砂光机调整及故障处理.docx
《砂光机调整及故障处理.docx》由会员分享,可在线阅读,更多相关《砂光机调整及故障处理.docx(11页珍藏版)》请在冰豆网上搜索。
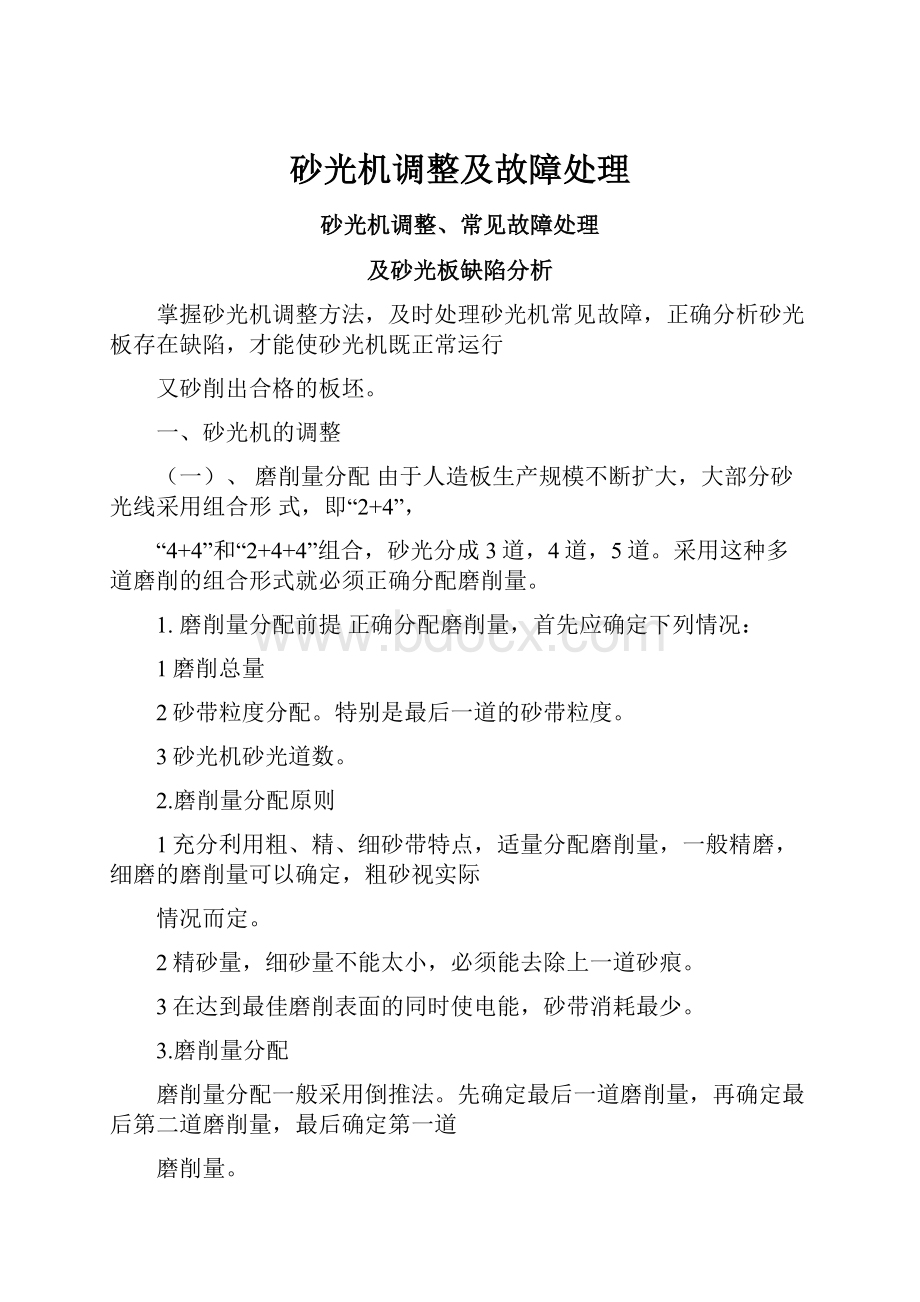
砂光机调整及故障处理
砂光机调整、常见故障处理
及砂光板缺陷分析
掌握砂光机调整方法,及时处理砂光机常见故障,正确分析砂光板存在缺陷,才能使砂光机既正常运行
又砂削出合格的板坯。
一、砂光机的调整
(一)、磨削量分配由于人造板生产规模不断扩大,大部分砂光线采用组合形式,即“2+4”,
“4+4”和“2+4+4”组合,砂光分成3道,4道,5道。
采用这种多道磨削的组合形式就必须正确分配磨削量。
1.磨削量分配前提正确分配磨削量,首先应确定下列情况:
1磨削总量
2砂带粒度分配。
特别是最后一道的砂带粒度。
3砂光机砂光道数。
2.磨削量分配原则
1充分利用粗、精、细砂带特点,适量分配磨削量,一般精磨,细磨的磨削量可以确定,粗砂视实际
情况而定。
2精砂量,细砂量不能太小,必须能去除上一道砂痕。
3在达到最佳磨削表面的同时使电能,砂带消耗最少。
3.磨削量分配
磨削量分配一般采用倒推法。
先确定最后一道磨削量,再确定最后第二道磨削量,最后确定第一道
磨削量。
例:
某公司采用“4+4”砂光组合(见图1),根据市场对板面质量要求,最后一道要求采用150#砂
带,总磨削量为2.2-2.8mm。
根据上述条件,首先选择砂带为40#、80#、120#150#,再选择第五道磨削量为0.15mm(双面),第四道磨削量为0.15mm(双面,组合砂架磨垫),第三道磨削量为0.4mm(双面,组合砂架砂辊),第二道磨削量为0.5mm第一道磨削量为1-1.6mm
4.磨削量分配方法
采用逐道分配方法,首先根据磨削量分配,确定每道砂光完成以后的板厚尺寸。
根据确定的板厚尺寸,先砂第一道,后几道砂带暂时去掉。
第一道砂光后板坯尺寸满足要求后,套上第二道砂带进行磨肖U,确定第二道板厚尺寸,以此类推。
直到最后一道尺寸符合要求,一般在确定每道尺寸时,至少砂两
张符合尺寸要求,方能确定这道砂光已调整正确
5磨削量分配不当引发的问题:
1粗砂磨削量太小,会增加精砂、细砂的负担,使精、细砂带消耗量增加,不能充分利用粗砂功能,送进速度有所下降,影响生产效率。
2前道磨削量太多或后道磨削量太少,都会引起密集横向波纹(实际是前道横向波纹未消除,后道又同时产生,两道横向波纹重叠),表面光洁度降低。
可见,正确分配磨削量,不仅可提高板面质量,而且可以节省砂带,降低能耗,提高生产效率。
值得注意的是采用上述办法调整完毕后,应根据实际情况在使用过程中做适当微量调整,因为磨削过程是个变数,砂带磨损,磨垫磨损,板的密度和硬度在变化。
