钴冶炼生产工艺设计报告.docx
《钴冶炼生产工艺设计报告.docx》由会员分享,可在线阅读,更多相关《钴冶炼生产工艺设计报告.docx(21页珍藏版)》请在冰豆网上搜索。
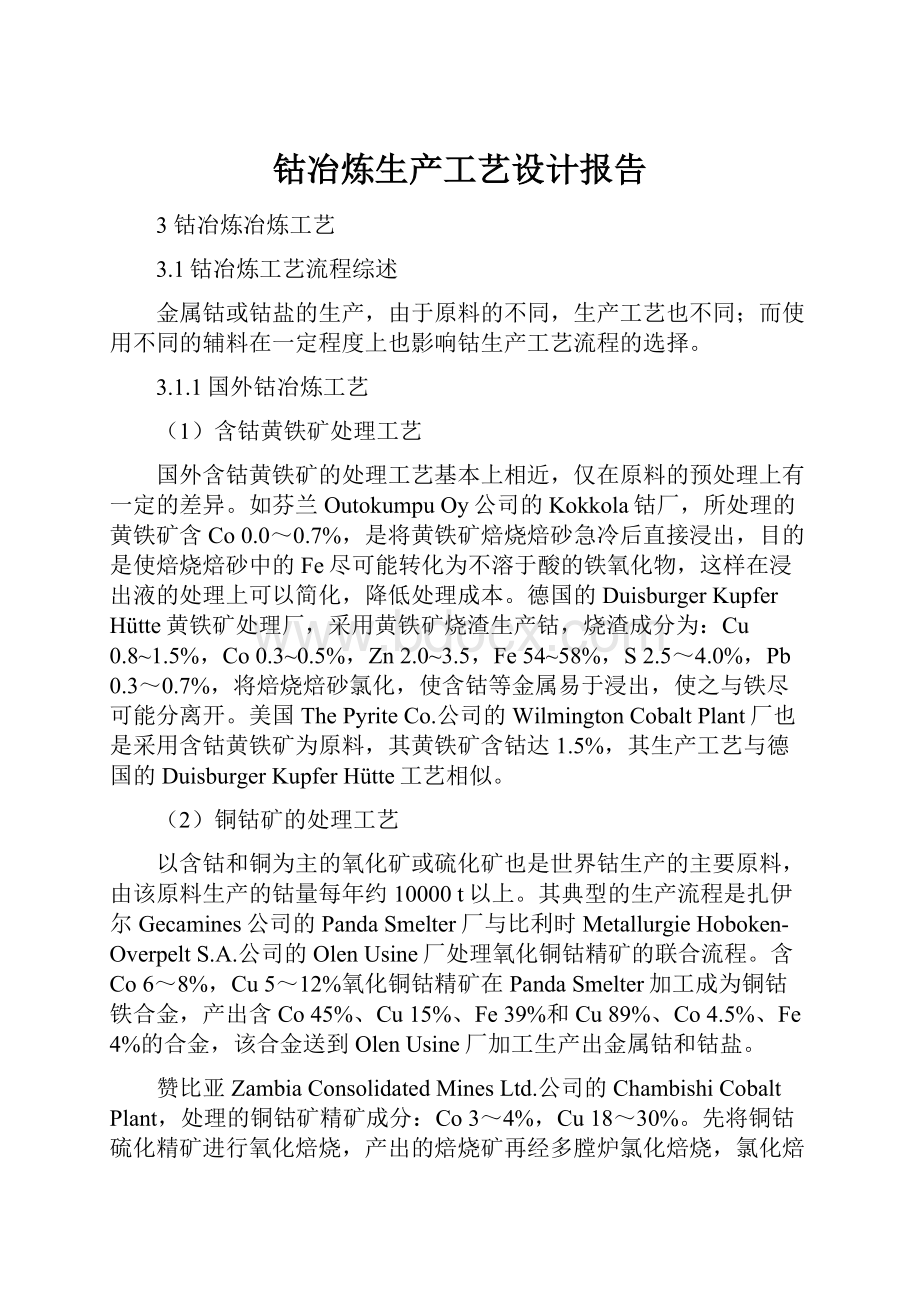
钴冶炼生产工艺设计报告
3钴冶炼冶炼工艺
3.1钴冶炼工艺流程综述
金属钴或钴盐的生产,由于原料的不同,生产工艺也不同;而使用不同的辅料在一定程度上也影响钴生产工艺流程的选择。
3.1.1国外钴冶炼工艺
(1)含钴黄铁矿处理工艺
国外含钴黄铁矿的处理工艺基本上相近,仅在原料的预处理上有一定的差异。
如芬兰OutokumpuOy公司的Kokkola钴厂,所处理的黄铁矿含Co0.0~0.7%,是将黄铁矿焙烧焙砂急冷后直接浸出,目的是使焙烧焙砂中的Fe尽可能转化为不溶于酸的铁氧化物,这样在浸出液的处理上可以简化,降低处理成本。
德国的DuisburgerKupferHütte黄铁矿处理厂,采用黄铁矿烧渣生产钴,烧渣成分为:
Cu0.8~1.5%,Co0.3~0.5%,Zn2.0~3.5,Fe54~58%,S2.5~4.0%,Pb0.3~0.7%,将焙烧焙砂氯化,使含钴等金属易于浸出,使之与铁尽可能分离开。
美国ThePyriteCo.公司的WilmingtonCobaltPlant厂也是采用含钴黄铁矿为原料,其黄铁矿含钴达1.5%,其生产工艺与德国的DuisburgerKupferHütte工艺相似。
(2)铜钴矿的处理工艺
以含钴和铜为主的氧化矿或硫化矿也是世界钴生产的主要原料,由该原料生产的钴量每年约10000t以上。
其典型的生产流程是扎伊尔Gecamines公司的PandaSmelter厂与比利时MetallurgieHoboken-OverpeltS.A.公司的OlenUsine厂处理氧化铜钴精矿的联合流程。
含Co6~8%,Cu5~12%氧化铜钴精矿在PandaSmelter加工成为铜钴铁合金,产出含Co45%、Cu15%、Fe39%和Cu89%、Co4.5%、Fe4%的合金,该合金送到OlenUsine厂加工生产出金属钴和钴盐。
赞比亚ZambiaConsolidatedMinesLtd.公司的ChambishiCobaltPlant,处理的铜钴矿精矿成分:
Co3~4%,Cu18~30%。
先将铜钴硫化精矿进行氧化焙烧,产出的焙烧矿再经多膛炉氯化焙烧,氯化焙烧矿经湿法处理得到钴盐,钴盐经锻烧和电炉熔炼产出金属钴,金属钴经电解精炼得到商品钴。
(3)砷钴矿的处理工艺
每年全世界以砷钴精矿为原料生产的钴估计为3000~5000t。
加拿大的DeloroSmeltingandRefiningCo.公司的DeloroCobaltPlant厂,处理摩洛哥的砷钴矿和加拿大自产的银砷钴矿,电炉熔炼产出的黄渣先经焙烧后成为可溶性的钴,电炉渣则经鼓风炉熔炼产出砷冰铜,鼓风炉和黄渣焙烧烟尘回收As2O3,砷冰铜和黄渣浸出后的浸出液合并采用化学法净化,然后生产金属钴。
