热电分厂干法脱硫静电除尘运行规程.docx
《热电分厂干法脱硫静电除尘运行规程.docx》由会员分享,可在线阅读,更多相关《热电分厂干法脱硫静电除尘运行规程.docx(105页珍藏版)》请在冰豆网上搜索。
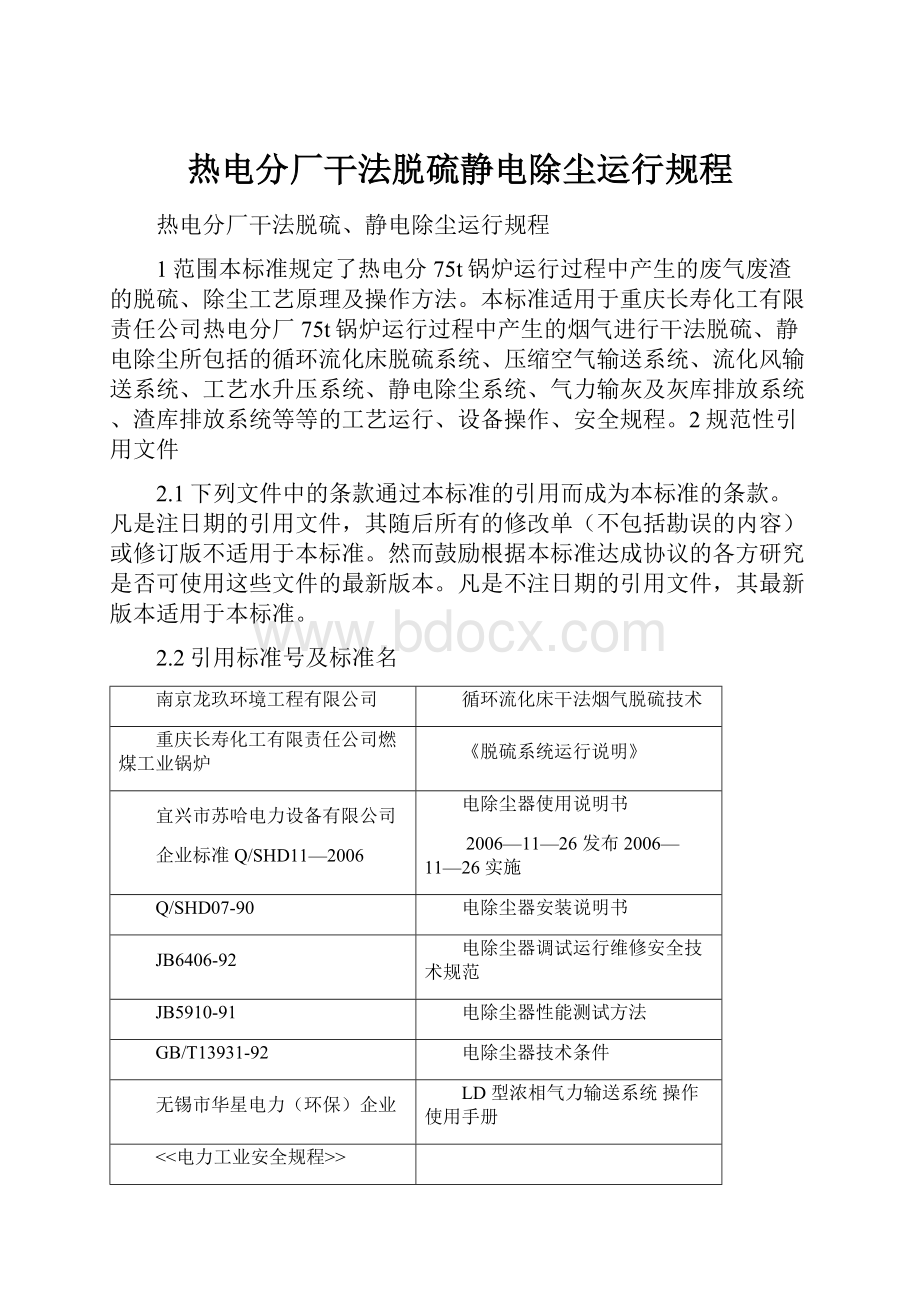
热电分厂干法脱硫静电除尘运行规程
热电分厂干法脱硫、静电除尘运行规程
1范围本标准规定了热电分75t锅炉运行过程中产生的废气废渣的脱硫、除尘工艺原理及操作方法。
本标准适用于重庆长寿化工有限责任公司热电分厂75t锅炉运行过程中产生的烟气进行干法脱硫、静电除尘所包括的循环流化床脱硫系统、压缩空气输送系统、流化风输送系统、工艺水升压系统、静电除尘系统、气力输灰及灰库排放系统、渣库排放系统等等的工艺运行、设备操作、安全规程。
2规范性引用文件
2.1下列文件中的条款通过本标准的引用而成为本标准的条款。
凡是注日期的引用文件,其随后所有的修改单(不包括勘误的内容)或修订版不适用于本标准。
然而鼓励根据本标准达成协议的各方研究是否可使用这些文件的最新版本。
凡是不注日期的引用文件,其最新版本适用于本标准。
2.2引用标准号及标准名
南京龙玖环境工程有限公司
循环流化床干法烟气脱硫技术
重庆长寿化工有限责任公司燃煤工业锅炉
《脱硫系统运行说明》
宜兴市苏哈电力设备有限公司
企业标准Q/SHD11—2006
电除尘器使用说明书
2006—11—26发布2006—11—26实施
Q/SHD07-90
电除尘器安装说明书
JB6406-92
电除尘器调试运行维修安全技术规范
JB5910-91
电除尘器性能测试方法
GB/T13931-92
电除尘器技术条件
无锡市华星电力(环保)企业
LD型浓相气力输送系统操作使用手册
<<电力工业安全规程>>
<<电除尘设计技术规范>>
DMC脉冲袋式除尘器说明书
湖北潜江江汉环保有限公司
3脱硫工段的工艺设备开、停车——75t/h锅炉系统
3.1锅炉排烟工艺:
脱硫:
保证烟囱所排烟气含SO2<400mg/m3
烟气工艺指标
除尘:
保证烟囱所排烟气含烟尘<50mg/m3
(锅炉空预器)(烟气)(第一电场静电除尘器)(循环流化床脱硫反应器)
(机械除尘器)(脱硫后四电场静电除尘器)
(锅炉引风机)(净化烟气从烟囱排空)
3.2脱硫工段开车操作:
3.2.1首先启动运行静电除尘器的低压控制系统:
锅炉点火前一天或提前8h,绝缘子加热,阴极瓷轴加热。
锅炉点火前2h,手动连续运行阴极振打、阳极振打0.5h~2h,
然后投入自动定时振打程序运行。
3.2.1.1加热控制系统的具体操作步骤:
a)低压柜后门的总电源空气开关合闸。
b)用钥匙打开低压柜前门,合闸电源空气开关,合闸PLC控制系统电源空气开关。
c)用钥匙打开门面上的控制系统门锁,出现PLC控制画面。
d)锅炉点火前一天,或锅炉点火前8h,绝缘子加热,阴极瓷轴加热。
打开低压柜前门,合闸绝缘子加热的5个控制系统电源空气开关,合闸阴极瓷轴加热的5个控制系统电源空气开关。
e)PLC控制画面触摸屏,在主画面点出加热控制系统。
