01水轮机及其辅助设备运行规程定稿.docx
《01水轮机及其辅助设备运行规程定稿.docx》由会员分享,可在线阅读,更多相关《01水轮机及其辅助设备运行规程定稿.docx(99页珍藏版)》请在冰豆网上搜索。
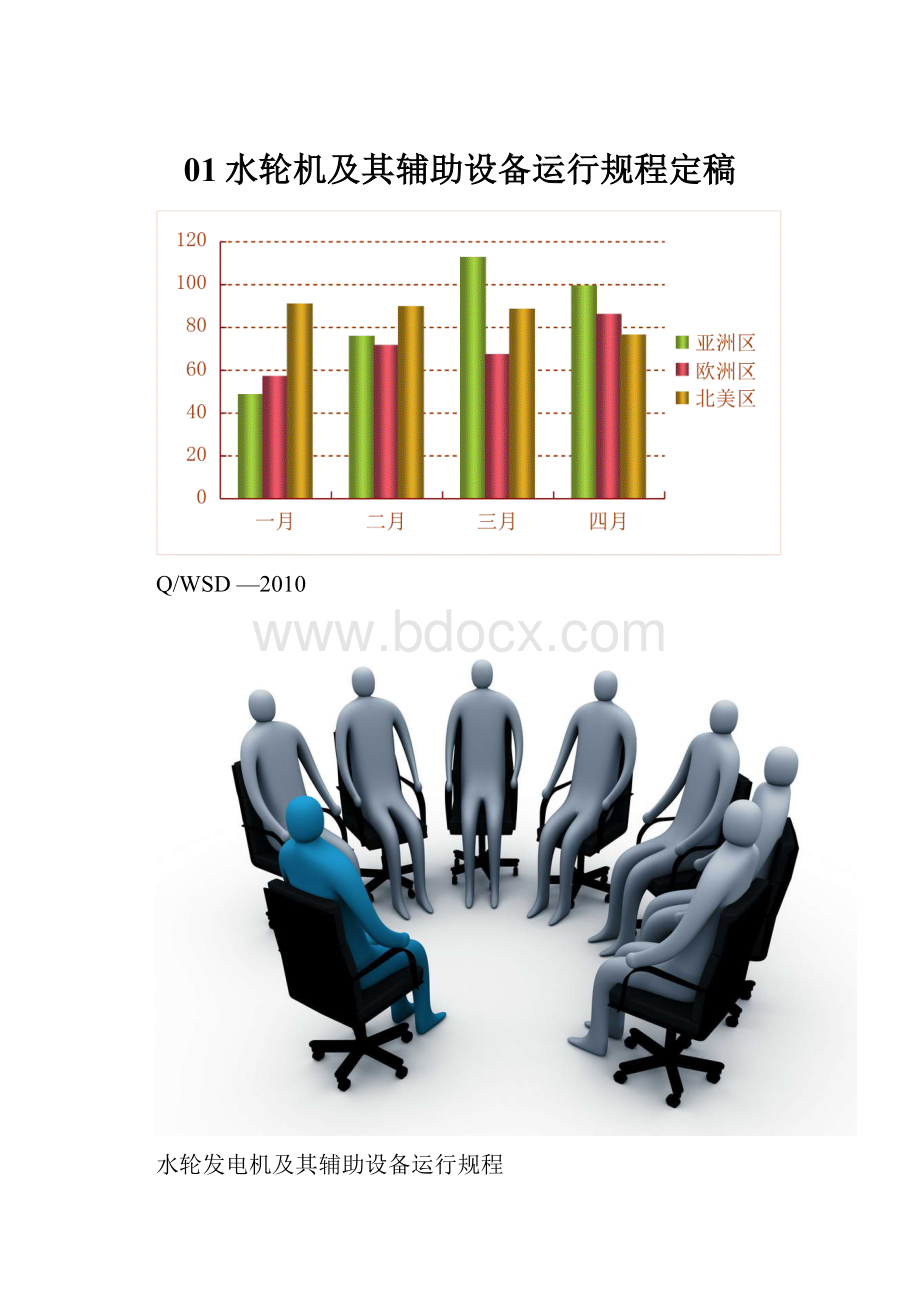
01水轮机及其辅助设备运行规程定稿
Q/WSD—2010
水轮发电机及其辅助设备运行规程
范围
本标准规定本厂水轮发电机组及其辅助设备的运行注意事项、运行限额数据,机组恢复备用和开停机前的检查,机组检修及试验安全措施,机组故障和事故处理等方面的内容。
本标准适用于水轮发电机组及其辅助设备的运行。
1规范性引用文件
下列文件中的条款通过本标准的引用而成为本标准的条款。
凡是注日期的引用文件,其随后所有的修改单(不包括勘误的内容)或修订版均不适用于本标准,然而,鼓励根据本标准达成协议的各方研究是否可使用这些文件的最新版本。
凡是不注日期的引用文件,其最新版本适用于本标准。
DL/T710—1999《水轮机运行规程》
DL/T792—2001《水轮机调速器及油压装置运行规程》
本标准依据制造厂家有关技术文件。
2水轮发电机运行
注意事项
3.1.1机组注意事项
3.1.1.11F、2F、4F机组调速器上因手操缸反馈钢丝绳已取消,调速器切手操缸操作后无反馈,故其正常运行方式为:
开度机械开度限制全开,其操作增、减按纽电源小空开“断开“位置。
只有机组在停机状态须做防转动措施时,才可将机组开限压至零。
机组运行时,严禁切“手操缸”模式运行,特殊情况必须经发电部和生技部领导同意后方可切“手操缸”控制。
3.1.1.2机组的开停机,尾水门和进水口工作门的起落操作,必须经值守长允许。
对设备的操作、巡回检查、检修交待、定期工作、事故处理等工作完成后,必须向值守长汇报。
3.1.1.3开启机组进水门、尾水门之前应检查下列设备:
a)蜗壳、支持盖、尾水管、转轮室各人孔门均已封闭。
b)蜗壳、尾水管各盘形排水阀全部关闭并锁锭。
c)压油装置和事故压油装置工作正常。
d)调速系统工作正常,导水叶全关。
e)顶盖排水泵工作正常。
f)机坑漏油泵工作正常。
g)主轴密封水投入或空气围带投入。
h)进水口检修门在提起位置。
3.1.1.4Q/WSD105
范围1
注意事项1
3.1.1.5
3.1.1.6闸门的操作顺序:
机组检修:
先关进水口检修门,后关尾水门;检修后恢复备用:
先开尾水门,后开进水口检修门。
3.1.1.7机组继电保护、自动装置和仪表的整定值,运行或备用机组的有关设备,任何人员不得任意改变和退出。
机组水机保护(机组过速、轴承超温、事故低油压)的投、退,应得到生产付厂长(或总工程师)批准后方可进行,执行后应通知发电部、维护、生产技术部相关负责人。
3.1.1.8设备经过检修后,办票人员应进行全面检查,并会同检修人员进行必要的启动操作试验,同时要求进行检修交待。
3.1.1.9油、水、风系统检修后应做设备启停、充油、充水、充气等试验,不得有漏油、漏水、漏气现象。
3.1.1.10机组大修、小修工作结束,检修各工作面应在检修记录本上对检修情况进行交待。
