光驱外客注射模设计.docx
《光驱外客注射模设计.docx》由会员分享,可在线阅读,更多相关《光驱外客注射模设计.docx(17页珍藏版)》请在冰豆网上搜索。
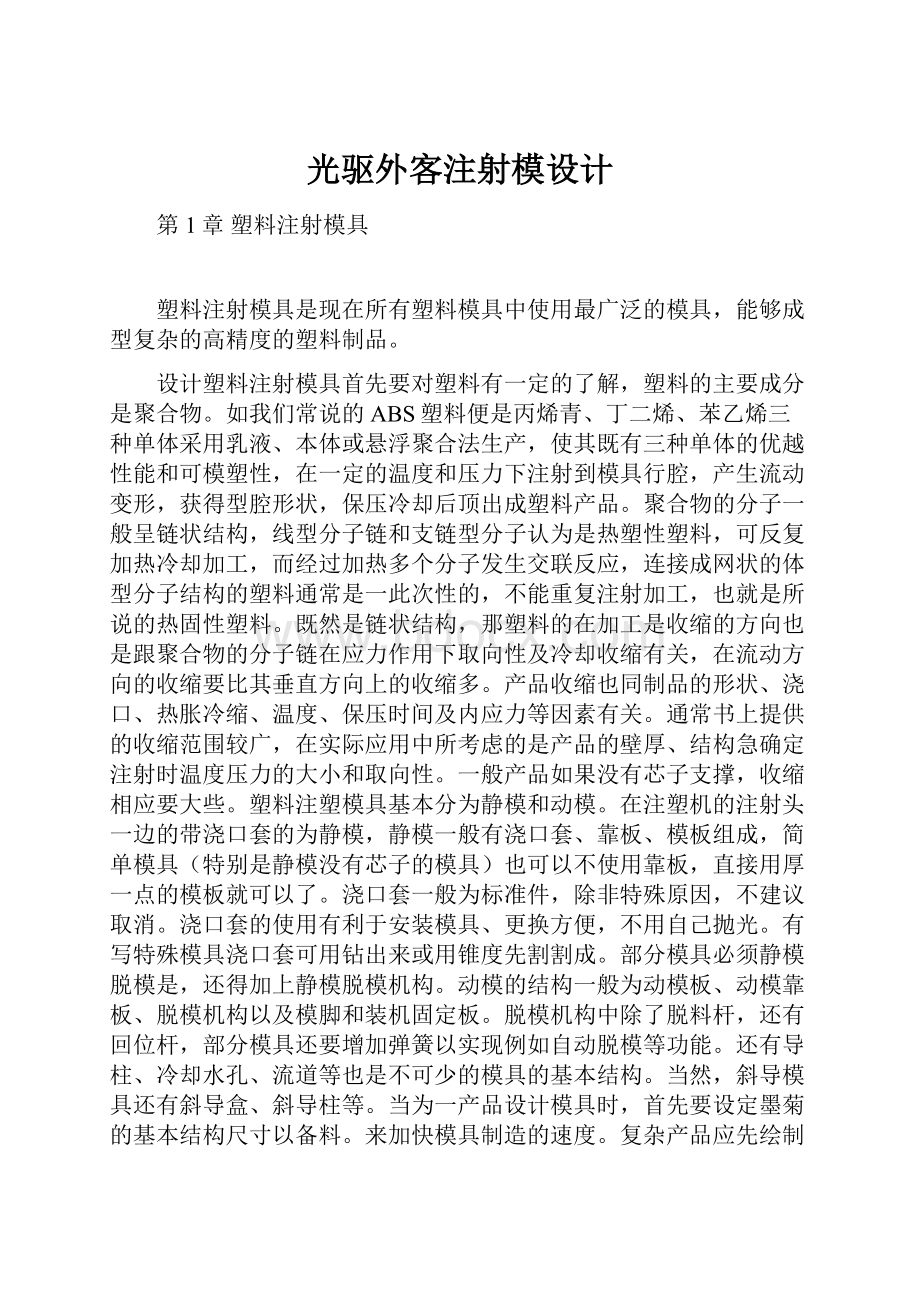
光驱外客注射模设计
第1章塑料注射模具
塑料注射模具是现在所有塑料模具中使用最广泛的模具,能够成型复杂的高精度的塑料制品。
设计塑料注射模具首先要对塑料有一定的了解,塑料的主要成分是聚合物。
如我们常说的ABS塑料便是丙烯青、丁二烯、苯乙烯三种单体采用乳液、本体或悬浮聚合法生产,使其既有三种单体的优越性能和可模塑性,在一定的温度和压力下注射到模具行腔,产生流动变形,获得型腔形状,保压冷却后顶出成塑料产品。
聚合物的分子一般呈链状结构,线型分子链和支链型分子认为是热塑性塑料,可反复加热冷却加工,而经过加热多个分子发生交联反应,连接成网状的体型分子结构的塑料通常是一此次性的,不能重复注射加工,也就是所说的热固性塑料。
既然是链状结构,那塑料的在加工是收缩的方向也是跟聚合物的分子链在应力作用下取向性及冷却收缩有关,在流动方向的收缩要比其垂直方向上的收缩多。
产品收缩也同制品的形状、浇口、热胀冷缩、温度、保压时间及内应力等因素有关。
通常书上提供的收缩范围较广,在实际应用中所考虑的是产品的壁厚、结构急确定注射时温度压力的大小和取向性。
一般产品如果没有芯子支撑,收缩相应要大些。
塑料注塑模具基本分为静模和动模。
在注塑机的注射头一边的带浇口套的为静模,静模一般有浇口套、靠板、模板组成,简单模具(特别是静模没有芯子的模具)也可以不使用靠板,直接用厚一点的模板就可以了。
浇口套一般为标准件,除非特殊原因,不建议取消。
浇口套的使用有利于安装模具、更换方便,不用自己抛光。
有写特殊模具浇口套可用钻出来或用锥度先割割成。
部分模具必须静模脱模是,还得加上静模脱模机构。
动模的结构一般为动模板、动模靠板、脱模机构以及模脚和装机固定板。
脱模机构中除了脱料杆,还有回位杆,部分模具还要增加弹簧以实现例如自动脱模等功能。
还有导柱、冷却水孔、流道等也是不可少的模具的基本结构。
当然,斜导模具还有斜导盒、斜导柱等。
