课程设计小方坯连铸机设计 二.docx
《课程设计小方坯连铸机设计 二.docx》由会员分享,可在线阅读,更多相关《课程设计小方坯连铸机设计 二.docx(33页珍藏版)》请在冰豆网上搜索。
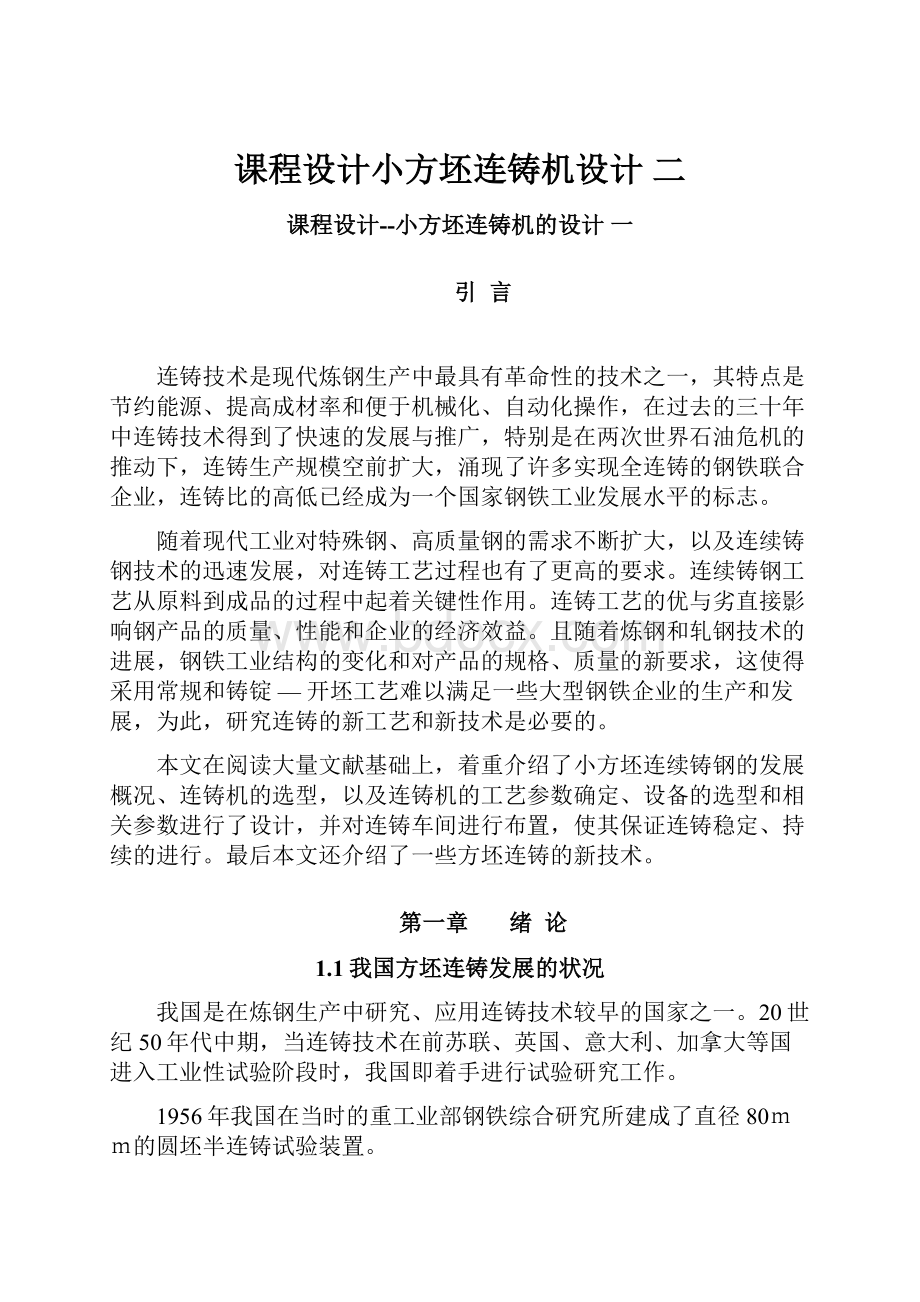
课程设计小方坯连铸机设计二
课程设计--小方坯连铸机的设计 一
引 言
连铸技术是现代炼钢生产中最具有革命性的技术之一,其特点是节约能源、提高成材率和便于机械化、自动化操作,在过去的三十年中连铸技术得到了快速的发展与推广,特别是在两次世界石油危机的推动下,连铸生产规模空前扩大,涌现了许多实现全连铸的钢铁联合企业,连铸比的高低已经成为一个国家钢铁工业发展水平的标志。
随着现代工业对特殊钢、高质量钢的需求不断扩大,以及连续铸钢技术的迅速发展,对连铸工艺过程也有了更高的要求。
连续铸钢工艺从原料到成品的过程中起着关键性作用。
连铸工艺的优与劣直接影响钢产品的质量、性能和企业的经济效益。
且随着炼钢和轧钢技术的进展,钢铁工业结构的变化和对产品的规格、质量的新要求,这使得采用常规和铸锭—开坯工艺难以满足一些大型钢铁企业的生产和发展,为此,研究连铸的新工艺和新技术是必要的。
本文在阅读大量文献基础上,着重介绍了小方坯连续铸钢的发展概况、连铸机的选型,以及连铸机的工艺参数确定、设备的选型和相关参数进行了设计,并对连铸车间进行布置,使其保证连铸稳定、持续的进行。
最后本文还介绍了一些方坯连铸的新技术。
第一章 绪 论
1.1我国方坯连铸发展的状况
我国是在炼钢生产中研究、应用连铸技术较早的国家之一。
20世纪50年代中期,当连铸技术在前苏联、英国、意大利、加拿大等国进入工业性试验阶段时,我国即着手进行试验研究工作。
1956年我国在当时的重工业部钢铁综合研究所建成了直径80mm的圆坯半连铸试验装置。
1957年在上海钢铁公司中心试验室建成一台高架立式方坯连铸机;
