UHPLF电炉冶炼工艺技术操作规程.docx
《UHPLF电炉冶炼工艺技术操作规程.docx》由会员分享,可在线阅读,更多相关《UHPLF电炉冶炼工艺技术操作规程.docx(11页珍藏版)》请在冰豆网上搜索。
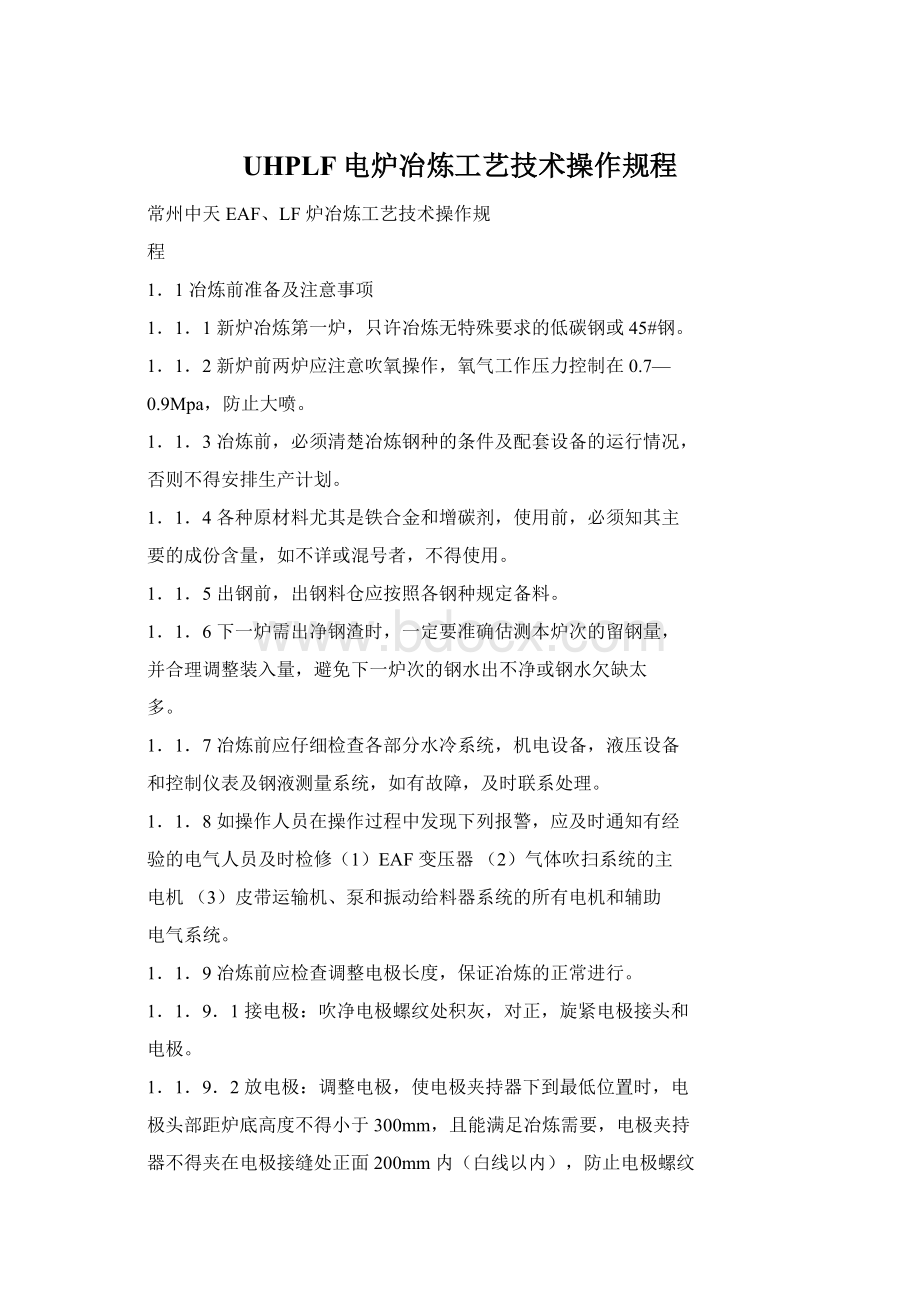
UHPLF电炉冶炼工艺技术操作规程
常州中天 EAF、LF 炉冶炼工艺技术操作规
程
1.1 冶炼前准备及注意事项
1.1.1 新炉冶炼第一炉,只许冶炼无特殊要求的低碳钢或 45#钢。
1.1.2 新炉前两炉应注意吹氧操作,氧气工作压力控制在 0.7—
0.9Mpa,防止大喷。
1.1.3 冶炼前,必须清楚冶炼钢种的条件及配套设备的运行情况,
否则不得安排生产计划。
1.1.4 各种原材料尤其是铁合金和增碳剂,使用前,必须知其主
要的成份含量,如不详或混号者,不得使用。
1.1.5 出钢前,出钢料仓应按照各钢种规定备料。
1.1.6 下一炉需出净钢渣时,一定要准确估测本炉次的留钢量,
并合理调整装入量,避免下一炉次的钢水出不净或钢水欠缺太
多。
1.1.7 冶炼前应仔细检查各部分水冷系统,机电设备,液压设备
和控制仪表及钢液测量系统,如有故障,及时联系处理。
1.1.8 如操作人员在操作过程中发现下列报警,应及时通知有经
验的电气人员及时检修
(1)EAF 变压器
(2)气体吹扫系统的主
电机(3)皮带运输机、泵和振动给料器系统的所有电机和辅助
电气系统。
1.1.9 冶炼前应检查调整电极长度,保证冶炼的正常进行。
1.1.9.1 接电极:
吹净电极螺纹处积灰,对正,旋紧电极接头和
电极。
1.1.9.2 放电极:
调整电极,使电极夹持器下到最低位置时,电
极头部距炉底高度不得小于 300mm,且能满足冶炼需要,电极夹持
器不得夹在电极接缝处正面 200mm 内(白线以内),防止电极螺纹
处损坏,折断电极。
1.1.9.3 换电极:
如果电极的端部已出电炉盖的弧形坑,且伸出
夹持器的距离只有几厘米,则更换电极。
更换电极时,将一个合适
的吊具挂到行车中,稍微用力吊住电极,打开夹持器,吊出电极至
电极接长站,将接好的电极放入电极夹持器内,调整电极长度。
1.2 补炉
1.2.1 每炉出钢后,炉长要对炉壁,渣线,炉盖中间耐材部位,
出钢口及水冷元件进行检查。
1.2。
2 出钢口的检查,更换,填充。
1.2.2.1 出钢后,检查出钢口管砖浸蚀程度。
如端砖内径超过直
径 200mm,或出钢时间小于 80 秒,应立即通知有关人员,做好更
换出钢口管砖,端砖的准备。
1.2.2.2 出钢后,如不需要更换出钢口,立即清净出钢口残渣钢
(如局部有缺陷,可用耐火材料修补),关好出钢口托板,从偏心区
填料孔加入填充料,填满时,使填充料呈馒头状,填料时应注意填
充料清洁干燥。