当为一产品设计模具时,首先要设定墨菊的基本结构尺寸以备料。
来加快模具制造的速度。
复杂产品应先绘制好产品图,再定好模具的尺寸。
现在的模具基本上要进行热处理,家高
模具的硬度,提高模具使用寿命。
早热处理前,先对模板进行初步加工:
钻好导柱孔、回位孔(动模)、型腔孔、螺丝孔、浇口套孔(静模)、拉料孔(动模)、冷却水孔等,铣好流道、型腔,有些模具还应铣好斜导盒等。
现在普通精密模具的模板一般用Cr12、Cr12Mov和一些专业模具钢,CR12等硬度不能太高,在HRC60度时经常开裂,模板的常用硬度一般为HRC55度左右。
芯子的硬度可在HRC58以上。
如果材料为Cr2W8v,制造后在氮化处理表面硬度,硬度应为HRC58以上,氮化层应越厚越好。
浇口直接关系到塑件的美观,浇口设计不好的话,容易产生缺陷。
在没有任何阻挡的情况下和容易产生蛇型流。
对于要求高的产品,还应设计溢流和排气。
溢流处可以用顶杆,不要在模板上留有溢流飞边,才不至于影响模具寿命。
第2章塑件分析
2.1材料分析
(1)产品的材料为:
尼龙1010
(2)查资料可知道尼龙1010的主要物理参数:
聚酰胺俗称尼龙(Nylon)英文名称为Polyamide(简称PA),是分子主链上含有重复酰胺基团—[NHCO]—的热塑性树脂总称。
摆阔脂肪族PA和芳香族PA。
其中,脂肪族PA品种多
,产量大,应用广泛,其命名由合成单体具体的碳原子数而定。
尼龙中的主要品种是尼龙6和尼龙66,占绝对主导地位,其次是尼龙11,尼龙12,尼龙610,尼龙612,例外还有尼龙1010,尼龙46,尼龙7,尼龙9,尼龙13,新品种有尼龙6I,尼龙9T和特殊尼龙MXD6(阻隔性树脂)等,尼龙的改性品种数量繁多,如增强尼龙,但体浇铸尼龙(MC尼龙),反应注射成型(RTM)尼龙,芳香族尼龙,透明族尼龙,高抗冲(超韧)尼龙,电镀尼龙,导电尼龙,阻燃尼龙,尼龙与其它聚合物工混合合金等,满足不同特殊要求,广泛用作金属,木材等传统材料代用品,作为各种结构材料。
尼龙是最重要的工程材料,产量在五大通用工程塑料中居首位。
性能:
尼龙为韧性角状半透明或乳白色结晶树脂,作为工程塑料的尼龙分子量一般为1.5-3万尼龙具有很高的机械强度,软化点高,耐热,摩擦系数低,耐磨损,自滑润性,吸震性和消音性,耐油,耐弱酸,耐碱和一般溶剂,电绝缘性好,有自熄性,无毒,无臭,耐候性好,染色性差。
