火力发电厂金属受监部件失效分析.docx
《火力发电厂金属受监部件失效分析.docx》由会员分享,可在线阅读,更多相关《火力发电厂金属受监部件失效分析.docx(21页珍藏版)》请在冰豆网上搜索。
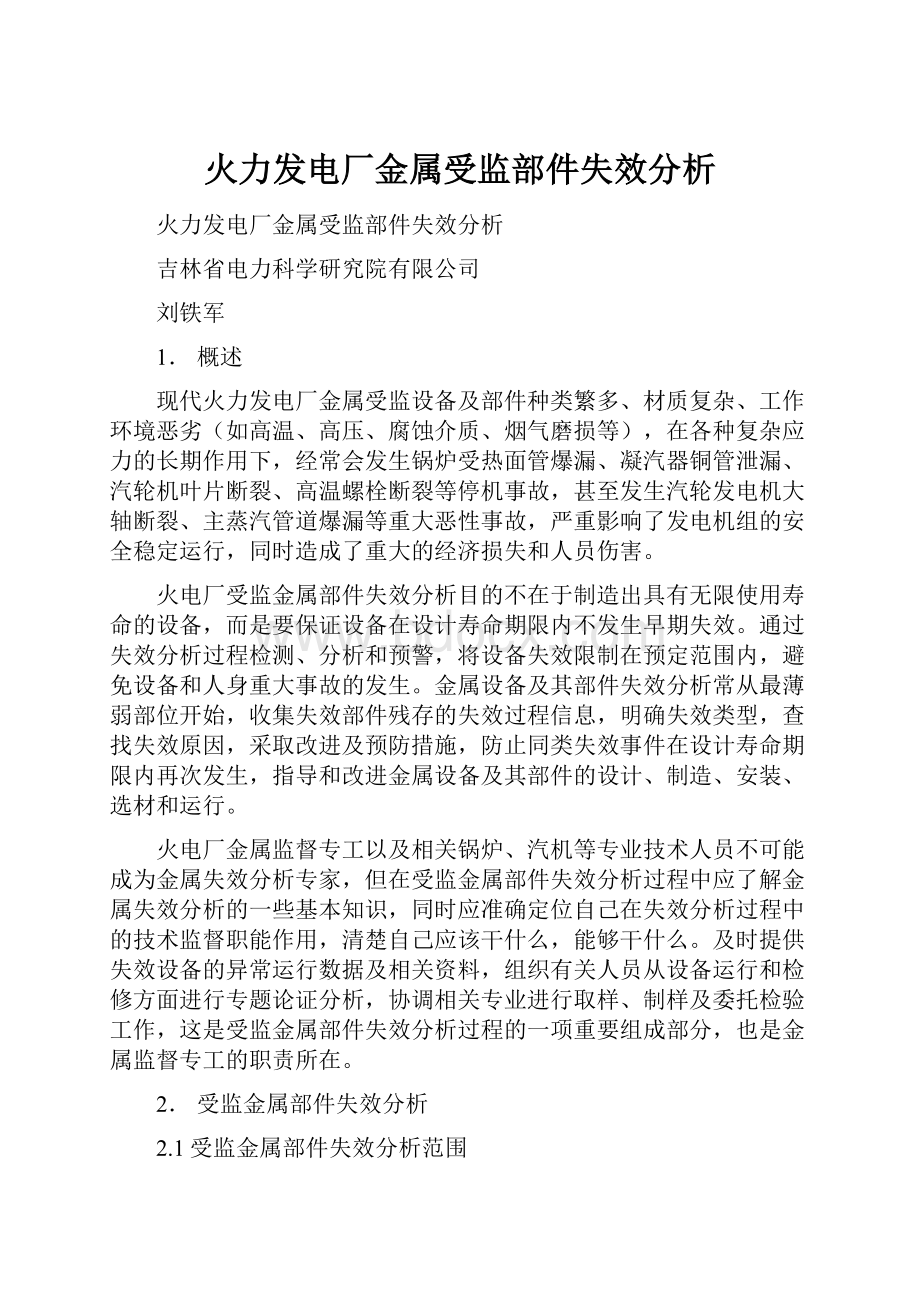
火力发电厂金属受监部件失效分析
火力发电厂金属受监部件失效分析
吉林省电力科学研究院有限公司
刘铁军
1.概述
现代火力发电厂金属受监设备及部件种类繁多、材质复杂、工作环境恶劣(如高温、高压、腐蚀介质、烟气磨损等),在各种复杂应力的长期作用下,经常会发生锅炉受热面管爆漏、凝汽器铜管泄漏、汽轮机叶片断裂、高温螺栓断裂等停机事故,甚至发生汽轮发电机大轴断裂、主蒸汽管道爆漏等重大恶性事故,严重影响了发电机组的安全稳定运行,同时造成了重大的经济损失和人员伤害。
火电厂受监金属部件失效分析目的不在于制造出具有无限使用寿命的设备,而是要保证设备在设计寿命期限内不发生早期失效。
通过失效分析过程检测、分析和预警,将设备失效限制在预定范围内,避免设备和人身重大事故的发生。
金属设备及其部件失效分析常从最薄弱部位开始,收集失效部件残存的失效过程信息,明确失效类型,查找失效原因,采取改进及预防措施,防止同类失效事件在设计寿命期限内再次发生,指导和改进金属设备及其部件的设计、制造、安装、选材和运行。
火电厂金属监督专工以及相关锅炉、汽机等专业技术人员不可能成为金属失效分析专家,但在受监金属部件失效分析过程中应了解金属失效分析的一些基本知识,同时应准确定位自己在失效分析过程中的技术监督职能作用,清楚自己应该干什么,能够干什么。
及时提供失效设备的异常运行数据及相关资料,组织有关人员从设备运行和检修方面进行专题论证分析,协调相关专业进行取样、制样及委托检验工作,这是受监金属部件失效分析过程的一项重要组成部分,也是金属监督专工的职责所在。
2.受监金属部件失效分析
2.1受监金属部件失效分析范围
《火力发电厂金属技术监督规程》DL438—2000规定了火力发电厂金属部件监督的适用范围,受监金属部件失效分析工作主要应在此范围内开展。
2.1.1工作温度≥450℃高温承压金属部件(包括主蒸汽和高温再热蒸汽管道、过热器和再热器管、联箱、阀壳和三通),与主蒸汽管道相联的小管道。
2.1.2工作温度≥435℃导汽管。
2.1.3工作压力≥3.82MPa锅筒。
2.1.4工作压力≥5.88MPa承压汽水管道和部件(包括水冷壁和省煤器管、联箱和主给水管道)。
2.1.5300MW及以上机组低温再热蒸汽管道。
2.1.6汽轮机大轴、叶轮、叶片和发电机大轴、护环、风扇叶。
2.1.7工作温度≥400℃螺栓。
2.1.8工作温度≥435℃汽缸、汽室、主汽门。
上述范围以外的金属部件失效,如果危及设备运行及人身安全,也应开展失效分析工作。
金属失效分析的目的不仅仅局限于修复或更换,而是要查明失效原因,制订安全防范措施,实现受监金属设备设计、制造、安装、运行和检修的全过程和全方位技术监控。
