炼铁机械装料器和无料钟.docx
《炼铁机械装料器和无料钟.docx》由会员分享,可在线阅读,更多相关《炼铁机械装料器和无料钟.docx(9页珍藏版)》请在冰豆网上搜索。
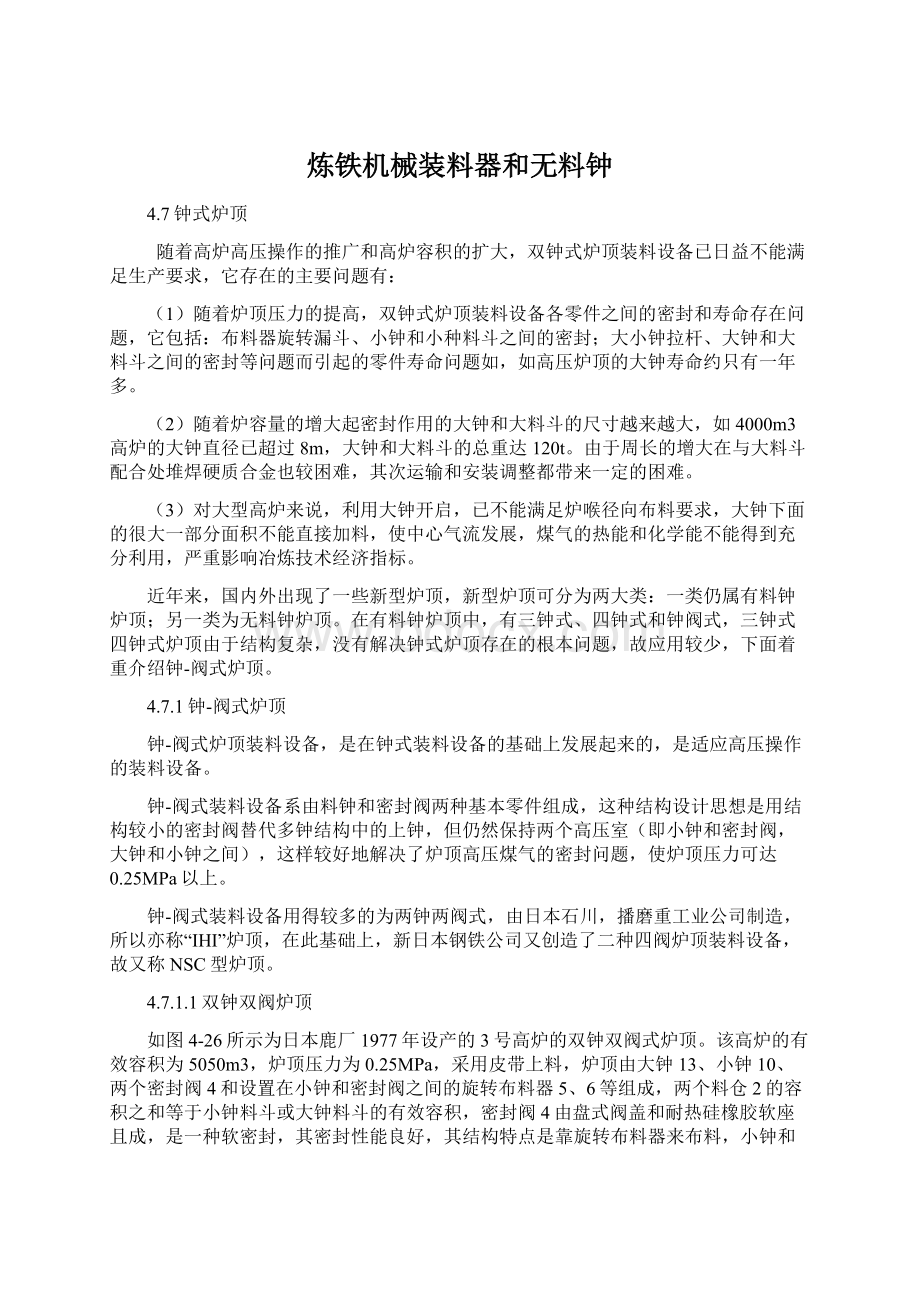
炼铁机械装料器和无料钟
4.7钟式炉顶
随着高炉高压操作的推广和高炉容积的扩大,双钟式炉顶装料设备已日益不能满足生产要求,它存在的主要问题有:
(1)随着炉顶压力的提高,双钟式炉顶装料设备各零件之间的密封和寿命存在问题,它包括:
布料器旋转漏斗、小钟和小种料斗之间的密封;大小钟拉杆、大钟和大料斗之间的密封等问题而引起的零件寿命问题如,如高压炉顶的大钟寿命约只有一年多。
(2)随着炉容量的增大起密封作用的大钟和大料斗的尺寸越来越大,如4000m3高炉的大钟直径已超过8m,大钟和大料斗的总重达120t。
由于周长的增大在与大料斗配合处堆焊硬质合金也较困难,其次运输和安装调整都带来一定的困难。
(3)对大型高炉来说,利用大钟开启,已不能满足炉喉径向布料要求,大钟下面的很大一部分面积不能直接加料,使中心气流发展,煤气的热能和化学能不能得到充分利用,严重影响冶炼技术经济指标。
近年来,国内外出现了一些新型炉顶,新型炉顶可分为两大类:
一类仍属有料钟炉顶;另一类为无料钟炉顶。
在有料钟炉顶中,有三钟式、四钟式和钟阀式,三钟式四钟式炉顶由于结构复杂,没有解决钟式炉顶存在的根本问题,故应用较少,下面着重介绍钟-阀式炉顶。
4.7.1钟-阀式炉顶
钟-阀式炉顶装料设备,是在钟式装料设备的基础上发展起来的,是适应高压操作的装料设备。
钟-阀式装料设备系由料钟和密封阀两种基本零件组成,这种结构设计思想是用结构较小的密封阀替代多钟结构中的上钟,但仍然保持两个高压室(即小钟和密封阀,大钟和小钟之间),这样较好地解决了炉顶高压煤气的密封问题,使炉顶压力可达0.25MPa以上。
钟-阀式装料设备用得较多的为两钟两阀式,由日本石川,播磨重工业公司制造,所以亦称“IHI”炉顶,在此基础上,新日本钢铁公司又创造了二种四阀炉顶装料设备,故又称NSC型炉顶。
4.7.1.1双钟双阀炉顶
如图4-26所示为日本鹿厂1977年设产的3号高炉的双钟双阀式炉顶。
该高炉的有效容积为5050m3,炉顶压力为0.25MPa,采用皮带上料,炉顶由大钟13、小钟10、两个密封阀4和设置在小钟和密封阀之间的旋转布料器5、6等组成,两个料仓2的容积之和等于小钟料斗或大钟料斗的有效容积,密封阀4由盘式阀盖和耐热硅橡胶软座且成,是一种软密封,其密封性能良好,其结构特点是靠旋转布料器来布料,小钟和密封阀、大钟和小钟之间形成两个均压室,靠小钟和密封阀来密封,大钟均压室与炉喉连通,大钟处在等压气体下工作,不起密封作用,其寿命可达到一代炉龄。