1958年在唐山钢铁厂建成了第一台工业生产的立式连铸机,同年在重庆第三钢铁厂建成投产一台两机两流,配合30t转炉,浇铸175mm×250mm矩形坯的立式连铸机。
1960年在唐山钢铁厂建成一机一流,配合5t转炉浇铸150mm×150mm小方坯的立式连铸机。
我国发展的连铸机型大多为立式连铸机,生产效率低。
因此,我国连铸生产的发展极其缓慢,到1978年我国的钢产量为3178万t,其中平炉钢1127万t,占总产钢量的35.46%,连铸比仅为3.5%。
为了改变我国连铸生产发展的落后状况,1974年,我国从原西德施罗德—西马克和德马克公司引进了3套弧形板坯连铸机。
1980年,我国又与原西德曼内斯曼—德马克公司签订了引进小方坯连铸设备及技术转让与合作制造合同,在国内增建一批旨在浇铸90mm×90mm,120mm×120mm及150mm×150mm供成品轧机一火成材使用的小方坯连铸机。
上述即是我国设备发展情况。
随着钢铁工业的发展,我国小方坯连铸生产技术也得到了迅速的发展。
我国钢产量呈直线增加;连铸机总台数已由1979年的24台增加到1995年的247台,截止1995年底,我国已经建成投产小方坯连铸机近200台,能力约为3000万t/年,1995年实际小方坯产量达2500万t以上。
现代化转炉(电炉)—二次冶金(精炼)—连铸三位一体技术的发展推动了我国工业迅速、稳定的增长。
对钢铁工业的节能降耗、提高成材率做出重大贡献。
1.1.1我国连铸生技术的基本现状
1、我国连铸比已超过世界平均水平,接近工业发达国家水平,连铸比可以说接近饱和状态。
2、我国小方坯连铸机高效化改造取得很大成绩小方坯连铸机单流产量已达到国际先进水平,但我国连铸机平均作业率与世界连铸机平均水平还存在较大差距,提高连铸机作业率以增加连铸机产量还有较大发展潜力。
3、经过近10多年来的努力,我国连铸在高效化改造!