2.2失效分析概念
失效分析发展起源于十九世纪中期宝剑制造技术的脆断研究。
我国失效分析工作从七十年代开始,直到八十年代才步入正轨。
失效分析是一门综合性边缘学科,涉及到电力、机械、石化、航空、航天等各个工业领域;同时涉及到材料力学、断裂力学、工程力学、断口金相、热处理、腐蚀、摩擦和无损检测等诸多学科。
几个专有名词介绍:
失效:
金属设备及其部件在使用过程中,由于应力、时间、温度、环境介质和操作失误等因素作用,不能正确可靠地服役,丧失其规定功能的现象。
失效又称故障、损坏、事故等。
失效并不意味着断裂或漏泄。
磨损、腐蚀、形变、硬度下降、弹簧丧失弹性等都属于失效。
失效部件必须具备以下三个条件之一。
①完全不能运行。
如大轴、螺栓断裂。
②已严重损伤,不能继续安全可靠运行。
如受热面管严重腐蚀、磨损导致壁厚减薄。
③能够运行,但不能完成规定功能。
如机床长期运行后无法达到规定精度。
正常失效:
金属设备及其部件初期适应性运行失效,末期达到设计寿命预料中失效。
异常失效:
在正式运行期间,金属设备及其部件何时、以何种方式失效是随机事件,无法完全预料。
失效分析:
分析研究金属设备及其部件在运行过程中发生各种形式失效现象的特征及规律,确定产生失效的主要原因,提出防止同类部件发生同样失效的措施。
3.失效分析程序
3.1收集失效部件背景材料
金属受监部件失效后,首先应收集该部件的相关背景材料。
资料收集应认真查证原始出处,如设计和安装图纸,锅炉、汽机运行和检修规程、检修消缺记录等。
绝不能凭个人记忆或道听途说提供资料,原始资料失误将引起失效分析过程失控,甚至导致失效分析结论的错误。
背景资料收集工作应在事故专题分析会议召开之前完成。
为此要求金属监督专责及其他相关专业技术人员应在平时建立完善金属受监设备及其部件技术监督数据库,需要时能够及时调出,为失效分析提供准确可靠的背景资料及相关数据。
3.1.1制造、安装资料:
包括制造厂家、安装日期、加工处理工艺、检验项目及结果、材质、规格等。
3.1.2部件损坏部位:
简要文字描述并附注示意图记录部件损坏位置,要求通用性强、再现性准确无误。
3.1.3设备累计运行时间,启、停次数,超温超压运行记录。
3.1.4设备运行参数:
包括设计正常运行参数,损坏前异常运行参数。
3.1.5事故检验分析历史资料:
包括同一设备及其部件类似失效分析结论及常规性金属检验报告及检验结果。
3.2现场宏观检查
火力发电机组各类设备大部分是由金属受监部件组合而成。
如锅炉受热面管排、凝汽器等。
有些单体部件大而笨重,如汽轮发电机大轴等。
这些部件一旦失效,专业人员应力争在第一时间到达现场进行勘查,以便通过宏观检查结果,初步确定失效破坏的性质,并据此确定取样检验部位和检验方法。
现场宏观检查非常重要,应细心观察、收集并记录相关信息(如同公安人员勘查现场时,不放过任何蛛丝马迹一样)。
同时应掌握一定的金属失效分析基本常识。