1.2.3 炉壁的维护,出钢后,清净炉门坎残钢残渣,观察炉坡,
渣线浸蚀情况,如需要喷补,应趁高温快速补炉。
1.2.3.1 如需补炉时,出钢前应做好补炉准备工作,准备好补炉
工器具和材料,并将补炉料 500—1000kg 灌入补炉机中,调试正常。
1.2.3.2 用离心式补炉机时,则将炉盖旋开,吊起补炉机补炉,
用直喷式补炉机时,从炉门喷入。
1.2.3.3 用直喷式补炉机时,要调整补炉机空压,水压力,使喷
补料呈糊状附于炉坡渣线处,以增加喷补料附着率,减少反弹率。
1.2.3.4 补炉后垫好炉门坎,炉门坎应两边高,中间稍低,使之
有利于自动流渣。
1.2.4 炉底的维护:
用手提式测温枪测量炉底温度,如炉底连续
测温高于 350℃,则需要垫补炉底,出钢时要将炉内钢水,钢渣尽
量出净,检查炉底及透气砖损坏,浸蚀情况。
若炉底有坑,需要垫
补时,用炉底捣打料垫补。
1.2.5 炉盖的检查:
小炉盖中心区厚度太薄,不能保证下一炉正
常冶炼,要及时更换。
1.3 废钢、铁水装入制度
1.3.1 废钢装入制度
1.3.1.1 装料前,炉长应和料场联系装料情况(特别是对需出净
的炉次),如有疑问,应消除后再行装料。
1.3.1.2 新修炉体第一炉炉底必须用大刀片,薄钢板等废钢覆盖。
1.3.1.3 装料时料篮中心发行量与炉子中心重合,并且料篮底部
稍沉入炉内,以不损坏水冷炉壁为直,然后快速打开料篮,将料卸
入炉内,连续生产时,用预热料篮向炉内配料。
1.3.1.4 空炉子第一料篮不得装入废钢锭和锭模等大块废钢,防
止损坏炉底。
1.3.1.5 装料后,如炉料超高,要用料篮料压平凸起钢铁料,但
要谨慎,不得挤压水冷炉壁,并避免料篮脱钩。
料篮移走后,炉沿
挂有废钢时,必须清除后,炉盖方可旋回,不准用炉盖推料或压料。
1.3.1.6 如需装二次料,二次料应在一次料送电前到达冶炼跨,
并在一次料加入后,迅速指挥行车落下料篮,吊起二次料(有铁水
时,先吊装铁水)。
待第一次料基本熔清后,将料篮至资金准备位,
将二次料装入炉内。
1.3.1.7 如不需装二次料,则下一炉的第一料篮运行方法同
1。
3。
1.3.2 铁水装入制度
1.3.2.1 在电炉装第一次料时,由调度室或炉前通知废钢领行将
铁水包开至电炉冶炼跨待装,运行过程中,铁水车两侧不能站人。
1.3.2.2 电炉加完第一次料后,,指挥行车进行铁水包吊装,将
铁水兑加入炉内。
1.3.2.3 一次料送电 3—7 分钟穿井结束后,送电时,炉门烧咀
(5MW)开时最大限度使用,将炉门废钢熔化。
铁水不能及时到站
时,如有二次料可在二次料向炉内兑入铁水,但熔清后,严禁向炉
内兑铁水。
1.3.2.4 兑铁水时,炉子四周平台除一人指挥外不能站人。
1.4 熔化
1.4.1 电力曲线:
起弧电压 10 级,穿井电压 3-5 级,熔清电压 3-
