制造学院数控技术实验指导书.docx
《制造学院数控技术实验指导书.docx》由会员分享,可在线阅读,更多相关《制造学院数控技术实验指导书.docx(38页珍藏版)》请在冰豆网上搜索。
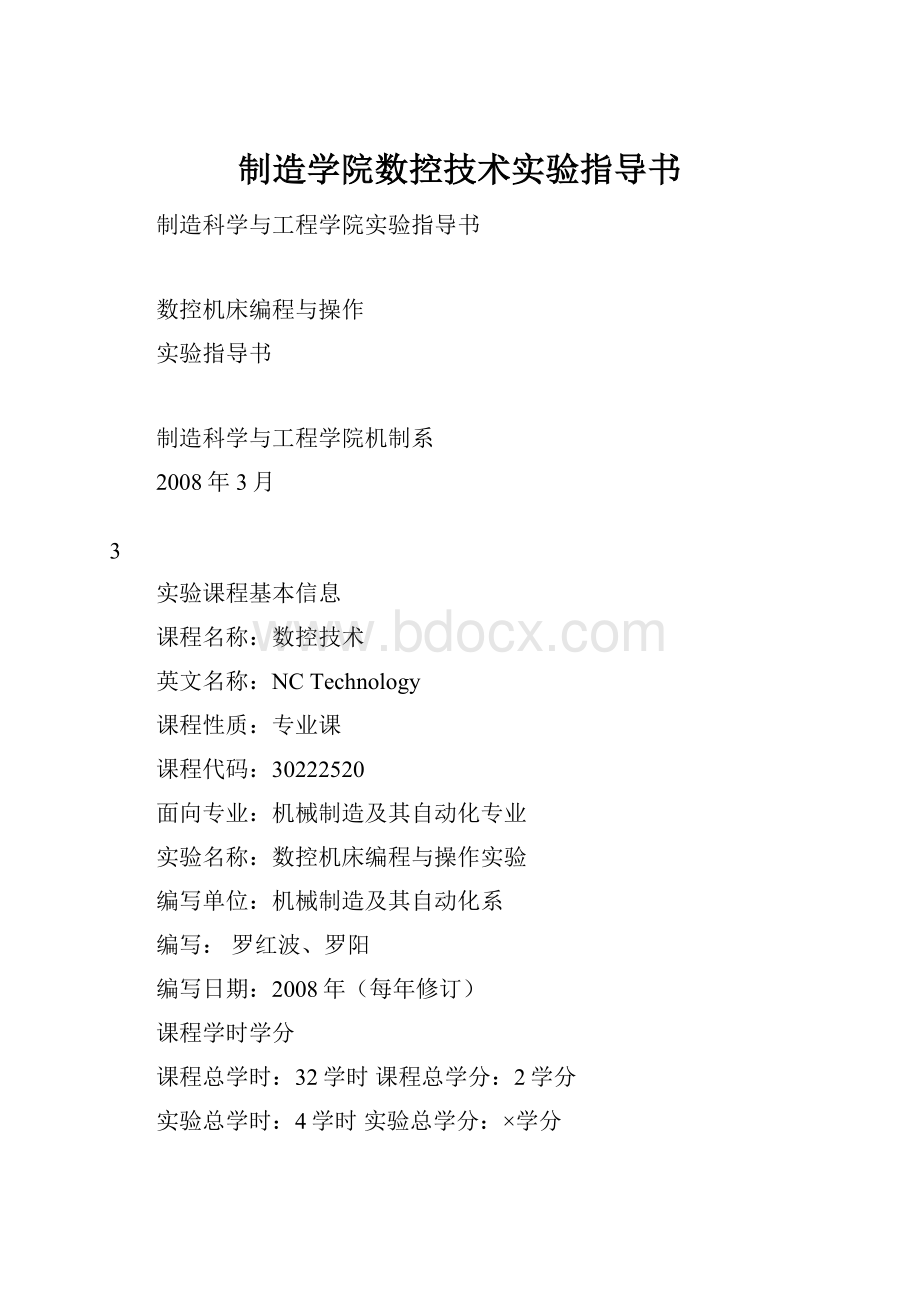
制造学院数控技术实验指导书
制造科学与工程学院实验指导书
数控机床编程与操作
实验指导书
制造科学与工程学院机制系
2008年3月
3
实验课程基本信息
课程名称:
数控技术
英文名称:
NCTechnology
课程性质:
专业课
课程代码:
30222520
面向专业:
机械制造及其自动化专业
实验名称:
数控机床编程与操作实验
编写单位:
机械制造及其自动化系
编写:
罗红波、罗阳
编写日期:
2008年(每年修订)
课程学时学分
课程总学时:
32学时课程总学分:
2学分
实验总学时:
4学时实验总学分:
×学分
目录
一、实验目的2
二、实验条件2
三、实验步骤2
四、数控编程基础2
五、FANUC0MD数控铣床操作8
六、FANUC0TD数控车床操作12
七、GSK928TA数控车床操作17
实验报告23
一、
实验目的
《数控技术》是一门讲述数控技术原理、数控编程技术以及数控机床操作技术的工程学科。
数控编程与机床操作实验教学有助于学生对课程教学重点内容的理解。
通过本实验,学生可以完整的演练从零件图、数控工艺分析、代码编制、程序调试的数控程序编制过程,同时可演练对刀、机床参数设定等数控机床操作技术,加深对现代数控机床编程与操作技术的认识,了解其工作过程和相关设计计算方法,初步掌握数控机床的编程与操作技术。
二、实验条件
实验中学生可自由组合,1-3人一组,每组一套实验设备,分工协作完成实验。
要求根据实验项目中实验内容进行相关计算,绘制相关图表,填写实验报告。
实验报告式样及要求见附件。
实验设备包括:
一台计算机(预装CIMCOEDIT、数控加工仿真系统等软件)
三、实验步骤
实验给定或由学生自行选择一个难度适中的车削类或铣削类零件,首先按照数控编程的方法、计算步骤,编制数控加工程序;然后选定数控机床,设定零件毛坯、刀具,在机床上完成零件与刀具的安装、对刀、机床参数设定、传入数控程序等操作,最后试切加工出该零件。
四、数控编程基础
手工编程的步骤如下图4-1所示
图4-1数控编程步骤
1.FANUC数控铣床G指令
代码
分组
意义
格式
G00
01
快速进给、定位
G00X--Y--Z--
G01
直线插补
G01X--Y--Z--
G02
圆弧插补CW(顺时针)
XY平面内的圆弧:
ZX平面的圆弧:
YZ平面的圆弧:
G03
圆弧插补CCW(逆时针)
G04
00
暂停
G04[P|X]单位秒,增量状态单位毫秒,无参数状态表示停止
G15
17
取消极坐标指令
G15取消极坐标方式
G16
极坐标指令
GxxGyyG16开始极坐标指令
G00IP_极坐标指令
Gxx:
极坐标指令的平面选择(G17,G18,G19)
Gyy:
G90指定工件坐标系的零点为极坐标的原点
G91指定当前位置作为极坐标的原点
IP:
指定极坐标系选择平面的轴地址及其值
第1轴:
极坐标半径
第2轴:
极角
G17
02
XY平面
G17选择XY平面;
