支架零件的数控加工工艺设计及程序设计.docx
《支架零件的数控加工工艺设计及程序设计.docx》由会员分享,可在线阅读,更多相关《支架零件的数控加工工艺设计及程序设计.docx(9页珍藏版)》请在冰豆网上搜索。
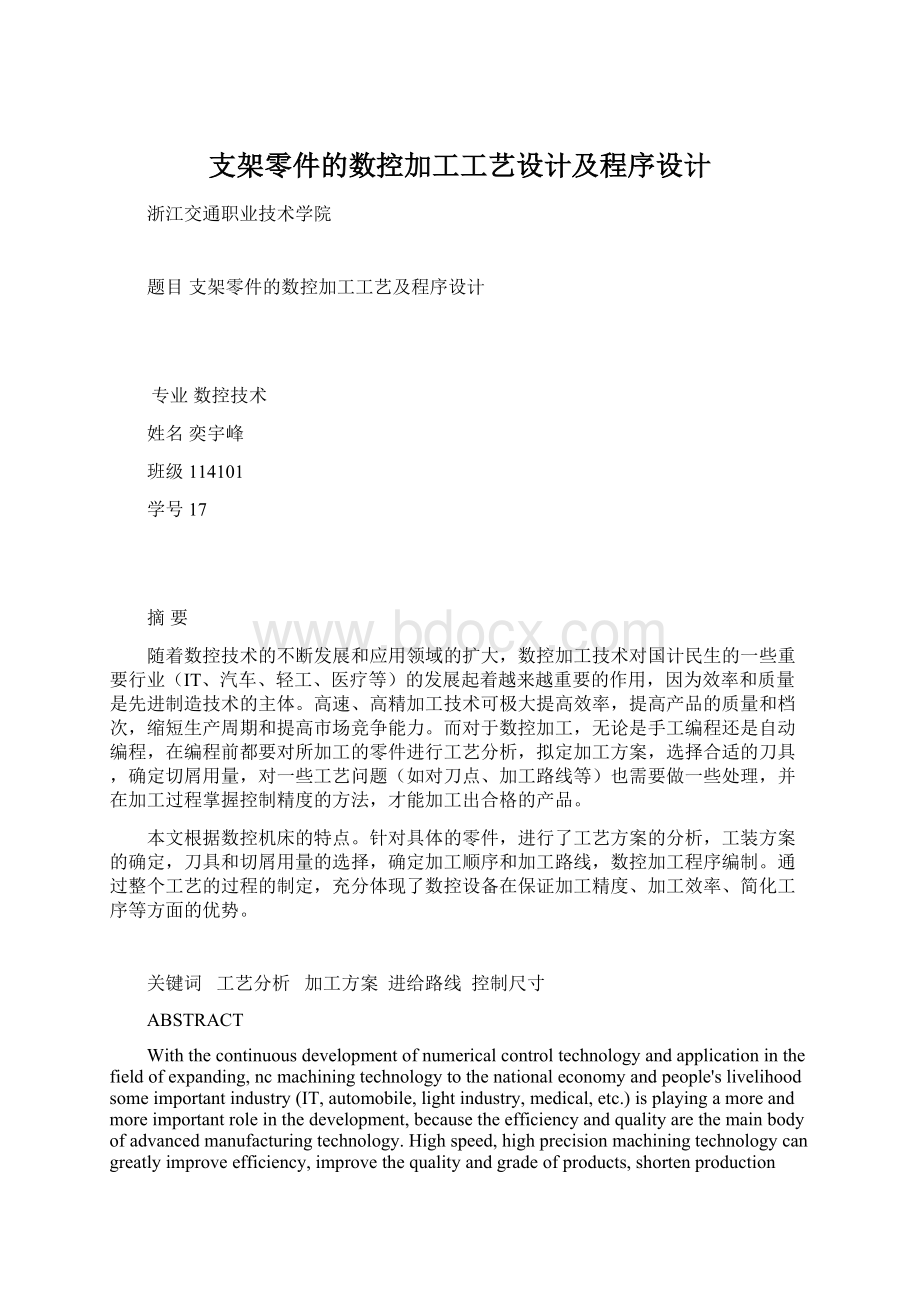
支架零件的数控加工工艺设计及程序设计
浙江交通职业技术学院
题目支架零件的数控加工工艺及程序设计
专业数控技术
姓名奕宇峰
班级114101
学号17
摘 要
随着数控技术的不断发展和应用领域的扩大,数控加工技术对国计民生的一些重要行业(IT、汽车、轻工、医疗等)的发展起着越来越重要的作用,因为效率和质量是先进制造技术的主体。
高速、高精加工技术可极大提高效率,提高产品的质量和档次,缩短生产周期和提高市场竞争能力。
而对于数控加工,无论是手工编程还是自动编程,在编程前都要对所加工的零件进行工艺分析,拟定加工方案,选择合适的刀具,确定切屑用量,对一些工艺问题(如对刀点、加工路线等)也需要做一些处理,并在加工过程掌握控制精度的方法,才能加工出合格的产品。
本文根据数控机床的特点。
针对具体的零件,进行了工艺方案的分析,工装方案的确定,刀具和切屑用量的选择,确定加工顺序和加工路线,数控加工程序编制。
通过整个工艺的过程的制定,充分体现了数控设备在保证加工精度、加工效率、简化工序等方面的优势。
关键词 工艺分析 加工方案 进给路线 控制尺寸
ABSTRACT
Withthecontinuousdevelopmentofnumericalcontroltechnologyandapplicationinthefieldofexpanding,ncmachiningtechnologytothenationaleconomyandpeople'slivelihoodsomeimportantindustry(IT,automobile,lightindustry,medical,etc.)isplayingamoreandmoreimportantroleinthedevelopment,becausetheefficiencyandqualityarethemainbodyofadvancedmanufacturingtechnology.Highspeed,highprecisionmachiningtechnologycangreatlyimproveefficiency,improvethequalityandgradeofproducts,shortenproductioncycleandimprovethemarketcompetitionability.Forthenumericalcontrolprocessing,whethermanualprogrammingorautomaticprogramming,beforewillbemadeofpartsmanufacturedbytechnologyanalysis,draftingprocessingscheme,choosingtherighttool,determinethecuttingdosage,forsomeprocessproblems(suchasthecuttingpoint,processingroute,etc.)alsoneedtodosomeprocessing,andmasterthemethodsofcontrolaccuracyinmachiningprocess,toworkoutqualifiedproducts.