机组大、小修过程中安全措施的增减应由工作总负责人与值守长联系,检修机组安全措施的拆除、机组的启、停等试验必须得到值守长的命令方可进行。
3.1.1.11机组停机备用时,应投入机组大轴密封水止漏,密封水压一般调整在0.02—0.05Mpa之间。
停机后若顶盖漏大,可用气将大轴密封块顶起,若经多次冲气无效漏水依然较大,可投入空气围带止水。
3.1.1.12机组因防转动措施投入2GDP后,应注意监视事故油槽油压、油位,以及相邻机组回油箱油位有无异常,防止非供油机组回油箱溢油或供油机组的回油箱油位过低。
3.1.1.13机组做防转动措施需投入2GDP前,为减少对油系统管路的冲击,可按以下步骤操作:
全关X151阀--投入2GDP电磁阀--缓慢打开X151阀--检查事故配压阀投入正常—全开X151阀。
3.1.1.14机组压油装置或高压气系统贮气罐零起建压时,则应将各机组压油装置自动补气回路关闭。
3.1.1.15做措施时关闭5DF、6DF阀前,应将机组的二台技供泵设置为“检修态”,操作把手放“切”。
非汛期时,应将机组的技供泵设置为“检修态”,并切断其动力电源。
3.1.1.16机组大修后,在蜗壳未充水前恢复技术供水系统,应先开2DF、4DF,再手动慢慢打开5DF一点,停顿一下之后,再将5DF开到所需开度,同时不得将6DF打开,以防止水锤或管路振动破坏设备。
机组技术供水人为停止后要恢复时,应按前面的操作步骤进行。
机组备用时,5DF、6DF在开位置。
3.1.1.17监控上若出现机组排水压力异常升高或降低,应检查1DF—4DF位置或进行正反向供排水倒换与滤水器反冲排污,必要时调整总排水阀X208阀的开度。
3.1.1.18若机组空冷器进出水压力差大于0.04MPa,应进行正反向供排水倒换或滤水器倒换。
3.1.1.19机组压油装置通往事故油槽的供油小阀门只能打开一个。
3.1.1.20正常运行方式下,机组×101阀电源空气开关、阀门控制器电源小开关均应在断开位置。
若需操作×101阀,应先投入×101阀电源空气开关,再投入阀门控制器电源小开关,操作完后及时拉开电源。
3.1.1.21机组小修时,若×101阀未关,此时压油泵一定要能自动运行,否则要设专人监视压油槽压力和油位。
3.1.1.22机组检修结束前,若开×101阀,则机组漏油泵应恢复自动或手动运行,防止漏油箱溢油。
175F机组检修做措施时,为防止调速系统油管振动而损坏设备应严格按照先关5101阀,再关5101-1阀;拆除措施时应先打开5101-1阀,再开5101阀。
3.1.1.23复归调速器电柜故障时,应注意调速器可能会溜负荷,若出现异常,应立即切手动,调整好机组负荷。
3.1.1.24机组运行过程中若因永磁机、转速信号器等故障,出现“不定态”造成机组不能增减负荷、
Q/WSD—2010
停机等现象时,可将机组转速信号切换压板切至北疆DJ1010型转速信号器工作。
3.1.1.25机组并网运行中,如出现紧急情况,按机旁盘“紧急停机”按钮后,将启动事故停机流程,跳开机组出口开关,实现紧急事故停机。
机组事故配压阀动作后的复归,必须到现场检查、确认事故配压阀复归是否到位。