G18选择XZ平面;
G19选择YZ平面。
G18
ZX平面
G19
YZ平面
G20
06
英制输入
G21
米制输入
G28
00
回归参考点
G28X--Y--Z--
G29
由参考点回归
G29X--Y--Z--
G40
07
刀具半径补偿取消
G40
G41
左半径补偿
G42
右半径补偿
G43
08
刀具长度补偿+
G44
刀具长度补偿-
G49
刀具长度补偿取消
G49
G50
11
取消缩放
G50缩放取消
G51
比例缩放
G51X_Y_Z_P_:
缩放开始
X_Y_Z_:
比例缩放中心坐标的绝对值指令
P_:
缩放比例
G51X_Y_Z_I_J_K_:
缩放开始
X_Y_Z_:
比例缩放中心坐标值的绝对值指令
I_J_K_:
X,Y,Z各轴对应的缩放比例
G52
00
设定局部坐标系
G52IP_:
设定局部坐标系
G52IP0:
取消局部坐标系
IP:
局部坐标系原点
G53
机械坐标系选择
G53X--Y--Z--
G54
14
选择工作坐标系1
GXX
G55
选择工作坐标系2
G56
选择工作坐标系3
G57
选择工作坐标系4
G58
选择工作坐标系5
G59
选择工作坐标系6
G68
16
坐标系旋转
(G17/G18/G19)G68a_b_R_:
坐标系开始旋转
G17/G18/G19:
平面选择,在其上包含旋转的形状
a_b_:
与指令坐标平面相应的X,Y,Z中的两个轴的绝对指令,在G68后面指定旋转中心
R_:
角度位移,正值表示逆时针旋转。
根据指令的G代码(G90或G91)确定绝对值或增量值
最小输入增量单位:
0.001deg
有效数据范围:
-360.000到360.000
G69
取消坐标轴旋转
G69:
坐标轴旋转取消指令
G73
09
深孔钻削固定循环
G73X--Y--Z--R--Q--F--
G74
左螺纹攻螺纹固定循环
G74X--Y--Z--R--P--F--
G76
精镗固定循环
G76X--Y--Z--R--Q--F--
G90
03
绝对方式指定
GXX
G91
相对方式指定
G92
00
工作坐标系的变更
G92X--Y--Z--
G98
10
返回固定循环初始点
GXX
G99
返回固定循环R点
G80
09
固定循环取消
G81
钻削固定循环、钻中心孔
G81X--Y--Z--R--F--
G82
钻削固定循环、锪孔
G82X--Y--Z--R--P--F--
G83
深孔钻削固定循环
G83X--Y--Z--R--Q--F--
G84
攻螺纹固定循环
G84X--Y--Z--R--F--
G85
镗削固定循环
G85X--Y--Z--R--F--
G86
退刀形镗削固定循环
G86X--Y--Z--R--P--F--
G88
镗削固定循环
G88X--Y--Z--R--P--F--
G89
镗削固定循环
G89X--Y--Z--R--P--F--
2.FANUC数控车床G指令
重要提示:
FANUC系统中车床只能采用直径编程。
G20,G21,G40,G41,G42,G54-G59与FANUC数控铣相同,参考上一节。
代码
分组
意义
格式
G00
01
快速进给、定位
G00X--Z--
G01
直线插补
G01X--Z--
