焦炉集气管压力控制系统研究样本.docx
《焦炉集气管压力控制系统研究样本.docx》由会员分享,可在线阅读,更多相关《焦炉集气管压力控制系统研究样本.docx(11页珍藏版)》请在冰豆网上搜索。
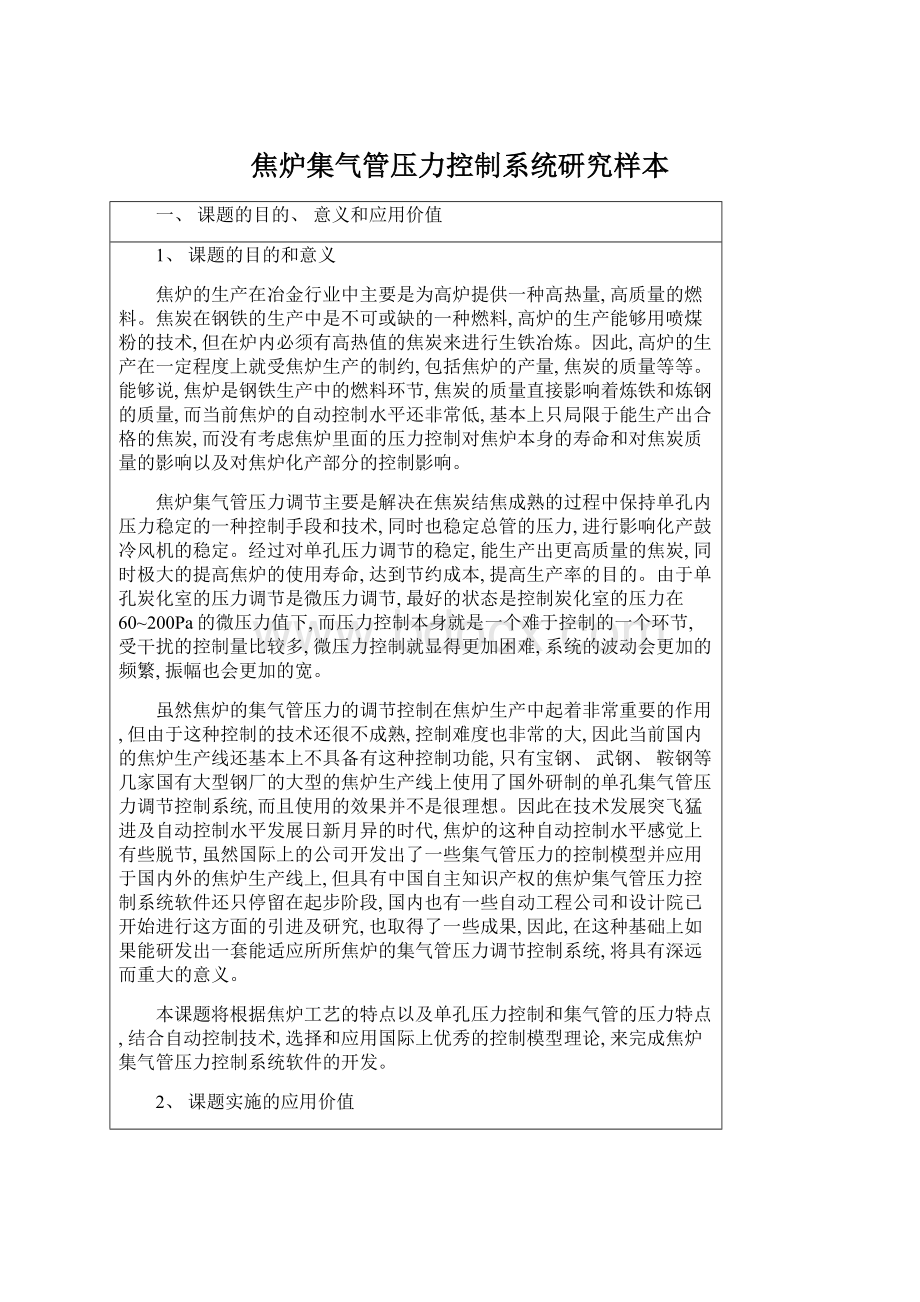
焦炉集气管压力控制系统研究样本
一、课题的目的、意义和应用价值
1、课题的目的和意义
焦炉的生产在冶金行业中主要是为高炉提供一种高热量,高质量的燃料。
焦炭在钢铁的生产中是不可或缺的一种燃料,高炉的生产能够用喷煤粉的技术,但在炉内必须有高热值的焦炭来进行生铁冶炼。
因此,高炉的生产在一定程度上就受焦炉生产的制约,包括焦炉的产量,焦炭的质量等等。
能够说,焦炉是钢铁生产中的燃料环节,焦炭的质量直接影响着炼铁和炼钢的质量,而当前焦炉的自动控制水平还非常低,基本上只局限于能生产出合格的焦炭,而没有考虑焦炉里面的压力控制对焦炉本身的寿命和对焦炭质量的影响以及对焦炉化产部分的控制影响。
焦炉集气管压力调节主要是解决在焦炭结焦成熟的过程中保持单孔内压力稳定的一种控制手段和技术,同时也稳定总管的压力,进行影响化产鼓冷风机的稳定。
经过对单孔压力调节的稳定,能生产出更高质量的焦炭,同时极大的提高焦炉的使用寿命,达到节约成本,提高生产率的目的。
由于单孔炭化室的压力调节是微压力调节,最好的状态是控制炭化室的压力在60~200Pa的微压力值下,而压力控制本身就是一个难于控制的一个环节,受干扰的控制量比较多,微压力控制就显得更加困难,系统的波动会更加的频繁,振幅也会更加的宽。
虽然焦炉的集气管压力的调节控制在焦炉生产中起着非常重要的作用,但由于这种控制的技术还很不成熟,控制难度也非常的大,因此当前国内的焦炉生产线还基本上不具备有这种控制功能,只有宝钢、武钢、鞍钢等几家国有大型钢厂的大型的焦炉生产线上使用了国外研制的单孔集气管压力调节控制系统,而且使用的效果并不是很理想。
因此在技术发展突飞猛进及自动控制水平发展日新月异的时代,焦炉的这种自动控制水平感觉上有些脱节,虽然国际上的公司开发出了一些集气管压力的控制模型并应用于国内外的焦炉生产线上,但具有中国自主知识产权的焦炉集气管压力控制系统软件还只停留在起步阶段,国内也有一些自动工程公司和设计院已开始进行这方面的引进及研究,也取得了一些成果,因此,在这种基础上如果能研发出一套能适应所所焦炉的集气管压力调节控制系统,将具有深远而重大的意义。
本课题将根据焦炉工艺的特点以及单孔压力控制和集气管的压力特点,结合自动控制技术,选择和应用国际上优秀的控制模型理论,来完成焦炉集气管压力控制系统软件的开发。
2、课题实施的应用价值
本课题中焦炉集气管压力控制系统的应用价值是延长焦炉的使用寿命以及提高焦炭的质量指标,极大的减少对环境的污染,改进鼓冷风机的控制能力:
1、提高焦炉的使用寿命:
由于在整个结焦过程中,炉内的压力是不一样的,刚装煤时,产生的煤气最大,因此这个时间的压力也最大,在结焦过程中直到结焦成熟,压力就会慢慢变小,直到基本上没有压力,如果不能保持炭化室的压力稳定,而焦炉会一天天的处在不断变化的压力中,对焦炉的寿命会产生很大的影响。
2、提高焦炭的质量:
如果单孔炭化室的压力维持一定程度的稳定,将大大的提升焦炭的质量,使焦炭更紧密,而且提高焦炭的热值。