Inthispaper,basedonthecharacteristicsofncmachinetools.Forspecificpartsoftheprocessofanalysis,theschemedeterminationoftooling,dosageoftoolandchipselection,determinetheprocessingorderandprocessingroute,thencmachiningprogramming.Throughthewholeprocessofdevelopingprocess,fullyembodiesthencequipmentintheguaranteemachiningaccuracy,efficiency,simplifytheprocedureofadvantage.
KEY WORDStechnologyanalysis,processingscheme,
feedline,controlthesize
一、零件工艺分析————————————————6
二、零件加工工艺设计——————————————7
1定位基准的选择—————————————————7
2零件表面加工方法的选择——————————————7
3制定工艺路线——————————————————8
三、程序设计——————————————————9
1选择加工设备与工艺装备——————————————9
2.确定工序尺寸(工序Ⅸ)——————————————9
四、确定切削用量及基本时间——————————10
1切削用量的计算—————————————————10
2基本时间tm的计算———————————————10
3辅助时间的计算————————————————11
4其他时间的计算—————————————————11
五、夹具————————————————————12
1定位方案与夹紧机构———————————————12
2导向装置与夹具与机床连接元件———————————12
3夹具体————————————————————12
六、参考文献——————————————————15
七、致谢————————————————————16
一、零件工艺分析
通过对该零件图的重新绘制,知原图样的视图正确、完整,尺寸、公差及技术要求齐全。
该零件需要加工的表面均需切削加工,各表面的加工精度和表面粗糙度都不难获得。
以下是支架需要加工的表面以及加工表面之间的位置要求:
1.通孔φ20H7,粗糙度为1.6,此孔为加工其他孔的基准。
2.孔φ7/φ14,粗糙度为12.5。
3.孔φ6,粗糙度为3.2。
4.M面,粗糙度为6.3
5.S面,粗糙度为6.3。
6.T面,粗糙度为6.3。
5.R面,粗糙度为6.3。
6.N面,粗糙度为6.3
根据各加工方法的经济精度及一般机床所能达到的位置精度,该零件没有很难加工的表面,上述各表面的技术要求采用常规加工工艺均可以保证。
二、零件加工工艺设计
1.定位基准的选择
粗基准的选择:
按有关基准的选择原则,即当零件有不加工表面时,应以这些不加工表面作粗基准;若零件有若干不加工表面时,则应以与加工表面要求相对位置精度高的不加工表面作粗基准。
现以零件的侧面为主要的定位粗基准。
精基准的选择:
考虑要保证零件的加工精度和装夹准确方便,依据“基准重合”原则和“基准统一”原则,选择以圆柱体的Φ20H7孔为精基准。
2.零件表面加工方法的选择
(1)R端面公差等级为IT10,表面粗糙度为Ra6.3,需进行粗铣。
(2)Φ30外圆面为未注公差尺寸,根据GB1800-79规定起公差等级按IT14,需进行粗铣。
(3)N端面为未注公差尺寸,根据GB1800-79规定起公差等级按IT14,需进行粗铣。
。
