基于人工神经网络粒子群算法激光烧蚀制备PDPhSM基纳米复合薄膜的工艺优化.docx
《基于人工神经网络粒子群算法激光烧蚀制备PDPhSM基纳米复合薄膜的工艺优化.docx》由会员分享,可在线阅读,更多相关《基于人工神经网络粒子群算法激光烧蚀制备PDPhSM基纳米复合薄膜的工艺优化.docx(13页珍藏版)》请在冰豆网上搜索。
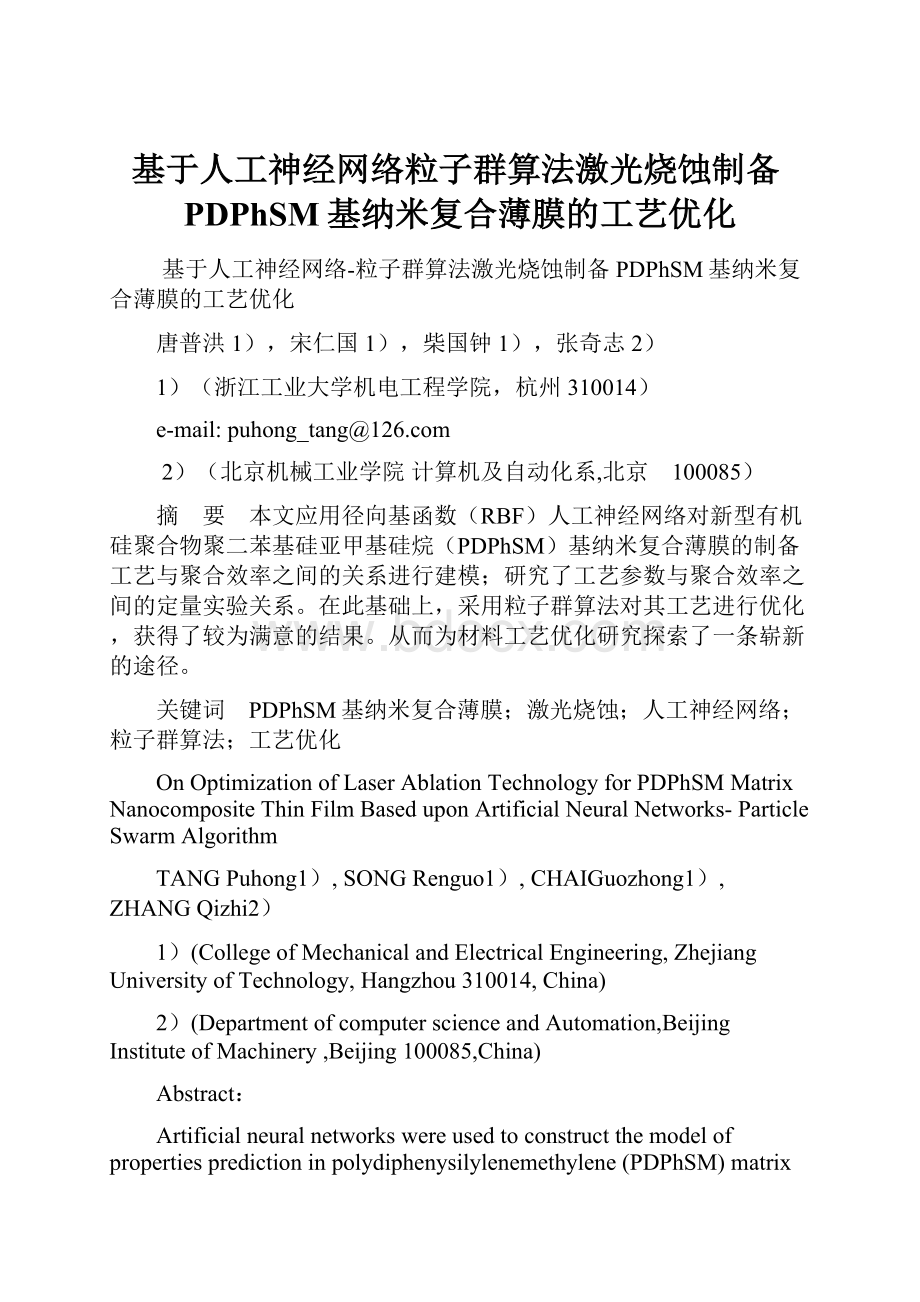
基于人工神经网络粒子群算法激光烧蚀制备PDPhSM基纳米复合薄膜的工艺优化
基于人工神经网络-粒子群算法激光烧蚀制备PDPhSM基纳米复合薄膜的工艺优化
唐普洪1),宋仁国1),柴国钟1),张奇志2)
1)(浙江工业大学机电工程学院,杭州310014)
e-mail:
puhong_tang@
2)(北京机械工业学院计算机及自动化系,北京 100085)
摘 要 本文应用径向基函数(RBF)人工神经网络对新型有机硅聚合物聚二苯基硅亚甲基硅烷(PDPhSM)基纳米复合薄膜的制备工艺与聚合效率之间的关系进行建模;研究了工艺参数与聚合效率之间的定量实验关系。
在此基础上,采用粒子群算法对其工艺进行优化,获得了较为满意的结果。
从而为材料工艺优化研究探索了一条崭新的途径。
关键词 PDPhSM基纳米复合薄膜;激光烧蚀;人工神经网络;粒子群算法;工艺优化
OnOptimizationofLaserAblationTechnologyforPDPhSMMatrixNanocompositeThinFilmBaseduponArtificialNeuralNetworks-ParticleSwarmAlgorithm
TANGPuhong1),SONGRenguo1),CHAIGuozhong1),ZHANGQizhi2)
1)(CollegeofMechanicalandElectricalEngineering,ZhejiangUniversityofTechnology,Hangzhou310014,China)
2)(DepartmentofcomputerscienceandAutomation,BeijingInstituteofMachinery,Beijing100085,China)
Abstract:
Artificialneuralnetworkswereusedtoconstructthemodelofpropertiespredictioninpolydiphenysilylenemethylene(PDPhSM)matrixnanocompositethinfilm.Experimentalrelationshipbetweentechnologicalparametersandpolymerizationefficiencywasinvestigated.Particularly,anartificialneuralnetworks-particleswarmalgorithmwasfirstlyintroducedtooptimizethematerialstechnology,andasatisfyingresulthasbeenobtained,hence,providingabrand-newwayformaterialstechnologyoptimizationinvestigation.
