英文翻译.docx
《英文翻译.docx》由会员分享,可在线阅读,更多相关《英文翻译.docx(27页珍藏版)》请在冰豆网上搜索。
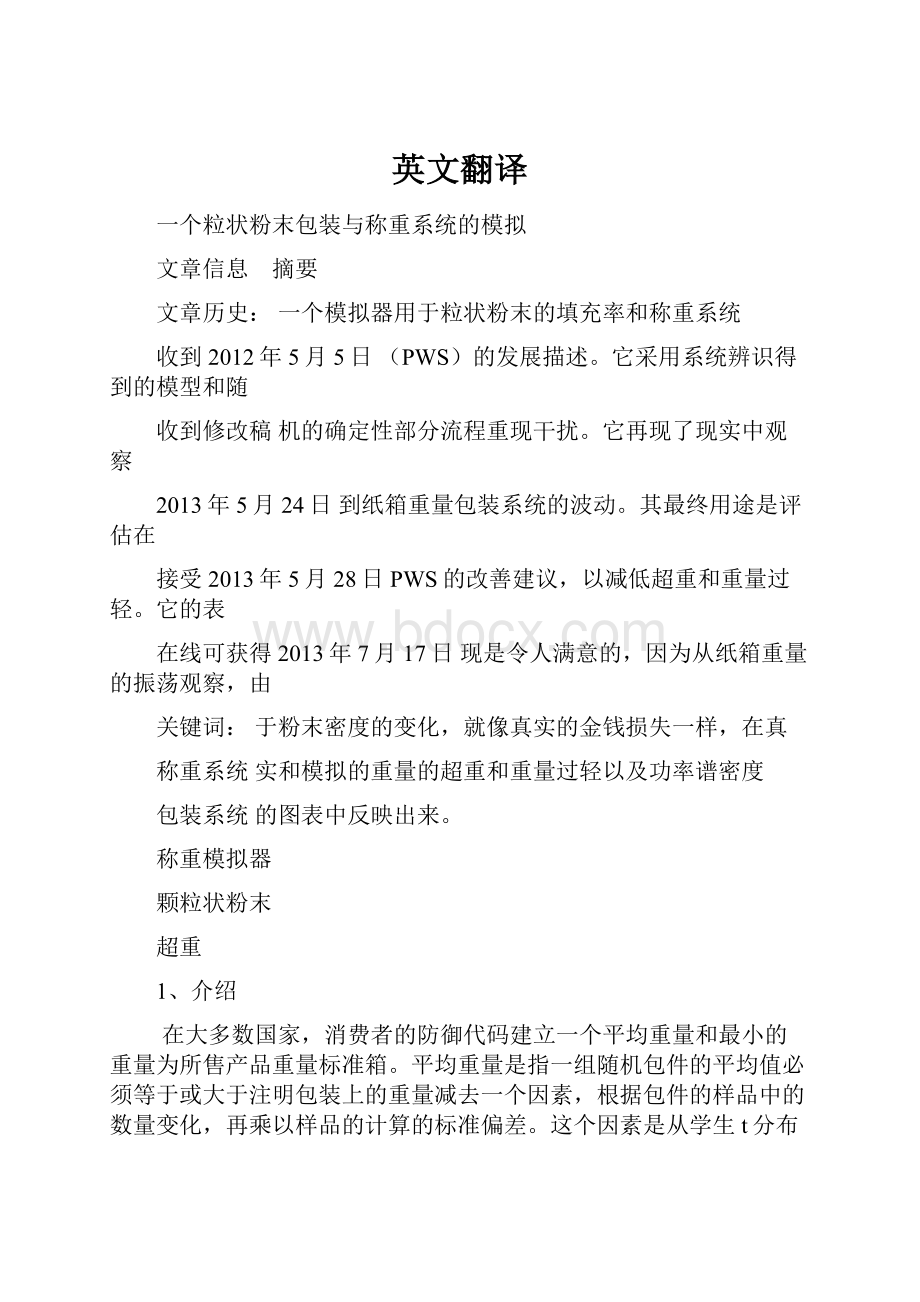
英文翻译
一个粒状粉末包装与称重系统的模拟
文章信息摘要
文章历史:
一个模拟器用于粒状粉末的填充率和称重系统
收到2012年5月5日(PWS)的发展描述。
它采用系统辨识得到的模型和随
收到修改稿机的确定性部分流程重现干扰。
它再现了现实中观察
2013年5月24日到纸箱重量包装系统的波动。
其最终用途是评估在
接受2013年5月28日PWS的改善建议,以减低超重和重量过轻。
它的表
在线可获得2013年7月17日现是令人满意的,因为从纸箱重量的振荡观察,由
关键词:
于粉末密度的变化,就像真实的金钱损失一样,在真
称重系统实和模拟的重量的超重和重量过轻以及功率谱密度
包装系统的图表中反映出来。
称重模拟器
颗粒状粉末
超重
1、介绍
在大多数国家,消费者的防御代码建立一个平均重量和最小的重量为所售产品重量标准箱。
平均重量是指一组随机包件的平均值必须等于或大于注明包装上的重量减去一个因素,根据包件的样品中的数量变化,再乘以样品的计算的标准偏差。
这个因素是从学生t分布来获得,考虑到的概率为99.5%的假设检验。
最小重量意味着没有包件的重量可以小于98.5%标准重量或1千克包重。
在这项工作中,假定包超重,也就是说,重量大于注明净重,不由称重系统拒绝并提供给客户。
在另一方面,封装体重过轻(称为作废料),即与重量比最小的重量还小,是要报废的。
在这种情况下,该粉末被手动发送回包装系统并且包本身被丢弃。
因此,无论过轻还是超重的纸箱对洗衣粉生产厂家都意味着金钱损失。
在实践中损失的最小化是一项艰巨的任务去完成。
这里考虑的体积称重系统,通过填满包材料的体积变化力求保证纸箱重量在所要求的值。
由于材料的密度沿时间随机变化(密度
变化)。
因此,有了一个开发模拟器的想法,能够表示粉末洗涤剂密度的变化以及模拟实际过程中的干扰,对PWS系统及其相关不确定性和称重控制系统是一个非常合理的解决方案。
本文的结构如下:
在第2节提出这项工作的目标和贡献。
在第3节有一个对PWS的描述洗衣粉。
在第4节模拟器提出效仿PWS进行说明。
第5节为模拟器开发的模型进行验证。
在第6节得出结论。
2、这项工作的目的和贡献
在对相关文件进行搜索时,并没有找到既不是一篇描述一个模拟器称重和包装类似的粒状材料也没有任何的系统建模与仿真呈现在这里。
出于这个原因,没有提到参照其它模拟器,这里提出所有的建模和仿真PWS的想法都是由作者创建的。
这个创意性是本文的新颖处。
这项工作的主要贡献有:
作为变化的原因是未知的,用统计的方法来模拟它,实现了一个模型,当与实际情况相比时它提供了精确的模拟结果。
这种形式的建模避免深入研究的可变性,否则这将是非常耗时的,甚至是不可能的;
●模拟器在工业上的应用在过去的几十年一直在增长,一般来说是为了避免不必要的资金
投入去完善这个过程[1],但并非旨在减少由最终产品的过重和过轻包装引起的过程成本。
在这样的问题中,有许多影响变量,通常改变的花费是非常昂贵,只能通过提高利润而不是通过增加产量。