(4)铜镍钴矿的处理工艺
大量的钴是从镍生产系统中综合回收的。
每年全世界以此类含钴料为原料生产的钴在10000t左右。
从镍冶金工艺中回收钴根据镍冶金工艺的不同而不同。
在镍的电解工艺中基本上采用非常类似的工艺,只是在最近将新工艺溶剂萃取技术用于Ni-Co的分离上。
加拿大InternationalMetalsCo.公司的PortColborneCobaltPlant厂,从含Co0.1g/l,Ni50g/l,Cu0.3g/l,Fe0.1g/l镍电解废液中回收钴,先采用化学方法净化含钴溶液,然后综合沉淀产出Co(OH)3,经锻烧得到氧化钴,氧化钴经反射炉还原熔炼得到阳极钴,再经电解精炼后产出商品钴。
是英国的InternationalMetalsCo.公司的ClydachNickelRefinery厂,从镍羰基法生产工艺的残渣中回收钴,采用的生产工艺流程为:
羰基钴渣经氧化焙烧,焙砂浸出,浸出经化学净化,NaOCl和苏打沉钴产出粗氢氧化钴,粗氢氧化钴又经复溶、净化和二次沉钴,产出精氢氧化钴,氢氧化钴经锻烧得商品氧化钴。
这两个工艺在一定程度上相似。
首先将钴转化到富钴溶液中,然后用化学的方法净化处理,最后得到金属钴或氧化钴。
(5)锌冶金含钴料钴回收工艺
少数钴处理厂以锌冶金过程中净化处理时得到的含钴料为原料生产金属钴或氧化钴。
澳大利亚的Elect.ZincCorp.ofAudtraliaLtd.公司的RisdonZincPlant厂用α—亚硝基β萘酚除钴得到的钴渣提钴。
这种钴渣经过选矿获得钴精矿后煅烧得到氧化钴。
而意大利的MonteponieMontevecchioSPA公司的MargheraZincPlant厂则用α—亚硝基β萘酚除钴得到的钴渣经过直接煅烧,然后用硫酸进行调浆-硫酸化焙烧-浸出-除铁-除铜、锌、镉-沉CoCO3-溶解-电解的工艺得到电解钴。
从上述分析可知,世界上各国由于含钴原料的不同采用的生产方法各不一样。
但基本上都是将含钴的物料溶解使钴进入溶液(或已经在各种废液中),然后采用化学净化法或萃取等方法除去各种杂质特别是Fe、Cu、As等,然后进行Ni、Co分离,镍钴分离通常利用Co(III)有较低的溶度积,用各类氧化剂将Co(II)氧化为Co(III)后与Ni分离或
萃取分离Ni、Co。
分离过程有时要反复进行,使得钴中的杂质能有效地被分离。
3.1.2国内钴冶炼工艺
我国主要由钴土矿、砷钴矿、硫钴矿、铜镍钴矿等含钴原料提取钴。
(1)钴土矿处理工艺
我国钴土矿主要在云南、江西、广东、福建、浙江等地,随着近年来的开采和冶金
处理,矿源基本上枯竭。
云南易门有色选冶厂的钴土矿的处理工艺是硫酸浸出-萃取净化-草酸沉钴-煅烧。
(2)砷钴矿的处理工艺
我国砷钴矿的处理厂以赣州冶炼厂处理工艺为代表。
