文献综述化工类资料.docx
《文献综述化工类资料.docx》由会员分享,可在线阅读,更多相关《文献综述化工类资料.docx(11页珍藏版)》请在冰豆网上搜索。
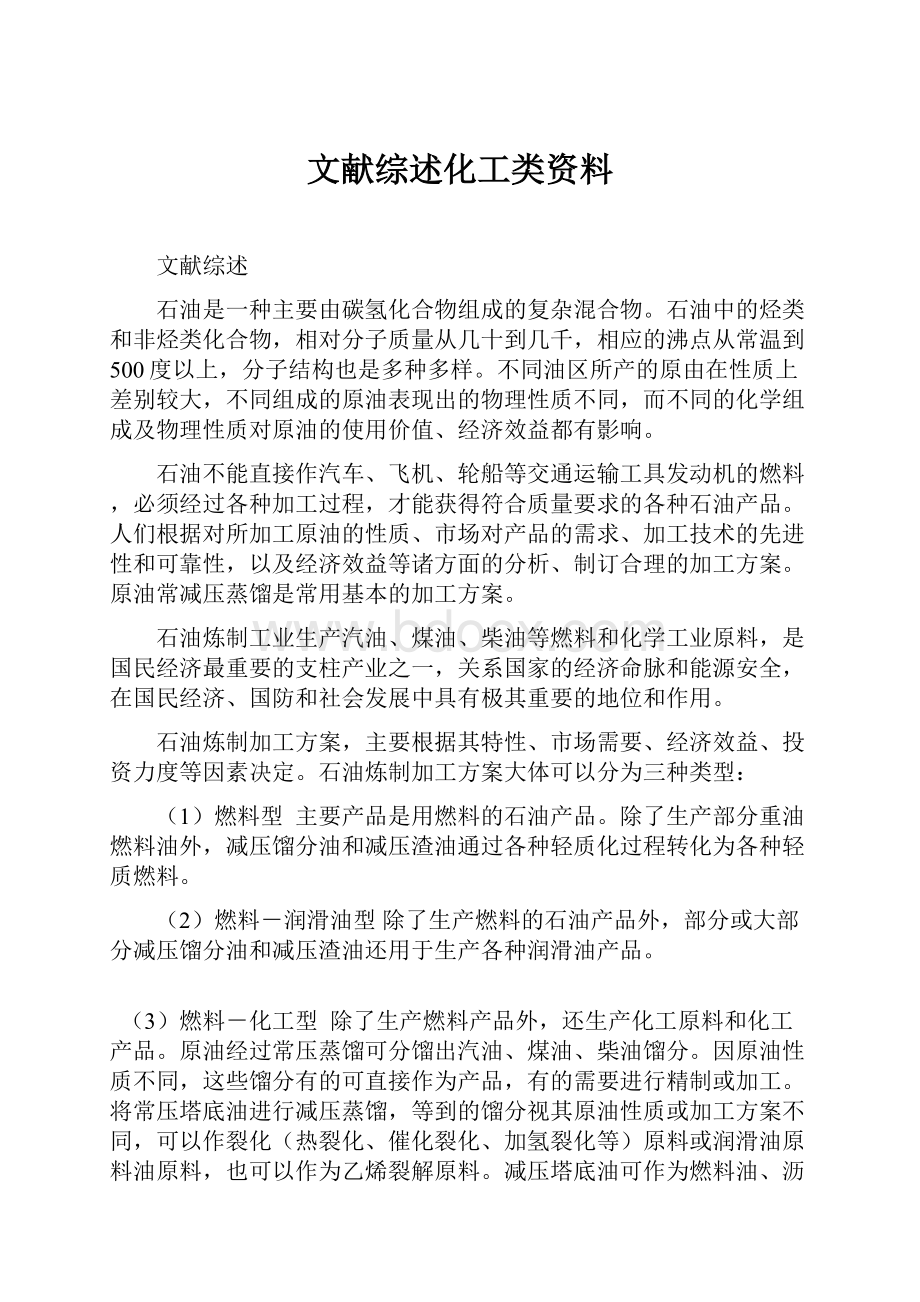
文献综述化工类资料
文献综述
石油是一种主要由碳氢化合物组成的复杂混合物。
石油中的烃类和非烃类化合物,相对分子质量从几十到几千,相应的沸点从常温到500度以上,分子结构也是多种多样。
不同油区所产的原由在性质上差别较大,不同组成的原油表现出的物理性质不同,而不同的化学组成及物理性质对原油的使用价值、经济效益都有影响。
石油不能直接作汽车、飞机、轮船等交通运输工具发动机的燃料,必须经过各种加工过程,才能获得符合质量要求的各种石油产品。
人们根据对所加工原油的性质、市场对产品的需求、加工技术的先进性和可靠性,以及经济效益等诸方面的分析、制订合理的加工方案。
原油常减压蒸馏是常用基本的加工方案。
石油炼制工业生产汽油、煤油、柴油等燃料和化学工业原料,是国民经济最重要的支柱产业之一,关系国家的经济命脉和能源安全,在国民经济、国防和社会发展中具有极其重要的地位和作用。
石油炼制加工方案,主要根据其特性、市场需要、经济效益、投资力度等因素决定。
石油炼制加工方案大体可以分为三种类型:
(1)燃料型主要产品是用燃料的石油产品。
除了生产部分重油燃料油外,减压馏分油和减压渣油通过各种轻质化过程转化为各种轻质燃料。
(2)燃料-润滑油型除了生产燃料的石油产品外,部分或大部分减压馏分油和减压渣油还用于生产各种润滑油产品。
(3)燃料-化工型除了生产燃料产品外,还生产化工原料和化工产品。
原油经过常压蒸馏可分馏出汽油、煤油、柴油馏分。
因原油性质不同,这些馏分有的可直接作为产品,有的需要进行精制或加工。
将常压塔底油进行减压蒸馏,等到的馏分视其原油性质或加工方案不同,可以作裂化(热裂化、催化裂化、加氢裂化等)原料或润滑油原料油原料,也可以作为乙烯裂解原料。
减压塔底油可作为燃料油、沥青、焦化或其它渣油加工(溶剂脱沥青、渣油催化裂化、渣油加氢裂化等)的原料。
一、设计方案
设计一套年处理量为320万吨俄罗斯原油加工装置,由于原料中轻组分不多,所以原油蒸馏装置采用二段汽化,设计常压塔,减压塔。
设计中采用水蒸气汽提方式,并确定汽提水蒸汽用量;由于浮阀塔操作弹性大,本设计采用浮阀塔。
原油蒸馏在炼油厂是原油首先要通过的加工装置。
一般包括预处理系统(原油电脱盐)、常压分馏系统、减压分馏系统、注剂系统、轻烃回收系统(加工轻质原油且达到经济规模时一般设置轻烃回收系统)等。
常压蒸馏就是在常压下对原油进行加热、气化、分馏和冷凝。
如此得到各种不同沸点范围的石油馏分。
常减压蒸馏是指在常压和减压条件下,根据原油中各组分的沸点不同,把原油“切割”成不同馏分的工艺过程。
二、生产规模
规模原油处理量320万吨/年。
按年开工8000小时计,即处理量为400000kg/h。
三、工艺技术路
大港原油属于低硫环烷─中间基原油。
煤油具有相当好的挥发性能,比较高的闪点,适宜的粘度等特性,是一种优良的有机溶剂,有着广泛的应用前景,但是,直馏煤油和一般的加氢煤油芳烃含量都较量,氮的非烃化合物也很多,致使在使用过程中,不仅使人感到有不舒服的臭味,还对人体有害。
在应用上,煤油馏分除用作喷气燃料、特种溶剂油、灯用煤油以外,还有很大一部分作为铝轧油基础油使用。