为了工业应用一个创新的方法被提出了,通过一个模拟器将金钱损失量化与纸箱的超重和过轻联系一起,当在PWS中执行修改时,从而使制造商基于成本与效益(低风险投资)来决定是否实施这些,这是工作的主要目的。
●大多数公司包装颗粒状粉末使用相同的系统而超重加下脚料是其中的主要损失,即占总
销售额的0.5-3%的范围内。
在现场,这项工作被执行后,能实现每年节省120万美元。
据评估,在巴西粉末洗涤剂市场,大约有160万的消费者,总损失达到每年2000万美元。
这样的潜在损失减少仍然是比较大的,如果这种观念被应用到这里或另一种颗粒和非颗粒产品,如作为零食和食物。
因此,建立颗粒粉末PWS模型体现了这种工业的强大经济实力。
PWS的描述
在生产场地,一个大的区域被称为“料车楼”,是一个制造材料转移到车(车)里的地方,将货物不断倒入筒仓。
该系统的概述,如图1所示。
从筒仓,该材料被卸入包装机里,其中有9瓶,如见于图2,在那里材料被排出,并
在被包装前进行剂量体积。
作为填充头继续旋转,该瓶的一部分被填满,通过在其顶部粉末沉积,而另一部分被清空,通过一个突然的开口底盖。
每个瓶的容积大约为2L。
作为粉末洗衣粉具有的预期平均密度为500g/L,整个瓶含有大约1千克洗衣粉,是每
个包中所期望的重量。
瓶的总高度是由称重控制系统改变的,从而改变它们的体积。
灌装头仍然有一个刮板,以确保所有的瓶的顶部有一个均匀平整的粉末表面。
检重秤是一个设备以极快的速度(每秒3包)来衡量纸箱的重量,并将数据发送到重量控制器。
在完全充满的瓶子和检重秤之间还有28个纸箱。
在图1中,装填与纸箱称重之间所引起的一个延迟距离是可以被观察到。
为了调节重量,控制器发送一个脉冲命令到交流电动机来调整高度和每个瓶的容量,试图弥补洗衣粉密度变化。
在包装和称重控制系统中存在的主要问题分别是:
在灌装头和检测称重之间引起一个传输延迟,在控制回路引起一个时间延迟
较大的粉末密度扰动
除此之外,在系统中存在其它问题如检重的不准确性和瓶子高度的变化。
为了研究这些影响,在PSW中提出了改进,开发了动态模拟器,如下面描述。
它能评估工厂改造和称重控制系统调整的影响,目的是减少超重及废料。
图一包装系统概述。
图二灌装头的部分设计
4、模拟器说明
对粉末材料在包装机上存在的超重及废料是一个问题。
虽然这项工作专注于粉末洗涤剂制造商的事情,但是对颗粒粉末材料模拟器可以适用于任何种类的包装和称重机器。
确定性和随机部分的过程是被分开的。
确定性部分的造型很简单,采用基本的系统识别技术。
在另一方面,对过程的变化性与图形重量变化模型进行了深入分析,低频率和高频率的存在在振荡中被检测到,些波的统计特性被评价,并将这种干扰纳入模拟器中,在纸箱重量上产生振荡是和实际系统密切相关的。
如第13章[4]节中,“但是模型扰动仅仅是可以从第一原则被确定的。
实验往往是能得到骚乱模型的唯一途径”。
所以,这意味着可能很难从它的物理或化学现象确定扰动模型,而通常唯一途径是从实验收集数据。
在这项工作什么方法能更好推导出扰动模型,既不是从基本原理,也不是直接从实验,而是基于在过程输出特性中的观察。
4.1、系统模型
该系统模型的框图如图3所示。
它由下列部分组成:
填充头,所述粉末洗涤剂密度发生器,规模(检重秤)和重量控制器。
与传统闭环控制回路比较图3中的元素,可以在它们之间画出一个平行线:
在填充头相对应的过程中,粉末洗涤剂密度产生对应的扰动,检重对应于反馈组件和配重控制器回路调节器。