5 级,电流曲线采用 5—6 号曲线,根据废钢情况和兑铁水量
大小决定起弧穿井,熔化及停电吹氧时间。
1.4.2 氧碳枪使用
1.4.2.1 新炉第一炉,大补炉第一炉在钢铁料加齐前不吹氧,在
全部废钢基本熔清后,氧碳喷枪采用中等氧压向炉内供氧,炉门及
炉墙氧燃烧咀不使用。
1.4.2.2 正常炉次加料供电后即开始用最大氧压供氧,并视炉内
废钢熔化情况及渣况,调整枪位,同时喷碳粉,造泡沫渣,避免弧
光暴露,辐射到炉壁。
1.4.2.3 炉门及炉墙咀在每批废钢加入后,开始使用,,视炉门废
钢熔化情况决定使用时间,炉墙烧咀氧气,使用时间为加每批料后
5—8min。
废钢熔清后应关闭氧气。
1.4.2.4 使用氧枪而不使用碳枪时,碳枪应通压缩空气,以免碳
枪堵塞。
1.4.3 批料加入后送电 3~5 分钟,开始加入石灰,石灰用量依钢种[P]、
[S]含量要求。
1.4.5 氧化精炼
1.5.1 废钢基本熔清,测温 T≥1550℃,停电,取样分析:
C、Mn、P、S、Si 以及根据冶炼钢种不同要求的其它元素,
如 Ni、Cr、Cu 等。
1.5.2 取样后,采用光谱分析法确定钢中的碳含量,视钢水中碳
含量高低调整吹氧量和吹氧方式。
碳高时,提高供氧强度,吹氧脱
碳。
1.5.3 钢中[P]含量较高时,适时倾动炉子进行流渣,并按每批
100~500kgCaO 补造新渣。
1.5.4 钢液中[C]、[P]等达到要求后,应迅速升温至出钢温度准备
出钢。
1.5.4.1 出钢条件
终点成份
碳结钢[C]≤0.12%、[P] ≤0.03.%;
HRB335[C] ≤0.15%、[P] ≤0.030%
对于碳结构[C]0.12%~0.20%、HRB335[C]
0.10%~0.20%,可根据供氧量情况,在保证出钢后 LF 炉第一样合格
的前提下,不再另取终点样出钢。
其它钢种终点成份见分钢种质量计划。
出钢温度:
1610~1650℃,新炉,新包,换渣线第一炉,
冷包出钢温度可提高上限 20℃。
1.5出钢
1.6.1 将载有烘烤好的钢包车开至电炉出钢位置,调整包位,使
出钢流对正钢包中心。
1.6.2 出钢前,由高位料仓称出所需脱氧剂、合金料、渣料。
1.6.3 出钢时先向出钢侧倾炉+1~5°,然后打开出钢口托板,此
时填料,钢水应自动流出,如不自动出钢,则采用氧气引流。
1.6.4 打开出钢口前,钢包开始吹 Ar,流量 180~250L/min,至出
钢完毕时,调小 Ar 流量,流量 80~110 L/min。
1.6.5 钢水出至 10~30t 时,进行包中脱氧合金化,按计划出钢量
进行成份调整,成份按下限调。
合金从高位仓加入,增碳剂在出钢
前由 LF 位加入,出到 30~60t 时加入渣料,出钢量大小根据钢包情
况及后道工序要求上 VD 炉次,保证钢包自由空间 0.9m,上 VOD
炉次保证 1.2m。
1.6。