由于铝轧制在冷却、润滑和改善铝制品表面光洁度等方面都极其重要的作用,因此,随着铝加工业的迅猛发展,铝轧制油的用量越来越大。
铝轧制油除应用具有馏分范围窄、饱和烃含量高、闪点高的特点外,还要求具有较低的硫含量和芳烃含量。
煤油加氢工艺是生产高档铝轧制油最有效的工艺手段,该工艺主要是对其进行深度脱硫、脱氮和脱芳烃。
采用加氢法生产无味煤油、铝轧制油,有着其它方法无法比拟的优点。
首先是产品质量好,收率高,其中产品芳烃含量小于0.1%;其次是不产生酸渣、碱渣等污染物,属于环境友好工艺。
特种油品精馏与一般的炼油装置不同,馏分窄分馏精度要求高,产品的种类繁多,生产操作完全由市场决定,操作灵活要求非常高,根据产品方案要求,分馏部分采用双分馏塔多侧线抽出,其中第二分馏塔为减压操作,满足不同产品分割及质量要求。
四、工艺技术特点
由于装置规模较小,在保证安全平衡生产的前提下,尽量简化工艺流程和自动控制系统,以节省工程投资。
反应部分采用冷高压分离流程。
分馏部分设置两台分馏塔,其中第二分馏塔为减压操作,两台分馏塔产品侧线抽出及塔底均设重沸器,塔内装填高效规整填料,确保分馏精度。
设置热载体回执系统,热载体作为塔底重沸器热源。
开题报告
一、常减压蒸馏技术现状
(1)国外蒸馏装置技术现状及发展趋势
炼油传厂的大型化是提高其劳动生产率和经济效益,降低能耗和物耗的一项重要措施。
按2004年一月底的统计,全世界共有717座炼油厂,总加工能力4103Mt/a。
其中加工能力在10Mt/a以上的炼油厂126座,分散在34个国家和地区,有16座加工能力在20Mt/a以上。
现在单套蒸馏装置一般都在5Mt/a以上,不少装置已达到10Mt/a。
现在最大的单套蒸馏装置处理量为15Mt/a。
整体蒸馏装置将原油分为:
常压渣油、含蜡馏分油、中间馏分油和石脑油组分。
常压部分出常压渣油、中间馏分和石脑油以下的馏分。
中间馏分在加氢脱硫分馏塔中分馏煤油、轻、重柴油,常压渣油进入高真空减压蒸馏,分馏出的蜡油作为催化裂化装置和加氢裂化装置的原料。
整体蒸馏装置可以节省投资30%左右。
产品质量方面,国外蒸馏装置典型的产品分馏精度一般为:
石脑油和煤油的脱空度ASTMD86(5%-95%)13℃;煤油和轻柴油的脱空度ASTMD86(5%-95%)-20℃;轻蜡油与重蜡油的脱空度ASTMD1160(5%-95%)5℃,润滑油基础油也基本满足窄馏分、浅颜色。
(2)国内蒸馏装置技术现状
我国蒸馏装置规模较小,大部分装置处理能力为2.5Mt/a,仅有几套装置的加工能力超国4.5Mt/a。
我国蒸馏装置的总体技术水平与国外水平相比,在处理能力、产品质量和拨出率方面存在较大的差距。
最近几年,随着我国炼油工业的发展,为缩短与世界先进炼油厂的差距,我国新建蒸馏装置正向大型化方向发展,陆续建成了镇海、高桥8Mt/a及西太平洋10Mt/a等大型化的蒸馏装置等,其中高桥为润滑油型大型蒸馏装置,拟建的大型蒸馏装置也基本为燃料型。
我国蒸馏装置侧线产品分离精度差别较大,如中石化有些炼油厂常顶和常一线能够脱空,但尚有40%的装置常顶与常一线恩氏蒸馏馏程重叠超过10℃,最多重叠达86℃。
多数装置常二线与常三线恩氏蒸馏馏程重叠15℃以上,实沸点重叠则超出25℃。
润滑油馏分切割也同国外先进水平存在一定差距,主要表现在轻质润滑油馏分的发挥及中质润滑油馏分的残碳、颜色和安定性等方面存在差距较大。
