闪光焊及缺陷.docx
《闪光焊及缺陷.docx》由会员分享,可在线阅读,更多相关《闪光焊及缺陷.docx(26页珍藏版)》请在冰豆网上搜索。
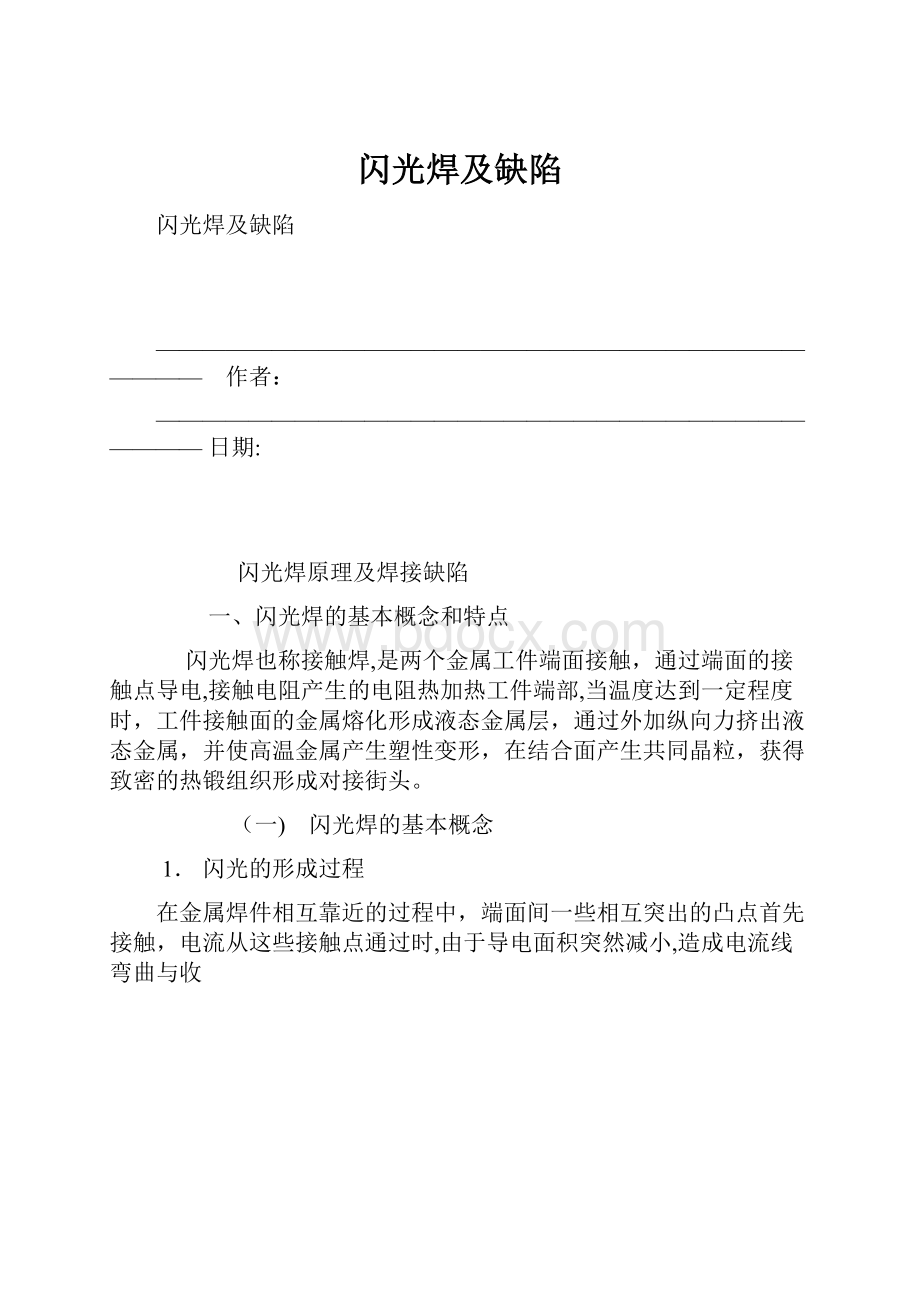
闪光焊及缺陷
闪光焊及缺陷
———————————————————————————————— 作者:
————————————————————————————————日期:
闪光焊原理及焊接缺陷
一、闪光焊的基本概念和特点
闪光焊也称接触焊,是两个金属工件端面接触,通过端面的接触点导电,接触电阻产生的电阻热加热工件端部,当温度达到一定程度时,工件接触面的金属熔化形成液态金属层,通过外加纵向力挤出液态金属,并使高温金属产生塑性变形,在结合面产生共同晶粒,获得致密的热锻组织形成对接街头。
(一) 闪光焊的基本概念
1.闪光的形成过程
在金属焊件相互靠近的过程中,端面间一些相互突出的凸点首先接触,电流从这些接触点通过时,由于导电面积突然减小,造成电流线弯曲与收
图1 闪光面的接触点
缩从而形成了接触电阻,如图1所示。
这些小接触点的电阻很大,电流流过时被迅速加热、熔化,形成一个个液体金属过梁,这些金属过梁将热量传入焊件的内部。
每个过梁都存在液态表面张力、径向压缩效应力、电磁引力和电磁斥力的作用,径向压缩力与流过过梁的电流强度平方成正比,在这些力的作用下过梁直径减小,电流密度急剧增大,温度迅速上升,使过梁内部出现金属蒸气。
金属蒸气使液体过梁体积急剧膨胀而爆破,熔化的金属微粒从对口间隙中飞溅出来,形成了飞溅的火花。
爆破后的位置留下一定深度的火口,为临近产生过梁创造了条件。
闪光过程就是焊接端面不断产生液态金属过梁又连续不断的爆破过程。
2.闪光的作用
(1)加热焊件。
闪光过程中金属液体过梁的电阻热和过梁爆破时一部分喷射熔滴飞溅到对口面上带来的热量对焊件加热。
(2)烧掉焊件端面上的赃物和不平之处。
因此也就可以降低焊接前对焊件端面的打磨要求,用手提砂轮粗打磨即可。
(3)金属的液体过梁爆破时产生的高压力、金属蒸气及CO、CO2气体形成了保护气氛,减低了焊件端面间隙中气体介质的氧化能力。
(4)闪光后期,焊件断面形成液态金属覆盖层,为顶锻时排除端面的氧化物和过热金属提供了有利条件。
3. 获得闪光对焊优质接头的条件
(1)闪光过程不出现闪光中断,加速烧化时闪光稳定、激烈,有良好的保护气氛。
(2)焊接端头应形成足够的加热区和适当的、均匀的温度梯度;断面温度均匀。
(3)焊接端面要有足够的塑性变形区。
(二)钢轨闪光焊
钢轨闪光焊接按照闪光过程的特征分为连续闪光焊、预热闪光焊、脉动闪光焊三种类型。
1.连续闪光焊
图2连续闪光焊曲线
图2是钢轨连续闪光焊接过程,它记录有电压、电流、力、位移四个主要焊接参数与时间的关系,从图中可见,其焊接过程中的焊接电流是连续的。