f)在加热控制系统的绝缘子加热画面上,设定低限温度90℃,设定高限温度105℃,依次点出一、二、三、四、五电场的绝缘子自动加热,画面上自动控制红灯亮,每个电场的绝缘子加热状态指示灯在加热时亮绿灯。
所加热的绝缘子温度低于90℃时,控制系统持续加热升温,当所加热的绝缘子温度高于105℃时,控制系统自动跳开,停止加热。
g)在加热控制系统的阴极瓷轴加热画面上,设定低限温度90℃,设定高限温度105℃,依次点出一、二、三、四、五电场的阴极瓷轴自动加热,画面上自动控制红灯亮,每个电场的阴极瓷轴加热状态指示灯在加热时亮绿灯。
所加热的阴极瓷轴温度低于90℃时,控制系统持续加热升温,当所加热的阴极瓷轴温度高于105℃时,控制系统自动跳开,停止加热。
h)加强循环检查,每小时记录绝缘子加热和阴极瓷轴加热的当前温度,如果发现参数波动很大,立即联系相关职能人员处理。
绝缘子
加热
当前温度
设定
上限温度
设定
下限温度
自动加热指示灯
手动加热指示灯
加热状态指示灯
一
105℃
90℃
○
○
○
二
105℃
90℃
○
○
○
三
105℃
90℃
○
○
○
四
105℃
90℃
○
○
○
五
105℃
90℃
○
○
○
阴极瓷轴
加热
当前温度
设定
上限温度
设定
下限温度
自动加热指示灯
手动加热指示灯
加热状态指示灯
一
105℃
90℃
○
○
○
二
105℃
90℃
○
○
○
三
105℃
90℃
○
○
○
四
105℃
90℃
○
○
○
五
105℃
90℃
○
○
○
3.2.1.2振打控制系统的具体操作步骤:
a)阳极振打就地控制柜和阴极振打就地控制柜的控制系统切换到远程自动控制。
b)打开低压柜前门,合闸阳极振打的5个控制系统电源空气开关,合闸阴极振打的5个控制系统电源空气开关。
c)在低压加热控制系统正常运行的情况下,点出PLC控制画面触摸屏主画面上的振打控制系统。
d)在阳极振打控制系统的画面上,设定运行时间和停止时间。
1首先手动连续进行阳极振打和阴极振打约0.5h~2h,这时电场的手动振打指示红灯亮。
2然后依据设定的时间,自动定时进行阳极振打和阴极振打,这时各电场的自动振打指示红灯亮,并且振打状态指示绿灯亮,并且显示当前振打或停止的时间。
e)加强循环检查,每小时记录阳极振打和阴极振打的运行时间或停止时间,如果发现参数波动很大,立即联系相关职能人员处理。
阳极
振打
当前
运行时间
当前
停止时间
设定
运行时间
设定
停止时间
自动振打指示灯
手动振打指示灯
振打状态指示灯
一
150s
150s
○
○
○
二
150s
300s
○
○
○
三
150s
450s
○
○
○
四
150s
600s
○
○
○
五
150s
750s
○
○
○
阴极
振打
当前
运行时间
当前
停止时间
设定
运行时间
设定
停止时间
自动振打指示灯
手动振打指示灯
振打状态指示灯
一
300s
300s
○
○
○
二
300s
600s
○
○
○
三
300s
900s
○
○
○
四
300s
1200s
○
○
○
五
300s
1500s
○
○
○
3.2.2其它系统运行前的准备工作
a)准备好脱硫剂加料仓的消石灰物料。
b)手动打开脱硫塔底部烟道的手动插板阀。