图3中的每个块都被进行了说明。
要注意的是这是一种重要的混合动力系统[5]该过程具有持续时间部分(电机和控制器)和离散的时间部分(自动检重秤,灌装头和干扰)。
在工业应用这是一个正常的情况。
4.2、灌装头模型
从理论上说,对于相同的密度和相同的刮具的高度,瓶子应该提供相同的重量,但它除被验证外,还通过在灌装头及纸箱的分析测量称重,由于他们之中的物理差异它不会发生。
这些差异的出现,是因为瓶相对于刮板不具有相同的相对位置;其它换言之,它们不完全一致。
此外,在装配中由于轴弯曲存在物理差异的问题,还有盖子与陈腐插头,等等。
这也是创建一个小的高度差异的原因烧,因此,不同量之间的粉末,每个可存储。
观察到的另一事实是,在对瓶的直径进行测定时,他们之间的差异是如此之小,他们肯定会被忽视的,因为它们造成的重量比的差异不大于至0.1g。
因为每个烧瓶中的平均直径是D瓶=0.1256米和设计粉末密度为500克/升,身高每毫米差,有一个平均的7.5克重量差异的。
那不同的是相同的每个烧瓶中,也就是说,在每个烧瓶中它的量是一个周期性变化的。
测试完成了对每个瓶的重量差异的量化。
对于本试验中,171个纸箱被编号和整理的包装和称重机。
在试验期间,将烧瓶保持与一个约2升体积不变,这意味着该控制器被禁用。
这些包,在检重秤上被称重后,采取了关闭生产线,而且称重精密刻度为0.05g精确度。
在此之后,平均体重为每组9烧瓶进行了计算,使用测量经精密制造规模,产生19平均权重值,如见于式
(1)。
然后,计算每个瓶的重量差,每组9取精确的测量之间的差重量(1的各烧瓶中,平均重量的完整旋转)为19的手段,如式2)。
在这之后,计算每个瓶中的重量差的算术平均值,如在方程给出式(3)。
每个瓶中它产生的九种平均体重的差异。
得到的结果如表1。
由瓶释放的重量的标准偏差通过μweight的先前值估计;dif(i),i=1to9,结果是:
sflasks=5.65克。
图4显示了考虑或不考虑瓶的重量变化的差异。
不过,由称重控制器发送命令同时影响九瓶的平均高度。
为了对瓶间这些小的差别进行建模,有必要要转换高度差引起的重量差异,如方程4所述。
µ高度,dif(i)=
(4)
表1烧瓶中平均体重差异
图4、使用和不使用瓶重量变化的比较图
平均密度值被假定为μ密度=500克/升,从1千克/2L中提取和瓶子的平均面积是A瓶=0.01239平方米。
因此,一个恒定值被添加到各瓶的高度上,以模拟其中真实的高度差,那就是,μ高;差离值(i),i=1to9
此外,考虑该瓶高度σ瓶的标准偏差和其余的短期标准偏差(每九个纸箱)纸箱的重量是由其它五个随机的和变量:
局部噪声密度(在4.4节计算),由自动检重秤带来的噪声(第4.3节计算),由施加到纸箱襟翼的涂胶量变化带来的噪声,由空纸箱重量和非均匀填充过程带来的噪音,最后三个在这段被评估。
为了确定空箱的重量变化,编号100个空纸箱在精密称重秤前被精确测量。
根据得到的值,标准偏差计算如下:
σ空箱=0.1克
把大量编号相同不含洗涤剂的空纸箱插入包装和称重机上,以至于他们没有粘结在一起。
然后他们被精确称重,纸箱加胶水重被单独减去空箱重量。
计算重量差值的标准差为:
Σ胶水=0.2克
标准偏差s空箱和s胶水被忽视,因为它们的值比s瓶小得多以及局部密度的标准偏差。
