第三章修改版.docx
《第三章修改版.docx》由会员分享,可在线阅读,更多相关《第三章修改版.docx(26页珍藏版)》请在冰豆网上搜索。
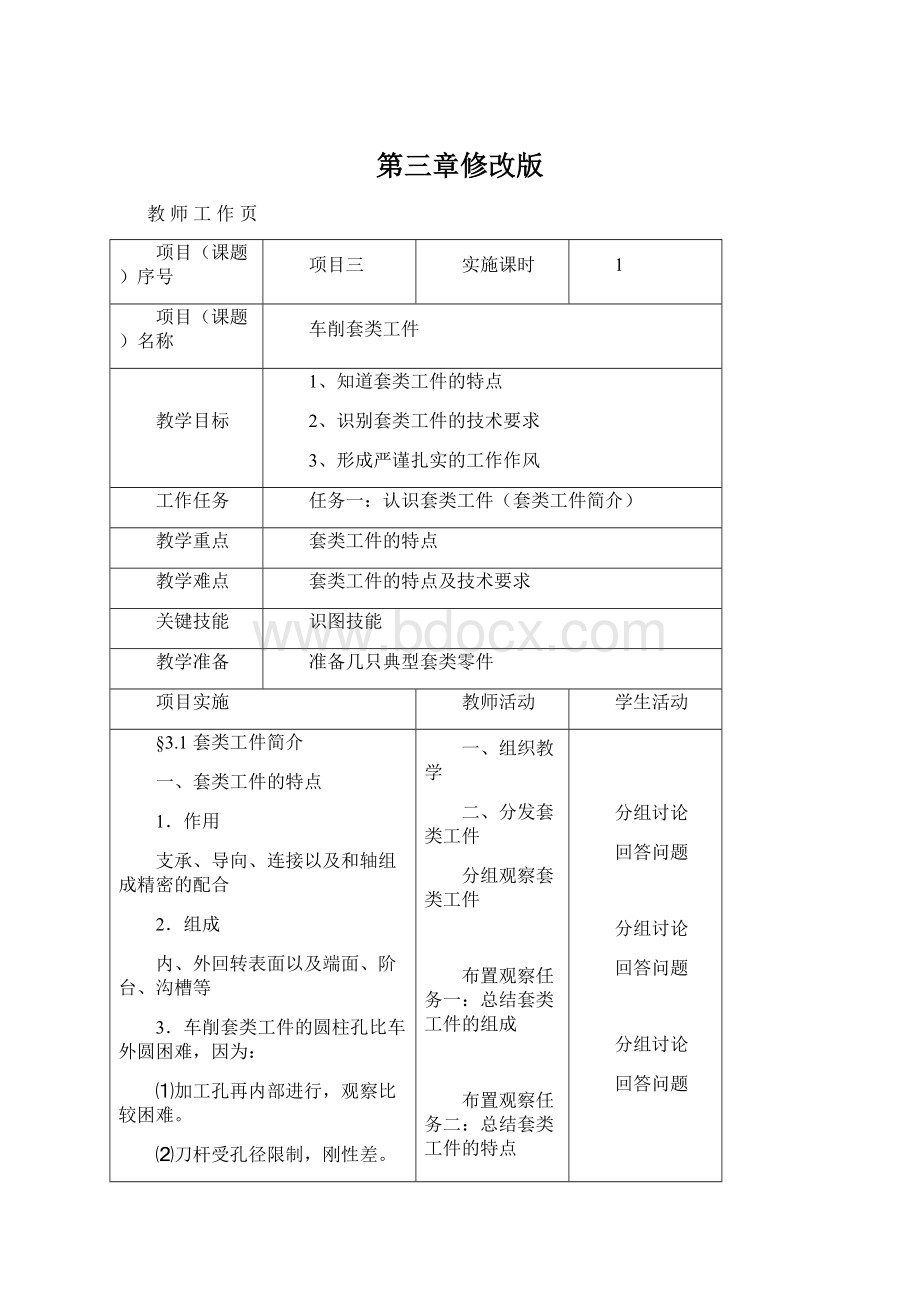
第三章修改版
教师工作页
项目(课题)序号
项目三
实施课时
1
项目(课题)名称
车削套类工件
教学目标
1、知道套类工件的特点
2、识别套类工件的技术要求
3、形成严谨扎实的工作作风
工作任务
任务一:
认识套类工件(套类工件简介)
教学重点
套类工件的特点
教学难点
套类工件的特点及技术要求
关键技能
识图技能
教学准备
准备几只典型套类零件
项目实施
教师活动
学生活动
§3.1套类工件简介
一、套类工件的特点
1.作用
支承、导向、连接以及和轴组成精密的配合
2.组成
内、外回转表面以及端面、阶台、沟槽等
3.车削套类工件的圆柱孔比车外圆困难,因为:
⑴加工孔再内部进行,观察比较困难。
⑵刀杆受孔径限制,刚性差。
⑶排屑和冷却比较困难。
⑷测量比较困难。
⑸装夹时容易变形(特别是薄壁的套类工件)。
二、套类工件的技术要求
尺寸精度
形状精度圆度、圆柱度、直线度、平面度等
位置精度同轴度、平行度、垂直度、径向圆跳动和端面圆跳动等
表面粗糙度在普车上,可达0.8um~1.6um
一、组织教学
二、分发套类工件
分组观察套类工件
布置观察任务一:
总结套类工件的组成
布置观察任务二:
总结套类工件的特点
二、分发套类工件图纸
分组分析套类工件图纸
布置分析任务一:
分析图纸上有哪些技术要求
小结本课内容
分组讨论
回答问题
分组讨论
回答问题
分组讨论
回答问题
课后作业:
P89第1题
教师工作页
项目(课题)序号
项目三
实施课时
1
项目(课题)名称
车削套类工件
教学目标
1、知道套类工件的装夹方法
2、能根据套类工件的不同选择装夹方法
3、形成严谨扎实的工作作风
工作任务
任务二:
装夹套类工件(套类工件的装夹)
教学重点
套类工件的装夹方法
教学难点
薄壁套类工件的装夹
关键技能
装夹方法及装夹技巧
教学准备
多媒体、膨胀螺丝几只
项目实施
教师活动
学生活动
§3.2套类工件的装夹
一、保证套类工件形位精度的方法
1.在一次装夹中完成车削加工
优点:
无定位误差,如果车床精度较高,可获较高的形位精度
缺点:
需经常转换刀架,尺寸较难掌握,切削用量需经常改变。
2.以内孔为定位基准采用心轴
适用于车削中小型的轴套、带轮、齿轮等工件
(1)实体心轴
小锥度心轴C=1/1000~1/5000
特点:
制造容易,定心精度高,但轴向无法定位,承受切削力小,装卸不方便
圆柱心轴
特点:
一次可以装夹多个工件,定心精度低