3、减少对环境的污染:
在整个炼焦过程中,炭化室的压力是不断变化的。
如果压力在炼焦过程中不能调节,则在装煤及结焦阶段将会导致大量的污染有毒烟气外溢,不但影响设备,而且也会造成对大气的污染以及有可能会影响到生产人员的安全,因此对炭化室的压力调节就显得非常有必要,而且很关键。
4、稳定集气管的压力调节:
由于采用单孔炭化室的压力调节,相当于是对每一孔焦炉在不同的阶段都实再压力检测及控制,从而使集气总管的压力更加的稳定,使鼓冷风机的控制更加的稳定,降低了操作人员的操作强度。
二、课题所属领域国内外研究现状和发展趋势
1、炭化室集气管压力控制的工艺流程
集气管的压力控制是焦炉生产过程中的一道工序,所有的焦炉生产都将经过一套集气管设备,再经过鼓风机的抽风,把焦炉内的烟气从焦炉炭化室抽到化产工段。
焦炉结焦过程本身就是一种动态的过程,从装煤阶段开始,在焦炉的炭化室内就开始燃烧并进行结焦,在结焦过程中将会产生大量的烟尘及有毒的二氧化碳、一氧化炭、氢气等有毒及可燃烧的气体,在整个结焦过程中,炭化室的压力也是不稳定的,如果只是经过鼓冷风机的抽风,只调节集气管总管的压力,则针对具体的炭化室的压力就起不到调节的功能,因为每一孔的炭化室内的烟气排出是有一定的设计的,在产生大烟气的阶段,由于排出系统的原因,会使压力升高很大,而且针对炭化室的控制工艺要求来说,把炭化室的压力控制在微正压力状态是最有利于焦炉的生产的。
因此从整个焦炉工艺来看,对集气管的压力控制是起到改进焦炉生产,提高焦炭质量减少对环境污染及减少对人员伤害的一种工艺控制。
从工艺角度来看并不复杂,从检测方面来看也不复杂,但从控制设备的设计及控制来看,由于是对压力的微差压控制,因此对控制程序及精度都要求很高。
焦炉集气管的压力控制工艺主要由以下方面组成:
1.1、炭化室内的信号检测。
炭化室内的压力由于工艺的制约,并不能直接经过检测设备进行检测,因为炭化室内都是燃烧的红焦炭,而且空间也不一定,如果直接想经过压力仪表来检测的话,将及大的提高成本以及维护的难度,因此我们在工艺允许的情况下,选择在炭化室的上升管处来进行对烟气的引压检测,同时需要检测这个引压点的温度值。
1.2、上升管的烟气冷却。
由于从炭化室出来的烟气都是高温有毒而且带有很多灰尘颗粒的气体,因此在上升管处安装了一套工艺设备,这套工艺设备起到把烟气冷却,同时除掉大部分烟气中的灰尘的目的,这套设备是经过喷洒氨水来实现的,氨水的喷洒能够不进行控制流量控制,只要生产就能够一直喷淋,同时增加了防堵措施,也就是增加一路喷淋系统,进行轮流喷淋。
1.3、工艺控制设备。
喷氨水工段是整个焦炉集气管压力控制的重要一个环节,在焦炉集气管压力控制中,就是经过控制在上升桥断部分的喷淋出来的氨水的高度来进行烟气流量的大小,进而进行对炭化室压力控制的调节,这部分是集气管压力控制的关键设备,主要由一套PLC控制的气缸设备组成,这套气缸设备包括气源的流量控制,同时对气缸的行程进行回路控制,也需要采集气缸的行程量,包括气缸的行程与氨水高度位置的对应关系,这部分是我们程序控制的关键点,当然,这一套设备是机械工艺提供的特殊设备,也是为焦炉集气管压力控制而开发出来的特殊机械设备,在其它焦炉中也还没有用到。
