优化注塑流动.docx
《优化注塑流动.docx》由会员分享,可在线阅读,更多相关《优化注塑流动.docx(14页珍藏版)》请在冰豆网上搜索。
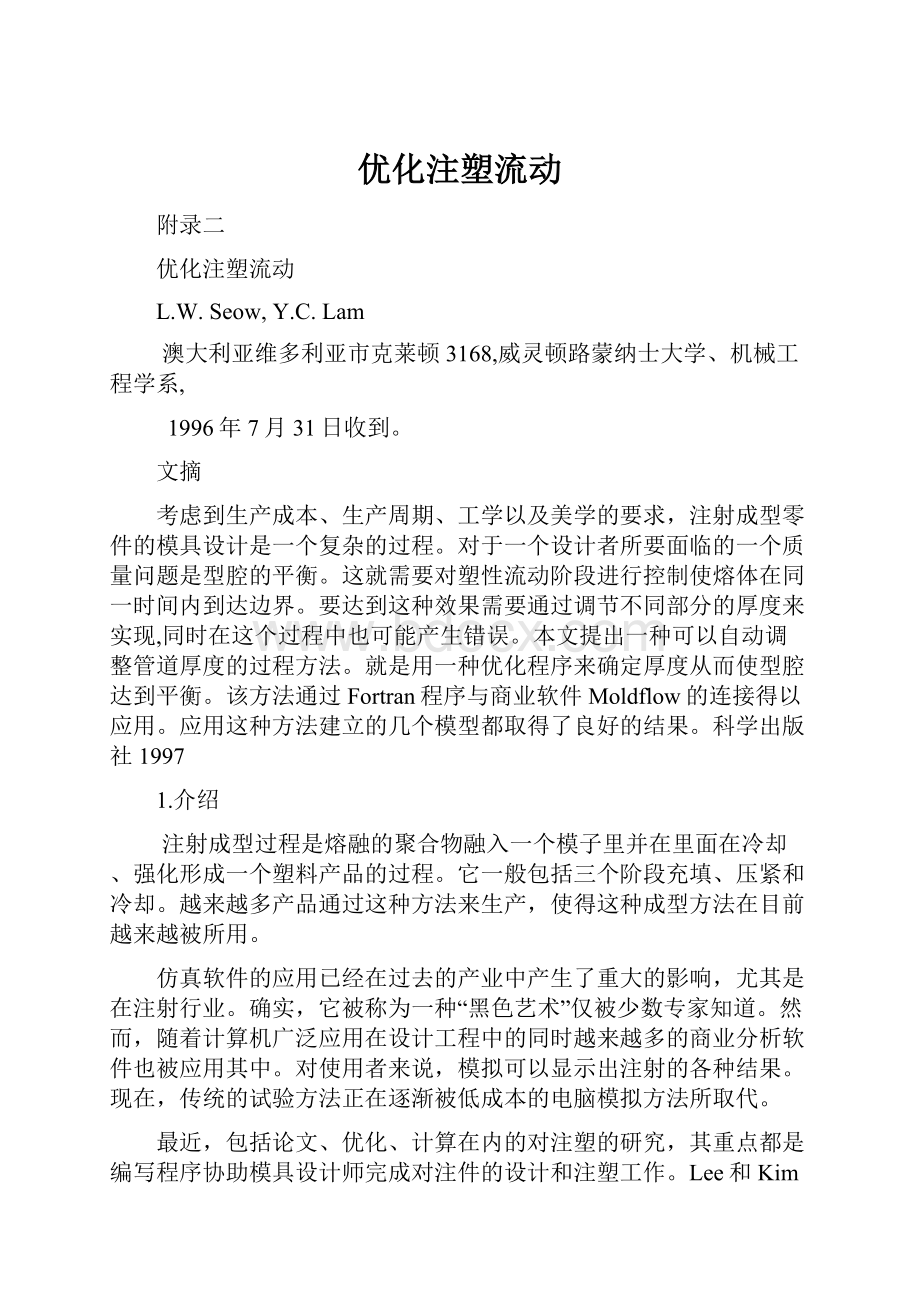
优化注塑流动
附录二
优化注塑流动
L.W.Seow,Y.C.Lam
澳大利亚维多利亚市克莱顿3168,威灵顿路蒙纳士大学、机械工程学系,
1996年7月31日收到。
文摘
考虑到生产成本、生产周期、工学以及美学的要求,注射成型零件的模具设计是一个复杂的过程。
对于一个设计者所要面临的一个质量问题是型腔的平衡。
这就需要对塑性流动阶段进行控制使熔体在同一时间内到达边界。
要达到这种效果需要通过调节不同部分的厚度来实现,同时在这个过程中也可能产生错误。
本文提出一种可以自动调整管道厚度的过程方法。
就是用一种优化程序来确定厚度从而使型腔达到平衡。
该方法通过Fortran程序与商业软件Moldflow的连接得以应用。
应用这种方法建立的几个模型都取得了良好的结果。
科学出版社1997
1.介绍
注射成型过程是熔融的聚合物融入一个模子里并在里面在冷却、强化形成一个塑料产品的过程。
它一般包括三个阶段充填、压紧和冷却。
越来越多产品通过这种方法来生产,使得这种成型方法在目前越来越被所用。
仿真软件的应用已经在过去的产业中产生了重大的影响,尤其是在注射行业。
确实,它被称为一种“黑色艺术”仅被少数专家知道。
然而,随着计算机广泛应用在设计工程中的同时越来越多的商业分析软件也被应用其中。
对使用者来说,模拟可以显示出注射的各种结果。
现在,传统的试验方法正在逐渐被低成本的电脑模拟方法所取代。
最近,包括论文、优化、计算在内的对注塑的研究,其重点都是编写程序协助模具设计师完成对注件的设计和注塑工作。
Lee和Kim通过优化翘曲变形来降低模具厚度进而进一步减小了表面变形获得了理想的加工条件。
Pandelidis对最佳浇注位置进行了研究。
另外,Zou通过对不同外部摩擦和加热温度对注件质量、功能所产生的的影响的研究确定了最佳浇注位置。
基于爬山法和模拟退火法相结合的混合运算方法被用在了寻找最佳浇点的过程中。
这个过程中的一些变量在以后的文献中被进行了优化。
此外,Lee和Kim研究、优化浇口位置翘曲变形的标准也被应用在研究焊接、冲击强度各方面。
经过彻底的调查之后,允许设计者可以不按常规的规定首先确定一些浇口的位置。
一种局部搜所法被当作确定节点质量的标准。
Jong和Wang描述了这个系统优化设计(这个系统在注射上的使用使模具技术得到了很大的提高)。
在本文中是通过平衡型腔的方法来减少注塑件的失真。
通过平衡流动来减少残余应力和二次注塑。
此外,为了缩短生产周期和节约材料,熔接痕和气泡的出现也应该被避免。
1.1型腔平衡
型腔平衡仍然是人机互动和输入的一个需要解决的重要区域。