新技术的应用等方面取得了很大成就,就大中型企业连铸机装备水平来看已与国外钢厂水平相当,要重视工艺软件技术开发与创新,新技术要用出实效来,要依靠传统的板坯和大方坯连铸机来生产和解决高品质,高附加值的连铸坯质量问题。
4、薄板坯连铸连轧技术已引入大中型企业,我国薄板坯连铸—连轧生产已跨入世界先进行列,它对改变我国钢材产品结构,提高板带比,改变热轧带卷的市场竞争力起重大的变革作用。
1.1.2我国连铸技术的发展和所取得的主要成绩
由统计结果可知,“七五”和”八五”期间我钢铁生产发展迅速,尤以“八五”更为显著。
早在“八五”初期,冶金部提出“以连铸为中心,以炼钢为基础,以设备为保证”的连铸生产技术方针,从总体上抓投产导向,连铸机配套完善,提高炼钢水平和铸机备品备件的国产化供应等关键。
因此,到1992年,从总体上已经解决了连铸机达产问题。
在此基础上,又把连铸生产技术方针扩展为”以连铸为中心,以炼钢为基础,以设备为保证,以全连铸为方向,实现炼钢、二次冶金、连铸组合优化”。
到”八五”末期,又明确了连铸生产完善的重点是全连铸、高效连铸、连铸坯热送热装;计算机控制和近终形连铸,引导连铸水平逐步提高。
1.1.3连续铸钢的优越性
1、节省工序缩短流程
连铸与模铸相比,最大的特点是省掉了模铸的脱摸,整摸,钢锭均热和开坯等工序。
基建投资少,占地面积小,节省劳动力。
2、提高金属收得率
3、降低能量消耗
4、生产过机械化和自动化程度高
炼钢厂铸锭车间劳动环境恶劣,手工劳动多,是炼刚生产中最落后的生产工序。
尤其是对转炉的发展而言,注定以成为提高生产率的限制性环节。
采用连铸后。
由于设备和操作水平的提高以及采用全程计算机控制和管理,劳动环境得到了根本性改善。
连铸操作自动化和智能化已成为现实。
5、连铸钢种的扩大,产品质量日益提高
目前几乎所有的钢种都可采用连住生产。
连铸的钢种已扩大到500多个。
就钢种而言。
超纯净钢。
高牌号钢。
不锈钢,Z向钢,管线钢,重轨,硬线,工具钢以及合金钢都可用连铸生产。
1.1.4我国连铸生产存在的问题:
1、大量低水平连铸机的重复建设。
目前,我国生产能力低下的低效率连铸机仍占70%左右。
以方坯生产为例,我国连铸机平均单流年产不到7.5万t,而国际上先进连铸机单流年产能力超过13万t。
2、可浇品种少。
以合金钢连铸为例,我国合金钢连铸比仅为5%左右,而工业发达国家已达90%。
3、连铸机作业率低。
我国连铸机平均作业率不到65%,而工业发达国家连铸机多采用大部件更换、离线检修等手段,大大缩短了停机时间,连铸机实际作业时间多在85%以上,甚至有些国家的个别连铸机实际作业时间达到了94%。
4、自动化控制水平低。
我国绝大部分企业在诸如连铸的测温、测速等方面还是凭经验或用手控方式进行,偏差较大;有些连铸机在建成时配备了一些自动控制设备,但由于仪器设备存在着各种质量问题,不能保持良好的运行状态。
就拿连铸机结晶器液面控制来说,本是最需要依靠自动控制来实现的,但目前结晶器液面实现自动控制的尚不足全部连铸机的10%。
而工业发达国家连铸生产的自动控制已发展到整个连铸过程的计算机控制,样品采集、分析、逻辑控制都是建立在数学模型上的,其精确程度和准确性是用手控或凭经验所无法做到的。
1.2设计的意义
随着现代工业对特殊钢、高质量钢的需求不断扩大,以及连续铸钢技术的迅速发展,对连铸工艺过程也有了更高的要求。
连续铸钢工艺从原料到成品的过程中起着关键性作用。
连铸工艺的优与劣直接影响钢产品的质量、性能和企业的经济效益。
且随着炼钢和轧钢技术的进展,钢铁工业结构的变化和对产品的规格、质量的新要求,这使得采用常规和铸锭—开坯工艺难以满足一些大型钢铁企业的生产和发展,为此,研究连铸的新工艺和新技术是必要的。
本文主要从连铸机的选型、工艺参数、主机设备进行有关方面的设计。
并对铸钢车间进行了布置。
第二章连铸机机型的选择
2.1连铸机机型及特点
2.1.1连铸机机型的分类