这些变量的所有平均值也都被忽视,因为它们可以由自动检重秤的偏移量的补偿来调整。
此外,还有一个来自瓶的随机变化,那就是不均匀的填充结果。
这是因为刮板的设计使来自筒仓的粉末去填补瓶子因瓶中的空气被赶出来,所以没有一点缝隙。
因此,情况是,空气被赶出与对瓶灌粉的方向相反,于是产生了震动和非均匀填充。
有时,也可以清楚地看到某些气泡从瓶中上来,同时粉末灌装它们。
一项实验被进行以确定这种变化。
一千个纸箱在正常刮板和烧瓶的条件下固定为2L运行在机器上,另外1000个新的纸箱在相同的条件下进行(包括同一洗衣粉)除刮板,将其改变为消除这种空气现象,使得空气从烧瓶中的二分之一的顶部被释放然后另一半由粉末充满。
比较两个短期变化结果,测试结果表明,标准偏差由于非均匀填充s填=1.1克而对应于高斯分布。
因此,该模型被分成两部分:
确定性和随机的。
如前面所述由于其中的差异,确定性部分的每个瓶加上或减去一个来自预期重量的恒定值。
执行的计算示见于式(5):
重量=
(5)
其中:
由称重控制器所确定的瓶高度等于瓶的高度
密度等于洗衣粉密度生成器确定的值,在第4.4节描述。
灌装头模型的确定性部分被划分分为九个模块,分别模拟每个烧瓶。
输入到每个模块是:
粉末洗涤剂浓度由洗衣粉密度发生器所产生,如4.4节中描述;烧瓶高度由称重控制器控制,
如4.5节中描述。
每个模块的输出等于每个烧瓶释放的重量。
该模型的随机部分,对应于所述每个烧瓶中随机变化解放出来的重量,增加白高斯噪声
到先前计算的重量中。
这种噪声的平均值是零和标准偏差σ装。
填充头模型的块示意图如图5。
图5灌装头模型的框图。
4.3、检重秤模型
检重秤过去常常是一个称量纸箱重的工具。
这里有两个因素影响其称量:
码间干扰[6],用在通讯中的一个专有名词和测量(动态和静态)的不精确性。
这两个因素被动态称重严重
影响。
前者是由于重量传感器的电压输出暂时的行为产生的。
图6所示,检重秤在两种截然不同的情况下的电压输出情况:
遥远的纸箱(上图),纸箱的快速序列(下图)。
它可以很容易地注意到,在图6的下部没有足够的稳定时间,因此,一个测量的结果影响到下一个,代表一个码间干扰。
图6检重秤的输出电压图7检重秤的不精确性
图8输入信号的标准自动校正图9检重秤模型的框图。
该电压峰值越高,越会影响到下一个纸箱重量,结果导致下一个峰值较低。
系统识别技术应用于描述这样的影响,由于下一个再讨论。
第二个作用是由于以下原因:
称重传感器电路的电压噪声,机械部件的振动,移动箱的垂直振荡,从而导致由传感器产生振荡张力曲线和相对于带运动的纸箱有点歪斜。
这些原因在图7中可以看出。
在第4.2节中所用的相同的数据集,相对于上述测试用的171个纸箱,还用在这里。
在这种情况下,输入信号是对应于精密刻度测量的重量且输出信号是检重测定的重量。
输入信号的自动校正被计算且值得注意的是这不是白色噪声。
因此,这是不可能的确定一个动态传递函数通过输入和输出之间的相关性。
标准自动校正如图8。
正如在第4.2节中所述,检重秤模型被划分为两部分:
确定性和随机性。
为了定义确定的部分,码间干扰的建模以下列方式:
(6)
其中,y(k)为码间干扰模块的输出,u(k)为输入(精确的权重值),考虑到对应于衡量一纸箱的平均时间的采样时间,其中有一个28个纸箱的延迟。