它所处理的砷钴矿是从摩洛哥进口。
砷钴矿火法焙烧使砷以As2O3形态从物料中挥发出来,钴转化为易于酸浸的氧化物,再进行溶液净化-分离除杂后得到钴盐,然后还原钴盐得到金属钴。
(3)硫钴矿的处理工艺
我国硫钴精矿的处理厂较多,如山东淄博钴业有限公司、海南金亿新材料有限公司、葫芦岛锌厂、湖北光化磷肥厂、老河口光磷化工有限公司。
在我国的钴资源中,硫钴精矿的钴占现有钴资源总量的30~40%,是重要的钴资源之一。
以硫钴精矿为原料的生产处理厂所采取的工艺流程基本上相似,如图3-1。
图3-1a是葫芦岛锌厂的硫钴精矿生产氧化钴及金属钴的的工艺流程,多数以硫钴精矿为原料的厂家采用这种工艺。
图3-1b是老河口光磷化工有限公司的处理工艺流程,它所处理的硫钴精矿是湖北大冶的含钴黄铁矿。
部分黄铁矿用来焙烧生产硫酸,其产出的焙砂与黄铁矿精矿再混合配成含硫12%的混合矿,然后进入沸腾炉焙烧。
硫钴精矿和烧渣平均含钴各为0.245%、0.258%。
山东淄博钴业有限公司生产工艺与老河口光磷化工有限公司的处理工艺相似,它所处理的矿为山东金岭铁矿的硫钴精矿为主,外购海南、中条山、大冶等的硫钴精矿,金岭铁矿的硫钴精矿含钴0.25~0.35%。
ab
图3-1硫钴精矿的处理工艺流程
(4)镍钴矿的处理工艺
伴生钴的铜镍矿是我国重要的钴资源之一,其占可供应钴资源量的50%以上。
在镍的冶金过程中,矿石在造锍熔炼时90%以上的钴随镍一道进入高镍锍中,高镍锍电解或加压浸出时进入溶液,溶液或电解液中的钴用黑镍氧化沉淀钴得到钴渣,这种含钴渣即为提钴的原料。
镍钴渣的处理工艺如图3-2。
它是金川有色公司的处理工艺流程,采用纯化学和萃取的方法处理钴渣。
虚线框中的工艺为萃取工艺。
阜康冶炼厂也采用萃取工艺,但镍钴分离所使用的萃取剂不是P507,而是Cyanex272,其它基本上相似。
图3-2镍钴渣处理工艺流程
四川铜镍公司所采用的工艺与金川公司不同。
在四川铜镍公司中,镍钴渣用HCl还原溶解,黄钠铁矾(或仲辛醇萃取除铁)除铁,再用N235萃取分离镍钴,HCl反萃后的钴溶液用330树脂除铅,717树脂除锌,再用330树脂除镍等一系列离子交换技术进行深度净化后电解得到电解钴。
重庆冶炼厂又与四川铜镍公司、金川公司不同。
镍钴渣用HCl还原溶解,用N235、TBP及溶剂油萃取除铁,溶液浓缩后用N235萃取分离镍钴,反萃后的钴溶液H2S除铜,氯气氧化除As、Fe,然后加高锰酸钾除锰,活性炭吸附有机物,330树脂除微量镍,最后电解得到金属钴。
对于富钴锍则采用加压氧化浸出,然后硫代硫酸钠除去部分铜,除铜后液用P204深度除铜,再用P507进行镍钴分离,HCl反萃,反萃液氯化钴用草酸沉淀,得到草酸钴。
草酸钴用回转窑煅烧得到氧化钴。
我国的钴冶金工艺与国外的钴冶金工艺相比,技术水平基本上相当,所采取的工艺流程相似,仅原料相差比较大。
