精益术语和定义汇总.docx
《精益术语和定义汇总.docx》由会员分享,可在线阅读,更多相关《精益术语和定义汇总.docx(14页珍藏版)》请在冰豆网上搜索。
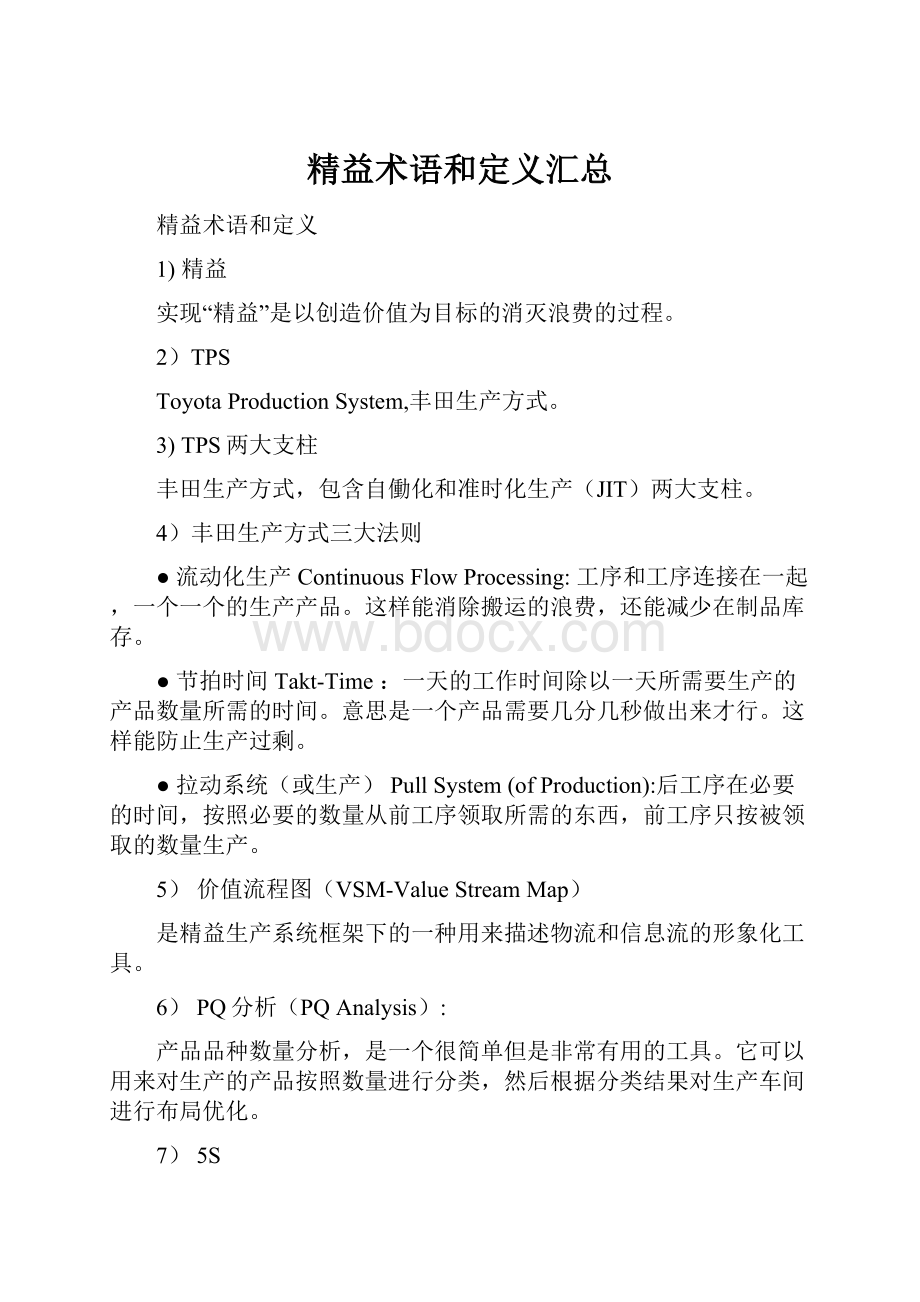
精益术语和定义汇总
精益术语和定义
1)精益
实现“精益”是以创造价值为目标的消灭浪费的过程。
2)TPS
ToyotaProductionSystem,丰田生产方式。
3)TPS两大支柱
丰田生产方式,包含自働化和准时化生产(JIT)两大支柱。
4)丰田生产方式三大法则
●流动化生产ContinuousFlowProcessing:
工序和工序连接在一起,一个一个的生产产品。
这样能消除搬运的浪费,还能减少在制品库存。
●节拍时间Takt-Time:
一天的工作时间除以一天所需要生产的产品数量所需的时间。
意思是一个产品需要几分几秒做出来才行。
这样能防止生产过剩。
●拉动系统(或生产)PullSystem(ofProduction):
后工序在必要的时间,按照必要的数量从前工序领取所需的东西,前工序只按被领取的数量生产。
5)价值流程图(VSM-ValueStreamMap)
是精益生产系统框架下的一种用来描述物流和信息流的形象化工具。
6)PQ分析(PQAnalysis):
产品品种数量分析,是一个很简单但是非常有用的工具。
它可以用来对生产的产品按照数量进行分类,然后根据分类结果对生产车间进行布局优化。
7)5S
●整理Seiri:
将需要和不要的东西分开,不需要的东西立即处理;
●整顿Seiton:
将需要的东西按规范摆好以方便使用;
●清扫Seiso:
日常清扫、保持完好可用;
●清洁Seiketsu:
保持整理、整顿、清扫的状态,并标准化;
●素养Sitsuke:
个人掌握规定或规范并付于实践,养成良好习惯。
8)目视化管理
基本在于使什么是正常,什么是不正常明确化。
从质量上说,就是使不良品暴露出来,从数量上来说,就是相对于计划使人一眼就能知道有在进展。
不仅是机器、生产线,这种思考方法也适用于东西的摆放、在制品数量、“看板”的传递方法、人的作业方法等任何问题。
导入丰田生产方式的现场都在彻底贯彻“目视化管理”。
目视化也可以叫做可视化。
9)安东(Andon)
也叫信号灯,是“目视化管理”的代表,这是挂在生产管理现场的“停线显示板”、设备呼叫灯等。
关于异常表示灯的状态就是,运行当中亮绿灯;生产线慢了操作人员需要调整,寻求帮助的时候亮黄灯;如果是为了纠正异常需要停线的话,亮红灯。
为了彻底消除异常,就要建立不能怕停线的思想。
10)准时化生产(JIT-Just-In-Time)
如果能够在所需要的时候,按所需数量,获取所需要的东西,那么就可以清除生产现场的浪费、不均衡、不合理,提高生产效率。
给思想的开山鼻祖是丰田汽车的创始人-丰田喜一郎,其后继者将此思想展开,概况成为了一个生产体系。
不单是intime,而是justintime,这是一个重要的关键。
“Just-In-Time”和“自働化”共同形成丰田生产方式的两大支柱。
11)自働化(Jidoka)
在丰田的生产方式当中,必须完全是带人字旁的“自働化”。
“自働化”是指将人类的智慧赋予机器。
“自働化”的思想来自于丰田公司鼻祖丰田佐吉的自动织布机。
丰田自动织布机的构造是如果经线断了或是纬线没了,机器会立即停机,即机器内置了使其判断好坏的装置。
不仅在机器上,丰田还将其思想扩大到了有操作人员的生产线上。
即彻底贯彻如果发生异常,操作人员要把生产线停下来的规则。
通过“自働化”,可以防止产生不良品,控制生产过剩,还有能自动检查生产现场异常的益处。
