组合件工艺分析与数控加工编程毕业设计.docx
《组合件工艺分析与数控加工编程毕业设计.docx》由会员分享,可在线阅读,更多相关《组合件工艺分析与数控加工编程毕业设计.docx(46页珍藏版)》请在冰豆网上搜索。
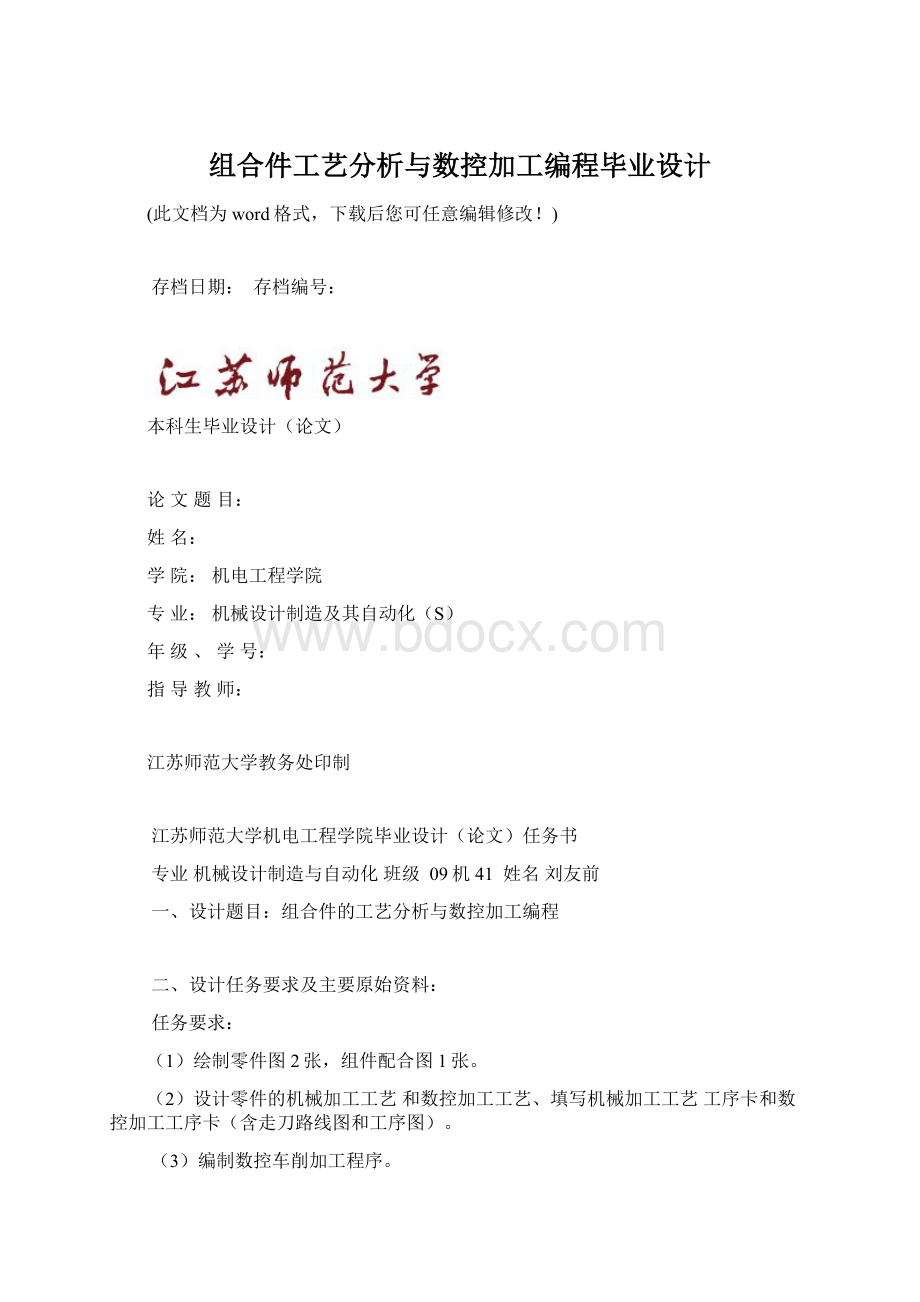
组合件工艺分析与数控加工编程毕业设计
(此文档为word格式,下载后您可任意编辑修改!
