太阳能电池生产工艺及关键设备.docx
《太阳能电池生产工艺及关键设备.docx》由会员分享,可在线阅读,更多相关《太阳能电池生产工艺及关键设备.docx(13页珍藏版)》请在冰豆网上搜索。
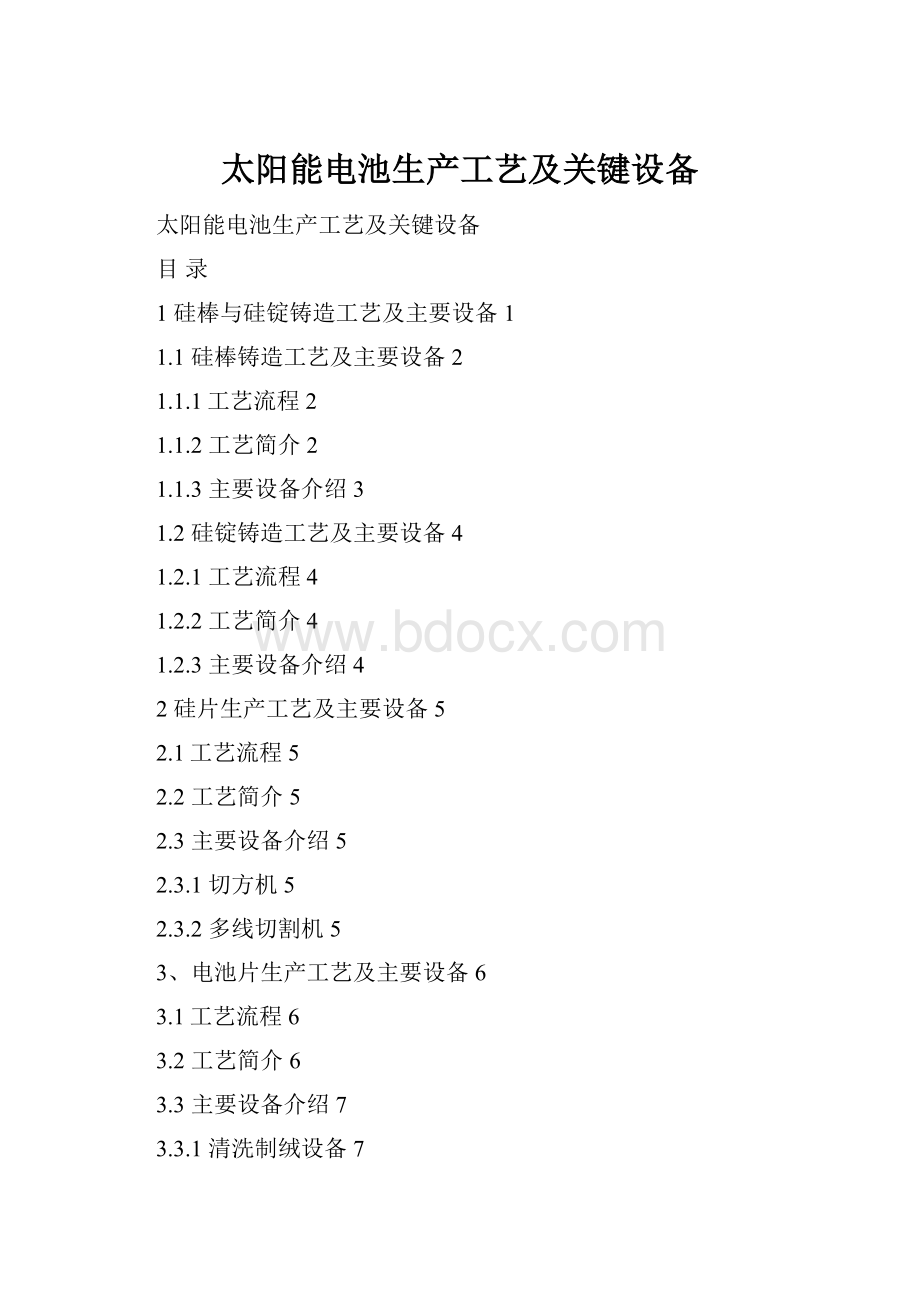
太阳能电池生产工艺及关键设备
太阳能电池生产工艺及关键设备
目录
1硅棒与硅锭铸造工艺及主要设备1
1.1硅棒铸造工艺及主要设备2
1.1.1工艺流程2
1.1.2工艺简介2
1.1.3主要设备介绍3
1.2硅锭铸造工艺及主要设备4
1.2.1工艺流程4
1.2.2工艺简介4
1.2.3主要设备介绍4
2硅片生产工艺及主要设备5
2.1工艺流程5
2.2工艺简介5
2.3主要设备介绍5
2.3.1切方机5
2.3.2多线切割机5
3、电池片生产工艺及主要设备6
3.1工艺流程6
3.2工艺简介6
3.3主要设备介绍7
3.3.1清洗制绒设备7
3.3.2扩散炉7
3.3.3等离子刻蚀机8
3.3.4PECVD8
3.3.5丝网印刷机8
3.3.6烧结炉9
4组件生产工艺及主要设备9
4.1工艺流程9
4.2工艺简介9
4.3主要设备介绍10
4.3.1层压机10
4.3.2太阳能电池分选仪10
4.3.3组件测试仪11
1硅棒与硅锭铸造工艺及主要设备
在硅锭和硅棒的制备中存在两种不同的技术路线,即多晶铸造和直拉单晶,两种生长技术相比,各有优劣。
直拉单晶棒中[C]杂质非常少,且基本无位错存在,所以制得的优质电池片最终转换效率在17%-23%之间。
但由于一炉只能拉取一根硅棒,产量有限,能耗非常高,且圆形硅棒需要切除四个圆弧边才能继续使用。
同时直拉单晶过程的自动化程度不高,晶棒的质量在很大程度上有赖于操作工的技能。
由于坩埚和晶棒在这个拉制过程中处于旋转状态,强迫对流使得杂质和缺陷出现径向分布,极易引起氧诱导推垛层错环(OSF)和空隙或空位团的漩涡缺陷,这些因素会让单晶片质量直线下降。
同时由于坩埚的原因,单晶棒中氧杂质的控制非常困难,使得单晶电池片的衰减非常厉害,影响使用寿命。
多晶铸造一次成锭16-36块,随着技术的发展该单锭所包含的块数也会随之增加,能耗也较之直拉单晶降低很多。
且多晶铸造可以实现大规模全自动化的生产过程,极大减少了人力成本,且降低了误操作带来的风险。
但是多晶在晶核生成阶段有很大的随机性,这就使得硅晶粒之间的边界形成各种各样的“扭折”,使位错的簇或线形式的结构缺陷成核。
这些位错缺陷往往吸引硅中的杂质,并最终造成了多晶硅制成的光伏电池片中电荷载流子的快速复合,降低电池的转换效率。
目前多晶硅制得的电池片转换效率16%-18%之间。
以下将对两种不同的制造工艺进行介绍:
1.1硅棒铸造工艺及主要设备
1.1.1工艺流程
装料与熔料——熔接——引细颈——放肩——转肩——等径生长——收尾
1.1.2工艺简介
装料与熔料:
将多晶硅料投入单晶炉中,加热使其溶化。
熔接:
当硅料全部熔化后,调整加热功率以控制熔体的温度。