c)手动打开静电除尘器灰斗底部排灰的手动插板阀。
d)手动打开每一个仓泵顶部的手动进料插板阀。
第一电场静电除尘器的5#仓泵、脱硫后四电场的1#仓泵、2#仓泵、3#仓泵、4#仓泵
e)启动运行空气吹送系统的设备(启动运行空压机、冷干机)。
f)手动打开各个启动控制系统的气源调节阀(包括仓泵、灰库气化槽),并且调节好流量。
g)启动运行流化风及加热系统的设备
h)手动调节各个加热的流化风控制阀。
(脱硫剂加料仓,脱硫中间灰仓,脱硫剂返料空气斜槽,包括静电除尘器的4个灰斗,机械沉降室灰斗。
)
i)确认渣库、粗灰库、细灰库已经排空,有足够的容积储存渣、灰。
j)启动运行输灰系统的设备。
k)启动运行渣库的排渣系统设备。
3.2.3空气吹送系统工艺流程:
(1#或2#或3#螺杆式空压机输出压缩空气)(冷干机)(1#储气罐)
(除盐水系统)
(锅炉点火系统)、(电磁调节阀气动控制系统)(气力输灰系统)
(1#或2#螺杆式空压机输出压缩空气)(2#储气罐)
(脱硫反应器的增湿喷雾风)
3.2.4空气吹送系统的具体操作步骤:
a)在配电室合闸送电空压机和冷干机。
b)在空压机房确认备用空压机的出口阀关闭。
压缩空气过滤筒的旁道阀关闭,将要运行的空压机出口阀打开,压缩空气过滤筒前后的控制阀打开,储气罐的进口阀打开。
c)打开冷干机的排污阀排空污水,然后关闭排污阀。
d)点击空压机的启动运行按钮。
e)观察冷干机的冷凝压力约11KPa×100,蒸发压力约11KPa×100,点击启动运行冷干机。
f)观察冷干机的蒸发压力约4~5KPa×100,冷凝压力约15KPa×100左右,约15分钟后,关闭它的排污阀。
g)观察储气罐的压力逐步上升到0.6~0.8MPa,
(除盐水系统)
(锅炉点火系统)、(电磁调节阀气动控制系统)(气力输灰系统)打开各自所需要的供气阀。
(脱硫反应器的增湿喷雾风)
并且调节各供气阀的阀位开度,保证各系统所需的气源压力。
h)加强巡回检查,每小时记录空压机的排气压力和排气温度,每小时记录冷干机的冷凝压力和蒸发压力。
i)每个班组检查冷干机的自动疏水阀定时排出污水及杂质。
然后完全关闭排污阀。
每个班组每小时打开储气罐底部的排污阀1次,排尽污水及杂质。
3.2.5输灰系统运行流程:
开空压机开冷干机开1#灰库和2#灰库的仓顶布袋除尘器运行5台仓泵
输灰流程:
(机械除尘器)(第二、第三电场灰斗)
(第一电场
静电除尘器灰斗)(脱硫中间灰仓)(第四电场灰斗)(第五电场灰斗)
(5#仓泵)(1#、2#台仓泵)(3#仓泵)(4#仓泵)
(1#灰库300m3)(2#灰库150m3)
双轴加湿搅拌机双轴加湿搅拌机
排放湿灰排放湿灰
干灰散装机干灰散装机
(排放干灰)(排放干灰)
汽车运走汽车运走
(罐车运走)(罐车运走)
3.2.5.1仓泵的运行流程:
进料加压输出物料吹扫管道
具体的操作步骤
开排气阀、开进料阀料位计显示仓满、关进料阀、关排气阀开加压阀
观察压力表显示约100~150(KPa×100)开防堵阀、开输出阀
观察压力表降压到0(KPa×100),关输出阀、关防堵阀,关加压阀系统吹扫。
以上程序循环往复,不断排出灰斗的存灰。