G02
圆弧插补CW(顺时针)
G03
圆弧插补CCW(逆时针)
G04
00
暂停
G04[X|U|P]X,U单位:
秒;P单位:
毫秒(整数)
G20
06
英制输入
G21
米制输入
G28
0
回归参考点
G28X--Z--
G29
由参考点回归
G29X--Z--
G32
01
螺纹切削(由参数指定绝对和增量)
GxxX|U…Z|W…F|E…F指定单位为0.01mm/r的螺距。
E指定单位为0.0001mm/r的螺旋
G40
07
刀具补偿取消
G40
G41
左半径补偿
G42
右半径补偿
G50
00
设定工件坐标系:
G50XZ
偏移工件坐标系:
G50UW
G53
机械坐标系选择
G53X--Z--
G54
12
选择工作坐标系1
GXX
G55
选择工作坐标系2
G56
选择工作坐标系3
G57
选择工作坐标系4
G58
选择工作坐标系5
G59
选择工作坐标系6
G70
00
精加工循环
G70PnsQnf
G71
外园粗车循环
G71UΔdRe
G71PnsQnfUΔuWΔwFf
G72
端面粗切削循环
G72W(Δd)R(e)
G72P(ns)Q(nf)U(Δu)W(Δw)F(f)S(s)T(t)
Δd:
切深量
e:
退刀量
ns:
精加工形状的程序段组的第一个程序段的顺序号
nf:
精加工形状的程序段组的最后程序段的顺序号
Δu:
X方向精加工余量的距离及方向
Δw:
Z方向精加工余量的距离及方向
G73
封闭切削循环
G73UiWΔkRd
G73PnsQnfUΔuWΔwFf
G74
端面切断循环
G74R(e)
G74X(U)_Z(W)_P(Δi)Q(Δk)R(Δd)F(f)
e:
返回量
Δi:
X方向的移动量
Δk:
Z方向的切深量
Δd:
孔底的退刀量
f:
进给速度
G75
内径/外径切断循环
G75R(e)
G75X(U)_Z(W)_P(Δi)Q(Δk)R(Δd)F(f)
G76
复合形螺纹切削循环
G76P(m)(r)(a)Q(Δdmin)R(d)
G76X(u)_Z(W)_R(i)P(k)Q(Δd)F(l)
m:
最终精加工重复次数为1—99
r:
螺纹的精加工量(倒角量)
a:
刀尖的角度(螺牙的角度)可选择80,60,55,30,29,0六个种类
m,r,a;同用地址P一次指定
Δdmin:
最小切深度
i:
螺纹部分的半径差
k:
螺牙的高度
Δd:
第一次的切深量
l:
螺纹导程
G90
01
直线车削循环加工
G90X(U)---Z(W)---F---
G90X(U)---Z(W)---R---F---
G92
螺纹车削循环
G92X(U)---Z(W)---F---
G92X(U)---Z(W)---R---F---
G94
端面车削循环
G94X(U)---Z(W)---F---
G94X(U)---Z(W)---R---F---
G98
05
每分钟进给速度
G99
每转进给速度
3.FANUC数控M代码
代码
意义
格式
M00
停止程序运行
M01
选择性停止
M02
结束程序运行
M03
主轴正向转动开始
M04
主轴反向转动开始
M05
主轴停止转动
M06
换刀指令
M06T--
M08
冷却液开启
M09
冷却液关闭
M30