转化公式如式(6),z的值域如(7),所得到的离散传递函数是:
(7)
为了表征该模型的随机部分,噪声影响趋向图7中显示的干扰,因此,下面的模型提出:
(8)
其中,w(k)是检重模块的输出,e(k)是的噪音。
检重秤模型的框图如图9。
要确定方程(8)的参数,Matlab系统辨识工具箱的函数OE(输出错误),它采用最小二乘估计。
该函数在系统中设置的方程比未知数还多(这种情况下有171个方程和两个未知数)。
通过最小化平均平方误差,它提供传递函数的系数值。
这样,每一个噪声都消失在码间干扰模块的输出中(不精确的比例)。
该参数的值是:
b=1.0202
正如期望“a”为接近零的值,“b”为接近1的值,但不可能简单地忽略传递函数,因为其影响是在本系统中的可变范围内。
图10表示由检重器供给的重量和重量y(k)在传递函数的输出,在测试过程中开始生成从配合精密刻度测量的输入数据。
可以注意到的是,结果的不同是由于测量的不精确性(噪声),当函数OE被使用时它消失了,因为建模过程唯一考虑到的是信号的相关部分。
为了确定噪声(不精确性),传递函数的输出值生成了相同的171个输入数据。
然后,传递函数的输出值从检重秤的测量值中被减去(W(k),式(8))。
因此,信号的部分被确定是不相关的。
从这些值,噪声的概率密度函数(图11),标准偏差和噪音的平均值被进行测定,具体如下:
=1.8克
=0.0055克
正如预期的那样,平均约为零。
概率密度函数[9]被近似为一个正常的分布,因为它是最相似的分布,如图11中获得的。
用于验证所提出模型的随机部分的方法是通过对检重秤总标准偏差的计算。
众所周知测重误差由检重秤提供相对于正确的重量等于由内部象征性干扰的传递函数提供的误差的总和及测量的不准确性。
因此,总的误差的标准偏差等于每两个误差的平方之和的平方根[9]。
计算三个误差,平等进行了验证,作为进一步的观察结果。
图10图表检重秤重量比较和传递函数的输出。
图11直方图检重秤不精确度(噪声)每单位3克图12密度变化
=1.81克
=0.22克
传递函数的标准偏差对应于标准偏差的输出和输入之差。
=1.8克(信息由检重秤供应商证实)
在模拟器中,检重秤模型包含一个延迟,传递函数表示码间干扰和附加高斯白噪声(AWGN)[6]来表示测量的干扰。
AWGN信具有零均值和标准偏差等于1.8。
4.4、洗衣粉密度发生器
洗衣粉有一个较大的密度变化,由于粉末的水分,非均匀制粒,颗粒致密等[10]。
为了重现这些变化,很多密度测定是在工厂中制造,包括在车和在粉末洗涤剂箱的测量,以确定密度的变化。
为了测量密度,一个标准的程序是采用定义的INMETRO,这是巴西重量计量学院,在市场上应用到控制产品功能。
图12表示出了观察到的每个纸箱的密度变化。
数据分析后,密度表现如下:
各车的容量具有不同的平均密度,其密度纸箱的序列呈现的振荡接近正弦波,斜波和三角波,以不同周期和峰,除了从一个AWGN(加性高斯白噪声)纸箱纸盒。
总之,可以观察到存在于纸箱的三种类型的密度变化:
●当地一名(从一个纸箱到另一个纸箱作为一个AWGN);
●中期变化(振荡注意到在50〜1500的纸箱的顺序);
●由于车辆的变化(它们具有不同的平均密度)。
然后从这些测量得出的结论提出一个定性的方法,然后再提出定量的方法。
