物流仓储成本优化改善作业现场.docx
《物流仓储成本优化改善作业现场.docx》由会员分享,可在线阅读,更多相关《物流仓储成本优化改善作业现场.docx(7页珍藏版)》请在冰豆网上搜索。
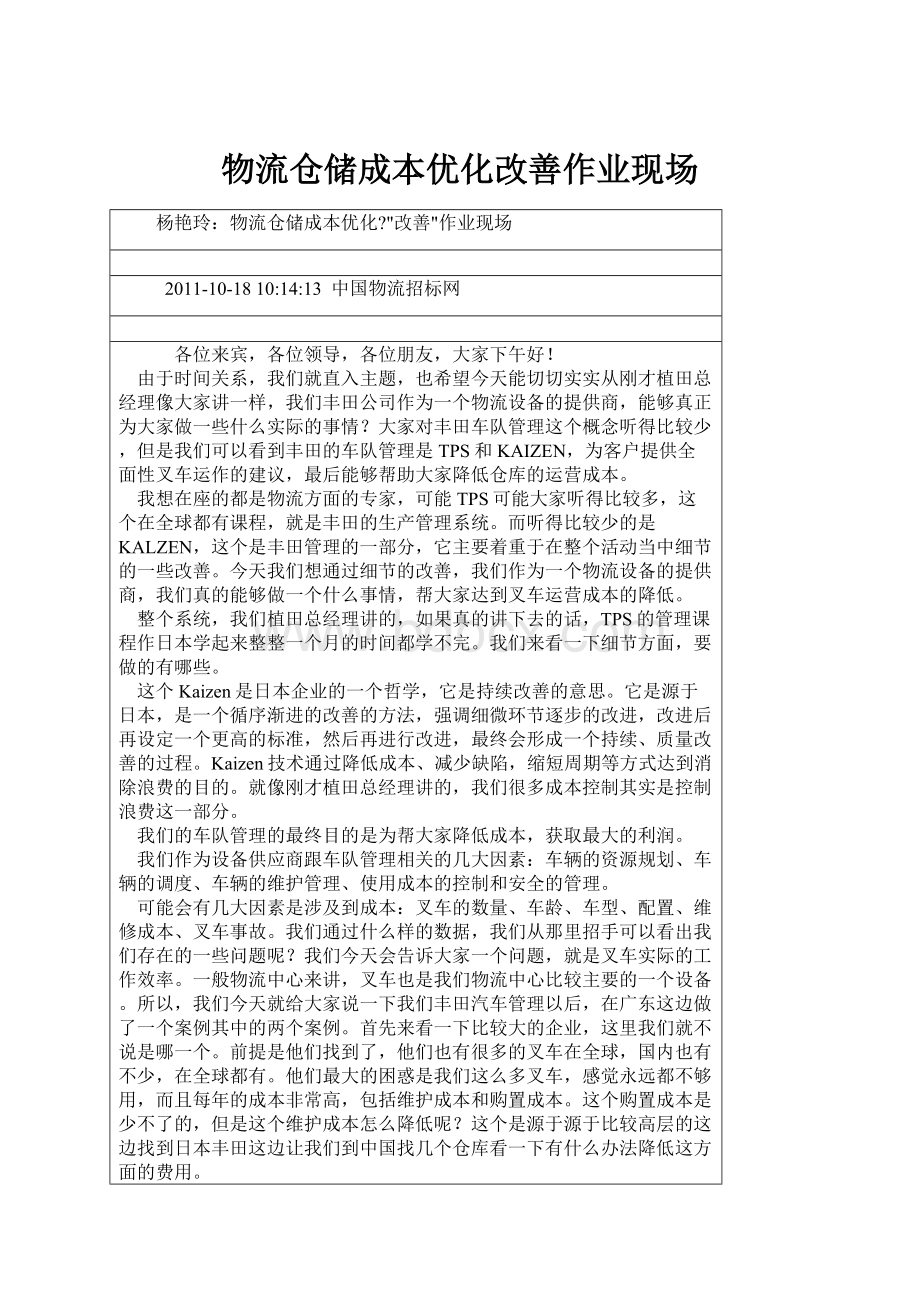
物流仓储成本优化改善作业现场
杨艳玲:
物流仓储成本优化?