综合上述钴生产工艺可知,不论采用何种钴原料,钴的生产工艺均可分解为三部分。
1)可溶性钴的制取。
根据原料的不同,采用氧化或还原使钴成为酸溶性的物质。
2)含钴溶液的化学净化或萃取净化。
化学净化是利用Co(III)的氢氧化物具有较低的溶度积,同时氢氧化钴(III)可以还原溶解于酸溶液中,这样反复可以得到比较纯净的钴盐溶液;萃取除杂是利用不同的萃取剂对不同金属离子的选择性溶解而使得钴溶液得到净化。
3)净化得到的钴盐溶液可直接生产各类钴盐,或草酸沉淀得到草酸钴,然后煅烧得到各类氧化物,或不溶阳极电解得到电解钴,或对得到的氧化钴还原,然后进行可溶阳极电解得到电解钴。
净化后的钴盐溶液可根据市场需求的不同有效地调整产品结构以满足市场的需求。
3.2冶炼工艺流程选择
3.2流程选择
根据前面的不同钴物料的处理工艺和现有处理钴铜精矿的处理工艺,结合永平县弥勒山钴铜精矿及老炉渣的物料特点,我们采用图1的处理工艺流程。
该工艺一方面使废的老炉渣和铜钴精矿中的钴和现有的铜钴精矿中的钴得以回收,使含钴资源得以充分利用,也使物料中的其它有价金属如铜得以回收,资源得到综合利用,另一方面,该工艺流程简短,适合地方工业化生产。
同时,该钴处理工艺流程也适合处理砷钴矿、锌生产过程的钴渣及各类钴的中间物料,具有较强的钴原料的实应性,拓宽企业的生产原料的来源,有利于企业的稳定生产。
硫酸化焙烧使老炉渣中的钴和钴铜中的钴转化为可溶性的钴盐或化合物,并充分利用物料中元素硫,使有价金属和脉石矿物形成可分离的不同物相。
硫酸化焙烧的回转窑可根据钴原料的不同性质,可进行氧化焙烧或还原焙烧,使钴转化为酸可溶的钴盐或钴化合物。
浸出过程由二段逆流浸出组成。
浸出过程实现有价金属与脉石矿物的分离,也使钴转化到溶液中,实现提取钴或钴盐的第一步。
一段采用低酸浸出,浸出液的pH值2~3,这样减少或消除浸出液净化时碱的消耗,二段浸出采用高酸浸出,使物料中的有价金属能充分溶解,提高焙砂中的有价浸出率,从而提高该工艺的钴等金属的回收率。
焙砂浸出液主要由Co、Cu有价金属和Fe、Zn等杂质的硫酸盐和砷酸盐和锑酸盐所组成。
为了使产品中的杂质含量符合产品的质量要求,必须脱除杂质Fe和砷酸盐及锑酸盐。
砷和锑是使其形成稳定的砷酸盐和锑酸盐而从溶液中分离脱除,Fe是使其氧化成高价铁,然后高价铁水解和与砷酸或锑酸形成稳定的化合物的方法将其从溶液中脱除,为此我们采用廉价的氧化剂空气进行氧化低价的铁。
浸出液的净化采用空气氧化进行净化处理,使溶液中影响铜电积的铁、砷、锑等脱除,满足电积过程对溶液中杂质的要求。
净化后的溶液含有比较高的铜,与部分电积返回的后液混合后得到铜电积的电积液的要求,其中的少量的杂质不影响电积过程和电积阴极铜的质量,溶液中的钴也不影响铜的电积,实际上在铜的电积过程中还需要添加硫酸钴作为电积添加剂。
电积铜后的废电积液还含有较高的铜,为了使其中的铜充分回收,我们利用铜和钴水解性能的差异。