Keywords:
PDPhSMmatrixnanocompositethinfilm;laserablation;artificialneuralnetworks;particleswarmalgorithm;technologyoptimization
1引言
聚二苯基硅亚甲基硅烷(Polydiphenysilylenemethylene,PDPhSM)具有高热稳定性(670K以上),从而引起了人们的特殊兴趣[1]。
最近的研究发现,PDPhSM可以在紫外激光(波长为248nm)辐照下发出长余辉可见光[2],这一奇异的光学性能使得PDPhSM在光学器件领域成为一种具有广阔应用前景的材料而倍受重视。
然而,由于该类材料在大多数溶剂中不溶解且熔点较高,因此很难用现有的方法(如自旋涂膜法)将其制备成薄膜;又由于其在稍微高于聚合物熔点温度以上便会降解而失去苯基团,因此应用化学合成PDPhSM粉末后再在衬底上沉积成膜的方法也不适用。
在这种情况下,应用脉冲激光烧蚀技术在真空蒸镀的1,1,3,3-四苯基-1,3-二硅环丁烷(1,1,3,3–Tetraphenyl-1,3-disilacyclo–butane,TPDC)单体薄膜上沉积了铜金属纳米粒子,并用加热开环聚合的方法制备各种金属纳米粒子弥散分布的PDPhSM基纳米复合薄膜便成为一个崭新的研究领域[3]。
由于所有的激光烧蚀参数和环境变量都会对烧蚀工艺效果产生很大的影响。
并且制备工艺参数与性能之间关系的复杂性,利用传统的实验方法来开发新工艺的周期长、成本太高。
因而有必要寻求一种新方法建立众多工艺参数与性能之间的有机联系,以确定最佳工艺[4]。
鉴于此,本文采用人工神经网络-粒子群算法对新型有机硅聚合物PDPhSM基纳米复合薄膜的激光烧蚀制备工艺进行建模和优化。
2材料与试验过程
试验材料为TPDC粉末,其熔点为402K;高纯度Cu金属板(纯度:
99.99%)以及单晶硅片。
有机硅聚合物PDPhSM基纳米复合薄膜的制备过程如图1所示。
(a)首先采用真空蒸镀的方法将TPDC粉末沉积在单晶硅片的衬底上制备出厚度约为10m的单体膜;(b)然后再采用脉冲激光烧蚀技术将各种金属纳米粒子沉积在TPDC单体膜上。
激光烧蚀试验前,将反应腔体抽成1.33×10-4Pa高真空。
在激光烧蚀反应的同时,向反应腔体中引入氦气作为环境气氛,以保持反应腔体中的环境压力恒定。
试验采用Quanta-RayGCR-130型Nd:
YAG固体激光器作为光源,激光波长为532nm,重复频率为10HZ,脉冲宽度为10ns,激光束的光斑直径在靶上为3mm。
激光能量密度,环境压力,激光烧蚀沉积时间,靶与衬底之间的距离为见表1;(c)最后将沉积有金属纳米粒子的单体膜放在电炉中,在553K保温10min进行热聚合反应。
图1PDPhSM基纳米复合薄膜的制备过程示意图
Fig1SynthesisprocessofPDPhSMnanocompositesthinfilms
为了验证是否发生聚合反应,用傅里叶变换红外光谱仪(FT-IR,Perkin-Elmer1600)对薄膜试样进行分析。
聚合反应前后薄膜的厚度用触针式表面形状测定仪进行测量。
由于在加热过程中聚合反应与再蒸发进行竞争,所以我们定义聚合物PDPhSM基纳米复合薄膜与TPDC单体薄膜的厚度比为聚合效率。