焊接中期闪光电流稳定在100~200安培(焊接变压器初级电流),动架夹持钢轨送进稳定,焊接压力值恒定,位移是一条斜线。
连续闪光焊分为预闪、连续闪光烧化、加速闪光烧化、顶鍛、锻压(保持)五个阶段。
预闪的作用有二:
一是闪平钢轨倾斜的端面、使随后开始的焊接过程保持全断面接触闪光;二是对钢轨端面预加热,减少焊接初期不稳定闪光时间。
连续闪光焊的主要焊接参数有:
焊接时间、焊接电压变化程序、烧化速度、烧化末速、反馈电流、顶鍛量。
加速烧化是顶锻前的重要阶段,加速烧化时间和加速末速是重要的焊接参数。
2.预热闪光焊
预热闪光焊的主要焊接阶段有:
闪平、预热、闪光烧化、加速烧化、顶锻和鍛压。
图3是预热闪光焊记录曲线,记录的主要参数有焊接压力、焊接电流、位移和时间的关系。
预热过程是加热钢轨的主要阶段。
图3 预热闪光焊记录曲线
3.脉动闪光焊
图4是脉动闪光焊记录曲线,记录有焊接压力、焊接电流、位移和时间的关系。
脉动闪光焊与连续闪光焊相比较,其闪光过程中几乎没有过梁的自发爆破现象;在加热钢轨的主要阶段,闪光电流是不连续的。
在焊接过程中它跟踪的是电阻、电流;烧化过程中焊接电流与送进速度无关;烧化过程的送进油压是脉动的。
图4脉动闪光焊曲线
(三)焊接参数调节功能
1.电压的调节
焊接电压(焊接变压器次级电压)是决定钢轨加热状态的基本焊接参数,它可以显著地改变焊接时间和钢轨的温度梯度分布以及闪光过程的稳定性,稳定的闪光过程是具有很细小的过梁尺寸和火口深度。
结合焊接过程选择适合的电压是很重要的。
焊接电压增高,则焊接电流增大,闪光过程也就更加激烈;会形成大尺寸的过梁爆破,造成大量熔化金属的飞溅,使钢轨端面的加热深度减小,火口的深度加大,导致端面温度分布不均匀,不能形成良好的焊接接头。
当焊接电压较低时,焊接电流减小,将导致钢轨送进速度大于闪光烧化速度,易出现钢轨焊接端面短路。
2.反馈电流的调节
稳定的闪光烧化是通过焊接电流的反馈进行控制。
闪光初期,可能出现一次或几次较大的短路电流,它与焊接电源功率、钢轨焊接回路阻抗、钢轨端面接触面积、及钢轨初始温度有关。
在以后的低电压闪光阶段一般不应出现闪光中断;在加速烧化闪光阶段也不应出现闪光中断。
顶锻前出现闪光电流短路或断路都将会影响焊接接头质量。
3.加速烧化
加速闪光烧化过程是焊接循环必不可少的一个阶段,也是顶鍛前的重要阶段,加速时间和加速末速是重要的焊接参数。
加速使钢轨端面接触的触点增多,形成过梁的爆破也逐渐激烈,可以看到激烈的火花飞溅。
激烈的闪光能够形成良好的保护气氛,为顶锻创造了良好条件。
加速闪光烧化阶段通常是切断电流反馈控制,或加大反馈电流值。
4. 顶鍛和鍛压
顶锻量、顶锻时间、顶锻力是重要的焊接参数。
顶锻过程通常分为两个阶段:
(1)有电流顶锻。
该阶段是在通电状态下进行的,以保证钢轨端部的温度并有利于液态金属及氧化物夹杂的排出。
带电顶锻时间通常设置在0.5秒~1.2秒,时间长一点有利于液态金属及氧化物夹杂的排出。
(2)无电流顶锻。
该阶段是在切断电压(实际上是切断电流)后,继续保持顶锻压力,使液态金属及氧化物夹杂彻底被挤出,并排除过热金属,使焊缝继续产生塑性变形,形成致密的焊接接头。
顶锻压力的大小取决于钢轨的断面尺寸、材质的高温性能和钢轨的加热状态及加热区的分布。
顶锻力过小,夹杂物不容易排净,塑性变形不足;顶锻力过大,则塑性区被过分挤压,晶纹弯曲,接头冲击性能下降。
顶锻开始的合缝速度(顶锻速度)应越快越好,以防止端面氧化。
顶锻速度应大于30mm/sec。
二、钢轨闪光焊接头缺陷分类及形成的原因
焊接接头缺陷包括两类,一类是焊接加工造成的,另一类是钢轨外形尺寸偏差造成的。
(一)闪光焊接头的组成
焊接接头是由焊接区和毗邻的钢轨母材构成的,焊接区又划分为焊缝和热影响区,其力学性能差于钢轨母材。
1.焊缝
焊缝实际上是一层垂直于钢轨纵向的金属薄层,宽度只有零点几毫米,垂直于钢轨纵向。
在焊头精加工后的宏观照片上,焊缝是一条白线(见图5),它是一层氧化脱碳的贫碳层,金相组织是珠光体和少量的网状铁素体,硬度低落较大。
2.热影响区(HAZ)
热影响区分为粗晶区、细晶区、不完全重结晶区。
粗晶区是焊接高温(1200℃左右)形成的过热区,其奥氏体晶粒粗大,该区金属硬度高、塑性和韧性差。
细晶区是焊接温度小于1000℃正火区,晶粒较细,该区金属塑性和韧性较好。
不完全重结晶区又称为部分相变区,其晶粒大小不一。
热影响区对称分布焊缝两侧,总宽度约40mm左右。
图5是精加工后焊头纵向板宏观照片,焊缝两侧白色影线之间区域是热影响区。
图5焊缝及热影响区宏观形貌
(二)外观质量缺陷
1.表层灼伤
此类缺陷分为打磨灼伤和电极灼伤(打火)。
(1)打磨灼伤:
钢轨焊接的顶锻阶段是闪光焊机夹持两根钢轨纵向加力,将焊接端头液态金属和过热塑性金属挤出、凸出钢轨表面。
为了获得良好的外观质量和平直度要求,必须用砂轮机进行打磨。
图6是焊机推凸后焊头外观及粗磨后外观。
图6(a)粗磨前焊头外观
图6(b)砂轮机打磨
图6(c)粗磨后的轨头外侧和轨底角
当手持砂轮长时间的用力打磨已经完全冷却焊头某个部位表面时,极易形成表层马氏体组织并伴随有微裂纹。
图7是打磨过热引起钢轨的轨腰水平纵向裂纹,此焊头是在地铁线路探伤时发现的。
图7纵裂
通过对此焊头检验分析,马氏体白层的硬度值达到752HV,而基体的硬度值仅为283HV。
在内应力作用下,裂纹疲劳扩展成纵向裂纹。
焊头温度在200℃以上打磨时出现的发蓝现象与打磨灼伤是不同的两个概念,发蓝是打磨表面迅速氧化形成的。
(2)电极灼伤:
只发生在焊机电极与钢轨接触的导电部位,它是电极与钢轨接触不良或存在残渣,在焊接开始出现“灼伤”或“打火”而产生马氏体、渗铜现象,并会留下明显灼伤痕迹。
其危害是钢轨在线路上断裂。
移动闪光焊的焊机电极是在夹持轨腰部位(距离焊缝约8cm之外位置),当轨腰与电极接触不良时,通电后的电流会立刻将电极与轨腰接触的局部区域加热升温,导致该处轨腰过热,基体金属组织发生变化。
由于此位置处在正火范围之外,也就不可能通过正火解决其组织变化。
固定式焊机电极是上下夹持轨顶和轨底,常在轨底及轨顶出现电极灼伤。
图8是K型焊机焊接再用轨时轨顶电极灼伤。
图8 钢轨顶面电极灼伤
轨底“打火”是最严重的电极灼伤。
产生“打火”的原因有两个:
一个是在钢轨压紧的过程中焊渣落入电极面上,压紧钢轨时,焊渣被钢轨压在电极面上;另一个原因是钢轨对中过程中焊机钳口再次压紧钢轨之前,轨底存有从下电极的定位螺栓孔中吸附的焊渣,二次压紧钢轨时,焊渣被压在电极面上(最新GAAS80/580焊机已改进)。
图9是轨底打火断口(疲劳)宏观形貌特征,断口的轨底半月形黑区为打火点。
图9(a) 轨底与焊机电极打火断口(轨底黑区为打火点)
图9(b)打火点断口形貌 4.4×
图9(c) 打火点金相组织:
马氏体1000×
2.推凸缺陷
(1)闪光焊接头的推凸过程
固定式焊机通常有4把推凸刀分别对轨头、两侧轨腰和轨底梯级推除顶锻后接头的凸出量。
图10显示的是GAAS80焊机的推凸过程。
图10(a) 钢轨顶锻完成后(推凸前)形成的接头
钢轨轮廓外突出的红热的高温金属、毛刺和焊渣,温度大约1200℃。
图10(b)推凸刀正在推凸
图10(c)推凸完毕
(2)推凸余量导致的缺陷
两根焊接轨的断面尺寸不可能完全相同,总是存在偏差,因此推凸刀和钢轨断面之间必然存在间隙。
当推凸刀将顶锻挤出的高温金属推凸到焊缝另一侧钢轨表面时,会形成舌状包边,紧紧粘在钢轨表面,相当于一个尖劈,出现应力集中。
它会造成在线路上焊头早期疲劳断裂,这种推凸缺陷与推刀是否锋利、钢轨的外形尺寸偏差和错边大小相关联。
图11是推凸缺陷导致焊头折断的照片。
图11(a) 疲劳断裂的断口形貌
图11(b)疲劳断口侧面的宏观形貌
从图中可以看到疲劳区与推凸余量的关系,残存的熔渣为疲劳源。
图12是焊头的轨底未打磨而残存有舌状包边引起的焊头疲劳断裂。
图12 疲劳断口宏观形貌
从图中看出,疲劳源在轨底中间位置,存在应力集中,是疲劳裂纹核心产生的策源地。
在低倍下观察扇形疲劳区的底边有明显的分层;金相观察发现,断裂源处的金相磨面上有大量的孔洞和夹杂;断裂源处的金相组织形貌有明显的氧化脱碳特征。
推凸过程中推刀将冷却的焊渣挤入炙热焊头基体会形成“夹渣”缺陷。
(三)内部质量缺陷
1.灰斑
灰斑是允许存在的缺陷,但是其面积大小有限制。