我们用廉价的中和剂石灰乳中和溶液,使溶液的中和终点的pH为6.0~7.5,使铜转化为碱式盐沉淀,然后从溶液中分离,实现与钴分离的目的。
产出的含铜渣返回二段浸出,使该渣中的铜得以回收。
石灰中和除铜后的溶液主要由钴等组成,考虑目前的投资规模,我们将其处理生产出粗碱式碳酸钴。
如果将来资金容许和市场需要,再将碱式碳酸钴进行溶解-化学深度净化-萃取的工艺处理,生产出工业标准要求的各类钴盐和氧化钴等产品。
沉钴是是采用苏打或碳铵沉淀溶液中的钴,使钴转化为溶解度不高的碱式碳酸钴。
沉钴时溶液中的部分杂质元素如Mg、Cu、Zn、Ni等也和钴一同沉淀,因此碱式碳酸钴产品中的杂质含量高,该产品需要经过进一步的处理特别是净化除去少量的杂质后才能产出满足市场质量标准的各类钴产品。
]将来,如果需要生产市场需要的各类钴盐时,石灰除铜后液采用氧化的方法使钴氧化为三价的钴与溶液中的Mg、Ni、Zn、Cu等大部分杂质分离,产出的氢氧化高钴再还原溶解,萃取分离少量的杂质后得到纯净的氯化钴溶液,或草酸沉淀得到草酸钴,或草酸钴焙烧产出氧化钴等市场需要的各类钴盐。
图钴铜矿生产碳酸钴工艺流程图
从工艺分析可知,该工艺流程简短,所需要的原材料消耗少,价值低,从而生产成本低,保障企业将具有较好的经济效益。
3.3产品方案
根据上述的生产流程,目前生产的产品为电积铜和粗碳酸钴。
铜已经达到最终的产品,钴仍然为中间物料,将来如果资金等允许,对粗碳酸钴进行进一步的处理或从流程的最后进行漂水或氯气氧化沉淀,然后由该沉淀物生产各类钴盐或氧化钴等产品。
生产的电积铜达到GB的标准,碳酸钴为中间物料,含钴为45%。
该工艺每天和全年产出的产品量如表
表每天或每年的产品产出量
名称
单位
日产出量
年产出量
№1
电解铜
吨
3.549
1064.700
№2
碳酸钴(折合金属钴)
吨
0.201
60.300
3.4过程
3.4过程主要技术指标和物料流量计算
在该工艺过程中,钴的回收率为68.50%,铜的回收率为91.5%。
所处理的老炉渣和钴铜精矿的成分见表。
生产厂年工作300天,老炉渣和钴铜精矿按1:
1使用,年生产120吨碳酸钴需要钴铜精矿为(混合后的平均含钴0.45%):
120×45%÷0.45%÷68.50%=8759.12(t/a)
老炉渣由于在破碎细磨工序中有损失,其直收率和回收率尾99%,则老炉渣需要量为:
8759.12÷99%=8847.60(t/a)
各工序的技术经济指标和物料流量见下
3.4.1破碎-细磨工序
老炉渣首先进行破碎,破碎后粒度<50m,破碎后的老炉渣和回转窑产出沉降室烟尘一同在球磨机中进行细磨,细磨后的粒度为-120目。
破碎-细磨工序物料各元素直收率和回收率为99%。
该工序的日物料流量见表
3.4.2混料工序