“自働化”含有如果发生异常情况,就自动停机或停线的意思。
12)单元式生产线
一系列的机器按适当的流程顺序排列,工人只需站在自己的单元内,物料会从外面递送给他们的生产线。
13)单件流
一种产品从一个工位移动到下一个工位时,一次只能移动一个,工位之间不允许有存货的生产原理。
14)瓶颈
影响整个系统产量的工位或流程。
15)节拍时间(TT-Takt-Time)
Takt-Time生产节拍又称客户需求周期、产距时间,是指在一定时间长度内,总有效生产时间与客户需求数量的比值,是客户需求一件产品的市场必要时间,Takt-Time=计划运转时间/客户总需求数量。
节拍时间是20世纪30年代德国飞机制造工业中使用的一个生产管理工具。
(Take是一个德国词汇,表示像音乐节拍器那样准确的间隔时间),指的是把飞机移动到下一个生产位置的时间间隔。
这个概念于20世纪50年代开始在丰田公司被广泛应用,并于60年代晚期推广到丰田公司所有的供应商。
丰田公司通常每个月评审一次节拍时间,每10天进行一次调整检查。
16)循环时间(CT-Cycle-Time)
生产过程中,一个操作者完成所有生产动作循环所需的时间。
17)机器自动时间
机器生产一件产品所需要的时间,不包括装料与卸料时间。
18)机器周期时间
机器生产一件产品所需要的时间,包括装料与卸料时间。
19)工人周期时间
一个工人按预定次序完成所有操作所需要的时间,包括装料和卸料,但不包括等待的时间。
20)前置周期(LT-LeadTime)
是指从采购方开始下单订购到供应商交货所间隔的时间,通常以天数或小时计算。
减少前置时间可以使生产商和零售商平均库存水平得到较少,而且前置时间的减少可以使零售商订货模型更加稳定,也会给生产商的生产决策带来很大好处,能保证处于同一条供应链上的生产商和零售商实现双赢。
21)生产周期(MCT-ManufactureCycleTime)
生产周期时间(MCT,ManufacturingCycleTime),也叫制造周期,是从生产计划发放到车间直到最后成品入库的时间。
预备时间越短,制造商的库存越少,当市场需要变化时报废的材料越少,调整适应变化的灵活性越大。
制造周期时间(MCT),工厂车间可能出现的问题越多。
22)在制品(WIP-WorkInProcess)
原料或零件已被处理成半成品,但尚未成为产品,尚未完成入库手续。
广义:
包括正在加工的产品和准备进一步加工的半成品;狭义:
仅指正在加工的产品。
23)库存周转率
库存周转率(英文为Inventoryturnover一般缩写为ITO),一种衡量材料在工厂里或是整条价值流中,流动快慢的标准。
最常见的计算库存周转的方式,就是把期间使用产品的数量(或成本)作为分子,除以期间平均库存数量(或价值)。
因此,库存周转率=期间使用品数量(或成本)/期间平均库存数量(或价值)。
●库存周转率计算公式是(以月平均库存周转率为例):
a)原材料库存周转率=月内出库的原材料数量(或总成本)/原材料平均库存
b)在制库存周转率=月内出库的原材料数量(或总成本)/平均在制库存
c)成品库存周转率=月销售成品数量(或总成本)/成品在库平均库存
24)先进先出(FIFO-FirstInFirstOut)
是指根据先入库先发出的原则。
25)标准作业
一种以人为中心,按照没有浪费的步骤,通过人和设备的工作组合进行最有效率生产的方法。
标准作业三大要素:
●节拍时间Takt-Time
●作业顺序WorkingSequence:
不是产品生产的加工顺序,而是作业人员搬运东西,往设备上装、卸料等作业顺序。
