重介质选煤 专题辅导报告.docx
《重介质选煤 专题辅导报告.docx》由会员分享,可在线阅读,更多相关《重介质选煤 专题辅导报告.docx(8页珍藏版)》请在冰豆网上搜索。
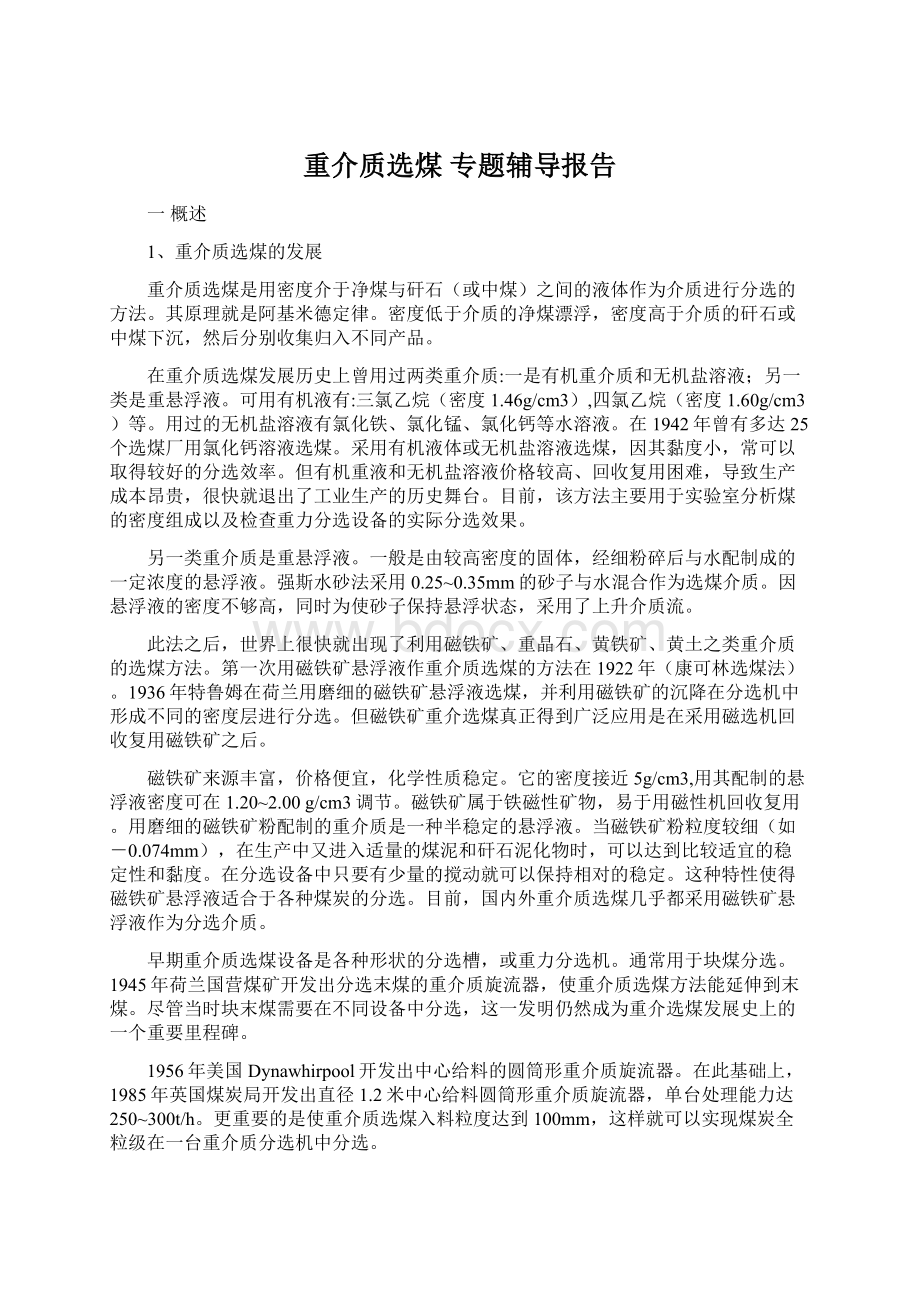
重介质选煤专题辅导报告
一概述
1、重介质选煤的发展
重介质选煤是用密度介于净煤与矸石(或中煤)之间的液体作为介质进行分选的方法。
其原理就是阿基米德定律。
密度低于介质的净煤漂浮,密度高于介质的矸石或中煤下沉,然后分别收集归入不同产品。
在重介质选煤发展历史上曾用过两类重介质:
一是有机重介质和无机盐溶液;另一类是重悬浮液。
可用有机液有:
三氯乙烷(密度1.46g/cm3),四氯乙烷(密度1.60g/cm3)等。
用过的无机盐溶液有氯化铁、氯化锰、氯化钙等水溶液。
在1942年曾有多达25个选煤厂用氯化钙溶液选煤。
采用有机液体或无机盐溶液选煤,因其黏度小,常可以取得较好的分选效率。
但有机重液和无机盐溶液价格较高、回收复用困难,导致生产成本昂贵,很快就退出了工业生产的历史舞台。
目前,该方法主要用于实验室分析煤的密度组成以及检查重力分选设备的实际分选效果。
另一类重介质是重悬浮液。
一般是由较高密度的固体,经细粉碎后与水配制成的一定浓度的悬浮液。
强斯水砂法采用0.25~0.35mm的砂子与水混合作为选煤介质。
因悬浮液的密度不够高,同时为使砂子保持悬浮状态,采用了上升介质流。
此法之后,世界上很快就出现了利用磁铁矿、重晶石、黄铁矿、黄土之类重介质的选煤方法。
第一次用磁铁矿悬浮液作重介质选煤的方法在1922年(康可林选煤法)。
1936年特鲁姆在荷兰用磨细的磁铁矿悬浮液选煤,并利用磁铁矿的沉降在分选机中形成不同的密度层进行分选。
但磁铁矿重介选煤真正得到广泛应用是在采用磁选机回收复用磁铁矿之后。
磁铁矿来源丰富,价格便宜,化学性质稳定。
它的密度接近5g/cm3,用其配制的悬浮液密度可在1.20~2.00g/cm3调节。
磁铁矿属于铁磁性矿物,易于用磁性机回收复用。
用磨细的磁铁矿粉配制的重介质是一种半稳定的悬浮液。
当磁铁矿粉粒度较细(如-0.074mm),在生产中又进入适量的煤泥和矸石泥化物时,可以达到比较适宜的稳定性和黏度。
在分选设备中只要有少量的搅动就可以保持相对的稳定。
这种特性使得磁铁矿悬浮液适合于各种煤炭的分选。
目前,国内外重介质选煤几乎都采用磁铁矿悬浮液作为分选介质。
早期重介质选煤设备是各种形状的分选槽,或重力分选机。
通常用于块煤分选。
1945年荷兰国营煤矿开发出分选末煤的重介质旋流器,使重介质选煤方法能延伸到末煤。
尽管当时块末煤需要在不同设备中分选,这一发明仍然成为重介选煤发展史上的一个重要里程碑。
1956年美国Dynawhirpool开发出中心给料的圆筒形重介质旋流器。
在此基础上,1985年英国煤炭局开发出直径1.2米中心给料圆筒形重介质旋流器,单台处理能力达250~300t/h。
更重要的是使重介质选煤入料粒度达到100mm,这样就可以实现煤炭全粒级在一台重介质分选机中分选。