实现型腔平衡设计的最基本目的是如何使熔融塑料同时到达边界或者在同一注塑成型阶段有着相同的压力值。
流量平衡是决定最后产品质量的关键,流量不平衡会导致充盈扭曲。
设想一个中心矩形型腔封闭且厚度均匀,如图1
图1、填充模式的一个矩形模具
在填补阶段将熔化塑胶注射入模具,在扩大循环流动波前首先填补顶部和底部的边缘。
随后这些边缘被继续填充并且材料充了满各个角落和边缘。
结果,过多的充填和边缘高压力差的产生导致了不愿看到的现象—产品扭曲。
2.现在的方法
为了取得流动的平衡和满足设计的标准,图1圆形流动图会变为图2的矩形流动图。
图2、矩形流动图
对角落和更短的边缘部分的充填必要加速。
由于导向机构的采用这些现在已经被实现了。
导向机构可以使融料往一定方向流在局部增加模具的厚度。
相反地,导向机构也可以为了制模局部薄一些使熔体流向其他指定方向。
一个可能的方法来解决如图1的情况使融料流向角落,如图3所示。
图3、导向流动优化图
型腔平衡的过程可能是一个复杂的过程。
对经验不丰富的设计师来说,这是一个反复实验的过程。
这很大程度上取决设计师如何识别在什么地方加导向装置。
一些物理特性如宽度、长度以及厚度的变化能力也是有要求的。
使用商用软件Moldflow对设计师在确定这些变化的影响时提供了宝贵的协助,而不需要昂贵的试验。
然而,专业知识在型腔平衡中仍然是必需的,因为现在的软件还不能确定修改必要的优化流程。
3.得出流量方程式
在充填阶段的塑性流动就像是在两个被分开很小距离的盘子之间的流动。
在最近这已经由Hele-Shaw用近似法创建出模型。
假设一个不可压缩的,广义的,非牛顿流体方程的充填,方程可以写成:
连续性方程:
(1)
动量方程:
(2)
(3)
(4)
能量方程:
(5)
分别在笛卡尔坐标和速度分量坐标系中得到。
T代表温度,P代表压力,
代表密度,
代表比热容,k代表材料导热性而
代表剪切度,剪切率计算公式为:
(6)
Kennedy由连续性和动量方程相结合得到屈服方程:
(7)
(8)
熔体溶导率常被称为流动性术语,h表示了一半的间隙厚度。
例如:
(5)—(8)是简化控制方程适用于充填阶段。
Hieber和Shen对这些方程的解决运用了有限元:
有限元差分法和控制体积法相结合自动控制流体的前进。
大多数商业软件采用这种方法。
从那时起,通过Chiang的建议填料阶段指令被加上了。
3.1厚度变化对流变率的影响
在注塑过程中熔体流动的两个假定条件可以确定。
首先,在坐标(u、v、w)=0的地方有一层冷却层在模具型腔周围。
其次,流场关于型腔中线也是假定对称的(如图4)。
通过证明,适用的边界条件如下:
(9)
图4横截面主视图
(10)
将
(2)和(3)与在z方向上的边界条件整理可得:
(11)
(12)
通过整理式子(11)和(12)并取平均速度可得:
(13)
(14)
如果质量流动速率在长度x和y方向定义为:
(15)
(16)
然后结合(13)和(14)可以得到:
(17)
(18)
很明显,流动性是描述流动特性的重要术语:
高温意味着可以低阻力流动,相似的,低温意味着流动阻力大。
重要的是要注意流动度不是一项物质特性虽然它涉及到取决于温度和剪切速率的粘度。
在这里一中特殊的方法被使用即运用有限元的方法解决了控制方程的问题。
即使整个模型表面和地区元素,厚度不受约束,但是每一个元素都有一个单独的厚度值。
流动性贯穿整个网格可控制元素薄膜厚度。
同样地,基本任务会持续进行直到每一个单元确定达到达到最理想的流量。
该程序将会生成一个满足标准的厚度分布。
4.程序优化
4.1流动路径的概念
流动路径就是颗粒进入浇道口直到注塑模被填满所经过的路径。
对于一个几何形状简单的镶嵌件,不平衡的注入可表示为一旦融料遇到边界流动方向就会发生改变。
这个流动路径图可能看起来如图5所示;
图5.流动路线图
为了平衡流程,流体必须在所有通道内同时到达边界处。
要实现这一过程,一个可能的解决方案是在填充和调整注塑率去适应不懂厚度的要求时必须对流动有一个指引。
同样的,在浇道中的注塑率是变化的,但是变化取决于融料流过的距离。
因此,任何从注射点到边界的路径将都是一条直线,就如图6所示;
图6.平衡注射时的流动路线
在现实中这可能不是一个实际的流动路线,但是这是一个非常逼真的演示。
这样熔体便可以假设沿着这些直线所示的路径平衡地流到边界。
通过沿着流动路径改变流道的厚度才可以使型腔的平衡和流动率的改变得以实现。
4.2参数更新
为了调整流道的厚度,假设流速和厚度之间有一个直线性关系。
这是基于一种平面线图下,展示了在充填时间过程中不同厚度从一个中心获得封闭的、圆盘状空腔。
(如图7)分析软件演示了在恒定注射压力下聚丙烯的情况。
图7
很明显,经过一定程度的线性观测不同型腔的充填时间和厚度成反比即随着厚度的增加,充填时间将会减少,反之亦然。
因此,在分析了聚丙烯的充填过程后更新方程可叙述如下:
(19)
表示更新后的厚度,
表示当前的厚度,
表示熔体填满浇点时的时间,
表示熔体到达边界时的时间。
最短路径的充填时间
作为参考时间,所有其他充填时间即可与之相比较。
相反地,最长流动路径的充填时间可以被使用或在适当情况下填充时间可以被一些参考时间来代替。
4.3流程的相关元素
厚度的变化会影响式子(19)的结果,型腔内的所有元素都要通过节点与流程相联系。
要实现这个必须设定好到节点的最近距离而且节点决定流道的厚度,然后基本的厚度变为节点厚度的平均值。
4.4最优准则
注射成型过程的特征之一是注塑最末端的压力大约为零。
在不平衡的流动中,压力不平衡大都在边缘处因为熔体先填充边缘就像被描述成图1那样。
然而,在平衡流动中就不是这样了。
当熔体同时到达边界,二次注塑不会发生。
此外,在边界节点处的压力就是在流动前沿处的压力。
