高温轴承9Cr18Mo.docx
《高温轴承9Cr18Mo.docx》由会员分享,可在线阅读,更多相关《高温轴承9Cr18Mo.docx(17页珍藏版)》请在冰豆网上搜索。
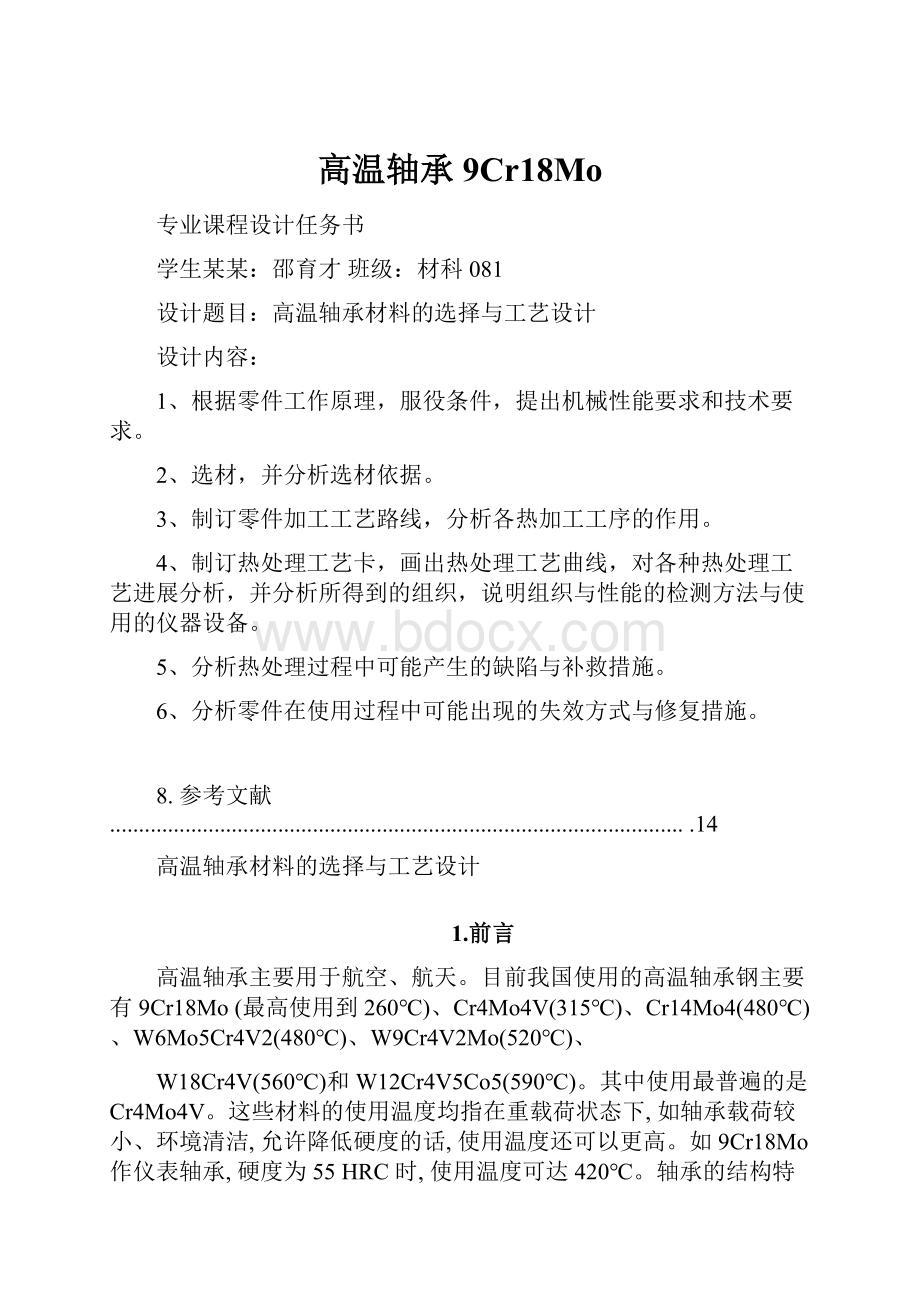
高温轴承9Cr18Mo
专业课程设计任务书
学生某某:
邵育才班级:
材科081
设计题目:
高温轴承材料的选择与工艺设计
设计内容:
1、根据零件工作原理,服役条件,提出机械性能要求和技术要求。
2、选材,并分析选材依据。
3、制订零件加工工艺路线,分析各热加工工序的作用。
4、制订热处理工艺卡,画出热处理工艺曲线,对各种热处理工艺进展分析,并分析所得到的组织,说明组织与性能的检测方法与使用的仪器设备。
5、分析热处理过程中可能产生的缺陷与补救措施。
6、分析零件在使用过程中可能出现的失效方式与修复措施。
8.参考文献....................................................................................................14
高温轴承材料的选择与工艺设计
1.前言
高温轴承主要用于航空、航天。
目前我国使用的高温轴承钢主要有9Cr18Mo(最高使用到260℃)、Cr4Mo4V(315℃)、Cr14Mo4(480℃)、W6Mo5Cr4V2(480℃)、W9Cr4V2Mo(520℃)、
W18Cr4V(560℃)和W12Cr4V5Co5(590℃)。
其中使用最普遍的是Cr4Mo4V。
这些材料的使用温度均指在重载荷状态下,如轴承载荷较小、环境清洁,允许降低硬度的话,使用温度还可以更高。
如9Cr18Mo作仪表轴承,硬度为55HRC时,使用温度可达420℃。
轴承的结构特点和工作条件要求轴承材料必须具备高的硬度、耐磨性、接触疲劳强度、弹性极限、良好的冲击韧性、断裂韧性、尺寸稳定性、防锈性能和冷热加工性能。
为保证这些性能要求,对轴承用钢提出了严格要求的冶金质量。
2.高温轴承工作条件与性能要求
通常认为超过120℃的温度条件,便算是高温工作条件,此时普通轴承钢会发生组织变化和屈服强度降低,精度逐步丧失;而当轴承工作温度超过轴承材料回火温度时,其硬度就明显下降,工作温度超过180℃时硬度就急剧下降,很快出现早期疲劳和磨损。
保证轴承在高温下运转精度和使用寿命的中心环节是保证轴承在高温下具有足够的硬度和尺寸与形状的稳定程度,因此对于高温轴承钢提出如下要求,1)高温下硬度不低于HRC50~56;金相组织稳定;
2)高温尺寸稳定性良好,温度膨胀系数小,没有显著的组织变化,抗蠕变性好,剩余应力小;
3)抗氧化性好,生成的氧化膜与基体结合结实,而且耐磨性和疲劳强度好,耐热震性好,能经受较快的温度变化,导热性要好;
4)作为轴承钢所应有的其他材料特性。
如高温耐冲击性能、低的热膨胀性和高的抗蠕变强度和高温尺寸稳定性等。