混料过程是将老炉渣和钴铜精矿及旋风收尘器烟尘一同混均匀,目的是使该物料在焙烧过程中充分相互反应,是物料中的钴等有价金属转化为可酸溶的物质。
混料过程中物料有一定的飞扬损失,飞扬损失为物料量锝0.2%,各元素的回收率和直收率99.80%。
混料过程的物料流量见表。
3.4.3制粒工序
制粒的目的是将混均匀的物料加入少量的水分后形成颗粒,这样在回转窑焙烧时随烟气所带到收尘系统的数量少,收尘系统符荷小,返料少,减少过程中循环的物料和过程损失。
制粒颗粒大,不利用硫酸化焙烧的进行,制粒的颗粒小,返料多,因此制粒后的物料粒径为3~6mm,水分8~10%(选择10%),损失率0.2%,该工序的各元素的回收率和直收率为99.8%。
该过程的物料流量见表。
3.4.4焙烧工序
焙烧是在回转窑内将物料中的硫化物及氧化为硫酸盐,同时也将老炉渣中的钴硅酸盐分解,使钴也转化为硫酸盐。
焙烧温度650~680℃,物料高温停留时间120~150min,焙砂产率80%,空气过剩系数160%。
钴、铜的硫酸化转化率>95%。
焙烧过程主要利用物料中的元素硫燃烧作为热源,如果该燃烧热不足,利用回转窑的燃烧室煤燃烧补充不足的热源。
焙烧脱硫率68.25%,As的挥发率49.79%,Sb的挥发率34.26%,钴和铜的直收率89.32%,回收率98.02%。
焙烧过程的投入产出如表。
3.4.5一段浸出工序
将回转窑产出的焙砂进行湿磨,细磨后的焙砂颗粒粒度为-120目,细磨后矿浆打入中间槽,然后低流用砂泵打入一段浸出槽。
用二段浸出液及二段浸出渣洗涤后液进行调浆,液固比为2.5:
1,浸出温度50~70℃,浸出时间120~150min。
一段浸出时钴的浸出率30%,铜的浸出率70%,锑的浸出率10%,砷的浸出率75%,Ni、Fe、Mg、S、Zn的浸出率分别为40%、5%、30%、96.67%、30%。
浸出终点pH=2.0~3.5。
一段浸出过程的物料流量如表。
3.4.6二段浸出工序
一段浸出料浆经板框压滤后的渣送入二段浸出槽,二段浸出用其前面的浸出渣洗涤水并补充部分新水后调浆,然后补加适量的硫酸进行浸出。
液固比为:
2.0:
1,浸出温度60~70℃,浸出时间150~180min。
一段浸出时钴的浸出率93.30%,铜的浸出率96.65%,Sb、As、Ni、Fe、Mg、S、Zn的浸出率分别为83.62%、69.83%、68.67%、10.61%、59.22%、97.46%、83.88%,浸出终点pH<0.5。
浸出工序的各元素浸出率为:
Co95.22%、Cu98.12%、Fe15.08%、Sb85.23%、Mg71.03%、S97.80%、Ni80.74%、As92.12%、Zn88.51%。
3.4.7氧化除铁砷等工序
氧化是将溶液中的铁氧化为高价的铁,其然后与溶液中的砷酸离子等结合为稳定的砷酸铁和高价铁水解,从而脱除溶液中的砷铁等杂质。
