表面工程期末大作业.docx
《表面工程期末大作业.docx》由会员分享,可在线阅读,更多相关《表面工程期末大作业.docx(11页珍藏版)》请在冰豆网上搜索。
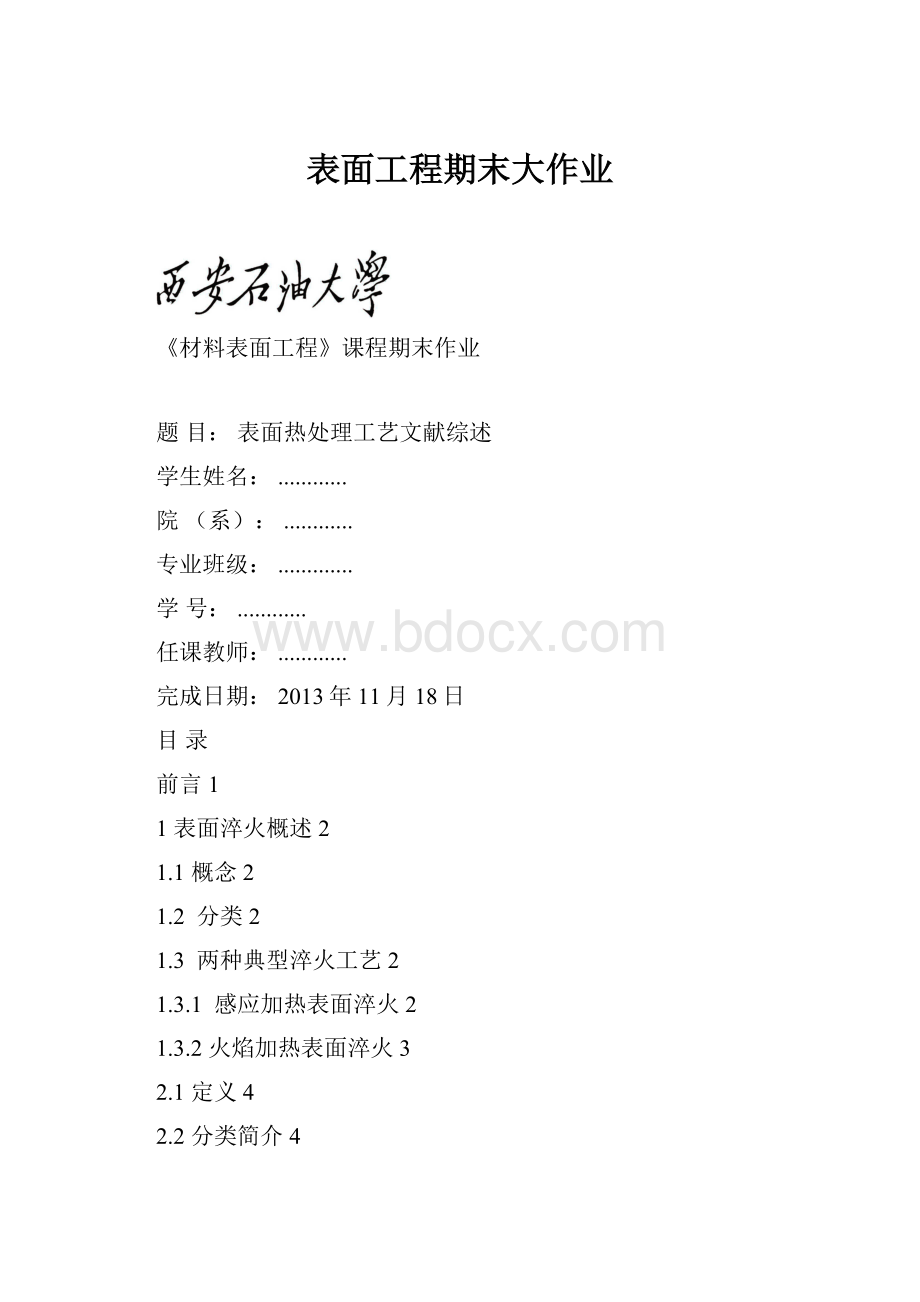
表面工程期末大作业
《材料表面工程》课程期末作业
题目:
表面热处理工艺文献综述
学生姓名:
............
