强夯施工方案.docx
《强夯施工方案.docx》由会员分享,可在线阅读,更多相关《强夯施工方案.docx(9页珍藏版)》请在冰豆网上搜索。
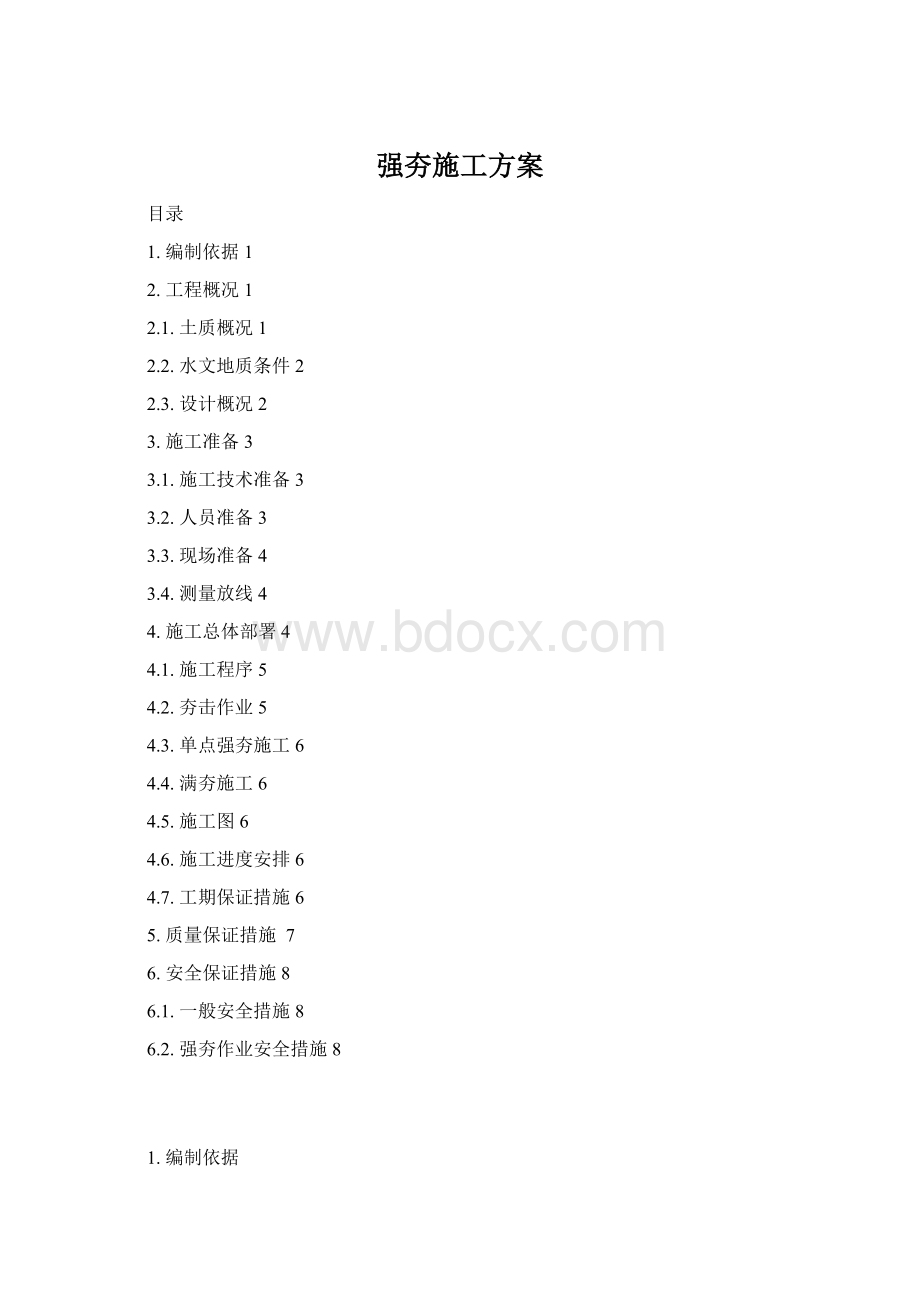
强夯施工方案
目录
1.编制依据1
2.工程概况1
2.1.土质概况1
2.2.水文地质条件2
2.3.设计概况2
3.施工准备3
3.1.施工技术准备3
3.2.人员准备3
3.3.现场准备4
3.4.测量放线4
4.施工总体部署4
4.1.施工程序5
4.2.夯击作业5
4.3.单点强夯施工6
4.4.满夯施工6
4.5.施工图6
4.6.施工进度安排6
4.7.工期保证措施6
5.质量保证措施 7
6.安全保证措施8
6.1.一般安全措施8
6.2.强夯作业安全措施8
1.编制依据
1.1.总平面图;
1.2.岩土工程勘察资料;
1.3.《建筑地基基础设计规范》(GB5007—2002);
1.4.《建筑地基处理技术规范》(JGJ79—2012);
1.5.《强夯地基技术规程》(CECS279:
2010);
1.6.《工程测量规范》(GB50026—2007,国家标准);
1.7.《建筑地基基础工程施工质量验收规范》(GB50202—2002,国家标准);
1.8.《建筑施工安全检查标准》(JGJ59—2011,行业标准);
1.9.《建筑机械使用安全技术规程》(JGJ33—2012,行业标准)。
2.工程概况
2.1.土质概况
根据钻孔揭露,勘察场地地层主要为杂填土、第四系全新统陆相冲、洪积物。
在勘探深度范围内,自上而下可划分为5个主要工程地质层,各层土的特征分述如下:
①杂填土(Q4ml):
场地分布连续,杂色,松散,稍湿,主要由粉土和细砂及卵石组成,含建筑垃圾。
层厚为1.20~6.50米,层顶标高为53.45~58.79米。
②粉土(Q4al):
场地内大部分分布,褐黄,中密~密实,稍湿~湿,切面粗糙,摇震反应中等,干强度低、韧性低,局部夹细砂薄层。
层厚为0.40~1.20米,层顶标高为51.51~53.85米。
③细砂(Q4al):
场地内大部分分布,黄褐,稍密~中密,稍湿,主要由长石、石英组成,局部充填圆砾及卵石,夹粉土薄层。
层厚为0.50~4.10米,层顶标高为48.65~53.72米。
④卵石(Q4al+pl):
场地内分布连续,杂色,稍密~中密,稍湿,主要由岩浆岩及变质岩碎块组成,一般粒径2-5cm,最大可见8cm,局部夹细砂薄层,充填物为圆砾及细砂,含量约为30%-35%。
层厚为0.60~7.00米,层顶标高为47.85~51.90米。
⑤卵石(Q4al+pl):
场地内部分布连续,杂色,中密~密实,稍湿~饱和,主要由岩浆岩及变质岩碎块组成,一般粒径3-7cm,最大可见10cm,局部夹细砂薄层,充填物为圆砾及细砂,含量约为25%。
层厚最大揭露为22.50米。
2.2.水文地质条件
本工程位于滦河Ⅰ级阶地,地下水位埋深为9.50~14.80米,水位高程43.87~44.29米。
含水层为⑤卵石层,按埋藏条件属潜水,根据区域水文地质资料,地下水年变幅约2.0米。
