铝合金表面处理原理.docx
《铝合金表面处理原理.docx》由会员分享,可在线阅读,更多相关《铝合金表面处理原理.docx(26页珍藏版)》请在冰豆网上搜索。
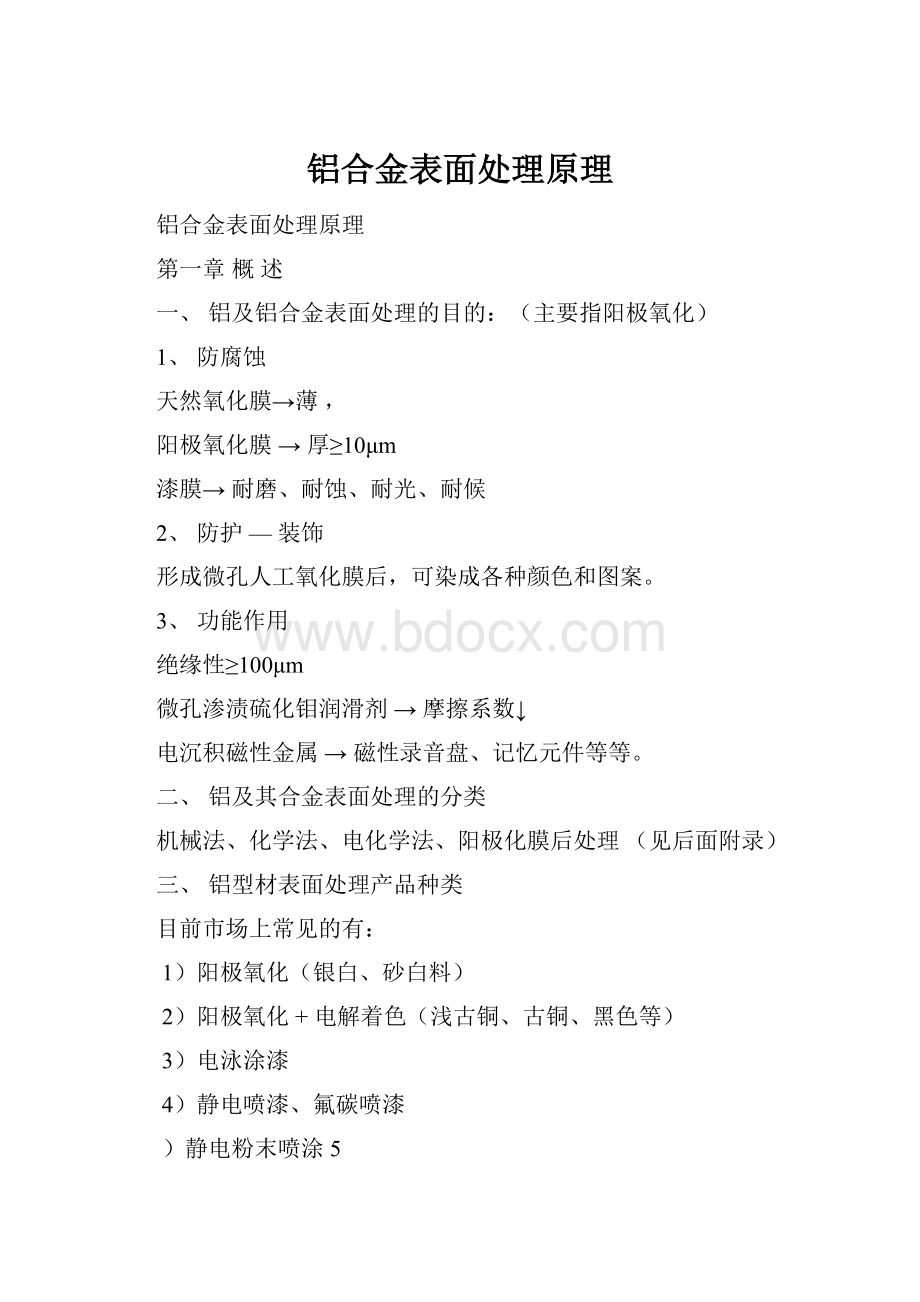
铝合金表面处理原理
铝合金表面处理原理
第一章概述
一、铝及铝合金表面处理的目的:
(主要指阳极氧化)
1、防腐蚀
天然氧化膜→薄,
阳极氧化膜→厚≥10μm
漆膜→耐磨、耐蚀、耐光、耐候
2、防护—装饰
形成微孔人工氧化膜后,可染成各种颜色和图案。
3、功能作用
绝缘性≥100μm
微孔渗渍硫化钼润滑剂→摩擦系数↓
电沉积磁性金属→磁性录音盘、记忆元件等等。
二、铝及其合金表面处理的分类
机械法、化学法、电化学法、阳极化膜后处理(见后面附录)
三、铝型材表面处理产品种类
目前市场上常见的有:
1)阳极氧化(银白、砂白料)
2)阳极氧化+电解着色(浅古铜、古铜、黑色等)
3)电泳涂漆
4)静电喷漆、氟碳喷漆
)静电粉末喷涂5
铝及铝合金表面处理工艺流四、建筑铝型材阳极氧化处理和喷涂工艺流程
电泳→固化成
脱脂→碱蚀→中和出光→阳极氧化D法)→电解着色A法)→封
脱脂→酸洗→化学转化→静电喷→固化成
、通用工业用铝合金部件(机械部件、电器部件等)阳极氧化处工艺流程
草酸
脱脂→酸洗→中和出光→阳极氧化→硫酸法(染色)→封
硬质阳极氧化
、装饰用铝合金部件(汽车装饰部件、照相机部件等)阳极氧化理工艺流程
机械喷染色→印
(人工修整→振动抛光)→脱脂→化学炮→阳极氧化(硫酸法)→封
电化学抛光
第二章铝材阳极氧化前的处理
铝合金建筑型材生产工艺流程:
铝材装架→脱脂→水洗→碱蚀→水洗(二道)
→中和(出光)→水洗→阳极氧化(DC法)→水洗→封孔
水洗→着色(AC法)→水洗
→水洗→卸架