装料时,卸料流槽1将料同时分装到两个料仓2内。
往小钟料斗装料前,先起动布料器6,接着先打开两个密封阀,再打开两个装在料仓底部、密封阀上面的闸板阀3,以使密封阀在打开过程中不受炉料冲击。
这时,由于布料器的旋转,使料均匀地分布在小钟料斗内(也可进行定点布料),打开小钟后,由于原料下落过程的扩散作用,大料斗内的料堆尖趋向平缓。
图4—27是该炉顶的布料器驱动装置。
电动机1通过减速箱2和小齿轮3,使大齿轮4旋转。
大齿轮4通过定心套筒轴与小钟漏斗内的布料器旋转拉杆7连成一体,因此,带动布料器旋转。
通常,布料器以均匀布料的方式工作,转速为12~14r/min。
在大齿轮上面有三个锥形压辊,下面有三个锥形托,侧面还有六个径向挡辊,以保证齿轮的正确啮合。
大小钟以及料仓的密封阀、闸板阀开闭均采用油压传动。
双钟双阀式炉顶的主要缺点是,布料器旋转漏斗的工作环境差,支承辊和六个径向挡辊的均压室内工作,灰尘多、磨损快、检修不便。
其传动系统虽然放在外面,但要通过较长的套筒轴传进去,刚性较差,并且增加了套筒轴的密封问题,为了克服这些缺点,可以把布料器放到外面,于是出现了双钟四阀工炉顶。
4.7.1.2双钟四阀炉顶
图4-28所示为双钟四阀炉顶的结构筒图。
由于把布料器1移至贮料仓上面,在大气环境下工作,可以不设密封装置,减少维修工作量,这种炉顶有四个漏料孔,并装设四个闸门和四个密封阀,在密封阀上面有一个贮料仓。
当皮带机往炉顶装料时,布料器不仅能通过边卸料边旋转的偏嘴把料均匀地分布在贮料内,而且也可采用固定角度进行定点布料,由于四股料流是对称分布的,尽管在小料斗内要形成四个堆尖,但经过小钟和大钟装料时的扩散作用,可以使圆周方向的布料基本上分布均匀。
这种炉顶布料均匀性不如双钟双阀炉顶,上于贮料仓下面是四个放料口,故对定点下偏料来说,定点位置局限性较大,并且炉顶高度和设备重量比双钟双阀炉顶更大,当然投资也更高。
为了延长上钟及料斗的寿命,在小钟上表面和小钟漏斗的内表面都设有可以更换的板保护(大钟和大料斗也是如此)。
在小钟和小料斗接触处,都采用了软
硬封相结合的结构(图4-29),小钟关闭时,小钟金属表面先和硅橡胶相接触,当硅橡胶被压缩后,再和料斗接触环的硬质合金加工面接触,由衅4-26和图4-28还可看出,小钟和小钟料斗都分成两段,当接触环吹损后,可以单独更换。
图4-30是密封阀传动结构示意图,它是通过油缸推动齿条,然后带动齿轮使轴旋转,在轴上固定着操纵密封阀盖开闭的连杆。
4.7.1.3密封阀结构及设计
A密封阀的结构