3.高温轴承技术要求
2.1硬度
套圈和滚动体淬火后硬度一般不应低于63HRC。
回火后硬度:
套圈为60HRC~65HRC:
滚动体为61HRC~66HRC。
2.2同一零件的硬度差
淬、回火后同一零件的硬度差为;
a)套圈外径不大于100mm,滚动体直径不大于22mm时,同一零件硬度差不应大于1HRC:
b)套圈外径大于100mm,滚动体直径大于22mm时,同一零件硬度差不应大于2HRC;
c)钢球直径不大于1.588mm(1/16in)不检查同一零件硬度差。
2.3脱碳层
轴承零件的脱碳层应在最深处测量,其深度不应超过淬火前每边最小加工余量的三分之二。
2.4回火稳定性
按零件的正常回火温度重新回火2h,在原来位置相应点测量硬度,相应点的最大硬度差不得超过1HRC。
2.5裂纹和软点
轴承零件淬、回火后与磨加工过程中不应有裂纹和软点。
2.6脱碳层和其他外表缺陷
轴承零件经淬、回火后产生的外表脱碳层、腐蚀坑和氧化皮等缺陷应在磨加工过程中除净,成品轴承零件不应有脱碳层和其他外表缺陷。
4.9Cr18Mo高温轴承钢
9Cr18Mo钢是一种高碳高铬马氏体不锈钢,它是在9Cr18钢的根底上加Mo而开展起来的,因此它具有更高的硬度、高耐磨性、抗回火稳定和腐蚀性能,该钢还具有较好的高温尺寸稳定性,适宜制造在腐蚀环境条件下又要求高负荷、高耐磨的塑料模具。
该钢属于莱钢体,容易形成不均匀碳化物偏析而影响模具使用寿命,所以在热加工时必须严格控制热加工工艺。
9Cr18Mo钢的化学成分〔GB/T1220—1992〕w/%
C
Si
Mn
Cr
Mo
S
P
≤
≤
0
≤
≤
主要元素的作用:
碳(C):
钢中含碳量增加,屈服点和抗拉强度升高,但塑性和冲击性降低,碳能增加钢的冷脆性和时效敏感性。
铬(Cr):
能显著提高强度、硬度和耐磨性,但同时降低塑性和韧性。
钼(Mo):
钼能使钢的晶粒细化,提高淬透性和热强性能,在高温时保持足够的强度和抗蠕变能力。
3.2物理性能
9Cr18Mo钢的物理性能示于表4-19-2和表4-19-3,其热导率〔20℃〕λ为29.3W/(m·K)。
9Cr18Mo钢的临界温度
临界点
Ac1
Ar1
Ms
温度〔近似值〕/℃
815~865
765~665
145
9Cr18Mo钢的线〔膨〕胀系数
温度/℃
20~100
20~200
20~300
20~500
线〔膨〕胀系数/℃-1
×10-6
×10-6
×10-6
×10-6
9Cr18Mo钢热加工工艺示于表4-19-4。
表4-19-49Cr18Mo钢的热加工工艺
项目
加热温度/℃
开始温度/℃
终止温度/℃
冷却
钢锭
钢坯
1130~1150
1100~1120
1080~1095
1050~1080
850~900
850~900
砂冷
砂冷
9Cr18Mo钢的热处理示于表4-19-5,与热处理有关的曲线示于图4-19-1图4-19-5,与热处理有关的性能示于表4-19-6和表4-19-7。