)
存档日期:
存档编号:
本科生毕业设计(论文)
论文题目:
姓名:
学院:
机电工程学院
专业:
机械设计制造及其自动化(S)
年级、学号:
指导教师:
江苏师范大学教务处印制
江苏师范大学机电工程学院毕业设计(论文)任务书
专业机械设计制造与自动化班级09机41姓名刘友前
一、设计题目:
组合件的工艺分析与数控加工编程
二、设计任务要求及主要原始资料:
任务要求:
(1)绘制零件图2张,组件配合图1张。
(2)设计零件的机械加工工艺和数控加工工艺、填写机械加工工艺工序卡和数控加工工序卡(含走刀路线图和工序图)。
(3)编制数控车削加工程序。
(4)编写设计书一份。
原始资料:
零件图两张装配图一张,年产量2000组件
三、设计时间:
2013年3月11日至2013年6月1日
指导教师:
(签名)
教学院长:
(签名)
组合件的工艺分析与数控加工编程
刘友前
[摘要]:
数控车床是目前使用最广泛的数控机床之一。
数控车床主要用于加工盘类、轴类等回转体零件。
通过数控加工程序的运行,可自动完成内外圆柱面、成形表面、圆锥面、端面和螺纹等工序的切削加工,并能进行钻孔、扩孔、铰孔、车槽等工作。
数控车床种类较多,但主体结构都是由:
数控装置、车床主体、伺服系统三大部分组成。
数控机床的编程方法有手工编程和自动编程两种。
手工编程,编制复杂零件时,易出错;而自动编程则不会发生这种情况。
本文是对典型轴类零件加工技术的应用及数控加工的工艺性分析,主要是对零件图的分析、毛坯的选择、零件的装夹、工艺路线的制订、刀具的选择、切削用量的确定、数控加工工艺文件的填写、数控加工程序的编写。
选择正确的加工方法,设计合理的加工工艺过程,充分发挥数控加工的高效、优质、低成本的特点。
还重点对轴类零件的加工艺进行了分析,最后对零件自检数据进行分析,和加工的结果分析。
关键字:
工艺分析加工程序切削用量公差
AssemblyprocessanalysisandNCprogramming
LiuYouqian
[Abstract]:
CNClatheiscurrentlythemostwidelyusedoneofCNCmachinetools.CNClatheismainlyusedformachiningshaft,diskandotherrotatingbodyparts.NCprogramtorunthrough,canbedoneautomaticallyandexternalcylindricalsurface,conicalsurface,formingsurface,threadandendmachiningprocesses,andcanbegrooving,drilling,reaming,reamingandsoon.MoretypesofCNClathes,butthemainstructurearemade:
lathebody,CNCequipment,servosystemtwo.Manualprogramming,thepreparationofcomplexparts,error-prone;whiletheautomaticprogrammingwillnot.
ThisarticleisatypicalapplicationofshaftpartsprocessingtechnologyandCNCmachiningprocessanalysis,mainlyonthepartsdiagramanalysis,roughselection,clampingparts,routingsformulation,toolselection,cuttingparametersdeterminedCNCmachiningprocessdocumentstofill,CNCmachiningpreparationprocess.Selectthecorrectprocessingmethods,therationaldesignofmachiningprocess,givefullplaytoCNCmachiningquality,thesleevepartsplusprocesswereanalyzed,andfinallythepartself-analysisofthedataandprocessinganalysisofresults.