有些金属监督专工不具备金属失效分析能力,又不寻求上级专业人员的技术支持。
现场检查过程中不能准确为自己定位,即不知道自己要干什么,又不知道自己能干什么。
在事故专题分析会上,或者不发表意见,或者乱发表意见。
这是一种不负责任的失职行为。
电厂专工可参照以下步骤进行现场宏观检查:
3.2.1查找、确定第一损伤破坏部位以及邻近部件损伤破坏情况。
3.2.2失效设备及部件中裂纹、断口记录,拍摄并保存影像资料。
3.2.3保存失效部件原始缺陷和断口完好无损
螺栓或叶片断裂,因其材质和工作环境状况较好,断口往往能够完整地保留下来。
应应保存完好查获的断口,防止断口表面氧化锈蚀及磕碰。
有人习惯将断口对合演示,尤其是领导在场的情况下。
这样做的后果,将损毁断口表面的某些细微结构,给以后断口宏观形貌特征分析工作造成了不利的影响,应杜绝此陋习。
3.2.4测量并记录缺陷性质
裂纹缺陷:
测量裂纹长度和深度、分布方向(轴向、径向)、部件局部形变等。
破断部件:
由于部件已经断开,通过观察断口宏观形貌,可以查找分析引起部件断裂的相关信息。
如受热面爆管,测量爆口长度、张开最大尺寸、爆口边缘减薄及变形程度,外壁氧化层及内壁垢层厚度及其分布等。
汽机叶片断裂可以从断口上获取疲劳断裂源、疲劳扩展纹及最后纤维断裂区。
通过上述断口宏观形貌特征,可以分析判断部件在断裂前经历的不同过程,初步确定断裂性质,并据此决定后续取样检验分析项目及内容。
3.2.5表面氧化腐蚀产物取样
检查测量失效部件表面氧化物颜色、厚度和形貌,收集样品供化学成份分析使用。
如金属酸性、碱性和氢脆坑内腐蚀产物分析,受热面管内壁垢层和外壁氧化物分析等。
4.失效部件取样加工
4.1失效部件取样
根据金属受监部件失效宏观特征确定下一步金属检验项目,并据此确定取样部位和数量。
割取样品时建议尽量采用机械加工方法,当必须采用火焰切割时,应预留机械加工余量,以彻底去除火焰切割时产生的热影响区,避免金属检验结果因此而出现偏差。
一般情况下,金属部件尺寸越大,管壁越厚,火焰切割产生的热影响区范围也越大,机械加工预留的余量也更大。
取样前应对失效部件进行相关的测量记录,否则取样加工后,因样品无法复原将使一些检查项目无法准确测量。
如受热面管管径胀粗、壁厚减薄、爆口尺寸等。
4.2试样机械加工
常规金属机械性能试验包括拉伸试验、冲击试验、弯曲试验和硬度试验等项内容。
试样加工尺寸及精度是否符合相关规程的标准要求,对试验结果起着至关重要的作用。
锅炉受热面管拉伸试验一般取条形试样,应保证试样加工尺寸和表面光洁度均符合标准要求。
由于机加人员不了解不合格试样对试验结果产生的影响,认为只要把试样拉断即可。
为图省事,加工的试样两侧不平行,平面加工成斜面,并且加工表面光洁度远达不到标准要求。
而有些金属监督专工也认识不清、把关不严,将加工不合格的试样送检。
建议金属检验员应拒收加工不合格的试样,并对由此产生的后果追究机加人员直至金属专工的责任。
5.金属失效分析方法
5.1金属表面宏观失效分析方法