缺点是吸水性大,影响尺寸稳定性和电性能,纤维增强可降低树脂吸水率,使其能在高温、高湿下工作。
尼龙与玻璃纤维亲合性十分良好。
尼龙中尼龙66的硬度、刚性最高,但韧性最差。
各种尼龙按韧性大小排序为:
PA66〈PA66/6〈PA6〈PA610〈PA11〈PA12。
尼龙的燃烧性为UL94v-2级,氧指数为24-28,尼龙的分解温度〉299摄适度,在449~499摄适度时会发生自燃。
尼龙的溶体流动性好,故制品壁厚可小到1mm。
水份Q-GHPF3-19991.0
熔点Q-GHPF3-1999大于等于
相对粘度Q-GHPF3-19991.70
细度(通过φ180um筛网)Q-GHPF3-199996
尼龙1010的收缩率在0.5%-5%。
由于塑件的料厚为5mm,故最终确定注塑件是收缩率在2.5%。
2.2塑件缺陷分析
(1)变形:
产品出模时变形,有模温、料温和产品出模时温度较高,保压时间不够和残余应力的作用等非设计原因,产品壁厚和收缩不均,浇口位置不当和顶杆位置不当、粘模造成的等是设计是必须考虑的。
(2)断裂:
回料或填料过多、顶杆太小太少、顶速过快、料湿太低、粘模、间隙太小造成的真空态等,有嵌件的嵌件预热不够也回造成裂痕。
少数产品须经退火消除应力。
(3)磨损:
脱模斜度太小脱模困难、垂直度不行,磨损处有加工残留,如磨床后在型腔锋角处毛刺。
粗糙度过大等,很容易解决。
气泡温度太低、太高,壁厚悬殊或过厚,水份过高,含溶剂或易挥发无,压力过大、排气不畅,注射周期太长造成塑料在料筒里分解。
(4)飞边:
锁模压力敌不过注射压力,模板变形、闭合不紧,温度过高,芯子型腔间隙太小、位置偏移等。
(5)斑纹:
塑料过热分解,压力太低,流道、浇口太小和位置不当,当浇口设计不合理,发生喷射,塑料没有充分干燥。
温度太低在充模时形成波纹。
熔接痕在多芯子并破坏时是很难避免的,合理的调控温度和注射温度,设计好浇口和排气溢流位置以改善产品外观。
第3章注射机的选择
3.1初选注射机:
根据制件要求
初选注射机的型号为:
XS—ZY—125型号的螺杆式注射机!