1.4、控制描述。
由于炭化室产生的烟气是随结焦时间变化而变化的,但在初始装煤阶段将产生最大的煤气量,而在炼焦成熟阶段将基本上不产生煤气,因此,想要对炭化室的压力进行调节,使炭化室的压力保持在一个微正压力状态,就需要对产生的煤气进行按量排放,从而经过煤气流量的排出来控制炭化室内的煤气量,进而达到调节压力的目的,排出煤气的主要动力可来自鼓冷风机的抽几力度,但如果在煤气产生量很小的后期阶段,同样开度的情况下,就将会对炭化室产生一个负压力,含氧的空气就将进入到炭化室,对焦炭产生非常不利的影响,为此就需要建立一个对煤气流量的调节。
根据工艺的要求,在装煤开始炼焦阶段,控制氨水高度的气缸实行全开控制,使炭化室内的煤气能尽快的排出炭化室,以降低炭化室的压力,而在结焦后期,气缸生程达到最到,全关煤气排出口,保持炭化室内的微正压力,只在这二个阶段的正常结焦阶段进行氨水的高度控制,因此,经过控制气缸的行程就能够实现炭化室压力的控制。
2、焦炉自动控制技术简介
随着自动化技术的发展和计算机技术的进步,大量的计算机控制应用到了钢铁生产线中,当然在焦炉的生产控制中,也引入了计算机控制技术。
在焦炉自动控制中,一般都会使用智能仪表进行数据采集,再经过PLC来计算及处理采集进来的数据,并根据制作相关的程序,控制数据的输出,控制现场设备的精确运行,并把相关的数据送到计算机终端,也就是HMI上显示,同时经过HMI能够直接把生产指令下到PLC,再经过程序的运行和执行,把指令转化为数据入信号经过输出模块送到现场的执行设备上,进而实现调节的目的。
当前在冶金自动控制技术广泛应用的生产线上,能够提高工厂设备的装备水平,而且节约能源,促进生产的柔性化和集成化,提高劳动生产率以及提高产品的产量和质量。
焦炉集气管压力控制的目的是为了提高产品的质量,减少环境污染,提高操作人员的安全,并延长焦炉的使用寿命而开发的一套控制系统。
在新开发的这套焦炉集气管压力控制系统中使用的自动控制技术主要有以下几个方面。
2.1、检测技术
随着检测技术、自动化技术以及计算机技术的不断发展,越来越多的检测技术应用到冶金生产线的自动控制中。
跟随着检测技术的应用之一就是检测仪表的应用,在此套控制系统中,由于信号的采集并不复杂,主要是解决微压力的控制,同时对信号进行补偿,因此主要采集的信号只有压力、温度和气缸的行程值。
温度的采集及处理相正确简单;对微压力的采集需要进行引压处理,同时根据差压原理来进行检测采集;由于气缸的行程是一个相对微小的量,控制的效果完全体现在对气缸行程的控制上,因此气缸行程的精度也就决定了控制的效果,因此对气缸行程的检测采用了磁位移检测技术。
根据控制理论,对生产过程中所需的各个参数必须进行准确而又及时的测量,才能使各种控制技术和方法得以实施。
2.2、自动化技术
①模型研究:
本控制系统只提供了一个模型——微压力控制模型。
