天然橡胶的成型加工.docx
《天然橡胶的成型加工.docx》由会员分享,可在线阅读,更多相关《天然橡胶的成型加工.docx(14页珍藏版)》请在冰豆网上搜索。
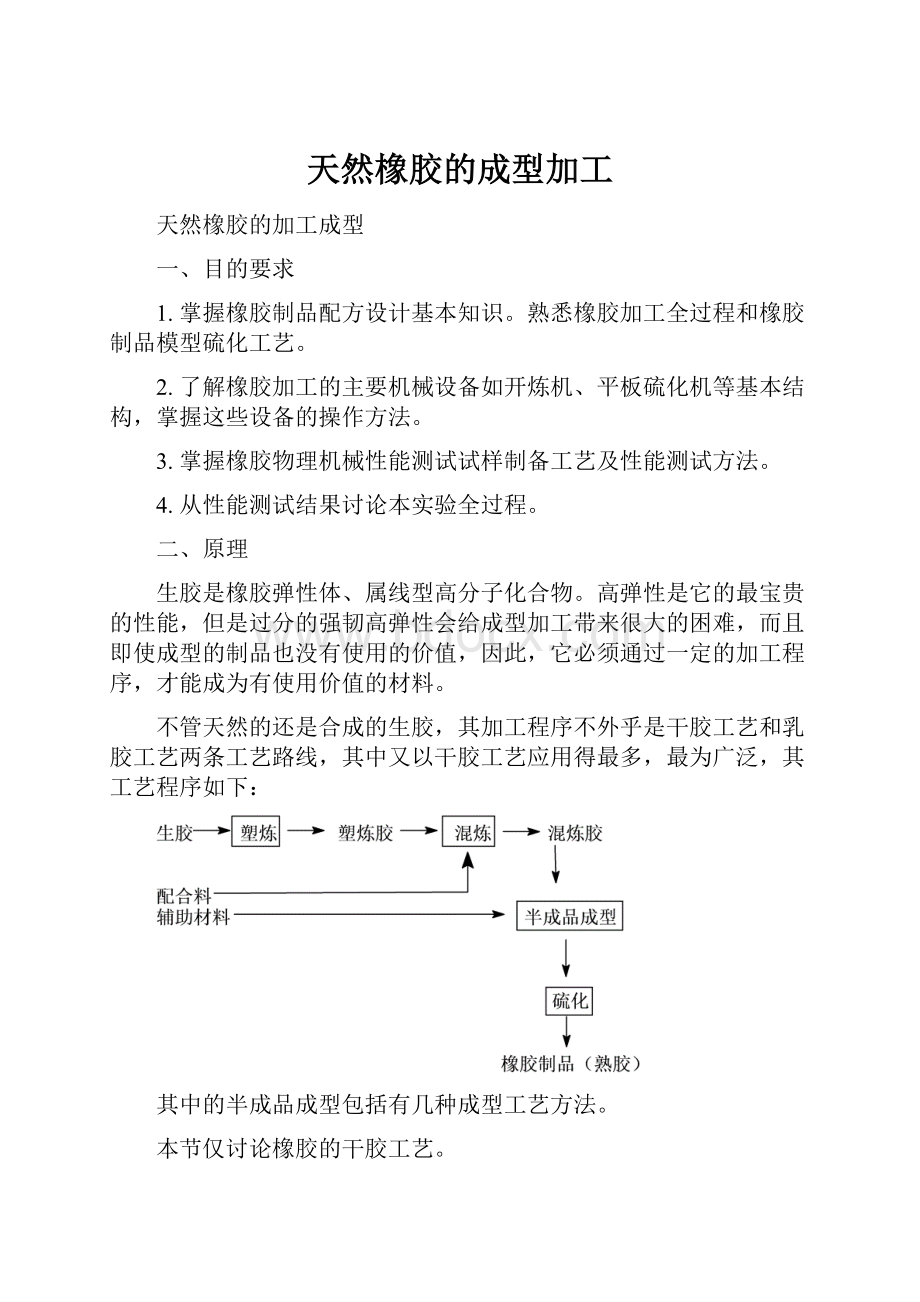
天然橡胶的成型加工
天然橡胶的加工成型
一、目的要求
1.掌握橡胶制品配方设计基本知识。
熟悉橡胶加工全过程和橡胶制品模型硫化工艺。
2.了解橡胶加工的主要机械设备如开炼机、平板硫化机等基本结构,掌握这些设备的操作方法。
3.掌握橡胶物理机械性能测试试样制备工艺及性能测试方法。
4.从性能测试结果讨论本实验全过程。
二、原理
生胶是橡胶弹性体、属线型高分子化合物。
高弹性是它的最宝贵的性能,但是过分的强韧高弹性会给成型加工带来很大的困难,而且即使成型的制品也没有使用的价值,因此,它必须通过一定的加工程序,才能成为有使用价值的材料。
不管天然的还是合成的生胶,其加工程序不外乎是干胶工艺和乳胶工艺两条工艺路线,其中又以干胶工艺应用得最多,最为广泛,其工艺程序如下:
其中的半成品成型包括有几种成型工艺方法。
本节仅讨论橡胶的干胶工艺。
塑炼和混炼是橡胶加工的两个重要的工艺过程,其目的是要取得具有柔软可塑性,将赋予一定使用性能的、可用于成型的胶料。
生胶的分子量通常都是很高的,从几十万到百万以上。
过分高的分子量带来的强韧高弹性给加工带来很大的困难,必须使之成为柔软可塑性状态才能与其它配合剂均匀混合,这就是需要进行塑炼。
塑炼可以通过机械的、物理的或化学的方法来完成。
机械法是依靠机械剪切力的作用助以空气中的氧化作用使生胶大分子降解到某种程度,从而使生胶弹性下降而可塑性得到提高,目前此法最为常用。
物理法是再生胶中冲入相容性好的软化剂,以削弱生胶大分子的分子间力而提高其可塑性,目前以充油丁苯橡胶用的比较多。
化学塑炼则是加入某些塑解剂,促进生胶大分子的降解,通常是在机械塑炼的同时进行的。
本实验是天然橡胶的加工,选用开放式炼胶机进行机械法塑炼。
天然生胶置于开炼机的两个相向转动的滚筒间隙中,在常温(小于50℃)下反复被机械作用,受力降解;与此同时降解后的大分子自由基在空气中的氧化作用下,发生了一系列力学与化学反应,最终可以控制达到一定的可塑度,生胶从原先强韧高弹性变为柔软可塑性,满足混炼的要求。
塑炼的程度和塑炼的效率主要与滚筒的间隙和温度有关,若间隙愈小,塑炼效率愈高。
此外,塑炼的时间,塑炼的工艺操作方法及是否加入塑解剂也影响塑炼的效果。
生胶塑炼的程度是以塑炼胶的可塑度来衡量的,塑炼过程中可取试样测量,不同的制品要求具有不同的可塑度,应该严格控制,过分塑炼是有害的。
随着合成橡胶工业的发展,为了适应橡胶加工的需要,目前国内外合成橡胶工业上在聚合反应时严格控制聚合物的分子量,使生胶具有一定的可塑性,这便可以省去了塑炼工序,此时炼胶就仅限于生胶与配合剂的混炼了。
但是,由于橡胶制品种类繁多,胶料的配方和成型工艺过程的不同,对胶料可塑度的要求差异是很大的,所以,在大多数的情况下,塑炼仍然是必要的。
本实验的天然橡胶加工,塑炼是必不可少的。