6 当距规定出钢量还剩 2.5~3t 时,将炉子倾回,最后停止在
出渣侧-3~4°
1.6.7 钢包合金化加料情况
1.6.7.1 脱氧剂:
采用脱氧造渣剂或其它脱氧剂,用量随钢种确
定。
1.6.7.2 增碳剂:
碳按照规程下限调整,(计算时考虑铁合金带
入的碳量)收得率按 100%计算。
1.6.7.3 造渣材料:
采用石灰,萤石。
用量:
CaO700—
900kg,CaF2150—300kg。
1.6.7.4 其它合金元素见下表
CMnSi
调整规格下限下限下限
收得率100%100%90%
Fe—Si 或 Fe—Mn 用量包括脱氧剂带入的 Si,钢渣出
净的炉次的各元素成份应适当调低,以防钢水量少,成份偏高。
1.6.8 留钢留渣时,根据上次的留钢量及本炉废钢加入量及回收
率情况决定出钢量大小。
1.6.9 若一炉钢渣出净,则出钢前采用低电压送电,向炉内适量
补加萤石,稀释渣并向出渣侧倾炉,通过炉门最大限度流渣,然后
向出钢侧倾炉+1°--+5°出钢。
1.6.10 当正常出钢过程中发现有钢渣流出时,将炉体迅速翻回,
停止出钢,必要时钢包应开出倒渣。
出钢毕将钢包开至 LF 炉精炼
工位。
1.7 电炉炼钢配比
1.7.1 炉料配比
1.7.1.1 铁水或生铁配比:
按钢种要求配入。
生铁要在第一料篮
中加入。
1.7.1.2 废钢配比
1.7.1.2.1 两次装料,在全部采用废钢冶炼情况下,要求第一
料篮装入 50—65t,第二料篮装入 45—55t 废钢。
1.7.1.2.2 一次装料:
在有铁水情况下,铁水加入量为 35—
40t,则第一大料篮装入 55—65t 废钢。
1.7.1.2.3 如使用直接还原铁,由高位料仓加入或料篮加入。
如在料仓加入,加入速度应在 700—800kg/min。
则废钢数量应适应
减少。
1.7.1.2.4 根据后道工序要求,上 VD 或 VOD 炉次,废钢装入
量适当减少。
1.7.2 电炉出钢钢包内铁合金配入量规定:
出钢量*(下限规格-炉内残余量)%
铁合金加入量= ────────────────────
铁合金成份*合金收得率
2开新炉(含垫补炉底第一炉)电炉冶炼工艺技术操作规程
2. 1 开新炉(含垫补炉底第一炉)前需用大刀片覆盖炉底,如果
8 小时内不送电,不得装料,48 小时内不能冶炼,需在炉底铺
50mm 厚的石灰。
2.2 开新炉(含垫补炉底第一炉)不使用炉墙和炉门烧咀,废钢基
本熔清前不使用氧碳喷枪。
2.3 供电方式:
第一料篮废钢冶炼电压级数为 17 级,电流曲线为 3 号。
供电
冶炼 15—20 分钟后,停电烧结炉底 20 分钟(含垫补炉底)第一炉
停电烧结 10 分钟),再供电 10—15 分钟后,停电烧结炉底 20 分钟
(含垫补炉第一炉停电烧结 10 分钟),继续供电。