3.1.1.26压油泵先导阀控制操作电源取至本泵交流电源,若压油泵不能建压,打不上油,应检查先导阀控制电源保险。
3.1.1.27做机组压油泵或顶盖泵检修安措时,应在监控上将其设为“检修”态。
恢复时,应记住将其设为“运行”态。
3.1.1.28目前,1-4号机组漏油箱各安装一套油混水装置;5号机装有4套油混水装置,分别为推力、水导、上导、漏油箱,油混水装置上有红线和绿线二根线条指示,当绿线超过红线时,报油混水信号。
3.1.1.29我厂机组转速保护共设置了电气115%Ne、140%Ne两级、以及纯机械液压145%NE过速保护。
115%Ne、140%Ne过速保护接点信号取自ZZX-4(6)转速信号器。
当出现机组直流电源消失、转速信号继电器等电气故障时,机组电气115%Ne、140%Ne两级过速保护均失灵,机组转速上升到145%Ne左右时,安装大轴上的机械甩块在离心力的作用下,撞击油路切换阀,利用备用油源直接关闭导叶并启动事故停机流程。
3.1.1.30目前,我厂1、2、3、5号机组分段关闭流程存放于现地PLC中。
当事故停机或甩负荷试验时,导叶关闭到主接行程的30--35%左右,启动PLC中分段关闭流程,分段关闭电磁阀动作开放油路。
分段关闭电磁阀动作后由自动停机继电器复归。
各机组在分段关闭阀上安装了一个反馈接点,即当分段关闭阀投入时,该接点接通动作并报“分段关闭阀动作”信号,并闭锁“空载”开机流程(开机条件不满足)和“甩负荷试验”流程。
机组在运行过程中或甩负荷后机组未停机时,一旦出现“分段关闭阀动作”报警信号,值班员守长立即安排人员到现场检查并复归分段关闭电磁阀。
3.1.2备用机组注意事项
3.1.2.1备用机组应处于下列状态:
a)进水口闸门和尾水闸门全开。
b)各动力电源、操作电源正常、机组在“停机”态,现地LCU运行正常。
c)机组保护及自动装置良好并投入使用。
d)压油装置和事故压油装置工作正常。
e)调速器在自动,导叶全关,机械开限在相应水头的额定出力位置。
事故电磁阀和事故配压阀未动作。
f)各轴承油槽及集油槽油位正常、油质合格。
g)制动风压在0.55∽0.70MPa,风闸全落下。
h)主轴密封装置及顶盖排水系统完好。
i)漏油泵在自动。
j)机组油、水、风系统处于备用状态,各阀门处于正常运行位置。
k)中控室上位机上机组状态为“停机”态。
3.1.2.2未经值长同意,不准在备用机组上进行影响机组备用的工作。
3.1.2.3应对备用机组及其辅助设备进行巡回检查和监视其状态。
Q/WSD—2010
3.1.3开停机注意事项
3.1.3.1机组安全稳定运行水头范围12.8∽32.3M,在7.8∽12.8M水头下发电时应加强对机组监视,若遇异常应立即处理或停机。
3.1.3.2运行人员应注意检查调速器电柜上的水头设定值是否与实际值一致,汛期应根据水头变化及时调整机组运行水头。
3.1.3.3自动开停机过程中,若自动装置动作不良,应手动帮助并及时通知维护人员处理。
3.1.3.4事故停机后,未查明原因和未排除故障前不准再次开机,各种故障、事故信号未经值守长许可,不得复归。
3.1.3.5机组开停机调整负荷以中控室自动操作为主,因试验需要或特殊情况(转速信号器故障,调速器运行不稳定等)可手动操作,机组大修后首次开机,应手动操作。