三、设计任务依据
设计任务有指导教师指定课题
四、主要原材料
主要原材料是俄罗斯原油,其属低硫环烷─中间基原油。
五、节能措施
炼油厂加工所消耗的能量占原油加工量的4%-8%,而常减压蒸馏装置又是耗能量大的生产装置。
2001年中石化常减压蒸馏装置平均能耗为0.496GJ/t(不包括不开减压装置),最低0.438GJ/t,最高0.686GJ/t,与国外常减压蒸馏装置相比,我国常减压蒸馏装置的能耗显然偏高,具有较大的节能潜力。
常减压蒸馏装置能耗主要是工艺过程必须消耗的燃料、水蒸汽、电力、水等所产生的能量消耗。
其中燃料能耗比例最大,达60%-85%;其次是电和蒸汽,均占总能耗的10%-15%;水的能耗的占总能耗的4%左右。
因此,应从降低燃料消耗着手,节约能源。
常减压蒸馏装置主要从五个方面着手:
改进工艺流程、提高设备效率、优化操作、采用先进的自动控制流程、加强维修管理。
降低燃料消耗,就是在保证产品收率和质量的条件下,减少加热炉有效热负荷和提高加热炉效率。
加热炉负荷通常包括加热常压塔和减压塔进料及蒸汽所需热负荷。
减少加热炉有效负荷的主要措施有:
提高常压炉进料温度、降低加热炉出口温度、减少加热炉进料量(包括蒸汽);提高加热炉热效率的主要措施有:
回收烟气余热,降低排烟温度、提高燃烧器燃烧效率、优化及自动控制加热炉各操作参数(如烟气含氧量、炉膛负压,排烟温度等)、应用新型隔热材料,减少加热炉热损失。
同时,节能措施的采用,不仅在技术上可行,而且必须经济合理。
节能与投资的关系实质上是操作费用与投资的关系在节能领域的体现。
工艺流程设计
一、原料油性质及产品性质
俄罗斯原油一般性质如下表所示:
名称
单位
数值
名称
单位
数值
密度
D204
0.8896
含盐
mgNaCl/L
74
特性因数
11.8
水分
%
1.4
运动粘度(50℃)
Mm2/s
20.64
初馏点
℃
82
凝点
℃
20
200℃馏出
%
10
含蜡量
%
14.1
300℃馏出
%
25
沥青质硅胶胶质
%
12.56
Ni含量
PPm
18.5
残炭
%
3.5
V含量
PPm
〈1
含硫
%
0.14
Cu含
PPm
0.76
俄罗斯原油实沸点蒸馏数据:
累计馏出%(重)
累计馏出%(体)
馏出温度℃
2.42
3
气体
6.44
8.13
15~60
10.07
12.47
60~80
14.2
17.16
80~100
18.74
22.17
100~120
24.96
28.89
120~145
29.4
33.59
145~165
32.96
37.3
165~180
36.79
41.24
180~200
40.63
45.13
200~220
42.53
47.05
220~230
48.48
49
230~240
48.48
52.97
240~260
52.29
56.98
260~280
56.21
60.47
280~300
59.78
63.91
300~320
65.36
69.2
320~350
68.38
72.02
350~370
71.34
74.76
370~400
73.61
76.84
400~420
78.99
81.77
420~450
81.98
84.49
450~470
85.72
87.83
470~500