(4)T端面公差等级按IT10,表面粗糙度为Ra6.3,粗铣即可。
(5)M端面公差等级按IT10,表面粗糙度为Ra6.3,粗铣即可。
(6)S端面公差等级为IT10,表面粗糙度为Ra6.3,粗铣即可。
(7)Φ20H7通孔,公差等级为IT7,表面粗糙度为Ra1.6,需钻、精扩、精铰。
(7)Φ6H7孔,公差等级为IT7,表面粗糙度为Ra3.2,需钻、精扩、精铰。
(8)3-Φ7通孔公差等级为IT10,表面粗糙度为Ra12.5,需钻即可。
(9)3-Φ14沉头孔公差等级为IT10,表面粗糙度为Ra12.5,需钻即可。
3.制定工艺路线
工序Ⅰ:
粗铣M面。
工序Ⅱ:
粗铣N面。
工序Ⅲ:
粗铣R面。
工序Ⅳ:
钻-精扩-铰孔至Ø20H7,°。
工序Ⅴ:
粗铣T面。
工序Ⅵ:
粗铣S面。
工序Ⅶ:
粗铣-半精铣Ø6相贯孔。
工序Ⅷ:
钻孔3-Ø7、3-Ø14。
工序Ⅸ:
清洗。
工序Ⅹ:
终检。
三、程序设计
1.选择加工设备与工艺装备
工序号
设备
工艺装备
工序Ⅰ
立式铣床X51
高速钢套式面铣刀,游标卡尺,专用夹具
工序Ⅱ
立式铣床X51
高速钢套式面铣刀,游标卡尺,专用夹具
工序Ⅲ
立式铣床X51
高速钢套式面铣刀,游标卡尺,专用夹具
工序Ⅳ
Z550
莫氏直柄麻花钻,扩孔钻,铰刀,卡尺,塞规
工序Ⅴ
立式铣床X51
直柄键槽铣刀,游标卡尺
工序Ⅵ
立式铣床X51
高速钢套式面铣刀,游标卡尺,专用夹具
工序Ⅶ
立式铣床X51
圆柱形铣刀,卡尺
工序Ⅷ
Z550
莫氏直柄麻花钻,游标卡尺
工序Ⅸ
清洗机
工序Ⅹ
塞规,百分表,卡尺等
2.确定工序尺寸(工序Ⅸ)
钻Φ=18.6mm。
查表可依次确定各工步尺寸的加工精度等级为,精铰:
IT9;钻:
IT12;根据上述结果,再由表可查得,Φ20mm的孔精铰余量Z精铰=0.2mm;钻孔余量Z查标准公差数值表可确定各工步的公差值分别为,精铰:
0.030mm;钻:
0.120mm。
综上所述,该工序各工步的工序尺寸及公差分别为,精铰:
Φ20+0.0300mm;钻孔:
Φ18+0.1200mm.
四、确定切削用量及基本时间
1切削用量的计算
(1)钻孔工步
①被吃刀量的确定取ap=5.8mm。
②进给量的确定由表,选取该工步的每转进给量f=0.4mm/r。
③切削速度的计算由表,按工件材料为HT200的条件选取,切削速度v可取为25m/min。
由公式n=1000v/Πd可求得该工序钻头转速n=265r/min,参照表所列Z550型立式钻床的主轴转速,取转速n=351/min.再将此转速代入公式,可求出该工序的实际钻削速度v=nΠd/1000=33.06m/min.
(2)精铰工步
①背吃刀量的确定取ap=0.10mm。
②进给量的确定由表,选取该工步的每转进给量f=0.40mm/r。
③切削速度的计算由表,切削速度v可取为4m/min。
由公式n=1000v/Πd可求得该工序铰刀转速n=42.4r/min,参照表所列Z550型立式钻床的主轴转速,取转速n=47r/min.再将此转速代入公式,可求出该工序的实际切削速度v=nΠd/1000=4.42m/min.
2基本时间tm的计算
(1)钻孔工步根据表,钻孔的基本时间可由公式tj=L/fn=(l+l1+l2)/fn求得。
式中l=53mm;l2=1mm;l1=(D/2)×cotkr+(1~2)=(15mm/2)×cot54°+1mm=11.89mm;f=0.4mm/r;n=351r/min.将上述结果代入公式,则该工序的基本时间tj=(53mm+1mm+11.89mm)/(0.4mm/r×351r/min)=0.46min=28.1s。
(2)精铰工步根据表,可由公式tj=L/fn=(l+l1+l2)/