30万吨合成氨优化及研究.docx
《30万吨合成氨优化及研究.docx》由会员分享,可在线阅读,更多相关《30万吨合成氨优化及研究.docx(21页珍藏版)》请在冰豆网上搜索。
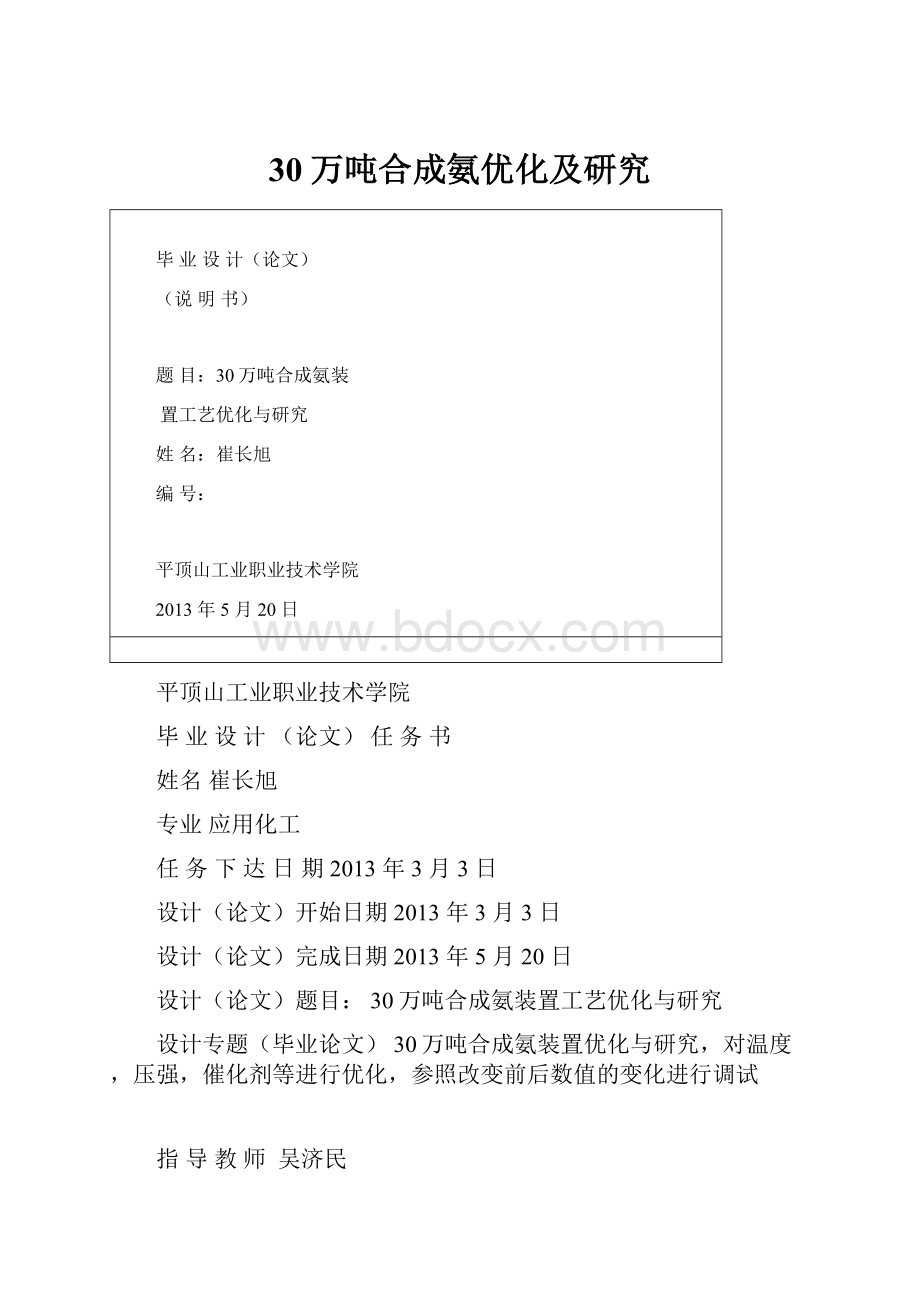
30万吨合成氨优化及研究
毕业设计(论文)
(说明书)
题目:
30万吨合成氨装
置工艺优化与研究
姓名:
崔长旭
编号:
平顶山工业职业技术学院
2013年5月20日
平顶山工业职业技术学院
毕业设计(论文)任务书
姓名崔长旭
专业应用化工
任务下达日期2013年3月3日
设计(论文)开始日期2013年3月3日
设计(论文)完成日期2013年5月20日
设计(论文)题目:
30万吨合成氨装置工艺优化与研究
设计专题(毕业论文)30万吨合成氨装置优化与研究,对温度,压强,催化剂等进行优化,参照改变前后数值的变化进行调试
指导教师吴济民
系(部)主任
2013年5月20日
平顶山工业职业技术学院
毕业设计(论文)答辩委员会记录
化工系应用化工专业,学生崔长旭于2013年5月
进行了毕业设计(论文)答辩。
设计题目:
30万吨合成氨装置工艺优化与研究
专题(论文)题目:
30万吨合成氨装置工艺优化与研究
指导老师:
吴济民
答辩委员会根据学生提交的毕业设计(论文)材料,根据学生答辩情况,经答辩委员会讨论评定,给予学生毕业设计(论文)成绩为。
答辩委员会人,出席人
答辩委员会主任(签字):
答辩委员会副主任(签字):
答辩委员会委员:
,,,
,,,
平顶山工业职业技术学院毕业设计(论文)评语
学生姓名:
崔长旭专业应用化工年级10级毕业设计(论文)题目:
30万吨合成氨装置工艺优化与研究
评阅人:
指导教师:
(签字)年月日
成绩:
系(科)主任:
(签字)年月日
毕业设计(论文)及答辩评语:
30万吨合成氨装置工艺优化与研究
摘要
本文介绍了合成氨生产基本情况以及年产三十万吨合成合成氨系统流程,介绍了一氧化碳变换的基本原理,工艺条件以及工艺参数和变换催化剂的选择原则。
并且对第一和第二变换炉进行热量和能量衡算,对催化剂装填量进行计算,掌握了变换系统的设计方法。
经过实际运行和工艺优化的改进,合成合成氨生产基本情况反应工段中,将反应温度控制在500℃,反应压力20~50MPa的条件下,此时的反应状态为最佳,反应过程中的负荷,对催化剂的影响较小;催化剂再生过程优化后,经济效益良好。
关键词:
变换,催化剂优化,温度的优化,压强的选择
Abstract
Thispaperintroducesthebasicsituationandannualoutputofthreehundredthousandtonsofammoniaproductionofsyntheticammoniasystemprocess,introducesthebasicprincipleofcarbonmonoxideconversion,processconditionsandtheprincipleofchoosingprocessparametersandshiftcatalyst.Andforthefirstandsecondtransformfurnaceheatandenergybalance,thecatalystloadingquantitycalculation,masteredthetransformationdesignmethodofthesystem.Afteractualoperationandimprovementoftheprocessoptimization,basicsituationinthereactionsectioninammoniaproduction,tocontrolthereactiontemperature500℃,20~50mpaundertheconditionsofreactionpressure,reactionconditionisthebestatthistime,intheprocessofreactionload,lesseffectonthecatalyst;Catalystregenerationafterprocessoptimization,economicbenefitisgood.