(2)胀力心轴
依靠材料弹性变形所产生的胀力来固定工件装卸方便,定心精度高,应用广泛。
3.以外圆为定位基准采用软卡爪
软卡爪用未经淬火的45钢制成。
可确保装夹精度,不易划伤工件表面。
二、薄壁套类工件的装夹——刚性差,防止或减小变形
(1)应用开缝套筒装夹——增大装夹的接触面积,使夹紧力均匀分
布在工件外圆上,减小夹紧变形。
(2)应用开缝套筒——使夹紧力沿工件轴向分布
一、组织教学
二、分组自主学习
布置学习任务一:
看多媒体上展示的一次装夹实例分析总结这种方法的优缺点
布置学习任务二:
看多媒体上展示的实体心轴实例分析总结这两种方法的优缺点
分发膨胀螺丝
布置学习任务三:
对比膨胀螺丝和胀力心轴图样分析总结这两种方法的优缺点
布置学习任务四:
了解软卡爪、开缝套筒、开缝套筒用途
小结本课内容
分组学习讨论
回答问题
分组学习讨论
回答问题
分组学习讨论
回答问题
学生讨论后总结
课后作业:
P89第2、3题
教师工作页
项目(课题)序号
项目三
实施课时
2
项目(课题)名称
车削套类工件
教学目标
1、知道钻头的组成
2、能根据前面学习的刀具知识分析钻头上的角度
3、形成严谨扎实的工作作风
工作任务
任务三:
加工套类工件(套类工件的加工方法)
教学重点
麻花钻的几何形状
教学难点
麻花钻的几何形状
关键技能
读图识图技能
教学准备
Ф42钻头几支
项目实施
教师活动
学生活动
§3.3套类工件的加工方法
一、麻花钻钻孔
钻孔定义:
用钻头在实体材料上加工孔的方法
用到工具:
麻花钻、扁钻、中心钻、深孔钻、锪孔钻等
1.麻花钻的几何形状
⑴组成(见图3-1)
①柄部传递扭距和定心。
分锥柄和直柄
②颈部标注商标、钻头直径和材料牌号
③工作部分切削、导向作用
⑵组成部分的几何形状(见图3-2)
螺旋槽两条,构成切削刃、排出切屑和通入切削液
②螺旋角β
螺旋槽上最外缘螺旋线的切线与轴线之间的夹角
越近中心,β↓。
β∈(18°~30°)
③前刀面切削部分的螺旋槽面,切屑从此表面排出
④主后刀面钻顶的螺旋圆锥面
⑤主切削刃两个,切削作用
⑥顶角2Kr
两主切削刃之间的夹角
=118°,主切削刃为直线
>118°,主切削刃为凹曲线
<118°,主切削刃为凸曲线
顶角↑→主切削刃↓、前角↑、定心↓、切削省力→孔径↑
⑦前角γ0
过主切削刃上任一点的基面与前刀面之间的夹角
越近中心,γ0↓。
γ0∈(+30°~-30°)
⑧后角α0
过主切削刃上任一点的切削平面与主后刀面之间的夹角
越近中心,α0↑。
α0∈(8°~14°)
⑨横刃两主切削刃的连接线
横刃太短,影响钻尖强度
横刃太长,轴向力增大,不利切削
⑩横刃斜角Ψ=55°α0↑→Ψ↓、横刃↑
