标准电池箱体C箱技术协议鹤壁天汽0119 1.docx
《标准电池箱体C箱技术协议鹤壁天汽0119 1.docx》由会员分享,可在线阅读,更多相关《标准电池箱体C箱技术协议鹤壁天汽0119 1.docx(22页珍藏版)》请在冰豆网上搜索。
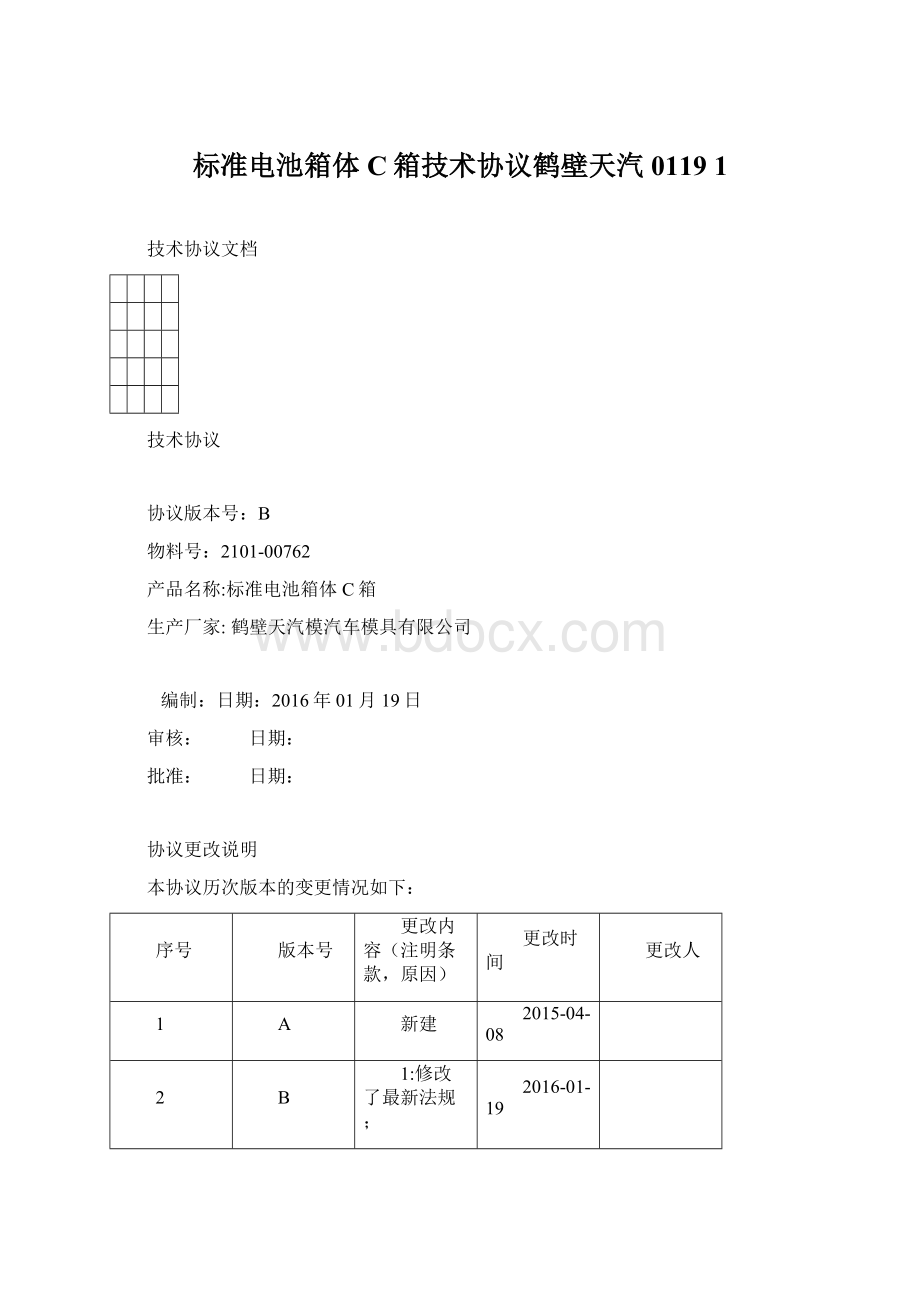
标准电池箱体C箱技术协议鹤壁天汽01191
技术协议文档
技术协议
协议版本号:
B
物料号:
2101-00762
产品名称:
标准电池箱体C箱
生产厂家:
鹤壁天汽模汽车模具有限公司
编制:
日期:
2016年01月19日
审核:
日期:
批准:
日期:
协议更改说明
本协议历次版本的变更情况如下:
序号
版本号
更改内容(注明条款,原因)
更改时间
更改人
1
A
新建
2015-04-08
2
B
1:
修改了最新法规;
2.1:
由于密封体单独供货,工艺设计电池自动化组装线要求各物料单独供货,删除了密封体部分,修改了供货方式;
3-1:
完善电泳、喷漆、螺纹连接具体要求
3-2:
完善公差具体详细要求;
3-5:
完善相关试验具体要求;
3-6:
修改了标示参数参考图片,增加电池类型;
3-10:
由于工艺设计电池自动化组装线对标准件有特殊要求,修改了物料清单;
3-11:
增加了适用车型。
2016-01-19
甲方:
乙方:
鹤壁天汽模汽车模具有限公司
本协议旨在确定甲方要求乙方所供应产品达到的标准,乙方所供应的产品的技术必须能够满足双方所约定的以下条款,以下条款未涉及的,按照双方签订的《采购合同(协议)》所约定的标准及国家标准执行。
1.满足的技术法规
乙方所供的零部件应满足整车销售区域(包括海外)的法规。
如果销售区域(包括海外)有认证要求,应取得相应的认证证书。
标准电池箱体C箱需符合以下标准:
GB/T2423
电工电子产品环境试验
GB4208-2008
外壳防护等级(IP代码)
QC/T413-2002
汽车电气设备基本技术条件
GB/T2408-2008
塑料燃烧性能的测定水平法和垂直法
GB/T228.1-2010
金属材料拉伸试验第1部分室温试验方法
QC/T625-2013
汽车用涂镀层和化学处理层
GB/T1804-2000
一般公差未注公差的线性和角度尺寸的公差
GB/T1184-1996
形状和位置公差未注公差值
GB/T708-2006
冷轧钢板和钢带的尺寸、外形、重量及允许偏差
GB/T2975-1998
钢及钢产品力学性能试验取样位置及试样制备
GB/T222-2006
钢的成品化学成分允许偏差
GB/T31467.3-2015
电动汽车用锂离子动力蓄电池包和系统第3部分:
安全性要求与测试方法
JB/T4129-1999
冲压件毛刺高度
附件2
焊接技术要求
2.技术资料
2.1甲方应在本协议中向乙方明确以下与采购合同零部件相关的技术要求及资料提供方式、来源:
1)产品图纸或技术描述:
标准电池箱体C箱件包括上盖、下箱总成(含绝缘板)、加热片托板、模组压条及标准件;甲方向乙方提供3D数模,上盖、下箱总成、加热片托板及模组压条四份2D图纸,其余单个组件2D图纸由乙方根据3D图纸绘制完成后与甲方确认。