Keywords:
ProcessanalysisProcessingproceduresCuttingTolerance
摘要2
Abstract2
目录3
前言5
第一章零件的分析6
1.1零件的结构工艺性分析6
1.1.1零件的形状及尺寸分析7
1.1.2零件的技术要求分析7
1.1.3零件的加工表面的分析7
1.2零件的材料分析8
第二章毛坯的设计9
2.1确定零件的生产类型和生产纲领9
2.2确定零件毛坯的制造形式9
2.2.1毛坯的种类9
2.2.2毛坯种类的选择9
2.2.3毛坯的形状和尺寸的选择9
第三章零件机械加工工艺规程的设计10
3.1定位基准的选择10
3.1.1粗基准的选择10
3.1.2精基准的选择10
3.2零件表面加工方法的选择10
3.2.1球面加工方法及误差补偿的选择11
3.3加工顺序的安排13
3.3.1加工阶段的划分13
3.3.2工序的合理组合13
3.3.3加工顺序的安排13
3.4工艺的制定14
3.4.1工序基准的选择:
14
3.4.2确定工序尺寸的方法15
3.4.3加工余量的确定16
3.4.4机床的选择17
3.4.5夹具的选择17
3.4.6刀具的选择17
3.4.7量具的选择19
3.4.8冷却液的选择19
3.4.9切削用量的确定19
第四章数控加工程序的编制24
4.1数控加工的特点24
4.2数控编程方法及特点24
4.2.1数控编程的分类24
4.2.2编程零点及坐标系的选择24
4.2.3对刀点的选择24
4.2.4对刀过程24
4.2.5加工路线的确定25
4.3数控加工程序的内容26
4.3.1螺纹的加工方法26
4.3.2椭圆宏程序的分析26
4.3.3车床程序27
总结34
致谢35
参考文献36
前言
随着数控技术的不断发展和其应用领域的不断扩大,数控技术及数控机床在当今机械制造业中起着非常重要的作用。
而现在机械产品的结构,性能,形状和材料的不断的改进,精度不断提高,生产类型由大批量生产向多品种小批量生产转化。
对零件精度和加工质量要求越来越高。
而数控技术是现代化加工设备的基础,又是精密、高可靠性、高效加工技术的支撑。
发展先进制造技术必须以数控技术为基础。
现代数控机床是综合应用了自动控制、计算机、自动检测以及精密机械等高新技术的产物,集成了数控仿真,可以检查出代码的正确性,从而可以提高编程质量,加快编程速度,减少出错率,是典型的机电一体化产品,是完全新型的自动化机床;这显示了其在国家基础工业现代化中所起到的战略性作用,并已成为传统机械制造工业提升改造和实现柔性化、自动化、集成化生产的重要手段和标志。
数控加工技术对国计民生的一些重要行业(汽车、轻工、IT、医疗等)的发展起着越来越重要的作用,因为效率、质量是先进制造技术的主体。
高速、高精加工技术可极大地提高效率,提高产品的档次和质量,缩短生产周期和提高市场竞争能力。
而对于数控加工,无论是手工编程还是自动编程,在编程前都要对所加工的零件进行工艺分析,拟定加工方案,选择合适的刀具,确定切削用量,对一些工艺问题(如对刀点、加工路线等)也需做一些处理。
并在加工过程掌握控制精度的方法,才能够加工出合格的产品。
本文根据数控机床的特点,针对具体的零件,进行工艺方案分析,工艺方案的确定,刀具和切削用量的选择,确定加工顺序和加工路线,数控加工程序编制。
通过整个工艺的过程的制定,充分体现了数控设备在保证加工精度,加工效率,简化工序等方面的优势。
机械加工工艺是实现产品设计,保证产品质量,节约能源,降低消耗的重要手段,是企业进行生产准备,计划调度,加工操作,安全生产,技术检测和健全劳动组织的重要依据,也是企业_上品种、上质量、上水平,加速产品更新,提高经济效益的技术保证。
工艺规程的编制是直接指导产品或零件制造的工艺过程和操作方法的工艺文件,他直接对企业的产品质量、效益、竞争能力起着重要的作用。
机械工业是国民经济各部门的装一备部,国民经济各部门的生产技术水平和经济效益,在很大程度上取决与机械l_业所能提供装备的技术性能、质量和可靠性,因此,机械止业的技术水平和规模是衡量一个国家科技水平和经济实力的重要标志。