●标准在制品StandardizedIn-ProcessStock:
装在设备上的物品、传送带上的物品、需要冷却时间的物品等,指为了能够按照同样的步骤,进行循环性作业的所需最低限度的在制品。
26)标准作业票
是明确工程全体技能员每个作业状态,直接反映操作者走动路线、设备、工装、工具、工位器具实际位置的目视简图,是发现问题的改善工具、是监督标准作业执行的管理工具。
27)标准作业组合票
以节拍时间为基础,通过记录操作者的手动时间(手工作业时间)、自动时间(机械自动加工时间)、步行时间和等待时间,以线图形式组合人与设备的动作、确定作业分配和作业顺序的改善工具。
28)山积表
是将操作者的一个循环时间或各分解动作时间,以直方图的形式表现出来,以研究作业时间结构的一种改善工具。
29)工程别能力表
表现部品在各工程进行加工时,工程的定时生产能力的方式。
“是算出不论加多少人,最大生产能力的方式”。
此表需计入手工作时间、机械设备自动加工时间及刃具交换时间;是制作标准作业组合票的基准。
30)作业编成
依据生产线个产品的TT需求,考虑生产所需生产设备,及各要素作业的CT等作业限制因数来决定:
1)生产线及其人力配置;2)每个作业人员的工作分配及产能设定。
31)作业指导书
将标准操作步骤和要求以同一的格式描述出来,用来指导和规范日常工作,是指导员工正确作业的指导文件。
32)生产效率
也叫生产力,指单位人时的产出。
33)拉动生产
以客户或后工序需求来拉动前工序的生产。
34)SMED:
SingleMinuteExchangeofDie,单分钟的快速换模(或称:
快速换模,快熟切换)
35)看板Kanban
“看板”是用来实现形成丰田生产方式第一大支柱“JustInTime”的管理工具。
多为将小纸片放入四方形塑料袋的一种东西。
该纸片上显示领取“什么,多少”,还有“什么东西怎样去做”。
“JustInTime”生产是指后道工序在所需要的时候,按所需数量去前道工序领取所需要的东西,前道工序按照所被领取的数量进行补充生产。
这种情况是后道工序去前道工序领取,作为“领料信息”或是“搬运信息”,连接两者之间的称为“领料看板”或“搬运看板”。
这是“看板”其中的一个重要的作用。
还有一个就是用来让刚才的前道工序按照所领取数量生产,进行生产指示的“工序内看板”。
这两种“看板”共同的丰田汽车工厂内的各道工序内、丰田汽车和配套企业间、还有各个配套企业内部的各道工序间…以这些情况进行传递。
其他还有不得不批量生产的,比如冲压部件的生产所用的“信息看板”。
“看板”可以说是包含人类想法的一种“信息”。
丰田生产方式或者精益生产所说的“看板”,不同于我们一般管理中使用的管理看板或目视看板。
36)5W2H
Why,What,When,Who,Where,How,Howmuch
37)A3报告
A3报告(A3Report)是一种有丰田公司开创的方法,通常用图形把问题、分析、改正措施、以及执行计划囊括在一张大的(A3)纸上。
在丰田公司,A3报告已经成为一个标准方法,用来总结解决问题的方案,进行状态报告,以及绘制价值流图。
38)五个为什么(5Why分析)
要发现问题点,请反复问5次“为什么”,这才是丰田的科学性研究方法的基本态度。
即在丰田生产方式里,5W是5个Why。
重复5次“为什么”,就知道真正的原因,也知道了怎样做(HOW).找“真因”而不是“原因”,“原因”的下面隐藏着“真因”。
不管什么情况,如果不问“为什么”、“为什么”去挖掘原因,抓住真正的原因采取对策的话,就不能实行有效的行动。
39)根本原因(RootCause)