按工艺要求调整气体的流量、压力、坩埚位置、晶转、埚转。
硅料全部熔化后熔体必须有一定的稳定时间达到熔体温度和熔体的流动的稳定。
装料量越大,则所需时间越长。
待熔体稳定后,降下籽晶至离液面3~5mm距离,使粒晶预热,以减少籽晶与熔硅的温度差,从而减少籽晶与熔硅接触时在籽晶中产生的热应力。
预热后,下降籽晶至熔体的表面,让它们充分接触,这一过程称为熔接。
在熔接过程中熔硅表面的温度适当,避免籽晶熔断(温度过高)或长出多晶(温度过低)。
引细颈:
虽然籽晶都是采用无位错硅单晶制备的,但是当籽晶插入熔体时,由于受到籽晶与熔硅的温度差所造成的热应力和表面张力的作用会产生位错。
因此,在熔接之后应用引细颈工艺,可以使位错消失,建立起无位错生长状态。
在籽晶能承受晶锭重量的前提下,细颈应尽可能细长,一般直径之比应达到1:
10。
放肩:
引细颈阶段完成后必须将直径放大到目标直径,当细颈生长至足够长度,并且达到一定的提拉速率,即可降低拉速进行放肩。
目前的拉晶工艺几乎都采用平放肩工艺,即肩部夹角接近180°,这种方法降低了晶锭头部的原料损失。
转肩:
晶体生长从直径放大阶段转到等径生长阶段时,需要进行转肩,当放肩直径接近预定目标时,提高拉速,晶体逐渐进入等径生长。
为保持液面位置不变,转肩时或转肩后应开始启动埚升,一般以适当的埚升并使之随晶升变化。
放肩时,直径增大很快,几乎不出现弯月面光环,转肩过程中,弯月面光环渐渐出现,宽度增大,亮度变大,拉晶操作人员应能根据弯月面光环的宽度和亮度,准确地判断直径的变化,并及时调整拉速,保证转肩平滑,晶体直径均匀并达到目标值。
等径生长:
当晶体基本实现等径生长并达到目标直径时,就可实行直径的自动控制。
在等径生长阶段,不仅要控制好晶体的直径,更为重要的是保持晶体的无位错生长。
收尾:
收尾的作用是防止位错反延。
在拉晶过程中,当无位错生长状态中断或拉晶完成而使晶体突然脱离液面时,已经生长的无位错晶体受到热冲击,其热应力往往超过硅的临界应力。
这时会产生位错,并将反延至其温度尚处于范性形变最低温度的晶体中去,形成位错排,星形结构。
一般来说,位错反延的距离大约等于生长界面的直径。
因此,在拉晶结束时,应逐步缩小晶体的直径直至最后缩小成为一点,这一过程称为收尾。
收尾可通过提高拉速,也可通过升高温度的方法来实现,更多的是将两种方法结合起来,收尾时应控制好收尾的速度,以防晶体过早地脱离液面。
目前先进的单晶炉可以实现从引晶到收尾的整个过程。
1.1.3主要设备介绍
单晶炉
单晶炉是一种在惰性气体环境中,用石墨加热器将多晶硅等多晶材料熔化,用直拉法生长无错位单晶的设备。
单晶炉市场国产化率已达到95%以上,国内厂家主要有晶龙集团、北京京运通、西安理工、上海汉虹、常州江南和天龙光电等。
据业内估计,2011年,中国单晶炉的市场容量在3000台左右。
相关参数:
国内现在主流的单晶炉炉产量为60~120kg,拉晶时间为40~50小时,月产12~14炉,年产能为1.5~2MW,成品率为80%左右。
