裂解气的净化和分离第一章 烃类热裂解剖析.docx
《裂解气的净化和分离第一章 烃类热裂解剖析.docx》由会员分享,可在线阅读,更多相关《裂解气的净化和分离第一章 烃类热裂解剖析.docx(19页珍藏版)》请在冰豆网上搜索。
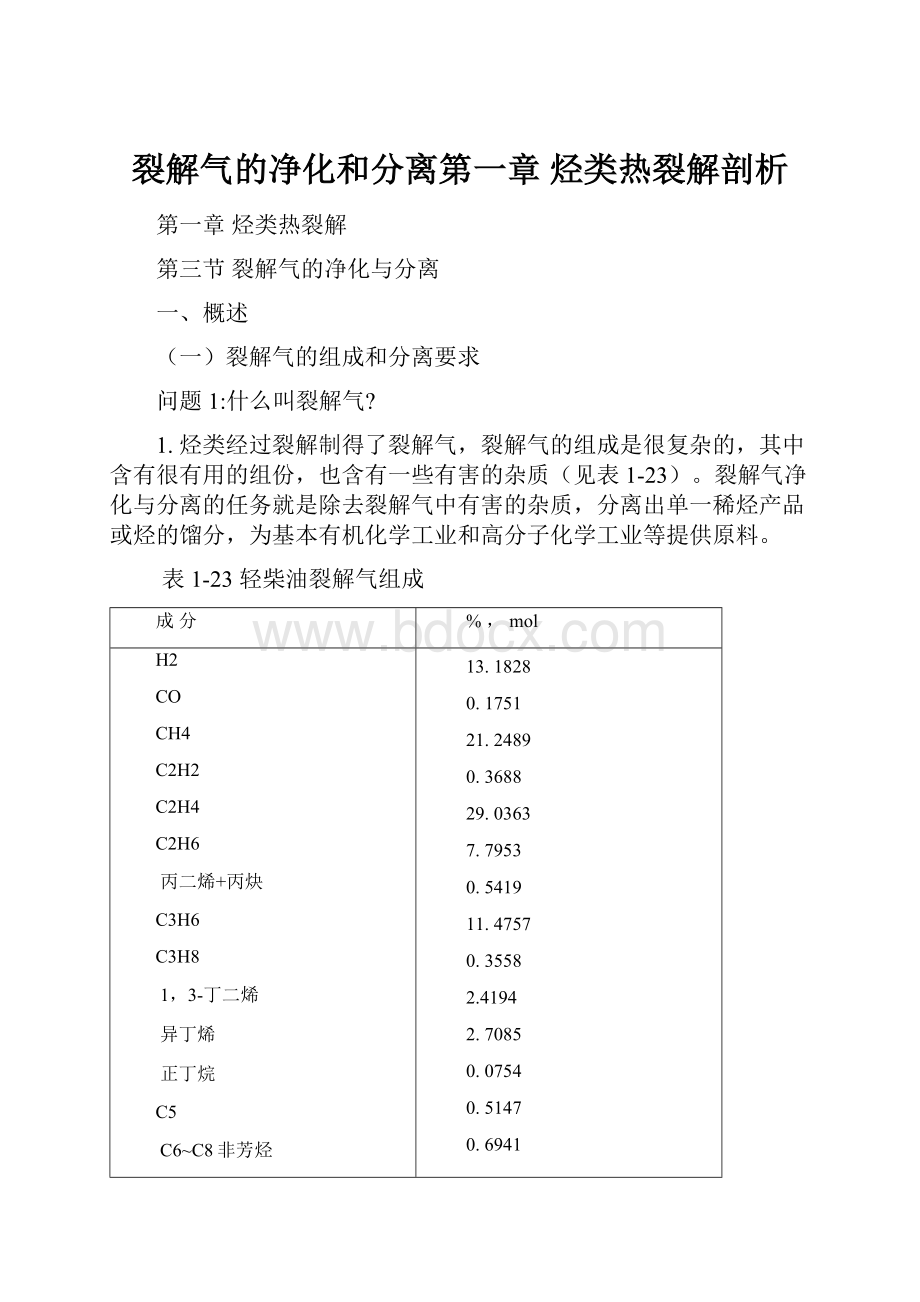
裂解气的净化和分离第一章烃类热裂解剖析
第一章烃类热裂解
第三节裂解气的净化与分离
一、概述
(一)裂解气的组成和分离要求
问题1:
什么叫裂解气?