注:
吹扫流程:
开加压阀观察压力表显示约100~150(KPa×100),
开防堵阀、开输出阀,观察压力表降压到0(KPa×100),
关防堵阀、关输出阀,关加压阀。
3.2.5.2可现场“手动”控制运行仓泵,或就地柜投到“自动”档,利用PLC控制5台仓泵运行。
a)5#仓泵独立运行,输灰送到1#灰库。
2#灰库
1#管道切换阀
b)1#仓泵出口阀2#仓泵出口阀
2#管道切换阀
3#仓泵出口阀4#仓泵出口阀
所以:
1#仓泵、2#仓泵、3#仓泵、4#仓泵必须轮流运行,并且轮流打开切换阀,
保证输灰过程中避免管道堵塞。
3.2.5.3自动排灰系统运行:
a)先吹扫管道2次:
根据设定的下限压力值打开加压阀达到设定下限压力值(约100~150(KPa×100)),
关闭加压阀打开防堵阀、打开出料阀排空仓泵内的物料。
b)然后依据下面的3个工作流程循环往复运行。
排气阀开、进料阀开(根据设定的时间)到达设定时间(或仓泵内的高料位满)
关闭进料阀、关闭排气阀,根据设定的下限压力值(约100~150(KPa×100)),
打开加压阀仓泵内的压力达到设定下限值(约100~150(KPa×100)),
打开防堵阀、打开出料阀输出物料,观察压力表降压到0(KPa×100)
关防堵阀、关输出阀,关加压阀。
c)停车时,退出相应的仓泵运行后,自动控制系统还会发出指令,继续吹扫输灰管道2次,
清空仓泵及输灰管道内的积灰。
3.2.5.4自动输灰控制系统的注意事项:
a)如果设定的进料时间未到,但是仓泵的高料位已经报警,这时进料阀、排气阀会自动关闭。
b)如果设定的进料时间已过,但是进料阀、排气阀没有自动关闭,判定进料阀或自动控制系统可能已经出现故障。
c)如果设定的加压时间未到,但是仓泵的设定下限压力已足,这时加压阀会自动关闭,然后自动打开防堵阀、出料阀。
d)如果设定的加压时间已过,但是仓泵的设定下限压力不足,排定加压阀或压力控制系统可能出现故障。
e)仓泵在排灰时,如果仓泵内加足的压力很快就降下了,在设备状况良好的情况下,判定仓泵内没有积灰。
3.2.6流化风系统启动运行:
开罗茨风机开电加热器(出口温度约110℃)
打开各个气化槽的流化风控制阀
气化槽所在部位:
脱硫剂加料仓、脱硫中间灰仓、机械除尘器灰斗、
脱硫灰返料系统的空气斜槽、脱硫后四个电场的灰斗。
3.2.7脱硫:
运行循环流化床脱硫控制系统(工艺指标:
出口烟气含SO2<400mg/m3)
锅炉排烟的脱硫工艺流程简图
烟气
1#
灰库
a)脱硫剂储备及输送系统:
(罐车)(加料仓)(给料螺旋输送机)(循环流化床脱硫反应器)
b)脱硫灰返料系统:
(机械除尘器和第一、第二电场灰斗排灰)(中间灰仓)返料螺旋输送机输灰系统
(空气斜槽)(循环流化床脱硫反应器)
(罗茨风机)(电加热器)
c)气水系统:
(工艺水升压泵)电磁调节阀(增湿喷雾枪)
(空压机)(冷干机)脱硫喷雾风
d)循环流化床启动运行:
压缩空气:
1#或2#空压机冷干机2#储气罐脱硫喷雾风
根据脱硫塔出口的运行烟气压差调节返料螺旋输送机的转速
(针对相应的锅炉负荷,引风机转速,确定有相应的脱硫基础压差)