直接用肉眼或借助放大镜观察金属表面缺陷和断裂类型的方法。
根据金属部件失效方式不同,又可分为金属宏观分析和断口宏观分析两种方法。
5.1.1表面宏观失效分析方法
将金属截断面或表面磨制后,经过侵蚀或直接观察金属表面缺陷。
宏观分析方法可以发现以下缺陷。
⑴金属内部缺陷:
如裂纹、气孔、缩孔、疏松等。
⑵铸件内部缺陷:
如树状晶体及晶粒度分布。
⑶锻件内部缺陷:
如纤维状组织、裂纹、夹层等。
⑷焊缝内部缺陷:
如裂纹、未焊透、未熔合、气孔、夹杂等。
⑸化学成分偏析:
如硫、磷区域分布偏析。
⑹化学热处理渗层:
如渗氮层、渗碳层、碳氮共渗层深度等。
5.1.2断口宏观失效分析方法
金属部件断裂后,直接在断口上查找裂纹源、裂纹扩展路径、断面与主应力方向、塑性变形量等宏观形貌特征,根据部件的断裂机理、断裂速度和应力状态,初步判断金属断裂性质。
几种常见断口形式:
⑴静载拉伸断口
塑性圆形光滑拉伸试样在轴向拉力的缓慢作用下直至断裂,其断口呈现三个典型区域,也称断口三要素。
纤维区:
试样受拉伸力作用时将会产生局部缩颈。
由于缩颈中心处于三维应力状态,在该形变塑性区受形变约束作用,该区首先形成显微孔洞。
随着孔洞不断增多、长大、相互连接而形成裂纹。
呈现粗糙纤维状正断形断面。
放射区:
在缩颈中心纤维区形成后,裂纹快速不稳定扩展。
断面呈平行于裂纹扩展方向的放射状条纹,并逆指裂纹源。
放射条纹粗大表明塑性变形大。
随着材料的强度增加、塑性降低、试验温度降低,放射状条纹将由粗变细直至消失。
剪切唇区:
在平面应力作用下裂纹扩展到临界尺寸后,发生快速不稳定低能量撕裂。
最终断裂区域与主应力成45°交角,为环形剪切斜断口。
在平面应力作用下裂纹发生快速不稳定扩展。
实际金属部件静载拉伸断口可能只显示出一个或两个要素特征,根据断口三要素分布位置、大小和形态特征,可以分析部件断裂时的应力大小和状态、尺寸和缺口效益,温度和材料强度。
如随着温度增高,材料塑性增加,纤维区+剪切唇区增大,放射区缩小。
随着部件尺寸增大,材料塑性降低,放射区增大。
⑵冲击断口
冲击标准试样10×10×55mm,其中一侧加工V形或U形缺口(深度2mm)。
在一次冲击载荷作用下,缺口侧承受拉应力,对应侧承受压应力,断口三要素有别于静拉伸试样。
纤维区:
断裂源形成试样缺口处,断面呈纤维状。
放射区:
裂纹沿缺口向试样内部快速扩展,断面呈放射状。
剪切唇:
裂纹扩展至缺口以外的三个自由表面附近时,最终以剪切方式断裂。
⑶疲劳断口
疲劳断口三要素:
疲劳源区:
通常产生于金属部件表面原始微裂纹、几何变形突变、焊接热处理残余应力集中、划痕损伤、腐蚀、磨损等部位。
裂纹扩展区:
多呈现海滩状(或称贝壳状)花样。
标志部件在每一次应力循环过程中,裂纹扩展的前沿位置。
疲劳纹垂直于裂纹扩展方向,呈弧形向内部推进。
常见于低应力高周疲劳断口,如叶片断裂。
瞬时破断区:
裂纹发展到临界尺寸后,发生快速失稳破断。
该区具有放射区和剪切唇特征,有时仅存在剪切唇。