1.烃类经过裂解制得了裂解气,裂解气的组成是很复杂的,其中含有很有用的组份,也含有一些有害的杂质(见表1-23)。
裂解气净化与分离的任务就是除去裂解气中有害的杂质,分离出单一稀烃产品或烃的馏分,为基本有机化学工业和高分子化学工业等提供原料。
表1-23轻柴油裂解气组成
成分
%,mol
H2
CO
CH4
C2H2
C2H4
C2H6
丙二烯+丙炔
C3H6
C3H8
1,3-丁二烯
异丁烯
正丁烷
C5
C6~C8非芳烃
苯
甲苯
二甲苯+乙苯
苯乙烯
C9~200度馏分
CO2
硫化物
H2O
13.1828
0.1751
21.2489
0.3688
29.0363
7.7953
0.5419
11.4757
0.3558
2.4194
2.7085
0.0754
0.5147
0.6941
2.1398
0.9296
0.3578
0.2192
0.2397
0.0578
0.272
5.04
2.需要净化与分离的裂解气,是由裂解装置送过来的。
3.裂解气的定义:
它已经脱除了大部份C5以上的液态烃类,它是一个含有氢气,C1-C5的烃类和少量杂质气体的复杂气态混合物。
4.裂解气的分离要求:
见表1-24,1-25.
表1-24乙烯聚合级规格
组分
单位
A
B
C
乙烯甲烷乙烷丙烯乙炔
S
H2O
O2
CO
CO2
%(mol)
ppm(mol)
ppm(mol)
ppm(mol)
ppm(mol)
ppm(w)
ppm(w)
ppm(w)
ppm(mol)
ppm(mol)
>=99.9
1000
<250
<10
<10
<10
<5
<10
<10
>=99.9
500
500
—
<10
<4
<10
—
—
<100
99.9
<1000
—
<50
2
<1
<1
<1
<5
<5
表1-25丙烯聚合极规格
组分
单位
A
B
C
丙烯
乙烯
丁二烯
丙二烯
丙炔
乙烷
丙烷
S
CO
CO2
O2
H2
H2O
%(mol)
ppm
ppm
ppm
ppm
ppm
ppm
ppm
ppm
ppm
ppm
ppm
ppm
>=99.9
<50
<20
<5
—
—
<5000
<1
<5
<5
<1
—
—
>=99.9
<5000
<10
<20
<10
<100
<5000
<10
<10
<1000
<5
<10
<10
98
—
—
<10
—
—
<5
<10
<20
—
—
<10
(二)裂解气分离方法简介
问题2:
深冷分离法的分离原理是什么?
1.工业生产上采用的裂解气分离方法,主要有深冷分离法和油吸收精馏分离法两种。
本章重点介绍深冷分离方法。
2.在基本有机化学工业中,冷冻温度小于等于-100度的称为深度冷冻,简称“深冷”。
♀3.分离原理就是利用裂解气中各种烃的相对挥发度不同,在低温下除了氢气和甲烷以外,把其余的烃类都冷凝下来,然后在精馏塔内精馏塔进行多组份精馏分离,利用不同的精馏塔,把各种烃逐个分离下来。
其实质是冷凝精馏过程。
4.图1-24可知,深冷分离流程可以概括成三大部份:
(1)气体净化系统;
(2)压缩和冷冻系统;
(3)精馏分离系统.
二、酸性气体的脱除
问题3:
酸性气体有哪些?
它们有什么危害?
除去方法是什么?