目前钟-阀式炉顶的密封阀基本上都采用如图4-29中的密封结构,无料钟炉顶的密封阀也采用这种结构,图4-31是密封阀部分的详细结构,这种密封结构是在原有结构的基础上改进的,其阀盖6由操纵密封盖开闭的连杆带动(图4-29),环形气囊2具有足够的断面积,可以使排气口3形成连续的环状气幕,由原来的单刃改为双金属刃4,并固定在阀体1上,耐热橡胶圈5固定在阀盖6上,当阀盖处于关闭位置时,冷却气不认排气口排出,只有当阀盖打开或关回的短时间进行排气,其目的是为了清扫橡胶表面的灰尘,以免尘粒附在刃口和橡胶表面之间,影响密封性。
这种结构的耐热橡胶可以在250°~300℃的环境中长期工作,可以不用连续喷气冷却,然而,对于炉喉温度较高的高炉,对耐热橡胶进行连续冷却是必要的,最好在橡胶座周围的金属体上,开有冷却水环槽,使橡胶在和金属座接触的三个面温度较低,再加上橡胶表面有冷却气冷却,就可以显著降低耐热橡胶的工作温度,从而提高其使用寿命。
在上述关系中,当单位压力q值大于许多比压[q]时,橡胶圈使用寿命将会降低或老化。
当密封比压qMF值大于单位压务q值时,说明保证密封所需要的单位压力大,而外部对密封面所施加的单位压力小,以致达不到两个接触面之间所需要的贴紧力。
目前,国内外某些高炉,为了进一步提高密封阀的寿命和密封效果,已采用在密封阀座上设置电加热装置,使阀座上处于无水状态,以降低尘粒在阀座上的粘结。
此外,为了控制橡胶密封阀受力后产生的允许变形,工作时,应使硅橡胶的压缩量限制在2~3mm之间,为此,在阀座上可增设一组可调的环型档圈,以防止压缩量的增加。
橡胶密封阀的允许变形和密封阀冷却,吹尘的氮气需用流量的计算,可以参阅有关资料。
4.7.1.4可调炉喉
在高炉大型化以后,大钟直径也相应增大,因此不论采用什么装料制度,只利用大钟径向布料都不能达到满意的效果,因为大钟下面很大面积不能直接加料,所以,炉内中心煤气流显著高于边缘,影响技术经济指标。
国内外近来在大型高炉上采用了可调炉喉挡料板或炉喉载截锥,以改变径向布料,后者由于结构复杂未在我国推广使用。
可调炉喉板结构和工作原理如图4-32所示,沿炉喉圆周有24块炉喉调节板1,它们通过板座2,转轴3,转臂4,上下拉杆5、7及调节螺母5,联接在一个环梁上,在环梁下面有三个油缸9驱动环梁升降,以使炉喉板摆动,达到改变炉喉直径的目的,指针10可显示炉喉板调节位置,此设备已在我国钟-阀式大型高炉使用。
4.7.2无料钟炉顶
钟-阀式炉顶比马基式炉顶有很多优点,但这种炉顶还未彻底消除大、小料钟,如对4000m3高炉,大钟及大料斗的合重已达120t,大钟直径达8m以上,这给制造、运输及维修带来很大困难。
1970年,卢森堡的威尔斯与波尔、乌尔斯公司共同创造了PW式无料钟炉顶装料设备,并于1972年在原西德汉堡四号高炉上投产之后,充分显示了其优越性,并很快在世界各国得到推广使用。
4.7.2.1无料钟炉顶的结构组成和基本参数的计算
A无料钟炉顶的结构组成