Keywords:
Conversion,catalyst,processconditions,carbonmonoxidecontent
目录
第一章合成氨的用途3
第二章合成氨的制作4
2.1固体燃料气化法5
2.2重油部分氧化法5
第三章催化剂的选择与优化8
3.1合成氨催化剂的反应机理8
3.2合成氨催化剂的发展9
3.4催化剂的中毒10
四.影响合成氨的因素11
4.1温度对氨合成反应的影响11
4.2压力对氨合成反应的影响14
4.3.空速对氨合成反应的影响15
4.4氢氮比对氨合成反应的影响17
结论20
致谢20
参考文献21
第一章合成氨的用途
合成氨是化学工业中产量最大的产品之一,是化肥工业和其他化工产品的主要原料。
现约有80%的合成氨用于制造化学肥料,除合成氨本身可用作化肥外,可以加工成各种氮肥和含氮复合肥料如尿素、硫酸铵、氯化铵、硝酸铵、磷酸铵等。
可以生产硝酸、纯碱含氮无机盐等。
合成氨还被广泛用于有机化工、制药工业、化纤和塑料工业以及国防工业中。
因此合成氨在国民经济中占有重要地位。
目前合成氨是由氮气和氢气在高温、高压和催化剂作用下直接合成而得。
除电解法外,不管用何种原料制得的粗原料气中都含有硫化物、一氧化碳、二氧化碳。
这些物质都是合成氨合成催化剂的毒物在进行合成之前,需将其彻底清除。
因此,合成合成氨的生产过程包括以下三个主要步骤。
原料气的制取,制备含有氢气、一氧化碳、氮气的粗原料气。
原料气的净化,指除去原料气中氢气、氮气以外的杂质一般由原料气的脱硫,一氧化碳的变换,二氧化碳的脱除,原料气的精炼等组成。
原料气压缩与合成,将符合要求的氢氮混合气压缩到一定的压力,在铁催化剂与高温条件下合成为合成氨。
第二章合成氨的制作
目前,合成氨生产原料按状态分主要有固体原料。
如:
焦炭和煤气体原料.如天然气、油田气、焦炉气、石油废气、有机合成废气。
液体原料:
如石脑油、重油等。
生产方法主要有固体燃料气化法,煤或焦炭,烃类蒸汽转化法,气态烃、石脑油、重油部分氧化法、重油。
2.1固体燃料气化法
固体燃料气化过程是以煤或焦炭为原料在一定的高温条件下通入空气、水蒸气或富氧空气-水蒸气混合气经过一系列反应生成含有一氧化碳、二氧化碳、氢气、氮气及甲烷等混合气体的过程。
在气化过程中所使用的空气、水蒸气或富氧空气-水蒸气混合气等称为气化剂。
这种生成的混合气体称为煤气。
用于实现气化过程的设备称为煤气发生炉。
煤或焦炭气化因采用不同的气化剂可以生产出下列几种不同用途的工业煤气
①空气煤气。
以空气作为气化剂所制得的煤气。
按体积分数计,其中约有50%的N2一定量的CO及少量的CO2和H2。
②水煤气。
以水蒸气作为气化剂所制得的煤气。
按体积分数计,其中H2和CO的含量约85%以上。
③混合煤气。
以空气和适量水蒸气的混合物作气化剂所制得的煤气。
按体积分数计,CO+H2与N2的比为1.43。
④半水煤气。
分别以空气和水蒸气作气化剂,然后将分别制得的空气煤气和水煤气两者按混合后气体中,CO+H2与N2的摩尔比为3.1~3.2的比例进行掺配,这种混合煤气称为半水煤气。
也可以直接控制气化剂——空气-水蒸气二者的流量来制取半水煤气,用作合成氨的专用原料气。