混炼是在塑炼胶的基础上进行的又一个炼胶工序。
本实验也是在开炼机上进行的。
为了取得具有一定的可塑度且性能均匀的混炼胶,除了控制辊距的大小,适宜的辊温(小于50℃)之外,必须注意按一定的加料混合程序。
即量小难分散的配合剂首先加到塑炼胶中,让它有较长的时间分散;量大的配合剂则后加。
硫磺用量虽少,但应最后加入,因为硫磺一旦加入,便可能发生硫化反应,过长的混合时间将使胶料的工艺性能变坏,与其后的半成品成型及硫化工序都不利。
不同的制品及不同的工艺要求混炼胶的可塑度、硬度等都是不同的,混炼过程要随时抽样测试,并且要严格混炼的工艺条件。
本实验所列的配方表明是通过实验取得一软质的橡胶片(制品)。
橡胶制品即硫化胶的硬度主要取决于其硫化程度,按软硬程度通常可分软质胶、半硬质和硬质胶。
本实验配方中的硫磺含量在5份之内,交联度不很大,所得制品柔软。
选用两种促进剂对天然胶的硫化都有促进作用;不同的促进剂协同使用,是因为它们的活性强弱及活性温度有所不同,在硫化时将使促进交联作用更加协调、充分显示促进效果。
助促进剂即活性剂在炼胶和硫化时起活化作用。
化学防老剂多为抗氧剂,用来防止橡胶大分子因加工及其后的应用过程的氧化降解作用,以达到稳定的目的。
石蜡与大多数橡胶的相容性不良,能集结于制品表面起到滤光阻氧等防老化效果,并且对于加工成型有润滑性能。
碳酸钙作为填充剂有增容降成本作用,其用量多少也影响制品的硬度。
由于橡胶制品种类繁多,其成型方法也是多种多样的,最常见的有模压、注压、压出和压延等。
由于橡胶大分子必须通过硫化处理才能成为最终制品,所以橡胶制品的成型有很大部分仅限于半成品的成型。
例如压出和压延等方法所得的具有固定面形状的连续型制品以及某些通过几部分半成品贴合而成的结构比较复杂的模型制品,其后要经硫化反应才定型为制品。
至于注压和模压成型的制品其硫化已在成型时同时完成,所得的就是最终的制品。
本实验要求制取一块天然软质硫化胶片,其成型方法采用模压法,通常又称为模型硫化。
它是一定量的混炼胶置于模具的形腔内通过平板硫化机在一定的温度和压力下成型,同时经历一定的时间发生了适当的交联反应,最终取得制品的过程。
天然橡胶的主要成分是异戊二烯的聚合物,在分子的主链上有双键,硫化反应主要发生在大分子间的双键上。
其机理简述如下:
在适当的温度,特别是达到了促进剂的活性温度下,由于活性剂的活化及促经剂的分解成游离基,促使硫磺成为活性硫,同时聚异戊二烯主链上的双键打开形成橡胶大分子自由基,活性硫原子作为交联键桥时橡胶大分子间交联而成立体网状结构。
双键处的交联程序与交联剂硫磺的用量有关。
硫化胶作为主体网状结构并非橡胶大分子所有的双键处都发生交联,交联度与硫磺的量基本上是成正比关系的。
所得的硫化胶制品实际上是松散的、不完全的交联结构。
成型时施加一定的压力有利于活性点的接近和碰撞,促进了交联反应的进行;也为了利于胶料的流动,以便取得具有适宜的密度和与模具型腔相符的制品。
硫化过程要保持一定的时间,主要是由胶料的工艺性能来决定,也是为了使交联反应达到配方设计所要求的程序。