架装第一节方式:
横吊式、竖吊式一、纵吊式特点:
适合大批量生产:
每批可装载大量铝材、1
减少装卸工人:
减轻了装卸时的劳动力2、
夹具不减少化学品消耗量,降低生产成本:
溶液带出量少,3、浸入处理液中,减少夹具消耗量。
减少用水量:
带出水量减少,耗水量及废水处理量减少。
、4月以上。
吨/适于生产能力在600
目前,一般采用横吊式为多。
注意事项:
(横吊式)二、
便于氧化时气泡逸出。
o~5o)→1)铝材要有一定倾角(3→保证导电良好。
2)扎料要紧,导电杆脱模要干净
防止色差。
)每根料之间间距应保证→3防止色差。
4)避免不同型号、长度的料扎在一起着色→。
80%,最大100%5)每次上料面积要一定,最好是对极面积的脱脂处理第二节目的:
一、
除去制品表面的工艺润滑油、防锈油及其他污物,以保证在碱
洗工序中,制品表面腐蚀均匀和碱洗槽的清洁,从面提高氧化制品质量。
二、油脂种类:
动物油、植物油→属皂化油,可与苛性碱发生皂化反应
矿物油→属非皂化油,不与苛性碱发生皂化反应
锯切液
三、脱脂方法与原理
1)有机溶剂:
酒精、煤油、汽油、丙酮、甲苯、三氯乙烯、四氯化碳等。
利用溶剂对油污很强的溶解能力将油除去。
对Al基体无腐蚀性。
2)表面活性剂:
合成洗涤剂、金属清洗剂等。
利用有效成份对油污的优良的皂化、乳化、分散、渗透能力将油污除去,对铝基体无腐蚀作用。
3)碱性溶液:
NaoH+添加剂(乳化剂)
利用溶液中的某些碱性物质与油污发生皂化或乳化作用来达到除油污之目的。
皂化作用—→除去动、植物油
乳化作用—→除去矿物油
皂化反应:
CH(CHCOO)+3NaOH→3CHCOONa+3CH(OH)35351733517353硬脂酸苛性钠肥皂甘油
乳化作用:
略
成份及其作用:
:
皂化反应,除油作用。
NaOH①.