"改善"作业现场
2011-10-1810:
14:
13 中国物流招标网
各位来宾,各位领导,各位朋友,大家下午好!
由于时间关系,我们就直入主题,也希望今天能切切实实从刚才植田总经理像大家讲一样,我们丰田公司作为一个物流设备的提供商,能够真正为大家做一些什么实际的事情?
大家对丰田车队管理这个概念听得比较少,但是我们可以看到丰田的车队管理是TPS和KAIZEN,为客户提供全面性叉车运作的建议,最后能够帮助大家降低仓库的运营成本。
我想在座的都是物流方面的专家,可能TPS可能大家听得比较多,这个在全球都有课程,就是丰田的生产管理系统。
而听得比较少的是KALZEN,这个是丰田管理的一部分,它主要着重于在整个活动当中细节的一些改善。
今天我们想通过细节的改善,我们作为一个物流设备的提供商,我们真的能够做一个什么事情,帮大家达到叉车运营成本的降低。
整个系统,我们植田总经理讲的,如果真的讲下去的话,TPS的管理课程作日本学起来整整一个月的时间都学不完。
我们来看一下细节方面,要做的有哪些。
这个Kaizen是日本企业的一个哲学,它是持续改善的意思。
它是源于日本,是一个循序渐进的改善的方法,强调细微环节逐步的改进,改进后再设定一个更高的标准,然后再进行改进,最终会形成一个持续、质量改善的过程。
Kaizen技术通过降低成本、减少缺陷,缩短周期等方式达到消除浪费的目的。
就像刚才植田总经理讲的,我们很多成本控制其实是控制浪费这一部分。
我们的车队管理的最终目的是为帮大家降低成本,获取最大的利润。
我们作为设备供应商跟车队管理相关的几大因素:
车辆的资源规划、车辆的调度、车辆的维护管理、使用成本的控制和安全的管理。
可能会有几大因素是涉及到成本:
叉车的数量、车龄、车型、配置、维修成本、叉车事故。
我们通过什么样的数据,我们从那里招手可以看出我们存在的一些问题呢?
我们今天会告诉大家一个问题,就是叉车实际的工作效率。
一般物流中心来讲,叉车也是我们物流中心比较主要的一个设备。
所以,我们今天就给大家说一下我们丰田汽车管理以后,在广东这边做了一个案例其中的两个案例。
首先来看一下比较大的企业,这里我们就不说是哪一个。
前提是他们找到了,他们也有很多的叉车在全球,国内也有不少,在全球都有。
他们最大的困惑是我们这么多叉车,感觉永远都不够用,而且每年的成本非常高,包括维护成本和购置成本。
这个购置成本是少不了的,但是这个维护成本怎么降低呢?
这个是源于源于比较高层的这边找到日本丰田这边让我们到中国找几个仓库看一下有什么办法降低这方面的费用。
它总共有2个仓库,总共有55台车,包括2台是租赁的车。
我们花了4天的时间,去了4人,2个人为一组。
我们看了它每一个仓库的叉车配置。
我们都是做物流的,我们一看觉得这些配置是非常合理的。
作为一个非常正常的物流中心来讲,前移式的叉车是上后架的,平衡这种叉车是装卸的,还会配合一些电动托盘车。
我们这样看上去,这也是我们作为物流设备商以前以来一直做的事情,以前给大家选型,都是按照这个思路选择叉车的。
我自己本身也做了十几年的,在丰田管理这个概念进来以前,我自己本身也没有办法发现有什么问题。
我们来看一下第二个仓库也是一样的,这个叉车的分配都是非常合理的。
那我们4天是干什么呢?