2.4 开新炉第二料篮开始冶炼电压级数 14,供电 10—20 分钟后,
停电烧结炉底和炉坡 20 分钟,烧结结束后,可适当提高电压级数,
但不能超过 12 级。
2.5 后几料篮不需停电烧结,冶炼电压级数为 10 级。
电流曲线 5—
6 号。
2.6 开新炉不得冶炼高碳钢和有特殊要求的钢种,一般冶炼普碳钢。
2.7 开新炉(含垫补炉底第一炉)不兑铁水。
3LF 炉冶炼工艺技术操作规程
3. 1 精炼前的准备
3.1.1 检查电极长度,避免在冶炼过程中接放电极。
3.1.2 电极安装程序
3.1.2.1 用压缩空气将电极联接处吹净
3.1.2.2 对正旋紧接头和电极
3.1.2.3 抬起炉盖至最高极限位置,调整电极,使电极下端略高
于炉盖下沿,且电极夹持器的夹紧器和夹紧位置在白线以外。
3.1.2.4 夹紧电极。
3.1.3 测温、取样等生产工具齐全,工作状态良好。
喂丝机具备
工作条件,所备盘线满足本炉次要求。
3.1.4 了解所用原料,特别是增碳剂和合金成份,成份不明不得
使用。
3.1.5 确认上料系统状态良好,料仓内合金、造渣料等块度合适,
干燥无杂质,供应充足。
3.1.6 确认台上增碳剂粒度合适;SiC、FeSi 粉等干燥,供应充足。
3.1.7 确认压缩空气系统、水冷系统工作状态良好。
3.1.8 确认供氩系统运行正常,PAr1.OMPn。
3.1.9 确认 LF 炉电气、机械、液压、仪表等设备运转正常。
3.2 精炼
3.2.1 电炉出钢前接上氩氮管,并作氩气吹通试验,如氩气不通,
则检查处理,根据冶炼钢种及电炉终点样碳含量,适当加入脱
氧剂和增碳剂,然后将钢包车开至出钢位置,打开出钢口的同
时,开通 Ar 气,流量 180—250L/min。
出钢至总量 3/4 时,适
当减小 Ar 气流量。
3.2.2 电炉出钢完毕,将钢包车开至 LF,调节 Ar 气流量控制,
以钢包车开动时,渣面微动,钢液不裸露为限。
3.2.3 钢包到位后,降下包盖。
Ar 气流量 80—150L/min,然后测
温。
3.2.4 根据渣况适量加入 Fe-Si 粉和 SiC,通常每炉总用量 70—
150kg,其中 FeSi 粉总用量在 20kg 以内,根据测温和是否上 VD 或
VOD 处理以及连铸需要钢水时间,决定供电制度。
3.2.5 供电大于 3 分钟炉渣发白,切电。
Ar 流量调至 150—
250L/min 搅拌 2—3 分钟,再调至 80—150L/min,测温,低碳钢温
度大于 1560℃,中、高碳钢温度大于 1540℃,取样
(1)后,可向
包中加入 50~80kg 白云石。
3.2.6 根据渣的还原情况,适当补加脱氧剂 SiC、FeSi 粉和电石,
根据电炉渣料加入量和电炉终点样中[S]含量及渣况,可适当补加
CaO、CaF2 和白云石,其中 CaF2 加入量占 CaO 的 2/5~1/5,白云石