②NaCO(碳酸钠)、NaPO(磷酸三钠):
缓冲剂,保持溶液4233PH=10~11。
③硅酸钠(水玻璃):
湿润剂、乳化剂、分散剂,不易水洗去掉
4)酸性溶液
HSO、HNO等342Al+HSO=Al(SO)+H↑223442利用H小泡包围油珠,离开铝表面层达到除油目的。
25)电解脱脂
即将制品放在碱性溶液中作为阴极而进行电解处理除去油污。
四、脱脂工艺制度
轻油级:
1)HSO150~250g/l常温3~5分钟422)HNO150~200g/l常温2~3分钟33)HNO120~150g/l3HSO120~80g/l常温2~5分钟42重油级:
1)NaPO40~60g/l(弱碱性)43NaOH8~12g/l
NaSiO20~30g/l50~60℃2~3分钟322)NaPO30g/l
43NaCO20g/l40℃2~3分钟32)金属清洗剂3.
20~30g/l常温5~8分钟(根据说明书要求)
碱性除油工艺:
NaOH10~15g/l,添加剂20~30g/l,45~60℃,3~7分钟
第三节碱蚀
一、目的:
1)除去铝材表面的自然氧化膜,使金属基体暴露出来,
活化表面,有利于氧化着色。
2)整平基体表面,使其均匀一致。
3)调整金属光泽。
4)进一步除去铝材表面污物。
二、方法:
碱法、磷酸钠法、硫酸铬酸法等。
一般采用强碱热溶液。
三、碱蚀原理:
碱蚀过程主要有以下三步化学反应:
AlO+2NaOH→2NaAlO+HO
2223
2Al+2NaOH+2HO→2NaAlO+3H↑222
2NaAlO+4HO→2Al(OH)↓+2NaOH322
AlO↓+3HO232第一步反应是除去铝材表面的天然氧化膜;
第二步是铝基体与碱反应,起整平表面的作用;
生成胶状的氢第三步是前二步反应所生成的偏铝酸钠不断水解,
氧化铝和苛性钠,氢氧化铝进而脱水变成AlO硬水铝石。
32现在工业上普遍使用长寿命碱蚀添加剂。
四、添加剂的作用:
具有防止产生铝石、增光、整平、缓蚀等多种作用。
特点:
3+铝量达100g/l(甚至120g/l)以上,而不会产1)允许溶存Al生硬水铝石,即使偶有发生水解也不结块,易于清除。
2)具有缓蚀整平功能,碱蚀效果更好。
3)铝腐蚀率能保持在1~2%之间,减少铝溶蚀量及氢氧化钠消耗量。
成份:
一般有葡萄糖酸钠、酒石酸盐、柠檬酸盐、羧甲基纤维素等多元多组份的混合物。
五、碱蚀工艺:
NaOH:
50~60g/l,碱蚀添加剂:
视说明书要求,温度:
50~70℃
时间:
视工艺要求
第四节中和(出光)
一、目的:
①中和残碱,防止污染氧化槽。
②洗去残留在表面的Cu、Fe、Zn、Si、Mn等元素的氧化物(挂灰),光亮表面。
二、方法:
1)硝酸法:
HNO150~250g/l,温度室温,时间:
1~3分钟3烟雾大。
易污染氧化槽,但成本高,出光效果较好,为氧化性酸,
3~5,温度:
室温,时间:
SO150~250g/l硫酸法:
H)242,以增)HO、分钟。
出光效果不甚理想,可加入少量氧化剂(HNO223强其氧化性,或加入添加剂。
不污染氧化槽,成本低。
体积比):
1硝酸+氢氟酸(33)
用于高硅铝合金、铸造铝合金。
特殊要求预处理第五节一、消光处理
1、化学方法:
1)NaOH溶液(全面均匀腐蚀)
浓度:
5~25%,温度:
50~70℃,时间:
1~10min
2)NHHF+(NH)SO溶液(斑点腐蚀)44243)NHF溶液(斑点腐蚀)4浓度:
3~5%,温度:
20~40℃,时间:
1~5min
2、电化学方法(电解消光处理法):
1)HCl溶液
浓度:
5~20%,温度:
20~60℃,时间:
1~2min,
2~30A/dm电流密度:
102)HCl+HSO溶液42HCl浓度:
0.3%,HSO浓度:
1~2%,温度:
75~80℃,时间:
0.5~422,电流密度:
70A/dm1min3)HCl+NHCl溶液4、机械方法:
喷砂处理等等3.