1.由表1-23的数据可以看出,裂解气中含有的少量硫化物、二氧化碳、一氧化碳、乙炔、丁炔以及水等杂质。
2.裂解气中的酸性气体,主要是二氧化碳(CO2)和硫化氢(H2S),另外还有有机硫化物。
3.这些酸性气体含量过多时,对分离过程会带来如下的危害:
(1)硫化氢能腐蚀设备管道,并能使干燥用的分子筛寿命缩短,还能使加氢脱炔用的催化剂中毒;
(2)二氧化碳能在深冷的操作中结成干冰,堵塞设备和管道,影响正常生产。
(3)酸性气体中的杂质对于乙烯和丙烯的进一步利用,也会产生很大的影响。
总上所述,必须将这些酸性气体脱除。
4.工业上常用化学吸收的方法,来洗涤裂解气,可同时除去硫化氢和二氧化碳等酸性气体。
对于吸收剂的要求是:
(1)对硫化氢和二氧化碳的溶解度大,反应性能强,而对于裂解气中的乙烯,丙烯的溶解度要小,不起反应;
(2)在操作条件下蒸气压低,稳定性强,这样吸收剂损失小,也避免产品被污染;
(3)粘度小,可节省循环输送的动力费用;
(4)腐蚀性小,设备可用一般钢材、;
(5)来源丰富,价格便宜。
工业上已经采用的吸收剂有氢氧化钠(NaOH)溶液,乙醇胺溶液,N-甲基吡咯烷酮等,具体选用哪一种吸收剂要同根据裂解气中酸性气体的含量多少,以及净化要求的程度、酸性气体是否回收等条件来确定。
管式炉裂解气中一般硫化氢和二氧化碳含量较低,多采用氢氧化钠溶液洗涤方法,简称碱洗法。
下面介绍碱洗脱除酸性气体的方法。
♀
(一)碱洗法原理
碱洗法的原理是将裂解气中的硫化氢和二氧化碳等酸性气体,还有硫醇、氧硫化碳等有机硫化物与氢氧化钠溶液发生下列反应而除去,以达到净化的目的。
COS+4NaOH--->Na2S+Na2CO3+2H2O
RSH+NaOH--->RSNa+H2O
通常采用:
CO2+2NaOH--->Na2CO3+H2O
H2S+2NaOH--->Na2S+2H2O
反应生成的Na2CO3、Na2S、RSNa等溶于碱液中。
※
(二)碱洗法流程
碱洗法脱除酸性气体的工艺原则流程图见图1-25。
裂解气无首先进入碱洗塔底部,碱洗塔分成四段,最上段为水洗,用以除去裂解气中夹带的碱液;其余三段为碱洗段,上段碱洗用10~15%的碱液,第二段碱洗用5~7%的碱液,最下段碱洗碱液浓度为1~3%。
碱液用水泵打循环。
新鲜碱液用补充泵连续送入碱洗的上段循环系统。
塔底排出的废碱液中含有硫化物,不能直接用生物化学方法处理,由水洗段排除的废水稀释后,送往废碱处理装置。
裂解气在碱洗塔内与碱液逆流接触,酸性气体被碱液吸收,脱除了酸性气体的裂解气由塔顶流出,去下一个净化分离设备。
(三)碱洗塔操作条件
下面举出一种碱洗塔的操作条件:
塔内压力……………………………1.0MPa
塔内温度………………………40c(摄氏度)
补充碱液浓度……………………30%NaOH
注:
本章内所有压力都是绝对压力
碱洗塔操作压力一般为1.0~2.0MPa,上述压力条件1.0MPa是碱洗塔位于压缩机三段出口处的,如果碱洗塔位于压缩机的四段出口处,则碱洗塔的操作压力约为2.0MPa。
显然从脱除酸性气体的要求来看,压力大有利于操作,吸收吸收塔的尺寸小,循环碱液量小。
碱洗塔在整个净化分离流程中的位置是可以变动的,要根据具体的条件来确定。
碱液温度一般为30~40摄氏度,温度低不利于脱除有机硫,而且C4以上的烃类也会冷凝下来,进入到碱液中去。
但是,为节省碱液的用量,塔底碱液的浓度可以控制得比较低,以利于碱液与硫化氢和二氧化碳发生如下反应:
H2S+NaOH--->NaHS
CO2+NaOH--->NaHCO3
显然上述反应比生成Na2CO3和Na2S反应能节省碱。
三、脱水
问题4:
裂解气为什么要脱水?
用什么方法?
问题5:
何谓分子筛?