(脱硫基础压差之上加200~400Pa为脱硫喷水压差)
(脱硫基础压差之上加600~800Pa为脱硫运行压差)
附:
脱硫基础压差统计表及脱硫运行要点。
调节加料仓底部电动插板阀的开度,调剂给料星排的转速,控制脱硫SO2达标。
根据脱硫喷水压差起始值,启动工艺水管道泵投运增湿喷雾系统
调控喷雾水工作压力:
0.3MPa调控喷雾风工作压力:
0.5~0.6MPa
控制脱硫塔出口温度约80℃~120℃,调节增湿喷雾水量。
3.2.8静电除尘器高压电场启动运行(工艺指标:
出口烟气含烟尘<50mg/m3)
当锅炉燃烧70%以上,或烟气温度达到110℃,依次投入高压电场运行:
第一电场电场、第一电场、第二电场、第三电场、第四电场。
高压静电场控制系统的具体操作步骤:
a)静电除尘器顶部的二点式高压隔离开关打到电源位置。
b)高压柜后门的连锁控制箱,用钥匙打开门锁,合闸柜内的电源空气开关。
c)用钥匙打开连锁柜门上的高压连锁预除尘电场、一电场、二电场、三电场、四电场的
上、下连锁开关。
d)用钥匙打开高压柜前门,合闸电源空气开关,合闸PLC控制系统电源空气开关。
e)依据烟气流向,逐个启动运行预除尘电场、一电场、二电场、三电场、四电场的高压放电控制系统,应当确认上一级高压电场运行正常后,才可以投运下一级高压电场,
f)加强循环检查,每小时记录预除尘电场、一电场、二电场、三电场、四电场的PLC控制画面显示一次电流、一次电压,二次电流、二次电压,点击菜单显示硅整流变压器的当前油温(随后的跳闸油温为95℃)。
投运初期,二次电流控制在100mA内。
如果发现参数波动很大,立即联系相关职能人员处理。
3.2.9渣库排渣系统投运,可适当打开振打器(振打时间1分钟/次)。
保证存渣不能超过80%
确认渣库仓顶布袋除尘器开。
渣库容积300m3(存渣不能超过80%)
湿渣:
开加湿水开加湿搅拌机开湿渣卸料电动闸板阀
干渣:
开抽风机下降放料筒(料位风机自动运行)开干渣卸料阀
3.2.10灰库排渣:
(存灰不能超过80%)
确认灰库仓顶布袋除尘器开。
干灰:
开抽风机下降放料筒(料位风机自动运行)开干灰卸料阀
3.3脱硫工段的停车操作:
3.3.1停脱硫:
停增湿喷雾系统(停工艺水升压泵)停给料系统返料螺旋输送机转化为反转输灰。
3.3.2停静电除尘器:
a)值班长通知锅炉停车10~30分钟后,停高压电场。
PLC控制画面点击下移解裂高压电(阴极、阳极为开路)高压直流电降低到0,
点击停止按钮,退出高压电场。
用钥匙打开高压柜门,断开电源空气开关和PLC控制电源空气开关,然后关闭高压柜门上的
PLC控制画面电源锁,取出钥匙保管好备用。
必须依五、四、三、二、一、倒退的顺序,逐个退出高压电场。
最后按停止运行。
关闭联锁控制柜上各个电场的上、下联锁,取出钥匙保管好备用。
b)停低压控制系统
高压电场停止后手动连续振打约0.5h~2h后,停阴极振打、停阳极振打
停绝缘子加热,停阴极磁轴加热断开控制柜的电源
3.3.3停输灰系统:
排空每个静电场灰斗内的灰尘停止灰斗加热系统停止仓泵输灰
依次退出5台仓泵停灰库顶布袋除尘器断开控制柜的电源
3.3.4停流化风系统:
停电加热器停罗茨风机