88.55
90.34
500~530
89.23
90.93
530~540
100
100
>540
产品性质:
产 品
沸点范围
℃
产率
%(w)
D
恩氏蒸馏馏出温度 ℃
初馏
10%
50%
90%
干点
石脑油
42—150
19.4
0.7355
66
91
119
157
168.6
汽油
134—230
12.6
0.7866
166
173
181
196.8
208.7
煤油
170-276
9.3
0.8063
189.4
200.9
220.1
250.6
265.1
轻柴油
219—305
11.4
0.8213
227.6
236.0
247.5
269.4
281.1
重柴油
305-382
12.2
0.8474
303.6
312.1
331.5
341.3
重 油
>350
35.1
0.9200
二、工艺流程
(1)工艺流程
工艺流程简介:
本设计采用二段汽化的常减压蒸馏装置技术(双塔流程)。
设有常压塔、减压塔和附属的汽提塔。
原油在进入常压塔前经过电脱盐系统的脱盐、脱水后,换热到240℃,再经常压炉加热到370℃进入常压塔,经过分馏,塔顶分馏出重整原料,侧线自上而下分别出航空煤油、轻柴油、重柴油,塔底分馏出重油。
重油经减压炉加热至400℃左右,进入减压塔,塔顶抽真空,经分馏,减一线出重柴油,减二、三线出蜡油,减四线出润滑油,塔底出减压渣油。
工艺流程草图如下:
(2)塔器结构
根据设计要求和实际情况,采用板式塔。
本设计采用浮阀塔板。
其优缺点为:
优点为:
生产能力大,操作弹性大,塔板效率高,气体压降小,结构简单,造价低;
缺点为:
不宜处理易结焦,或黏度大
(3)环保措施
污染源的分析:
常减压蒸馏装置污染源有电脱盐排水、初顶排水、机泵冷却水、常顶排水、减顶排水、常压加热炉烟气、减压加热炉烟气,所以环保工作应围绕这些污染源采取相应措施。
废气处理:
1加热炉烟气
烟气中的二氧化硫与燃料中硫含量有关,使用燃料气及低硫燃制能有效降低二氧化硫的排放量。
二氧化氮的排放与燃料中的N2含量及燃烧火嘴结构有关。
2停工排放废气
装置在停工时,需对塔、容器、管线进行蒸汽吹扫,大部分存油随蒸汽冷凝水排出,还有部分未被冷凝的油气随塔顶蒸汽放空进入大气;检修时,需将塔、容器等设备的人孔打开,将残存的油气排入大气;要制定停工方案并严格执行,严格控制污染。
3无组织排放废气
一般情况下含硫废水中硫化氢及氨的气味较大,输送这种含硫废水必须密闭,如有泄漏则毒害严重。
含硫化氢废气经常泄漏的部位是在“三顶”回流罐脱水部位。
减少措施是控制好塔顶注氨。
输送轻质油品管线、碱渣管线及阀门的泄漏会造成大气污染,本装置设计常压塔顶减压阀为紧急放空所用,放空气体进入紧急放空罐。
管线阀门的泄漏率应小于2%c。
另外,蒸馏装置通常设“三顶”瓦斯回收系统,将初顶、常减顶不凝气引入加热炉作为燃料烧掉或回收,这样对节能、安全、环保均有利。
废水处理
1电脱盐排水
制电脱盐过程所排的废水,来自原油进装置时自身携带水和溶解原油中无机盐所注入的水。
此外,加入破乳剂使原油在电场的作用下将其中的油和含盐废水分离。
由于这部分水与油品直接接触,溶人的污染物较多,特别是电脱盐罐油水分离效率不高时,这部分排水中石油类和COD均较高。
排水量与注水量有关,一般注入量为原油的5%~8%。