3.1.3.6机组遇下列情况应手动加闸:
a)顺控停机流程未完成而退出。
b)制动电磁阀动作不正常。
c)转速继电器故障。
d)手动停机。
3.1.3.7若顺控停机不成功,可再次发“停机”令。
3.1.3.8若顺控开机发电不成功,可再次发“发电”令。
3.1.4运行中注意事项
3.1.4.1正常运行中,调速器应在自动运行,1、2、4F机组机械开度限制应在全开位置。
3.1.4.2机组正常运行2~3小时后,轴承温度或油温在负荷不变的情况下升高2-3度或出现普遍下降时,应及时查明原因(轴承油位是否偏低或偏高,冷却水是否正常,油槽是否进水等)进行处理,并加强监视,汇报值长。
3.1.4.3机组运行出现振动、摆度超过允许范围,应立即调整负荷使机组脱离异常工况运行。
3.1.4.4机组发生冲击后,应在上位机检查有关运行参数值有无较大变化,机组各部有无异常情况出现。
3.1.4.5系统事故造成机组甩负荷时,应使机组维持空载运行,做好随时并网准备。
同时注意检查分段关闭动作情况(运行监控语音光字报警)并复归
3.1.4.6调速器自动运行不稳定时,应将调速器切手动运行(1、2、4F为手动脉冲、3、5F为手动),
汇报值守长通知维护人员处理,并现场监视运行情况。
3.1.4.7发电机空气冷却器水压根据水温、负荷变化及时调整,保持其温度均匀。
同时注意进出水压差不能超过规定值,否则应进行正反向倒换或调节出水阀开度。
3.1.4.8运行中不能同时将相邻的两个空气冷却器同时停水。
3.1.4.9运行中若主轴密封漏水大或顶盖排水泵故障,应设法排除故障,恢复水泵运行,并及时调整密封水压,尽快降低顶盖水位。
3.1.4.10运行中发现受油器大量甩油,致使油盆积聚大量漏油,应调整运行工况减小漏油量。
3.1.4.11若上游水位低,造成用加压供水泵对机组供水,若二台技术供水泵出现故障不能恢复时,应改为自流供水,同时将主变冷却水倒至由相邻的机组供给。
3.1.4.12技术供水泵投入运行时,应加强监视水泵电动机运行情况,防止电动机及轴承过热,水泵盘
Q/WSD—2010
根漏水过大。
3.1.4.13机组运行中或停机后发现真空破坏阀漏水,应及时处理,一时不能处理要联系检修处理。
3.1.4.14机组停机后,若顶盖漏水特大,应投空气围带。
3.1.4.15机旁动力盘Ⅰ、Ⅱ段母线运行方式倒换操作规定:
a)正常运行时,Ⅰ、Ⅱ段母线分段运行,特殊情况或事故处理需要时可联络运行。
b)动力母线倒换操作或电源消失后的恢复,应做好辅助设备的倒换操作,以防断电。
c)当一个刀闸控制多个负荷时,若须拉开该刀闸,应注意有些负荷事先须倒换好。
3.1.4.16机组参加AGC调节时,若压油泵启停频繁,致使压油槽内的油太烫,可向中调申请将该台机退出AGC调节,并将情况汇报有关领导。
3.1.4.17机组运行时,若事故低油压压力表大量漏油或喷油,应立即切除事故低油压压板,关闭事故低油压压力表进油阀。
若不能判断为哪一块具体压力表喷油需关闭总进油阀前,也应将事故低油压压板切除,同时应通知值守人员将油泵控制方式切换为模拟量控制。