目前,工业上固体燃料为原料制取合成氨原料气的方法根据气化方式不同,主要有固定床间歇气化法、固定床连续气化法、沸腾床连续气化法和气流床连续气化法。
2.2重油部分氧化法
重油是350℃以上馏程的石油炼制产品。
根据炼制方法不同分为常压重油、减压重油、裂化重油。
重油的化学组成与物理性质有差别但均以烷烃、环烷烃和芳香烃为主其虚拟分子式可写成CmHn。
除碳、氢以外重油中还有硫、氧、氮等组分若将硫计入,可写为CmHnSr。
此外,还有微量的钠Na、镁Mg、钒V。
镍Ni、铁Fe和硅Si等。
重油部分氧化是指重质烃类和氧气进行部分燃烧,由于反应放出的热量,使部分碳氢化合物发生热裂解及裂解产物的转化反应,最终获得以H2和CO为主要组分,并含有少量CO2和CH4、CH4通常在0.5以下的合成气。
重油部分氧化化学反应,如果氧量充足,则会发生完全燃烧反应:
如果氧量低于完全氧化理论量,则发生部分氧化,放热量少于完全燃烧反应式为:
当油与氧混合不均匀时,或油滴过大时,处于高温的油会发生烃类热裂解反应较复杂这些副反应最终会导致结焦。
所以,渣油部分氧化过程中总是有炭黑生成。
为了降低炭黑和甲烷的生成,以提高原料油的利用率和合成气产率,—般要向反应系统添加水蒸气,因此在渣油部分氧化的同时,还有烃类的水蒸气转化以及焦炭的气化,生成更多的CO和H2。
氧化反应放出的热量正好提供给吸热的转化和气化反应。
渣油中含有的硫、氮等有机化合物反应后生成H2S、NH3、HCN、COS等少量副产物。
最终生成的水煤气中四种主组分CO、H2O、H2、CO2之间存在的平衡关系要由变换反应平衡来决定。
工艺流程:
重油部分氧化法制取合成气CO+H2的工艺流程由四个部分组成原料重油和气化剂、氧和蒸汽的预热,重油的气化,出口高温合成气的热能回收炭黑清除与回收。
主要按照热能回收方式的不同,分为德士古Texaco公司开发的激冷工艺与谢尔shell公司开发的废热锅炉工艺。
这两种工艺的基本流程相同。
只是在操作压力和热能回收方式上有所不同。
图3-4为典型的德士古重油部分氧化激冷工艺流程。
原料重油及由空气分离装置来的氧气与水蒸气经预热后进入气化炉燃烧室油通过喷嘴雾化后,在燃烧室发生剧烈反应,产物气经水洗塔得到合成气。
激冷流程具有以下特点工艺流程简单,无废热锅炉,设备紧凑,操作方便,热能利用完全,可比废热锅炉流程在更高的压力下气化。
不足之处是高温热能未能产生高压蒸汽。
此流程若采用高变催化剂,则要求原料油含硫量低一般规定S1,否则需用耐硫变换催化剂。
图3-5为典型的谢尔重油部分氧化废热锅炉工艺
原料重油经高压油泵提压后压力升至6.9MPa,预热至260℃左右与预热后的氧气和高压过热蒸汽混合,约310℃的混合气进入喷嘴,进入气化炉进行气化反应生成含,CO+H2,90~92的合成气。
从气化炉出来的高温气体进入火管式废热锅炉回收热量后,温度由1300℃降至350℃,通过炭黑捕集器、洗涤塔将大部分炭黑洗涤和回收后离开气化工序去脱硫装置。
废热锅炉壳程产出10.5MPa蒸汽废热锅炉流程具有以下特点,利用高温热能产出高压蒸汽,使用比较方便灵活,特别是喷嘴所需要的高压蒸汽缺乏汽源时,采用废锅流程自供蒸汽就更为有利,对原料重油含硫量无限制,下游工序可采取先脱硫、后变换的流程。
不足之处是废热锅炉结构复杂,材料及制作要求高,目前工业上气化压力限于6MPa以下。