硫化过后,不必冷却即可脱模,模具内的胶料已交联定型为橡胶制品。
三、仪器设备和原料
(一)仪器设备
1.双辊筒炼胶机
(1)主要技术参数:
辊筒工作直径:
160mm
辊筒工作长度:
320mm
前辊筒转速:
24r/min(后辊)17.8r/min
最大辊距:
4.5mm
最小压片厚度:
0.2mm
加料量:
0.2-0.5KG
最高加热温度:
200℃
(2)配套电机
齿轮减速三相异步电动机
电动机功率5.5kW
2.电热平板硫化机
平板硫化机是电动油压机,有两个工作层、柱式、下压式。
平板压机是模压成型时通过模具对胶料施加压力和提供热源的设备,可用于橡胶和塑料等压制成型。
(1)主要技术参数:
公称合摸力:
500KN
液压系统工作压力:
16MPa
柱塞最大行程:
250mm
柱塞直径:
200mm
合模速度:
13mm/s
热板间距:
125mm
热板块数:
2
垫板尺寸:
400mm×400mm
热板单位压力:
3.12MPa
单块热板加热功率:
3KW
最高工作温度:
200℃
电动机功率:
1.5KW
平板硫化机的动作是由一组按钮操纵电动机的运转及停止的,此外,装在控制阀上的操作手柄可以控制油压系统的液流方向。
压板的加热温度由热电偶温度控制器及接触器控制。
3.LWK微控电子拉力实验机
本机主要有测力及载荷指示机构、加荷机构、试样变形测量机构、载荷—变形曲线记录装置以及控制部分、电器转动部分等组成。
本机基本原理是采用硅整流、直流电动机无级调速系统传统,以一定的拉伸速度对试样加荷,试样所受载荷由杠杆—摆式测力机构测量并在指示盘上指出数值。
本机适用于高分子材料如橡胶、塑料及编织物等作拉伸实验;变换相应的夹具还可以做压缩、弯曲等力学强度试验。
(1)主要技术参数:
最大载荷:
2500N
载荷指示盘测量范围与最小格指示值:
0~500N1N/格
0~1000N2N/格
0~2500N5N/格
示值精度:
相对误差:
(按国家标准规定)≤1%
拉伸速度调节范围:
5~500mm/min
试验净空间:
1000mm×400mm
4.其它仪器、设备
(1)胶机械性能测试试样裁剪机及裁刀
(2)A型邵氏硬度计
(3)测厚仪、游标卡尺
(4)橡胶试片标准模具等
(二)原料(配方)
实验配方由指导教师给出,引导学生对配方的分析。
天然橡胶100.0(Wt)
硫磺2.5
促进剂CZ1.5
促进剂DM0.5
硬酯酸2.0
氧化锌5.0
轻质碳酸钙40.0
石蜡1.0
防老剂4010-NA1.0
着色剂0.1
此配方为软质胶制品,用于成型标准试样用的胶片。
四、实验程序
1.配料
按上列的配方准备原材料,准确称量并复核备用。
2.生胶塑炼
(1)在指导教师和实验室工作人员指导下,按机器的操作规程开动开放式炼胶机,观察机器是否运转正常。
(2)破胶:
调节辊距1.5mm,在靠近大牙轮的一端操作,以防损坏设备。
生胶碎块依次连续投入两辊之间,不宜中断,以防胶块弹出伤人。
(3)薄通:
胶块破随后,将辊距调节到约0.5mm,辊温控制在45℃左右(以自来水降温)。