1967年在原苏联出现了三产品重介旋流器,它利用第一段旋流器余压将其重产物送入第二段进行再次分选。
因为重介质悬浮液经历了一段浓缩,提高了密度,所以在第二段旋流器能选出较纯的矸石。
这样可以用一套重介质系统,单一密度的合格介质分选出三个产品。
至此,使传统的两粒级双密度复杂的重介分选工艺简化为单密度全粒级重介分选工艺,这就大大简化了重介分选工艺流程。
我国从20世纪50年代中期开始试验重介质选煤方法。
起初采用黄土和高炉灰之类作为加重质,成效不大。
到50年代末60年代初开始研究采用磁铁矿粉作为加重质选煤。
到1986年重介质选煤占各种选煤方法比例已达到23%左右。
1986年中国矿业大学与重庆南桐矿务局合作,研究使用中心给料的圆筒重介质旋流器脱硫,1990年通过了原煤炭工业部的鉴定。
1991年中国矿业大学与重庆中梁山矿务局合作,在煤炭部支持下,对中梁山选煤厂进行技术改造,1993年建成“难选高硫煤脱硫降灰示范工程”,在国内首次采用了“跳汰初选—中心给料圆筒形重介质旋流器精选—煤泥旋流微泡浮选柱分选”的联合脱硫新工艺。
1995年通过了煤炭工业部组织的工业验收和技术鉴定,开始了中心(无压)给料圆筒形重介质旋流器在我国选煤生产中的应用。
20世纪90年代是我国重介质选煤技术和入选量快速发展的年代,其中发展最快的是重介质旋流器选煤技术,特别是中心给料圆筒形重介质旋流器以及三产品重介质旋流器的大型化与推广应用。
与此同时,重介质选煤的辅助设备和耐磨材料的生产技术也取得了长足进步,为我国重介质选煤技术的大规模工业化推广提供了成熟的外部条件。
2、重介质选煤的实质和特点
如前所述,重介质选煤是在密度介于净煤和矸石(或中煤)的重介质悬浮液中按照阿基米德原理进行分选的方法。
除了分选设备以外,介质的制备和回收复用以及介质的稳定性是生产过程的关键。
首先要配置好具有要求密度的重介质,然后将准备好的物料以一定的速率与重介质一起或分别给入分选机,按(接近介质的)密度分选出轻产物和重产物,用在筛上喷水洗涤的方法脱除和回收产品带出的介质,常用磁选机回收并送回介质循环系统复用。
在介质循环系统中配备有重介质特性测控系统。
它能够以不同的方式保持循环重介质特性的相对稳定。
选煤所用的重介质通常是由微细高密度固体与水混合而成的非均相重悬浮液。
因此,在分选过程中,煤粒在其中运动时,既受到分散介质(如水)的阻力,还受到分散相(如磁铁矿粉)颗粒的阻力。
然而,实验证明,与在真溶液中相似,对于粒度粗且与重介质密度差别大的颗粒,在悬浮液中运动(上浮或下沉)的阻力主要是惯性阻力;而粒度小以及密度与重介质密度差别小的颗粒,在悬浮液中运动速度小,其运动阻力主要是粘性阻力。
同时实验还表明,当煤粒粒度与加重质粒度接近时,悬浮液中加重质颗粒对分选煤粒的机械作用变得很明显,这对细颗粒运动(分选作用)有重要影响。
为说明重介选煤过程实质,目前普遍被接受的、也比较符合实际的理论认为,当煤粒粒度为加重质粒度的数十倍以上时,悬浮液可以看成是密度为两相平均密度的均相液体,对在其中运动的煤粒的阻力和真溶液一样;但当两者粒度接近时,则煤粒的运动应被看作是在干扰沉降条件下的运动。