2)供货技术条件:
(1)乙方必须保证所提供产品与数模一致,符合技术要求,如果因为乙方提供的产品错误造成设计变更,导致甲方车间返工、延误交车等情况事故,其后果由乙方负责。
(2)上盖、下箱总成(含绝缘板)、加热片托板、模组压条及标准件(固定部分)分开包装供货(包装状态以协商为准)。
(3)技术资料双方确认后,乙方因制程及工艺需要对数模或焊接组装等做的任何变更,应事先通知并得到甲方技术部门认可,相关变更符合**供应商及设计变更的规定。
3)企业标准:
乙方所提供的产品按国家标准、行业相关标准执行。
4)其它资料:
乙方须积极配合甲方提供甲方所需要的与钣金、焊接、标准件固定技术要求(包括标准件强度等级、拧紧扭矩值)相关的资料,并保证资料的准确性与真实性。
2.2在本协议生效后,如果甲方计划对采购合同零部件作任何修改,应及时通知乙方。
若上述技术修改涉及乙方工装要作相应更改,乙方应及时按新方案作相应修改。
3.零部件特殊要求
1)外观质量要求(包括油漆,镀层质量,颜色,产品标记、标识,定尺情况、触感、声感、气味);
(1)标准电池箱体C箱要求整体(除搭铁柱部分、绝缘板、模组压条外)电泳并着底漆、黑色面漆;搭铁柱部分禁止电泳,并且需要喷涂导电漆。
外观具体要求以送样双方确认为准;标准电池箱体C箱应无锈蚀、霉斑、镀层脱落、划痕、毛刺、开裂、隐裂、变形等缺陷;下箱总成应安装或焊接正确、完整;毛刺高度要求:
符合JB/T4129-1999规定f级;
(2)焊接部位按照附件2:
《焊接技术要求》执行,焊缝连续、平整,无虚焊、漏焊及焊渣、杂质粘附。
螺纹连接部分:
按照技术要求(如扭矩、涂螺纹紧固胶等)拧紧、防松、无遗漏等;
(3)喷塑、油漆表面平整、光滑,无气泡或剥落现象。
油漆涂层符合QC/T625-2013规定要求;产品外部油漆层应均匀、无气泡、无空白、无堆积和溢流现象;产品油漆层应与被覆盖物的表面牢固结合,经栅格法试验后漆层应不脱落;
(4)整体无损伤、无锈蚀及其他影响性能的缺陷;焊接要求满足附件《焊接技术要求》;
(5)成形拉延件允许有局部材料变薄或增厚,变薄后的最小厚度为:
tmin=70%t(tmin—材料的最小厚度,mm;t—材料的公称厚度,mm。
);
2)关键参数要求含外形尺寸、安装尺寸、尺寸公差或相关的产品图纸中特殊特性尺寸和三维电子模型及CAD图纸要求):
产品总体尺寸以甲方提供的3D图纸及2D图纸要求为准;对于后续由于开发需求甲方在产品图纸上的修改,乙方应按照修改后的图纸要求修改产品,未标注尺寸以3D图纸为准,未注尺寸公差按照国标GB/T1804-2000中的M级(中等级)相应要求执行,未注形位公差按GB/T1184-1996中的K级(中等级)相应要求执行;乙方应随批次提供所供物料的全尺寸报告。
3)主要性能指标及质量要求(物理性能(硬度、强度)、化学成分等):
材质按图纸要求,材料厚度符合GB/T708-2006标准,其力学性能符合GB/T2975-1998标准,化学成分符合GB/T222-2006,并由供应商提供相关原材料、力学性能检测报告;