我们会到现场进行勘察和数据的采集,他们公司也提供了一些数据,我们会做叉车现状的分析,最终有了很详细的方案建议。
当然这4天时间是远远不够的,只是最初步的提案。
我们在现场会统计所有叉车的型号,门价的类型、提审高度、叉车力度、仪表的读数、出厂时间、货叉长度等。
这些都有什么用呢?
我们来看一下表格。
我们看到这总共有26台车。
这个表是客户提供给我们的,其实也是非常完善的物流公司的管理,它平时都会有很详细的数据统计、品牌、型号、叉车的车龄、12周叉车的使用时间。
这是第1周的叉车使用时间,这是第12周的叉车时间,这是我们现场抄的。
前面第1周的时间是客户提供给我们的。
作为这么大一个物流公司,在管理比较完善的情况下,我们把这个表格一统计之后,我们就发现整个仓库26台车,我们算了一个平均叉车的使用效率只有21%。
但是据我们了解,这个物流公司在我们这三条里面来讲是非常大的,所以他们的管理比较有序,而且运作量很大。
但是实际上我们发现一个惊人的数据,叉车的有效率才只有21%,但是他们还说车不够用。
我们来看一下叉车使用效率实际算出来,就是用叉车实际的运作时间除以实际的上班时间和自然工作时间,也就是自然放假时间除外,把两班倒的工作时间都算上去,得出的结果是48%。
比如有一个食品工资,我们会把它放假的时间都去掉以后,实际的运作效率是48%。
我们来看一下刚才的表格里面有什么问题存在。
当我们把这些数据都放大以后,我们会发现这些非常合理的叉车配置,这台45号车的使用率是0,买了很多年都是放在这里。
40号车几乎没有用过。
还有7号是使用率是1.5%,经常放在那里,给人感觉长期在用。
还有一台长期待修的车也在这里放着。
我们看到这个大型公司的操作作业很频繁,20个小时都在上班,但是我们看到实际平均使用率非常低,是什么原因造成这样一个数据呢?
刚才我们有很详细地抄这个数据,它有几个仓库,都是标准仓,所以高度都是一样,但是为什么会出现这样的情况呢?
我们带看一下门架的高度,有9.5米的,有4.5米的,有5米高的、6米等不同的门架高度。
我们统计了另一个仓库26台车,何种有7种车型,但是存在着9种门架。
大家都知道门架的高度都不一样,基本上货架的高度都是8米以上。
所以会存在一个问题就是你在使用一过程中不停地换车,所有的叉车都不能通用,只有几台有门架的,这样就造成我们的叉车越来越多,怎么样买都不够用。
第二个仓库的统计数据和操作方法是一样的,我们会发现可能会高一点,有33%。
但在这样一个使用效率,我们看到这个车都没有用,实际工作效率是1.4%,还有一台是长期待用的车,还有一台几乎是长期待修的。
在跟他们物流主管交流当中获得一个信息,这个车为什么没有用。
因为我们知道很多物流公司的叉车司机是计件的,有些甚至工资也是计件的,当时选型的时候,这个车可能是一个错误的选型。
为什么呢?
因为货柜车跟卸货平台有一个高度差,会高出来一点。
所以,当我们用卸货车进货柜的时候,里面的那些都能够放,但是作为最边上那一板的时候,电动卸货车是放不了,如果存在这个高度差。
所个,造成很多叉车司机不愿意用这个车,因为他们觉得用的以后,会影响他们的工作效率和奖金,因为他们是计件的。
所以,这样就造成长期的浪费在这里。
当我们选型的时候,我们要考虑所有的作业和因素在里面。
这个也跟刚才一样,门架总共有6个车型,门架高度有9种,也存在不能通用的结果,造成车型越来越多,越来越浪费。
我们来看一行叉车的车龄,平均是4.9的车龄。
第一个车库1至3年的有10台,4至6年的有7台,7至9年的有2台,9年以上的有10台。
第二个仓库的平均车龄是3.8年,前面就不一一讲到了,我们可以看到超过9年的车龄有1台。
那么,操作的实际效率跟这个有什么关系呢?