院(系):
............
专业班级:
.............
学号:
............
任课教师:
............
完成日期:
2013年11月18日
目录
前言1
1表面淬火概述2
1.1概念2
1.2分类2
1.3两种典型淬火工艺2
1.3.1感应加热表面淬火2
1.3.2火焰加热表面淬火3
2.1定义4
2.2分类简介4
2.3工艺过程5
3国内外发展现状及发展趋势6
3.1大力发展多参数热处理和复合热处理工艺6
3.1.1多参数热处理6
3.1.2复合热处理7
3.2采用新的加热源和加热方式7
3.2.1新的加热源7
3.2.2新的加热方式7
3.3采用新的淬火介质和改进淬火方法8
3.4 研制开发各种新型热处理设备8
3.5 重视热处理节能和环境保护8
3.6 热处理生产的自动化和专业化9
参考文献10
前言
许多机械零件,如各种齿轮、凸轮,机床导轨等,是在弯曲、扭转等交变载荷、冲击载荷及摩擦条件下工作的,其表面承受着更高的应力,同时又不断地被磨损,因此要求表面具有高的强度、硬度、耐磨性和疲劳强度;而心部为了能承受冲击载荷,要求保持足够的塑形和韧性。
为了达到表强内韧的要求。
可对零件进行表面热处理,既先选用一定成分的零件,在保证满足心部的力学性能的前提下,然后用表面热处理的方法来强化零件的表面层。
表面热处理是指仅对零部件表层加热、冷却,改变表层组织和性能而不改变成分的一种工艺【1】,是最基本、应用最广泛的材料表面改性技术之一。
当工件表面层快速加热时,工件截面上的温度分布是不均匀的,工件表层温度高且由表及里逐渐降低。
如果表面的温度超过相变点以上达到奥氏体状态时,随后的快冷可获得马氏体组织,而心部仍保留原组织状态,从而得到硬化的表面层,即通过表面层的相变达到强化工件表面的目的。
常见的表面热处理有表面淬火和化学热处理。
1表面淬火概述
1.1概念
表面淬火是一种不改变零件的表面化学成分,只改变表层组织的局部热处理。
它通过对零件表面的快速加热,使其很快达到淬火温度,在热量尚未充分传至心部时立即进行淬火。
这时零件表面获得了硬而耐磨的马氏体组织,而心部仍为原来塑形、韧性较好的退火、正火、调质等状态的组织。
【1】
1.2分类
根据加热方法的不同,表面淬火可分为:
(1)感应表面淬火;
(2)火焰表面淬火;(3)电接触表面淬火;(4)激光加热表面淬火等。
1.3两种典型淬火工艺
以下主要介绍生产中应用较广泛感应加热表面淬火和火焰表面淬火。
1.3.1感应加热表面淬火
1.3.1.1分类及适用范围
根据选用电流频率的不同,感应加热表面淬火常有以下几种:
(1)高频感应加热表面淬火。
常用频率为200~300,淬硬层深度一般为1~2mm,主要用于中小莫属齿轮、小型轴等表面淬火。
(2)中频感应加热表面淬火。
常用频率为2500~8000,淬硬层深度一般为2~10mm,主要用于要求淬硬层较深的零件,如较大直径的轴类和较大模数的齿轮的表面淬火。
(3)工频感应加热表面淬火。
所用频率50Hz为工业电频率,其淬硬层深度一般为10~20mm,主要用于要求淬硬层深的大直径零件,如轧辊的表面淬火。
1.3.1.2基本原理及工艺过程
将一个线圈通以交变电流,在线圈周围便会产生交变磁场。
若再将一导体(零件)置于该交变磁场中,则导体中将会产生感应电流。
感应电流的频率域线圈中电流的频率相同。
由于零件本身又阻抗,当有电流通过时便会发出热量,因而感应加热时,零件时依靠在其自身中通过的感应电流(或称涡流)产生热量而被加热的。