结束程序运行且返回程序开头
M98
子程序调用
M98Pxxnnnn
调用程序号为Onnnn的程序xx次。
M99
子程序结束
子程序格式:
Onnnn
…
M99
五、FANUC数控铣床操作
1.启动数控仿真系统
如图5-1设置服务器、用户名、密码,点击运行进入FANUC0MD数控铣床仿真界面。
注意选择右下角“南通机床厂FANUC0MD”面板,关闭右侧的“程序保护开关”。
图5-1FANUC0MD数控铣床仿真系统
2.机床回零
如图5-2所示,在操作面板的MODE旋钮位置点击鼠标左键,将旋钮拨到“回零”档,再依次点击“+Z”“+X”“+Y”按钮,此时Z、X、Y轴将分别回零,相应操作面板上Z、X、Y轴的回零指示灯亮,同时CRT上的坐标显示工作台参考点位置(0,0,0)。
图5-2操作面板上的MODE旋钮和坐标移动按钮
3.安装零件
点击菜单“工件操作/设置毛坯…”,在定义毛坯对话框(如图5-3)中设置零件尺寸高、长和宽,并按确定按钮。
以下步骤以毛坯尺寸(长250,宽250,高40)为例来对刀。
图5-3“设置毛坯”对话框
点击菜单“工件操作/工件装夹”,在选择夹具对话框(如图5-4)中,选择夹具栏选取“工艺板装夹”的第2中方式,夹具尺寸用缺省值,并按确定按钮。
图5-4“工件装夹”对话框
4.设置刀具
选择菜单“机床操作”-“刀具管理”进入刀具管理对话框。
如图5-5。
选择编号“001”的刀具,将其直径用“修改”改为8mm。
用“添加到刀库”装入主轴。
图5-5刀具管理
5.对刀并设置刀具信息
在主轴上没有安装刀具时,可以安装芯棒来对刀,如图5-6。
利用芯棒检测工件坐标系零点的X和Y坐标的数值。
检测中系统在左下角将有“过紧”、“过松”、“合适”的提示。
检测的结果可以与“工件设置”对话框中,假定工件上平面中心的X、Y数值为-400、-200相互验证。
安装上刀具以后,先定位到工件上平面的上方,然后运用“手动”、“快速”和“手轮”移动Z坐标,使刀具正好位于工件上平面。
此时Z坐标就可以计算工件零点的Z坐标值。
图5-6选择芯棒
检测出工件零点的坐标值以后,假设为(-400,-200,-175),则可以设置G54的数值。
“MENUOFST”-“工件”,设置G54的X、Y、Z数值如上。
“MENUOFST”-“补正”,设置刀具半径为4mm。
如图5-7设置结果。
图5-7G54与刀具半径设置
6.输入NC程序
数控程序可以通过CIMCOEDIT等数控编辑软件输入并保存为文本格式文件,也可直接用FANUC系统的MDI键盘输入。
以下是一个示例程序:
O0100
N010G90G54G00X0Y0Z100
N020G00Z2.S150M03
N030X20.Y-44.
N040G01Z-4.F100
N050G41X0.Y-40.D01
N060G02X0.Y-40.I0.J40.
N070G01G40X-20.Y-44.
N080G00Z2.
N090X0.Y15.
N100G01Z-4.
N110G42X0.Y0.D01
N120G02X-30.Y0.I-15.J0.
N130X30.Y0.I30.J0.
N140X0.Y0.I-15.J0.
N150G40G01X0.Y15.
N160G00Z100.