这个模型包括三个部分,一个就是刚开始装煤时,系统的气缸要全关,使氨水的位置到达最低位置,也就是把整个上升管全开,使炭化室的煤气全部尽快的经过鼓冷风机产生的负压力,抽到集气管总管上,随其它炭化室出来的煤气一起送到化产工段;第二个部分就是结焦的中间段,这也是这个控制系统的核心阶段,要把炭化室的压力值稳定在微正压力值上,控制的来源就是上升管桥处的压力值,控制的设备就是气缸行程,行程的大小影响着氨水的高度值,模型中需要解决氨水高度与气缸行程的关系,建立一套对应模型来满足这方面的控制要求;第三个部分就是在结焦的后期,如果在炭化室产生的煤气量很小的情况下,需要保持炭化室的微正压力,因此需要全开气缸行程,进而经过氨水实现全封闭,不让煤气抽出到集气总管上。
②控制技术:
从控制技术角度来看,本控制系统相对来说不是那么复杂,所涉及的工艺也不复杂,对信号的处理也相对简单,滞后性也较小,但由于炭化室的煤气产生是一个不定性的过程,而且并不是连续线性的,是一会大,一会小,同时也会有压力突变的过程,而且在整个结焦段是不允许间断工作的,因此需要确保这个控制系统具有长期运行的连续性和高可靠性,同时要求系统在运行过程中要能实时地采集数据,处理数据,在很短的时间内完成推理和决策,所需的数据都需要在线采集。
根据这种工艺情况,自动控制采用PLC或DCS加中央控制计算机的模型来建立控制系统。
③人工智能技术的应用:
由于控制系统并不复杂,只是控制精度要求高,同时对参数的变化也是随炭化室的压力而随机变化的,突变性较大,因此在人工智能技术上采用可自整定的模型PID控制技术。
在建立控制模型时,就分三个阶段来建立系统模型,因此在三个阶段有不同的参数值,能够在PLC程序中固定,也能够经过HMI画面来在线设定,这点能够根据现场的调试情况而定。
由于主要控制阶段是在结焦的中间段,因此模型的重点也体现在这个阶段,因此这部分的控制参数并不是固定的,需要根据炭化室的压力来进行调整,而且每一个炭化室的压力参数也是不相同的,同时相邻二个炭化室之间的压力也会有一定的影响,需要把这个影响作为干扰因素引入并量化到控制模型中。
2.3、控制系统
国外六十年代初期就开始在焦炉生产过程中采用电子计算机。
初期仅作为检测、报警、记录、打印等,后来逐步用作开环和闭环控制。
当前焦炉的生产控制都采用PLC或DCS系统和微型计算机相结合、计算机与常规仪表相结合、控制设备与通讯设备相结合的最优控制与管理系统。
近年来由于检测装置的不断完善,大规模集成电路及计算技术的飞跃发展,致使计算机控制功能日臻完善,可靠性不断提高以及价格不断降低,使焦炉生产中计算机的应用日趋广泛。
这对提高产品质量,减轻劳动强度等起了较大的作用。
国外钢铁工业计算机控制系统的发展基本经历了三个阶段:
在1965年前为第一阶段,各控制回路采用模拟调节器进行控制,计算机是用来给出调节器的设定值。
1970年前后为第二阶段,使用一台直接数字控制计算机及程序控制器控制,这样要求较高的可靠性,因此要有备用系统。
1975年以后为第三阶段,由微型计算机控制几个回路,代替一个多回路的直接数字控制计算机,这样使控制功能分散,可靠性较高。
进入上世纪90年代开始,大量的控制计算机、PLC、DCS应用到钢铁生产线上,极大的改进了钢铁生产的自动控制,焦炉生产线上也全部采用PLC或DCS加工业控制计算机的控制模式,使钢铁工业的自动控制水平跃上了一个全新的台阶。
由于一般的焦炉都包括几十个炭化室,俗称孔,因此,不论是大型焦炉还是小型焦炉,虽然每一孔的控制量不多,控制回路也不多,但对于整个焦炉控制来说,就是一套相对大型的控制系统,因此一般情况下都采用大型的PLC或DCS来控制,特别是在资金允许的情况下,能够采用冗余的DCS来搭建控制系统就更加完善。
