电镀镍厚控制以及金成本改善重点.docx
《电镀镍厚控制以及金成本改善重点.docx》由会员分享,可在线阅读,更多相关《电镀镍厚控制以及金成本改善重点.docx(32页珍藏版)》请在冰豆网上搜索。
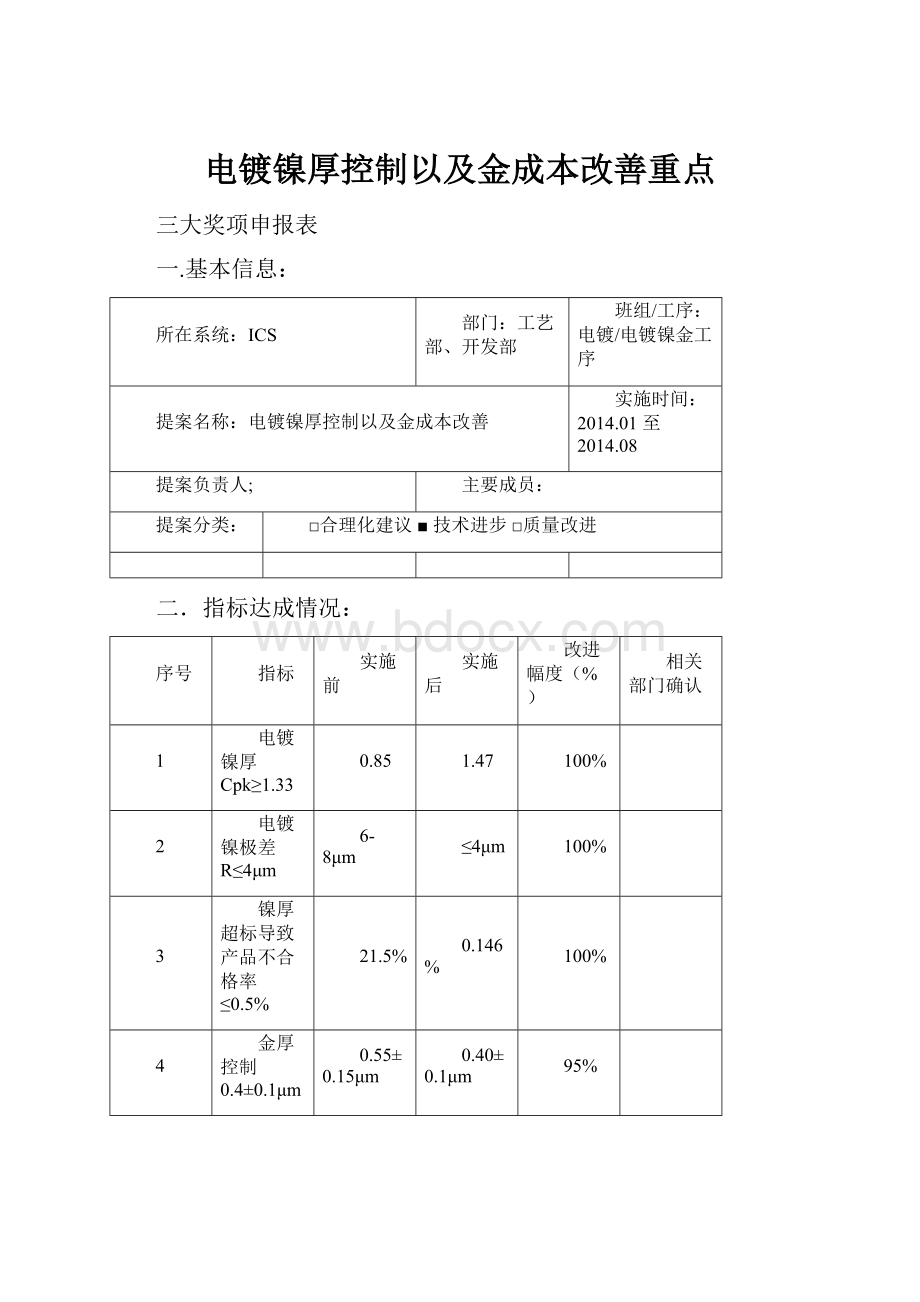
电镀镍厚控制以及金成本改善重点
三大奖项申报表
一.基本信息:
所在系统:
ICS
部门:
工艺部、开发部
班组/工序:
电镀/电镀镍金工序
提案名称:
电镀镍厚控制以及金成本改善
实施时间:
2014.01至2014.08
提案负责人;
主要成员:
提案分类:
□合理化建议■技术进步□质量改进
二.指标达成情况:
序号
指标
实施前
实施后
改进幅度(%)
相关部门确认
1
电镀镍厚Cpk≥1.33
0.85
1.47
100%
2
电镀镍极差R≤4μm
6-8μm
≤4μm
100%
3
镍厚超标导致产品不合格率≤0.5%
21.5%
0.146%
100%
4
金厚控制0.4±0.1μm
0.55±0.15μm
0.40±0.1μm
95%
5
金成本控制减低30%
0%
40.26%
100%
6
金成本节约70万/月
0
89.8425万元/月
100%
设备产出5000平米可节约金额。
7
镍厚改善良率提升产品节约成本200万/月
0
336.473万元/月
100%
同上。
备注:
1.指标(提案价值点及实际成果)的填写可参考三大奖项评价标准,包含但不限于:
价值增加额度、质量改进幅度、效率提升幅度、成本降低幅度,相关数据均需相关部门负责人签字确认。
2.涉及“增加税前利润”的计算过程(计算数据须以财务部核准的数据为基本依据,并经财务经理确认):
(期间:
6个月以上;计算公式=增量收入-相关的成本费用支出。
)
三.周边评价
序号
评价部门(班组)
评分(0-100分)
建议或意见
评价人
1
品质部
90
该项目措施已应用于生产
2
生产部
90
有显著改进
备注:
周边评价部门为该提案实施以及应用中相关关联部门。
四.审核意见(详细内容请参阅总结报告):
部门意见:
1.指标达成情况:
□目标达成■目标部分达成□目标未达成
2.转化成熟度:
□无须形成规范
□成果尚未形成规范或检验中□成果已形成临时规范
□成果已形成正式规范,局部需改进■成果已形成正式规范运行持续有效
3.创新性评价:
□公司内领先■行业内国类领先□行业内全球领先
□改进型创新□根本型创新
3.其余说明与意见:
签名:
日期:
系统意见:
签名:
日期:
电镀镍厚控制以及金成本改善总结报告
1.背景
ICS封装基板电镀镍-金产品中,95%以上的客户对电镀镍金厚度以及手指宽度、间距提出明确的品质管控要求。
如手指宽度控制因客户工程文件要求存在一定制作难度以及前工序(蚀刻)制成能力偏差,这对电镀镍金工序的电镀镍厚控制提出更高要求。
ICS电镀镍金线设备初期电镀镍厚极差为6-8μm,这很难满足客户对电镀镍金产品的品质要求,使得前期电镀镍金产品因镍厚不合格产生大量报废,特殊产品报废率可达60%,制程能力低下。
因此改善电镀镍厚控制,提高镀镍制程能力具有积极的意义。
在封装基板生产过程中,金厚控制范围为0.3-1.0μm,金成本在整个ICS物料消耗中占据很大的组成部分。
因此通过提高镀金均匀性、优化板边设计、控制金厚以及减少金盐带出等手段对金成本控制具有非常显著以及积极的效果。
2.目标
通过优化改善电镀镍厚控制,提高产品合格率,使得电镀镍极差R≤4μm,电镀镍镍金产品因电镀镍厚超标的报废率由最高50-60%降低至0.25%。