近年来,世界各国都把提高产业竞争力和发展技术、抢占未来经济的制高点作为科技发展提出更高的要求,特别是制造技术更加得到了重视。
所以,我们要振兴机械工业,使之成为国民经济的支柱产业。
从而确定机械工业在国民经济中的重要地位,同时也向机械工业提出更高的要求。
第一章零件的分析
1.1零件的结构工艺性分析
图1零件1
图2零件2
对零件图的分析和研究,首先应熟悉零件在产品中的作用、位置、装配关系和工作条件,搞清楚各项技术要求对零件装配质量和使用性能的影响,找出主要的关键的技术要求,然后对零件图样进行分析。
零件的结构工艺性是指所设计的零件在能满足使用要求的前提下制造的可行性和经济性,即所设计的零件结构应便于成形,并且成本低,效率高。
它的涉及面广,因此有必要对零件进行结构工艺性分析,找出技术关键,以便在拟定工艺规程时采用适当的工作措施加以保证。
首先,对零件轮廓各线段进行尺寸分析,看各线段的尺寸是否标注齐全?
是否需要间接计算?
在数控编程中,所有点、线、面的尺寸和位置都是以编程原点为基准的,因此零件图样上最好直接给出坐标尺寸,或尽量以同一基准引注尺寸。
零件1直径方向尺寸的设计基准是轴的中心线,长度方向的尺寸设计基准是轴的左端面。
所以,把编程原点(对刀点)设置在轴的右端面中心处,既便于编程又有利于设计基准、工艺基准、测量基准和编程原点的统一。
其次,构成零件轮廓的几何元素(点、线、面)条件(如相切、相交、垂直和平行)是数控编程的重要依据。
手工编程时要计算构成零件轮廓的每一个节点坐标,因此零件图应当完整地表达构成零件轮廓的几何元素。
图1中,有两处点的坐标没有直接标出,需要间接计算出来。
零件1左端X坐标可以用椭圆方程计算出来。
用函数公式计算节点的坐标值很麻烦,更简便的方法是用CAD画图,然后测量出点的坐标值。
1.1.1零件的形状分析
(1)零件的形状分析
轴系组合件较为复杂,从外形上看件一右端是不完整的球端面。
外阶梯形圆柱表面及圆柱表面质量,左端有部分椭圆圆弧,右端有梯形圆柱内孔及圆柱内孔,左端内部为螺纹及退刀槽。
件2是椭圆外表面,右端外螺纹加工,左端内孔及凹球面。
同时两个零件螺纹配合松紧适中,组合件的球面间接触面积应大于80%。
(2)零件的尺寸分析
对数控加工来说,最倾向与以同一基准引注尺寸或直接给坐标尺寸,这就是坐标标注法。
这种标注法,即便于编程,也便于尺寸之间的相互协调,保证设计、定位、检测基准与编程原点设置的一致性方面带来很大方便。
由于零件设计人员往往在尺寸标注中较多的考虑装配等使用特性要求。
而不得不采取局部分散的标注方法,这样会给工序安排与数控加工带来很多不便,事实上,由于数控加工精度及重复定位精度都很高,不会因产生较大的累计误差而破坏使用特性,因而改变局部的分散标注法为集中引注或坐标式尺寸、标注是完全可行的。
零件一总长度为60mm,上下偏差均为0.033,Φ23的内孔上偏差为0.21,下偏差为0。
Φ56外圆的上偏差为0,下偏差为-0.021。
最左端内孔直径为36,上偏差为0.021,下偏差为0。
零件二总长度为60mm,上下偏差均为0.033,配合槽的深度为5上偏差为0.021下偏差为0,槽的位置为直径36上偏差为-0.1下偏差为-0.2,另一端位置为上偏差0.2下偏差0.1,椭圆短轴58长轴100。
1.1.2零件的技术要求分析
零件的技术要求主要包括尺寸精度、形状精度、位置精度、表面粗糙度及热表处理要求等。
进行零件技术要求分析,主要是分析这些技术要求的合理性以及实现的可能性,重点分析重要表面和部位的加工精度和技术要求,为制定合理的加工方案做好准备。
零件图纸上标注的技术要求:
1)球接触面积大于等于80%。
2)未注倒角C1。
3)椭圆圆弧过渡光滑。
4)未注尺寸公差按IT14加工和效验。
5)锐边倒钝。
1.1.3零件的加工表面的分析
从零件图可以看出轴系零件的主要加工表面是:
(1)φ56的圆柱:
它的表面粗糙度是Ra1.6,而且其轴心线是设计基准。
(2)M30X1.5-6H的螺纹:
此螺纹是一个标准螺纹,虽然没有特殊要求,但它在配合时起传递扭矩的作用,故其配合精度要求高。
(3)椭圆:
表面粗糙度Ra1.6,轴心线是设计基准。
(4)球面:
尺寸以确定,表面粗糙度Ra3.2球心是设计基准.