首先,可以确认各车的容量具有不同的平均密度,因为粉末的生产也有密度变化每4-5吨,生产的粉末被馈送到1.7吨的车辆中,是随机储存在车辆中的。
它创建快速坡道或突然变化,因为上述填充头料仓装满由一个随机序列手推车,每一个具有不同的平均密度。
每次手推车的内容结束然后填充头接收从另一种材料,可能会突然出现密度变化。
有这种情况发生在中期第二变异性(50〜1500箱)。
值得注意的是:
从上面的采样和从手推车的底部呈现不同的密度,确认有相同的手推车内密度变化,由制造过程中产生的。
于是,也有人注意到,洗衣粉的纸箱序列密度呈现缓慢振荡,压缩和分离产生来自从推车到瓶子的粉末流动。
因此,这两种现象导致中期密度变化。
最后,混合这两个振荡,也有高频的干扰,作为加性高斯白噪声和其影响的连续纸箱的密度。
加性高斯白噪声的标准偏差取决于许多因素,如湿度,存储时,粉末洗涤剂的质量等等。
在进行密度变化的定性分析后,进行了定量分析,接下来对密度变化的三种类型进行描述。
4.4.1、局部密度变化
首先在纸箱中定量试验是评价密度的平均值和标准偏差。
要获得这些值,下面的测试是:
称重控制器被禁用,烧瓶的体积始终保持在2升。
三万箱被检重秤称重(历时2小时,45分钟)。
很显然,这些重量不仅受粉末洗涤剂的密度变化影响,而且受到9个烧瓶体积的差异和称重的不准确性影响。
用该试验中,有可能确定局部密度平均值
=500.5克/L和重
量标准差(
),然后,计算局部密度纸箱(局部密度)的标准偏差,具体如下:
(9)
三万箱的
由估算九个烧瓶的每一个重量标准偏差所获取,然后提取这些标准偏差的平均值。
它被发现
=7.88克,对应于总的局部可变性。
在4.3节中找到的自动检重秤标准偏差为
==1.81克,在4.2节烧瓶标准偏差估计为
=5.65克,在4.2节非均匀的填充标准偏差计算为
=1.1克。
纸箱的体积为2L。
它的结果:
=2.54克/升
为了模拟这种效果,加性高斯白噪声具有零均值和标准偏差局部密度被使用。
4.4.2、由于料车变化导致密度变化
在这里关心的是了解包装机送料过程如何影响密度变化。
制备的粉末洗涤剂被存储在车里是随机分配车板上的。
因此,每一个手推车的装料都是所产生的材料的一部分:
一旦被随机存储,所生成的序列的重排发生。
这些手推车随机定向到两个馈送开口于筒仓,这意味着它可通过使用两个手推车同时喂料仓。
图13示出在料仓的粉末流。
图13在筒仓的粉末流动
因此,在填充由一个随机更迭部分中的生产,每个车呈现的平均密度与周围振荡。
然而,所有的中期振荡,包括这一项已经为蓝本,在本款所述的研究。
另一个重要的事实是这个交替发生,在筒仓的粉末流的功能的方式。
进行一项研究,以了解这种交替,值得注意的是粉末从固定槽的后面部分出来(从排水更遥远)当前部表面处理的粉末排出。
也就是说,背面部分的粉末可以作为一个附加的缓冲,以避免粉末短缺,给操作者提供了一些额外的填充时间。
平均而言,一个返回的料车被替换为每三个前置料车与前方料车的排空时间大约是8分钟,因为每个车装载1540公斤,这是足以装满1517左右个纸箱(考虑平均超重约15克/盒)。
为了对料车的变化进行建模,在其上执行一个测试150手推车密度进行测定,包括在30,000箱中运行使用的料车。
所得到料车的平均密度与粉末的标准偏差是:
=501.0克/升
=5.7克/升
因此,一个随机变量可以被创建,它模拟了料车的平均密度。