3.2注射机的有关工艺参数校核
3.2.1型腔数量的确定和校核
对于多型腔对于多型腔注射模,其型腔数量与注射机的塑化速率、最大注射量及锁模力等参数有关,此外,还受塑件的精度和生产的经济性等因素影响。
(1)按注射机的额定塑化量进行校核
nm≤KMt/3600-m1公式(3-1)
式中K—注射机最大注射量的利用系数,一般取0.8;
M—注射机的额定塑化量,g/h或cm3/h;
t—成型周期,S;
m1—浇注系统所需塑料质量或体积,g或cm3;
m—单个塑件的质量或体积,g或cm3;
n—型腔的数量。
(2)按注射机的额定锁模力进行校核
npA≤FP-pA1公式(3-2)
式中FP—注射机的额定锁模力,N;
A—单个塑件在模具分型面上的投影面积,mm3
A1—浇注系统在模具分型面上的投影面积,mm3
P—塑料熔体对型腔的成型压力,MPa,其大小一般是注射压力的80%。
按上述方法确定或校核型腔数量是,还必须考虑成型塑件的尺寸精度、生产的经济性及注射机安装模板的大小。
一般说来,形腔的数量越多,塑件的精度就越低(经检验认为,没增加一个行腔,塑件的尺寸精度便降低4%-8%),模具的制造成本也越高,但效率会明显增加。
由于本制品为小尺寸塑件,为了不浪费材料,选用一模二腔。
3.2.2最大注射量的校核
最大注射量是指注射机一次注射塑料的最大容量。
设计模具时,应保证成型塑件所需的总注射量小于所选注射机的最大容量,即:
nm+m1≤Kmp公式(3-3)
式中mp—注射机允许的最大注射量,g或cm3
因聚苯乙烯塑料的密度是1.05g/cm3近似于1g/cm,因此规定注塞式注射机的允许最大注射量是以一次注射聚乙苯的最大克数为标准的;而螺杆式注射机是以体积表示最大注射量的,与塑料品种无关。
nm+m1≤Kmp关
n—型腔的数量为1
m—单个塑件的质量或体积,g或cm3
m1—浇注系统所需塑料质量或体积,g或cm3
k—注射机最大注射量的利用系数,一般取0.8
mp—注射机允许的最大注射量,g或cm3
系统的凝料设为0.4cm3,则m1=0.4
所以左边=2×9.9+0.4=20.2
右边=0.8×125=100
因此满足公式(3-3)
所以不等式成立!
所以注射量的标准符合要求
3.2.3锁模力的校核
当高压的塑料熔体充满模具型腔时,会产生使模具分型面涨开的力,这个力的大小等于塑件和浇注系统在分型面上的投影面积之和乘以型腔的压力,它应小于注射机的额定锁模力FP,才能保证注射时不发生溢料现象,即:
Fz=p(nA+A1)式中Fz—熔融塑料在型面上的涨开力,N。
型腔内的压力约为注射机注射压力的80%左右,通常取20~40MPa。
常用塑料注射成型时所用的型腔压力值列于表3-1。
表3-1常用塑料注射时所选用型腔压力
塑料品种
高压聚乙烯(PE)
低压聚乙烯(PE)
PS
AS
ABS
POM
PC
型腔压力
10~15
20
15~20
30
30
35
40
Fz=p(nA+A1)Fz_—熔融塑件在分型面上的涨开力;
A—单个塑件在模具分裂面上的投影面;
P—成型压力MPa,大小一般为注射压力的80%;
由于制品为ABS材料,
左边=125x(1x
πx16+2xx16)=100480N=100.48KN
右边=900
因此满足公式3-4
所以不等式成立
所以锁模力符合要求!