连铸机的机型经历了一个由立式、立弯式到弧形演变过程。
连铸机可按多种形式来分类。
若按结构外形可把连铸机分为立式连铸机、立弯式连铸机、带直线段的直弧形连铸机、弧形连铸机和水平连铸机。
若按连铸机一个机组,在共用一个钢水包下所能浇注铸坯的流数来区分,则可分为单流、双流和多流连铸机。
若按连铸机所浇注的断面大小和外形来区分,连铸机可分为板坯连铸机,小方坯连铸机,大方坯连铸机,圆坯连铸机,异形断面连铸机和薄板坯连铸机。
2.1.2各种类型连铸机机型的特点
立式连铸机的基本特点是从钢液到铸坯切成定尺的整个流程是在一条垂直线上进行的,铸坯自始至终不承受强制的弯曲变形,冷却比较均匀,夹杂物易于上浮,但设备高度大,笨重,不方便维修,另外基建投资也高。
立弯式连铸机具有立式连铸机在垂直方向进行浇注和凝固的特点。
设备的高度比立式减少了,且这种类型的连铸机夹杂物上浮条件较好,没有向内弧聚集的问题。
缺点是铁静压力大以及弯曲的应力易引起铸坯内裂和表面裂纹,所以新建连铸机很少采用这种类型。
直—弧形连铸机是在立弯式连铸机的基础上,演变的带液相弯曲及矫直的弧形连铸机。
与立弯式连铸机相比,铁静压力减小,设备高度降低,夹杂物上浮条件好,无向内弧聚集的问题。
但这种连铸机在凝固过程中受到附加的应力,会增加内裂的危险,设备也比较复杂,维修的工作量也大。
弧形连铸机的特点是采用弧形结晶器,铸坯在被矫直前,整个凝固过程都是沿着圆弧线移动,没有附加的弯曲应力,因而不易产生裂纹。
设备高度低,铁静压力小减少了由于鼓肚引起的内裂以及偏析,有利于提高拉速。
弧形连铸机高度低、维护检修以及处理事故较方便。
2.2连铸机机型的选择
在设计连铸车间时,首先要解决的问题是连铸机机型的选择,要根据产品的方案、质量要求和节省投资确定一种合适的机型。
机型选择的合适,为优秀的设计打下了基础,为连铸机投产后优质高产创造了条件。
2.2.1连铸机机型选择的原则
1、满足钢种和断面规格的要求;
目前,发展比较成熟的机型有立式﹑直弧形、弧形、多点矫直弧形﹑超低头和水平式等连铸机,几种机型都有采用,但是弧形连铸机应用最多.
2、满足铸坯质量的要求;
连铸机对铸坯质量的影响主要包括两个方面;一是铸坯裂纹及中心偏析,二是铸坯的纯净度。
这些缺陷都与连铸机机型直接相关。
从中仔细分析得到机型对铸坯质量两个方面的影响是相互矛盾的。
若综合两者考虑两者对铸坯质量影响,则直结晶器、弧形、多点矫直弧形连铸机是比较理想的机型。
3、节省建设投资
近年来随着钢铁冶金技术的发展,各种形式钢包冶金技术,无氧化浇注以及中间包冶金技术等,组成了一个完整的纯净钢水的生产流程,以能做到满足不同档次产品对纯净度的要求。
机型对铸坯的夹杂物含量以及分布的影响正在逐步减弱。
由于多点矫直、连续矫直及压缩浇注技术的发展,铸坯可以带液芯矫直而不产生裂纹。
因此,理想的连铸机是设备高度低、钢水静压力小。
这样可以简化连铸机辊列设计,可减少建设投资。
2.2.2连铸机机型的确定
连铸机的确定应根据上述原则综合考虑。
新建连铸机应在保证钢种和质量的前提下,尽量选择投资省的机型。
不同钢种、不同断面等选择机型也不同。
对于生产小型材和线材的小方坯连铸机,一般选用弧形连铸机。
这种连铸机结构简单,维护方便,投资省,并能保证品种和质量要求。
综合上述条件,本设计选用弧形连铸机。
2.3小方坯连铸机的主要特征
小方坯得铸坯断面小,热熔量比较小。
所以比大方坯、板坯连铸设备工作条件要好。
小方坯浇铸过程,坯壳有自支撑作用,铸坯没有鼓肚现象,象采用刚性银锭杆的洛克普连铸机,二冷区导向段的设计非常简单。
实践表明,铸坯质量完全满足标准要求。
A 钢包支撑
钢包支撑主要有以下两种:
1、对于转炉连浇炉数多,多采用钢包回转台,有利于快速更换钢包,保证多炉连浇。
现增设钢包升降和秤量装置,有利于长水口安装,显示钢包重钢水量。
2、平炉、电炉配连铸,当连铸炉数少时也可采用钢包更换座架,钢包座架结构简单,重量轻,投资少。