但导体中通过交变电流会产生“极肤”效应,时截面上电流的分布不均匀,即表层的电流密度大,而心部的电流密度小,并且这种不均匀程度随电流频率的增加而增加。
【2】
1.3.1.3主要特点
由于感应表面淬火加热速度快,时间短,因此与普通淬火相比有以下特点:
(1)加热速度快,零件变形小;
(2)生产率高;
(3)淬火后表面能获得优良的机械性能;
(4)淬透层易控制;
(5)淬火操作易实现机械化。
但是由于感应淬火加热设备较贵,而且属于单件生产,形状复杂零件的感应器不易制造,因此限制了它的使用范围。
1.3.2火焰加热表面淬火
火焰加热表面淬火是指将乙炔-氧或煤气-氧的混合气体燃烧的火焰喷射到工件表面,使表面快速加热至奥氏体区,立即喷水冷却是表面淬硬的工艺。
淬硬层深度一般为2~6mm,此法简便,无需特殊设备,适用于单间或小批量生产的各种零件,如轧钢机齿轮、轧辊,矿山机械的齿轮、轴,机床导轨和齿轮等。
缺点是要求工熟练操作,否则加热不均匀,质量不稳定。
2化学热处理概述
2.1定义
化学热处理是将零件放置在某种化学介质中加热、保温、冷却,使介质中某些原子渗入零件表层。
从而改变表层的化学成分、组织和性能的热处理工艺。
与其他热处理相比,化学热处理不仅改变了金属的组织,还改变了表面层的化学成分。
【3】
2.2分类简介
(1)化学热处理的分类可采取三种方法(如表2-1所示):
表2-1化学热处理的类别
根据深入元素分类
渗入非金属元素
单元渗:
C、N、B、O、S、Si等
多元渗:
C+N、O+N、O+C+N
渗入金属元素
单元渗:
Al、Cr、Ti、V、Nb、Zn等
多元渗:
Al+Si、Al+Cr、Al+V、Al+Cr+Si
根据渗入元素对工件
表面性能的作用分类
提高渗层强度及耐磨性(如渗碳、氮、硼、铌、钒等)
提高抗氧化、耐高温性能(如渗铝、渗铬)
提高抗咬合、抗摩擦性能(如渗氮、渗硫、磷化等)
提高抗腐蚀性能(如渗氮、渗硅、渗锌等)
根据介质的物理
状态分类
固体法
液体法
气体法
(2)基本概念
1)渗碳:
向材料表面渗入碳原子的过程。
零件渗碳后经淬火、回火处理可提高零件表面的硬度、耐磨性和疲劳强度,而心部具有高的韧性。
渗碳主要用作齿轮、活塞销等零件。
2)渗氮:
向材料表面渗入氮原子的过程。
零件渗氮的目的是提高其表面的硬度、耐磨性、耐蚀性及疲劳强度。
零件经渗氮后不需再进行其它热处理。
由于渗氮温度低,处理前后的零件变形小。
3)合金化:
即零件表面渗入铬、铝等金属元素的方法。
同渗碳相比,深金属一般需要高的温度和更长的保温时间,渗层厚度也远比渗碳层薄的多,因为渗入金属原子在金属中进行的是置换扩散,需要更大的激活能。
化学热处理原则上可应用于一切金属材料,而化学介质又无限多样,它在改善材料性能方面存在巨大地潜在可能性。
但在有色金属材料中,化学热处理应用较少。
2.3工艺过程
任何一种化学热处理的过程都是由分解、吸收和扩散三个基本过程组成的。
(1)分解。
在一定温度下,化学介质的化合物分解出能够渗入零件表面的活性原子。
所谓活性原子,是指那些通过化学反应析出的化学性能活泼的原子。
(2)吸收。
活性原子在零件表面被吸收并溶解形成固溶体,当超过溶解度时便形成化合物。
吸收是活性原子由表面进入到铁的晶格的过程。
(3)扩散。
扩散是溶入的原子向零件内部迁移的过程。
由于表层原子的的浓度高,内部浓度低,引起渗入原子由表层向内部的定向扩散,从而获得一定厚度的扩散层。