(11)棱边(韧带)保持钻削方向、修光孔壁、作为切削部分的后备部分
复习
一、组织教学
分发Ф42钻头
二、分组自主学习
布置学习任务一:
配合钻头实物了解钻头的组成及各部分作用
布置学习任务二:
复习刀具角度知识,利用原有知识在钻头实物上分析钻头的相关面、线点
在学生完成自主学习后与同学一起分析得出结论
小结本课内容
复习第一课的知识
布置学习任务三:
复习刀具角度知识,利用原有知识在钻头实物上分析钻头的角度
在学生完成自主学习后与同学一起分析得出结论
适时提问
、
小结本课内容
分组学习讨论
回答问题
分组学习讨论
钻头中前面、后面、副后面、主切削刃、副切削刃、刀尖的位置
学生共同参与分析
分组学习讨论
钻头中前角、后角的位置及大小
学生共同参与分析
学生回答
课后作业:
P89第4、5题、第6、7题
教师工作页
项目(课题)序号
项目三
实施课时
2
项目(课题)名称
车削套类工件
教学目标
1、知道钻头的刃磨和修磨要求
2、能进行钻头的刃磨操作
3、形成严谨扎实的学风
工作任务
任务三:
加工套类工件(套类工件的加工方法)
教学重点
麻花钻的修磨
教学难点
麻花钻的缺点
关键技能
钻头的刃磨操作
教学准备
Ф42麻花钻几支
项目实施
教师活动
学生活动
§3.3套类工件的加工方法
一、麻花钻钻孔
1.麻花钻的几何形状
2.麻花钻的刃磨要求
⑴刃磨要求
只磨两个主后刀面,要保证顶角、Ψ、α0正确
①两主切削刃对称角度、长度相等
②Ψ=55°
⑵对钻孔质量的影响
①麻花钻顶角不对称只有一个切削刃切削,两边受力不平衡会使钻出的孔扩大和倾斜
②顶角对称但切削刃长度不等使钻出的孔扩大
③顶角不对称且切削刃长度不等孔径扩大,出现阶台。
3.缺点
⑴外缘处的γ0较大(+30°),切削刃强度↓
横刃处的γ0=-54°,挤压严重,切削条件差
⑵横刃是挤压和刮削,消耗的能量大,产生热量大,轴向力增大定心↓
⑶切屑占较大的空间,排屑不顺利,切削液难进入切削区
⑷外缘处磨损加快
4.修磨
⑴横刃
目的缩短长度,横刃处γ0↑,钻削力↓
原则:
工件材料软,横刃↓
工件材料硬,横刃↑
⑵前刀面
外缘处:
工件材料较硬→γ0↓→钻头强度↑
横刃处:
工件材料较软→γ0↑→钻头强度↑
⑶双重刃磨
双重顶角,改善外缘转角处的散热条件,钻头强度↑,孔的表面粗糙度↓
⑷开分屑槽
当麻花钻直径较大时,可在钻头前刀面或后刀面上开分屑槽,以便断屑。
前刀面上的分屑槽在制造时已经做出。
主后刀面上的分屑槽须由操作者在砂轮机上磨出来。
⑸开断屑槽——钻削塑性金属
复习
一、组织教学
分发Ф42麻花钻
二、分组自主学习
布置学习任务一:
刃磨钻头有那些要求?