B 中间包及中间包车
中间车采用升降装置,以便安装进入式水口;为适应钢水的温度的波动及控制拉速,中间包钢流多采用塞棒控制。
C 结晶器及震动机构
采用管式结晶器,结晶器下加足辊或多机结晶器,并将单足辊改为双足滚,减少铸坯菱变。
结晶器冷却水缝改为5mm,以增加水的流速到6m/s以上,水套壁加厚以增强刚性。
加大铜管的倒锥度,铜管圆角半径的适当,以减少角裂,120×120~150×150mm方坯铜管倒锥度为0.6~0.8%/m;120×120方坯管圆角半径为4~6mm,150×150mm方坯铜管圆角半径6~8mm.振动机构改为振幅可调。
结晶器液面采用铯137对液面自动控制。
结晶器材质采用磷脱氧铜,内壁镀锣、镍等材料,提高结晶器寿命。
D 二冷区
设计院改进的型的小方坯连连铸机的二冷区分为二冷活动段和二冷固定Ⅰ、Ⅱ段,在浇铸时,二冷活动段为可移开式,即开浇后,弧形导向托板由气缸移开,避免漏钢烧损,便于维护检修,提高作业率。
为简化后部布置,将结晶器进出水管,二冷给水管都移开到内弧,并且二冷区分段供水,喷嘴纵向排列,冷却均匀,调节方便,维护简单。
E 引锭杆型式
引锭杆有链式引锭杆和刚性引锭杆两种形式,采用刚性引锭杆比较受欢迎。
F 拉矫机
拉矫机采用固定机架,下辊传动,简化了需要升降的上辊机构,底座加强,检修时只需拆卸辊子,不必移动机架,压下气缸安装在下部便于防护冷却。
采用五滚拉矫机,该拉矫机具有结构紧凑,设备可靠,操作方便,拉坯和矫直灵活等特点。
G 铸坯切割
铸坯切割有剪切机切割也有火焰切割,对于小方坯以剪切机为主。
为提高剪切能力,现将剪切力加大到400~500t。
电动机剪显得设备庞大,为将低设备重量采用45度液压剪,改善减少铸坯质量。
H 辊道
辊道采用分组链条集中传动,减少设备维修和更换时间。
I 翻钢及冷床
采用翻钢推钢机,可将铸坯翻坯90度推钢,这样铸坯并在一起不致顶弯。
由分散冷床改为集中冷床,节省占地面积。
步进式翻钢冷床,单坯运动前进,冷却效率高,铸坯一面前进、一面翻钢,保证了平直度,特别合适运送冷却小断面铸坯
课程设计--小方坯连铸机设计 二
第三章 工艺参数的确定及计算
3.1工艺参数的确定
主要参数确定及计算包括铸坯断面、弧形半径、拉坯速度、铸机冶金长度计算及铸机流数等。
3.1.1铸坯断面的确定
铸坯的断面尺寸受冶炼设备容量、轧机组成、轧材品种规格和产品质量等因素的影响,在确定合理的铸坯尺寸时,必须考虑以下原则:
连铸机生产能力与炼钢能力合理匹配,以便充分发挥设备生产能力,获得最佳生产效益。
1、根据轧机组成、设备性能、轧材品种、规格以及不同钢种要求的压缩比,兼顾炼钢、连铸和轧钢都能取得合理的经济效益为前提,在满足轧材品种质量的条件下,力争一火成材,不易过分加大铸坯断面。
另外,每台连铸机的铸坯断面种类应尽量少。
2、可供选择的铸坯断面范围。
表3-1连铸机常见的方坯浇注断面尺寸
连铸机类型
连铸坯尺寸/mm
备注
方坯连铸机
小方坯
≤160(边长)
最小断面不宜小于120mm(边长)
方坯
>160至≤200(边长)
大方坯
>200(边长)
3.1.2连铸机弧形半径的确定
连铸机的弧形半径取决于生产钢种和铸坯断面尺寸。
一般根据已经投产的连铸机的设计和生产经验得到的铸机半径(R)和铸坯厚度(D)之间的关系式来确定。
小方坯连铸机 R=(30~40)D
大方坯连铸机 R=(30~50)D
板坯连铸机 R=(40~50)D
对于质量要求比较高的钢种,通常采用较大半径或多点矫直方式来提高铸坯质量。
采用计算法确定铸坯半径时必须满足的两个条件
1、铸坯矫直时,内弧表面变形率必须控制在钢种的允许范围内,以避免表面产生裂纹。
2、铸坯带液芯矫直时,应使两相区的变形率小于钢种允许的变形率,避免内部产生裂纹。
为此,本实验选择小方坯为130×130的,由此计算R=33×130=4.29m
3.1.3钢包容量的确定
根据公式:
车间年产钢水量=nNq