3.2.4注射压力校核
塑料成型所需要的注射压力是由塑料品种、注射机类型、喷嘴形式、塑件形状和浇注系统的压力损失等因素决定的。
对于粘度较大的塑料以
及形状细薄、流程长的塑件,注射压力应取大些。
由于柱塞式注射机的压力损失比螺杆式大,所以注射压力也应取大些。
注射压力的校核是核定注射机的额定注射压力是否大于成型时所需的注射压力。
由于注射机的额定注射压力为120MPa,而成型时所需的注射压力为100MPa
所以注射压力符号要求!
3.2.5开模行程的校核
注射机的开模行程是有限制的,塑件从模具中取出是所需的开模距离必须小于注射机的最大开模距离,否则塑件无法从模具中取出。
本模具是具有侧向抽芯是的最大形成。
当模具需要利用开模动作完成侧向抽芯时,开模行程的校核应考虑侧向抽芯所需的开模行程,若设完成侧向抽芯所需的开模行程为Hc,当Hc≤H1+H1,Hc对开模行程没有影响。
当Hc
S≥H1+H2+(5~10)㎜公式(3-5)
Hc—侧向抽芯所需的开模形成mm;
H1—推出距离mm;
H2—包括浇注系统在内的塑件高度mm;
S=160mm
经计算Hc=10mm
H1=4.5+2=6.5mm
Hc
S≥H1+H2+(5~10)
所以开模行程符合要求!
3.2.6模具与注射机的安装部分相关尺寸的校核
为了使注射模具能顺利的安装在注射机上并生产出合格的塑件,在设计模具时必须校核注射机与模具安装有关的尺寸。
一般情况下设计模具时应校核的部分包括喷嘴尺寸、定位圈尺寸、模具的最大和最小厚度及模板上安装螺孔尺寸等。
(1)喷嘴尺寸
设计模具时,主流道始端的球面必须比注射机喷嘴头部球面略大一些,
如图3.1所示,即R比r大1~2㎜。
主流道小端直径略大,即D比d大0.5~1㎜,以防止主流道口部积存凝料而影响脱模。
已知:
r=12㎜d=4㎜
又R=r+(1~2)㎜
D=d+(1~2)㎜
用数控铣床,甚至加工中心来进行。
斜滑块(斜型芯)是模具的重要成型零件,常用T8、T10、45钢等材料来制造,热处理硬度要求HRC≥50,对于45钢HRC≥40。
本设计中的制品要求不高,为减少成本,提高经济性,可采用45钢,HRC≥40。
图7-4
7.4锲紧块的设计
由于在注射成型过程中,侧向分型在成型压力的作用下会使侧滑块向外位移,侧向力会通过侧滑块传给斜导柱,使其变形,如果斜导柱与侧滑块上的斜导孔采用较大的间隙配合,侧滑块的外移会降低塑件侧向凹凸处的尺寸精度,所以必须采用锲紧块。
设成型的过程中,侧向成型零件在成型压力的作用下会使侧滑块向外位移,如果没有锲紧块锲紧,侧向力会通过侧滑块传递给斜导柱,使其发生变形。
如果斜导柱与侧滑块上的斜导孔采用较大的间隙(0.4-0.5㎜)配合,侧滑块的外移会极大降低塑件侧向凹凸处的尺寸精度,因此,在斜导柱侧向抽芯机构设计时,必须考虑侧滑块的锁紧。
锲紧块的结构形式如图8.5所示。
由于本设计中,侧滑块的抽芯方向垂直于合模方向
所以α′=α+(2~3)
即α′=18
图7-5
第8章温度调节系统
模具温度是指模具型腔和型芯的表面温度。
模具温度是否合适,均匀与稳定,对塑料熔体的充模流动,固化定型,生产效率以及塑料的外形和精度尺寸都有重要的影响。
模具中设置温度调节系统的目的就是要通过控制模具的温度,使注射成型塑件有良好的产品质量和较高的生产效率。
8.1冷却系统的设计