刃磨不当会有什么影响?
老师示范麻花钻的刃磨方法及操作要领
布置学习任务二:
复习钻头前角、后角的变化。
分组讨论分析钻头的缺点
在学生完成自主学习后与同学一起分析得出结论
小结本课内容
复习第一课的知识
钻头的缺点
布置学习任务三:
在复习钻头缺点后,自足学习钻头的修磨
在学生完成自主学习后与同学一起分析得出结论
适时提问
小结本课内容
分组学习讨论
回答问题
学生学习刃磨操作
分组分析讨论
学生共同参与分析
分组学习讨论
钻头中前角、后角的位置及大小
学生共同参与分析
学生回答
课后作业:
P89第8、9题
教师工作页
项目(课题)序号
项目三
实施课时
2
项目(课题)名称
车削套类工件
教学目标
1、知道钻孔、扩孔、锪孔的方法
2、能进行钻孔、扩孔、锪孔的方法操作
3、形成严谨扎实的学风
工作任务
任务三:
加工套类工件(套类工件的加工方法)
教学重点
钻孔、扩孔、锪孔的方法
教学难点
钻孔、扩孔、锪孔的方法
关键技能
钻孔的方法
教学准备
多媒体
项目实施
教师活动
学生活动
§3.3套类工件的加工方法
一、麻花钻钻孔
1.麻花钻的几何形状
2.麻花钻的刃磨要求
3.缺点
4.修磨
5.装夹
⑴直柄麻花钻用钻夹头装夹,再装入尾座套筒锥孔中
⑵锥柄麻花钻
⑶用V形架装夹
⑷用专用夹具装夹
6.钻孔方法
⑴切削用量
①apap=Φ/2(Φ为钻头直径)
②Vc
Vc=πDn/1000
式中:
Vc——切削速度m/min
D——钻头直径㎜
n——车床主轴转速r/min
高速钢钻头钻钢料,Vc为15~30m/min
钻铸铁,Vc为10~25m/min
③f钻头直径为12㎜—25㎜钻钢料,f为0.15—0.35㎜/r
⑵注意事项
①将钻头装入尾座套筒中,找正钻头轴线与工件旋转轴线相重合
②钻孔前,端面要车平,中心处不能有凸头
③刚接触工件端面和快钻通孔时,进给量要小
④钻小而深的孔时,先用中心钻钻中心孔
⑤钻深孔时,钻头经常退出清除切屑
⑥钻削钢料时,浇注充分的切削液,钻铸铁时可不用
⑶孔质量分析
废品种类
产生原因
预防措施
孔歪斜
工件端面不平,或与轴线不垂直
车平端面,中心不能有凸头
尾座偏移
调整尾座与主轴的轴线同轴
钢性差,初钻时,进给量过大
进给量要小
钻头顶角不对称
正确刃磨钻头
孔直径过大
钻头直径选错
看清图样,仔细检查钻头直径
主切削刃不对称
仔细刃磨,使两主切削刃对称
钻头未对准工件中心
检查钻头是否弯曲
二、扩孔
用扩孔工具将原工件的孔径扩大的加工过程称扩孔。
1.麻花钻扩孔
防止钻削轻快,出现打滑,应把钻头外缘处前角磨小,适当控制进给量
2.扩孔钻扩孔
⑴种类
高速钢、硬质合金
⑵特点
①齿数较多(一般为3~4齿),导向性好,切削平稳
②切削刃不必自外缘一直到中心,无横刃
③钻心粗,刚性好,可选用较大的切削用量
三、锪孔
在工件孔口表面,用锪钻加工出一定的孔或表面称为锪孔
1.种类
圆柱沉头孔锪钻、圆锥锪钻和端面锪钻
2.角度
60°,75°,90°,120°
75°锪钻用于锪埋头铆钉孔