单晶炉生产出来的硅棒直径一般为200mm。
价格:
一般90kg为80~90万元。
1.2硅锭铸造工艺及主要设备
1.2.1工艺流程
预热——熔化——长晶——退火——冷却
1.2.2工艺简介
预热阶段:
对坩埚中硅料进行缓慢加热,预热前要抽真空,预热过程是在真空条件下进行的。
熔化阶段:
在氩气的环境中使硅料充分融化为液态,为下一步凝固长晶做好准备。
长晶阶段:
坩埚中的熔融硅料自下而上,缓慢的进入冷场中,完成凝固长晶。
由于保温层的提升速度可自由控制,因此长晶速度可自由控制,缓慢进入冷场中,完成凝固长晶。
退火阶段:
防止降温过快对已长晶完成的硅锭造成的不良影响。
冷却阶段:
硅锭自然降温,为出炉做好准备。
硅料投入多晶硅铸锭炉后经过预热、熔化、长晶、退火、冷却五个步骤后凝固成具有固定形状的硅锭。
1.2.3主要设备介绍
多晶硅铸锭炉
多晶硅铸锭炉主要用于太阳能级多晶硅锭的大生产,是多晶硅铸锭的必需设备。
它采用先进的多晶硅定向凝固技术,将硅料高温熔融后通过特殊工艺定向冷凝结晶,从而达到太阳能电池生产用多晶硅品质的要求,是一种适用于长时间连续工作,高精度、高可靠性、自动化程度高的智能化大生产设备。
近年来多晶硅铸锭设备的制造取得了长足的进步,国内设备企业精功科技、京运通、晶盛机电的设备在市场上销售业绩成绩斐然,逐步夺回了由美国GTSOLAR和德国ALD占据多年的国内市场。
相关参数:
国内现在主流的多晶炉投炉量为450~550kg,铸锭时间在55~65小时,月产10~12炉,年产能为6~8MW,成品率为68%左右。
铸锭炉生产出来的硅锭的底面积一般为840mm*840mm(主流)。
价格:
一般500kg的设备国产价格为270~300万元,进口价格为320~350万元。
一般50MW的单晶生产线设备成本为2000~2500万元;多晶生产线,设备成本在1600~2100万元。
2硅片生产工艺及主要设备
2.1工艺流程
硅锭(硅棒)——切块(切方)——倒角抛光——粘胶——切片——脱胶清洗——分选检验包装
2.2工艺简介
切块或切方:
将硅锭或者硅棒切成适合切片的尺寸,一般硅锭切成25块(主流)。
倒角抛光:
将晶柱的圆面棱角研磨成符合要求的尺寸,对表面进行抛光处理,从而获得高度平坦的晶片。
粘胶:
用粘附剂把晶柱固定在由铝板和玻璃板组成的夹具上,自然硬化或用恒温炉使其硬化。
切片:
把晶柱切割成硅片,切割的深度要达到夹具上的玻璃板,以便在之后的程序中把硅片和玻璃分开。
脱胶清洗:
用清水清洗切成的硅片,在用热水浸泡,使硅片与玻璃板分开。
分选检验包装:
抽样检查厚度、尺寸、抗阻值等指标,全部检查破损、裂痕、边缘缺口,挑选出符合要求的硅片进行包装。
2.3主要设备介绍
2.3.1切方机
切方机是用来对硅棒、硅锭进行切割的设备。
该设备目前在国内已实现规模化生产,上海日进、大连连城、北京京仪世纪等公司都有成熟的产品投入市场。
一条50MW的硅片生产线需要配1台切方机即可,国产设备价格在280万左右。
2.3.2多线切割机