2.3.设计概况
2.3.1.地基强夯处理对象及区域划分
1)地基强夯处理的对象
①层杂填土:
回填质量较差、为机械自然抛填,结构松散,欠固结,为高压缩性土层。
新近堆积,不宜作为天然地基基础持力层使用。
②层粉土:
稍密。
标准贯入试验锤击数N=5.0击~9.0击,平均值为7.0击。
通过强夯处理增加①层杂填土、②层粉土的密实度,提高承载力,降低压缩性。
2.4.地基强夯处理技术要求
地基强夯处理后的地基承载力特征值不小于150KPa,压实系数达到强夯设计要求,场地平整后标高符合设计场地标高要求。
2.4.1.单击夯击能
强夯的单击夯击能根据地基土类别、性质,上部结构类型、荷载大小、基础形式和要求处理深度等综合考虑,并通过试夯确定。
本工程处理深度为8m。
本工程中拟采用夯锤质量为16t,锤径为2.4m,点夯落距为10m,满夯落距为8.0m,则:
QHg≈16×10.0×10=1600(kN•m),QHg值即为单击夯击能。
2.4.2.夯击遍数与夯点布置
本工程强夯采用二遍点夯,一遍满夯。
第一遍点夯布点采用5m×5m正方形布点,第二遍布置于第一遍点夯布点正方形中心点,最终布置成梅花形。
满夯夯锤印间搭接0.3~0.5m。
强夯布点图
注:
一遍点夯布点,夯点间距为5米二遍点夯布点,夯点位于正方形中心。
3.施工准备
3.1.施工技术准备
1)点夯每点夯击数:
点夯每点夯击数均为6~8击。
2)满夯夯击能及每点夯击数
根据《建筑地基处理技术规范》的规定:
点夯完成后,应以低能量满夯1遍,锤印搭接。
在本工程中,根据现场回填土的实际情况,结合施工单位以往的施工经验,采用一遍满夯,满夯夯击能取1280kN•m;满夯每点夯击数为3击。
3.2.人员准备
要使施工顺利进行,保工期、保安全、保质量地完成任务,除必须配备足够的材料及机械设备外,还须进行合理的人员配置与分工,成立以项技术负责人为核心的项目经理部,实行项目负责人全权负责制,具体职责如下。
技术负责人:
负责向有关施工人员及施工班组进行技术交底,并监督其按设计要求及本施工组织设计进行施工,负责组织本专业工作的签证、验收、整理分析原始材料,对一般技术问题做出处理,重大技术问题向公司汇报。
质安员:
分管施工质量、安全检查。
施工员:
现场监督各施工班组按本施工方案进行各工序的施工,收集、掌握、整理施工现场的进展及原始施工资料,发现问题及时处理或上报。
后勤:
负责全体施工人员的生活、伙食、劳保及后勤事宜。
机长:
负责本机台安全、质量工作,并协助施工员工作。
主司机:
强夯机台操作及维修管理。
副司机:
协助主司机工作。
测工:
夯沉量观测及记录。
普工:
挂钩作业、辅助测量。
3.3.现场准备
1)按施工进度要求,组织人员安排临时设施,并组织设备进场。
2)进场后收集并查明现场的填土、在建建(构)筑物各种地下情况,保障施工顺利进行。
强夯场地要满足“三通一平”的要求,清除场内所有障碍物(包括空中的可能影响强夯机起重臂移动各种拉线、电线等),清除地下管线,或按要求将地下管线移位。