3.1.4.18关于机组技术供水操作的规定:
a)机组检修后技术供水系统充水程序:
1)开启X208排水阀。
2)开启1DF、2DF、4DF供水或3DF、4DF、2DF供水。
3)手动慢慢开启机组供水取水阀5DF、6DF。
4)关闭4DF或2DF。
b)机组技术供水正、反向切换操作:
1)正常情况下,通过流程进行正、反向供水切换。
2)如不能进行流程自动切换,必须在1DF、2DF、3DF、4DF全开情况下,再关闭1DF、2DF或关闭3DF、4DF,实现正、反向切换。
c)做安全措施切断技术供水时,必须先关闭1DF(正向供水)或3DF(反向供水),后关闭2DF或4DF;恢复措施时(若5DF或6DF)在开)先开启2DF或4DF后,再手动将1DF或3DF缓慢打开30%
左右开度,待系统压力平稳后,逐渐将1DF或3DF全开。
d)单步或现场进行1DF、2DF或3DF、4DF的电动操作或调试必须在反向供水操作切换成功或正向供水操作切换成功后进行。
3.1运行限额参数
3.2.1转速限额(表1)
Q/WSD—2010
表1:
转速限额
名称(测量元件)
作用
整定值(N/ne)
备注
额定转速(1YH,永磁机)
飞逸转速(永磁机)
机械过速
二级过速(1、2ZSX)
一级过速(1、2ZSX)
启励转速(1ZSX)
加闸转速(1ZSX)
停机复归转速(1ZSX)
SP动作,停机
2GDP.SP动作,停机
1GDP.SP动作,停机
机组建压
机组加闸
停机复归
100%
209%(5F:
241%)
145%
140%
115%
95%
20%
5%
76.9转/分
160.4转/分(5F:
185转/分)
频率10HZ
3.2.2温度限额(表2)
表2:
温度限额
名称
运行温度
报警温度(高限)
报警温度(高高限)
停机温度(两块瓦超温)
推力瓦温
发导瓦温
水导瓦温
冷风温度
冷却水温
转子线圈温度
定子线圈温度
热风温度
<60℃
<60℃
<60℃
<37℃
<30℃
<130℃
<120℃
<55℃
55℃
57℃(5F:
60℃)
57℃(5F:
60℃)
57℃
62℃(5F:
65℃)
62℃(5F:
65℃)
60℃
65℃
65℃
3.2.3压力限额(表3)
表3:
压力限额
部位
名称
压力(MPa)
备注
最低
最高
油压装置
压力油槽
事故油槽
备I油压
备II油压
3.55
3.55
3.45
3.30
4.0
4.0
4.0
4.0
事故低油压
2.75
风压
制动风压
围带风压
0.55
0.55
0.7
0.7
技术供水水压
水导冷却水压
发导冷却水压
推力冷却水压
空气冷却水压
大轴密封水压
空冷器水压差
0.1
0.1
0.1
0.05
0.02
0.3
0.3
0.3
0.20
0.15
0.04
(报越高限)
Q/WSD—2010
3.2.4机组各部油位限额(表4)
表4:
机组各部油位限额
名称
静止油位(mm)
运行油位(mm)
上限
下限
上限
下限
推力油槽
水导油槽
压力油槽
事故油槽
集油槽
漏油槽
5F上导油槽
+20(5F:
530)
+20(5F:
480)
1900
650
1200
330(5F:
450)