3国内外发展现状及发展趋势
热处理是机械工业的一项重要基础技术,通常像轴、轴承、齿轮、连杆等重要的机械零件和工模具都是要经过热处理的,而且,只要选材合适,热处理得当,就能使机械零件和工模具的使用寿命成倍、甚至十几倍的提高,实现“搞好热处理,零件一顶几”的目标,收到事半功倍的效果。
热处理对于充分发挥金属材料的性能潜力,提高产品的内在质量,节约材料,减少能耗,延长产品的使用寿命
及提高经济效益都具有重大意义。
近几年国内外热处理技术主要发展在以下几个方面:
3.1大力发展多参数热处理和复合热处理工艺
传统的热处理,就主要控制的参数而言,多为常压下的温度、时间两个参数的热处理;就工艺方式而言,多为单一的热处理。
这样热处理的效果也只能是单一化。
为此,要大力发展多参数热处理和复合热处理工艺。
【4】
3.1.1多参数热处理
(1)真空热处理:
这是一种附加压力的多参数热处理。
它具有无氧化、无脱碳、工件表面光亮、变形小、无污染、节能、自动化程度高、适用范围广等优点,是近年来发展最快的热处理新技术之一,特别是在进行材料表面改性方面获得了很大的进展,许多新近开发的先进热处理技术,如真空高压气淬、真空化学热处理等,也需在真空下方能实施。
采用真空热处理技术可使结构材料、工模具的质量和使用寿命得到大幅度的提高,尤其适合于一些精密零件的热处理。
在工业发达国家,真空热处理的比例已达到20%左右,而我国目前约有真空热处理炉1200台,占热处理炉总数的1%左右,与国外的差距很大。
预计今后随着热处理行业的技术进步和对热处理工件质量要求的越来越高,真空热处理将会有较大的发展。
(2)化学热处理:
这是一种附加成分的多参数热处理。
普通化学热处理,如渗碳、碳氮共渗、碳氮硼共渗等,分别属于附加单成分、双成分和三成分的多参数热处理。
近年来,又发展了许多利用新技术的新型化学热处理,如真空化学热处理,流态床化学热处理、离子渗金属、离子注入、激光表面合金化等,均可提高工件的耐磨损及耐腐蚀等使用性能。
稀土在化学热处理中的应用(即与稀土共渗),能显著提高渗速,缩短处理周期,并可提高渗层的耐磨性和耐腐蚀性,这是我国的一大特色。
此外,固溶化学热处理也是一个值得注意的动向,内蒙农机研究所黄建洪等人开发了含氮马氏体化处理(N・M处理)工艺,这是第一个以获得固溶N的含氮马氏体为目的的渗氮工艺,已成功地应用于剪毛机刀片生产。
(3)形变热处理:
这是一种附加应力的多参数热处理。
采用压力加工和热处理相结合的工艺,把形变强化和相变强化结合起来,使材料达到成型与复合强化的双重目的。
形变热处理能提高材料的综合力学性能,并可以简化工序,利用余热,节约能源及材料消耗,经济效益显著。
形变热处理的应用广泛,从结构钢、轴承钢到高速钢都适用。
目前工业上应用最多的是锻造余热淬火和控制轧制。
美国采用控制轧制来生产高硬度装甲钢板,可提高抗弹性能。
我国兵器工业系统开展了火炮、炮弹零件热模锻余热淬火、炮管旋转精锻形变热处理、枪弹钢芯斜轧余热淬火等试验研究,取得了很好的效果。
3.1.2复合热处理
复合热处理是将两种或两种以上的热处理工艺复合,或将热处理与其它加工工艺复合,这样就能得到参与组合的几种工艺的综合效果,使工件获得优良的性能,并节约能源,降低成本,提高生产效率。
如渗氮与高频淬火的复合、淬火与渗硫的复合、渗硼与粉末冶金烧结工艺的复合等。
前述的锻造余热淬火和控制轧制也属于复合热处理,它们分别是锻造与热处理的复合、轧制与热处理的复合。