如何进行微调,需要不断积累经验,摸透每一台设备的机械特性。
按上述方法调整完毕后,以后一般不需要做大的调整,即使在变换板坯的规格时也不需要做大的调整,因此应对偏心轮,磨垫位置作记录,避免有人误操作而需要重新调整。
(二)、砂光机调整
为实现砂光机磨削量正确分配,就必须对砂光机进行调整。
砂光机调整一般采用下机架基准原则,即首先调整下机架,然后以下机架为基准调整上机架。
调整下机架比较困难,必须升起上机架,采用平尺及条式水平仪精细调整,耗时较长。
因此用户调整完下机架后,应保持下机架状态,做好必要的记号,这样会大大节省时间。
通常机器出厂前,已基本调整完毕,调试人员在现场做微调即可。
但用户使用一段时间或更换主关另部件时,会作大范围调整。
因此维修人员必须掌握调整方法。
(具体调整方法略)二、砂光板缺陷分析
砂光板缺陷主要有二种,一是砂光板厚度精度;二是砂光板表面质量。
多年使用经验证明,控制砂光板厚度精度较容易,但控制砂光板表面质量十分困难。
厚度精度有数据可确定,而表面质量只能凭手感、、目测,有较大的不确定性。
针对上述情况,下面重点分析砂光板表面缺陷。
(一)、厚度精度误差分析
1.砂光板两侧尺寸不一致,截面成斜楔形,这是由于上下砂辊不平行所致。
2.砂光板两侧薄、中间厚,截面近似菱形。
此现象出现在四砂架以上的砂光机,相邻两对砂辊都不平行,且方向相反。
3.砂光板厚薄不均,在截面上无规则,但位置相对固定。
原因有二,一是砂辊出现无规则磨损;二是磨垫、羊毛毡、石墨带厚度不均,或磨垫体变形,或磨垫安装(指安装羊毛毡、石墨带)不当。
4.在砂光板两侧距端部10-15mm范围内,尺寸明显少于正常范围,称塌边。
在常规测量中,塌边往往会忽
视,检测方法有二种:
1把钢皮尺或游标卡尺直线段侧放在板端部,用塞尺塞端部间隙或用肉眼观察。
2观察或用塞尺塞成垛板两侧端部。
塌边对贴面十分不利,贴面后边部容易脱落,所以应严格控制,一般采取以下措施:
1减少磨垫磨削量,从而减少板两侧的磨削压力,减轻塌边程度。
2把接近砂光板两侧端部的羊毛毡截成三角形或把石墨带剪一个矩形(20X50mm,减少板部两侧的磨
削量,减轻塌边程度。
采用这种办法比较有效,但板边部的光洁度有所下降,应适可而止。
3采用先砂后锯工艺,可彻底解决塌边问题,对砂光机调整要求明显下降。
但采用这种工艺方式有两大缺点:
一是砂光与锯边由于各自的故障,会相互影响,锯边强烈噪音对操作环境也有影响;二是增加边部砂光,耗费电能大。
5•啃头、啃尾、啃角。
在砂光板前后端或四角距端部10-15mm处,尺寸明显小于正常范围称啃头、啃尾、啃角。
在常规检测中容易忽略,检测方法和塌边一样。
这种现象对贴面同样会产生不利,必须严格控制,主要采取以下措施:
1严格按调整要求调整输送辊和导板的位置,过高或过低都会产生啃头、啃尾、啃角的现象。