通过以上的分析可知,零件的结构较为复杂,其难点在于椭圆外轮廓的加工及宏程序的应用、内外螺纹的加工和球面的加工。
所以应当认真对零件的加工工艺进行仔细分析否则废品率会相对较高。
1.2零件的材料分析
零件材料的选用是非常重要的,选材不当导制零件不能满足使用要求,过早损伤和破坏产生不良影响或经济效益差等。
机械零件选材的一般原则是:
首先满足使用性能的要求,同时兼顾工艺性、经济性和环保性。
对于轴类零件的选材应具有以下几点要求:
(1)优良的综合力学性能,即要求有高的强度和韧性,以防止由于过载和冲击而引起的变形和断裂。
(2)高的疲劳极限,防止零件疲劳断裂。
(3)良好的耐磨性。
(4)在特殊条件工作时,还应有特殊要求。
本零件的材料是45号钢,它属于低淬透性合金调质钢,其化学成分是:
碳的含量0.37%~0.45%,锰的含量0.17%~0.37%,铬的含量0.8%~1.1%,硫的含量0.5%~0.8%,其中碳含量过高、过低均不能满足经调质后获得良好综合力学性能的要求,主加元素为铬,在配以硫、锰等合金元素,其作用是提高淬透性,强化铁素体和细化晶粒,因此,此钢的热处理变形小,废品率低,因而降低了工艺成本。
其热处理特点是:
当原始组织为珠光体温回火工艺,即调质处理工艺,调质处理可使材料具有良好的综合力学性能。
材料长度的选择:
件一取φ60×64,件二取φ60×64的棒料
第二章毛坯的设计
2.1确定零件的生产类型和生产纲领
生产类型是指企业(或车间,班组,工段,工作地)生产专业化程度的分类,一般分为大批量生产,中批生产和单件小批生产三种类型。
它可根据生产纲领和产品及零件的特征或工作地每月担负的工序数来进行具体的划分。
生产纲领是指在计划期内应当生产的产品产量和进度计划。
计划期常定为一年,所以生产纲领也称年产量。
零件的生产纲领要计入备品和废品的数量,其计算式为:
N=Q*n(1+α)(1+β)
N—零件的年产量(件年)
Q—产品的年产量(台年)
n—每台产品中,该零件的数量(件台)
α—备品的百分率
β—废品的百分率
其中Q=2000n=2α=5%β=2%所以=4000(1+5%)(1+2%)=2142件年)
=2000(1+5%)(1+2%)=1071件年。
由上所述,查《机械制造工艺学》中表1-3知该零件为中批生产。
2.2确定零件毛坯的制造形式
毛坯是根据零件所要求的形状、工艺尺寸等方面而制成的供进一步加工使用的生产对象。
毛坯种类的选择不仅影响着毛坯制造的工艺装备及制造费用,对零件的机械加工工艺装备及工具的消耗,工时定额的计算有很大影响。
2.2.1毛坯的种类
常用的毛坯种类有:
冷压件、锻件、焊接件、型材、铸件等。
1)冷压件:
适用于形状复杂的板料零件,大多用于中小零件的大批量生产。
2)锻件:
适用与零件强度较高,形状较简单的零件。
尺寸大的零件因受设备限制,故一般用自由锻;中、小型零件可选模锻;形状复杂的刚质零件不宜用自由锻。
3)焊接件:
对于大件来说,焊接件简单方便,特别是单件小批生产可大大缩短生产周期,但焊接后变形大,需经时效处理。
4)型材:
热轧型材的尺寸较大、精度低,多用作一般零件的毛坯;冷轧型材尺寸较小、精度较高,多用于毛坯精度要求较高的中小零件,适用于自动机床加工。
5)铸件:
适用于形状复杂的毛坯。
2.2.2毛坯种类的选择
选择毛坯种类需考虑的因素有以下几点:
1)根据图纸规定的材料及机械性能选择毛坯。
2)根据零件的功能选择毛坯。
3)根据生产类型选择毛坯。
4)根据具体生产条件选择毛坯。
根据以上分析应当选择型材作为毛坯。
2.2.3毛坯的形状和尺寸的选择
确定毛坯的形状与尺寸的步骤是:
首先选取毛坯加工余量和毛坯公差,其次将毛坯加工余量叠加在零件的相应加工表面上,从而计算出毛坯尺寸,最后标注毛坯尺寸与公差。
其总的要求是:
减少“肥头大耳”,实现少屑或无屑加工。
因此,毛坯形状应力求接近成品形状,以减少机械加工的劳动量。
本零件的大部分加工表面是回转体表面,根据本零件的生产纲领,年生产数量,经济价值及复杂程度,另外本零件为轴类零件,考虑其复杂程度,所以本零件毛坯为棒料。
因为棒料的经济性好,加工余量小而且成本较低。
根据本零件的结构特征和尺寸要求及考虑到经济性,所以两零件毛坯圆棒料的尺寸均为φ60mm×64mm。
第三章零件机械加工工艺规程的设计
机械加工工艺规程是规定产品或零部件工艺过程和操作方法等的工艺文件,它是指导生产的主要技术文献,是组织和管理生产的基本依据,是新建和扩建工厂或车间的基本资料,是进行技术交流的重要手段。
3.1定位基准的选择
在制订零件的加工工艺规程时,正确地选择工件的基准有着极其重要的意义。
基准选择的好坏不仅影响零件的加工位置精度,而且对零件各表面的加工顺序也有较大的影响。
基准有粗基准与精基准之分。
选择定位基准时是从保证工件精度要求出发的,因而分析定位基准选择的顺序就应从粗基准到精基准。
3.1.1粗基准的选择
粗基准选择的要求应能保证加工面与非加工面之间的位置要求及合理分配加工表面的余量,同时,要为后续工序提供精基准。
(1)为了保证加工面与非加工面之间的位置要求,应选非加工面作为粗基准。
(2)粗基准应避免重复使用,在同一尺寸方向上,通常只允许使用一次。
(3)合理分配各加工面的加工余量。
(4)选作粗基准的表面应平整光洁,要避开锻造飞边和铸造浇冒口,分型面,毛刺等缺陷,以保证定位准确、夹紧可靠。
由于本工件毛坯为棒料,所以采用φ60棒料的外圆柱面为粗基准,车削零件一的右端外圆柱面,再以车削后的圆柱面为基准,车削零件的左端。
车削零件二采用φ60棒料的外圆柱面为粗基准,车削零件二的左端外圆,再以车削后的圆柱面为基准,车削零件的右端。
由以上分析可知本零件采用两种基准原则,一是基准重合原则,它是以零件的轴心线为定位基准也是设计基准,对零件的外圆、内孔、槽以及螺纹等表面进行切削加工;另一种是基准统一原则,它是多个加工表面都以一个基准作基准面加工定位的。
3.1.2精基准的选择
1)互为基准原则:
为了使加工面间有较高的位置精度,又为了使其加工余量小而均匀采取此原则。
2)自为基准原则:
当某些表面精加工要求加工余量小而均匀时,选择加工表面本身作为定位基准,用于提高加工面本身的精度。
3)基准统一原则:
位置精度要求较高的某些表面加工时尽可能选用同一定位基准,这样有利于保证各加工表面的位置精度。