3.3.5停空气吹送系统:
停冷干机停空压机打开冷干机和压缩空气储罐的排污阀,
排尽污水和杂质后完全关闭排污阀断开冷干机和空压机的电源
3.3.6灰库停止放灰(排灰装满罐车后停止放灰)
干灰:
停干灰卸料阀上升放料筒(料位风机自动停)5分钟后停抽风机
3.3.7渣库停止放渣(排渣装满翻斗车厢后停止放渣)
湿渣:
停湿渣卸料电动闸板阀5分钟后停加湿搅拌机停加湿水
干渣:
停干渣卸料阀上升放料筒(料位风机自动停)5分钟后停抽风机
4干法脱硫工艺运行规程
4.1脱硫系统工艺、系统及规范
4.1.1脱硫工艺原理简述
4.1.1.1CFB烟气脱硫工艺是八十年代末德国鲁奇(LURGI)公司开发的一种新的干法脱硫工艺,这种工艺以循环流化床原理为基础,通过吸收剂的多次再循环,延长吸收剂与烟气的接触时间,大大提高了吸收剂的利用率。
它不但具有干法工艺的许多优点,如流程简单、占地少,投资小以及副产品可以综合利用等,而且能在很低的钙硫比(Ca/S=1.1~1.3)情况下达到湿法工艺的脱硫效率,即95%以上。
实践证明,CFB烟气脱硫工艺处理能力大,对负荷变动的适应能力很强,运行可靠,维护工作量少,且具有很高的脱硫效率。
CFB工艺是本公司在自主知识产权干法脱硫技术的基础上,结合本公司在大型火电厂烟气脱硫工程实践中积累的丰富经验,并消化吸收国外先进技术,开发的一种先进的干法脱硫工艺。
CFB工艺系统由吸收剂加料系统、吸收塔、吸收剂循环除尘器以及控制系统等组成。
烟气由流化床下部布风板进入流化床反应塔,与消石灰颗粒充分混合,HCl、HF、SO2、SO3和其他有害气体与消石灰反应,生成CaCl2·2H2O、CaF、2CaSO3·1/2H2O、CaSO4·2H2O和CaCO3。
反应产物由烟气从反应塔上部带出,经循环除尘器分离。
分离出的固体绝大部分被送回流化床反应器,以延长吸收剂的作用时间,提高利用效率。
将水直接喷入反应室下部,使反应温度尽可能接近露点温度,以提高脱硫效率。
CFB烟气脱硫工艺的吸收剂可以外购成品氢氧化钙细粉,由于这种消石灰颗粒很细,因此无须磨细,既节省了购买磨机等大型设备的投资费用,也减少了能源消耗,使运行费用大为降低。
CFB烟气脱硫工艺所产生的副产品呈干粉状,其化学组成与喷雾干燥工艺的副产品相类似,主要有飞灰、CaCl2、CaSO3、CaSO4、CaF2以及未反应的吸收剂等组成,其处置方法与喷雾干燥的副产品基本相同。
脱硫系统运行后,脱硫运行产出物为飞灰与硫酸钙、亚硫酸钙及脱硫剂的混合物,含钙量较高,脱硫渣利用价值较高。
主要的综合利用途径有:
a)脱硫渣量较小时,可直接制作噪音吸声板;
b)如多台机组实施脱硫后,脱硫渣量较大,可设置一小型建材厂,利用脱硫渣做原料,制备建筑材料;
c)可作为建材行业灰渣砖制备原料;
d)由于脱硫渣含灰量低,密实度高,可用于道路基础底料。
e)可用于盐碱地的土壤改造。
4.1.1.2工艺原理
循环流化床干法工艺的原理是Ca(OH)2粉末和烟气中的SO2和几乎全部的SO3、HCl、HF等酸性气体,在Ca(OH)2粒子的液相表面发生反应,反应如下:
Ca(OH)2+2HCl→CaCl2+2H2O