表4-19-59Cr18Mo钢的热处理
工序名称
退火
再结晶退火
淬火
回火
加热温度和保温时间
850~870℃4~6h
730~750℃
1050~1100℃
150~160℃2~5h
冷却
30℃/h冷至600℃,空冷
空冷
油冷
空冷
硬度〔HB〕
≤255
HRC≥58
为减少剩余奥氏体数量,可以于-75~80℃冷处理。
表4-19-69Cr18Mo钢的室温力学性能
热处理
σb/MPa
δ5
ψ
ak/J·cm-2
HRC
/%
850℃退火
1060℃淬火,150℃回火
760
16
40
HB≤225
61
表4-19-79Cr18Mo钢的耐腐蚀性能
热处理制度
硬度
〔HRC〕
介质条件
腐蚀速度/g·〔m2·h〕-1
介质
浓度/%
温度/℃
1050℃油淬
硫酸
硫酸
硝酸
2
5
40
沸腾
沸腾
沸腾
1050℃油淬
150℃回火1h
硫酸
硫酸
硝酸
2
5
40
沸腾
沸腾
沸腾
5.高温轴承加工工艺
轴承由四局部构成:
外圈、内圈、滚子和保持架。
其总的加工工艺是:
下料-成型-退火-车加工-热处理-磨加工-装配等。
4.1成型
4外圈、内圈锻造成型工艺
9Cr18Mo钢在锻造时的要求:
(1)锻造模具应预热,预热温度在300℃左右
(2)坯料端面与外外表不能有裂纹,假如发现有裂纹,应与时去除。
(3)锻造过程中不能用水冷却模具,以免毛坯接触水引起材料开裂。
(4)模具可采用石墨为主的润滑剂润滑。
4滚子和保持架成型工艺
a〕滚子
热冲球,软磨。
b〕保持架
切环、冲压成型,整形和冲孔。
4.2外、内圈退火
退火就是将轴承钢加热到Ac3以上温度,保温一段时间以适当的速度冷却,以降低硬度、改善组织、提高此后的车加工性能。
9Cr18Mo轴承零件退火后的组织为粒状珠光体,硬度为197HB~241HB(压痕直径为4.3mm~3.9mm)或94HRB~100HRB。
轴承零件的脱碳层应在最深处测量,其深度不应超过淬火前每边最小加工余量的三分之二。
4.3外、内圈车加工
车加工主要有车内径、倒角、车沟道和车两侧密封槽。
由于存在合金元素,使钢的拉伸、屈服强度、塑性和韧性都增高,切削加工性变差。
不锈钢的强度,特别是高温强度和硬度高,切削时的变形大,切削力与切削热亦大,而导热性差,使刀具易发热和产生塑性变形,降低了刀具的切削能力,使刀具的磨损加剧。
由于钢的这些特殊性质,在车加工中,刀具材料、切削速度与切削液的选择都是影响套圈加工效率和质量的关键因素。
刀具的选择和使用:
根据轴承钢的特性因此,要求刀具材料必须具有很高的硬度,良好的耐磨性与耐热性以与能承受一定的冲击载荷。
另外,合理选择刀具角度是保证加工质量和刀具寿命的重要因素,同时还要勤于观察刀具磨损情况,与时更换刀具,提高工件外表质量和尺寸精度。
切削速度:
车加工时,提高切削速度,这样能使切屑底层与刀具前刀面摩擦产生的温度增高,使这一薄层金属变软,甚至已成微熔状态,形成润滑膜,能起到一种特殊的润滑作用,使切削变形减小。
因此提高切削速度可减小车削加工变形与切削力,降低外表粗糙度。
切削液:
在加工中应参加切削液,它能带走切削区的大量热,降低切削温度,减小热变形与刀具磨损,与时冲走碎屑,提高加工效率。
4.4热处理
球化退火
球化退火作为预备热处理,以改善组织性能。
如果存在严重网状碳化物等缺陷组织时,在球化退火前须进展一次正火,消除网状、改善碳化物分布。
800~920℃,缓冷。
4.4.2淬火工艺
淬火后要获得的组织为马氏体、碳化物和剩余奥氏体。
硬度要求为64HRC左右。
a〕淬火温度
9Cr18Mo钢中含有大量难溶解的碳化物,如加热温度稍高于Ac1〔815-850℃〕淬火,碳化物的溶解量较少,随着温度的升高,碳化物不断向奥氏体中溶解,使奥氏体合金化浓度不断增加,同时奥氏体晶粒度呈长大的趋势,使淬火后钢中的剩余奥氏体量增加。
如图,钢中剩余奥氏体的数量随淬火加热温度的上升而增加,加热温度达到1150℃时,钢中奥氏体含量达到90%以上,当加热温度达1200℃时,钢中根本上成为奥氏体组织。
钢中碳化物的含量随淬火加热温度的上升而减少,在1050-1125℃温度下碳化物的含量显著减少。
图19Cr18Mo钢淬火奥氏体化温度对钢中剩余奥氏体
和碳化物含量的影响
因此,综合以上分析,应当是9Cr18Mo钢淬火温度确定在1110℃左右。
其淬火工艺分为三个阶段:
650℃左右一次预热,850℃左右二次预热以与1110℃烧透和合金化。
b〕加热时间
研究明确,随着淬火加热时间的延长,钢中的剩余奥氏体量逐渐增加。
经过试验和综合分析,将淬火加热时间保持60分钟左右。
c〕冷却方式
试验结果明确,随着冷却时间的延长,剩余奥氏体量逐渐减少。
因此钢的冷却方式为随炉冷却。
d〕炉子的选择
传统的炉子加热易导致钢的氧化脱碳现象,此高温轴承要求精度高,使用性能优良,综合考虑应使用真空淬火炉。
综合以上分析,轴承淬火工艺曲线如如下图所示:
图2淬火工艺曲线
4.4.3冷处理
冷处理是精细轴承的尺寸稳定化处理。
冷处理温度一般为-30~-80℃,时间1-1.5小时。
淬火后立即进展,减少剩余奥氏体。
冷处理后正常回火。
回火工艺
回火后钢的组织为回火马氏体、碳化物和少量剩余奥氏体,硬度要达到63-64HRC。
对于9Cr18Mo材料回火而言,回火温度、回火次数和冷却方式对剩余奥氏体的转变影响较大,而回火时间影响较小,通常将回火时间定为120分钟。
a〕回火温度
随着回火温度的升高剩余奥氏体量不断减少。
为使钢的硬度既达到标准要求,又能使剩余奥氏体含量减少到规定的X围内,回火温度选取为545-555℃。
b〕回火次数
由于剩余奥氏体中析出弥散的碳化物,使剩余奥氏体的合金度降低,Ms升高。
在回火冷却过程中,剩余奥氏体又转变成为二次马氏体。