=(n×q×1440×365×)/
式中 ——车间年供需钢水量
n——车间吹炼炉数;
N——每一吹炼炉座的年初钢炉数;取1;
q——转炉公称容量,吨;
——连铸机的年作业率
T1——浇注时间
由公式=(n×q×1440×365×)/可得:
=(n×q×1440×365×85%)/42
nq=198
联合实际,选容量为130t的转炉两座,设计时每个钢包的钢水量也按130t计算。
3.1.4钢包允许的最大浇铸时间
1、钢包允许的最大浇铸时间的确定
钢包允许的最大浇铸时间受多种因素的影响,如钢种、钢包容量、包衬材质、烘烤条件、覆盖保温剂、钢包加盖等。
可用经验公式计算:
=(log130-0.2)×f/0.3
=(log130-0.2)×11/0.3=70.03min
式中:
Tmax——钢包允许的最大浇铸时间,min;
G——钢包容量,t;
f——质量稀疏,主要取决于对浇铸温度控制的要求。
在这里取f=11
2、实际浇铸时间的确定
在确定连铸机的实际浇铸时间时,必须考虑连铸机与冶炼设备相配合进行多炉连浇的件。
在本设计中,用一座转炉向一台连铸机提供钢液,这样调度方便,多炉连浇条件好,考虑到炉外精炼时间的,则确定实际浇铸时间为50分钟。
3.1.5拉坯速度
1、工作拉速的确定:
拉速是连铸机生产能力的重要标志。
当铸机浇铸稳定以后,其拉坯拉速称为工作拉速。
从提高生产率的要求出发,希望尽量提高拉速。
其工作拉速可按下列公式计算:
式中:
vmax——最大理论拉速,m/min;
K——凝固系数,mm/min0.5
Lm——冶金长度,m;
D——铸坯厚度,mm.
断面是140×140时的工作拉速的确定:
V=(K×L)/S
=(65~100)×130×4/(130×130)
=2.0~3.08m/min
2、理论拉速的确定
当铸坯的液芯长度等于冶金长度时的拉速,即为最大拉速,最大拉速一般为工作拉速的1.15~1.2倍。
所以理论拉速为:
vmax=v实际×1.2=2.54×1.2=3.04m/min
生产中,实际操作拉速必须小于冶金长度确定的最大拉速,否则铸坯导向段装置出口处将可能产生严重喷流。
3.1.6铸坯的冶金长度及铸机长度
1、液芯长度的确定
铸机的冶金长度取决于铸坯的液相深度(即液芯长度),铸坯的液相深度是指钢水从结晶器液面至铸坯全部凝固完毕时的长度,它是确定弧形连铸机半径和二冷区长度的一个重要工艺参数。
液相深度与浇注的钢种、铸坯厚度和拉速有关。
可按下列公式计算:
式中:
L液——铸坯液芯长度,m
vmax——最大拉坯速度,m/min;
D——铸坯厚度,mm
K——凝固系数,与钢种有关,一般为25~30mm/min0.5
所以:
=(130×130×2.54)/(4×28×28)=13.69m
2、冶金长度的确定
在设计连铸机时,应考虑连铸机可能达到的最大拉速,而且还应考虑投产后,由于连铸技术的发展,进一部提高拉速的可能性。
根据最大拉速计算出来的液芯长度,就是连铸机的冶金长度。
连铸机的冶金长度可按下式计算:
=(130×130×3.08)/(4×28×28)=16.598m
3、铸机长度的确定:
连铸机长度一般指结晶器液面至铸机拉矫机最后一对夹辊之间的距离。
对方坯连铸机可延伸到切割机起切点;对弧形板坯连铸机,可采用增加水平段夹持辊数量来增加铸机长度。
铸机长度按冶金长度确定,通常铸机长度取1.1倍冶金长度。
L铸=1.1×L冶=1.1×16.598=18.26m
3.1.7连铸机流数的确定
一台连铸机同时浇注的铸坯根数,主要取决于炼钢炉容量、钢包允许浇注时间、铸坯断面和拉坯速度,并与铸机所需完成的产量以及铸机与冶炼周期的配合等有关。
通常,在一台连铸机上浇注一种断面时计算流数的公式为:
9.27
式中:
N——一台连铸机的流数;
G——每炉钢水量,t;
F——铸坯断面面积,mm2;
t——钢包浇注的时间,min;
vg——该断面的平均拉速,m/min;
r——冷坯密度,取7.6t/m3.