经过验证的导致问题发生的原因,根本原因消除了问题不会重复再发生,根本原因也叫真因。
从问题发生的原因来看,有分为几个层次的原因,可能原因(表面原因)、最可能原因、根本原因
40)省力化→省人化→少人化
如果导入高性能的大型设备,可以省人力,即实现“省力化”,但是更重要的是通过其设备减去人手,将其安排到所需要的部门,进行“省力化”比如说即使减了0.9的人也是毫无意义的,因为只有减了一个人才能降低成本挂钩,所以必须实现“省人化”,进行了“自働化”,但减产的时候,却不能按产量减少的比例减人。
这是因为“自働化”是定员制。
在低速增长的时候,需要使用智能打破定员制,建立一跳能够对应所需生产数量,无论是几个人都能进行生产的生产线。
这就是【少人化】的目的。
41)增值活动和非增值活动
增值活动(ValueAdded)是客户愿意出钱购买的一些活动,而这些活动会改变产品的外观、形状、装配关系、功能型能等。
非增值活动(Nonvalueadded)是任何占用时间,单不能为你的顾客创造价值活动。
在生产活动中非增值活动又分为非增值但必要的活动(如拿取钻孔机、放下扳手、开质量讨论会议、清理工厂等)个非增值也不必要的活动,即纯粹是非增值活动(如:
走动,去取零件。
等待时间。
储存零件、运输、补修不良品、过多库存的成本等),这部分活动也叫浪费。
42)浪费(Muda):
未能创造价值;
生产活动中不能生产增值也不必要的活动都属于浪费,具体的将生产现场的浪费分类,有七大浪费①生产过剩的浪费、②等待的浪费、③搬运的浪费、④加工的浪费、⑤库存的浪费、⑥动作的浪费。
⑦不良品的浪费、以上的浪费。
从浪费的形态上,
43)Muri:
员工或设备的负荷过重
44)Mura:
不均衡
45)动作和工作
就算动作再好,也不能成为工作。
工作是指有增值的活动,动作却不一定产生增值。
因此基层管理人员必须努力变部下的“动作”为“工作”。
46)防错Pokayoke
防错法,日文称Pokayoke,又称愚巧法、防呆法。
意即在过程失误发生之前即加以防止。
是一种在作业过程中采用自动作用、报警、标识、分类等手段,使作业人员不特别注意也不会失误的方法。
47)流动作业与传送作业
流动作业指产品在流动当中,各工序对其加工被附加了价值。
如果只是使用传送带传送产品的话,这就不是流动作业,而是传送作业。
作为丰田生产方式的基本条件,我们提出要使生产现场(流动作业)。
48)操多道工序
比如在机械加工的工序当中,按照生产流程,纵向平行地各摆有车床、铣床、钻床5台。
如果一个操作人员操作5台车床称为(操多台机)。
操铣床5台、钻床5台也是同样。
与此不同,一外操作人员像1台车床、一台铣床、一台钻床…这样,负责多道工序(操多道工序)。
因为在丰田生产方式当中很重视生产的流动化,彻底努力实现(操多道工序)。
这同(少人化)直接相关。
对于生产现场的操作人员来说,是要从(单能工)发展成为(多能工)。
49)建立接力区
游泳当中的接力,快的人、慢的人都要负责同样的距离。
田径接力,快的人可以在接力区照顾慢的人。
在生产线作业当中也希望是田径接力的方式。
为了提高生产线的效率,基层管理人员建立接力区是很重要的事情。
50)不建立孤岛
如果零零散散地安排人员的话,就做不到互助。
如果对工作组合进行研究,作业分配或作业安排能够做到互助的话,也能够实现少人化。
如果在生产现场建立的流程是活的话,就不会产生孤岛。
51)生产的均衡化(Heijunka)
也叫平准化,在生产现场,产品的排产波动越大,浪费就会越多。
因为设备、人员、库存及其它生产所需要的要素必须要配合高峰期进行准备。