所以,进展屡次回火对剩余奥氏体的转变是有效的。
通常将回火次数定为3次。
c〕冷却方式
冷却方式对剩余奥氏体没有太大的影响,考虑到节能,可选择随炉冷却。
d〕炉子的选择
同淬火工艺类似,采用真空回火炉。
因此,回火工艺曲线如下
图4回火工艺曲线
4.5磨加工
4磨加工套圈
磨削套圈双端面-粗磨套圈外圆-精磨套圈外圆
a)外圈:
精磨外圈沟道-修磨外圈外径-清洗
b)内圈:
精磨内径-精磨内圈沟道-清洗
4磨加工钢球、保持架
粗磨-校正-精磨-清洗
4.6装配
套圈、钢球分选合套-装保持架-校正-清洗-装箱
6.热处理过程中可能出现的缺陷与补救
5.1缺陷
轴承零件经热处理后常见的质量缺陷有:
淬火显微组织过热、欠热、淬火裂纹、硬度不够、热处理变形、外表脱碳、软点等。
a〕过热从轴承零件粗糙口上可观察到淬火后的显微组织过热。
但要确切判断其过热的程度必须观察显微组织。
假如在钢的淬火组织中出现粗针状马氏体,如此为淬火过热组织。
形成原因可能是淬火加热温度过高或加热保温时间太长造成的全面过热;也可能是因原始组织带状碳化物严重,在两带之间的低碳区形成局部马氏体针状粗大,造成的局部过热。
过热组织中残留奥氏体增多,尺寸稳定性下降。
由于淬火组织过热,钢的晶体粗大,会导致零件的韧性下降,抗冲击性能降低,轴承的寿命也降低。
过热严重甚至会造成淬火裂纹。
b〕欠热淬火温度偏低或冷却不良如此会在显微组织中产生超过标准规定的托氏体组织,称为欠热组织,它使硬度下降,耐磨性急剧降低,影响轴承寿命。
c〕淬火裂纹轴承零件在淬火冷却过程中因内应力所形成的裂纹称淬火裂纹。
造成这种裂纹的原因有:
由于淬火加热温度过高或冷却太急,热应力和金属质量体积变化时的组织应力大于钢材的抗断裂强度;工作外表的原有缺陷〔如外表微细裂纹或划痕〕或是钢材内部缺陷〔如夹渣、严重的非金属夹杂物、白点、缩孔剩余等〕在淬火时形成应力集中;严重的外表脱碳和碳化物偏析;零件淬火后回火不足或未与时回火;前面工序造成的冷冲应力过大、锻造折叠、深的车削刀痕、油沟锋利棱角等。
总之,造成淬火裂纹的原因可能是上述因素的一种或多种,内应力的存在是形成淬火裂纹的主要原因。
淬火裂纹深而细长,断口平直,破断面无氧化色。
它在轴承套圈上往往是纵向的平直裂纹或环形开裂;在轴承钢球上的形状有S形、T形或环型。
淬火裂纹的组织特征是裂纹两侧无脱碳现象,明显区别与锻造裂纹和材料裂纹。
d〕热处理变形轴承零件在热处理时,存在有热应力和组织应力,这种内应力能相互叠加或局部抵消,是复杂多变的,因为它能随着加热温度、加热速度、冷却方式、冷却速度、零件形状和大小的变化而变化,所以热处理变形是难免的。
认识和掌握它的变化规律可以使轴承零件的变形〔如套圈的椭圆、尺寸涨大等〕置于可控的X围,有利于生产的进展。
当然在热处理过程中的机械碰撞也会使零件产生变形,但这种变形是可以用改良操作加以减少和防止的。