因此,在平衡型腔中边界节点处的压力应该等于零。
正因为如此,上述情况可以作为一种优化准侧来终止程序。
很明显,事实上,不可能产生同时到达边界节点的注射流动并且会产生二次注塑。
在这种情况下,如果在边界节点处的压力少于型腔所受最大压力的1%还是可以接受的。
然后,我们就可以将边界节点处的压力设定为零。
收敛的条件就是100%的最优下面给出了最优性的百分比;
N代表边界节点为零的结点个数,
代表所有节点的个数。
4.5提出假设
为了找到开始时的注射点,必须进行一些假设。
这些假设是不被看成必要条件的并且他们的形式在需要的时候可以进行修改。
对于目前的研究可假设为:
(1)所有初始元素厚度均为1mm
(2)参考节点之间是最短的路径(3)在整个优化过程中使用相同的参考节点(4)相同传递路径处的边界节点的厚度都相同(5)注射点处的厚度是定值(6)每一个单元的厚度是各处厚度的平均值。
4.6研究方法
这种方法已经应用在计算机上并且扮演了充填分析软件Moldflow的外部循环部分。
5.结果
下面的一些模型的优化应用了以上的方法。
通过这个方法,平衡之前和平衡之后的充填模式都被显示出来。
填充模式就是时间常量递增过程中漩涡线出现的次数以及在注射过程中对熔体填充过程的描述。
5.1.模型1
第一个模型是一个被描述为黑色广场的内部带有一个注射点简单的椭圆型注射型腔。
图10(a)显示了一个厚度分布均匀的型腔填充模式;这是优化前的情景,而图10(b)是取得了最终优化后的模式。
图11显示了优化后的壁厚分布。
为了清楚地看出原因,只有更厚的厚度被用灰色水平尺度表示出来。
在该模型中,只有薄膜厚度超过最大厚度的64%才被表示出来。
越黑的部分表示该部分越厚。
图10
图11
5.2.模型2
第二种模式是一个底边封闭的矩形腔。
未被优化前的填充模式图如14(a)所示而优化后填充模式所显示的是图14(b)。
在图15中壁厚的分布也被显示出来。
在模拟实验中,流动引导是很明显的,从注射点延伸到两个拐角已达到型腔平衡。
对三种模型的结果表明了获得的最优解的方法的有效性。
一旦参考路径被设定为最短的,Eq.(19)导致了所有单元厚度的增加。
这本质上导致了流动指引的形成。
6.观察结果
当一个嵌件出现时,谁也不会确定该运算法则是否还会使流动达到平衡。
原因是这一内嵌件在最初并没有明确的当成一个问题假想过。
为了说明这个方法可以解决这个问题,图16就描绘了一个带有内嵌件的填充模型。
图中的模式是厚度均匀分布的填充模式。
注射点处用黑色方块表示。
如图16所示点A是最后需要注射的点。
在不带内嵌件的相同型腔内,由于点A距离注射点最远所以它也会是最后被填充的点。
然而,内嵌件的出现加剧了两个结果的出现,一个是熔融物流过的距离被增加了,另一个是流动的方向被完全改变了。
内嵌件有效地使流体分叉并避开它绕道而行。
在这种情况下,假设流体的路径是直线是不成立的。
图16.