其断口特征取决于材料的塑性和脆性、截面积和环境因素。
高脆性材料可出现解理或晶间脆性断口。
⑷解理和晶间断口
解理和晶间断裂均属于脆性断裂。
纯解理或结晶断口无纤维区、剪切唇和放射条纹。
解理断口由众多结晶面构成,在光线照射下可见闪闪发光特征。
晶间断口特征:
粗晶材料断口呈冰糖块状。
细晶材料断口呈结晶状,颜色较纤维断口亮,比解理断口暗。
5.1.3断口宏观分析步骤
查找裂纹源:
断裂原因分析的最重要依据,可初步评价产生断裂的诸多因素。
评定裂纹扩展特征:
解理断口、放射线、人字纹线具有快速扩展特征。
沿放射线逆向或人字纹尖顶可追溯到裂纹源位置。
估算三要素比例:
纤维区大—韧性好;放射区大—脆性大。
分析疲劳弧线:
断口弧形线显示裂纹扩展时应力和环境变化,可据此判断裂纹断裂性质。
恒定载荷下裂纹扩展没有弧形线。
查看断口粗糙度:
断口粗糙—剪切断裂比重大;断口细微—晶间和解理断裂比重大。
查看断口颜色:
断裂面由许多具有金属光泽和颜色的小断面构成,其细微变化表明不同的断裂方式。
估算最大正应力方向:
应力状态、材质和环境不同,断口与最大正应力方向交角也不同。
平面应变下成90°,平面应力下成45°,依此推算部件断裂时的应力状态。
查找内部缺陷:
材料在铸造期间会遗留下一些原始缺陷,如夹渣、气孔和疏松等,在经历锻压后,这些缺陷会发生不同程度的形变,并在其附近形成应力集中区,从而影响裂纹的扩展。
断口内部原始缺陷特征不同,其断裂方式也不同。
6.金属分析主要设备
6.1光学显微镜
光学显微镜是一种通过透镜组产生光学放大效应,观察金属内部细微组织的光学仪器。
显微镜放大倍数为目镜和物镜的乘积。
即总放大倍数=目镜倍数×物镜倍数。
受照明光线(可见光)波长限制,光学显微镜最大分辨仅为0.2µm,极限放大倍数仅为1600倍。
显微镜分类:
⑴按用途分生物显微镜、金相显微镜。
⑵按成像分透射式、反射式显微镜。
⑶按结构分卧式、立式、台式、便携式显微镜。
6.2电子显微镜
电子显微镜以电子束代替光束,以光阑代替光学透镜,在极高倍数下成像的仪器。
按结构和用途分类,电子显微镜分为透射式、扫描式、反射式和发射式四种。
6.2.1透射式电子显微镜
电子束穿透超薄金属样品或复膜片后高倍放大成像。
通过接收和处理透过样品的电子散射线信号,将样品的细微结构(如样品厚薄、密度大小等)转换成图像亮度和对比度,从而形成样品的高倍放大图像。
如果附加电子衍射仪,可以分析金属中第二相粒子相结构。
目前,透射式电子显微镜最高放大倍数已超过300万倍,分辨率可达纳米数量级(1nm=10-9mm)。
能够直接观察到某些重金属原子和原子排列整齐的晶体点阵(金属晶体布拉维点阵共有16种排列方式),是迄今人类观察物质细微结构的唯一有效的仪器。
火电厂主蒸汽管道在高温高压下长期运行后,金属内部组织中会析出新的金属化合物第二相粒子。
利用透射电子显微镜观察这些新相的析出位置及其晶体结构,可以深入分析金属材料的寿命损耗过程,同时科学的指导合金管道材质的研制和制造加工工艺过程。