将破胶后的胶片在大牙轮的一端加入,使之通过辊筒的间隙,使胶片直接落到接料盘内。
当辊筒上已无堆积胶时,将胶片扭转90o角重新投入到辊筒的间隙中,继续薄通到规定的薄通次数为止。
(4)捣胶:
将辊距放宽至1.0mm,使胶片包辊后,手握割刀从左方向右割至近右边边缘(不要割断),再向下割,使胶料落在接料盘上,直到转筒上的堆积将消失时才停止割刀。
割落的胶随着辊筒上的余胶带入辊筒的右方,然后再从右方向同样割胶。
这样的操作反复操作多次。
(5)辊筒的冷却:
由于辊筒受到摩擦生热,辊温要升高,应经常以手触摸辊筒,若感到烫手,则适当通入冷却水,使辊温下降,并保持不超过50℃。
(6)经塑炼的生胶称苏炼胶,塑炼过程要取样作可塑度试验,达到所需塑炼程度时为止。
3.胶料混炼
(1)调节辊筒的温度在50~60℃之间,后辊较前辊略低些。
(2)包辊:
塑炼胶置于辊缝间,调整辊距使塑炼胶既包辊又能在辊缝上部有适当的堆积胶。
经2~3分钟的辊压、翻炼后,使之均匀连续地包裹在前辊筒上,形成光华无隙的包辊胶层。
取下胶层,放宽辊距至1.5mm左右,再把胶层投入辊缝使其包于后辊,然后准备加入配合剂。
(3)吃粉:
不同配合剂要按如下顺序分别加入。
1首先加入固体软化剂,这是为了进一步增加胶料的塑性以便混炼操作;同时因为分散较困难,先加入是为了有较长的时间混合,有利于分散。
2加入促进剂、防老剂和硬酯酸。
促进剂和防老剂用量少,分散均匀度要求搞,也应较早加入多混些时间,有助于分散。
此外,有些促进剂如DM类对胶料有增塑效果,早些加入利于混炼,防老剂早些加入又可以防止混炼时可能出现温升而导致的老化现象。
硬酯酸是表面活性剂,它可以改善亲水性的配合剂和高分子的润湿性,当硬酯酸加入后,就能在胶料中得到良好的分散。
3加入氧化锌。
氧化锌是亲水性的,在硬酯酸之后加入有利于其在橡胶中的分散。
4加入补强剂和填充剂。
这两种助剂配比较大,要求分散好本应早些加入,但由于混炼时间过长会造成粉料结聚,应采用分批、少量投入法,而且需要相当长的时间才能逐步混入到胶料中。
5液体软化剂具有润滑性,又能使填充剂和补强剂等粉料结团,不宜过早加入,通常要在填充剂和补强剂混入之后才加入的。
6硫磺是最后加入的,这是为了防止混炼过程出现焦烧现象,通常在混炼后期加入。
但对于丁腈胶混炼,硫磺则宜早些加,因为它在丁腈胶中分散尤其困难。
再者,若配方中的硫磺用量高达30~50份的硬质胶中,如果最后加硫,在较短时间内是难以分散均匀的,而混炼时间过长又易引起焦烧,此情况下,可以先加硫磺混匀,最后才加入促进剂,即促进剂和硫磺必须前后分开加入。
吃粉过程每加入一种配合剂都要捣胶两次。
在加入填充剂和补强剂时要让粉料自然地进入粉料中,使之与橡胶均匀接触混合,而不必急于捣胶;同时还需要逐步调宽辊距,使堆积胶保持在适当的范围内。
待粉料全部吃进后,由中央处割刀分往两端,进行捣胶操作促使混炼均匀。
(4)翻炼:
全部配合剂加入后,将辊距调至0.5~1.0mm,通常用打三角包、打卷或折叠及走刀法等进行翻炼至符合可塑度要求时为止。