标准电池箱体C箱所用塑料类材料(含密封圈、绝缘板)应具有阻燃特性,并符合GB/T2408-2008标准的HB等级(水平燃烧)和V-0等级(垂直燃烧)的要求;
物质(材料)禁用要求:
序号
物质(材料)类别
是否禁用(不禁用应说明包含该物质的零件或位置)
1
石棉
是
4)车内非金属材料环保性要求
物料有害物质限值和气味等级应符合下表的规定。
序号
检测方法
检测项目
限值要求
备注
1
VDA277
TVOC
<50µgC/g
2
VDA277
苯
<5µg/g
3
VDA277
甲苯
<5µg/g
4
VDA277
二甲苯
<15µg/g
5
VDA275
甲醛
<10mg/Kg
6
DIN75201B
雾气试验
<5mg
7
VDA270
气味试验
≤3
23℃/40℃
≤3.5
80℃
注:
材料的环保性还需满足相关的国家标准及行业标准。
对应的检测方法或检具按标准要求执行,PPAP审批前乙方应提供甲方认可的第三方检测机构出具的检测报告;
5)可靠性和寿命要求(技术规范进行的寿命试验、磨损试验等要求):
使用寿命:
≥8年(以整车寿命起始日开始计算);
质保期:
8年(以整车质保起始日开始计算);
防护要求:
乙方所提供的标准电池箱体C箱总成组装完成后,在整车全寿命周期内应满足GB4208-2008中IP67的要求;乙方应在出厂前做标准电池箱体C箱总成的IP67测试,要求全检;
标准电池箱体C箱应按照下面的试验条件进行试验,试验结束后标准电池箱体C箱应无开裂、生锈、变形等不良;油漆层应无皱缩或起层现象;
耐高温:
标准电池箱体C箱在80℃环境中存储8h,恢复常温后进行检查;
耐低温:
标准电池箱体C箱在-40℃环境中存储8h,恢复常温后进行检查;
耐温度变化:
按照GB/T2423.22-2012规定Na试验方法进行耐温度变化试验,低温-40℃,高温80℃,低温或高温的暴露持续时间均为3h,循环次数5次;
耐温度、湿度循环变化:
标准电池箱体C箱按GB/T2423.34-2012的规定进行试验;
耐振动试验:
标准电池箱体C箱组装后(内部至少固定135Kg物体)按GB/T31467.3-2015的规定进行试验,试验结束后,箱体无损伤。
盐雾试验:
标准电池箱体C箱应经过168h的盐雾试验(NSS),试验应按照GB/T2423.17-2008中Ka:
盐雾试验方法的规定进行。
乙方应提供上述型式试验报告,批量供货后1年1次。
乙方开发产品所用材料,必须保证时效性;对于因材料失效所造成的后果,甲方有权向乙方进行索赔。
6)标示和包装要求:
每只标准电池箱体C箱上必须要有正负极标识、高压危险警告标识、铭牌等,标识要求为永久性标识。
标识参数:
(图片仅供参考)
最小包装应注明:
产品名称、产品物料号、生产厂家代码(禁止出现生产厂家名称、标识)、生产日期、产品单位和数量,字体要求清晰、明确;
标识参数:
(表格为参数,图片仅供参考)
供应商代码
9083
物料号
2101-00762
生产日期
根据实际生产日期填写
包装箱应牢固,产品在箱内不应串动,必须保证在堆放、搬运及运输过程中不降低制件品质,包装箱内应有装箱单和出厂合格证等技术文件;
7)零部件的标示应满足整车销售区域的法规要求。