实验所得到的数据用于人工神经网络建模与预测。
表1:
人工神经网络训练与预测点
Table1Artificialneuralnetworktrainingandpredictionpoints
Sample
Fluence
(mJ/cm2pu)
Pressure
(Torr)
Distance
(mm)
Time
(Seconds)
Polym..Effic.Desired
(%)Output
RBF
1
3140
2.0
15
60
5858.112
2
3
4
5
6
7
8
9
10
11
12
4700
4760
4780
4760
4760
4050
4760
4780
4760
4050
4760
6.0
10.0
15.0
2.0
2.0
10.0
0.5
6.0
2.0
10
2.0
15
15
15
15
15
15
15
15
15
15
25
30
30
30
30
5
30
30
30
5
30
20
4848.139
7776.941
8585.006
7070.010
8484.049
6262.001
5353.092
8180.967
8483.943
6262.000
5655.973
13*
14*
15*
16*
4760
4050
4320
3680
2.0
10.0
1.0
1
15
15
5
5
60
30
20
80
8887.558
6262.145
6463.695
3433.012
*Testingsample
图2RBF神经网络的结构
Fig2StructureofRBFneuralnetwork
3人工神经网络建立模型[5-6]
RBF神经网络是具有单隐层的三层前馈网络,其通常分为输入层、隐含层和输出层,如图2所示。
其中,从输入层到隐含层空间的映射是非线性的,而从隐含层到输出层空间的变换,则是线性的。
在RBF网络中,隐含层单元采用径向基函数作为映射函数。
它对输入激励产生一个局部化的响应,即仅当输入落在输入空间中的一个很小的指定区间中时,隐单元才做出有意义的非零响应,输出层的输出为各隐单元的输出加权和。
现在采用三层的RBF网络结构(图2)。
其中网络的四个输入分别为激光能量密度
、环境压强
、沉积时间
和靶与衬底之间的距离
作为输入参数,聚合效率
预报模型的输出参数。
中间隐含层为7个高斯基函数。
输入层到隐含层的权值固定为1,隐含层到输出层之间的权值可调。
人工神经网络的学习算法如下:
(1)选择RBF网络隐层节点的中心:
中心可从学习样本中选取,在样本数较为密集处,中心数可适当多选;本文选择学习样本为基函数的中心;
(2)确定网络的基宽向量B;基宽向量的基宽度b由公式
计算选取,其中
为隐层中心节点间的最大距离,
为中心节点的个数;由上算法中的公式计算取为1.2;
(3)隐含层与输出层之间权值
的初始化:
选取数值较小量;
(4)输入一个学习样本,计算网络输出值
(1)
(5)输出权值
j、隐层节点中心
和节点基宽函数
的学习迭代算法:
(2)
(3)
(4)
(5)
(6)
其中
为学习步长;各个学习步长都取一个较小值0.2。
(6)反复输入学习样本,并调整所学习的三个参数;
(7)若学习达到所要求的性能指标,则停止;否则返回第4步;
其中网络的性能指标函数(误差精度)为:
(7)
N为学习的样本个数。
学习终止条件为
。