图4-33是并罐式无料钟炉顶总体结构示意图,它由可移动的受料漏半1、两个密封料仓4、叉形管11和中心管16、气密箱(包括溜槽传动装置)15和布料溜槽14等五部分组成,其余还包括监测系统(料面探测、温度显示、料仓测重、空满显示等),料仓均匀和放散系统及冷却系统等设备。
无料钟炉顶操作过程是,当某个料仓需装料时,受料漏斗先移到该料仓的上部,并使该料仓的放散阀打开,然后打开上密封阀,将第一车料装入料仓,关闭上密封阀和放散阀,并向料仓内充入均压煤气,以减少下密封阀的压力差,以同样顺序将第二车料装入同一个料仓,然后把第三、第四车料装入另一个密封料仓,一般是一个料仓装矿石,另一个料仓装焦炭,形成一个料批。
当炉内需装料时,提升探尺到最高位置(水平探尺退到原位),溜槽按布料
选择要求由等待点转动到起始点,打开卸料料仓的下密封阀,再打开调节某一开度的料流节流阀,原料按预定的卸料时间经过叉形管,中心喉管和溜槽向炉内布料,当料,仓卸空后由测力仪(电子称)发出信号,先关闭料流节流阀,再关闭下密封阀,然后打开放散阀,溜槽回到原等待位置。
当第一个料罐往炉内装料时,第二个料罐可以接受装料,两个料罐交替工作,使炉顶装料具有足够的能力。
在工作中要求联锁装置有:
探料尺提升到最高位置才允许溜槽启动,下密封阀没关闭,上密封阀不能打开,下密封阀没全部打开,料流调节阀不能打开,当料仓内有料时,不能打开该料仓的上密封阀,以免重复装料。
无料钟炉顶主要优点是:
(1)炉喉布料用一个重量轻、既或旋转又可摆动的溜槽来进行,能实现炉喉最合理的布料,操作灵活,调节手段多,能充分满足高炉布料和调剂的要求,因此,可提高产量,降低能耗。
(2)取消了庞大笨重的大钟、大料斗和旧式旋转布料器,比较彻底地解决了制造、运输、安装和维护更换等问题。
(3)炉顶用尺寸较小、密封性良好的两层密封阀代替原有料钟密封。
炉顶压力得进一步提高,且密封阀不受原料的磨损,寿命较长;阀和阀座的重量尺寸小,可以整体更换也可单独更换某个零件(如硅橡胶),检修比较方便。
(4)炉顶结构大为简化,炉顶设备重量减轻一半;同时炉顶上的吊装设备能力要求降低,炉顶总高度约降低三分之一,使整个炉顶设备总投资减少一半以上,无料钟与钟-阀式炉顶设备重量比较见表4-1。
B基本参数和结构要求
为了确保无料钟料顶有足够的装料能力和周向布料均匀,其设计时基本参数有,料罐容积、料流调节阀内径、中心喉管内径和布料器转速等。
a料罐料罐的有新途径容积一般取半批料的体积,即相当于两个料车的有较容积。
为防止炉料对罐内壁的磨损,其内部半有材质为高铬铸铁的衬板,两个料罐分别放在电子秤8上,其上设置有料罐空满的检测显示器,以及时发现卡料现象,由于两上料罐设有电子秤,所以不能与叉形漏斗11进行刚性连接,中间通过一段不锈钢做成的波纹管连接。
b料流调节阀和密封阀料流调节阀的作用有两上:
一是避免原料与下密封阀接触,以防止密封阀磨损;二是可调节阀的开度,以控制料流的速度与布料溜槽合理配合而达到各种形式布料的要求。
料流调节阀和下密封阀的内径越小,每次下料时间越长,当布料器转速一定的情况下可以增中炉喉的布料层数,因此有利于均匀布料,此外,密封阀的尺寸小有利于修理更换,特别对于耐热橡胶圈的制造,涉及到胎具有尺寸也希望小一些,但对小的密封阀容易卡料。
工作中料流阀阀板由于受到炉料经常摩擦和挤压,阀板应使用高强度合金铸钢材料。
为了提高整个阀体在阀箱中的刚性,阀板开启轴应将原先使用的悬臂曲拐型改成两侧支承的曲轴型,目前新设计的串罐无料钟的新型料闸,也使用了两侧支承的结构。
此外,为了提高料流调节阀的开启性能,还应提高其自动控制的能力。
c叉形管和中心喉管中心喉管是一段圆柱形短管,其上部通过叉形管与料罐连接。
中心喉管的内径应比节流阀放料口内径小一些(根据炉容量一般取600~800㎜),其下料能力应与下密封阀放料口的下料能力相等或小一些。
d旋转溜槽旋转溜槽的转速应能保证圆周均匀布料,转速太高对设备不利,一般来说,每次布料应有10层左右的料(环形布料时)或10圈左右的料(步进式同心圆布料时)。
图4-34是溜槽的一种结构,它是一个半圆形的槽体,由本体和衬板组成,本体一般用耐热合金钢铸件,能在600℃温度下正常工作,衬板表面堆焊高铬硬质合金,以提高内表面的抗磨能力。
为了提高溜槽的刚性和减少溜槽的倾翻力矩,可将溜槽的本体做成前小后大的锥形体,后部的壁厚也大一些,溜槽后部的侧壁设有导轨2和螺栓孔,以便与驱动臂固联在一起。
E布料层数的计算实例原料从放料口出来的速度可用下式计算(图4-35)
表4-2是以1445m3高炉为例的计算,焦炭和矿石的流动系数分别取0.6和1.0,料车容积为两车料(20m3),布料器转速为8r/min。
计算表明,当节流阀内径为0.8m,放流口为半圆形时,焦炭放料时间为88.5s,矿石放料时间为53s。
对于大型高炉,为了实现螺旋布料或同心圆布料,一般要求每次布料时间相等,由于各种原料流动系统不同,要做到每次布料时间相等,必须改变节流阀的开口度,如焦炭、天然矿或烧结厂、球团矿,下料时,闸门的开度应分别从大到小,但料仓内一般只装一种原料(烧结矿或焦炭,少量的杂矿和石灰石可以和烧结矿装在同一料仓内),所以在进行布料过程中,不必改变节流阀闸门的开口度,只需根据多次操作积累的数据或通过计算机处理,对下每种原料时确定一个合适的开口度。
中心喉管直径的大小也可用类似的方法确定,计算下料速度时,因为中心喉管是垂直的,因此,sina=sin90o=1,此外,中心喉管的原料从了节流阀下来,已具有一定速度,在中心喉管处又经过节流减速,因此实际速度比公式(4-4)算得的速度要大一些,为了使中心喉管及时将节流阀排出的不同原料顺利通过,在选用入系数时,应取焦炭的流动系数,本例中,节流阀的内径为800mm,中心喉管的内径为600mm,能满足下料需要。