8)一般标示要求:
符合国家、行业相关规定。
9)产品应满足的国家标准/行业标准/企业标准及海外目标市场标准对应条款要求。
10)物料清单:
随总成附件物料明细:
序号
厂家代码
物料描述
数量
物料类别(直接装车附件/需二次加工后装车附件/转交客户配件)
1
9083
电池箱体上盖
1
需二次加工后装车附件
2
9083
电池箱体下箱总成
1
需二次加工后装车附件
3
9083
模组压条(左)
1
需二次加工后装车附件
4
9083
模组压条(右)
1
需二次加工后装车附件
5
9083
M6X20外六角螺栓组合件(达克罗)
36
需二次加工后装车附件
6
9083
加热片托盘
5
需二次加工后装车附件
7
9083
M5外六角带法兰面自锁螺母(达克罗)
10
需二次加工后装车附件
要求:
发货时请按照所属物料分类,并将物料号在外包装上醒目位置张贴。
11)适用车型系列:
本协议适用的甲方车型平台如下(★标记为适用):
车型
车长系列
匹配情况
车型
车长系列
匹配情况
车型
车长系列
匹配情况
后置非公交
L≤7m
★
后置公交
L≤7m
★
前置车型
L≤7m
7m<L≤8m
★
7m<L≤8m
★
7m<L≤8m
8m<L≤9m
★
8m<L≤9m
★
8m<L≤9m
9m<L≤10m
★
9m<L≤10m
★
9m<L≤10m
10m<L≤11m
★
10m<L≤11m
★
10m<L≤11m
11m<L≤12m
★
11m<L≤12m
★
11m<L≤12m
L>12m
★
L>12m
★
L>12m
12)未尽事宜应符合国家和行业相关标准要求;
4.备证要求(是否需要提交相关的备证资料,以便于明确产品责任如:
产品服务协议、关键材料分析试验报告、检验报告、维修手册、易损件图册、配件清单等)
乙方在提供每批次产品的同时,必须提供该产品的《材料的性能检测报告》、《产品使用说明书》、《配件目录》、《配件图册》、《维护保养手册》售后服务类资料,《配件目录》、《配件图册》、《维护保养手册》以可编辑电子版形式提供给技术中心办公室***************,文字以中英文最佳、中文次之。
5.其它约定
1)在标准电池箱体C箱装配过程中,乙方负责对标准电池箱体C箱的装配进行技术支持和维护,后续运营过程中,乙方负责提供售后服务,确保不因标准电池箱体C箱方面的问题而影响车辆装车、调试、路试和正常运营。
因乙方产品问题对甲方造成的一切损失均由乙方负责。
对在商定运行时间内,乙方免费对已坏的标准电池箱体C箱进行更换。
2)乙方在接到甲方通知时,必须12小时内作出响应,如未能解决问题,乙方必须24小时内赶到现场解决,48小时内解决问题,如果乙方延期解决问题,乙方应承担由于延期给甲方造成的损失,每延迟一天,乙方需按逾期天数向甲方支付500元/天的违约金。
3)乙方供给甲方的所有产品不侵犯任何他人的知识产权,也未发生任何侵犯第三方知识产权事项,侵权范围包括但不限于专利、外观设计、实用新型、商标等。
如有侵权,与甲方无关,由乙方负责解决,并承担全部责任。
若因此给甲方造成损失的,乙方应据实赔偿。