e〕外表脱碳轴承件在热处理过程中,如果是在氧化性介质中加热,外表会发生氧化作用使零件外表碳的质量分数减少,造成外表脱碳。
外表脱碳层的深度超过最后加工的留量就会使零件报废。
外表脱碳层深度的测定在金相检验中可用金相法和显微硬度法。
以外表层显微硬度分布曲线测量法为准,可做仲裁判据。
f〕软点由于加热不足,冷却不良,淬火操作不当等原因造成的轴承零件外表局部硬度不够的现象称为淬火软点。
它象外表脱碳一样可以造成外表耐磨性和疲劳强度的严重下降。
补救措施
a〕磨加工
磨加工在一定程度上能够减轻缺陷所造成的影响。
轴承零件经淬回火后产生的外表脱碳、腐蚀坑和氧化皮等缺陷必须在磨加工过程中除净。
b〕化学沉积法
对于尺寸公差超出设计标准的轴承零件,可采用化学沉积法进展挽救。
化学沉积的原理是通过多种化学原料间的化学反响,均匀地在零件外表产生一定厚度的金属镀层,通过附加回火保证金属层与零件原有的硬度和力学性能一样。
化学沉积只增加零件的尺寸大小,不改变零件的形状公差,所以对于尺寸公差超差的零件,采用化学沉积是一种有效的挽救方法,目前,最大单边沉积厚度可达左右。
c〕热处理涨形法
轴承钢的淬火组织由淬火马氏体、少量未溶的二次碳化物与剩余奥氏体组成。
淬火马氏体和剩余奥氏体属于不稳定组织,在回火过程中马氏体的分解使钢的体积收缩,而剩余奥氏体的分解使钢的体积胀大。
随着回火温度的提高,剩余奥氏体转变分解量增大,在保证工艺要求硬度的条件下,适当提高回火温度,使剩余奥氏体分解,转变成比容较大的马氏体组织,可使工件体积相应增大,即相对使外径磨量增加,利用这种方法可以使轴承套圈缺陷处在正常磨削条件下成为废品的零件得以挽救。
7.失效方式与修复
接触疲劳失效
接触疲劳失效系指轴承工作外表受到交变应力的作用而产生的材料疲劳失效。
接触疲劳失效常见的形式是接触疲劳剥落发。
接触疲劳剥落发生在轴承工作外表,往往也伴随着疲劳裂纹,首先从接触外表以下最大交变切应力处产生,然后扩展到外表形成不同的剥落形状,如点状为点蚀或麻点剥落,剥落成小片状的称浅层剥落。
由于剥落面的逐渐扩大,而往往向深层扩展,形成深层剥落。
深层剥落是接触疲劳失效的疲劳源。
磨损失效
磨损失效系指外表之间的相对滑动摩擦导致其工作外表金属不断磨损而产生的失效。
持续的磨损将引起轴承零件逐渐损坏,并最终导致轴承尺寸精度丧失与其它相关问题。
磨损失效是各类轴承常见的失效模式之一,按磨损形式通常可分为最常见的磨粒磨损和粘着磨损。
磨粒磨损系指轴承工作外表之间挤入外来坚硬粒子或硬质异物或金属外表的磨屑且接触外表相对移动而引起的磨损,常在轴承工作外表造成犁沟状的擦伤。
粘着磨损系指由于摩擦外表的显微凸起或异物使摩擦面受力不均,在润滑条件严重恶化时,因局部摩擦生热,易造成摩擦面局部变形和摩擦显微焊合现象,严重时外表金属可能局部熔化,接触面上作用力将局部摩擦焊接点从基体上撕裂而增大塑性变形。
6.3断裂失效
轴承断裂失效主要原因是缺陷与过载两大因素。