灰斑只是出现在焊缝面,呈现平的和光滑的形貌,国外称其为平斑(flatspot)。
U71Mn钢轨焊头焊缝断面上的灰斑是无光泽的,U75V钢轨焊头焊缝断面上的灰斑是光亮的。
灰斑的形成原因说法不一。
一种意见认为是与氧化物有关,依据是用电子探针在灰斑的夹杂物中发现其主要成分是SiO2和MnO。
Гельман等人曾测定过闪光端面保护气氛的化学成分,发现这种气氛中含有少量O2(<2%)和大量CO、CO2气体,这种少量O2仍然可以使焊接端面的熔化金属发生氧化,尤其是液态高温金属的溶氧能力强,更容易被氧化。
因此,加速烧化速度过慢也会出现灰斑。
另一种意见认为熔化凹坑(火口)中液态金属成分的改变是这种缺陷产生的原因。
顶锻时,在较深的熔化的凹坑中,液态金属被封闭而不能排挤出,成为一薄层,并出现成分不同的区域。
不可否认的是灰斑和焊接工艺有关:
加速烧化速度慢、顶锻合缝速度慢、顶锻前的烧化过程出现大的脉冲电流或出现断路都可能出现灰斑缺陷。
灰斑可以出现在焊缝断面任何位置,当出现在轨头时,其成分中含有的硅酸盐夹杂物在运营线路中会产生应力集中,并以此为核心发展成纵横向裂纹形成核伤。
图13是焊缝断面轨底位置的灰斑。
图13(a)U75V钢轨的焊缝断面灰斑(多个灰斑)
图13(b) U75V钢轨的轨脚处焊缝断面灰斑(露头灰斑)
图13(c)落锤断口焊缝位置灰斑(图中箭头指处)
最近几年也曾多次发现轨头焊缝处的非金属夹杂物所引发的核伤,而灰斑中存在着硅酸盐夹杂物,并且分布是不均匀的,在某些部位是富集的。
夹杂物处产生应力集中并以此为核心,发展成疲劳裂纹,形成核伤。
下图是灰斑的金相组织,无规则黑色块状物为硅酸盐夹杂。
图13(d)灰斑金相组织
2.裂纹
裂纹的产生与焊接工艺、环境温度、冷却速度有关。
在低温焊接时,应采取有效的预热和保温缓冷措施。
车间内焊接钢轨时,焊缝冷却速度基本稳定在1℃/sec左右,不会产生马氏体组织,也就不会出现焊接微裂纹引起的脆性断裂(除非存在严重成分偏析)。
裂纹常分为热裂纹和低温裂纹。
低温裂纹与马氏体组织及应力有密切关系。
热裂纹是焊缝金属处于高温状态、强度较低时,受到外力、超过了该温度范围内焊缝金属的强度极限,将产生裂纹或断裂。
其表面呈现氧化蓝色。
左图是起源于轨腰热裂纹引发的焊头横向断裂。
移动闪光焊的焊缝或热影响区出现的裂纹主要是热裂纹,其断裂面有明显的高温氧化特征(黑色-蓝色)。
裂纹常起源于轨腰,向轨头或轨底发展。
断裂的原因是焊接接头在高温状态下(焊后或正火)受到纵向张拉力。
3.微量马氏体
它与钢轨母材中C、Mn、Si、V等元素偏析相关联。
经过焊接热循环作用,其偏析会加重,如果出现在近缝区,即使在正常的冷却速度也会出现不连续的马氏体组织。
图14是U76NbRE钢轨焊头中出现的微量马氏体金相照片。