230
-20(5F:
440)
-20(5F:
390)
1200
400
500
25
140
+70(5F:
530)
+20(5F:
480)
1900
650
1200
330(5F:
450)
230
-20(5F:
440)
-20(5F:
390)
1200
400
500
25
140
3.2.5振动及摆度限额(表5)
表5:
振动及摆度限额
项目
水导摆度
发导摆度
定子外壳振动
机架振动
水平
垂直
水平
垂直
高限值
60×0.01mm
60×0.01mm
4×0.01mm
10×0.01mm
4×0.01mm
10×0.01mm
高高限值
65×0.01mm
65×0.01mm
6×0.01mm
12×0.01mm
6×0.01mm
12×0.01mm
3.2.6时间限额(表6)
表6:
时间限额
项目
整定值(秒)
作用
一级过速保护延时
轴承过热保护延时
导叶直线关闭时间
加闸延时
5
10(5F:
14)
120
发信号并停机
发信号并停机
3.2.7水机保护一览表(表7)
表7:
水机保护一览表
保护名称
测量元件
整定值
动作后果
机械过速
二级过速
轴承超温
事故低油压
一级过速
轴承温升
主用油槽油位异常
备用油槽油位异常
油混水
推力油槽油位异常
1ZSX,2ZSX
WZX
事故低油压力表
1,2ZSX,EXWK
WZX
YWB
23FZX
YSX(5F:
YHS1-YHS4)
YWX
145%Ne
140%Ne
65℃(两块瓦同时超温,推力瓦为60℃)
2.75MPa
115%Ne
60℃(推力瓦为55℃高限、57℃高高限)
≧1900mm或≦1200mm
≧650mm或≦400mm
超表4上、下限参数
停机
停机
停机
停机
停机
停机
发信号
发信号
发信号
发信号
Q/WSD—2010
续上表
保护名称
测量元件
整定值
动作后果
水导油槽油位异常
5F机组上导油位异常
漏油箱油位升高
剪断销剪断
机组断水
滤水器堵塞
顶盖水位升高
密封水压中断
测温表及转速信号故障
YWX
Sayw
YLX
JDX
(1∽3)SLX5F:
CZX
YWX
MYX
WZJ.1ZSX'
≧230mm或≦140mm
超表4上限
0.03MPa
水压为“0”及顶盖“备II”水位同时满足
发信号
发信号
发信号
发信号
发信号
发信号
发信号
发信号
发信号
3.2机组恢复备用操作和开机前的检查
3.3.1调速器液压柜和电气柜的检查
3.3.1.1电柜水头指示与实际水头相符,必要时手动调整。
3.3.1.2导叶、轮叶均在自动位置,机柜油压表指示正常。
3.3.1.3柜内外清洁无杂物,各管路接头无漏油现象,阀门位置正确,无油路堵塞信号。
3.3.1.4传动杠杆完整无脱离现象,销钉无脱落,转动无蹩劲、松动、卡阻现象。
3.3.1.5电液比例伺服阀运行正常,无发卡现象。
3.3.1.6各电源投入良好,仪表指示正常。
3.3.1.7各运行参数整定正确。
3.3.1.8各部端子接触良好,继电器完好无异常。
3.3.2压油装置
3.3.2.1操作盘上切换开关位置正确,压油泵自动启动流程工作正常,上位机上在”运行”态。