如果后工序在时间和数量上以波动的形式去领料的话,越往前工序去,其波动的大小将会不断扩大。
包括配套合作企业,要防止所有生产线上的波动,就必须努力将最终装配线的波动降为零。
丰田汽车的各道最终工序不固定排同种东西,而是以生产一台台不同的车为前提,进行均衡化生产。
52)不要怕停线
生产线停不下来不是做得非常好的生产线就是存在很大问题。
如果线上安排了很多人工作,流程不停,问题也暴露不出来。
这是最好的生产线。
关键是要使生产线能够按照需要随时能够停下来,来防止产生不良品,通过不断改善,建立一条人数少的,最后不需要停下来的,体质过硬的生产线。
一点都不用怕停线。
53)负荷率
负荷率是指相对于该设备在一定时间内满负荷运转能力的当下时间的生产的实际产量。
销售情况不理想了,负荷率当然降低。
相反如果订单增加,因为加班或轮班倒也有可能达到120%的负荷率。
负荷率的好坏是相对于所需数量的设备选择的问题。
54)可动率
可动率是指想开机时候随时可以运转的状态。
这个理想是100%。
因此既要落实保养,还要实现缩短转产时间。
55)稼动率
稼动率是指设备在所能提供的时间内为了创造价值而占用的时间所占的比重。
是指一台机器设备可能的生产数量与实际生产数量的比值。
56)设备总效率
OEE的组成包含三大指标:
时间稼动率(可用率),性能稼动率(表现指数),良品率(质量指数),OEE=时间稼动率X性能稼动率X良品率
时间稼动率=负荷时间—停机时间/负荷时间
性能稼动率=理论节拍时间*投入数量/稼动时间
良品率=投入数量—不良数量/投入数量
57)从作业改善到设备改善
生产现场的改善方案从大方面分有决定操作上的规范,重新分配,明确标示物品的摆放区的作业改善和引进设备,将设备自働化的设备改善。
设备改善要花钱,而且没办法修正。
在精益生产方式中,首先要彻底地进行作业的步骤化,标准化。
由此大部分的问题都可以改善。
先行(设备改善)的话,生产现场就不会进行(作业改善)。
应该进行(作业改善)之后再进行(设备改善)。
58)产生效益的IE
IE即工业工程师是从美国伟来的生产管理技术、经营管理技术。
暂且不管它定义如何,在丰田生产方式当中,是把它当成涉及整个生产现场,在质、量、时机三者整体协调的基础上来实现成本降低的“生产方式”。
不单是学术界讨论的IE手法(method),“丰田式IE”的最大特征是同降低成本直接相关联,“产生效益的IE”。
59)TPM
全员共同参与珠生产维护(Total-member-participationproductiveMaintenance),简称全员生产维护(TotalproductiveMaintenance),这是70年代日本人在美国的生产维护体制的基础上提出的,其主要点就在“生产维护”及“全员参与”上,通过建立一个全系统员工参与的生产维护活动,使设备性能达到最忧。
同时也吸收了英国设备综合工程学、中国鞍钢宪法中群众参与管理的思想。
在非日本国家,由于国情不同,对TPM的理解是:
利用包括操作者在内的生产维护活动,提高设备的全面性能。
TPM的目标可以概括为四个“零”,即停机为零、废品为零、事故为零、速度损失为零。
60)TPM的八大支柱
●生产效率化个别改善活动
●操作者的自主保全活动
●保全部分的计划保全活动
●运转,保全的技能提升实施教育训练
●新制品,新设备的初期管理体制
●构筑品质保全体制品质保全活动
●间接管理部门的效率化间接办公活动
●安全,卫生和环境的管理体制环境安全活动
61)预防性维护(productiveMaintenance)
为消除设备失效和生产的计划外中断的原因而策划的措施,作为制造过程设计的一项输出。