二、抛光处、化学抛%1S体积最常用的是三酸抛光P75v/少量CuSHN1%CN抛光质量好,操作简单。
缺点是成本高,污染重。
代替方法是性抛光技术
、电解抛
P480S15Cr0.9
15A/d3mi,电流密度1温度79℃,时间多用于表面光洁性要求很高的装饰材料
、机械抛
设备有扫纹机、布轮
第三章阳极氧化
一、目的:
人为在制品表面生成(或加厚)氧化膜。
二、方法:
化学氧化、阳极氧化
第一节化学氧化
化学氧化是在一定的温度下,使清洁的铝表面与氧化溶液中的氧发生反应而生成氧化膜的方法。
化学氧化膜与自然氧化膜相比,厚度要大100一200倍。
与阳极氧化膜相比,具有以下特点:
(1)膜的生成速度快;
)处理设备简单,生产成本低;2(.
(3)涂料附着性良好,耐蚀性优良;
(4)膜薄(0.5~3μm)而软,耐磨性和着色性较差。
因此,—般只用作防蚀涂漆膜的底层。
在工业上,化学氧化常用于形状复杂的零件、室内装饰品以及屋面材料的氧化处理。
一、化学氧化原理
在一定温度下,在含有氧化剂(常用铬酸盐)和活化剂(常用碳酸盐)的溶液中,通过化学作用使铝离子和氧化溶液中的氧相互作用在制品表面生成一层致密氧化膜的方法。
溶液一方面应具有氧化能力,能使铝表面产生氧化膜,另一方面也应具有使氧化膜部分溶解而产生针孔的作用,促进氧化膜成长和厚度增加。
但要使氧化膜在溶液中的生长速度必须大于溶解速度。
一般所采用的酸有HF、NaSiF十酸、铬酸、酒石酸、磷酸等;42采用的碱性盐为铬酸盐、磷酸盐等。
化学氧化所采用的溶液的种类是很多的,最常用的是含有碳酸钠作为活化剂的溶液中进行化学氧化处理。
二、化学氧化处理法
现代一般广泛使用的铝及铝合金的化学氧化膜的处理方法有:
饱尔—福格耳法(BV法)、MBV法、E.W法、派卢明法、阿尔罗克法、阿洛克罗姆法等。
按溶液的组成可分为:
(1)以碳酸钠为主体;‘
以铬酪或重铬酸盐为主体;
(2).
以氟化物为主体(3)以磷酸为主体。
(4)常用的化学氧化膜有作为铝合金建筑型材粉末喷涂前的预处理,铬酸膜、磷酸膜和新开发的无铬膜。
阳极氧化第二节
利用电解所谓阳极氧化——即把铝型材人为阳极置于电解液中,
作用在制品表面形成多孔性的氧化薄膜。
阳极氧化的种类一、
脉冲电流阳极交流电阳极氧化、按电流形式分有:
直流电阳极氧化、氧化。
硫酸、草酸、磷酸、铬酸、混合酸及以磺基有机酸按电解液分:
为主的自然着色阳极氧化。
按膜层性质分:
普通膜、硬质膜、瓷质膜、光干涉膜
阳极氧化原理二、铝氧极氧化的原理实际上就是水电解的原理。
3+AlAl-3e→阳极:
2+-O3H+6OH3O→223-+卡)3992AlAl+3OO+热量(→32+H→2H阴极:
+2e2氧化膜的生成规律,可通过氧化过程的电压一时间曲线来详细说明。
.
2,1A/dmD=水溶液,阳极电流密度条件:
20%HSOA24温度22℃.
第一段(曲线ab段):
在通电十几秒内电压急剧上升,这是由于铝表面形成了连续的、无孔的氧化膜,叫做活性层。
由于它具有半导体整流作用,所以又叫阻挡层。
第二段(曲线bc段):
当电压达到一定数值后,开始下降,一般比最高值下降10~15%,
这是由于电解液对氧化膜的溶解作用所致,使铝表面产生无数微观孔穴,从而保证电流能够顺利通过。
第三段(曲线cd):
阳极氧化经过20秒以后,电压下降至一定数值就趋于稳定,然后以缓慢的速度上升。
这时无孔层的生成速度和溶解速度达到平衡,其厚度不再增加。
但氧化反应并未停止,在每个孔穴底部,活性层通随时间延长而向纵深发展最后形成了六梭体蜂窝状氧再生,过溶解、.