尤其在砂肖U厚板时,这个问题更加突出。
2在多道砂光组合中当产生上述现象时,应找出啃头、啃尾、啃角在哪道工序产生,如果在粗砂时就产生,而且程度严重,后道工序无法消除,必须在粗砂时解决问题。
3当毛板挠曲过大时,也会产生上述现象,应控制毛板质量。
4下输送辊在长期运行中,会有不同程度磨损,当磨损达到某一程度时,下输送辊的位置实际也发生变化,所以有时会发现砂光机运行一段时间后产生啃头、啃尾、啃角现象,应更换下输送辊。
6•砂光板上下磨削量分配不当。
大部分刨花板、中纤板表面都有预固化层,这种预固化层强度低,对今后使用会有影响,必须砂掉。
对刨花板而言,不仅存在预固化层问题,还存在表面结构细、中间粗的实际情况,在砂削过程中应保存表面细刨花,所以应根据实际情况适当分配上、下磨削量。
一般采用以下措施:
1分道检查,找出主要由哪道工序产生偏磨。
一般是粗砂。
2对顶砂辊只须调整砂辊偏心轮,同时升或同时降,两辊间隔保持不变。
3对叉开砂架只须调整反压辊,减少或增加间距。
(二)、表面缺陷分析
1.横向波纹
①横向波纹产生的原因横向波纹主要有二种,一种是由砂带接头引起的,另一种是由砂光机砂辊振动或跳动引起的。
大部分横向波纹属第一种,后一种情况极少。
砂带接头引起的横向波纹是有规律的,横纹
间隔均匀,且与进给速度有关,进给速度大,间隔大;进给速度小,间隔小。
间隔距离S为:
V砂一一砂带线速度度m/s;
l—砂带周长m
V进一一进给速度m/mi
2横向波纹对板的影响横向波纹彻底消除几乎是不可能的(包括Bison公司、steinemann公司生产的砂光机),一般情况下把横向波纹减弱到最小程度。
有些波纹看不见,画得出(用一支长粉笔平放在
板面,呈45°方向均匀划出);有些波纹看得见,但画不出;也有的波纹既看得见又画得出。
看得见但画不出的波纹对使用影响很小,如果能达到这样效果就可以了。
画得出的波纹也要视情况而定,轻微的对一般使用没有影响,严重的对使用肯定会造成影响。
3如何消除或减轻横向波纹消除横向波纹主要依靠砂光机的磨垫。
一道磨垫只能减弱横向波纹。
有些厂采用二道磨垫,效果会很明显。
另外应注意以下几点:
a.磨垫上使用的羊毛毡、石墨带应厚度均匀;
b.砂带接头应为对接接头,接头处的厚度比其它部分薄一些;
c.磨垫与板面的接触力应均匀,不宜过大,也不宜过小,通常以磨削量作为衡量标准,磨削量一般
为单面0.075mm
2.稀疏性横向部分
上述横纹属密集型,而稀疏性横向波纹在一张板上只有1-4条,分析如下:
1如果整张板只有1-2条横纹,且距板头或板尾距离固定,一般可判断为下输送辊位置过高或过低引起,调整下输送辊即可。
2如果整张板有4条,且间隔相等,约为下输送辊周长,则可判断为下输送辊失园,必须更换。
3.纵纹纵纹可分成三种:
直纹、S形纹、点划线。
①纵向直纹纵向直纹由设备中磨垫和砂辊引起,顺着产生纵纹的相应位置可找出原因,有以下几种情况。
a.砂辊表面特有石墨、胶团或损伤。
b.磨垫表面石墨带成波浪形、破损或石墨带、羊毛毡厚度不均。
c.可能导板机械划伤。
②纵向S形纹纵向S形纹由砂带引起,顺着产生S形纵纹的相应位置可可找出原因,有以下几种情况:
a.砂带表面有凸出粗砂粒。
b.砂带局部打趋。
c.砂带背面粘有石墨或胶团。
d.砂带接头处有缺陷。
4.点划线有些板产生类似于点划线。
这个点一般凸起,原因是:
当砂带由于本身质量或被砂光板硬物擦伤产生掉粒时,出现凸起点划线,此砂带如果是细砂,则该砂带必须报废。
砂光机在砂光过程中还会发现其它表面缺陷,如板表面局部粗糙、局部斑点,这是板本身质量问题。
大部分砂光后的板用手可感觉到顺逆方向粗糙度不同,这是由于被砂光板板表面细纤维在砂光过程中只是被烫平,并没有齐根去除,解决这个问题须从改变砂光机工艺着手。
在六砂架或八砂架中一般可以改变最后第二道砂带旋转方向来改善顺逆之差
砂光机常见故障分析与排除
砂光机在运行过程中,经常会出现故障,大多数故障可及时排除,但如果处
理不当,可能会影响生产,增加成本。
这就要求操作员对常见故障做到心中有数,迅速
反应,及时排除。
有些故障发现时并不严重,但如果不适当处理,就会引发大的故障,严重影响生产。
下面对苏福马砂光机18种常见故障进行分析。
1.砂带跑偏。
一般由于调整不当引起,正常的砂带摆动应该是摆幅为15-20mm摆频
为15-20次/分,摆速适中且摆进摆出速度一致。
如果处在非正常状态,时间一长,可能出现跑偏现象,尤其是摆进摆出速度不一致,更易引发。
砂带跑偏可能是光电管失灵,摆动气阀或摆动缸损坏引起。
吸尘不佳,粉尘浓度高会影响光电管正常工作,也可能引起砂带跑偏
2.限位失灵。
砂带两侧均有限位开关,当砂带摆动失灵,往一侧跑偏时,碰限位开
关,砂带松开,主电机自动停止,可有效保护砂带。
一旦限位失灵可引起砂带损坏,磨擦机架产生火星,甚至引起火灾和爆炸。
因此限位开关应经常检查动作是否可靠。
3.砂带起皱。
砂带一旦起皱就无法再使用,一般引起砂带起皱有三种可能。
一是砂
辊与张紧辊在垂直平面投影中不平行,需在中心支承缸处加垫,校正。
二是砂带受潮发软引发起皱,可采用烘干晒干等办法。
三是砂光机长时间不使用砂辊表面生锈粗糙,砂带摆动困难引发起趋,此时应对辊筒除锈或用较细砂纸打磨。
4.砂带断裂。
砂带断裂主要由于砂带跑偏,或砂带磨钝没有及时更换,或砂削负荷过大,或砂削过程中遇硬物,或砂带本身质量问题引起。
应尽量避免砂带断裂,否则可能引起火灾或爆炸。
当操作台的砂辊电流发生异常时,应观察砂带是否已磨钝,如果是应及时更换。
5.下机架油压表压力不正常。