还有一些新的复合表面处理技术,如激光加热与化学气相沉积(CVD)、离子注入与物理气相沉积(PVD)、物理化学气相沉积(PCVD)等,均具有显著的表面改性效果,在国内外的应用也日益增多。
3.2采用新的加热源和加热方式
3.2.1新的加热源
在新的加热源中,以高能率热源最为引人注目。
高能率热源主要有激光束、电子束、等离子体电弧等。
高能率热处理就是利用高能率热源定向地对工件表面施加非常高的能量密度(103~108w/cm2),从而获得很快的加热速度(甚至能达到1011℃/s),这样在极短的时间内(1~10-7S),将工件欲处理区的表层加热到相变温度以上或熔融状态,使之发生物理和化学变化,然后依靠工件自身冷却实现表面硬化或凝固,达到表面改性的目的。
高能率热处理在减小工件变形、获得特殊组织性能和表面状态方面具有很大的优越性,可以提高工件表面的耐磨性、耐蚀性,延长其使用寿命。
高能率热处理近年来发展很快,是金属材料表面改性技术最活跃的领域之一,其中激光热处理和离子注入表面改性技术在国外已进入生产阶段。
3.2.2新的加热方式
在热处理时实现少无氧化加热,是减少金属氧化损耗、保证工件表面质量的必备条件,而采用真空和可控气氛则是实现少无氧化加热的主要途径。
在表面加热方面,感应加热具有加热速度快、工件表面氧化脱碳少、变形小、节能、公害小、生产率高、易实现机械化和自动化等优点,是一种经济节能的表面加热手段,主要用于工件的表面加热淬火。
高能率加热具有加热速度快、表面质量好、变形小、能耗低、无污染等优点,也是一种极为有效的表面加热方式。
在整体加热方面,有真空加热、高压加热、流态床加热等方式。
流态床加热虽然能量密度不高,但加热快且均匀、工件变形小、表面光洁、处理后不需清洗、工艺转换容易、能提高产品质量、节能、公害小、成本低、并可以与化学热处理相结合,是一种很好的加热方式,特别适宜于多品种、小批量和周期性生产,可用来取代传统的盐浴热处理,其发展前景令人瞩目。
3.3采用新的淬火介质和改进淬火方法
为了使工件实现理想的冷却,获得最佳的淬火效果,除根据工件所用的材料、技术要求、服役条件等,来合理选用淬火介质外,还需不断改进现有的淬火方法,并采用新的淬火方法。
如采用高压气冷淬火法、强烈淬火法、流态床冷却淬火法、水空气混合剂冷却法、沸腾水淬火法、热油淬火法、深冷处理法等,均能改善淬火介质的冷却性能,使工件冷却均匀,获得很好的淬硬效果,有效地减少工件的变形和开裂。
3.4 研制开发各种新型热处理设备
热处理设备是实现热处理工艺的基础和保证,直接关系到热处理技术水平的高低和工件质量的好坏。
我国热处理设备的生产已有40年历史,现已具备一定的规模和能力。
最初是仿苏四、五十年代的在空气中加热的电阻炉,并以箱式炉和井式炉为主。
七十年代对主要炉种进行了整顿,品种规格有所增加,性能有所改进,系列化程度有所提高。
八十年代又进行了一次产品更新换代,发展了第二代节能系列产品,能生产多用炉、真空炉、离子渗氮炉、流态粒子炉等新型炉种【5】。
自改革开放以来,通过引进国外先进的热处理设备和中外合资合作生产,使我国热处理设备的设计制造水平和生产能力有了很大的提高。
我国现有电炉厂180多家,已形成年制造热处理炉9000台的能力。
3.5 重视热处理节能和环境保护
主要的两大举措:
(1)大幅度降低热处理的能耗;
(2)高度重视热处理生产的环境保护