经过1014次训练后网络收敛。
训练和检验结果见表1。
可见训练样本与检验样本的网络实际输出与期望输出非常接近。
4粒子群算法优化
优化的基本方法是建立一个指标函数,通过在可行解集中迭代来改进指标函数值。
传统的优化方法是产生一个确定的试验解序列,当满足一定条件时这个确定序列收敛于局部最优解,但欲寻求全局最优解或指标函数中存在随机摄动时传
统方法就无能为力了,有学者将遗传算法引入材料工艺优化中来,取得了不错的效果[7]。
但是遗传算法要通过交叉(crossover)、变异(mutation)、选择(selection)等算子操作,因此收敛速度较慢,优化效率不高[8]。
而粒子优化群算法(PSO)是根据自己的速度来决定搜索,因此能圆满地解决上述问题
粒子群优化算法是Kennedy和Eberhart等在1995年提出的一种优化算法。
该算法模拟鸟集群飞行觅食的行为,通过鸟之间的集体协作使群体达到目的[9]。
其基本思想如下:
设在
维空间上考虑一个优化问题:
(8)
为此在
维空间上取
个点构成该算法的种群,用
的大小来评价每个点的优劣。
粒子
的信息可以用
维向量表示,位置表示为
速度为
其他向量类似。
则速度和位置更新方程为
(9)
(10)
本文所建立的粒子群优化的主要参数叙述如下:
1)优化结果空间:
1维,聚合效率
;
2)搜索空间为
:
4维,分别是激光能量密度
、环境压强
、沉积时间
和靶与衬底之间的距离
。
初始点的位置
及其速度
通常是在允许的范围内随机产生的。
并用RBF神经网络计算出其相应的值
,记录其中最好值
和序号
并置为当前位置
3)群体规模
:
12个初始粒子;
4)惯性权重
的确定:
=0.729;惯性权重
使微粒保持运动惯性,使其有扩展搜索空间的趋势,有能力探索新的区域
5)加速常数
和
的确定:
选择
=
=1.494;加速常数
和
代表将每个微粒推向
t和
位置的统计加速项的权重。
6)最大速度
的确定;选择
=1;为防止粒子远离搜索空间飞过好解。
7)指标函数的取得:
本例取为训练好的RBF神经网络评价每一个粒子计算粒子的适应度值。
如果好于该粒子当前的个体极值,则将
设置为该粒子的位置,且更新个体极值。
如果所有粒子的个体极值中最好的好于当前的全局极值,则将
设置为该粒子的位置,记录该粒子的序号,且更新全局极值;
8)粒子的更新;用式(9)和式(10)对每一个粒子的速度和位置进行更新。
9)优化终止条件
的确定:
学习次数达到400次;
采用上述算法每迭代100次显示一次优化结果见下表2,收敛过程见图3。
图3粒子群优化的收敛过程曲线
Fig3TheConvergenceCurveofPSO
表2粒子群算法优化结果
Table2OptimizationResultsofParticleSwarm
IterativeTimes
Fluence
(mJ/cm2pu)
Pressure
(Torr)
Distance
(mm)
Time
(Seconds)
Polym..Effic.Desired
100
4771.7
13.3
14.5
31.5
86.9
200
4763.8
10.2
16.2
30.6
95.2
300
4764.0
11.1
15.0
30.0
96.0
400
4764.1
11.0
15.0
30.0
96.0