根据生产实践,中心喉管的直径增大,要求布料溜槽加宽,使溜槽比较笨重,因此,只要不引起卡料,同时在保证生产要求的前提下,中心喉管直径尽理小一些。
下密封阀的内径和节流阀的内径差不多,上密封阀的内径可以和下密封相同或稍大一些,这样可以加快装料速度和缩短装料时间。
C无料钟炉顶的传动机构及计算
布料器的旋转溜槽应有绕高炉中心线的回转运动和在垂直平面内改变溜槽倾角的运动,根据布料要求,这两种运动可以同时进行,也可分别独立进行,实现上述运动的传动机构方案较多,图4-36是国外使用的无料钟炉顶布料器的立体简图(a)和传动系统简图(b)。
由图b可知,它由行星减速器和气密箱两大部件组成,布料器气密箱壳30支承在高炉炉壳31上,行星减速箱支承在气密箱的顶盖上,由于气密箱处于炉喉顶部,而箱内工作温度不应超过50℃,必须通冷却气体进行冷却,冷却气的压力比炉喉压力应大0.01~0.015Pa,以防炉内荒煤气进入气密箱内,冷却气由密封箱底板与气密箱侧壁之间的间隙D排入炉内,行星减速箱处于大气环境中工作,不必通冷却气体,只有齿轮7和10的两根同心轴伸入气密箱内,因此需要转轴密封。
溜槽传动系统的工作原理是,溜槽20的回转运动由一台双速主电机1经两个对齿轮2,3,5,6,7使固定的旋转圆筒9上的齿轮8转动,同时,固定在旋转圆筒下部的隔热屏风29也跟着一起转动,而溜槽通过耳轴18挂在旋转圆筒侧壁上,因此,溜槽旋转圆筒也一起转动,这时副电机不动,所以倾角不变。
当主电机1工作时,不仅使圆筒9和隔热屏风29转动,而且由齿轮4通过行星轮系带动轴п转动,轴п下端的齿轮10带动双联齿轮11和12转动,由于设计时使齿圈8和12旋转速度相同,所以小齿轮13,溜槽摆蜗轮箱C和屏风29具圈12之间相对运动,一起绕高炉中心线旋转,此时溜槽只作旋转,没有摆动。
当副电机24h工作时,主电机不工作时,中心齿轮a转动,此时溜槽只作摆动,而当主、副电机同时工作时,由于行星轮系差动作用,使大齿圈8和齿圈12之间产生相对差动,从而传动齿轮13与齿圈12之间产生相对运动,此时溜槽既作转动又作摆动。
图4-37是国内设计使用的一种无料钟炉顶布料器的传动系统,它与上述国外传动系统不同之处是:
(1)溜槽的摆动采用双边驱动,以增加传递扭矩,但需解决传动时,两边受力均衡问题。
(2)下部隔热屏风采用固定式,不再与圆筒一起旋转,它可以通水冷却(见图4-38中21),使炉喉的辐射热不易传入气密箱内,并减少冷却气的用量。
在图4-37的结构中,上部主电机通过锥齿轮Z1、Z2和齿轮Z7、Z8带动圆筒旋转,这样比原结构减少了一对齿轮,少了一对分箱面,使安装调整比较方便。
