整,为了使模具各个位置都能充分填满材料,射出压高一点比较好而且也有必要,但是射出压应立即换成保压,为的是使闸门附近不会承受到不必要压力。
射出压是以成型机的射出压及保压切换位置以及射出速度来调整,保压是以成型机的保压以及保压时间来调整,一般地,保压大概是射出压的1/2程度,成型机所说的保压,实际也是模具内压力会渐渐的下降,这是因为成型材料会渐渐地冷却下来变坚固而引起的结果。
1.5成型条件的平衡
因成型条件操作有时会有满足这个条件,但无法满足那个条件,所以实际成型时,成型条件的平衡相当重要。
就以PS在成型时,会有毛边,欠肉,会胶,不好脱模的例子来说明,射出压(一次压)太低时,虽然易于脱模不易产生毛边,但是产生欠肉及会胶的状况,反过来说,射出压(一次压)太高时,虽然欠肉,会胶不易发生,但毛边易发生,脱模困难。
像这样达到这个要求,相对地就无法达到别个要求,如果仅以射出压的调高或调低来解决,会有困难的。
实际的成型条件是料管之温度调低、模具温度调高、射出速度要快、射出压(一次压)要低、保压(二次压)要高、保压时间要长,以上述原则实际来试试看,试后再以样品来参考,调整不好再调,调到整个条件都平衡才来定成型条件。
2.不良现象的观察以及原因
如何有把握地观察到不良现象?
首先观察其外观是否与标准一致?
不良品首先多由外观显现出来,如果外观没有问题,再检查尺寸,外观与尺寸都没有问题时,再以强度来确认看看。
在成型现场作外观检查时,须以标准样本以及限度样本比照方式来判断。
以尺寸不良的例子来说明一般不良的原因,有下列3个因素(其他不良项目也可以此方式来考虑)。
2.1.1成型材料的不稳定
昨天没有发生不良,但今天却发生不良,这种状况以成型材料的不稳定引起之成份较大,所以每批的成型材料有变化时,一定要先调整成型品的成型条件。
2.1.2模具的精确度大低(模具的误差)
主要是,因工作的精确度不好引起。
有些模具第一次开始生产时就有毛边,所以新的模具一定要在量产前,就要把所有尺寸检查完成不可。
其次是,成型收缩率的设定不对。
新的模具、新的成型机、或者新的材料在生产时,一定要连续生产到一定的数目,然后量尺寸,例如,生产100个,把成品尺寸标出来,当其中心值与设计数值不一样时,可能是成型收缩率设定不对,成型收缩率,会因成型材料、成型机、模具、成型品的形状、成型条件而有不一样。
使用时精确度不好。
模具静止时,检查结果精确度很高,但是成型时,因压力及温度的变化,影响模具的结构因而降低其精确度。
这是因为成型机之动作而引起成型之不良,所以在模具设计的阶段就要将模具的目标,设定在高精密及高刚性上,此点很重要。
磨损及破损之情形发生时。
如有毛边产生时,应立即送去修理,另外在闸门地方因磨耗而使得材料之流动状况有变动,也会使尺寸产生变化,所以模具须每日检查及定期检查。
2.1.3成型条件的变化(成型的变化)
成型条件,因成型机的不同而会有异,成型条件是指温度、压力、时间、速度、位置等,虽然成型机表上刻度定在同样之位置,实际的成型条件也会不一样,不会一样的原因也有外在因素。
成型现场的室温如果能控制一定,与对成型不良的解决非常有效果,针对尺寸的准确,要特别注意成型压力、模具温度及室温,室温应保持一定,而且每一成型循环时间要严格遵守,如能确实做到则不良情形会降低。
2.2不良再发生的防止
成型不良原则上非做到“0”的情况是不可能,切记一点“不良无法避免的想法”,是不可以有的,为防止不良之再发生,一个一个不良的地方应确实的改正,有时良品与不良品都无法确定的情形下就生产,然后再来检查好的与不好的,不良原因不把它完全排除掉,所生产的货品如有不良品混入,这样一定会产生问题。
八、塑胶制品的常见缺陷
色差、杂质、缩瘪、缺料、烧焦、银纹、流痕、熔接痕、顶白、拉裂、毛刺、划伤、油污、变形
缺陷现象可能成因:
色差:
制品的颜色与色板不符
1.原料色母配比不符。
2.成形温度过高,色母分解
3.塑胶老化变色。
杂质:
制品表面出现可见的不规则的黑点
1.原料混有杂质
2.设备脏污
缺料:
制品结构不完整,残缺不全
1.原料流动性较差
2.注射压力太小
3.胶料熔融温度或模具温度低,填充性差,易发生在筋部。
烧焦:
制品表面烧糊发黑现象
1.模具排气性能差,困气。
2.温度设定偏高,或注射压力、速度偏高
银纹:
制品表面出现的白色放射状条纹
1.原料含水量太高,熔融塑化时水分等小分子在塑胶表面蒸发的结果
熔接痕:
两股熔融胶料在模腔内融合时产生的条纹结合线
1.模具温度分布不均匀,熔胶前沿温度差别大
2.模具的流道胶口或模腔设计不合理
3.工艺设定不合理
顶白:
顶杆背面出现的白印
1.顶杆的长度位置不当,顶出时受力不均匀。
2.制品尺寸偏大脱模困难
缩瘪:
制品表面凹陷
1.制品壁厚设计不合理
2.保压压力或时间不够