(一)水的危害
1.裂解气经过急冷、脱硫和压缩等操作过程,多少还含有一些水分,大约还有400~700ppm。
2.裂解气者分离是在-100c以下进行的,在低温下,水能冻结成冰,并且能和轻质烃类形成固体结晶轻烃水合物,例如能形成:
CH4.6H2O、C2H6.7H2O、C4H10.7H2O
等等。
这些水合物在高压低温下非常稳定。
通过计算可知:
当压力为3.6MPa时,温度低于14度,就能生成水合物。
符合其稳定的条件。
3.危害:
冰和水合物凝结在管壁上,轻则增大动力消耗,重则堵塞管道,影响正常生产。
4.为了排除这个故障,可以用的积极的方法是,进行脱水干燥,使裂解气达到一定的露点要求。
5.工业上采用吸附的方法脱水,用分子筛、活性氧化铝或者硅胶作吸附剂。
(二)分子筛脱水
1.关于几种干燥剂的脱水效果和性能见图1-28所示。
由图中曲线可以看出,脱除气体中微量水分以分子筛吸附水容量最高,分子筛脱水效果比硅胶和活性氧化铝高好几倍,这是由于它的比表面积大于一般吸附剂。
但是在相对湿度较高时,活性氧化铝和硅胶的吸附水容量都大于分子筛。
因此有的脱水流程是采用活性氧化铝与分子筛串联,含水气体先进入活性氧化铝干燥器中脱除水分,然后再进入分子筛干燥器中脱除残余的水分。
分子筛脱水效率高,使用寿命长,工业上已经广泛使用。
也有使用性能良好的活性氧化铝脱除乙烯、丙烯馏分中的水分。
◆2.分子筛的定义:
人工合成的沸石,其主要成分是水合的硅铝酸盐晶体。
Mex/n[(AlO2)x(SiO2)y].mH2O
Me---->K,Na,Ca;
x/n---->可交换的离子数
3.分子筛具有许多相同大小的小洞和内表面很大的孔穴,能将比孔径小的分子吸附到内部,而不吸附比其孔大的分子,所以选择性高。
♀4.吸附机理:
(1)容积作用:
只能吸附小于它的孔径的分子,而且有比较强的吸附选择性。
例如4A分子筛能吸附水和乙烷分子,而3A分子筛只能吸附水而不吸附乙烷分子,所以裂解气、乙烯馏分以及丙烯馏分脱水用3A分子筛比用4A分子筛要好一些。
(2)极性分子:
分子筛是一种离子型极性吸附剂,它对于极性分子特别是水分子有极大的亲合力,容易吸附极性分子。
氢气、甲烷是非极性分子,所以这些分子虽然能通过分子筛的孔口进入分子筛的空穴,但是也不容易吸附。
5.分子筛的种类:
A型分子筛,X型分子筛,Y型分子筛。
6.分子筛吸附水是一个放热过程,所以降低温度有利于放热的吸附过程,高温则有利于吸热的脱附过程。
因此,在分子筛吸附了水分以后,用加热的方法可以使水分脱附出来,达到再生的目的,以便重新用来脱水。
※(三)分子筛脱水与再生流程
裂解气分离过程中,需要进行脱水的介质有:
裂解气、C2馏分、C3馏分以及甲烷化后的氢气等。
以裂解气等干燥为例,说明干燥及再生的操作过程,裂解气干燥与再生的工艺流程图见图1-30(P66)。
裂解气干燥用3A分子筛作吸附剂,分子筛填充在干燥器中,有两台干燥器,一台进行裂解气的脱水操作,另一台进行再生或者备用。
裂解气经过压缩以后,在进入冷冻系统之前,首先进入干燥器,自上而下通过分子筛的床层,这样可以避免分子筛被带出,机械磨损也小一些。
床层不至于被上升的气流而扰乱。
另一台干燥器进行再生和冷却,再生的时侯自下而上通入加热的甲烷、氢气馏分,开始应该缓慢地加热,用以除去大部分水分和烃类,这样,不至于造成烃类的聚合,将温度逐步升到230摄氏度左右,可以除去残余的水分。
气流向上流动,可以保证分子筛床层底部完全再生。
再生后需要冷却,冷却以后才能进行脱水操作。
因此,将再生以后的分子筛干燥器,用温度比较低的甲烷、氢气馏分自上而下地吹扫分子筛床层。
气流自上而下是因为冷的再生气中有水分冷凝下来,首先留在分子筛床层的上半部,这样做的好处是:
当进行裂解气的脱水操作时,再生气中冷凝下来的水分(都留在分子筛床层的上半部),不至于影响出口处裂解气脱水的质量要求,以保证出口的裂解气含水不超过规定的要求。
干燥器通过冷却后,当温度降低到吸附脱水时的温度时,可重新用来干燥裂解气体。
分子筛再生操作很重要,它关系到分子筛的活性和使用寿命。
分子筛吸附水容量及其活性的降低,主要是由于重质不饱和烃,尤其是双烯烃分子在分子筛表面积聚造成的。
所以在分子筛干燥之前,必须将裂解气中的重质烃类脱除掉。
另一方面,在分子筛再生的时候,必须必须将重质彻底脱除干净。
为了排除吸附的重质烃类,可进行增湿,也就是用水蒸气排出吸附的烃类。
四、脱炔
问题6:
炔的含量,危害,脱除方法各是什么?