如果微量马氏体存在轨头位置,微量马氏体伴随的微裂纹在运营线路上就会形成危险的核伤。
参看图16,严重的成分偏析出现马氏体,在内应力作用下形成裂纹源,裂纹疲劳扩展而断裂。
图14轨头焊缝和近缝区金相组织(100×)
图15 上图中的马氏体组织放大(400×)
图中从左到右的5个维氏硬度测点分别为321HV、524HV、603HV、358HV、345HV,其中第二、三点是马氏体的硬度。
进一步用扫描电镜分析马氏体成分,其中Mn含量达2.14%,超过钢轨标准1.20%的Mn含量近一倍;稀土La(镧)的含量达1.92%、Ce(鈰)的含量达2.00%,均已大大超过钢轨标准要求0.023%的含量。
图16 轨头马氏体引发的疲劳断裂(箭头指处为疲劳源)
4.过烧缺陷
过烧是组织缺陷,轻度过烧呈现很细小的炭黑斑点,严重过烧成黑色蜂窝状组织。
其起因是:
顶锻前的钢轨端面液态金属层厚薄不均匀;焊接端头的温度梯度陡,纵向没有足够的塑性变形区;顶锻时的钢轨端面过热熔渣未完全挤净形成过烧组织。
过烧常常出现在轨底和轨脚位置。
焊接前钢轨端面垂直度偏差大,造成顶锻前的钢轨断面温度严重不均,顶锻时的钢轨端面过热熔渣未完全挤净形成过烧组织。
图17是轨脚过烧断口的宏观形貌。
图18是过烧断口的微观形貌,黑灰色的氧化物已侵入金属晶界内,其破坏作用相当于多个碎裂纹存在焊缝中。
图17 轨底脚过烧断口(箭头指处为过烧部位)
图18 过烧断口的微观形貌:
蜂窝状,微裂纹
图19是轨底出现的过烧组织。
它是在钢轨轨底轮廓之外,没有侵入焊头基体内,可以通过砂轮的轨底打磨除去。
图19轨底过烧断口宏观形貌
5.未焊合缺陷
未焊合是焊接设备状态不良、出现加速烧化速度异常,或顶锻速度过慢等原因出现不正常焊接过程造成的。
图20是轨角未焊合的断口照片(轨脚锯切后)。
图20 轨角未焊合断口
图21是轨头大面积未焊合断口。
图中的1区有熔融状表层,其颜色呈深黑色。
2区断口为脆性断裂,
图21钢轨未焊合断口(1区有熔融状表层,2区脆性断裂)
图22 熔融状表层金相(灰色为熔融覆盖层,基体为珠光体)
6.正火缺陷
(1)不同的正火加热方法
图23是焊轨车间中频感应加热焊头,图24是火焰加热焊头。
图23 车间生产线上中频感应加热焊头
图24 现场采用的氧-乙炔火焰加热焊头
(2)晶粒粗大
正火缺陷主要是正火温度不足而未细化焊接接头粗晶区中的粗大奥氏体晶粒。
无论是中频感应加热,还是火焰加热,其焊头都有可能存在局部位置温度低于钢轨基体相变温度,由其是轨底脚部位。
当再次加热正火并提高加热温度时(最高温度不宜超过950℃),粗晶细化、缺陷消失。
图25是轨底脚温度过低出现的粗晶,其中反光较暗的区域已经达到金属相变温度,而发亮的区域未达到金属相变温度。
图25 轨脚正火温度低的断口面宏观形貌
(2010-11-8)