4)基准重合原则:
就是尽可能选用设计基准作为定位基准,这样可以避免定位基准与设计基准不重合而引起定位误差。
5)保证工件定位准确、夹紧可靠、操作方便的原则
综上所述加工零件一右端时应以粗车的左端为定位基准,加工右端时以左端为精基准。
零件二的右端加工以粗车的右端为精基准,以右端面为基准,加工零件的螺纹倒角,车槽,将零件二与零件一装配之后车削零件二的外椭圆轮廓,然后以φ55.5的外椭圆轮廓的左端为基准车削球面及加工内孔。
3.2零件表面加工方法的选择
零件表面的加工应根据这些表面的加工要求和零件的结构特点及材料性质等因素,而选用相应的加工方法。
在选择某一表面的加工方法时,一般总是首先选定它的最终加工方法,然后再逐一选定各有关前道工序的加工方法。
加工方法选择的原则如下:
(1)所选加工方法应考虑每种加工方法的经济加工精度范围要与加工表面的精度要求和表面粗糙度要求相适应。
(2)所选加工方法能够确保加工面的几何形状精度,相互位置精度的要求。
(3)所选加工方法要与零件材料的可加工性相适应。
(4)加工方法要与生产类型相适应。
(5)所选加工方法要与企业现有设备和工人技术水平相适应。
通过以上原则,本零件各主要表面加工方法为:
1)零件1、2的外圆Ra1.6,精度应当在IT8-IT7之间所以应当采用粗车→半精车→精车。
2)零件1的内孔按IT14进行加工,采用的加工方法粗镗→半精镗。
3)零件1的内螺纹和零件2的外螺纹Ra1.6采用粗车→半精车→精车的加工方法。
4)零件2的内孔采用Ra1.6采用粗镗→半精镗→精镗的加工方法。
3.2.1球面加工方法及误差补偿的选择
(1)车刀分析
车刀刀尖不可能是一个绝对的点,而且为了保证得到一定的加工光洁度,常磨成略带有圆角。
这在切削直线时,由于刀尖刃面上的切削点位置在切削过程中角度保持不变,如不考虑磨损,可以认为刀尖几何形状对切削精度没有任何影响,切削试验也证实这一点。
但是切削圆弧时,情况就不同了,切削过程中车刀刃面上的切削点位置将沿着加工零件的轮廓变动。
如图3-1a示,车刀在起始位置时,刀尖的A点与零件球面相切。
当A沿着圆心O、半径为R的圆移动到C时,刀尖所切出的实际轮廓已不在圆上,而是由刀尖的b点切人到零件上的B位置。
这样实际加工出来的零件轮廓与所要求的球面,将存在一个月牙状误差,如图3-1b。
这个误差的大小与刀尖的几何形状有关。
ab
图3-1切削过程中切削点位置的变化对零件形状的影响
(2)误差分析及补偿方法
如图3-2所示,在加工凸球面时,为了消除由刀尖圆弧半径r产生误差,我们在编制数控车床的程序时,将加工球面的圆心从移至,,球面半径相应相应增大为(R+r)。
这时计算机对圆心为,半径为(R+r)的圆弧进行插补运算。
这样切削得到的实际轮廓为曲线为。
其中AC段即我们所要求的球面。
在理想情况下,AC与要求的球面没有误差。
注意这时加工长度L如果计算y方向,则应取L=R十r。
加工圆弧AC,刀具可以有二种进给方向。
除了上述从A走逆圆到C外,亦可从C走顺
圆到才,如图3-3所示。
这时误差的形成及补偿方法与上述走逆圆时是一样的,但补偿方向不同,应向