化膜结构,即多孔质层。
99--,壁厚10mm,针孔内径为10~15活性层厚度约为15×10×29-,硫酸阳极氧化膜的5亿个/mm,针孔密度大约为4×12~1510~。
孔隙率为20~30%氧化膜厚度三、
?
tI?
?
K?
mμδ—氧化膜厚度,2—电流密度,A/dmImin
—氧化时间,t与电流效率和某一工艺条件下生成膜的密度或孔隙度为常数,K
0.26
K=0.25~有关。
我国采取DC法18~20℃,例:
某厂,20%HSO溶液,422m.
μ12~13δ,t=30min,=D1.4A/dm=A120.286KtIKδ由=··→=≈
1.4?
30四、直流硫酸阳极氧化工艺规范
电流——直流电DC
电解液——硫酸
铝及铝合金阳极氧化膜的优点:
、可大大提高铝材表面的耐磨、耐蚀、耐光、耐候及着色性能。
12、由于氧化膜是由基体金属直接生成的,所以与基体结合牢固,很难用机械的方法从基体金属上分离去掉。
3、氧化膜有良好的绝缘性。
直流电硫酸阳极氧化工艺最佳条通常使用范参数名
180g/l200g/l15含S35g/l20g/lA离子含21温2
1.5A/d电流密1.2A/dm按膜厚要求而时分13
m
16分19V1716电21V
1
∶极比∶2.5
1阴极∶工件=1
五、影响阳极氧化膜质量的因素:
硫酸浓度1、膜亮度↓从无色透明→灰色;溶液电阻↑→槽电压↑浪费电浓度↓
能;成膜速度↓(膜溶解速度↑)。
膜质量软;电解质粘度↑→水洗困难。
浓度↓200g/l.~工业实际使用范围150电流密度2、
↓→生产率↑。
↑、决定,It及可知:
膜厚δ由=K·I·tδ由It,膜厚I↓膜结构致密、硬;↑膜易“烧焦”I大小对膜质量有影响:
I21.5A/dm。
~。
一般采用不均匀性↑(大面料、复杂料)1.2槽液温度、3.
槽液温度↓(如0~5℃)氧化膜发脆,膜层透明度与染色性能↓(即吸附性能)。
槽液温度↑(如≥25℃)氧化膜疏松,(呈蜂窝状晶体,壁厚减薄),甚至起白粉。
理想的温度为20±2℃。
恒温方式:
加热——蒸汽,冷却——冷冻机或加添加剂。
4、电解电压
由于采用定电压阳极氧化则很难控制膜厚,铝合金硫酸阳极氧化采用定电流工作方式。
电解电压根据设定电流密度来确定,一般在10~22伏范围内,最佳范围15~17V。
5、氧化时间
在恒电流的条件下,由δ=K·I·t可知成膜时间和膜厚成正比。
6、杂质的影响
(1)合金成份:
Mg>2%膜变暗浊色。
Si>0.8%膜光泽↓>2%呈灰黑色,出现斑点。
Cu%↑膜色调深暗或灰黑色。
Zn↑膜呈灰暗色。
Mn即便<0.1%膜也带色与无光。
3+--→暗FFe(氟冷却液)→出现孔蚀现象。
(2)槽液杂质:
Cl、2+→正弦曲线状暗条纹。
最好使用纯水配电解液花纹和黑色斑点。
Cu3+3+↓↓(≤0.1g/l时),电解液溶解能力过强,膜厚)(3Al离子:
Al↓生成困难,耐蚀、耐磨、染色等性能↓∴配槽时,添加硫酸铝或部分3+↑电解液电阻↑,槽电压↑,Al易产生白斑点,膜的耐磨、老溶液。
3+<20g/lAl耐蚀性↓,透明性↓∴要求。
、搅拌(循环)7.