1.含量:
裂解气中含有少量的炔烃,如例如乙炔、丙炔以及丙二烯等。
乙炔主要集中于C2馏分中,含量一般为2000~7000ppm;丙炔以及丙二烯主要集中在C3馏分中,丙炔含量一般为1000~1500ppm,丙二烯含量一般为600~1000ppm。
它们是在裂解过程中生成的。
2.乙炔的危害:
(1)乙炔会造成聚合催化剂的中毒。
(2)在聚乙烯生产中,乙炔会降低乙烯的分压,影响聚合的进行,也影响聚合的最终产品质量。
(3)在高压聚乙烯生产中,当乙炔积累过多后,由于乙炔分压过高且活泼,会引起爆炸。
其它以乙烯为原料的合成过程对乙炔的含量也有严格的要求。
3.工业上脱炔的主要是采用催化加氢法,少量用丙酮吸收法。
(一)催化加氢脱乙炔
1.反应:
乙炔含量比较少时,生产规模比较大时,用催化加氢脱炔方法,在操作和技术经济上都比较有利。
催化加氢可以使乙炔变为乙烯,但乙烯也有可能催化加氢变为乙烷,生产中希望只发生乙炔加氢为乙烯的反应,这样既(既)脱除了乙炔,又能增加乙烯的速率,变有害为有利。
CH2+H2——>C2H4
从化学平衡来分析,乙炔加氢反应在热力学上是非常有利的,几乎可以接近全部转化,虽然在反应系统中有大量乙烯存在,但加氢以后,乙炔的含量可以达到ppm级的要求。
2.选择性:
要使乙炔进行选择性加氢,必须采用选择性良好的催化剂,常用的催化剂是载于a-Al2O3载体上的钯催化剂,也可以用Ni-Co/a-Al2O3催化剂,在这些催化剂上,乙炔的吸附能力比乙烯强,能进行选择性加氢。
3.CO的作用:
原料气中有少量一氧化碳存在,由于一氧化碳吸附能力比乙烯强,可以抑制乙烯在催化剂上吸附而提高加氢反应的选择性。
但是一氧化碳含量过高,会使催化剂中毒。
所以在加氢的氢气中或原料气中,如果一氧化碳含量过高就应该除去,脱除的方法是在Ni/Al2O3等催化剂的存在下,使一氧化碳加氢。
260~300度;3.0MPa
CO+3H2——>CH4+H2O
由于上述加氢反应产物是甲烷,所以这种方法又称为甲烷化法。
4.副反应:
加氢脱除乙炔时可能发生的副反应有:
(1)乙烯的进一步加氢反应;
(2)乙炔的聚合生成液体产物,既绿油;
(3)乙炔分解生成碳和氢。
当反应温度比较高时,有利于上述副反应的发生。
5.反应条件:
H2/C2H2摩尔比大,有利于乙烯加氢,摩尔比小时,则有利于乙炔的聚合,可以生成比较多的绿油。
问题7:
何谓前加氢流程和后加氢流程?