采用液压升降的砂光机在下机架前侧都有油压表,正常
情况油压表压力为70-90kg/cm2,且相对稳定。
如果压力频繁在70-90kg/cm2之间波动,
说明升降油缸可能产生内泄露或外泄露,如果压力小于70kgkg/cm2说明液压系统不正
常需调整。
如果没有压力,可能到位开关没有压住。
压力表在非正常时,可能引起砂光板尺寸超差或不稳定,影响砂光板质量。
6.进板跑偏、打滑、反弹。
在砂光机的调整中要求把上输送辊反压弹簧调整到三分之
二(剩三分之一),上输送辊和下输送辊间隔应比通过的板坯厚度少1.5mm或1mm否
则会引起板坯跑偏或打滑。
严重时引起反弹,这可能会伤及人身安
7.更换砂带后砂削板尺寸发生变化。
砂光机的悬臂在锁紧块松开或锁紧时,位置波动较大(见图二),正常应在0.5mm以内。
如果太大,当锁紧块锁紧悬臂时,锁紧力的大小差异会使悬臂的重复精度发生差别,引起砂光板尺寸波动,直接影响砂光机砂削精度。
当发生悬臂误差太大时(超过0.5mm应拧开锁紧块固定螺栓适当调整,同时在更换砂带时,锁紧块锁紧力度应一致。
图二
8.上砂架上升或下降时发生倾斜。
上机架上升或下降有时会发生倾斜,原因有三,一是由于上机架前后端重量差异大。
二是前后油缸的内摩擦力不同。
三是由于四角油缸的二位二通阀发生故障。
前两个原因可以调节液压系统中单向节流阀解决,第三个原因应检查二位二通阀是否通电,阀芯是否卡死。
当产生倾斜时必须马上纠正。
观察上机架倾斜方向,断开较低机架处油缸二位二通阀电源,下降机架直到上机架平衡,再接通电磁阀电源,同时应调节液压系统中单向节流阀,使机架上升下降平稳。
9.张摆辊张紧速度过快。
通常张摆辊在张紧和松开砂带时,上升或下降的速度平稳适中,不会对砂带产生冲击,但有时候会产生上升或下降速度过快,这样对砂带不利。
产生的原因是中间支撑缸漏油,缸中已无油或少油,支撑缸就不能起到缓冲作用,应找出支撑缸漏油原因,同时加满液压油。
10.主传动万向联轴器断裂。
主传动万向联轴器由德国进口,允许传递扭矩远大于
实际传递扭矩,即使采用适当反激制动,也不会使万向联轴器断裂。
但一般非紧急状态不要采用反激制动,尤其停车时,应让设备自然停车,频繁使用制动或制动太猛,可能会发生万向联轴器断裂。
在使用过程中,尽量不制动,以延长万向联轴器使用寿命。
车时才能发现,原因是传递动力的蜗轮减速中蜗轮部分磨损或全部磨损。
虽然不会对工作造成影响,但其他蜗轮会由于工作负荷加重,而缩短寿命,造成更大损失。
因此,一旦发现这种情况,应立即更换蜗
轮。
12.主轴承发热或声音异常。
砂辊、导向辊和张摆轴承称主轴承。
主轴承只有正常工
作,才可以保证砂光板质量稳定。
一旦主轴承出现故障,就会影响正常工作,而且更换
主轴承非常费时,在更换轴承过程中,有可能会损坏其他关键部件。
因此作为砂光机操