第三章催化剂的选择与优化
3.1合成氨催化剂的反应机理
热力学计算表明,低温、高压对合成氨反应是有利的,但无催化剂时,反应的活化能很高,反应几乎不发生。
当采用铁催化剂时,由于改变了反应历程,降低了反应的活化能,使反应以显著的速率进行。
目前认为,合成氨反应的一种可能机理,首先是氮分子在铁催化剂表面上进行化学吸附,使氮原子间的化学键减弱。
接着是化学吸附的氢原子不断地跟表面上的氮分子作用,在催化剂表面上逐步生成—NH、—NH2和NH3,最后氨分子在表面上脱吸而生成气态的氨。
上述反应途径可简单地表示为:
xFe+N2→FexN
FexN+[H]吸→FexNH
FexNH+[H]吸→FexNH2
FexNH2+[H]吸FexNH3xFe+NH3
在无催化剂时,氨的合成反应的活化能很高,大约335kJ/mol。
加入铁催化剂后,反应以生成氮化物和氮氢化物两个阶段进行。
第一阶段的反应活化能为126kJ/mol~167kJ/mol,第二阶段的反应活化能为13kJ/mol。
由于反应途径的改变(生成不稳定的中间化合物),降低了反应的活化能,因而反应速率加快了。
合成氨铁催化剂以来,铁催化剂在氨合成中的应用就越来越广泛。
该催化剂具有价格低廉、稳定性好等特点,一般采用熔融法制备,以磁铁矿和铁为主要原料,添加各类助剂化合物,经电阻炉熔炼后,再冷却、破碎筛分成不同颗粒的铁催化剂。
研究表明,最好的熔铁催化剂应该只有一种铁氧化物(单相性原理)任何两种铁氧化物的混杂都会降低催化活性,而铁氧化物氨合成的活性次序为:
Fe1-XO>Fe3O4>Fe2O3>混合氧化物[1]。
实际应用中,由于铁催化剂起活温度比较高,大型氨厂通常400℃~500℃和20.0MPa~30.0MPa的条件下使用,在氨合成生产过程中,对设备的要求也比较苛刻,能耗巨大。
而压力的降低,不仅可降低压缩气体能耗,还可采用廉价易得的机械和设备,使投资和操作费用降低。
因此,开发在低温和较低压力下仍具有较高活性的新型氨合成催化剂,就成为合成氨催化剂研究的关键。
目前研究开发的氨合成钌(Ru)基催化剂,由于在低温低压等温和的条件下具有较高的活性,被誉为第二代氨合成催化剂。
3.2合成氨催化剂的发展
1979年美国Kellogg公司与英国石油公司成立新合成氨工艺联合开发委员会1989年宣告第一个以非铁氨合成催化剂为基础的氨合成工艺完成了3t/d的示范工程能在低压、低温条件下合成氨生产能力最多可增加40%。
这一工艺称为KAAP(kellggadvancedammoniaprocess)工艺其核心是高效的、经过特殊处理的石墨为载体的钌催化剂活性是传统催化剂10到20倍;且在低压、低温下使用能保持高活性同时可以在较宽的氢氮比下操作最佳氢氮比要比使用传统铁催化剂的最佳值低。
1992年11月在加拿大的奥西罗合成氨厂,实现工业化生产不但生产能力提高40%而且节能十分显著。
非铁氨合成催化剂的开发成功是合成氨工艺的一个重大进步它对合成氨工业降低成本、降低能耗有着十分重大的突破性进展。
钌基催化剂堪称为第二代合成氨催化剂最近国内外有关这方面的报道很多。
研究开发钌基催化剂及其他非铁系催化剂是氨合成催化剂的一个发展方向但是也必须看到金属钌是非常稀有的贵金属,因此要全面推广使用钌基催化剂还有一段很长的路要走.