多线切割机是目前市场上用于切片最主流,也是最先进的设备。
它的基本原理是通过一根高速运动的钢线带动附着在钢丝上的切割刃料对硅棒进行摩擦,从而将硅棒等硬脆材料一次同时切割为数千片薄片的一种切割加工方法。
多线切割由于其更高效、更小切割损失以及更高精度的优势,对于切割贵重、超硬材料有着巨大的优势,近十年来已取代传统的内圆切割成为硅片切割加工的主要方式。
在光伏行业切片领域,到2009年底国内市场基本被瑞士的HCT、MeyerBurger(梅耶博格)和日本的NTC所统治。
近年来国内设备厂家上海日进、上海汉虹、电子集团45所、兰州瑞德、无锡开源、大连连城、北京京联发、湖南宇晶等也陆续推出了多线切割机样机。
从样机来看,技术原理和设计主要都是借鉴了日本的NTCMWM442D机型的很多理念,样机基本属于小型机。
国内开发的多线切割机样机都面临着类似的问题,成品率低、断线率高、控制精度差等。
加上硅料价格高昂,客户尝试新机器的成本非常高,每次的损失可能动辄几万甚至几十万,这也限制了设备制造企业很难获得更多的生产性实验数据来改进设备。
硅片的厚度对硅片成本的影响很大,如今市场上的硅片以180um和200um为主导,同时各企业正在不停地探索更薄硅片的切割工艺。
目前国内小部分企业硅片的硅耗量已经达到5.8g/w。
一条50MW的硅片生产线需要配置5~7台(单晶生产线所需切割机比多晶少)多线切割机,每台价格在200~400万元左右,国外同类产品的价格在500~600万元。
据估算,一条50MW的硅片生产线,设备总成本大概在2000~3000万元。
3、电池片生产工艺及主要设备
3.1工艺流程
硅片检测——清洗制绒——扩散制结——去磷硅玻璃——等离子蚀刻——镀减反射膜——丝网印刷——烘干烧结——测试分选
3.2工艺简介
硅片检测:
该工序主要用来对硅片的一些技术参数进行在线测量,这些参数包括硅片表面不平整度、少子寿命、电阻率、P/N型和微裂纹等。
清洗制绒:
通过硅的各向异性腐蚀,在每平方厘米硅表面形成几百万个金字塔结构。
由于入射光在表面的多次反射和折射,增加光的吸收,提高电池短路电流和转换效率。
制备绒面前,硅片须先进行初步表面腐蚀,用碱性或酸性腐蚀液去约20~25um,在腐蚀绒面后,进行一般的化学清洗。
经过表面准备的硅片都不宜在水中久存,以防沾污,应尽快扩散制结。
扩散制结:
形成PN结实现光能到电能的转换。
扩散炉为制备太阳能电池PN结的专用设备。
管式扩散炉主要由石英舟上下载部分、废气室、炉体部分和气柜部分四部分组成。
扩散一般用三氯氧磷液态源作为扩散源。
去磷硅玻璃:
通过化学腐蚀法将硅片放在氢氟酸溶液中浸泡,使其产生化学反应生成可溶性的络合物六氟硅酸,以去除扩散制结后在硅片表面形成的一层磷硅玻璃。
等离子刻蚀:
由于在扩散过程中,即使采用背靠背扩散,硅片的所有表面包括边缘都不可避免地扩散上磷。
PN结的正面所收集到得光生电子会沿着边缘扩散有磷的区域流到PN结的背面,而造成短路。
因此,必须对太阳能电池周边的掺杂硅进行刻蚀,以去除电池边缘的PN结。