90°锪钻用于锪埋头螺钉孔
复习
一、组织教学
播放多媒体“钻孔方法”
二、分组自主学习
布置学习任务一:
观看多媒体的同时总结钻头的装夹和钻孔方法
布置学习任务二:
复习切削三要素。
分组讨论分析钻头切削三要素。
与学生一起分析钻头钻孔的注意事项
小结本课内容
复习第一课的知识
钻头的钻孔方法
布置学习任务三:
在复习钻头缺点后,自足学习钻头的修磨
在学生完成自主学习后与同学一起分析得出结论
适时提问
小结本课内容
分组讨论总结
回答问题
分组分析讨论
学生共同参与分析
学生共同参与分析
学生回答
课后作业:
P89第8、9题
教师工作页
项目(课题)序号
项目三
实施课时
2
项目(课题)名称
车削套类工件
教学目标
1.掌握内孔车刀的种类和特点
2.掌握车内孔的关键技术
工作任务
车孔
教学重点
内孔车刀的种类和特点
教学难点
车内孔的关键技术
关键技能
车内孔的方法
教学准备
多媒体,内孔车刀,
项目实施
教师活动
学生活动
上堂课我们已经学了扩孔方法和锪孔的方法
【复习提问】
1.扩孔钻的主要特点有哪些?
2.锪钻有哪些类型?
【导入】
工件上的铸造孔、锻造孔或用钻头钻出的孔,为了达到所需的精度和表面粗糙度,还需要车孔(又称镗孔)。
【新授】
一、内孔车刀
车孔特点:
1.车孔可以作为粗加工,也可以作为精加工。
2.车孔的精度一般可达IT7-IT8,表面粗糙度为Ra3.2-Ra1.6。
精车可达Ra0.8或更小。
通过一段视频来了解如何车削孔。
车削孔用到的刀具是内孔车刀
内孔车刀可分为通孔和盲孔车刀两种
1.通孔车刀
A:
主偏角应取得大些,Kr=60°~75°之间,Kr’=15°~30°。
B:
一般磨成两个后角。
2.盲孔车刀
A:
主偏角大于90°
B:
后角的要求和通孔车刀一样
C:
刀尖在刀杆的最前端。
刀尖到刀杆的最外端的距离a小于孔半径R
车刀结构:
⒈整体式
⒉分体式
下面我们通过一段视频了解如何刃磨内孔车刀
2.内孔车刀的装夹
⑴刀尖与工件中心等高或稍高
⑵刀杆伸出刀架不宜过长
⑶刀杆要平行于工件轴线
二、车孔的技术要求
关键技术:
解决内孔车刀的刚性和排屑问题
1.尽量增加刀杆截面积
刀尖位于刀柄的中心线上
2.刀杆的伸出长度尽可能缩短
刀柄伸出太长,影响刚度
3.解决排屑问题
控制切屑流向
①精车通孔——正值刃倾角
②加工盲孔——负值刃倾角
⑵方法
①基本与车外圆同,选用小的切削用量
②控制阶台深和孔深的方法:
A:
应用车床的纵向刻度盘
B:
在刀杆上做标记
C:
应用挡铁等
组织教学,提问
鼓励,积极评价
提出工作任务一:
请同学与钻孔和锪孔相比较,看看谁的加工精度和表面质量更好?
播放内孔车削视频
提出工作任务二:
请学生先看图,总结通孔车刀的特点
教师巡回指导
提出工作任务三:
请学生先看图,总结盲孔车刀的特点
教师巡回指导,在学生回答的基础上总结
?
通过PPT出示分体式车刀的结构图
播放内孔车刀刃磨的视频
提出工作任务四:
内孔车刀如何装夹?