冷却回路的设计应该做到回路系统内流动的介能充分吸收成型塑料所导致的热量,使模具成型表面的温度稳定地保持在所需要的温度范围内,并且要做到使冷却介质在回路系统内流动畅通。
(1)冷却回路尺寸的确定:
A=Mq/3600a(θm+θw)
式中:
A—冷却回路总面积;
M—单位时间内注入墨菊中树脂的质量
C—单位质量树脂在墨菊内释放的热量
q—冷却水的表面传统系数
θm—模具成型表面的温度
θw—冷却水的平均温度
(2)冷却回路总长的确定:
L=100A/πd
式中:
L—冷却回路总长度
A—冷却回路总面积
d—冷却水孔直径
确定冷却水孔直径时应该注意,无论多大的模具,水孔的直径不能大于14毫米,否则冷却水难以成为最佳状态,以至降低交换效率。
一般水空的直径可以根据壁厚来确定。
平均壁厚为2毫米时水孔直径可去8—10毫米。
本墨菊设计中冷却水道直径为d=8mm
(3)冷却水体积流量计算
塑料树脂传给墨菊的热量与自然对流量到空气中的墨菊热量,辐射散发到空气中的墨菊热量以及模具传给注射机热量的差错,即为冷却水扩散的模具热量。
假如塑料树脂在模内释放的热量全部由冷却水传导的话,即忽略其它穿因素,那么模具所需要的冷却水体积流量则可用下式计算。
Qv=Mq/60cpρ(θ1-θ2)
式中:
Qv—冷却水体积流量
M—单位时间没注射模具的树脂质量
q—单位时间内树脂在模具内释放的热量
c—冷却水的比热容
ρ—冷却水的密度
θ1—冷却水出口处温度
Q
—冷却水入口处温度
(4)冷却水管的分布
设置冷却效果良好的冷却回路的模具是缩短成型周期,提高生产效率最有效的方法。
如果不能实现均一的快速冷却,则会使塑件内部产生应力而变形或开裂,随意应根据塑件的形状,壁厚以及塑料品种,设计与制造出能实现均一,高效的冷却回路。
冷却回路设置的基本原则:
①冷却水道应尽量多,截面应尽量大
②冷却水道离模具型腔表面的距离一般为10—15毫米
③水道入口的不止浇口处加强冷却和入口温差尽量小
④冷却水道应沿着塑料收缩的方向
⑤冷却水道的不止应避开容易产生熔接痕的部位
8.2加热系统的设计
由于本模具属于小型模具,所以不需要设置加热装置。
所以本模具采用四个直径为8㎜个冷却水道!
第9章模具的装配
(1)精修定模
①定模经过锻、刨后,磨削4面。
下,上平面留修模余量:
②划线技工型腔。
用铣床铣型腔回用电火花加工型腔。
深度按要求尺寸增加0.2毫米;
③用油石休整膜型腔表面。
(2)精修动模型芯以及动模固定板型孔
①按图纸将预加工的动模芯精修成型,钻铰顶杆孔;
②按划线加工动模固定板型孔,并与型芯配合加工。
(3)同时镗导柱,导套孔
①将定模,动模板固定合在一起,使分型面紧密接触,然后加紧镗削导柱,导套孔;
②括导柱,导套孔的台阶。
(4)复钻各螺孔,销孔以及推杆孔
①定模与定模固定板合在一起,夹紧复钻螺孔,销孔;
②动模固定板,垫板,支撑板,动模板合在一起夹紧,复钻螺孔,销孔。
(5)动模型芯压入动模固定板
①将动模型芯压入固定板并且紧密配合;
②装配后型芯外露部分要求符合图纸要求。
(6)压入导柱、导套
①将导套压入定模;
②将导柱压入动模固定板;
③检验导柱,导套配合的松紧程度。
(7)磨安装基面
①将定模上基面磨平;
②将动模固定板下基面磨平。
(8)复钻推板上的推杆以及顶杆孔
通过动模固定板以及型芯,复钻推杆以及推杆孔。
卸下后再复钻垫板各孔。
(9)将浇口套压入定模板
用压力机将浇口套压入定模板
(10)装配定模部分
定模板,定模复钻螺孔,销孔后,拧入螺钉和敲入销钉紧固