翻炼过程应取样测定可塑度。
1打三角包法:
将包辊胶割开用右手捏住割下的左上角,将胶片翻至右下角;用左手将右上角胶片翻至左下角,以次动作反复至胶料全部通过辊筒。
2打卷法:
将包辊胶割开,顺势向下翻卷成圆筒状至胶料全部卷起,然后将卷筒胶垂直插入辊筒间隙,这样反复至规定的次数,即混炼均匀为止。
3走刀法:
用割刀在包辊胶上交叉割刀,但不割断胶片,使胶料改变受剪切力的方向,更新堆积胶。
翻炼操作通常是3~4分钟,待胶料的颜色均匀一致,表面光滑即可终止。
(5)混炼胶的称量:
按配方的加入量,混炼后胶料的最大损耗为总量的0.6%以下,若超过这一数值,胶料应予报废,须重新配炼。
(6)混炼时的注意事项:
1在开炼机上操作必须严格按操作规程进行,要求高度集中注意力。
2割刀时必须在辊筒的水平中心线以下部位操作。
3禁止带手套操作。
辊筒运转时,手不能接近辊缝处;双手尽量避免越过辊筒水平中心线上部,送料时手应作握拳状。
4遇到危险时应立即触动安全刹车。
5留长辫子的学生要求戴帽或结扎成短发后操作。
4.胶料模型硫化
成型实验是要制备一块160mm×120mm×2mm的硫化胶片,供机械性能测试用。
模型硫化是在250kN平板硫化机上进行的,模型则是型腔尺寸为160mm×120mm×2mm的橡胶标准试片用的平板模。
(1)混炼胶试准备。
混炼胶首先经开炼机热炼成柔软的厚胶片,然后裁剪成一定的尺寸备用。
胶片裁剪的平面尺寸应略小于模腔面积,而胶片的体积要求略大于模腔的容积。
(2)模具预热。
模具经清洗干净后,也可以在模具内腔表面涂上少量脱模剂,然后置于硫化机的平板上,在硫化温度145℃下预热约30min。
(3)加料模压硫化。
将已准备好的胶料试样毛胚放入以预热好的模腔内,并立即合模置于压机平板的中心位置,然后开动压机加压,胶料硫化压力为2.0MPa。
当压力表指针指示到达所需的压力时,开始纪录硫化时间。
本实验要求保压硫化时间为10min,在硫化到达预定时间后,却掉平板间的压力,立即趁热脱模。
(4)硫化胶试片制品的停放。
脱模后的试片制品放在平整的台面上在室温下冷却并停放6~12h,才能进行性能测试。
5.硫化胶机械性能测试
试验在23℃左右的室温下进行。
(1)邵氏硬度试验(A型)
橡胶的硬度即其软硬程度,是表示其抵抗外力侵入的能力。
常用邵氏硬度计测量橡胶的硬度。
其工作原理是通过外力使硬度计的压针以弹簧的压力压入试样的表面,以压针陷入的深度程度来表示其硬度。
①试样的准备
待测的天然硫化胶试片厚度不小于6mm,若试样厚度不够,可用同样的试样重叠,但胶片试样的叠合不得超过4层,且要求上、下两层平面平行。
试样的表面要求光滑、平整、无杂质等。
②硬度测试。
a.首先在测试橡胶之前,于硬度计上加上定负荷10N,使硬度计的压针压在玻璃工作台上,此时硬度计指针应指示在100格的位置上,否则对硬度计应予调整。
b.把橡胶试样放在硬度计的玻璃工作台上,当硬度计的加压面与橡胶试样全部接触后,指针上的读数即为试样的硬度值。
c.试样上每一个测量点只测一次,每一试样测量三点,取其中值或平均值。