金成本减低30%左右。
实现电镀参数导入程序化、自动化,减少人为导入的错误,提高生产效率。
3.过程实施
3.1电镀镍厚控制
对电镀镍厚控制过程需结合电镀镍均匀性调整、飞巴与挂具间电镀镍厚偏差以及参数优化等过程。
其镍厚控制改善思路如下:
3.1.1电镀镍均匀性改善
电镀镍均匀性提升主要通过改善设备几何尺寸、设计阴极挡板、阴极排布以及阴阳极相关位置。
其改善过程如下表所示:
No
改善过程说明
改善示意图
改善结果
极差:
μm
1
设备初期,电镀镍几何条件为设备原厂设计。
设备初期测试电镀镍厚极差在6-8μm
8.625
2
增大阴极槽体顶部开窗尺寸,槽体开窗尺寸由原来400×505mm调整为400×545mm
6.076
3
去除阴极挡板:
由前期测试结果显示,除去阴极顶、底部挡板。
6.989
4
提高阳极高度,由电镀镍厚偏差计算将阳极高度提高20mm。
4.205
5
在前期电镀均匀性测试结果的基础上,通过增大阴阳挡板左右开窗尺寸,阴极挡板左右开窗尺寸由原来335mm增加到400mm
6.145
6
基于前期电镀均匀性测试结果显示,对阴极底部挡板进行调整优化
4.228
7
根据前期对阴极挡改善结果显示,影响目前电镀均匀性的主要因素有:
1:
整流器电流在各板面上分布;2:
电镀“边缘效应”,故优化阴极挡板改善。
4.185
8
优化阳极排布与堵孔改善,基于前期测试结果显示,为改善电镀边缘效应,此次测试采用左右堵孔进行改善。
3.508
由上表显示,经过对设备几何尺寸进行一系列的优化调整,使得电镀镍均匀性较设备初期有了很大的改善与提高。
其数据详细显示如下表所示:
控制指标
极差R:
μm
变异系数COV
Cpk
板编号
Panl1
Panl2
Panl3
Panl4
全巴
Panl1
Panl2
Panl3
Panl4
全巴
全巴
设备初期
6.54
7.32
5.47
6.87
8.625
——
——
——
——
21.50%
0.65
初期调整
2.4
3.887
3.14
4
4.407
——
——
——
——
15.27%
0.74
中期
调整
增大槽体开窗
6.006
4.657
6.002
4.573
6.076
14.04%
10.85%
15.81%
12.28%
13.60%
0.89
除去挡板
6.232
5.408
5.029
5.352
6.989
12.83%
13.44%
12.66%
12.33%
14.44%
1.05
调整阳极排布
7.12
4.88
6.02
5.15
8.62
12.60%
11%
13.70%
12.40%
14.80%
0.95
提高阳极高度
4.416
3.865
3.834
4.205
4.884
9.60%
8.80%
8.20%
9.70%
9.71%
1.37
增大阴极开窗
6.145
4.36
3.819
5.167
6.145
17.25%
10.59%
9.37%
10.28%
12.11%
1.59
提高液位
,中心堵孔
6.348
4.415
3.713
6.034
7.138
20.40%
12.50%
10.10%
13.80%
16%
1.06
优化底部挡板
4.524
3.388
2.892
3.064
4.228
6.73%
8.12%
6.21%
8.14%
8.42%
1.19
后期
优化
阴极挡板优化
2.327
2.031
3.179
4.04
4.185