Ca(OH)2+2HF→CaF2+2H2O
Ca(OH)2+SO2→CaSO3+H2O
Ca(OH)2+SO3→CaSO4+H2O
Ca(OH)2+SO2+1/2O2→CaSO4+H2O
在循环流化床干法工艺的循环流化床内,Ca(OH)2粉末、烟气及喷入的水分,在流化状态下充分混合,并通过Ca(OH)2粉末的多次再循环,使得床内参加反应的Ca(OH)2量远远大于新投加的Ca(OH)2量,即实际反应的吸收剂与酸性气体的摩尔比远远大于表观摩比,从而使HCl、HF、SO2、SO3等酸性气体能被充分地吸收,实现高效脱硫。
循环流化床干法工艺系统主要由消石灰贮存输送系统、循环流化床吸收塔、喷水增湿系统、回料系统、脱硫渣输送系统、脱硫除尘器以及仪表控制系统组成。
首先从锅炉的空气预热器出来的烟气温度一般为120~180℃左右,从底部进入吸收塔,然后烟气通过吸收塔底部的文丘里管的加速,进入循环流化床体,物料在循环流化床里,气固两相由于气流的作用,产生激烈的湍动与混合,充分接触,在上升的过程中,不断形成聚团物向下返回,而聚团物在激烈湍动中又不断解体重新被气流提升,使得气固间的滑移速度高达单颗粒滑移速度的数十倍。
这样的循环流化床内气固两相流机制,极大地强化了气固间的传质与传热,为实现高脱硫率提供了保证。
在文丘里的出口扩管段设一套喷水装置,喷入雾化水以降低脱硫反应器内的烟温,使烟温降至高于烟气露点20℃左右,从而使得SO2与Ca(OH)2的反应转化为可以瞬间完成的离子型反应。
吸收剂、循环脱硫灰在文丘里段以上的塔内进行第二步的充分反应,生成副产物CaSO3·1/2H2O,还与SO3、HF和HCl反应生成相应的副产物CaSO4·1/2H2O、CaF2、CaCl2·Ca(OH)2·2H2O等。
烟气在上升过程中,颗粒一部分随烟气被带出吸收塔,一部分因自重重新回流到循环流化床内,进一步增加了流化床的床层颗粒浓度和延长吸收剂的反应时间,从而有效地保证了脱硫效率。
喷入用于降低烟气温度的水,通过以激烈湍动的、拥有巨大表面积的颗粒作为载体,在塔内得到充分蒸发,保证了进入后续除尘器中的灰具有良好的流动性能。
由于SO3几乎全部得以去除,加上排烟温度始终控制在高于露点温度20℃,因此烟气不需要再加热,同时整个系统也无须任何防腐处理。
净化后的含尘烟气从吸收塔顶部侧向上排出,然后转向进入脱硫除尘器,再通过锅炉风机排入烟囱。
经除尘器捕集下来的固体颗粒,通过除尘器下的再循环系统,返回吸收塔继续参加反应,如此循环,多余的少量脱硫灰渣通过物料输送至脱硫灰仓内,再通过罐车或二级输送设备外排。
我们采用的循环流化床干法烟气脱硫技术的工艺、结构特点如下:
a)设备使用寿命长、维护量小
塔内完全没有任何运动部件和支撑杆件,操作气速合理,塔内磨损小,没有堆积死角,设备使用寿命长、检修方便。
b)烟气、物料、水在剧烈的掺混升降运动中接触时间长、接触充分,脱硫效率高。
由于设计选择最佳的操作气速,使得气固两相流在吸收塔内的滑移速度最大,脱硫反应区床层密度高,颗粒在吸收塔内单程的平均停留时间长,烟气在塔内的气固接触时间高达6秒以上,使得脱硫塔内的气固混合、传质、传热更加充分,优化了脱硫反应效果,从而保