d.硬度计的刻度盘上分为100格,每一小格为一硬度值,数值愈大,表示橡胶愈硬。
(2)拉伸强度试验。
拉伸强度实验是测量材料的物理机构性能的重要项目,对橡胶的加工成型过程的胶料及硫化胶,通过拉伸强度试验可以测其扯断强度、定伸强度、扯断伸长率和永久变形等指标。
可以衡量和比较成品、半成品的质量;也能为原材料、配方和加工工艺的研究等提供有力的依据。
①试样的准备。
硫化胶试片经过12h以上的充分停放后,用标准裁刀在剪裁机上冲裁成哑铃型的试样。
通用型裁刀的形状和尺寸规格如图3-1。
同一试片工作部分(C)的厚度差异范围不准超过0.1mm,每一种硫化胶试样的数量为5个。
试样的厚度规定为2mm。
试样裁切参阅国家标准GB528-76的规定。
②试验步骤。
拉伸强度试验在LWK—微控电子拉力实验机上进行。
a.将5个试样编号,在试样的工作部分印上两条距离为25±0.5mm的平行线,标线的粗度不超过0.5mm。
b.用测厚计测量标距内的试样的厚度,测量部位为中心处及两标线附近共三点,取其平均值。
c.对拉力机选择适宜的量程。
d.把试样垂直地夹在拉力机上的上、下夹具上。
使上夹具以500±10mm的速度上升,对试样进行拉伸。
根据实验项目要求记录测试的各项数据,当试样的工作部分被拉伸到达规定伸长的100%、300%时,记录其定伸负荷;当试样被拉断时,同时记录工作部分被扯断时的伸长值L1—L0;最后,把扯断的试样两部分取下来,放置三分钟后对接起来并测量原工作部分的长度L2。
拉伸强度实验的各项数据记录在下面的表格上。
③注意事项。
a.当试样被拉断是发生在试样的标距以外或断面上有严重的缺陷或杂质时,该试样所得的数值作废。
b.每组试样拉伸实验不少于5个。
五、实验结果分析、计算
1.天然橡胶拉伸强度:
试样编号
1
2
3
4
5
平均值
工作部分宽度b(cm)
工作部位厚度h(cm)
定伸100%负荷P(N)
定伸100%强度σ100(MPa)
定伸300%负荷P(N)
定伸300%强度σ300(MPa)
扯断负荷P(N)
扯断强度σ(MPa)
L1—L0(mm)
扯断伸长率ε(%)
L2(mm)
永久变形Hd(%)
2.同一实验的5个样品经取舍后的个数不应少于原试样的数的60%,试样取舍可以取中值,即舍弃最高和最低的数值;或把所有5个数值取其平均值。
3.计算
(1)拉伸(扯断)强度(MPa)
13-1
式中P:
拉伸(扯断)负荷(N)
b:
试样宽度(cm)
h:
试样厚度(cm)
(2)扯断伸长率(%)
×10013-2
式中L0:
试样原始标线距离(mm)
L1:
试样断裂时标线距离(mm)
(3)永久变形Hd:
13-3
式中L2:
断裂的两块试样静置3min后拼接起来的标线距离(mm)。
4.分析硫化胶的外观质量和机械性能与实验配方和工艺操作等因果关系。
六、思考题
1.天然生胶、塑炼胶、混炼胶和硫化胶,它们的机械性能和结构实质有何不同?
2.影响天然胶开炼机塑炼和混炼的主要因素有哪些?
3.胶料配方中的促进剂为何通常不只用一种呢?