62)预知性维护(productiveMaintenance)
也叫预测性维护或预见性维护,基于针对过程数据,通过预测可能的失效模式以避免维护性问题的活动。
这些方法可包括对有关项目的评审:
诸如制造厂建议、工具磨损、正常运行时间的优化、统计过程控制数据与预防维护活动的相互关系、易损工装的重要特性,也可以针对设备状态进行监控(如:
流体分析、红外线控制、振动分析等)的评审开展针对性维护活动。
63)BM:
事后保养,Break-downMaintenance
64)PM:
生产保养,ProductiveMaintenance
65)CM:
改良保养,CorrectiveMaintenance
66)MP:
保养预防,MaintenancePrevention
67)PVM:
预防保养,PreventiveMaintenance,见60)
68)PdM,预知保养,PredictiveMaintenance,见61)
69)APQP
AdvanedProductQualityPlanning产品质量先期策划
70)FMEA
PotentialFailureModeandEffectAnalysisi潜在失效模式和后果分析
71)SPC
StatisticProcessControl统计过程控制
72)MSA
MeasureSystemAnalysis测量系统分析
73)FAI
FirstArticleInspection首件鉴定
74)Cp/Cpk
过程能力/过程能力指数,是指稳定生产(小批量生产或量产过程均可使用)的过程能力的评价指数。
75)Pp/Ppk
初始性能/初始性能指数,是指在小批量生产过程中,初始过程的性能指数。
76)控制计划
对控制产品所要求的系统和过程的形成文件的描述。
典型的控制计划分为三个阶段:
样件阶段、小批量试生产阶段、量产阶段;主要内容包含(图标格式可以根据实际情况制定):
a)基本数据
—控制计划编号;
—发布尔日期和修订日期(若存在);
—顾客信息(见顾客要求);
—企业名称/制定的现场;
—零件编号;
—零件名称/描述;
—工程更改等级;
—覆盖的阶段(样件、试生产、生产);
—主要联系人;
—零件/过程步骤编号;
—过程名称/作业描述。
b)产品控制
—与产品有关的特殊特性;
—其他要求控制的特性(编号、产品或过程);
—规范/公差。
c)过程控制
—过程参数;
—与过程有关的特殊特性;
—制造用机器、卡具、夹具、工具。
d)
—评价测量技术;
—防错;
—严格不能容量和频次;
—控制方法。
e)反应计划和纠正措施
—反应计划(包括或引用)
—纠正措施。
77)持续改进
对每天都生产更好的产品、创造更好的工作环境以及不断地提升公司业绩所做出的承诺。
78)改善(Kaizen)与改善突破(kaikaiku)
实际上,改善(Kaizen),是日语单词“Kai(改变)”“Zen(更好)”的组合,意指变得更好,可能是非常大的改变,也可能是小的、增量的改变。
西方企业往往着重突破性创新,在小量的持续改善方面则较弱,因此,这等于是教导西方企业应该注重Kaizen。
改善(Kaizen)教导如何在小团队中有成效地工作、解决问题、记录与改善流程、收集与公析资料的技巧,以及如何在同僚团队中自我管理,它把决策或规划提案的工作放给员工,要求他们在作出及执行任何决策之前,必须开放讨论,并达成团体共识。
在某些情况下,日语kaikaiku(译注:
大改革)指全神贯注、团队合作、时间紧迫、快速布置的持续改善活动,指的是重大的、革命性的改变。
改善是追求尽善尽美、并在日常运作中维系丰田生产制度的大原则。