现以图4-37的传动系统为例进行有关计算
要实现
,
同步必须满足式(4-9)条件。
此外从结构看出,Z7,
和
两对齿轮中心距必须相等。
b溜槽倾角调整摆动速度当主电机不转,副电机开动,进行溜槽倾角调整时,其溜槽转动速度n16为:
正常工作时,溜槽倾角的最大调整范围是由0o~50o,常用范转为30o~50o,调整倾角可以在布料器不旋转时进行,也可以布料器旋转布料时同进行,当主副电机同时工作时,系杆的转整可以根据差动机构的叠加原理将上述单独传动算得的转速相加或相减(即代数和)求出。
螺旋布料时,溜槽由最大角度50o往内连续地调整到最小角度。
传动机构设计时还应考虑,第一级减速比Z6/Z5采用单头蜗杆传动,以利自锁,在修理或调整抱闸时不会由于溜槽的自动倾翻力矩而转动,此外,带动溜槽的最后一级圆柱齿轮的被动轮应采用扇形齿轮,这样不但可以缩短溜槽驱动轴和屏风之间的距离,而且在更换溜槽时能使溜槽摆成水平,便于更换。
D布料器的结构设计
在布料器设备中,工作条件最恶劣的部件是气密箱和布料溜槽的悬挂结构,气密箱是布料器的主体部件,设计时,寿命应尽可能达到一代炉龄,为了保证布料器正常工作,必须使布料器的最高温度不超过70℃,正常温度应控制在40℃左右,因此,布料器必须有可靠而廉价的冷却措施。
当使用气体(氮气或半净煤气)冷却时,其进气温度一盘在30℃左右,冷却气的含尘量(指煤气)应小于5mg/m3,条件差的也不得超过10mg/m3,排气口的缝隙宽度为2~5mm,通过缝隙的排气速度可以在6~12m/s的范围内选用,箱体内冷却气的压力比炉喉煤气压力高0.01MPa,当炉喉压力变化时,冷却气的压力也应能自动调整。
为了保证运动零件的正常温度,必须对箱体内的气流分布进行正确的设计。
图4-38是一种气密箱结构,它不但通入冷却气,而且在底部有水冷却屏风,中心喉客的外围也设有水冷外套15,这样冷却气用量大为减少。
布料器采用四个相同的推力向心球轴承,由于轴承型号相同,有利于订货和制造,四个轴承布置在同一直径上,有利于中心喉管直径的扩大,对于大型高炉采用这种结构比较有利,成对使用的推力轴承在安装时要考虑方便地调整轴承间隙,可在8和11的法兰面之间加调垫片来解决。
轴承座法兰11是用螺栓连接把载荷传递到顶盖上的,由于螺栓处于冷却区域内,又有水冷却的中凡固定圆筒保护,不会产生蠕变现象。
大轴承采用干油润滑,干油通过输油管10(在圆周上共有四个)进入布料器内的上面两个轴承,然后通过连接法兰盘12的孔进入下面两个轴承。
两个大齿轮同样用干没润滑。
两个蜗轮箱的上小齿轮4和齿轮对3也有同样的润滑油进行润滑。
蜗轮箱内部的零件采用稀油润滑,在箱体上安有稀油泵2,其动力由蜗杆轴通过小齿轮对3传动,当调整溜槽倾角时,通过齿轮对3带支油泵2,油泵2把辅助油箱的润滑油吸出,经过滤油器和油管送到蜗轮箱内部,喷到蜗轮杆和齿轮上。