脱砷时首先采用空气氧化溶液中的铁,氧化时间150~180min,氧化温度60~80℃,氧化终点的pH为2.5~3.5,空气氧化后再搅拌30min。
氧化后的渣进行浆化洗涤,使渣中吸附的有价金属尽可能被洗涤下来。
氧化过程中钴的损失率5%,铜的损失率3%,砷的脱除率98%,铁的脱除率99%,Sb、Mg、S、Ni、Zn的脱除率分别为98%、5%、0.05%、8%、5%,钴的回收率92%,铜的回收率98%。
氧化工序的物料流量如表。
3.4.8电积工序
氧化除杂后的溶液与部分的电积后液混合,调整电积前的溶液含铜45~50g/L。
电积的添加剂为硫脲,添加量为40g/t铜,电积的阴极电流密度160A/m2,电积温度45~55℃,同极间距100mm,槽电压2V,电流效率85%,电耗2150~2250度/吨铜。
阳极为铅合金板。
电积过程铜的直收率59.97%。
种板槽的电积同铜电积,阴极为316L的不锈钢。
电积过程的物料流量如1表。
3.4.9石灰中和沉铜
电解后液含有较高的铜,在该溶液回收钴以前必须将其中的铜回收。
铜的回收采用中和沉铜的方法。
石灰中和时首先将石灰调浆,然后加入溶液中。
中和过程的温度60~80℃,中和时间160~210min,中和终点的pH=6.0~7.5,中和后再搅拌30min。
中和渣用热水洗涤,洗涤液和中和后液一同进入下一工序。
中和过程中,铜的沉淀率96.52%,元素Fe、Sb、、Mg、S、Ni、As、Zn的沉淀率分别为60.96%、91.44%、5.08%、99.5%、5.08%、81.28%、5.08%,钴的直收率为94.92%。
石灰中和过程的物料流量如表。
3.3.10苏打沉淀钴
苏打沉钴是利用苏打与溶液中的硫酸钴反应生产在溶液中溶解度较小的碱式碳酸钴沉淀,使钴与其它部分杂质和溶液分离。
苏打沉钴过程中,程度温度50~70℃,沉钴时间120~150min,苏打或配成溶液加入沉钴液中或直接加入沉钴液中,苏打分多次加入。
苏打加入完后,再搅拌30min。
沉钴过程中,钴的回收率90%。
沉钴后液送废水进行净化,除去溶液中的重金属,使溶液的派放达到国家标准。
3.4.11全流程的各种原材料和辅料消耗
根据流程的物料流量计算,我们得到该工艺的全流程各中原材料和辅料的消耗如表。
表全流程的原材料和辅料消耗
序号
名称
单位
日消耗
年消耗
№1
煤
吨
10.500
№2
电
万度
2.3000
690.000
№3
硫酸
吨
9.870
2961.000
№4
石灰(85%)
吨
10.731
№5
苏打
吨
0.420
126.000
№6
硫脲
kg
0.142
42.600
№7
老炉渣
吨
29.492
8847.600
№8
钴铜精矿
吨
29.1970
8759.100
№9
钴铜精矿
吨
30.1970
№10
钴铜精矿
吨
31.1970
№11
钴铜精矿
吨
32.1970
№12
钴铜精矿
吨
33.1970