筛选好的破乳剂、确定合适用量、提高电脱盐效率都对提高油水分离效果有利;用含硫污水汽提后的净化水回注电脱盐可减少新鲜水用量,同时减少净化水排放的挥发酚含量;增加油水镧离时间,严格控制油水界面(必要时设二次收油设施)可减少油含量。
2塔顶油水分离器排水
常减压蒸馏装置其初馏塔顶、常压塔顶、减压塔顶产物经冷后均分别进入各自的油水分离器,进行油水分离并排水。
这部水是由原油加工过程中的加热炉注水,常压塔和减压塔底注汽产品汽提塔所用蒸汽冷凝水,大气抽空器冷凝水,塔顶注水,缓蚀剂所含水分等组成。
由于这部分水与油品直接接触,所以AN染物质较多,排水中硫化物、氨、COD均较高。
排水中带隋况与油水分离器中油水分离时间、界面控制是否稳定有关。
正常生产情况下,严格控制塔顶油水分离器油水界面是防止排‘重带油的关键。
3机泵冷却水机泵冷却水
由两部分构成,一部分是冷却泵体用水,全部使用循K冷却后进循环水回水管网循环使用。
另一部分是泵端面密封冷却K,随用随排入含油废水系统。
一般热油泵需冷却水较多,如端面十漏油较多.则冷却水带油严重。
如将泵端面密封改为波纹管式端i封,可以减少漏油污染。
4装置其他排水
a.油品采样该装置有汽油、煤油、柴油等油品采样口用于采j品进行质量检测。
一般在油品采样前,都要放掉部分油品,以便:
次采样滞留在管线中的油置换掉。
这部分油品会污染排水。
可采『动分析仪或密闭采样法,也可以将置换下的油品放入污油罐中回以减少污染。
b.设备如拆卸油泵、换热器等,需将设备内的存油放掉进入系统。
如果能在拆卸设备处,设专线将油抽至污油回收系统(或罐),可以减少污染。
c.停工扫线装置停工需将设备、管线中的存油用蒸汽吹扫于此阶段排放污染物最为严重。
应制定停工方案并严格执行,尽量油送至污油罐区,严禁乱排乱放。
d.地面冲洗原油泵、热油泵、控制阀等部位所在地面最易遭受污染。
一般不允许用水冲洗的地面,通常用浸有少量煤油的棉纱插去油污。
e,装置废水排放计量各种废水排出装置进入全厂含油废水系统之前,要设置计量井,并制定排水定额。
对控制排放废水的污染较为有效。
噪声防护
在生产装置,噪声的主要来源是:
①流体振动所产生的噪声。
如流体被节流后发出的噪声(尤其是调节阀节流造成的)、火焰燃烧所造成的气体振动等。
②机械噪声。
指各种运转设备所产生的噪声。
③电磁噪声。
指由电机、脱盐变压器等因磁场作用引起振动所产生的噪声。
加热炉噪声的防治一般有下列几种方法,可根据不同情况选用。
(1)采用低噪声喷嘴。
(2)喷嘴及风门等进风口处采用消声罩。
(3)结合预热空气系统,采用强制进风消声罩。
(4)炉底设隔声围墙。
电机噪声的防治一般有:
(1)安装消声罩。
一般应选用低噪声电机,若噪声不符合要求时,可加设隔声罩(安装全部隔声罩或局部隔声罩。
)
(2)改善冷却风扇结构、角度。
(3)大电机可拆除风扇,用主风机设置旁路引风冷却电机。
空冷器噪声的防治一般可选用以下几种方法:
(1)设隔声墙,以减少对受声方向的辐射。
(2)加吸声屏,可设立式和横式吸声屏。
(3)加隔声罩。
(4)用新型低噪声风机。
参考文献
[1]林世雄主编,《石油炼制工程》北京,石油工业出版社,2002
[2]米镇涛主编,《化学工艺学》北京,化工工业出版社,2005
[3]廖久明等编,《石油化学》北京,中国石化出版社,2009
[4]陈声宗主编,《化工设计》北京,化学工业出版社,2008