N170X0.Y0.M05
N180M30
先将上述NC程序创建立一个文本文件(后缀名可以为nc、cnc、txt)。
双击模式按钮选择“编辑”,依次点击“PRGRM”-“LIB”,用机床面板按钮输入“O0100”,点击“INSRT”进入NC程序输入状态。
点击菜单“文件/打开”,再打开文件对话框选取前述NC文件,点击“打开”按钮,即可在液晶屏上看见数控程序。
7.自动加工
机床位置确定和刀补数据输入后,就可开始自动加工。
将操作面板的模式旋钮切换到自动,点击“循环启动”按钮,机床就开始自动加工,加工完毕就会出现如图5-8所示的结果。
图5-8加工结果
8.数控铣削编程与加工操作练习
自行设计一个零件,或者选择如图5-10零件,请分析工艺过程,选择加工参数,选择加工刀具,计算轨迹数据,编制NC程序,在斯沃数控仿真软件中完成零件加工。
按照要求填写实验报告。
图5-10铣削编程练习零件
六、
FANUC数控车床操作
1.启动数控仿真系统
如图6-1设置服务器、用户名、密码,点击运行进入FANUC0TD数控车床仿真界面。
注意选择右下角“FANUC0TD标准面板”,关闭右侧的“程序保护开关”。
图6-1FANUC0TD数控车床仿真系统
同时,请注意设置机床参数(菜单“机床操作”-“参数设置”),选择后置刀架,8方刀架。
如图6-2。
图6-2设置车床刀架
2.机床回零
如图6-3所示,在操作面板上点击“HOME”,再依次点击“+X”“+Z”按钮,此时X、Z轴将分别回零,相应操作面板上X、Z轴的回零指示灯亮,同时CRT上的坐标显示工作台参考点位置(0,0)。
图6-3操作面板上的HOME按钮和坐标移动按钮
3.安装零件
点击菜单“工件操作/设置毛坯…”,在定义毛坯对话框(如图6-4)中设置零件尺寸,并按确定按钮。
以下步骤以毛坯尺寸(长200,直径130)为例来对刀。
图6-4“设置毛坯”对话框
4.设置刀具
选择菜单“机床操作”-“刀具管理”进入刀具管理对话框。
如图6-5。
选择编号“001”的刀具,长度160、宽度25的外圆车刀。
用“添加到刀盘”装入01号刀位。
图6-5刀具管理
5.对刀并设置刀具信息
选择菜单“视窗视图”-“2D视图”将机床视图变换成平面视图(图6-6),方便对刀操作。
假设工件坐标系的零点在工件的左端面中心。
Z方向对刀操作:
设置模式为“JOG”,打开“TRVRS”,将刀尖告诉移动到工件右端面附近。
然后换成“JOGINC”模式,分别使用“×100”、“×10”、“×1”三种设置,将刀尖靠在工件右端面上。
此时液晶屏上显示的Z即为工件坐标系零点的Z坐标值。
(本例为395.832)
图6-6平面视图
图6-7Z方向对刀结果
X方向对刀操作:
在“JOG”方式,按“SPDLCW”使主轴正转。
按“-Z”移动刀具,加工一小段外圆。
然后按“SPDLSTOP”停主轴,按“+Z”向右退出刀具。
注意不可移动X坐标。
如图6-8。
图6-8加工一小段外圆
选择菜单“工件测量”-“特征线”。
如图,测量出加工的一小段外圆直径为117.93。
则端面中心的X坐标为(-142.070-117.93=-260)。
至此我们测量出工件右端面中心,即工件坐标系零点在机床坐标系中的坐标值为:
(-260,-395.832)
按“工件测量”-“测量退出”,退出工件测量状态。
图6-9外圆直径测量
检测出工件零点的坐标值以后,假设为(-260,-395.832),则可以用于设置G54的数值。
“MENUOFST”-“工件移”-“坐标系”,设置G54的X、Z数值如上。
如图6-10设置结果。
图6-10设置G54
如果需要多刀加工时,每把刀具重复以上的对刀过程,并将每把刀具的X、Z信息存储在“MENUOFST”-“形状”参数中,如图6-11。
此时,NC程序中使用TXXYY换刀指令即可调出相应的坐标信息。
其中XX为刀位号,YY为形状补偿参数号。
例如T0101,表示使用1号刀位上的刀具,调用“刀具补正/几何参数”G01上的X,Z作为工件零点。
图6-11设置刀具形状参数
6.输入NC程序
数控程序可以通过CIMCOEDIT等数控编辑软件输入并保存为文本格式文件,也可直接用FANUC系统的MDI键盘输入。
以下是一个示例程序:
O0100
N0020G54
N0030T0100
N0040S500M3
N0050G00X160.0Z1.0
N0060G00X131.0
N0070G71U2.0R1.0
N0080G71P90Q200U0.6W0.3F100
N0090G01X40.0
N0100Z-24.0F100
N0110X42.0
N0120X60.Z-40
N0130X72.0
N0140Z-55.