※
(二)前加氢和后加氢的工艺流程
由于加氢脱乙炔过程在裂解气分离流程中所处的部位不同,有前加氢脱除乙炔和后加氢脱除乙炔两种方法。
加氢过程设在脱甲烷塔以前进行加氢脱炔的叫作前加氢。
前加氢的加氢气体是裂解气全留分,例如氢气、甲烷、C2、C3馏分或者氢气、甲烷、C2馏分。
由此可见加氢馏分中就含有氢气,不需要外来氢气,所以前加氢又叫做自给加氢。
设在脱甲烷塔以后进行加氢脱炔的叫做后加氢。
裂解气经过脱除甲烷、氢气后,将C2、C3馏分,用精馏塔分开,然后分别对C2和C3馏分进行加氢脱炔。
被加氢的气体中已经不含有氢气组份,需要外部加入氢气。
从能量利用和流程的复杂程度来看,前加氢流程是非常有利的。
不用提供额外的氢气,氢气可以自给,但是氢气是过量的,氢气的分压比较高,会降低加氢的选择性,增大乙烯的损失。
为了克服上述不利因素,要求前加氢催化剂的活性和选择性应该比较高;后加氢的氢气是按需要加入的,馏分的组份简单,杂质少,选择性高。
催化剂使用寿命长。
产品的纯度也比较高。
但是能量利用不如前加氢流程,流程也比前加氢流程复杂一些。
综合前加氢流程和后加氢流程,从产品角度来分析,一般都选择后加氢流程。
(三)加氢脱炔催化剂
前加氢和后加氢方法所用的催化剂及加氢脱炔的效果,见表1-26(P68)和表1-27。
钯和非钯催化剂的比较,见表1-28(P69)。
表1-27后加氢催化剂
催化剂
Pd-Fe
Pd-Ag
Pd
工
艺
条
件
温度,摄氏度
压力,MPa
空速,h^(-1)
H2/C2H2(mol)
80~145
2.5~2.7
2000~3500
2.0~4.0
30~210
2.4~2.6
3000~10000
2.0~2.5
50~100
2.1
6000
3.5~4.0
使用周期,月
>17
>6
4~6
寿命,年
—
—
4~7
乙炔
含量
反应前,%
反应后,ppm
0.15~0.38
<1
0.2~0.4
~0
1.0
<5
乙烯损失率,%
~0
较大
—
※(四)加氢脱乙炔流程
图1-31是C2馏分加氢脱乙炔流程,脱乙烷塔顶产物(乙炔、乙烷)馏分中还有5000ppm的乙炔,与预热到一定温度的氢气相混合,进入一段加氢绝热式反应器,进行加氢反应。
由一段出来的气体在加入补充氢气,经过调节温度后,再进入二段加氢二段加氢反应器,又进行加氢反应。
反应后气体经过换热降温,温度降低到-6度左右,送去绿油清洗塔,用乙烯塔侧线馏分洗涤气体中含有的绿油。
脱除掉绿油的气体进行干燥,然后去乙烯精馏系统。
在乙炔加氢过程中,有乙炔聚合生成绿油的副反应发生,生成的绿油数量多时,影响催化剂操作周期和使用寿命,严重时可能引起乙烯塔塔板结垢。
绿油生成量与氢气/乙炔摩尔比及催化剂床层温度有关,氢气与乙炔摩尔比越小,生成绿油量越多;催化剂床层温度升高,绿油生成量增多。
由于加氢反应过程中有聚合反应和分解生碳反应发生,这些聚合物和碳沉积在催化剂的表面上,降低了催化剂的活性,因此反应温度随着催化剂活性的降低而逐渐升高。
C3馏分中的丙炔和丙二烯,也可采用加氢方法脱除,一般用液相加氢法。
C3馏分液相加氢流程也分成两段加氢,一段是主反应器,使丙炔和丙二烯由含量2%左右降低到2000ppm左右;二段是副反应器,使剩余下的丙炔和丙二烯再加氢脱除到10ppm以下。
反应热的移出反应热的移出主要是借部分反应产物气化,将反应热带出反应器。
操作条件如下:
主加氢反应器:
温度………………………10~40摄氏度
压力………………………1.1~1.7MPa
H2/丙炔、丙二烯…………2.0(mol比)
副加氢反应器:
温度………………………10~50摄氏度
压力………………………2.6~2.65MPa
H2/丙炔、丙二烯…………2.0(mol比)
问题8:
为什么裂解气要进行压缩?