第二个仓库的平均作业效率会比第一个仓库高,是33%。
所以,第一个仓库的作业效率只有21%,这个车龄影响很大,超过9年的坏车率、停机率会比较高,会影响整体的车龄效率。
通过前面车型看到的一些现象,做了一个方案的分析,首先我们会建议为了提高叉车实际的使用效率,我们首先要把一些刚才讲的基本上不用的电动托盘车去掉,因为放在那里要不停地维护,不停地充电,包括电池的维护,而且也占用地方。
所以这些都是库内的浪费。
所以我们建议把两台车去掉,再加上一台长期待修的车,所以我们建议把这3台车去掉。
第一个仓库我们建议把2台车去掉,然后把长期待修、待用的车去掉或处理掉。
至少处理掉的话,还有一个折旧的价值在里面,如果不处理的话,一直放在那里,我们会永远要人工去维护它。
第二个,我们认为它是一个型号的标准化,我们刚才看到6种车型、7种车型都达到7、9种门架的高度,这样造成叉车不能通用,所以我们的叉车会越来越多,但是怎么买都不够用。
所以,我们建议车型一定要统一,门架的配置标准化。
像我们刚才看到那么多车型,我们会建议它只保留3种车型,一种是电平的。
电平的我们统一一种,它有几台内援机,我们保留得援机。
电动托盘车这么多年都没有用过,所以基本上都不用了。
还有车龄太老就要更换新车,这样有效降低维护费用,也可以提高叉车有效使用率。
实际上车龄比较老的车占得越多,使用效率越低,叉车的维护费用也会越高。
按照日本的习惯,5年以后叉车会更新。
中国比较实际,中国觉得还能用的就用一用,但是超过9年的车,我们建议要更换掉。
再从另外一个数据来看,这个数据是我们在美国做的一个案例的数据,但是如果要降低多少维护费的话,就要更多数据的支持。
这个是国内案例的数据。
差不多同样的车型,我们把老车型换成新的车以后,能降低9%的维护费。
如果有一对车很好管理技术的话,可以降低18%的维护费,还有一个调整作业,避免高峰期的作业,可以降低22%的维护费。
前面我们也了解到物流企业,为什么有这么多车呢?
因为很多五列企业是集中在晚上出货的。
所以我们建议客户适当态度一下你的作业时间。
因为晚上集中出货的话,你要有很多的平衡中车同时作业,这样不但车辆很多,而且作业人员也很多。
我们建议它把部分的作业提升到白天来做。
白天我们仓库都有一个区,白天用前移式车把一部分货物下架,放在建成区。
现在我们有仓库初始方案的建议,就是你的那个占成区要有多大。
现在很多物流企业在建设时一味追求库存量,但是我们要整体优化,通常也讲过提高库存量或降低库存量是最早。
从现在开始,我们要整体优化,如果现在存在集中作业的话,我们可以把它分成白天和晚上比较均衡的作业,这能够降低我们叉车频繁的作业和人工的成本。
前面我们是从车辆配置去分析,我们从那几天在工厂里面随便走过随意拍的照片,我们看了一下,其中我们讲到的很多浪费在里面,但是由于紧急的时间,我们就没有去做具体的数据分析,我们会发现其实这些管理都是很完善的,但是我们在现场的时候,我们会看到很多东西,包括我们看到的这些作业,存在一些不安全的因素,会造成一些工商的成本,这些都是隐性的。
还有货物会凸出一大块,这个是叉车的通道,不小心撞到的时候,会有倒塌等潜在危险在里面。
我们建议用这样一些节选车进行一些作业,或者加一个安全笼,我想这个大家都很熟悉。
我们看到这几台车都是现场拍的,这3台叉车全部堆在一起去,这样一旦发生碰撞以后,就会造成工伤成本、维修成本、误工成本。
其实这些都是成本,换一个说法,这些都是一些浪费。
这个是仓库的管理牌,进入仓库请戴安全帽,库内限速45公里/小时。
我们去了4天,从来没有看见叉车的司机戴安全帽,这样就容易造成一些工伤成本。
还有一个非常快的,这是我们拍的,这个数绝对超过5公里,库内的超速我们由谁来负责呢?