工业上应用较广的大型氨合成流程是15MPa以上合成压力的升压氨合成流程。
这一流程的优点是因为合成压力较高未反应物循环能耗较小也便于氨的分离。
而当前国外合成氨的发展趋势是制气压力逐步升高合成压力逐步降低其发展方向是实现等压氨合成即合成与制气在接近相等的压力下进行,从而省去功率很大的合成气压缩机以降低能耗并简化流程。
近年来,由于新型低温低压氨合成催化剂的开发与合成塔、氨分离技术的不断改进实现等压氨合成已成为可能。
朱继承等对升压氨合成与等压氨合成流程进行了比较并对等压流程进行了模拟与优化发现715MPa等压氨合成回路流程在操作能耗上远优于15MPa的升压流程。
可见开发能在等压流程中使用的低温低压氨合成催化剂将会是一个很好的发展方向,
3.4催化剂的中毒
催化剂的催化能力一般称为催化活性。
有人认为:
由于催化剂在反应前后的化学性质和质量不变,一旦制成一批催化剂之后,便可以永远使用下去。
实际上许多催化剂在使用过程中,其活性从小到大,逐渐达到正常水平,这就是催化剂的成熟期。
接着,催化剂活性在一段时间里保持稳定,然后再下降,一直到衰老而不能再使用。
活性保持稳定的时间即为催化剂的寿命,其长短因催化剂的制备方法和使用条件而异。
催化剂在稳定活性期间,往往因接触少量的杂质而使活性明显下降甚至被破坏,这种现象称为催化剂的中毒。
一般认为是由于催化剂表面的活性中心被杂质占据而引起中毒。
中毒分为暂时性中毒和永久性中毒两种。
例如,对于合成氨反应中的铁催化剂,O2、CO、CO2和水蒸气等都能使催化剂中毒。
但利用纯净的氢、氮混合气体通过中毒的催化剂时,催化剂的活性又能恢复,因此这种中毒是暂时性中毒。
相反,含P、S、As的化合物则可使铁催化剂永久性中毒。
催化剂中毒后,往往完全失去活性,这时即使再用纯净的氢、氮混合气体处理,活性也很难恢复。
催化剂中毒会严重影响生产的正常进行。
工业上为了防止催化剂中毒,要把反应物原料加以净化,以除去毒物,这样就要增加设备,提高成本。
因此,研制具有较强抗毒能力的新型催化剂,是一个重要的课题。
四.影响合成氨的因素
4.1温度对氨合成反应的影响
氨合成反应是一个可逆放热反应,所以降低反应温度有利于平衡向生成氨的方向进行。
但反应速度则随温度降低而减慢。
同时氨合成反应使用活性催化剂,所以反应温度的选择要首先考虑到适合催化剂的活性温度范围,一般在380—525℃之间。
另外,对于可逆反应,对于一定的反应物系组成具有最大总反应速度的温度称之为对应于该组成的最适宜温度,因此对应整个合成塔的反应过程存在着一条最适温度,因此对应整个合成塔的反应过程存在着一条最适温度线。
最适温度随着反应的进行而不断降低。
为此,对氨合成这一放热反应,在反应同事采取不同手段及时移走反应热,使反应温度尽可能接近最适温度线,以达到较好的技术、经济效益。
实际生产中,一般是控制出没床入口温度略高于触媒的活性其实温度,最高温度不超过催化剂的耐热温度,触媒使用的前期略低一些,以防触媒过早老化,而在后期则依据提温利用等高温活性。
当反应温度升高时,平衡向着氨的分解方向移动;温度降低反应向着氨的生成方向移动。
因此,从平衡观点来看,要使氨的平衡产率高,应该采取较低的反应温度。
但是从化学反应速度的观点来看,提高温度总能使反应的速度加快,这是因为温度升高分子的运动加快,分子间碰撞的机率增加,同时又使化合时分子克服阻力的能力加大,从而增加分子有效结合的机率.
总之,温度低时,反应有利于向合成氨的方向进行,但是氨合成的反应速度较低;提高温度不利于向氨的合成方向移动,但反应速度可以增加。
在实际生产中反应温度的选择主要决定于氨合成催化剂的性能变化反应是可逆放热反应。
从反应动力学的角度来看,温度升高,反应速率常数增大对反应速率有利,但平衡常数随温度的升高而变小,即CO平衡含量增大,反应推动力变小,对反应速率不利,可见温度对两者的影响是相反的。
因而存在着最佳反应温对一定催化剂及气相组成,从动力学角度推导的计算式为Tm=1212ln1EEEERTTee−+式中Tm、Te—分别为最佳反应温度及平衡温度,最佳反应温度随系统组成和催化剂的不同而变化。
依据合成产量=入塔气量Q*氨净值来看,要保证同样产量的前提下,空速和净值必须有一个最佳的配备,在空速不变的情况下,最大限度地提度高氨净值就能有效提高产能。
怎样提高:
让合成塔按最适宜的温度曲线分布移出反应的热量。
合成塔温度分布都应该遵循先涨后降的曲线,因为气体刚进入合成塔时,氨含量较低(≤3%),距离平衡很远,必须迅速进行反应以提高氨含量,所以提高上层温度就能加快反应速度;相反,当进入下层后,由于气体氨含量较高,为抑制逆反应的速度,必须适当降低操作温度,以达到较高的出口氨含量,提高氨净值,进而提高产量。
所以我们平时操作时必须控制好合成塔各层的温度,各段温度相差10℃左右(从上到下递降),让整个合成塔内温度分布达到理想要求。
另外要保证合成氨冷器出口温度在正常指标范围内,确保气氨的有效冷凝和分离。
在400-440℃操作范围内,计算了合成氨温度对氨含量的影响,由表1反应温度和合成氨浓度的影响显示。
表1温度和合成氨浓度的影响
温度/℃
400
410
420
430
440
氨产量/mol%
24.15
22.83
21.85
20.69
19.51
由表1的结果说明,随着温度的升高,合成氨浓度逐渐降低,主要是因为氨合成过程是放热过程,升高温度对反应热力学平衡不利。
在400-460℃的操作范围内,计算反应温度对氨产量的影响,结果见表2.