3、焦炉集气管压力控制系统的发展与研究
从冶金工业的自动控制水平的发展也能够看出焦炉在自动控制方面的发展历程。
从单一回路的控制到计算机集成系统的控制,到当前广泛应用的专家系统、人工智能,大量的数学模型、控制模型应用到了焦炉生产自动控制中,因此针对这一套集气管的压力控制系统,也不例外的基本上应用以上的控制技术来实现。
当前在焦炉上针对集气管压力调节应用方面主要分为三种情况:
(1)基本上不对集气管压力进行调节,只是经过后边化产工段的鼓冷风机的速度来进行调节集气管的总管压力,而且这种调节也只局限于经过升降鼓冷风机的运行速度来进行调节,也并不存在精确的回路控制。
这种控制方式比较适合对每一孔焦炭生产的起始和结束阶段,在炼焦过程中基本上起不到调节集气管总管以及每一孔炭化室的压力的作用。
但由于焦炉的自动控制水平相应的滞后,当前焦炉使用的控制系统还大部分是这种控制系统和控制模式。
(2)由国外公司如:
伍德公司开发的PROVEN系统是当前焦炉集气管压力调节应用最广泛的一套系统。
PROVEN系统能够实现对每一孔炭化室的压力进行调节,而且都是进行微正压力控制调节,经过机械设备的改造,配合精密的电气仪表自动控制系统来实现对单孔集气管压力的调节,应用效果还能够。
PROVEN控制系统针对集气管系统设有可调节单个炭化室顶部压力的装置使集气管压力保持在-300—-350Pa。
上升管水封盖、桥管水封阀的开闭以及PROven压力调节装置采用气动控制系统是实现本系统的特点之一,炭化室压力由桥管上测压元件测量,并传送到控制系统。
在结焦时间内,荒煤气初期压力约为200Pa,逸出压力为1200Pa,达到最大,结焦末期,压力最小。
炭化室压力是经过机械设备”皇冠管”来进行调节的,推焦时,炉门、上升管打开,炭化室需要与集气管隔绝,以免空气吸入集气管,要求用冲洗液注入固定杯,以关闭”皇冠”管中的沟槽。
装煤时,荒煤气发生量达到最高峰值,集气管要有足够的能力使煤气从炭化室中导出。
溢流调节装置彻底打开到最上部,固定杯中的液体全部排空。
此时荒煤气通道的阻力最小,集气管负压使得荒煤气从上升管、桥管、皇冠管到固定杯,一直到顺利导入集气管。
可是这种控制系统只适合应用于大型焦炉项目(6.3m以上的焦炉),对小型焦炉还从来没有采用过这套控制系统。
(3)由于国内外还有大量的小于6.3m的焦炉,这部分的焦炉的集气管压力调节基本上就是采用的第一种方法,对单孔炭化室的压力调节基本上就没有。
近期鞍山焦耐院也在开发一种类似PROVEN设备的控制系统来实现对单孔炭化室的压力调节,也在开始在焦炉上开始应用,但效果并不是很理想。
这套设备和控制方法与国外的PROVEN非常类似,不论上机械设备还是电气仪表自动设备及控制,基本上都源于PROVEN设备,但对这套设备进行了改进,在使用初期能取得非常好的效果。
三、课题现有工作基础
当前,焦炉工艺流程已相对比较成熟,对集气管压力调节的工艺研究及现场情况也都有相当的了解,对采用的控制系统也有非常成熟的经验,而且对焦炉生产以及集气管的压力调节都进行了前期的研究,掌握了焦炉自动控制方面的重要生产控制资料。