镀减反射膜:
抛光硅表面的反射率为35%,为了减少表面反射,提高电池效率,需要沉积一层氮化硅减反射膜。
用PECVD制备减反射膜,即等离子增强型化学气相沉积。
丝网印刷:
太阳电池经过制绒、扩散及PECVD等工序后,已经制成PN结,可以在光照下产生电流,为了将产生的电流导出,需要在电池表面上制作正、负两个电极。
丝网印刷是采用压印的方式将预定的图形印刷在基本上,该设备由电池背面银铝浆印刷、电池背面铝浆印刷和电池正面银浆印刷三部分组成。
快速烧结:
经过丝网印刷后的硅片,不能直接使用,需经烧结炉快速烧结,将有机树脂粘合剂燃烧掉,剩下几乎纯粹的、由于玻璃质作用而密合在硅片上的银电极。
当银电极和晶体硅在温度达到共晶温度时,晶体硅原子以一定的比例融入到熔融的银电极材料中去,从而形成上下电极的欧姆接触,提高电池片的开路电压和填充因子两个关键参数,使其具有电阻特性,以提高电池片的转换效率。
测试分选:
通过测试数据监控生产电池片的效率及暗电流等参数是否正常,并且对相同性能电池片分在一起做成组件。
3.3主要设备介绍
3.3.1清洗制绒设备
主要用于单、多晶硅太阳能电池片生产,扩散前的绒面腐蚀和清洗。
目前在清洗制绒方式上采用的设备较流行的是一体式清洗机,从研磨片到电池片一步到位。
这种设备效率高,自动化程度高,但对硅片尺寸要求严格,维护起来也不太方便。
一条50MW的电池生产线,需配置1台清洗制绒机,价格在135万左右。
3.3.2扩散炉
扩散炉经历了开管、闭管、全封闭扩散三个阶段,绝大部分电池企业采用国产装备。
几年时间里,我国光伏专用扩散设备经历了从处理125mm×125mm、156mm×156mm方硅片向210mm×210mm方硅片跃进;扩散的质量从原来的单片和整管扩散均匀性在7%以内的水平,提高到目前单片和整管扩散均匀性在4%以内的国际先进水平;扩散方式从原来的开管扩散到现在的环保、洁净、节能、安全的全封闭扩散;单批次产能从原来的150片、200片、300片发展到日前的400片;控制方式从原来的手动、PLC半自动控制到日前的微机全自动控制。
目前我国光伏电池装备市场上共有各类扩散设备上千多管,其中85%左右以处理125mm×125mm电池片为主,兼容156mm×156mm电池片,这其中又有90%以上为微机自动控制设备,只有不到10%为手动或PLC半自动产品。
目前国内生产扩散炉的企业有中电四十八所、北京七星华创、深圳捷佳创、青岛赛瑞达等。
一条50MW的电池生产线,需配置2台扩散炉,每台价格在215万左右。
3.3.3等离子刻蚀机
干法腐蚀设备全部国产为主,少量湿法腐蚀设备需要进口。
干法刻蚀(ICP)是目前主流的刻蚀设备工艺,它采用射频辉光放电将参与反应的化学气体电离形成等离子体,通过对刻蚀参数精确的控制和测量,把光刻形成的电路图转移到硅片上形成三维结构。
其间融合了等离子体、射频、超高真空、自动化控制等多种尖端技术,是电池片制造过程中至关重要的一环。
综观国内刻蚀设备生产企业,具有以下特点:
采用片架旋转密封技术,提高刻蚀的均匀性;硅片放置自动压紧技术,减少了钻蚀风险;ICP技术的形成及引入,提高了设备的各种效率;特别是大容量反应室的设计,大大提高了电池片的处理能力。
目前国内生产刻蚀机的企业有中科院微电子研究所、中电四十八所、武汉三工、深圳捷佳创、北京七星华创等。
一条50MW的电池生产线,需配置4台刻蚀机,每台价格在15万左右。
3.3.4PECVD
该设备是晶体硅太阳能电池生产线制备减反射钝化膜的主要设备,也是整条太阳能电池生产线的核心设备之一。
国内第一台半导体用PECVD设备是由中科院沈阳科学仪器研制中心有限公司研发的,零部件国产化率达到了70%左右。
管式PECVD基本国产,平板式PECVD国内已研发出来,正准备上市。
与管式PECVD设备相比,平板式PECVD具备产能大、装卸片容易,易于自动化集成等优点,但到目前为止,国产设备市场上仍未真正出现相关的成熟产品。
目前国内生产PECVD设备的企业有北方微电子、中电四十八所、青岛赛瑞达、北京七星华创、上海航天机电等公司。
一条50MW的电池生产线,需配置1台PECVD设备,国产价格在600~800万左右。
3.3.5丝网印刷机
丝网印刷机分为手动和全自动。
手动已全部国产,全自动丝网印刷机只有少数公司实现生产。
目前在国内,手动及半自动丝网印刷机已实现量产,并成功应用于电池生产线,全自动丝网印刷机已有研发,由深圳市网印巨星推出的全自动丝网印刷机已实现生产,正在电池生产线中进行测试,各项数据已达到国际先进水平。
而拥有更高定位精度的新一代半自动丝网印刷机已经在主流厂商试用。
一条50MW的电池生产线需要配2条国产丝网印刷线(每条3台丝网印刷机),每条线成本大概在460万人民币;进口设备1台,价格900~1350万元。
3.3.6烧结炉
高温烧结炉国内生产研发技术明显提高,开始批量在大生产线使用,但进口仍占多数。
国内高温烧结炉生产企业仍以中电四十八所为代表,其他企业有合肥恒力电子(中电43所)、北京七星华创(以干燥炉为主)、北京中联科利等企业。
一条50MW的电池生产线可以配置一台双结炉价格150万,国外180万。
据估算,一条50MW电池生产线设备成本预计在4000~6000万左右。
4组件生产工艺及主要设备
4.1工艺流程
电池检测——正面焊接——背面串接——敷设——组件层压——修边——装边框打胶——焊接接线盒——高压测试——组件测试
4.2工艺简介
电池测试:
由于电池片制作条件的随机性,生产出来的电池性能不尽相同,所以为了有效的将性能一致或相近的电池组合在一起,所以应根据其性能参数进行分类;电池测试即通过测试电池的输出参数(电流和电压)的大小对其进行分类。
以提高电池的利用率,做出质量合格的电池组件。
正面焊接:
是将汇流带焊接到电池正面(负极)的主栅线上,汇流带为镀锡的铜带,我们使用的焊接机可以将焊带以多点的形式点焊在主栅线上。
焊接用的热源为一个红外灯(利用红外线的热效应)。
焊带的长度约为电池边长的2倍。
多出的焊带在背面焊接时与后面的电池片的背面电极相连。