在一台连铸机上浇注多种断面时,应分别计算流数,取计算结果中的最大流数为连铸机流数。
目前,一般连铸机流数为:
方坯和圆坯1~8流,板坯1~2流。
本实验取8流。
3.2连铸生产能力计算
影响连铸机产量的主要因素有:
浇铸速度、连焦炉数、流速、断面尺寸、作业绿灯。
设备和铸坯断面一定时,连铸机产量主要取决于作业率和拉速。
当然,操作和管理水平对连铸机的产量也有是非重要的影响。
3.2.1连铸机作业率的确定
连铸机的作业率关系到连铸机的产量、每吨连铸机的操作的费用和投资费用的回收期。
连铸机的要获得较高的作业率,必须采取多炉连浇。
为了提高炉数,应避免在操作中发生的偶然事故,并对设备进行定期维修。
连铸机非生产时间占总时间的15%。
连铸机作业率为:
Y2=(A1-A2)×100%/A1=(8760-54.75×24)×100%/8760=85%
式中:
Y2 ——连铸机作业;
A1——日历时间,8760h;
A2——连铸机非作业时间;
表3-1非生产时间
项目
比例,%
备 注
定修
3.5
8h/次×3次/月
点修
4.5
辊子对中调整,铲除飞溅废钢,检修等
更换结晶器
1.0
4h/次×2次/月
等待
2.0
浇注完毕后,连铸机准备好等待钢水
内部故障
2.0
包括漏钢在内的连铸机故障
外部故障
2.0
炼钢炉,吊车和钢包设备的故障
总计
15.0
3.2.2每炉钢水量G
设计转炉的公称容量为130t连铸用钢水是按每炉130t计算的。
3.2.3浇铸时间的确定
本设计采用一台转炉配一台连铸机,所以转炉冶炼周期与炉外精炼时间的总时间与钢包浇铸时间相同。
3.2.4连浇炉数
连浇炉数与转炉及连铸的配合有关,同时与炉子的容量的大小,浇铸时间长短耐火材料质量也有密切的关系。
3.2.5准备时间
准备时间是指从上一炉浇铸的中间包关闭到下一炉浇铸时完成结晶器内引锭杆头密封为止所需的辅助操作时间。
1、尾坯封顶及拉出尾坯
完成这些操作需要的时间要根据钢种和铸坯断面等具体条件来确定。
中间包车开走一般为1。
尾坯封顶时间与铸坯断面有关,断面小,封顶时间短,断面大,封顶时间长。
小方坯的封顶时间约1.5min,板坯封顶时间约2min。
拉出尾坯时间与钢种和断面有关,合金钢的拉速比普碳钢低,大铸坯断面的拉速比小断面的拉速低.通常,普碳钢和大断面铸坯的拉尾坯时间取10~12min。
2、清理连铸机
清理;连铸机主要是清扫结晶器.这项作业实际上可以与拉尾坯同时进行。
板坯的作业时间一般为7~8min,方坯为6~7min。
3、送入引锭杆
如果是采用上装引锭杆,则可与拉尾坯和清扫结晶器的作业时间同时进行,待尾坯拉完,引锭杆也装完,不需要另外作业时间.如果是下装引锭杆,则必须待尾坯拉出,结晶器清扫完以后,才能把引锭杆摆入辊道,起动辊道送到拉矫机下,再启动拉矫机,把引锭杆送到结晶器下约500mm处,然后启动送入结晶器内。
上装引锭杆作业时间约为2,下装引锭杆作业时间约3~4min。
4、填塞引锭头
引锭头送入结晶器后,先定位,然后用石棉填塞引锭头周边