由表2可得新型有机硅聚合物聚二苯基硅亚甲基硅烷(PDPhSM)基纳米复合薄膜的制备最优工艺为:
激光能量密度4764(mJ/cm2pu)、环境压强11(Torr)、靶与衬底之间的距离15(mm),沉积时间30(Seconds)。
5结论
(1)聚二苯基硅亚甲基硅烷(PDPhSM)基纳米复合薄膜的制备工艺受工艺参数等诸多因素的影响,致使数学模型在聚合效率预测方面受到很大的限制,而人工神经网络则能避免建立数学模型的复杂性以及用数学模型预测的某些局限性,并可以很好地对材料工艺与性能建模。
(2)粒子群算法比遗传算法表现出了更好的性能。
该算法与神经网络模型相结合,无疑为解决多维非线性系统及模型未知系统的优化问题提供了一个崭新而有效的途径。
这一新技术可望在材料工艺优化研究中的进一步推广及其在材料计算机辅助设计方面获得更为广泛的应用。
参考文献
[1]T.Ogawa,M.Murakami,J.Polym.Sci.-PartB:
Polym.Phys.1996,34:
1317.
[2]M.Suzuki,Y.Nakata,H.Nagai,T.Okutani,N.Kushibiki,M.Murakami,Mater.Sci.Eng.B.1997,42:
171.
[3]R.G.Song,M.Yamaguchi,Q.Nishimura,KShimokawa,N.Kushibiki,M.Suzuki,Effectoflaser-ablatedcoppernanoparticlesonpolymerizationof1,1,3,3-trtrapheny1,1,3-disilacyclobutane,AppliedPhysicsA:
MaterialsScience&Processing,2004,78:
867-875.
2003,6;32(3)
[4]PanQingyue.SONGRenguo.ZHANGQizhi.HUANGWeidong.ZHOUYaoheOnOptimizationofLaserSurfaceMeltingTechnologyfor1Cr18Ni9TiSteelBaseduponArtificialNeuralNetwork-GeneticAlgorithm.ChineseJournalofMaterialsResearch.1998.6.12.(3).
[5]FredricM.Ham.神经计算原理[M].机械工业出版社.2003年7月第1版106-110
[6]宋宜斌,王培进.基于径向基函数神经网络的非线性模型辨识[J].计算机工程,2004,30(5):
142-144
[7]R.G.SongQ.Z.Zhang,M.K.TsengandB.J.Zhang,TheApplicationofArtificialNeuralNetworkstoInvestigationofAgingDynamicsin7175AluminiumAlloy,Materialsscience&EngineeringC,1995,C3:
39.
[8]改进遗传算法与粒子群优化算法及其对比分析,北京师范大学学报(工程技术版)第2卷第2期
[9]KennedyJ,EberhartRParticleswarmoptimization[A].ProcIEEEIntConfonNeuralNetworks[C].Perth,1995.1942-1948.
.