4.70%
5.50%
7%
9.90%
8.49%
1.36
阳极排布优化
4.677
2.452
2.065
2.067
4.85
11.40%
7.10%
5.70%
5%
8.90%
1.76
开孔优化
2.358
2.096
2.087
3.208
3.501
6.80%
6.30%
6.60%
10.10%
9.20%
1.37
总结;优化后电镀镍均匀性可以达到极差R<4μm,COV<10%,Cpk>1.33.
3.1.2飞巴、挂具电镀镍厚偏差测试
1)测试条件
每个飞巴测试均采用相同图形的板材,在相同电镀参数条件进行测试,在测试过程中,不同飞巴上电流输出精度偏差以及外电路电阻结果如下表所示:
Items
电流输出精度偏差:
外电路电阻:
欧姆
Top
Bottom
Top
Bottom
min
0%
0%
0.15
0.12
max
0.23%
0.08%
0.17
0.14
Average
0.12%
0.05%
0.152
0.13
由记录结果显示,各飞巴电镀镍过程为稳定过程,电流输出精度偏差为0.05-0.12%,说明没有出现电流输出异常,Top/Bottom面电阻在0.13-0.152欧姆,由此可以说明,在生产过程中,各飞巴接触、导电性良好,未出现导电性异常由电流输出结果显示,测试过程中不存在因接触不良以及导电不良等现象。
由此可以排除整流器输出对电镀镍厚偏差的影响。
2)不同飞巴电镀镍厚测试结果
不同飞巴电镀镍厚测试结果
不同飞巴电镀镍极差与Cpk数值
由不同飞巴上电镀镍厚极差R与Cpk值显示可知,极差R在一定程度上同Cpk成反相关关系。
从整体测试结果显示可知,不同飞巴极差满足R小于4μm,Cpk大于1.33的管控要求。
3)不同电镀镍槽体电镀镍厚偏差
通过对6个槽体电镀镍厚在Top/Bottom面进行对比分析。
统计960组数据,计算板材Top/Bottom面在6个槽体中电镀镍厚的Min、Max、R、Average、COV和Cpk值。
其结果如下所示:
Top
Bottom
Min
5.376
Min
5.617
Max
9.252
Max
10.02
Ave
7.35
Ave
7.111
R
3.876
R
4.403
COV
9.55%
COV
9.40%
Cpk
1.49
Cpk
1.29
由测试结果显示,电镀A槽6个槽体电镀镍具有较好的同一性,即在相同电镀参数条件下,相同图形的试板以及相同的挂板方式,在不同槽体中进行电镀镍,其镍厚偏差小,6个槽体的Top面与Bottom面电镀镍Cpk值可达1.3以上。
由此说明槽体间不存在明显电镀镍厚偏差。
总结;通过对不同飞巴,不同槽体电镀镍厚偏差测试,由测试结果显示,不同飞巴间以及不同电镀槽体间电镀镍厚偏差最大在1μm左右,这对电镀镍厚控制非常有利。
3.1.3电镀镍参数优化
因电镀镍金线在运行过程中,因程序设定,电镀时间为固定36min。
因此影响电镀镍厚的两个关键因素为电流密度设置以及电镀面积。
1)过程分析
由法拉第定律分析电镀镍厚度与电流密度关系,并通过理论与实际拟合方程进行对比,对电镀镍厚电流效率进行修正。
由法拉第定律可知有方程成立:
,
由图形电镀图形分布的因素,使得实际电镀镍厚不仅与电流密度、电镀时间和电流效率等因素有关,还以图形分布,阴阳极面积比等因素有关。
不同图形面积下电流密度分布如下图所示
2)实验设计
设计不同受镀面积的板材镀相同镍厚(按照7.5μm进行控制),得出电流密度的变化情况。
板材编号
1
2
3
4
5