因此,在离心力场中,能被分选的煤粒直径将会受到干扰沉降等沉比的限制。
一般认为,能被有效分选的粒度下限只能达到大约为加重质最大粒度的5倍以上。
上述理论在一般情况下只适用于固液两相悬浮液中分散固相的体积浓度不超过30%的条件。
若超过这个极限,即便对粒度较大的块煤,悬浮液也不能看作是均相液体。
比如,我们有时发现在高密度分选的重力分选机中,在重介质表面会有较大的矸石漂浮不下沉的现象。
因为在使用磁性物含量不够高的磁铁矿粉配制高浓度的重介质时,固体体积浓度可能会超过30%,加上系统中积存较多的煤泥,悬浮液的性质就有别于均匀液体了。
此外,一般选煤用的重介质属于不稳定的固液两相粗分散体系,静止时会发生沉降分层。
为保持重介质悬浮液密度相对稳定,使分选能够正常进行,分选机内需要有一定的扰动,或是机械的(如轻产物或重产物的排放装置),或循环介质流(上升流或水平流),都可达到此目的。
但所有这些扰动对各种密度和粒度的颗粒都会产生不同的影响,尤其是对细粒的密度接近重悬浮液的颗粒。
采用磨得较细的磁铁矿粉或在系统内积存适量的煤泥,会有助于重介质悬浮液的相对稳定,并减轻扰动的影响。
3、重介质选煤的优点和应用范围
1)重介质选煤分选效率高
重介质选煤的分选精度常用可能偏差E值衡量,一般来说它的数值越小,与其他选煤方法比较分选精度越高。
实验表明,重介质分选是精度最高,即E值最小的分选方法,因此可以应用于难选和极难选煤的分选。
分选精度高就意味着在相同质量条件下精煤产率高。
重介质选煤缺点是在选煤系统中增加了一个介质系统。
由于增添了一些生产过程的控制变量以及介质损失和设备磨损的问题,但这些问题现已得到合理的解决。
首先,重介质选煤可以用于分选各种可选性和不同粒度的原煤。
我国三产品旋流器第一段最大直径已达到1.4米,单台处理500吨/时,入料上限可达80~100毫米。
用重介质分选排矸是另一种选择。
对大含矸量的原煤,可选择重介分选机代替劳动强度较大的手选。
有些动力煤选去矸石后就能达到商品煤的质量要求,亦可用重介选排矸。
入选粒度下限取决于商品煤质量要求,但原煤干法筛分时粒度下限一般不低于6毫米。
这种方法的优点是工艺简单,煤泥水处理量小,商品煤水分低。
重介质分选机可采用静力分选机,也可采用大直径两产品重介质旋流器。
重介质选煤普遍用于跳汰选煤厂的技术改造。
有用于跳汰精煤再选,也有用于跳汰中煤再选。
前者重介质入选量大,多半用于难选煤;后者重介质入选量小,多对中等可选性煤采用。
上述情况现在一般都采用重介质旋流器。
而且上述两种工艺方案与原煤重介质分选相比较,不仅重介系统处理量大为减少,而且因大部分矸石已由跳汰排出,重介旋流器磨损减轻,使用寿命倍增。
这种改造投资较少,工期短,甚至选煤厂可以不停产改造。
重介质选煤用于高硫煤脱硫是最有效的。
要尽可能脱除煤中的黄铁矿硫,首先要把煤破碎到一定粒度,以便解离出单体黄铁矿,破碎粒度视黄铁矿在煤中的分布状态而定。