两上蜗轮箱支承在旋转圆筒13的托架上,它和旋转圆筒一起旋转,因此,滤油器和辅助油箱都要安装在托架上跟着一起转动,如果要简化润滑,也可以考虑采用干油润滑,这只有在高炉休风时打开气密箱的工作孔22用油枪打入干油。
图4-39是溜槽驱动轴和溜槽的悬挂结构图,溜槽的驱动轴是花键轴,溜槽和驱动轴连接的部位受扭力较大,一般宜单独制作,应选用较好的耐热合金钢或普通镍铬合金钢,驱动臂15和溜槽13之间有滑道相配,用螺栓连结,溜槽的尾部有挡板12,它是焊在溜槽端部的,通过上述结构,螺栓基本上不受剪力,溜槽的重量由滑道和尾部的档板传递到驱动臂上。
溜槽的驱动臂和驱动轴,受扭矩较大,又处在炉喉内工作,除庆选用较好的材质外,还应考虑冷却措施。
图4-39的驱动轴的外表面和内部是通冷却报的,为了正确引导花键槽表面的气流,并避免冷却气和炉内的脏煤气相混,设有保护套11,为使冷却气能够冷却溜槽驱动臂15的内表面,把驱动轴6做成空心,通过的气流在轴端部拐弯沿驱动臂表面向四周扩散出去,驱动臂内侧保护板14可以保证上述冷却气沿驱动臂表面的正确流动,并避免炉喉脏煤气混入。
E无料钟炉顶的布料方式和特点
无料钟炉顶的布料溜槽不但可作回转运动,并且可作倾角的调整,因此可有多种布料形式,但为简化电气控制系统,目前常用有如图4-40所示四种布料方式。
a自动环形布产(图4-40a)按选定溜槽倾角进行布料,布料时溜槽只作旋转运动(倾角根据炉况,由选择矩阵或计算机选定)。
b自动螺旋布料或同心圆岂有此理料(图4-40b)螺旋布料是连续无调整倾角,每次布料的调整时间等于下料时间,如果料层进行等高均匀布料,溜槽摆动倾角调整由最大倾角(一般为50℃)往内调整到最小角度,或用计算机根据炉况选择溜槽倾角内,外极限角及溜槽
每转一圈倾角的递增量,速度应由小到大变化,故要使用直流电机,为简化机控制系统,可采用步进式同心圆布料代替,布料时,溜槽每转一圈倾角由外往里变化一个角度,也可以溜槽在同一角度布几层后再跳变一个角度,这样就减少了溜槽跳变角度,采用步进同心圆布料时,由于间隙调整角度,故溜槽调整倾角速度应比螺旋布料高一些,可以考虑下料时间一半或更短时间达到全部的调整范围,倾解调整可以采用交流电机。
c手动定点布料(图4-40c)高炉内某一位置或某点发生管道或过吹过,可使用手动定点布料,此时溜槽对准某处固定不动。
d扇形布料(图4-40d)当高炉内产生偏析或局部崩料时,可采用扇形布料,溜槽倾角和它的方位角以及扇形弧段的摆动角都设有手动选择挖掘,布料溜槽在指定的弧段内慢速来回摆动。
f无料钟炉顶的发展随着无料钟炉顶的广泛使用和不断改进,不仅设备结构有了很大的变化,并且在总体布置上了出现了多种形式,目前应用的大大致可分为并罐式、串罐式和串并罐式三种。