4)乙方对产品的结构改进对甲方的产品性能和产品装配有影响时,应征得甲方技术部门的书面同意后,将更改内容及实施日期提前书面通知甲方。
5)乙方对工艺、产品内部结构进行更改时,应将更改内容及实施日期提前书面通知甲方,否则因更改造成甲方的一切损失均由乙方负责。
6)《保密协议》见附件1,作为双方签订的《标准电池箱体C箱技术协议》的附件,是《标准电池箱体C箱技术协议》不可分割的组成部分,具有同等法律效力。
7)技术协议无论何时签署,有效期均以采购合同(协议)的有效期为准,变更时双方另行签订书面协议。
8)任何一方均不得将本技术协议的内容向第三方泄露,否则守约方有权追究违约方的违约责任。
9)因履行本协议内容所发生的争议均按照与本协议相关的采购合同(协议)约定的争议解决方式处理。
10)本协议中所有甲方要求乙方所供的零部件或标示等应满足整车销售区域(包括海外)的法规的,其销售区域均以甲方整车实际销售到的区域为准,由甲方以书面形式告知乙方,并由甲方向乙方提供或协助乙方取得有关区域的法规要求。
11)本协议涉及的整车配置及参数,为首次匹配参数;在车辆匹配过程中,双方使用此协议状态,但不限于此车型参数;在整车参数发生重大变更时,甲方应通知乙方确认。
12)未尽事宜双方协商处理。
13)本协议是双方签订的采购合同的有效组成部分,具有同等法律效力。
本协议一式两份,甲方一份,乙方一份,自双方签字盖章后生效。
甲方使用符合《中华人民共和国电子签名法》要求的可靠的电子印章和电子签名,具有同实物印章同等的法律效力。
甲方:
乙方:
鹤壁天汽模汽车模具有限公司
甲方技术代表签字:
乙方技术代表签字:
日期:
:
2016年01月19日日期:
2016年01月19日
附件2
焊接技术要求
一、适用范围
适用于钣金制件点焊、凸焊、CO2保护焊及螺柱焊的焊接质量技术要求。
二、技术要求
1.焊接总成尺寸要求
总成在焊接过程中,各件相对位置应符合数模要求,误差不能大于1.0mm,焊接变形及其它变形不能大于0.5mm。
2.点焊要求
焊点分布合理,应与我方提供的资料相符合,根据不同材料、不同板厚选择合理的焊接参数,焊接质量可靠,焊点外观美观,不能有漏焊、虚焊、焊穿等不良现象,焊接参数设置可参考附表一。
2.1点焊焊点数量
2.2.1检查方法:
目视检查;
2.2.2评价依据:
产品图纸;
2.2.3评定结果:
合格――焊点数量符合产品图纸;不合格――焊点数量不符合产品图纸;
2.2.4缺陷类型:
漏焊、错焊。
2.2焊点强度
2.2.1检查方法:
使用扁铲楔入两焊点之间,以厚板处建立支点向薄板一方掰动,直到薄板焊点熔核处发生变形为止;方法见下图1
图1凿入深度尺寸
2.2.2评价依据:
焊点熔核处变形时焊点未发生破坏则为合格,若发生破坏则为不合格;
2.2.3评价结果:
合格——焊点熔核处变形时焊点未发生破坏;不合格——焊点熔核处未变形焊点发生破坏;
2.2.4缺陷类型:
虚焊、焊穿、开焊;
2.2.5在以下情况下一般不宜使用破坏性检查方法来判定焊点质量:
a、最薄板件厚度大于1.4mm;
b、有外观要求的部位;
c、胶接焊点;
d、扁铲无法作用到的部位;
3.凸焊要求
螺母、螺栓的焊接要达到强度要求,且要保证螺母螺栓与板件过孔同心度,不能出现遮盖螺纹现象。