教师巡回指导,在学生回答的基础上总结
提出工作任务四:
车内孔的关键技术是什么?
如何解决?
教师巡回指导,在学生回答的基础上总结
【课堂小结】
本堂课我们学了内孔车刀的结构、安装、刃磨方法、车内孔的关键技术的解决方法和内孔的车削方法。
仔细思考,积极回答问题
仔细思考,积极回答问题
仔细观看视频
学生先学,再分组学习讨论
【想一想】为什么主偏角应取得大些?
【想一想】为什么磨成两个后角?
回答问题
【想一想】通孔刀和盲孔刀有什么区别
【想一想】为什么主偏角应取得大些?
【想一想】为什么刀尖到刀杆的最外端的距离a小于孔半径R?
分组学习讨论
回答问题
观看结构图
仔细观看视频
【想一想】为什么不能低于工件的中心?
【想一想】为什么刀杆不能伸出刀架过长?
【想一想】假如刀杆需要伸出较长,怎么办呢?
【想一想】为什么刀杆要平行于工件轴线?
分组讨论
回答问题
分组讨论
回答问题
【想一想】为什么采用正值刃倾角?
【想一想】为什么采用负值刃倾角?
【想一想】为什么切削用量要比车外圆小一些?
【提问】车削阶台轴时,如何控制阶台长度?
学生总结
▪课后作业:
习题册
▪第一大题:
14、15、16
▪第二大题:
16、17、18
▪第三大题:
13、14、15、
▪第五大题:
4、5
▪
教师工作页
项目(课题)序号
项目三
实施课时
2
项目(课题)名称
车削套类工件
教学目标
1、知道铰孔、车内沟槽的方法
2、能进行铰孔、车内沟槽操作
3、形成严谨扎实的学风
工作任务
任务三:
加工套类工件(套类工件的加工方法)
教学重点
铰孔、车内沟槽的方法
教学难点
铰孔、车内沟槽的方法
关键技能
铰孔、车内沟槽的方法
教学准备
多媒体
项目实施
教师活动
学生活动
§3.3套类工件的加工方法
五、铰孔
是精加工孔的方法之一,在工厂中被广泛应用。
1.铰刀
⑴几何形状
柄部、颈部和工作部分组成
柄部的作用:
夹持和传递扭矩分直柄、锥柄和方榫形
⑵铰刀的种类
按用途可分机用铰刀和手用铰刀
按材料可分高速钢和硬质合金两种
⑶装夹
为保证同轴度,常采用浮动套筒
2.铰孔余量
高速钢铰刀为0.08㎜-0.12㎜;硬质合金为0.15㎜-0.20㎜
3.注意事项
①铰刀的选择和保管
②调整尾座轴线和使用浮动套筒
③选择合理的铰削用量
④合理选择切削液(干切削和非水溶性孔大;水溶性孔小)
⑤铰孔前对孔的要求
六、车削沟槽
1.车削内沟槽
①截面形状:
矩形(直槽)、圆弧形、梯形
②作用:
退刀、密封、定位、通气
③几何形状与切断刀相似,只是装夹方向相反,且在内孔中车
2.车端面沟槽
截面形状:
直槽、T形槽、燕尾槽
①车端面直槽:
一个刀尖相当于车内孔,另一个相当于车外圆
②车T形槽
③车燕尾槽
复习
一、组织教学
二、分组自主学习
布置学习任务一:
自主学习铰孔的方法
与学生一起分析学习内孔车刀知识
小结本课内容
复习第一课的知识
布置学习任务二:
观看车孔多媒体。
总结车孔的操作要领及注意事项?
在学生完成自主学习后与同学一起分析得出结论
适时提问
小结本课内容
分组讨论总结
回答问题
分组分析讨论
学生共同参与
分组自主学习并分析讨论
学生共同参与分析
学生回答
课后作业:
P89第11、12题
教师工作页
项目(课题)序号
项目三
实施课时
2
项目(课题)名称
车削套类工件
教学目标
1.尺寸精度的测量(内卡钳、塞规、内径千分尺、内测千分尺、内径百分表的简介和应用)
2.形位精度的测量
3.车削典型的套类工件
工作任务
任务:
尺寸精度的测量形位精度的测量
教学重点
尺寸精度的测量形位精度的测量
教学难点
形位精度的测量
关键技能
尺寸精度的测量形位精度的测量
教学准备
多媒体、各种量具
项目实施
教师活动
学生活动
Ⅰ.复习
1.车孔的关键技术是什么?