3)检查锤重和落距,确保单击的夯击能符合设计要求。
4)做好施工场地的排水。
场地平整时,使场地表面形成适当的排水坡,并在周边可能进水的地段设置好排水沟。
5)场地的地面强度要能承受住起重机械的负荷,必要时应采取压实、铺填砂、石垫层或其它措施。
6)强夯前应查明夯击所产生的震动对现场周围的建筑物及其它设施的影响,若有影响,应采取可靠的防震措施,如挖防震沟、打减震孔或对建(构)筑物采取适当的加固措施等,并在强夯过程中加强对其观测。
7)协调施工范围的交接及与其他施工单位的配合。
3.4.测量放线
由专业人员进行施工控制点线及强夯范围的测放。
做好控制点线的加固保护。
根据测放的点线按照设计图纸进行夯点布置。
4.施工总体部署
根据设计强夯区域、强夯参数及工程填土进度现状,考虑到夯机施工作业安全要求,将施工区域按现场情况进行划分区域,使夯机能流水作业。
4.1.施工程序
对于整平的场地测出其平均标高,以作为强夯后测量场地的平均沉降量的基准数。
根据测放的点线按照设计图纸进行夯点布置。
夯点位置要清晰、准确,以便夯锤对位和量测夯击后的锤位偏差值。
锤位偏差不得超过5cm。
若发现偏差过量或漏夯,应及时纠正。
每个夯击点都要编号,记录员要对号进行记录,不能错号,不能漏夯和重夯。
4.2.夯击作业
按照设计要求进行,先点夯后满夯施工。
施工时应做到:
1)每一锤在正式提升前,都要准确对好锤位,每一锤都要提升到设计要求的高度;
2)锤落下后,如夯坑底有倾斜,当超过20度时,要用土将坑底补平,才能进行下次夯击;
3)每个夯坑的每一击,都要记录下沉量;
4)当施工场地及夯坑由于降雨造成积水时,要及时采取排水措施,待水排干后,才能填坑;
5)点夯施工收锤控制标准:
每个夯击点的夯击次数不少于6次;
最后两击的平均沉降量要不大于5cm;
6)夯坑回填时,须用推土机等略加压实,并稍高于附近地面,以防止坑内填土吸水过多;
7)回填土时,须注意块石料与细粒料的合理搭配,避免块石架空现象;
8)最后一遍满夯完成后,应准确测定场地的平均标高(按既定的网格定点测量),再求出场地的最终平均沉降量。
该沉降量要注明由场外运进的土石方量。
9)对于整平的场地测出其平均标高,以作为强夯后测量场地的平均沉降量的基准数。
4.3.单点强夯施工
在单点强夯施工前根据设计原则,绘制夯点布置图(见附图)。
单点强夯
施工步骤如下:
1)清理并平整施工场地,清除耕土层和较集中分布的生活垃圾;
2)标出第一遍夯点位置,并测量场地高程;
3)起重机就位,夯锤置于夯点位置;
4)测量夯前锤顶高程;
5)将夯锤起吊到预定高度,开启脱钩装置,待夯锤脱钩自由下落后,放下吊钩,测量锤顶高程,若发现因坑底倾斜而造成夯锤歪斜时,应及时将坑底整平。
6)重复步骤5,按设计规定的夯击次数及控制标准,完成一个夯点的夯击。
7)用推土机将夯坑填平,并测量场地高程。
8)按上述步骤逐次完成全部夯击遍数,最后用低能量满夯,将场地表层松土夯实,并测量夯后场地高程。
各遍点夯施工夯机的先后顺序应根据现场夯击、补土等具体情况确定。
补土施工应在点夯施工过程中同时进行,所需土石方用推土机推入夯坑内。