、槽外热交换器进行热交换采用槽内排管进行热交换为了降温,、压缩空气搅拌。
。
膜层“烧焦”、“起粉”影响因素:
膜层溶解电流密度——电流密度过高,将引起电解液温升加快,速度增加,对复杂工件还会造成电流分布不均,使膜层厚度不均,甚至有烧毁工件的危险。
电解液温度——温度升高,溶液粘度降低,电流密度升高(电解。
这有利于氧化膜电压一定时)或电解电压降低(电流密度一定时)。
溶解的加剧。
若同时电流密度也低,则出现粉状膜层(即起粉),而常规的硫酸法,在低温和高电流密度时,膜层易被“烧焦”。
在高温和低电流密度时,膜层易“起粉”原因分析:
一般而言,阻挡层中氧化物/铝基体金属界面上总是粗糙的,即铝金属一侧存在许多凸出部位,电流往往就集中在这些部位上,造成这些部位孔的底部电流密度大,因而孔底温度受焦耳热大的影响又升高,这样又引起电流密度加大,如此恶性循环,造成氧化膜仅在工件局部位置上增厚,出现膜层“烧焦”现象,低温高电流密度时更为突出。
而“起粉”现象则是由于膜层过度化学溶解所致。
第三节高速阳极氧化
混合法③加添加剂②脉冲阳极氧化方法:
①.
一、脉冲阳极氧化
该技术电压为矩形波,有两个工作电压,即高电压V和低电压1V。
当用V电压进行阳极氧化时,稳定电流I通过铝阳极,阳极氧112化膜形成。
当电压突然从V降至V后,则出现短时内无电流通过而21随之电流又逐渐增大的现象,经T分钟后才出现对应于电压V的稳2定电流I通过铝阳极。
电流随时间发生了畸变,这种现象叫“阳极氧2化的电流恢复现象”(或称电流的回复现象),T称为电流恢复时间。
采用脉冲电流后,利用短时间的高电流密度使膜层迅速成长,在“烧焦”现象出现前,骤然将电压降至V,在电流恢复时间内,膜2层成长中止,这样降低了氧化物/铝基体金属界面上的粗糙度。
同时膜孔内积聚的焦耳热也得到散失,使制品各部件上温差缩小。
因此,采用脉冲电流后,能较好避免“烧焦”现象的出现。
由于膜孔内热量能及时得到散失,高电流密度氧化又是短时间的所以避免了膜层的过度化学溶解,于是又克服了膜层的“起粉”现象。
由此可见,脉冲电流具有许多优点:
膜层性能提高,温度电流密度等操作条件范围扩大,电流效率高等。
工艺条件:
217v,~V=15,3.5A/dmSO18%H~I=2,42.
℃。
T=25~30μm,t=20~30分钟,δ=10~15加入添加剂二、
.
,使电解液导热性↑加入添加剂NiSO42分钟。
10g/l,I=2A/dmt=25,工艺条件:
NiSO4混合法①+②三、其它阳极氧化工艺第四节
硬质阳极氧化一、生成硬度高、耐磨性好的厚氧化膜。
2=1200~1500kgf/mm上的氧化膜硬度纯AlHB
(超过了淬火工具钢和铬镀层的硬度)2~500kgf/mmAl合金上的氧化膜硬度H=250B
300μm膜层最大厚度可达250~工艺条件:
瓷质阳极氧化(膜灰白色)二、
配方及工艺条件:
(略)硫酸交流电阳极氧化三、交流电阳极氧化膜层薄(<10μm)、发黄、硬度↓,工业上几乎不采用。
可加入草酸、甘油及添加剂。
铝及铝合金电解着色第四章
根据其显色色素体所在的位置不同,着色方法有:
化学染色法、
自然发色法、电解着色法、有机涂层着色法和复合着色法。
化学染色法第一节
化学染色法是最早用于铝阳极氧化膜着色的方法。
工艺简单,作业性好,效率高,成本低,色域宽,色泽特点:
一、
鲜艳。
方法:
二、
分两大类一液法无机染料染色法
二液法
化学着色酸性有机染料
水溶性染料
有机染料染色法碱性有机染料
油性染料
三、化学染色的机理
化学染色是色素体靠氧化膜多孔层的物理和化学作用吸附于表面层内侧。
铝阳极化膜具有30%的孔隙率,有巨大的比表面积和化学活性。
靠染料分子或离子的静电力进行的吸附叫物理吸附,吸附力取决于氧化膜的表面电位和染料性质。
.