表2温度对氨产量的影响
温度/℃
400
410
420
430
440
450
460
氨产量/kg/h
49564
49390
49247
49141
48980
48782
48568
从表2可以看出,随着温度的升高,氨产量随之降低。
这主要是因为温度升高后,合成塔出口气循环比例不变的情况下,驰放气的量相对增大,原料的有效利用率下降。
达到平衡时混合气中氨的含量(体积百分含量)
氮气和氢气的体积比1:
3
压强
氨含量
温度
0.1MPa
10MPa
20MPa
30MPa
200℃
15.3
81.5
86.4
89.9
300℃
2.2
52.0
64.2
71.0
400℃
0.4
25.1
38.2
47.0
500℃
0.1
10.6
19.1
24.4
600℃
0.05
4.5
9.1
13.8
升温氨的含量降低/升压氨的含量增大
4.2压力对氨合成反应的影响
氨的合成反应是一个分子的氮与三个分子的氢结合生成两个分子的氨,即氨合成反应是分子数目减少、体积缩小的反应,提高压力,可使反应向着生成氨的方向进行。
对于氨合成反应来说,提高压力就是提高反应气体的浓度,从而增加反应分子间碰撞的机会,加快了反应的速率。
总之,增加压力对氨的合成反应是有利的,既能增大平衡转化率,又能加快反应速率。
但压力也不宜过高,否则,不仅增加动力的消耗,而且对设备和材料的要求也较高。
根据我国具体情况,目前在小型合成氨厂,设计压力一般为31.4MPa.
压力对变换反应的平衡几乎没有影响。
但是提高压力将使析炭和生成甲烷等副反应易于进行。
单就平衡而言,加压并无好处。
但从动力学角度,加压可提高反应速率。
从能量消耗上看,加压也是有利。
由于干原料气摩尔数小于干变换气的摩尔数,所以,先压缩原料气后再进行变换的能耗,比常压变换再进行压缩的能耗底。
具体操作压力的数值,应根据中小型氨厂的特点,特别是工艺蒸汽的压力及压缩机投各段压力的合理配置而定。
一般小型氨厂操作压力为0.7-1.2MPa,中型氨厂为1.2~1.8Mpa。
本设计的原料气由小型合成氨厂天然气蒸汽转化而来,故压力可取1.7MPa.
压力也常被我们用来考量能耗不过有研究表明压力对能耗的影响很小,合成氨能量消耗主要包括原料气压缩功、循环气压缩功和氨分离冷冻功,提高操作压力,原料气压缩功增加,循环气压缩功和氨分离功却减少。
总能耗在15-30MPa区间相差不大且数值较小。
压力过高则原料气压缩功太大压力过低则循环气压缩功、氨分离冷冻功又太高。
生产实践证明,操作压力在20-30MPa时总能量消耗比较低。
压力MPa
温度
温度
温度
温度
温度
温度
温度
-20
-10
0
10
20
30
40
15.99
2.15
3.14
4.46
6.19
8.39
11.13
14.61
30.398
1.53
2