4.4.满夯施工
点夯施工完毕后,测量场地标高,补土至交工面标高20~30cm,按设计要求进行满夯施工。
4.5.施工图
本施工组织设计后附图纸:
点夯布置示意图各一份。
4.6.施工进度安排
根据场地填土现状及甲方对场地的需求,做到提供一片场地,就能有设备投入该场地,并尽最大可能、尽快组织施工,确保不耽误整体进度要求。
4.7.工期保证措施
1)组成以项目经理为首的工期控制组织机构,经常检查工程实际进度与计划进度的偏离情况,及时采取措施进行调整。
2)编制工程进度计划,以便施工管理人员做到条理清晰,目标明确。
3)按照总体进度计划安排,编制各分享工程详细的周进度计划。
4)科学调配施工设备,尽量减少因各工序的相互干扰。
5)定期对施工机械进行检验、维修、保养,使机械设备保持良好状态;对施工人员进行技术培训熟练掌握施工工艺和操作规程,以便上岗时能熟练地操作。
6)建立专职的施工机械修理组,并储备足够的机械易损配件,施工过程中,定期配合司机对机械设备进行检查,并及时地排除故障,尽可能减少机械设备故障对施工的影响。
7)施工期密切关注气象预报,采取雨季施工措施,尽可能降低因降雨及其他不利天气因素对施工进度的影响。
8)妥善解决好强夯施工中的震动、飞石、噪音等对周围生产、生活的不利影响,以免此类问题的出现影响施工进度。
9)实行多劳多得的强夯计件制度,激发工人的积极性,提高工人的工作效率以加快施工进度。
10)如工期出现滞后,立即采取赶工措施,包括:
(1)适当延长有效工作时间;
(2)增加司机和工人,实行两班倒工作制;
(3)合理调配或增加施工机械设备等。
5.质量保证措施
1)建立由项目经理、技术负责、质量员、施工员以及施工班组长组成的质量领导机构。
项目经理要做到靠前指挥、高速运转,所配备的各类管理人员要业务精、技术好、事业心强,有较丰富的施工经验,各施工队由一些骨干力量组成,为工程质量合格提供组织保障。
2)施工前对所有施工人员进行技术交底,施工过程中,将测量放线、夯锤提升高度、夯位准确性、最后两击平均夯沉量的控制,做为工程质量控制点,设立质检员管理控制施工过程质量,做好施工过程中的自检抽检工作,并做好施工记录。
3)施工记录要清晰、真实、项目填写完整和规范,不得随意更改。
记录上除记录员要签名外,还要有值班负责人和监理人员签名。
及时做好施工过程中有关资料的整理。
工程完工后,要及时地提供完整的竣工资料。
4)加强同监理、业主的沟通,加强同其它施工单位的配合,使双方能够相互创造施工条件,为施工创造良好的外部环境,及时解决施工中出现的困难和问题,避免差错和下次少走弯路,以促进工程的顺利进展。
5)实行质量奖惩措施。
对弄虚作假、不按设计施工的人员,一经发现,对于初犯的,除责令其返工外,还对主要责任人罚款500元。
对于重犯的,除罚款1000元外,还需将其调离本工地。
6.安全保证措施
6.1.一般安全措施
1)坚持“安全第一、预防为主”的方针,认真落实“三级”安全教育,每周进行安全检查、考核,检查出的事故隐患,及时整改,最大限度地消除人的不安全行为和物的不安全状态。