五、裂解气的压缩
1.目的要求:
提高压力可以使分离温度提高,降低压力可以使分离反应温度降低。
裂解气的分离正是在这个原理下进行的。
裂解气中很多组份在常压下都是气体,常压沸点都很低,见表1-29中的数据。
表1-29低级烃类的主要物理常数
名称
分子式
沸点,
摄氏度
临界温度,度
临界压力MPa
氢
H2
-252.5
-239.8
1.307
一氧
化碳
CO
-191.5
-140.2
3.496
甲烷
CH4
-161.5
-82.3
4.641
乙烯
C2H4
-103.8
9.7
5.132
乙烷
C2H6
-88.6
33.0
4.924
乙炔
C2H2
-83.6
35.7
6.242
丙烯
C3H6
-47.7
91.4
4.600
丙烷
C3H8
-42.07
96.8
4.306
异丁烷
i-C4H10
-11.7
135
3.696
异丁烯
i-C4H8
-6.9
144.7
4.002
丁烯
C4H8
-6.26
146
4.018
1,3-
丁二烯
C4H6
-4.4
152
4.356
正丁烷
n-C4H10
-0.50
152.2
3.780
顺-2-
丁烯
C4H8
3.7
160
4.204
反-2-
丁烯
C4H8
0.9
155
4.102
例如:
H2的沸点是-252.5摄氏度,
甲烷的沸点是-161.5摄氏度,
乙烯的沸点是-103.8摄氏度,
乙烷的沸点是-88.6摄氏度,
乙炔的沸点是-83.6摄氏度,
丙烯的沸点是-47.7摄氏度,
丙烷的沸点是-42.07摄氏度。
如果在常压下将这些组份进行冷凝分离,则分离温度很低,需要很多冷量,冷量也是一种能量。
目的:
为了使分离温度不会太低,节省低温冷量及除去裂解气中相当数量的水和重质烃,可以适当提高分离的压力。
裂解气的深冷分离压力与相应的分离温度有如下的数据关系:
分离压力,MPa分离温度,摄氏度
3.0~4.0………………………-96
0.6~1.0………………………-130
0.15~0.3……………………-140
2.压力的确定:
从上述数据可以看出:
分离压力高的时候,则分离温度温度也高;反之,分离压力低的时候,分离温度也低。
分离操作压力高的时候,多耗压缩功,少耗冷量;P升高,W升高,L降低。
分离操作压力低的时候,则相反:
P降低,W降低,L升高。
另外分离压力高的时候,可以使精馏塔塔底温度升高,很容易引起重组份的聚合,并使烃类相对挥发度降低,增加分离难度;低压下则相反,塔底温度低不容易发生聚合,烃类相对相对挥发度大,分离比较容易。
3.压缩比和段间温度:
为了节省能量,降低压缩的功率,气体压缩一般都采用多段压缩,段与段段与段之间都设置中间冷却器。
裂解气体压缩基本上是一个绝热过程,气体压力升高后,温度也上升,气体经过压缩后的温度,可以用气体绝热方程式计算得出。
绝热方程式如下:
T2=T1*(P2/P1)^[(k-1)/k](1-22)
式中:
T1,T2——压缩前后的温度,K;
P1,P2——压缩前后的压力,MPa;
K——绝热指数,k=Cp/Cv。
例5:
裂解气自T1=20摄氏度,P1=0.105MPa,压缩到P2=3.6MPa,如果是一段压缩,请计算压缩气体出口温度。
解:
取裂解气的绝热指数k=1.288,则得:
T2=T1*(P2/P1)^(k-1)/k
=(273+20)*(3.6/0.105)^(1.228-1)/1.228
=566K(293摄氏度)
从以上计算可以看出,裂解气从入口压力P1=0.105MPa,一段压缩到P2=3.6MPa,温度要从20摄氏度升高到293摄氏度,这样会导致二烯烃发生聚合反应而生成树脂,严重影响压缩机的操作,甚至会破坏正常的生产操作。
因此必须采用多段压缩,使每段压缩比(P2/P1)不能太大。
以保证每段出口温度不高于90~100摄氏度。
例如,如果采用5段压缩,则每段压缩比为2.03,而且每段压缩后,升高温度的气体,都需要进行段间冷凝冷却,必须维持较低的入口温度,才能保证压缩气体出口温度不高于90~100摄氏度。
4.压缩机段数:
段数愈多,最终压力愈大。
5.压缩机形式:
现在大规模生产厂的裂解气体压缩机都是离心式的,一般为4~5段。
压缩机每分钟转数可达到3000~16000,表1-30是5段离心