随机变量的两个模块模拟每个料车反馈到料仓。
另一个测试是量化如何在料车发生变化转换速度。
料车发生变化之后,并且在同一时间,一个研究被进行在检重称测量重量时。
据观察,平均密度的变化速度为0.9克/升/箱。
为了对密度变化建模,由于车的变化,2个加性高斯白噪声与平均值等于
和标准偏差
被雇用和一个模型来模拟料车转换。
4.4.3、中期密度变化
这里的目的是为了找到密度随时间的变化情况。
根据以前收集相同的30000点,中期密度变化的统计研究中使用的6000个样本的窗口中完成。
平均密度变化被分析在一组九个纸箱中,并与第9个滑动窗口,也就是,每次一个新的纸箱到达时,一个新的计算平均值产生。
这组50箱被反复考虑。
这个数据操作是必要的,以消除局部变化,为了中期振荡的形象化。
在分析过程如下特点进行了研究:
密度振荡(正弦波,三角波和斜波)的形式,发生各形式,振幅或形式的倾斜的可能性,这些坡道振幅和周期的或倾斜的概率密度函数的振荡形式。
这些测量背后的想法是尝试创建一个随机模型来描述密度变化。
图17表示本研究中使用的局部图。
下面的振荡形式被进行鉴定在分析数据后:
期间没有振荡;长期的正弦由于制粉工艺;短期正弦由于漏斗上的灌装头被清空并且每36秒填充一个;三角波由于粉末的制作过程和粉末流动性;由于压实和隔离在主仓和料车缓慢下降的斜坡(见图13)和在50箱每200-250箱所发生的16%的时间突然下降,当后面的料车被馈送到机器(参见图13),占全部时间的4%。
在同一时间,观察该缓斜面周围发生的总时间为71%和仅仅当前料车被馈送到机器。
因此,表2列出了本研究的结果。
一般来说,一旦他们有不同的原因这些振荡的形式平行出现,并且不相关,除了长正弦波和三角波,这是同一个原因的变化并不会同时出现。
有趣的注意到,没有振荡周期的概率为0.5%,考虑到它会发生,只有当所有波没有发生一起。
这是表2中提到的概率的结果。
这是重要的,该波的出现在各自的波周期的每个角落进行评估,他们将根据实际的确定概率发生,也就是说,动作时间是多个其对应的周期。
只是突然在坡道45-55纸箱出现动作,慢坡道启动当前料车开始它的排放。
密度标准偏差计算为30000纸箱消除检重称的不精确度影响,烧瓶中的高度变化和非均匀填充,它导致了
=8.7克/L。
先前估计的料车的标准偏差为
=5.7g/L,先前计算的局部密度标准偏差为
=2.54克/L。
计算中期密度振荡的标准偏差,如方程(10):
(10)
这导致:
=6.06克/升
为了确认这个结果,估计从9纸箱滑动窗口的平均密度数据的标准偏差,消除了来自料车的突然变化的影响,这导致6.2克/升,是非常接近的前面的结果。
为了模拟期中密度变化,正弦,缓慢而陡的斜面,并与不同时期的三角波和振幅倾斜度被应用,其值是一个高斯或均匀分布的随机过程(见表2)。
这导致了总的中期标准差等于
。
作为
和
被精确地确定与
,为此,它更难以确定一个精确的随机模型,它被包含在模拟器相乘期中密度发生器的输出的一个因素,为了使微调用是否总密度的标准偏差不等于8.7克/升。
这个因素应该是非常接近1,在模拟期间所发生的。
4.4.4、建模的密度变化
根据前面讨论的不同密度的变化,这是可能的去模拟在制造过程中的密度变化,如图14所示。
如可以注意到在图如图14所示,粉末洗涤剂浓度产