CS
SS
CS
SS
CS
SS
CS
SS
CS
SS
残铜率%:
20
18
16
14
12
10
8
6
4
2
受镀面积dm2
4.23
3.81
3.39
2.96
2.54
2.12
1.69
1.27
0.85
0.42
3)测试结果
通过对不同产品(方案设计中不同电镀面积的板材)电镀镍厚的电镀参数进行总结,得出以电镀镍厚为7.5μm,不同电镀面积与电流密度的关系如图2所示:
由上测试结果不同电镀面积镀相同电镀镍厚,得出电流密度与电镀面积的函数关系式如下所示:
4)实际产品分析
在实际产品生产过程中,对于MSAP产品存在通孔导通,即由CS面导入电流值一部分用于CS面电镀过程,一部分用于SS面通过通孔导通的电镀过程,其示意图如下所示,如下为实际由CS导电电镀面积与SS面导电电镀面积推算过程。
由上述推算可知,在生产首板过程中,由于设定电流密度Dk、电镀镍厚H以及CAM文件电镀面积等数据,可推算出由CS/SS面导电的电镀面积。
5)总结:
由上分析可知,对于ICS不同流程的电镀镍-金板材电镀参数设置存在一定差异性。
根据以上测试与推算结果,不同产品电镀参数设置方法如下所示:
产品
TLP流程产品
MSAP流程产品
电流密度设置
首板
调整参数
3.1.4标准化文件形成
基于以上改善与测试形成电镀镍-金生产首板制作文件,其电镀参数设置表如下所示:
电镀镍厚
电镀面积dm2
0.4-0.5
0.5-0.6
0.6-0.7
0.7-0.8
0.8-0.9
0.9-1.2
1.2-1.4
1.4-1.7
1.7-2.0
2.0-2.4
电流密度ASD:
0.32
0.35
0.48
0.6
0.8
1.05
1.15
1.35
1.4
1.42
电镀面积dm2
2.4-2.7
2.7-3.0
3.0-3.4
3.4-3.8
3.8-4.2
4.2-4.5
镀金电流密度在0.1-0.13ASD范围内
电流密度ASD:
1.42
1.5
1.55
附件为SOP规范电镀镍金制作首板参数设置表:
3.1.5参数设置自动导入开发
ICS电镀镍金线产品的种类多样,料号与批次号多而复杂,在生产过程中极其容易发生生产员工参数导入错误产生报废。
因此开发参数自动导入系统,减少参数计算、导入失误。
其前后对比如下:
过程对比
改善前(手动参数导入)
改善后(自动导入系统)
1
生产效率低下
大大生产效率高
2
容易产生计算、导入错误
防错误率高
3
多样产品生产,容易产生混淆
多产品生产区分度高
4
手动计算生产板数量
自动感应叠加生产板数量
5
产品信息科追索性差
产品生产信息具有可追索性
6
操作过程繁琐、复杂
操作方便、简单
生产参数自动导入过程如下:
3.2金成本控制
电镀金成本占电镀工序成本比例的重要一部分。
因此控制金成本具有非常重大的意义。
金成本控制主要通过改善板边文件设计、降低板面金盐带出以及控制金厚等措施进行。
3.2.1改善板边文件设计
对于ICS厂产品线路的制作过程目前包括两种,分别为Tenting与MSAP流程。
上述两种流程制作的区别体现在板边即为:
Tenting流程的产品距离板边2mm位置由于干膜未覆盖,经DES工步后表面的铜被蚀刻;MSAP流程为在干膜未被覆盖的位置进行电镀,因此板边均被铜填充。
上述两种流程中的任何一种图形的制作方法,经过阻焊曝光、显影及固化后板边会有10mm的开窗未能被阻焊覆盖。
阻焊工序未被阻焊覆盖的铜表面在电镀金工序均会有电流通过,电流通过的位置则会被金所覆盖,如图所示:
未优化前的板边设计
进一步调研其他厂区的电镀硬金线及电镀镍金线(如图所示),其中电镀硬金线采用板边包蓝胶的方法进行成本控制,但是该方法存在的问题:
1.增加人力与物力成本,且降低了平均产能,2.未被蓝胶包裹的位置仍然被金所覆盖。
电镀镍金线为防止出现板边及板中间的电镀极差过大,因此目前采用产品周围均由铜皮相连,并且曝露在外的铜皮经电镀镍金后被金覆盖,如果采用电镀硬金线的包蓝胶的方法,存在的问题主要包括:
1.增加流程,且容易在板面残留杂物,影响后续的处理工艺;2.板边的包胶经过镍缸及金缸时存在污染镍缸与金缸的危险。
因此目前上述两条电镀硬金及电镀镍金线均存在不同程度的镍金成本的浪费。
电镀硬金板边设计
电镀镍金板边设计
其他厂区采用的电镀金工艺
3.2理论设计方案
根据电镀金的工作机理,仅有与电镀金Jig夹点相连接的位置会有电流通过,从而导致电镀金,因此基于工序的工作原理,人为调整板边位置的设计,将未被阻焊覆盖的区域与镀金夹点进行蚀刻隔离,具体的设计更改措施为:
镀金夹点直接与主引线相连;镀金夹点周围区域设计为交错圆盘排列;针对MSAP流程,在镀金夹点边缘设计一条宽200um的间隙(外侧距板边1mm)将夹点与板边铜皮隔离。
上述方案更改如图所示:
优化前板边设计
优化后板边设计
3.3测试结果分析
对于更新设计后的Tenting及MSAP流程的产品进行测试(为节省成本,本次测试经过电镀金工序只进行预镀金,金厚小于0.05um),电镀金工序后由外观进行确认发现板边仅镀金Jig的夹点位置有镍金覆盖,其余未被阻焊覆盖的位置均未被金覆盖,因此通过优化后的板边设计可以达到降低镀金面积的目的,实际产品如图所示:
优化后MSAP流程产品
优化后Tenting流程产品
改善板边文件设计,减少不必要的镀金区域面积,这能够有效地减低金成本,其改善过程如下:
总结:
实际生产过程中,产品单面平均电镀面积为1.7dm2左右,未优化前板边被镀金的面积为0.4068dm2,其中电镀夹点的面积为0.01dm2(每个产品共10个夹点),如上板边文件修改可以因板边文件改善节约金成本为:
w=(0.4068-0.01*10)/1.7=18.05%。
3.2.2减少板面金盐带出改善
减低金成本能够有效的减低生产总成本,提高效率和工业化利润。
减低金成本主要有两种方法:
一种是减低电镀金层厚度,但是客户对电镀金层厚度上、下限具有明确的要求;另外一种是通过减少板面电镀金液残留带出而导致金盐的损耗,一般工厂采用增长镀金后板材在金槽上的滴液时间,但是这种方法对于减少板面金液残留是有限的,同时对提高生产效率的不利。
如下为ICS通过增设高压吹气,减少板面金盐残留,减低金带出损耗,对节约金成本具有积极的意义。
高压吹气装置主要由压缩空气装置、气压调节装置、电磁感应阀以及喷气管组成。
其具有结构简单,全自动控制以及可调控性强等优点。
根据实际生产板材厚度、孔径比以及板材尺寸等情况,要达到良好的金液赶出率,可以对吹气压力、喷嘴角度、喷嘴排布以及喷头进行优化调节。
在实际生产过程中,具有操作的灵活性。
其结构如下:
喷管排布
高压喷气线路图
喷嘴设计
喷头角度设计
如上为电镀ICS电镀镍-金线金缸上高压吹气赶液装置,其优化调整相关参数设置如下:
吹气压力
喷头角度
喷头到板距离
持续吹气时间
0.3-0.4Mpa
300±20
16±2cm
20s
总结:
如上设置高压吹气赶液装置,板面金液残留量大大减少,使得残留在板面上金盐能够有效的的返回到金槽中,其能有效地减低2%-3%的金成本。