3.3.2.2各接触器、热继电器完好无异常,操作保险装上无熔断。
3.3.2.3阀门控制器工作正常,X101油阀全开。
3.3.2.4压油泵运行无异音和剧烈振动,打油建压正常。
3.3.2.5集油槽油位正常。
3.3.2.6设备清洁、阀门位置正确,无漏油、漏气现象。
3.3.2.7压油槽、事故压油槽压力、油位正常,压力信号器,各变送器工作正常。
3.3.2.8自动补气流程投入,自动补气装置工作正常。
3.3.3机旁盘
3.3.3.1制动柜上转速为0,各阀门位置正确无漏气现象,风压正常,“风闸落下”灯亮。
3.3.3.2调速器电柜工作正常,水头设定符合实际水头。
3.3.3.3现地LCU,主、辅PLC工作正常,联机秒灯闪烁。
Q/WSD—2010
3.3.3.4机组同期装置电源投入。
3.3.3.5各盘柜交、直流操作电源投入正常,各按钮位置正确。
3.3.3.6各继电器正常投入,各监视指示灯正确。
3.3.3.7温度巡检装置工作正常。
3.3.4机旁动力盘
3.3.4.1动力盘Ⅰ、Ⅱ段母线分段运行,电压指示、信号指示灯正常。
3.3.4.2各部接头无松动、无过热变色现象。
3.3.4.3各用电设备开关、刀闸投入良好,位置正确。
3.3.4.4各保护信号继电器正常,无动作信号。
3.3.4.5应挂的各种标示牌齐全、完好。
3.3.5发电机部分
3.3.5.1机组消防水压正常,消防供水阀不漏水。
3.3.5.2永磁机内、外清洁无杂物,轮叶指示正确无异常。
3.3.5.3励磁滑环及碳刷接触完好。
3.3.5.4风洞内无杂物,照明良好。
3.3.5.5推力油槽油位、油色正常。
3.3.5.6冷却水压合格,各管路阀门位置正确,空气冷却器无渗漏现象。
3.3.6水轮机部分
3.3.6.1各部清洁无杂物。
3.3.6.2各部水压指示正常,油、水、风系统各阀门位置正确。
3.3.6.3受油器回油畅通,回复钢丝绳无松动、断股现象,万向联轴器完好。
3.3.6.4导叶接力器锁锭拔出,密封良好。
3.3.6.5导叶回复机构、分段关闭装置完好。
3.3.6.6剪断销无破断,真空破坏阀不漏水。
3.3.6.7水导油槽油位油色正常。
3.3.6.8机组过速机械接点与参照指针平行位置正确。
3.3.6.9顶盖漏水正常,顶盖排水系统工作正常。
3.3.6.10漏油泵在”自动”。
3.3.6.11围带排气,主轴密封水投入。
3.3.7技术供水室
3.3.7.1滤水器运行正常,无漏水现象。
3.3.7.2各阀门控制器工作正常,控制开关放在”远控”位置。
3.3.7.3各控制电源投入正常,开关位置、仪表指示正常。
3.3.7.4供水系统水压正常,管路阀门无漏水,水泵甩水正常。
Q/WSD—2010
3.3机组及其辅助设备运行一般操作
3.4.1手动开机操作(停机—空载)
3.4.1.1查压油装置油压、油位正常。
3.4.1.2查密封水压正常,查冷却水正常。
3.4.1.3查锁锭拔出。
3.4.1.4查发电机断路器在断开,单步合上发电机出口刀闸。
3.4.1.5查轮叶在“自动”控制。
(3、5F为“手动”)
3.4.1.6将调速器导叶切“手动脉冲”(3、5F为“手动”)控制。
3.4.1.7按导