热处理生产对环境造成的污染很大,包括排出的废气、废水、废液、废渣、粉尘、噪声、电磁辐射等,且随着生产的发展,其危害也日益严重。
研究和采用无污染、无公害的热处理技术,并对排放的有害物质进行有效控制和综合治理,是消除热处理污染的主要措施。
1989年联合国环境署决定在全世界推行清洁生产技术。
所谓清洁生产技术,就是通过对生产过程和产品的综合防治,减少废弃物产生,最大限度地保护自然环境和利用自然资源,即选取清洁的原料,采用清洁的工艺,实现清洁的生产过程,制造出清洁的产品。
日本东京金属技术研究所金武典夫博士通过分析引起全球性的温室效应、空气污染、酸雨等对环境造成的影响,提出了一种“节能-高效-环保型热处理”的综合体系,它包括了预处理、热处理、后处理、技术保证体系和环境管理体系,而其关键是将高新技术应用于热处理生产中。
我国已把环境保护作为一项基本国策,并从1992年开始推进清洁生产技术。
根据清洁生产技术的要求,我国现阶段热处理生产的主要控制目标应是少无污染、少无氧化和节能,并应把真空热处理和可控气氛热处理作为热处理行业“九五”期间重点推广应用的清洁生产技术【6】。
3.6 热处理生产的自动化和专业化
(1)自动化:
电子计算机在热处理中的应用,包括计算机辅助设计(CAD)、计算机辅助生产(CAM)、计算机辅助选材(CAMS)、热处理事务办公自动化(OA)、热处理数据库和专家系统等,它为热处理工艺的优化设计、工艺过程的自动控制、质量检测与统计分析等,提供了先进的工具和手段。
机器人在热处理中的应用,可以有效地改善工人的劳动条件,提高产品质量和劳动生产率。
目前主要是用来进行自动装卸料。
由于热处理的生产环境差、劳动强度较大,也由于热处理生产向自动化、集成化、柔性化的方向发展,因此,今后机器人在热处理生产中的应用将日趋增多。
【7】
(2)专业化:
专业化生产是现代工业的基本特征之一,也是促进热处理行业技术进步的一种重要手段。
目前工业发达国家的热处理专业化程度已达到80%以上,而且工业越是发达的国家,其专业化水平也越高,而我国只有20%左右。
即使这些为数不多的热处理专业厂,也由于组织管理不善,设备利用率较低,新技术、新工艺采用不多,热处理标准贯彻执行不够,能耗较高,产品质量较差。
因此,今后要有目的、有重点地扶持一批有条件的热处理厂和车间,使其成为热处理专业厂和协作点。
对热处理专业厂要进一步加强管理,积极采用新技术、新工艺、新设备,严格按照标准化、规范化组织生产,形成技术、经济和服务上的优势,充分发挥专业化生产的优越性。
此外,热处理工艺材料,如各种淬火介质、渗剂、保护涂料、清洗剂、加热盐、保护气氛和可控气氛的气源等,也要固定生产单位,进行专业化生产,不断提高质量和扩大品种,并尽可能实现规格化、标准化、系列化。
参考文献
[1]工程材料与热加工技术/程晓宇主编.西安电子科技大学出版社,2006.2
[2]钢的热处理/胡光立,谢希文编著-4版-西安:
西北工业大学出版社,2012.7
[3]金属热处理及质量检验/马爱斌编著.-南京:
东南大学出版社,2001,10
[4]熊剑主编.国外热处理新技术.北京,冶金工业出版社,1990:
6~27
[5]BellT,etal.HeatTreatment1973:
39
[6]李 键.清洁生产与热处理.第五届全国青年热处理会议论文集.国外金属热处理,1996,17(增刊):
1~3
[7] 乔 健,张永安,刘 迨.我国热处理设备的改造与发展远景,中国机械工程学会三十五周年年会论文集,1986:
160