焦炉集气管压力控制系统主要有以下几个方面:
●信号的采集:
对单孔炭化室的压力控制而言,信号并不多,只有压力、温度、气缸行程等几个模拟量,以及一部分的开关量信号,但针对一个焦炉几十孔来说,信号总数还是相当多的,对本控制系统来说,主要是做一个回路控制。
确保每孔炭化室的压力能在生产过程中保持在微正压力状态。
●配合机械设备的对应系统:
由于在机械设备中进行对焦炉烟气的水封操作,因此从工艺角度来考虑不适合对水封的高度进行直接的测量,而从这套控制系统的控制角度来考虑,最好的控制量就是水封的高度值,因此需要与机械设备相配合,取得水封高度与烟气流量的对应关系,以及水封高度与气缸行程的对应关系,经过测量气缸的行程值来体现水封高度,最终得到烟气流量的控制,进而实现压力的调节。
●炭化室的压力控制:
单孔炭化室的压力需要保持在微正压力状态,这点与PROVEN系统有一些不同,因此,针对压力值很小,变动范围又很大的工艺状况下,需要采用精密的仪表设备以及完善的控制手段来实现微压力的稳定调节,否则不但调整不好压力值,而且会造成系统共振,并对焦炉总管的压力调节造成影响。
由于当前的焦炉的生产控制过程中大都使用PLC或DCS及上位计算机的控制模式,因此不同的控制设备之间是有着紧密联系的,需要在不同的CPU之间进行数据交换,根据项目的不同,客户可能会提出采用冗余的DCS控制系统。
在本控制系统中计划采用冗余的DCS来实现本系统的控制,确保系统的稳定,从而保证生产的稳定。
公司也具有了对冗余系统的项目经验,掌握了冗余DCS的开发及调试能力。
总体来讲,公司已具备本课题研发的基础和条件,在课题的应用方面也积累了一定的经验。
四、课题实施目标及考核指标
1、课题实施目标
本课题实施目标包括以下几个方面:
●焦炉集气管压力控制的方案设计
在方案设计方面,由于这套控制系统是跟机械设备相紧密结合的,因此需要针对机械设备的情况来制定相关的方案设计,也就是说,在机械设备的设计时,就能够加入自动控制的设计思路,在自动控制可行的基础上来考虑机械设备的设计及加工制造。
针对自动控制的设计而言,由于控制的量并不多,因此回路控制也不多,考虑到对控制的精度要求特别高,因此需要寻找一套适合工艺要求的控制设备,比如气缸的控制,行程的检测。
由于是微压力控制,这方面在方案设计时就需要考虑到。
另一方面就是现场的环境温度,由于在焦炉上升管段是高温段,而且管道内还存在喷火燃烧的情况,这些都需要的方案设计时进行考虑。
根据焦炉生产工艺的要求以及集气管压力调节的复杂性、时变性和控制目标的具体要求,计划采用一级计算机控制方案并在控制系统中加入模糊控制及数学模型,即Ll级基础自动化控制及HMI上进行数学模型制作的方式,并预留与L2级过程自动化控制的硬件通讯和软件接口。
系统采用以太网将L1级的电气控制站、仪表控制站、人机接口操作站、打印机等设备连接起来,各设备之间经过交换机相连接进行网络通讯,实现数据交换共享。
经过L1级负责工艺过程及设备状态的实时数据采集处理,完成各工艺过程及设备状态的画面显示及故障报警处理,并根据操作人员的操作指令。
●焦炉的数学模型研究及创新
当前在焦炉的集气管压力控制中还很少使用数学模型,因此本控制系统的研究是着重以经过L1级控制系统来完成信号的采集和处理,并在L1级控制系统中完成数学模型的计算,并经过自整定模拟PID的建立来调节集气管的压力。