背面串接:
背面焊接是将36片电池串接在一起形成一个组件串,我们目前采用的工艺是手动的,电池的定位主要靠一个膜具板,上面有36个放置电池片的凹槽,槽的大小和电池的大小相对应,槽的位置已经设计好,不同规格的组件使用不同的模板,操作者使用电烙铁和焊锡丝将“前面电池”的正面电极(负极)焊接到“后面电池”的背面电极(正极)上,这样依次将36片串接在一起并在组件串的正负极焊接出引线。
敷设:
背面串接好且经过检验合格后,将组件串、玻璃和切割好的EVA、玻璃纤维、背板按照一定的层次敷设好,准备层压。
玻璃事先涂一层试剂(primer)以增加玻璃和EVA的粘接强度。
敷设时保证电池串与玻璃等材料的相对位置,调整好电池间的距离,为层压打好基础。
(敷设层次:
由下向上:
玻璃、EVA、电池、EVA、玻璃纤维、背板)。
组件层压:
将敷设好的电池放入层压机内,通过抽真空将组件内的空气抽出,然后加热使EVA熔化将电池、玻璃和背板粘接在一起;最后冷却取出组件。
层压工艺是组件生产的关键一步,层压温度层压时间根据EVA的性质决定。
使用快速固化EVA时,层压循环时间约为25分钟,固化温度为150℃。
修边:
层压时EVA熔化后由于压力而向外延伸固化形成毛边,所以层压完毕应将其切除。
装边框打胶:
类似与给玻璃装一个镜框;给玻璃组件装铝框,增加组件的强度,进一步的密封电池组件,延长电池的使用寿命。
边框和玻璃组件的缝隙用硅酮树脂填充。
各边框间用角键连接。
焊接接线盒:
在组件背面引线处焊接一个盒子,以利于电池与其他设备或电池间的连接。
高压测试:
高压测试是指在组件边框和电极引线间施加一定的电压,测试组件的耐压性和绝缘强度,以保证组件在恶劣的自然条件(雷击等)下不被损坏。
组件测试:
测试的目的是对电池的输出功率进行标定,测试其输出特性,确定组件的质量等级。
4.3主要设备介绍
4.3.1层压机
太阳能层压机,常称作层压机,又叫做太阳能电池组件层压机,还可以叫做光伏组件层压机。
太阳能电池组件层压机是完成自原材料到太阳能电池板成品的关键设备。
它通常是把玻璃、EVA、衔接佳的双体电池、EVA、背板这几层物质压合在一起的机械装备。
常规的全自动层压机2300*3600产能是10MW。
层压机已基本实现国产,一般全自动层压机价格在60万元左右,半自动的20万元左右。
4.3.2太阳能电池分选仪
主要用于太阳能单晶硅或多晶硅单片电池的测试和结果记录。
一般100MW的组件生产线需用分选仪8台,每台价格在10万元左右。
电池划片机:
又称激光划片机,它不同于多线切割机。
前者是针对单个硅片进行修理,后者主要是对硅片批量切割。
一般100MW的组件生产线需用划片机2~4台,每台价格在7万左右。
4.3.3组件测试仪
也称“太阳能模拟器”,适用于高效能太阳能电池组件和其它特殊电池组件的电性能参数的自动测试和结果记录。
一般100MW的组件生产线需用测试仪4台,每台价格在9万左右。
一条100MW组件整线设备价格在500~800万左右。