当外加载荷超过材料强度极限而造成零件断裂称为过载断裂。
过载原因主要是主机突发故障或安装不当。
轴承零件的微裂纹、缩孔、气泡、大块外来杂物、过热组织与局部烧伤等缺陷在冲击过载或剧烈振动时也会在缺陷处引起断裂,称为缺陷断裂。
应当指出,轴承在制造过程中,对原材料的入厂复验、锻造和热处理质量控制、加工过程控制中可通过仪器正确分析上述缺陷是否存在,今后仍必须加强控制。
但一般来说,通常出现的轴承断裂失效大多数为过载失效。
腐蚀失效
有些滚动轴承在实际运行当中不可防止的要接触到水、水汽以与腐蚀性介质等,这些物质会引起滚动轴承的生锈和腐蚀,另外滚动轴承在运转过程中还会受到微电流和静电的作用,造成滚动轴承的电流腐蚀。
滚动轴承的生锈和腐蚀会造成套圈、滚动体外表的坑状锈,梨皮状锈与滚动体间隔一样的坑状锈,全面生锈与腐蚀。
最终引起滚动轴承的失效
本次课程设计我们用了两个周才最终完成,它是对我们材料专业综合知识学习的一个综合检测。
我们学习的课本知识只是理论,只有把它运用到实践中才能转化为自己的知识,正如古人所说“纸上得来终觉浅,绝知此事要躬行〞。
而此次课程设计就给了我们这样一个运用自己学习到的知识的机会。
在这次课程设计中,我首先仔细看了教师给的题目,然后在网上查了一些资料最后决定选题。
我选择的是高温轴承,我在网上查了很多资料和参考课本,才找到了高温轴承的有关知识。
在这次课程设计中,不仅检验了我所学的知识,也培养了我如何去把握一件事情,如何去做一件事,如何去完成一件事。
8.参考文献
[1]X剑桥.9Cr18Mo马氏体不锈钢的平衡相热力学计算[J].特殊钢.2010(06)
[2]庞国兴.淬火加热温度对9Cr18Mo钢组织与性能的影响[J].航天工艺.1996(02)
[3]王金玲,X书丽.钢制轴承零件的真空热处理工艺[J].轴承.2008,No.4:
16-17
[4]郝雪玲,谭曙光,陈社伟.9Cr18不锈钢轴承套圈套锻工艺[J].轴承.2000〔1〕
[5]庞国星.淬火加热温度对9Cr18Mo钢组织与性能的影响[J].航天工艺.1996(02)
[6]戴起勋.金属材料学[M].:
化学工业,2009:
84-86.
[7]才鸿年.现代热处理手册[M].:
化学工业,2009.
[8]
单位名称
中原工学院
热处理工艺卡
编号
共1页
第1页
工艺路线
产品名称
高温轴承
技术要求
正火:
156-207HB
零件名称
高温轴承
材料
9Cr18Mo
操作说明
每台件数
1
工序
工序名称
设备
工夹具
装炉
加热规X
冷却规X
温度℃
时间
冷却剂
时间
1
淬火1
淬火2
淬火3
RT2-150-9
650
850
1110
2-3h
散开空冷
2
检查
硬度
布氏硬度计
156-207HB
3
机加工
4
高温回火
RT2-150-9
600±10
2-3h
空气
更
改
文件号
标记
数量
修改者
拟定
描写
校核
会签
审核
批准