根据不同规格凸焊件、不同板厚及材料选择合理焊接参数。
螺母、螺栓焊接参数选择可参考附表二,凸焊件焊接强度要求可参考表三。
3.1凸焊螺母数量
3.1.1检查方法:
目视检查;
3.1.2评价依据:
产品图纸;
3.1.3评价结果:
合格——符合产品图纸;不合格——不符合产品图纸
3.1.4缺陷类型:
漏焊、错焊。
3.2凸焊螺母位置
3.2.1检查方法:
目视及检具检查;
3.2.2评价依据:
产品图纸;
3.2.3评价结果:
合格——符合产品图纸;不合格——不符合产品图纸,例如:
错位。
3.3凸焊螺母型号
3.3.1检查方法:
目视检查(必要时配合螺母或卡子试装配);
3.3.2评价依据:
产品图纸;
3.3.3评价结果:
合格——符合产品图纸;不合格——不符合产品图纸;
3.3.4缺陷类型:
型号错装。
3.4凸焊螺母与制件孔同轴度
3.4.1检查方法:
目视检查,若有争议或必要时可利用同轴度检测,检测方法见下图2;
3.4.2评价依据:
同轴度≤0.5mm;
3.4.3评价结果:
合格——同轴度≤0.5mm;不合格——同轴度>0.5mm;
3.4.4缺陷类型:
错位;
3.5外观检查
3.5.1检查方法:
肉眼观察凸焊螺母表面状况(必要时配合螺栓或卡子试装配);
3.5.2评价依据:
凸焊螺母表面不允许出现以下缺陷:
a、螺母螺纹上有影响螺栓或卡子装配的焊渣、飞溅或其它杂物;b、螺母螺纹因过烧等其它原因被损坏;
3.5.3评价结果:
合格——未出现以上缺陷;不合格——出现以上任一缺陷;
3.5.4缺陷类型:
螺纹损坏;
3.6凸焊螺母强度
3.6.1检查方法:
特制套筒配合扭矩扳手检测如图3,采用剥离试验检查焊接螺母的焊接强度,按图示方法进行、先将焊接的钢板固定住,施加与螺母的中心轴成直角的回转力,测定使螺母剥离所需要的扭矩;
3.6.2评价依据:
当检查力矩逐渐增大到标准规定值时(参见表三),焊接处不得出现任何断裂或变形;
3.6.3评价结果:
合格——最小剥离扭矩达到以上标准值,焊接处未出现任何断裂或变形;不合格——最小剥离扭矩未达到以上标准值,焊接处出现断裂或变形;
3.6.4缺陷类型:
虚焊。
4.CO2焊要求
CO2焊接质量应满足强度要求,且焊道不能出现虚焊、气孔等不良现象。
根据不同材料、不同板厚选择合理的焊接参数,焊接参数可参考表四。
4.1CO2焊缝
4.1.1焊缝数量;
4.1.2检查方法:
目视检查;
4.1.3评价依据:
产品图纸;
4.1.4评价结果:
合格——符合产品图纸;不合格——不符合产品图纸;
4.1.5缺陷类型:
漏焊、错焊。
4.2焊缝位置
4.2.1检查方法:
目视检查;
4.2.2评价依据:
产品图纸;
4.2.3评价结果:
合格——符合产品图纸;不合格——不符合产品图纸;
4.2.4缺陷类型:
焊偏。
4.3焊缝长度
4.3.1检查方法:
目视检查(必要时用钢板尺测量);
4.3.2评价依据:
对于CO2焊点,长度符合图纸要求;
4.3.3评价结果:
合格——符合要求;不合格——不符合要求;
4.3.4缺陷类型:
焊缝长度过长/过短。
4.4焊缝表面