解决措施是什么?
2.铰孔时,使用切削液对铰孔质量有什么影响?
3.铰孔时,孔的表面粗糙度与铰削速度有什么关系?
4.对端面直沟槽刀有哪些要求?
Ⅱ.引入新课
在加工孔的过程中要不断测量孔径的大小采取相应地加工方法才能生产出合格的产品。
那在这里面测量是一个关键的技术问题,如果测量不准确就会对加工造成影响,从而生产出的产品不合格。
为了进行准确测量就必须学习测量工具及其使用方法。
Ⅲ.进入新课
§3.4套类工件的测量
一、尺寸精度的测量
1.孔径尺寸的测量
要求较低时:
钢直尺、内卡钳、游标卡尺
要求较高时:
⑴内卡钳
孔口试切或位置狭小
⑵塞规
适用于成批生产时
组成:
过端(尺寸=Lmin)、止端(尺寸=Lmax)、手柄
图3-6塞规
过端与止端区别:
止端长度<过端长度
测量方法:
过端通过,过端不能通过,孔尺寸合格
⑶内径千分尺
在孔内摆动,径向摆动找出最大尺寸,轴向摆动找出最小尺寸,这两个重合尺寸就是孔的实际尺寸。
⑷内测千分尺
刻线方向与外径千分尺相反。
测量孔径小于25㎜以下的孔
图3-7内测千分尺
⑸内径百分表
测量前,百分表对零位,测量时,必须左右摆动百分表,测得的最小值就是孔径的实际尺寸。
主要应用于测量精度要求较高而且又较深的孔。
图3-8内径百分表
2.内沟槽的检验
⑴弹簧内卡钳测直径
测量时,先将弹簧内卡钳收缩,放入内沟槽,测出内沟槽直径,然后将卡钳收缩取出,恢复到原来的尺寸,再用游标卡尺或外径千分尺测出内卡钳的张开距离,就是内沟槽直径。
⑵钩形深度游标卡尺测轴向尺寸
⑶钢直尺、游标卡尺测内阶台深度
二、形状精度的测量
1.孔的圆度测量——内径百分表
测量的最大值与最小值之差的一半为单个截面上的圆度误差
2.孔的圆柱度误差——内径百分表
在全长上前、中、后各测量几点,比较其测量值,其最大值与最小值之差的一半即为孔全长上的圆柱度误差
三、位置精度的测量
1.径向圆跳动测量
测量面上径向圆跳动误差——百分表在工件转一周后所得到的最大读数差
该工件的径向圆跳动误差——取各截面上测得的跳动量中的最大值
图3-9用两顶尖支承检验径向及端面圆跳动
2.端面圆跳动的测量方法
测量面上的端面圆跳动——工件转一周,百分表的最大读数
3.端面对轴线垂直度的测量
①测量端面圆跳动是否合格,合格后再测量端面的垂直度
②对于精度要求较低——用刀口直尺或游标卡尺尺身侧面透光检查
③对于精度要求较高——当端面圆跳动合格后,再把工件装夹在V形架的小锥度心轴上,并放在精度很高的平板上检查端面的垂直度。
四、车削典型的套类工件
1.选择车削步骤的一般原则
⑴短而小的套类工件,最好在一次装夹中把内孔、外圆及端面都加工完毕
⑵内沟槽应在半精车之后,精车之前加工。
注意精车余量
⑶车削精度要求较高的孔的步骤:
粗车端面→钻孔→粗车孔→半精车孔→精车端面→铰孔或粗车端面→钻孔→粗车孔→半精车孔→精车端面→磨孔
⑷加工平底孔时,钻孔→平底钻锪平→盲孔车刀精车
⑸以内孔定位车外圆时,内孔精车后,再精车端面,以达到端面与内孔的垂直度要求
2.车典型的套类工件
⑴工件图样(见书上P82图3-45)
⑵装夹方法
粗车:
一夹一顶(提高工件加工时的刚性)
精车:
小锥度心轴定