所谓化学吸附指氧化膜与色素体以化学键、共价键或形成络合物等形式结合。
与化学吸附相比,物理吸附较弱,且受染色液温度的影响较大,所以化学着色的色牢度取决于化学吸附作用。
四、无机染料染色
1、一液法:
将阳极氧化膜浸入一种溶液中,这种金属盐在膜孔
内水化生成色淀而使膜层显色。
2、二液法:
将阳极氧化膜先浸入一种盐溶液中,取出经清洗后
再浸入另一种盐溶液中,两次浸渍吸附的盐发生反应生成不可溶的沉淀色素,使制品显色。
五、有机染料染色
用于铝阳极氧化膜染色的水溶性酸性染料主要有蒽醌系偶氮基以及三苯甲烷类。
六、工艺流程
基本上是:
预处理(同常规)→硫酸阳极氧化→水和纯水洗→染色→水和纯水洗→沸水封孔→烘干
第二节自然发色法
自然发色法指铝材在有机酸水溶液中经阳极氧化的同时而着色的方法。
由于氧化和着色一步完成,所以也叫一步法。
自然发色法(又称电解整体着色法)按着色原因不同,又可分为:
(开发中)电源发色法、(占主导)电解发色法、(次地位)合金发色法.
一、着色原理:
众说不一,原理不十分清楚,有如下观点:
1、合金元素及基体金属一起阳极氧化后残留于氧化膜中。
2、氧化膜中积累了由有机酸还原成的碳。
3、氧化膜中积累了有机酸生成的焦油状物质。
等等
二、合金发色法
由于合金元素不同,阳极氧化时这些元素不溶于电解液而残留在氧化膜结构中,其色素体是合金元素。
三、电解发色法
采用有机酸作主要成份,加入少量硫酸,在高电压大电流密度下着色,(DC电流)。
此法主要用在建筑型材的氧化着色上。
因其氧化膜在耐蚀性、耐候性、耐磨性方面都优于电解着色和化学染色法,曾广泛用于铝门窗、阳台、围栏等建筑型材及车辆外装材上。
但在使用过程中发现成本高(耗电量为浅田法的5~6倍),色种少(色调受合金限制),控制要求严,所以逐渐被电解着色法所代替。
四、电源发色法
采用普通硫酸氧化液,施加换向电流、不对称电流或脉冲电流,由于电源波形变化,使硫酸中的硫被还原,残留于氧化膜中而显色。
第三节电解着色
一、电解着色的概念及发展历史
使金将阳极氧化后的铝材浸在金属盐的水溶液中进行交流电解,
属盐沉积在氧化膜孔中而着色的方法,称为电解着色法。
日本人将电解着色法叫浅田法,国际上通称电解着色法或二次电解着色法。
二、电解着色的发展趋势
1、防护—装饰性着色膜的发展趋势
2、电解着色在机能方面的发展趋势
三、电解着色膜的特点和着色液的分类
1、电解着色膜的特点
2、电解着色液的分类(见后面附录)
四、电解着色的原理
电解着色实质是电镀,即是金属离子的一种电化学还原现象。
将阳极氧化铝置于金属盐溶液中,施加低压交流电,金属离子被电化学还原,以胶粒子状态沉积在氧化膜孔隙的底部,通过金属胶粒对光的散射作用而显色的一种方法。
1、氧化膜的结构和性质
阻挡层——厚150?
硫酸阳极化膜→孔径约120?
10um厚复合膜多孔层孔壁厚约300?
2/mm4~5亿孔孔密度2、浅田法铝阳极氧化电解着色的必要条件:
1)、采用酸性水溶液、交流电;
2;0.35A/dm~0.1、使用低电流密度2).
3)、采用的重金属盐能溶于水,且具还原和氧化作用;
4)、采用惰性材料,如石墨、不锈钢作对电极。
五、电解着色液
铝建筑型材着色膜以青铜系应用最为普及,九十年代约占我国铝电解着色的95%以上。
青铜色系包括香槟色(浅青铜色)——青铜色——深青铜色(棕色)——咖啡色——古铜色——黑色等六色,其中咖啡色只有在Ni—Sn混盐中才能获得。
有许多单金属盐(Ni、Co、Sn)着色液和混盐着色液(Ni—Sn、Ni—Co、Ni—Zn、Ni—Mn、Pb—Zn)等都可以获得青铜色系。
我国工业上应用的有Ni、Co、Sn和Ni—Sn混合盐。
应用最多的是Sn盐和Ni—Sn混合盐,其