由于本控制系统的出发思路是对小型焦炉的集气管压力进行调节,当前在这方面还没有控制系统的应用,因此希望经过在L1级控制系统中能完成对微压力系统的控制。
2、课题考核指标
1)焦炉集气管压力控制系统能实现过程参数的集中显示和管理,在现场的终端能提供友好的人机界面,包括工艺流程模拟、参数报警、趋势曲线等模块,实现数据的集成,方便人工的操作,使工人对现场设备运行情况有更加直观、准确的了解。
2)能够在整个结焦阶段,特别是在装煤结束到出焦之前的阶段把每一孔炭化室内的压力都保持在一定的微正压力状态。
3)经过此系统的应用,能够提高焦炭的质量,能够经过化验或高炉反馈回来的情况来反映焦炭的质量情况。
4)减少对环境的污染。
也就是在应用了这个控制系统后,从焦炉冒煤气烟尘的可能性减少。
5)提高对集气管总管的压力调节能力,使后续工段的鼓风机的控制更加稳定,能够经过鼓冷风机的速度调节来反映这个效果。
五、主要研究内容
1、主要研究开发内容
研究内容要解决的问题:
①根据焦炉的生产情况及集气管压力调节的情况,分析并研究确定一种控制设备来实现对单孔炭化室的压力调节。
②根据制定并开发出的机械设备,配套建立一套控制系统来满足机械设备的运行要求,进而满足焦炉集气管压力调节要求。
③在工艺提出的集气管压力的条件下,经过设计建立起来的控制系统,编程相关的模糊控制程序来实现对每一孔炭化室的微正压力调节。
④在HMI上制作一套可操作运行的画面来满足对集气管压力调节的参数设定及各过程参数的显示,并提供相关的报警及数据曲线。
2、关键技术
2.1信号处理
由于控制系统的信号来源是焦炉的烟气管道中的微压力,压力波动范围在焦炉的生产过程中原来就变化很大,而工艺要求的是在每一孔炭化室中的压力值要保持在一个微正压力的范围内,因此对压力信号的采集就显得特别重要。
从安装位置的选择到仪表类型的选择,到对压力信号的处理都很关键。
在本控制系统,准备采用对模拟量信号的量化程序来进行对信号的处理,对信号进行放大操作,这样只要有一点的变动,对控制程序来说也能够准确的进行反应,这类信号包括压力值和气缸的行程值。
2.2上升管的温度
由于对炭化室的压力直接测量不太合适,工艺不允许直接进行压力测量,从而把压力测量安装到上升桥管中,这样把温度值的测量也放在上升桥管段。
温度测量的目的是对压力进行修正,因为在不同的温度段,压力值与流量之间的关系是不一样的,因此,在原先建立起来的压力与水封高度以及气缸行程的对应关系的基础上,压力还要受温度信号的干扰,因此有必要有温度的修正来对压力进行补偿。
为此需要建立一个干扰的补偿计算关系。
2.3自整定模糊PID控制
由于不准备采用L2级控制系统,因此数学模型的建立是在L1级的基础上完成的,为了能在DCS系统中实现,因此建立的数学模型是具有自整定PID参数的模糊PID控制。
考虑到本控制系统的控制量是一个微压力系统,而且经过控制输出的执行单元是一个电/气转换的气缸控制系统,因此行程的采集也是一个微值变化系统,为此对信号及PID控制都需要进行转化,也就是需要进行量化处理。
同时由于压力的采集与气缸行程的控制没有直接的数量关系,是经过水封高度来进行转换的,因此计划