4.4.1检查方法:
目视检查;
4.4.2评价依据:
a、焊缝和板件的应均匀过度,无焊偏现象;b、焊缝表面应无明显金属氧化皮、焊瘤、咬边、气孔和未熔合等现象,焊缝应全部将间隙填满。
c、底盘焊缝:
底盘件多为中厚板焊接,如果图纸没有另作规定,缺陷的极限值为:
其单条焊缝缺陷的总长度不得大于此焊缝长度的25%。
4.4.3评价结果:
合格——符合要求;不合格——不符合要求。
4.5焊缝内在质量
4.5.1检查方法:
破坏性检查;
4.5.2评价依据:
双方协商确定;
4.5.3评价结果:
合格——焊缝熔深满足产品定义要求;不合格——焊缝熔深不满足产品定义要求。
备注:
对重要薄板焊接件,标准熔深一般定义为较薄板厚的1/3;当板厚大于3mm时,熔深达到1mm即可。
5.螺柱焊要求
焊接参数可参考表五。
5.1螺柱焊接质量应满足强度要求,且满足以下判定标准内容:
序号
项目
标准
图片
备注
1
虚焊
螺柱应完全插入溶池,螺柱周围焊接均匀
外观
2
熔池过大
熔池满足实际焊接效果,表面均匀美观
外观
3
螺柱倾斜变形
焊接时螺柱应垂直焊接表面倾斜角度为90°±5°
外观
4
母材背面变形
焊件背面无严重变形,不影响后续装配及功能要求
外观
5
焊穿
焊件背面无烧穿孔
外观
6
螺纹损坏
焊接过程中要保证螺纹不被损坏,用相应的螺母能够顺利拧入视为合格
外观
7
倾斜检验
捶击检验时,当螺柱倾斜角度不小于30°时,螺柱无裂纹或假焊等缺陷。
强度
8
扭力扳手检验
最小抗扭力值满足相关标准要求(见表4)
强度
5.2母材焊接的最小板厚要求母材焊接的最小板厚与螺柱端径有关。
为了充分利用紧固件强度,防止焊穿和减小变形,母材厚度≥螺柱端径的1/3,当强度不作为主要要求时,最薄也应≥螺柱端径的1/5。
5.3评价依据:
不同类型和不同直径螺柱焊的扭矩标准(参见表六)
5.4检查方法:
破坏、弯扭、扭力扳手扭力检查;检测如图4和图5。
6.工艺文件要求
在正常生产时应编写必要的工艺文件,以保证产品的焊接质量。
工艺文件应包括标准作业书、产品检查基准书等,并须经过乙方认可后方可使用。
表一:
低碳钢板点焊工艺参数表
板厚
(mm)
熔核直径
(mm)
最佳规范
中等规范
焊接时间
(S)
焊接压力
(KN)
焊接电流
(KA)
焊接时间(S)
焊接压力(KN)
焊接电流(KA)
0.6
4.3~5.3
0.14
1.6
7.5
0.22
1.00
6.3
0.8
4.5~5.5
0.16
1.9
7.8
0.30
1.25
6.5
1.0
5.5~6.0
0.20
2.25
8.5
0.40
1.50
7.2
1.2
5.8~6.2
0.24
2.7
9.8
0.46
1.75
7.7
1.5
6.0~7.0
0.26
3.6
10
0.50
2.40
9.1
2.0
7.0~8.0
0.40
4.7
11
0.72
3.0
10.3
3.2
8.0~10.0
0.64
8.2
12.4
1.20
5.0
11.9
注:
(1)本文件中的板厚指①不等板厚两层板焊接时较薄焊件厚度;②多层板焊接时焊件总厚度的二分之一;
(2)首先选用最佳规范,如最佳规范不能满足焊接要求