3.2.3金厚控制
影响金成本另一个重要因素为金层厚度控制,有效的控制金层厚度能够显著得改善金成本。
由于电镀程序固定镀金时间为8min。
因此金层厚度受电镀面积、电流密度影响最为显著(其他条件如温度、循环量等为固定)。
1)实验设计:
通过均匀设计方法,考察镀金厚度与电流密度、电镀面积的关系,以期通过均匀设计与回归分析得出金厚与电流密度、电镀面积的方式式,并通过生产实际修正,应用于实际生产的金厚控制中。
均匀设计表头选取:
表头
U5(53)
U6(64)
U7(74)
U8(85)
U9(95)
D值
0.31
0.188
0.234
0.145
0.194
通过D值显示,均匀设计实验采用U8(85)的表头进行实验,其实验设计表头如下所示:
设计表头选取
s
列号
偏差:
D
2
1
3
0.1445
3
1
3
4
0.2000
4
1
2
3
5
0.2709
均匀设计实验
U8(85)
1
2
3
4
5
1
1
2
4
7
8
2
2
4
8
5
7
3
3
6
3
3
6
4
4
8
7
1
5
5
5
1
2
8
4
6
6
3
6
6
3
7
7
5
1
4
2
8
8
7
5
2
1
2)因素水平选取
根据实际生产经验,电镀面积变化为0.5-4.0dm2,镀金电流密度变化为0.095-0.13ASD间,故水平按如下进行设计。
No
1
2
3
4
5
6
7
8
电流密度:
ASD
0.095
0.1
0.105
0.11
0.115
0.12
0.125
0.13
电镀面积:
dm2
0.5
1.0
1.5
2.0
2.5
3.0
3.5
4.0
3);设计实验测试结果
通过均匀设计、回归分析拟合出金厚H关于电镀面积S以及电流密度Dk的函数关系式:
令y=H;Dk=x1、S=x2既有:
实验结果
No
电流密度:
ASD
受镀面积:
dm2
多项式
测试结果
x1
x2
x3=x1^2
x4=x2^2
x5=x1*x2
1
0.095
2
0.009025
4
0.000857
0.427
2
0.1
4
0.01
16
0.001
0.364
3
0.105
1.5
0.011025
2.25
0.001158
0.441
4
0.11
3.5
0.0121
12.25
0.001331
0.372
5
0.115
1
0.013225
1
0.001521
0.462
6
0.12
3
0.0144
9
0.001728
0.426
7
0.125
0.5
0.015625
0.25
0.001953
0.635
8
0.13
2.5
0.0169
6.25
0.002197
0.528
4):
回归分析与结果
采用Minitab软件对测试结果进行回归分析以及方差分析:
其回归分析与方差分析结果如下所示:
Predictor
Coef
SE-Coef
T
P
常量
3.5841
0.9381
3.82
0.032
x1
-57.01
16.64
-3.43
0.042
x2
-0.12684
0.03406
-3.72
0.034
x3
270.11
73.89
3.66
0.035
x4
0.018456
0.007389
2.5
0.088
Source
自由度:
DF
平方和:
SS
均方:
MS
F
P
Regression
4
0.053161
0.01329
25.24
0.012
Residual
3
0.00158
0.000527
All
7
0.054741
回