作员应认真负责,经常检查是否发热和有异常声音,一旦发现,应及时查明原因。
在平时的维护过程中按时按要求的牌号加油是至关重要的。
13.主轴承座振动异常。
正常情况下主轴承座振动很小,有经验的操作员一摸就能判断是否正常,在现场一般没有条件用仪器测量,但可以采用和其他轴承座对比来判断,也可以从砂光板表面优劣来判断。
当发生轴承座振动异常时,可以认为有二种原因,一是轴承损坏,只要更换轴承即可,二是接触辊发生磨损,失园,原有动平衡破坏,造成振动异常,这种情况必须拆下砂辊进行维修。
U上机架不能上升、悬停、下降。
当升降油缸产生内泄露、外泄露,或系统压力无法
建立时,上机架无法上升;当油缸产生内泄露,或到位开关没有松开,或机架四角油缸
二位二通阀发生故障时,上机架不能悬停;当机架四角油缸二位二通阀发生故障,或系
统压力无法建立,或油缸外泄露,或机架发生倾斜时,机架不能下降。
由于机架升降频
率不高,尤其升高300mn高度进行维修的频率更低,所以在上升机架时不能一下子升得
太高,应在较低位置先升降若干次,确认升降正常,再大幅度升降,否则会带来更大麻
烦。
15.刹车失灵。
我公司近二年推出M型砂光机,有省电省砂带两大优点。
它具有
刹车系统,可有效保护砂带。
但有时会发生刹车失灵。
原因有四:
一是刹车气阀失灵。
二是控制刹车阀的光电管发生故障,在砂光机悬臂侧面有三对光电管,中间一对控制砂
带摆动,两边两对控制刹车,一对暗动,一对亮动,在砂带启动时,应检查光电管是否动作,一般由于光电管没有对齐引起。
三是气路系统压力未调好或系统压力不足。
四是刹车片磨损。
16.弹性联轴器的断裂。
这也是M型砂光机特有的。
当主传动轴与砂辊中心偏差超
过2mm寸,弹性联轴器的寿命会大大缩短。
应严格控制这种偏差,一般出厂的砂光机偏心轮的指针在0位,此时的偏心为0。
因此在调整时,初始状态务必使偏心在0位附近。
当必须调整偏心轮时,可在0位附近变动,尽量不要超出两大格。
17.主传动皮带打滑。
在Q型与M型砂光机中,都采用了高速平皮带。
这种传动
形式从理论上讲比三角带传动效率高。
但在实际使用中,会产生皮带跑偏或打滑现象,这主要是调整不当引起。
应严格按照皮带延伸率1.5-2%的要求调整,并且皮带两侧松紧一致。
当按要求调整完毕后,应进行试运转,特别是主电机电流突然升高时,观察皮带是否跑偏,如果跑偏,应进行二次调整。
18.上机架升降后引起砂光板尺寸波动。
当变更厚度规格时,须升起上机架,但有时会发现,当机架下降到位进行砂光时,砂光板尺寸发生厚度偏差,需重新调整,严
重影响生产效率。
产生原因有三种:
一是机架发生变形,这是最难判断的,也是最难处理的,但通常这种情况较少。
二是厚度调整螺栓处在未锁紧状态,升降机架时,产生旋转,引起尺寸波动。
三是在厚度规上下有异物。