(11)装配动模
将动模固定板,垫板,支撑板,动模板复钻后拧入螺钉,打入销钉固定
(12)修正推杆,复位杆,顶杆长度
将动模部分全部装配后,使支撑板底面和推板金贴与动模板。
自型芯表面测出推杆,顶杆的场地,进行修正
(13)试模与调整
第10章试模
(1)试模前的准备
①领取并对原材料进行检查
②准备好相关的试模资料
③准备好测量设备
④依据模具结构的具体要求,合适的注射机
⑤对模具进行自检
⑥对模具进行预热、清洗料管
(2)试模
1)架模:
①用布擦净工作台与模具上下面
②调整模具的闭合高度
③将定位环进入设备的定位孔内
④快速闭合设备
⑤用压板或螺钉锁紧模具
⑥卸下锁模扣
⑦接上水管并打开开关
2)调模
①进行定循环试验,在手动或半自动状态下检查模具的各运动机构是否顺畅
②对顶出距离进行调节
③清洗模面,避免模面上贴有物体等
④对模具和喷嘴筒进行预热
⑤按预先设定的参数进行成型加工,同时根据产品的状况,确认是否修改参数和如何修改工艺参数,直至生产出合格的产品。
(3)试模后的工作
①检验:
选一模按照产品图进行首件形状和尺寸的检查,对自检不合格的填写报告
②工艺参数的确定。
如检查合格,要将此工艺参数记录。
③试模完后需卸下模具并作保养
④检讨:
试模完后,有设计组里试模人员参加的试模检讨会
把试模中的问题,原因,解决办法写报告
第11章修模
根据试模留下的问题、原因,对模具进行修改。
若产品合格,通知生管出货。
第12章小结
此次(毕业)设计是我在大学期间做的最好最认真的依次作业!
在前面的塑件分析和尺寸计算方面我是结合在校期间所学的专业知识,严格按照所学的公式计算的!
在这里有温故知新的效果,发现以前好多是是而非的问题都有了明确的答案!
让我对塑料模具又有了更好的认识。
由于缺乏很多的社会实践,在设计中肯定会有一些不足之处。
第一次做设计也必然会存在一些问题和错误,再所难免,还希望各个评委能提出指正意见。
能完成这次设计,我很感谢我的指导老师,感谢他们给予的帮助使我认识到了这门专业在社会实践中的重要性,对于他们的大力支持,我表示忠心的感谢,在我做毕业设计时间里,是他们给我讲解了各个部分的加工,使我从中得到很大的启发。
这次毕业设计完成的质量好坏对于我以后的实践工作是一个小的考试吧,要想取得好成绩,只有不断的努力,你学的多,才会用的多,这是老师的一句话,这对我已经有了很深的感触了,所以在我以后的工作中我一定回更加努力的,要对得起所有关心过我的人。
在这次毕业设计中使我受益非浅,相信在以后的工作中会有很大的帮助!
我也会去努力再努力,学习再学习,一达到更好!
第13章参考文献
(1)《塑料成型工艺与模具设计》,作者:
层华昌,出版:
高教育出版社,2001年8月第一版。
(2)《塑料模具设计》,作者:
陈志刚,出版:
机工业出版社。
(3)《注塑成型及模具设计实用手册》,作者:
李海梅、张雨,出版社:
化学工业出版社
(4)《实用注塑模设计手册》,作者:
贾润孔、程志远,出版社:
中国轻业出版社
(5)《墨菊结构图册》,作者:
房金妹、谭平宇、立明,出版社:
机械工业出版社,1992年6月北京第一版
(6)《塑料模具设计》,作者:
刘昌祺,出版社:
机械工业出版社,2000年4月第一版
(7)《型腔模设计》,作者:
李学峰,出版社:
西北工业大学出版社
(8)《公差与配合标准简介》,作者:
国家标准工作组,出版社