图17显示结果的使用,提出了一种优化运行直线流路的假设。
在经过37重复试验后效果达到了最优性的87.8%。
进一步的重复试验并没有得到更好的改善并且这种方法也没事结果达到最好100%。
这个填充模式分析显示在经过52次反复填充后达到最优性的87.8%。
图17
解决的方法显然不令人满意,因此必须改善这个方法。
一个可能克服这个缺点的方法是先假定流体绕着内嵌件流动但随后展开的分支会再次成为直线。
如图18所示。
流道b被流动路径1和2共同使用。
流动路径a和c属于围绕内嵌件的直流道1.
图18
在这个例子中,由于两个或两个以上的流路部分流道共享所以这个假设就是将共同部分的流道的厚度定为流动路径厚度的平均值。
即在图18中,流动路径b的厚度将是路径1和2的平均值。
其他的标准也可能会被使用,但对于初步调查来讲这已经足够了。
图19是上面讨论的同一型腔的被经过改进的流动路径的分析结果。
图19
观察表2,改良后的方法更好,克服了内嵌件的复杂介绍以及在22次重复试验后就能达到100%最优。
最后的壁厚分布就像在前边一样用灰色度来表示一样显示如图20。
与先前的模型相比,可以看出流体被指引以及就像被期望的一样,流体被指引着流向了嵌入件的方向。
图20
尽管修改得到了改进,但是可以想象到模具的复杂性会增加,这种对模具限制可能更重要。
这种假设会被使用或不被使用目前正在研究和调查之中。
7.结论
平衡流体在各个型腔中的流动是一步重要的设计,因为它能提高最终开发产品的质量。
这种通过优化壁厚分布来取得平衡流动的的常规方法在本文中已被描述。
虽然方法很简单,但是其可以克服内嵌件影响的稳定性已被证明。
这种方法很容易实现并且很容使用在商业软件上。
对于进一步改善的方法目前正在研究中。
参考文献
[1]L.T.Manzione(Ed.),ApplicationsofComputerAidedEngineeringinInjectionMolding,Hanser,NewYork,1987.
[2]B.H.Lee,B.H.Kim,Optimizationofpartwallthicknesstoreducewarpageofinjection-moldedpartsbasedonthemodifiedcomplexmethod,Polym.-Plast.Technol.Eng.34(1995)793–811.
[3]I.Pandelidis,Q.Zou,Optimizationofinjectionmoldingdesign.PartI:
Gatelocationoptimization,Polym.Eng.Sci.30(1990)873–882.
[4]I.Pandelidis,Q.Zou,Optimizationofinjectionmoldingdesign.PartII:
Moldingconditionsoptimization,Polym.Eng.Sci.30(1990)883–892.
[5]B.H.Lee,B.H.Kim,Automatedselectionofgatelocationbasedondesiredqualityofinjectionmoldedpart,SPEAnnualTechnicalConference,ANTEC1995,pp.554–560
[6]W.R.Jong,K.K.Wang,Automaticandoptimaldesignofrunnersystemsininjectionmoldingbasedonflowsimulation,SPETech.Papers36(1990)385–389.
[7]P.Kennedy,FlowAnalysisofInjectionMolds,Hanser,Verlag,1995.
[8]C.A.Hieber,S.F.Shen,Flowanalysisofthenon-isothermaltwo-dimensionalfillingprocessininjectionmolding,IsraelJ.Technol.16(1978)248–254.
[9]C.A.Hieber,S.F.Shen,Afiniteelement:
finitedifferencesimulationoftheinjectionmoldingfillingprocess,J.Non-NewtonianFluidMech.7(1980)1–32.
[10]H.H.Chiang,C.A.Hieber,K.K.Wang,Aunifiedsimulationofthefillingndpostfillingstagesininjectionmolding.PartI:
Formulation,Polym.Eng.Sci.31(1991)116–124.
[11]H.H.Chiang,C.A.Hieber,K.K.Wang,Aunifiedsimulationofthefillingandpostfillingstagesininjectionmolding.Part2:
Experimentalverification,Polym.Eng.Sci.31(1991)125–139.
.