一般要破碎到-13毫米或-6毫米,必要时可能更细。
然后按低密度分选,选出含硫较低的精煤。
因为对于许多以无机硫为主的煤,含硫量随密度升高。
一般情况下密度大于1.4g/cm3(或1.5g/cm3)以上时,硫分虽密度升高很快,所以分选密度必须小于1.4g/cm3(或1.5g/cm3),此时煤的可选性都很难。
对这种粉煤含量大又极难选的煤,高分选精度的重介质旋流器可以发挥独特的作用。
而且希望旋流器达到有效分选粒度下限尽可能细,如0.25(0.15)毫米,以减轻浮选对煤泥脱硫的负担。
因此,高硫煤脱硫宜采用中小直径重介质旋流器。
重庆中梁山矿务局选煤厂和天府矿务局磨心坡选煤厂都是成功的例子。
这两个选煤厂均采用φ400mm无压给料圆筒形重介质旋流器脱硫,分选粒度下限可达到0.15~0.10mm,不仅可以使浮选入料含硫量基本达标,灰分也比原生煤泥降低5%,并使入浮煤泥量比原跳汰流程减少约1/3.
生产超净煤也是重介质旋流器特长。
和高硫煤分选相仿,要生产出灰分小于2.0%(或3.0%)的精煤,一定程度的粉碎和低密度分选(如<1.4g/cm3甚至<1.3g/cm3)是必须的。
所以煤变得更难选,分选精度要求更高(如E<0.02),分选密度稳定性也要求很高,而此类任务非重介质旋流器莫属。
当然,旋流器设备和生产工艺需要相应的精心设计和严格管理。
宁夏太西选煤厂的重介旋流器超低灰煤生产线就是一个成功的例子。
稳定可靠的高精确度的重介质选煤就意味着更高的精煤质量、更高的精煤产率和更高的经济效益。
如中梁山选煤厂、磨心坡选煤厂、老屋基选煤厂、南桐选煤厂、淮南望风岗选煤厂,这些选煤厂都是采用跳汰加重介或跳汰改为全重介流程。
跳汰—重介或全重介流程的几座炼焦煤选煤厂,如:
吕家坨选煤厂、大武口选煤厂、范各庄选煤厂、兴隆庄选煤厂、西曲选煤厂、安太堡选煤厂以及其后许多国内设计完全国产化选煤厂,标志着我国重介选煤技术已经成熟。
2)重介选煤分选原理明显,有利于实现自动化
与跳汰选煤比较,重介质选煤的分选原理要清楚的多。
目前,重介质悬浮液密度、液位、粘度、磁性物含量都已实现自动控制。
3)重介质选煤分选密度调节的范围宽
跳汰分选密度范围一般在1.5~1.9g/cm3之间,对少数煤种可达1.4g/cm3的分选密度,换句话说,跳汰机由于种种原因,对多数煤难以排出纯矸石,当精煤灰分要求较低时,跳汰机分选效率会迅速降低,且精煤质量不稳。
但对重介选煤,分选密度在1.3~2.2g/cm3范围内,都能高效率分选。
换句话说就是能选出很纯的矸石和灰分很低的精煤。
分选密度通过密度自动调控装置容易调整,精确度和稳定性可控制在±(0.05~0.01)g/cm3以内,这是其它选煤方法不可比拟的。
二重介质
重介质悬浮液是由颗粒状的固体(加重质)和水混配而成。
固体颗粒在1~500um之间,属于粗分散悬浮液,是一个不稳定的体系,静止时易发生沉降分层,使分选机内部各处密度不同,导致实际分选密度与重悬浮液密度有所差异。
选择加重质主要考虑:
合适的密度、机械强度(不易粉碎和