加入量占 CaO 的 2/6~1/8。
对于 LF 炉冶炼结束,经 VD、VOD 处理
的炉次,在[S]含量不高的情况下,渣厚不得超过 80mm。
3.2.7 根据样
(1)结果,并考虑 UHP-EAF 出钢合金加入量和出
钢前元素残存量,除易氧化元素 A1、Ti、B 等之外,将其它合金成
份调至规格下限,低碳钢调碳低于下限 0.02%,收得率按 100%计,
特殊情况以分钢种规程为准。
3.2.8 增碳、合金化后,Ar 流量调至 200~270L/min 搅拌 2~3 分钟
后,再调至 80~150L/min,增碳>80kg,送电 5 分钟以上;增碳
<80kg,送电 3 分钟以上。
抬起电极,Ar 流量调至 200~270L/min 搅
拌 2 分钟后,调至 80~150L/min,测温,取样
(2)。
3.2.9 根据渣况适当补加 SiC 和 FeSi 粉。
根据测温结果,采用相
应供电曲线供电。
计算升温时间要考虑加入渣料后所吸收的热量。
处理量为 100t 时,每加入 100kg 渣料,温损约 1.5℃,每加入
100kg 合金,温损按 2℃计。
3.2.10 根据样
(2)结果,调整合金成份,除易氧化的元素
A1、Ti、B 等之外,将其它元素调至期望值中限,合金收得率按
100%计,特殊要求以分钢种规程为准。
计算全金加入量时应考虑电
极、耐火材料、保温材料增[C]0.01~0.02%,以及不经 VD、VOD 处
理炉次喂入 Ca-Si 线时增[Si]0.01~0.06%。
3.2.11 在确保吊包温度和成品成份符合要求的情况下,对于不上
VD 或 VOD 处理炉次进入下步喂丝操作。
钢种成份判定以分钢种规程或公司质量计划为准。
温度要求:
当钢水温度比需吊包温度高 5℃时,可进行喂丝操作。
吊包温度:
见《电炉厂温度制度一览表》。
连铸第一炉、新包或换渣线第一炉钢液温度应比正常炉次高 10--
15℃,LF 炉应随时与调度室联系,确保钢水吊包温度符合要求。
3.3 不经 VD、VOD 处理炉次喂丝操作:
3.3.1 调整 Ar 流量 80~150L/min。
3.3.2 喂 Ca-Si 线
喂 Ca-Si 线后,不得进行任何升温,调合金等操作,否则
需重新喂丝; 喂丝量按分钢种工艺卡规定和 Ca-Si 线质量决定喂入
量;喂丝速度:
3.5~5.5m/s。
3.4 加保温剂吊包:
喂丝完毕,开出钢包车均匀加保温剂 0.4~0.7kg/t 钢,卸掉氩气
管,吊包上连铸软吹氩。
3.5 对于 LF 炉冶炼结束,经过 VD、VOD 处理的炉次,除易氧化
的元素 A1、Ti、B 等之外,碳调至成份中下限,其它元素调至成份
中限,温度符合《电炉厂温度制度一览表》后,直接吊包上
VD、VOD 处理。
编制朱富强审核王日红批准徐和平
2006.11.15