这都有一些工商成本、维修成本、营运成本在里面。
我们来看一下4S里面的整理、整顿这方面,我们看这么多的物流中心,这些托盘都很零乱,这里肯定摆不了一板货,现在地价很贵,还这么浪费,这样就增长了管理成本。
还有重复作业的管理成本在里面。
这是一个通廊式货架,叉车直接从这里进去。
通廊式货架进行作业,通常是由上自下放置货物,但是我们看到中间掏空的。
也就是当我们要取里面这板货的时候,我们要把这2层的货先取出来的。
当我们放进去的时候,我们也要把上面的货取出来。
所以,这里面有很多重复作业在里面。
包括这边都是现场的照片。
这里写着楼下严禁堆放货物,但是还是堆了很多货物在里面。
这2条线堆到这里来了。
我们来看这里写着停车位,这里就放着托盘、叉车我也不知道放在哪里。
这是一排叉车刚刚从这里开走,我差点在这里摔了一跤,所以把它拍了下来。
这个是叉车留下的油污,叉车多已经漏油的,但是它还在仓库里面用。
这些最表面能看到的东西都在这里,所以这里存在很多隐性的管理成本在里面。
从刚才讲,我们会有几个建议的方案,减少叉车的数量,老车换新车,车型和门架标准化,调整作业时间,规范和加强安全管理,我们可以看到上面公司管理规定是非常完善的,当然下面执行的时候,细节化的时候,没有真正落实到位的时候,我们就会有很多隐性成本的浪费。
减少叉车的数量,可以降低人工成本。
现在人工成本在不断增加,如果10台车10台车,如果有7台车的话,那你至少了7个司机。
老是换新车主要是提高我们作业效率,降低我们的维护成本。
车型和门架的标准化,也是要提高叉车的有效使用率,降低人工成本,降低维护成本,减少叉车的购置成本。
调整作业时间,我们避免高峰期的集中作业,可以有效减少叉车的数量,这样降低我们的购置成本。
规范和加强安全管理,降低了人工成本,降低管理成本和事故成本。
大家可以看一下实际叉车使用效率,这个是大型公司的叉车使用情况。
这是一个非常标准的,就是一个叉车,一个配置。
在这种情况下,我们也帮它找出了其中的一点小问题。
它平均使用率是48%,这是一个管理非常完善的大型公司。
我们通过这个表格我们发给物流总监看,我说只要稍稍调整一下,我们看到两个车的使用效率太高,当时中有3台车使用效率非常低,只有10%多。
通过我们帮它分析以后,我们会发现这3台车在固定的2个生产线上。
所以,我们建议他们把这几台车一个月调整一下,把这几台高和低的做一个互换就OK了。
所以我们做了一个表格,这样就作为公司内部的管理,现在他们每个都会做。
所以,我们会发现这几台车的使用效率都比较高,我们都会做定期的保养和维修,这几台车经常换油风比较高,这台车可能会很少用。
这样就降低了这几台车使用效率高的维修成本。
我们来看一个反向的案例,刚才我们都建议叉车要减少可以降低我们的成本,但是我们有另外一个案例,我们会通过我们增加了合适的搬运设备来降低我们的成本。
这个公司是2005年以前用车的状况,基本上都是平衡重叉车、前移式车等,总共有40多台。
但是从2005年到现在以后,我们不停地做了一些建议以后,它就增加了很多的车型。
以前别人说什么车,我们就卖什么车,但是现在都建议到现场去实际分析到底适合用什么样的车型,比如平衡式叉车会分成适合的车型,会用一些电动牵引车、电动托盘车,我们可以通过这个帮助公司降低成本。
这是这个公司的现状,它们基本上是以人力作业为主,这是一个非常大型的纺织集团,但是我们看到它几年以来纺织作业都是用手拉的,包括折价。