6.2.2扫描式电子显微镜
电子束进入金属样品表面后会激发出二次电子,接收这些二次电子信号,并对其进行放大处理,从而形成样品微观形貌的高倍放大图像。
扫描电镜放大倍数可从几倍至几十万倍之间连续调整,而且图像景深好、立体感强,适于观察粗糙的断口表面。
如果附加电子能谱仪或波谱仪,可以结合形貌观察的同时,定点分析微区金属中化学元素含量。
例如1Cr18Ni9Ti不锈钢,由于焊接工艺或热处理工艺不正确,将导致晶间贫铬。
将金属样品进行铬元素线扫描能谱分析,将以曲线分布形式定性或定量提供晶界中铬元素的含量。
为后续金属失效分析提供了科学准确的依据。
6.2.3X射线衍射仪
X射线衍射仪是进行晶体结构分析的仪器,主要用于X射线定性/定量物相分析,点阵常数精确测定,晶体颗粒度、晶格变形、单晶取向测定。
火电厂高温高压金属管道长期运行后,钢中的碳化物变化、金属间化合物析出可通过X射线衍射仪分析完成。
7电站主要受监设备失效及分析
7.1汽包
7.1.1苛性脆化
阳极溶解型应力腐蚀。
主要发生在中低压汽包铆钉和管子胀口处、铆钉和胀口的汽包钢板上。
裂纹源初始于缝隙处,沿晶发展且有分叉,金相组织无变化,呈冰糖状脆性断口,表面无法发现。
产生原因:
局部应力(胀管和铆接产生的残余应力,开孔处边缘应力和热应力)高于材料屈服极限;炉水NaOH浓度高并浓缩缝隙处。
防范措施:
更改结构消除缝隙,将铆接和胀管改为焊接结构(现今锅炉已取消该结构);控制锅炉启停运行工况,减少热应力;提高汽水品质。
7.1.2低周疲劳
锅炉启停频繁、运行工况经常变动易产生疲劳裂纹(与最大应力方向垂直)。
主要发生在给水管孔、下降管孔处;纵、环焊缝,人孔焊缝也时有发生。
断口形貌具有疲劳断口特征。
产生原因:
汽包温差产生的热应力(锅炉启停温度变化越快,热应力越大。
规程规定锅炉启停期间,控制汽包壁温差不大于40℃);局部应力集中(汽包整体或局部热处理后残余应力);原始焊缝缺陷和裂纹(疲劳裂纹源)。
防范措施:
降低热冲击;锅炉启停、运行避免温度和压力大幅变化;减少锅炉启停次数;改进汽包结构,降低应力集中;选用抗低周疲劳新型材料;提高焊缝质量。
7.1.3应力氧化腐蚀
汽包水汽波动区域应力集中部位(如人孔门焊缝处)易产生裂纹。
断口无疲劳特征;裂缝处充满坚硬氧化物,附加应力作用加速裂纹扩展;裂纹边缘脱碳、晶粒细化、晶界空洞等微观特征;裂纹尖端及其附近有沿晶氧化裂纹;裂纹源于焊缝原始缺陷和腐蚀坑处。
产生原因:
高压炉水引起应力腐蚀;局部综合应力超过屈服极限;金属表面Fe3O4膜破裂(反应Fe+4H2O--Fe3O4+8H和C+4H—CH4);水汽波动区的内壁缺陷缝隙处炉水杂质浓缩。
防范措施:
提高焊接质量;减少焊接残余应力;控制锅炉启停温度变化速度;保证汽包汽水品质;保证焊缝外部成形良好,焊缝处尖角或腐蚀坑应打磨圆滑过渡,避免几何突变而产生的局部应力集中。
7.1.4内壁腐蚀