N0150X80.0
N0160X100.Z-85.0
N0170X120.0
N0180Z-100.0
N0190X131.0
N0200G00Z1.0
N0205G70P90Q200
N0210G00X160.0
N0220G53
N0230M30
先将上述NC程序创建立一个文本文件。
双击模式按钮选择“编辑”,依次点击“PRGRM”-“LIB”,用机床面板按钮输入“O0100”,点击“INSRT”进入NC程序输入状态。
点击菜单“文件/打开”,再打开文件对话框选取前述NC文件,点击“打开”按钮,即可在液晶屏上看见数控程序。
7.自动加工
机床位置确定和刀补数据输入后,就可以开始自动加工。
选“AUTO”模式,点击绿色的“CYCLESTART”按钮,机床就开始自动加工,加工完毕就会出现如图6-12所示的结果。
图6-12车削加工结果
8.数控车削编程与加工操作练习
自行设计一个零件,或者选择如图零件,请分析工艺过程,选择加工参数,选择加工刀具,计算轨迹数据,编制NC程序,在斯沃数控仿真软件中完成零件加工。
按照要求填写实验报告。
七、GSK928TA数控车床操作
1.启动数控仿真系统
如图7-1设置服务器、用户名、密码,点击运行进入GSK928TA数控车床仿真界面。
按绿色的“电源开”启动系统,松开红色的“急停”按钮。
系统进入正常运行状态。
图7-1GSK928TA数控车床仿真系统
同时,请注意设置机床参数(菜单“机床操作”-“参数设置”),选择前置刀架,4方刀架。
如图7-2。
这样与实际机床结构形式相同。
图7-2设置车床刀架
2.安装零件
点击菜单“工件操作/设置毛坯…”,在定义毛坯对话框(如图7-3)中将零件尺寸,并按确定按钮。
以下步骤以毛坯尺寸(长200,直径80)为例来对刀。
图7-3“设置毛坯”对话框
3.设置刀具
选择菜单“机床操作”-“刀具管理”进入刀具管理对话框。
如图7-4。
选择编号“002”的刀具,长度160、宽度25的外圆车刀。
用“添加到刀盘”装入01号刀位。
选择编号“006”的刀具,长度160,刀片宽3mm。
图7-4刀具管理
4.对刀并设置刀具信息
选择菜单“视窗视图”-“2D视图”将机床视图变换成平面视图,方便对刀操作。
假设工件坐标系的零点在工件的左端面中心。
第01号外圆车刀的对刀方法如下:
(1)X方向对刀操作:
主界面选择“1-手动方式”,快速移动刀具到工件外圆附近。
按“主轴正转”启动主轴,切一小段外圆。
如图7-5。
然后停止主轴,进入外圆测量,得到切出的一小段外圆的直径。
按“Com”-“2-坐标设置”,X的坐标输入测量得到的直径值。
如图7-6。
图7-5X方向试切对刀
图7-6测量直径和设置X坐标
(2)Z方向对刀操作:
主界面选“1-手动方式”,使主轴正转。
按“-X”和“-Z”移动刀具靠近工件外圆和端面,切端面,X方向退出刀具,不得移动Z坐标。
然后按“Com”-“2-坐标设置”设置坐标系,跳过X设置,设置Z坐标为0。
如图7-7。
图7-7设置Z坐标
确定了以第01号刀具为参考的工件坐标系以后,其余各刀具均需以此为参考,试切、计算确定刀尖相对于01号刀具的位置补偿参数。
在手动方式,输入T20换02号刀。
第02号刀具确定位置补偿参数的方法如下:
(1)X方向对刀操作:
启动主轴正转,将刀具靠近工件外圆表面,以最小移动量缓慢接近工件外圆表面,待刚好有铁屑飞出时,停止移动。
按“Com”-“3-试切点”后,有“滴”声,液晶屏回到手动方式界面,但系统已记录下来当前位置。
再次按“Com”-“4-X试切数”后,输入当前刀具所靠近外圆的直径,系统自动计算与01号刀具的偏移值。
系统提示输入当前X偏移数值存储的参数编号,本例为02号刀具。
如图7-8。
图7-802号刀X方向的位置补偿参数
(2)Z方向对刀操作:
启动主轴正转,将刀具靠近工件端面,以最小移动量缓慢接近工件端面,待刚好有铁屑飞出时,停止移动。
同前述X方向,仍然按“Com”-“3-试切点”后,有“滴”声,液晶屏回到手动方式界面,但系统已记录下来当前位置。
再次按“Com”-“5-Z试切数”后,输入0,系