这样你就发现几个问题,人力搬运是原来工厂搬运最主要的方式,堆放也比较乱。
我们规划了三个方向,我们这几年一直在做三个事情,就是把不同的工序,不同的地方,一些人工搬运改换机械搬运,也推荐一些更合适的搬运工。
碰到要进行一些有序的规划,就像前面讲到的2S的管理。
我们通过一些很详细的数据来告诉它,在购之前我们会现场测试的数据,手动托盘车、电动托盘车以后,能省多少人工,总共的费用能省多少。
我们建议以后,其中一个部门买了4台电动托盘车以后,一年就减少了40个搬运工,一年减少的成本是120万。
我们会推荐它一些牵引车,包括这些大车,我们经过很长时间是帮他们怎么样去改良,怎么去拉这些手推车。
这样有一个详细的数据,就是人工搬运会有几万的手推车。
建议它用电动牵引车以后,一个小部门1600个推车的周转量,它有上万的车,5年下来一个总成本就能省掉100多万,包括我们会有很多车型会推荐给它。
这是我们做的一个大概表格,这是通过我们帮它在改变适合的车型以后,它整个购置成本从2005年至现在就节省了200多万。
更重要的是我们会不停地帮它把工厂的搬运进行规划和有序的堆放,所以会减少它们一些重复,比如刚才说的零乱的对方和重复的浪费。
包括像这些原来是这样摆放,我们会建议它这样有序摆放。
这样大的一个企业,我们是怎么样让它相信我们提供的这种,包括前面的物流企业,这些无序的浪费来缩减呢?
我们怎么样说服他,这些是很大的浪费。
刚才植田总经理也讲到,其实我们就是在不停地减少浪费。
因为之前没有一个很详细的数据说明,我想给大家做一个小小的测试,了解一下2S的重要性,就是进行一些有序的整理、整顿。
我这里准备了一个小游戏,等一下我们会有一些数据,其实它就是模拟仓库的管理,货物的堆放,我们会计时30秒钟,我们去找这些货物的摆放位置。
我们从1开始找,一定要先找到1、再找到2,再找到3,我们一定要按照这个顺序,我们实际感受一下操作工很零乱的情况下,一共要浪费多少时间找这些东西。
1、我想问一下能找到20的有吗?
没有。
2、找到15个有多少个?
1个。
3、能找到12个多少呢?
3个。
4、能找到10个肯定很多是吗?
对。
现在我们会进行一个初步的管理,我们的货物会进行一个排列再去找,不要那么零乱的时候,我们再找一下。
1、有找到20的吗?
5个。
2、能找到15的有多少?
十多个以上。
所以可以看出我们的时间减少了很多,减少了很多的浪费。
我们再来看一下一个比较标准的程序,进行一个有序的程序以后,我们看看能够减少多少的浪费。
我们接下来进行一个有序的测试。
我们之前讲到的几个大公司,包括刚才讲的那个纺织企业是丰田几十年的大客户,它以前是用丰田纺织的机械开始的。
所以,他们工厂一直零乱的东西,我们通过不停的建议,但是以前我们没有找到很好的方法去说明和告诉他,这些浪费会造成多少成本在里面,包括人工等各方面。
所以我们通过一个小测试,包括人工测试等小游戏的时候,真的很震撼。
因为我们没有很多数据来管理,我们这种2S管理到底能够节能多少人工,但是通过这3个小测试,我相信大家会很清晰。
所以,在这里我非常感谢大家。
因为时间关系,我们只能大概看一下。
如果你们需要叉车设备方面的一些提案,我们也会到现场帮大家看一下,找出一些具体的问题在哪里,我们希望切实帮大家降低一些成本,让大家获取更多的利润,做一些实实在在的事情。
非常感谢大家,谢谢!