№13
钴铜精矿
吨
34.1970
№14
钴铜精矿
吨
35.1970
3.3冶金计算
3.4主要设备选型计算
3.6.1老炉渣破碎
按冶金计算,年处理老炉渣8847.6t,物料粒度50~140mm,排料粒度要求小于20mm,工作制度为:
300d/a,采用一班制作业,每班有效作业时间为6h。
选用颚式破碎机:
日处理物料量:
8847/300=29.5(t/d)
老炉渣堆比重:
2.5t/m3
老炉渣体积:
29.5/2.5=11.8m3
选用:
PE-150型颚式破碎机一台,其最大生产能力为3m3/h,可满足破碎要求。
配套电机功率:
5.5kw。
3.6.2磨矿
年处理物料量9987.1t,包括破碎后的老炉渣,硫酸化焙烧的返回料。
要求干式磨矿、排料粒度小于0.5mm;磨矿工作制度为:
300d/a,采用三班连续作业。
日处理物料量:
9987.1/300=33.29(t/d)
选用Φ1500×1500mm干式球磨机一台,生产能力为1~3t/h,排料粒度<0.4mm,可满足要求。
配套电机功率:
60kw。
3.6.3混料
进制粒机前的物料有磨细后的老炉渣和返回料及浮选铜精矿,制粒前须进行混料,以保证物料化学成分均匀,并提高无聊的成球性能,设计选用水泥搅拌机进行混料。
混料工作制度为:
300d/a,采用三班连续作业。
日处理物料量:
63.4t/d
混料时间:
5min/次
选用:
J1-400型混凝土搅拌机一台。
搅拌机主要性能如下:
额定装料容量:
400l;
额定出料容量:
260l;
搅拌筒尺寸:
Φ1447×1178mm;
搅拌筒转速:
18rpm;
配套电机功率:
7.5kw。
3.6.4制粒
为保证焙捎质量,要求物料经制粒机制粒,选用圆筒制粒机制粒。
制粒工作制度为:
300d/a,采用三班连续作业。
日处理物料量:
63.3t/d;
选用:
Φ1000×2200mm圆筒制粒机一台。
制粒机生产能力:
2~4t/h;
配套电机功率为:
10kw。
3.6.5硫酸化焙烧
物料的硫酸化焙烧采用回转窑,焙捎温度630~660℃,焙烧时间为4h。
焙烧工作制度为:
300d/a,采用三班连续作业。
日处理物料量:
63.3t/d;
回转窑直径计算:
式中:
G——生产能力,G=63.2/24=2.64(t/h);
V烟——每吨产品离窑时的烟气量,1501m3/h;
t尾——烟气离窑时的温度,450℃;
ωt——窑尾排烟速度,1.2m/s;
ψ——炉料在窑内的填充系数,0.006。
=1.75(m)
回转窑有效内径为Φ1800mm。
回转窑长度计算:
L=τω
式中:
τ——物料在窑内的停留时间,5h;
ω——物料在窑内的轴向移动速度。
ω=5.78×D×β×n
式中:
D——回转窑有效内径,1.8m;
β——回转窑倾斜角,1.5°;
n——回转窑转速,0.5rpm。
L=5×5.78×1.