主要发生在汽包下部(水侧)内壁,焊缝和下降管内壁易发生点蚀。
特征:
腐蚀区无过热现象、无结垢覆盖;应力集中区的腐蚀坑沿轴向变长,甚至产生腐蚀裂纹;点腐蚀发展会引起穿透泄漏,甚至诱导出应力腐蚀和疲劳裂纹。
产生原因:
电化学腐蚀,发生在管壁内表面钝化膜破裂处。
在制造、安装、运行个阶段都会发生氧腐蚀;应力集中区促进点蚀形成;内壁中性区受到热冲击时会产生疲劳裂纹;停炉期间局部存水会产生内壁腐蚀。
防范措施:
加强管道制造、安装和停炉期间防腐保护;新炉运行前应化学清洗,去除杂物;新管道运行前应进行钝化处理,在内壁形成一层均匀保护膜;运行期间应保证炉水品质,控制Ph值含氧量。
7.2主蒸汽管道
高温高压管系在运行中承受三类复杂应力:
一次应力:
由内压和持续外载产生的应力;
二次应力:
由热胀冷缩等形变受约束产生的应力
峰值应力:
由局部应力集中产生的一次应力和二次应力的增量。
蠕变损坏主要原因:
一次应力+峰值应力过高。
疲劳损坏主要原因:
二次应力+峰值应力过高。
(二次应力多次交替)
7.2.1石墨化
低碳、低合金耐热钢在高温下(如碳钢≥450℃、钼钢≥485℃)长期运行,金相组织中会同时发生珠光体球化及石墨化现象。
从而使管道强度、塑性降低,脆性增加,加速了管道蠕变损伤速度。
珠光体球化及石墨化严重时,可导致管道发生突发性脆性爆管重大事故。
1943年,美国斯勃林格-焦耳电厂曾发生了主蒸汽管道爆破的重大恶性事故。
世界各国因此开展了火电厂中温中压主蒸汽管道石墨化的研究工作。
产生原因:
石墨化是金属在高温和长时间工作的条件下,碳化物中的碳原子扩散并缓慢迁移的过程。
随着时间的增加,碳原子逐渐聚集并长大,最终以圆形石墨的形式形成于晶界处。
由于石墨强度、塑性几乎为零,分布在钢中的石墨相当于钢中的一个个圆形孔洞,从而减少了钢的有效截面积,导致管道应力增加。
另外碳化物和固溶体中的碳原子大量迁移后,将分别削弱碳化物的强度以及固溶体的固溶强化作用,从而导致钢的强度、塑性降低,脆性增加,并加速了蠕变损伤破坏速度。
防护措施:
使用含铬的低合金耐热钢替代碳钢和钼钢,可有效的阻止石墨析出;不用铝、硅(促进石墨化元素)脱氧炼钢;控制锅炉运行参数,不超温、超压;对超十万小时运行的主蒸汽管道进行石墨化普查;及时更换严重石墨化的管道。
7.2.2内壁点蚀
主要发生在水平直管段和弯头处。
腐蚀特点、原因、防范措施同汽包内壁腐蚀。
7.2.3蠕变
蠕变失效多发生于弯头背弧侧,阀门壳体变截面处,三通内壁肩部和外壁腹部。
受管外壁高拉应力作用,蠕变裂纹首先沿管外壁形成并沿纵向发展。
在主裂纹附近,平行分布着众多的微小裂纹,裂纹沿晶扩展,与拉应力垂直沿轴向分布的蠕变孔洞较多。
断口粗糙无明显塑性变形、呈现脆性断口特征。
产生原因:
一次应力和峰值应力过高(如弯头背弧),长期超温超压运行,表面原始缺陷和划痕形成裂纹源,焊缝及热影响区焊接残余应力,均可加速蠕变破断速度;错用低等级钢材,可导致初期运行阶段蠕变破断。
防护措施:
检查调整支吊架,减少管系膨胀位移受阻而产生的局部应力集中;提高管件制造质量,减少表面原始缺陷;管件截面变化应圆滑过渡,避免几何形状突变产生局部应力集中;采用中频弯管,控制弯管椭圆度;严格执行热处理工艺,保证管件性能;管材逐根光谱复查,杜绝错用钢材;控制运行参数,防止超温超压运行。
7.2.4疲劳
疲劳裂纹主要发生在:
高应力低周疲劳裂纹沿管孔周向分布、局部应力集中区,垂直于气流方向;热疲劳产生于受水侵入的管道内外壁,成龟裂状。
断口具有疲劳断口特征,裂纹穿晶扩展,裂纹内充满氧化腐蚀产物。
产生原因:
在二次应力反复作用下(如锅炉启停过程),局部应力集中区产生高应力低周疲劳破坏;腐蚀加剧疲劳扩展速度。
防护措施:
检查调整支吊架,减少管系膨胀位移受阻而产生的局部应力集中;管道加装镀锌铁皮保护,防止水侵入保温层腐蚀管道;防止排气管道凝结水返回;控制运行调整,防止热冲击。
7.2.5焊缝
焊缝裂纹主要发生在:
联箱连接短管角焊缝;异径管对接焊缝;异种钢对接焊缝;管件与铸件焊缝。
产生原因:
焊缝缺陷超标、焊接残余应力过大、化学成分偏析、执行热处理工艺不当;焊缝外观成型不良(如焊缝超高、凹陷)、异径管对接接头未削薄处理,造成几何突变产生局部应力集中;组合应力值过高(一次应力+二次应力+峰值应力);焊缝硬度值超标;异种钢焊接接头在高温下发生碳迁移,高合金侧增碳、低合金侧脱碳,造成焊接接头局部强度降低。
防护措施:
严格执行焊接工艺,保证焊接质量;改善焊接接头结构,降低局部应力集中;正确执行热处理工艺规范,减少焊接残余应力;正确选用焊接材料,减少异种钢焊接接头增碳、脱碳现象;加强无损探伤检验,避免超标缺陷漏检误判。
7.2.6铸造件
铸件泄漏主要发生在:
三通披肩和阀门壳体局部应力集中处;盐垢浓度高的疏松处。
产生原因:
铸件局部疏松严重;局部应力集中;启停炉受到热冲击导致疏松处形成裂纹而泄漏;停炉防腐措施不利,造成疏松处氧腐蚀而产生裂纹。
防护措施:
选用热轧三通;提高铸件质量,对疏松严重部位进行挖补处理;改进铸件结构,降低局部应力集中。
7.3锅炉受热面管
锅炉受热面管泄漏引起机组非停占机组非停一半以上,少发电量占全部事故少发电量也达到一半以上。
近年监控数据表明,该项指标有逐年上升的趋势。
由此看出锅炉受热面管泄漏已成为影响机组安全稳定运行的最大隐患。
锅炉受热面管在锅炉中所处位置不同,其工作环境差异很大。
由于设计、制造、安装、检修、运行工况、监督管理以及煤质等诸多因素交互作用将导致锅炉受热面管泄漏失效。
在查找分析原因时,应本着“具体情况、具体分析”的原则,结合爆漏管和对比管样的金属检验结果,全面考虑各种因素之间的相互影响进行综合诊断。
避免就单一表面现象盲目断下结论。
7.3.1蠕变
金属在一定温度和应力作用下,随时间延长而缓慢发生塑性变形的现象。
锅炉受热面管长期处于高温条件下工作,虽然承受的应力远小于额定工作温度下材料的屈服强度,但长期运行过程中会发生连续缓慢的塑性变形,引起管径增大。
当