组织安全事故分析会议,听取各方面的事故意见,做出相关决议,提出整改方案、善后方案及预防类似事故的具体措施。
不断学习其他单位的成功经验和经验教训,加强本身安全生产保证体制的完善工作,并把此项工作作为一项长期任务来完成。
2)严禁无证驾驶和无证操作,严禁酒后作业,严禁非本车司机作业。
3)所有夯机在进入场地进行施工前必须经过公司安全技术鉴定小组严格鉴定,在确保无误的情况下方可施工;每天施工前要对机械设备进行检查,交接班要填写安全记录,如出现安全事故,应及时履行报告手续。
4)选用的机械设备要有足够的安全保障,起重机械要有足够的安全系数。
5)施工人员进入现场要戴安全帽、手套、穿工作服。
6)工地入口处主要道路边设置警示带,劝阻无关人员进入现场。
7)六级以上大风及阴雨天气或能见度低视线不良时,不能进行强夯作业,夜间没有相应的措施不能施工。
8)现场用电设备及线路应按照施工设计及有关电气安全技术、规定安装和架设,非电工人员不得随意拆装电气设备及路线。
9)强夯机的臂杆脱钩器等主要结构和部件的材料及制作质量,必须经过严格检查,凡不符合设计要求的一律不得使用。
6.2.强夯作业安全措施
1)应经常检查维修和保养好强夯机具,力求将隐患消除在萌芽状态。
2)施工现场必须统一指挥,起重指挥人员的指挥信号要明确,司机应按指挥信号进行操作。
3)起重机停稳,并将夯锤对好坑位后方可进行强行操作。
4)起吊夯锤时速度要均匀,夯锤及挂钩不得碰吊臂。
在吊杆臂的适当位置捆绑废汽车外胎进行保护。
5)从夯锤提升到夯锤落下,机下人员必须离开夯点20m以外,非工作人员应远离夯点30m以外。
严禁在起重机正前方和起重机臂杆下站立。
6)挂钩人员在完成挂钩工作后,应站在安全位置,观察夯锤提升情况,等待下次挂钩。
7)夯锤起升后,起重指挥人员及驾驶员要密切注意夯锤运动情况,防止在脱钩装置失灵的情况下,发生夯锤上升过高引起事故。
若夯锤不能落下,必须及时进行处理。
8)当夯锤即将升到预定的高度时,应稍微停一下,待锤不动后再继续提升,直到脱钩落下。
9)夯锤上升时,不得旋转,如发生旋转,应立即停止起落,及时采取措施使其恢复正常状态后进行工作。
10)夯锤在起吊过程中,严禁中途变速及倒转,如遇特殊情况,可拉开脱钩器,等锤落下后再进行处理。
11)夯锤落下后,在脱钩器尚未降至夯锤吊环附近前,操作人员不得提前下坑立杆、挂钩;从坑中提锤时严禁挂钩人员站在锤上随锤起升。
12)夯锤必须留有通气孔,在作业中通气孔被堵塞或锤顶堆积物过多时,必须及时清理,严禁任何人钻入孔底或站在锤下进行清理。
13)夯坑内积水或因粘性土产生锤底西历增大时,应采取措施排除,不得强行起锤。
夯坑地面出现倾斜时,应及时处理或回填,不得强行夯击。
14)夯锤埋入土中50cm以上时,起重机提升不要一次猛起,要先试提,当机械无异常现象时,方可起升。
15)强夯机变换夯位后,必须重新检查夯机的水平情况,不平时,要调整到稳固的水平状态,然后再将夯锤提起10~30cm,检查整机的稳定性,确认可靠后,方可作业。
16)严禁在非作业时将夯锤悬挂空中,作业完毕后,应将锤平稳地放在地面上。