碳纳米管对玻璃纤维复合材料高周疲劳寿命的延长.docx
《碳纳米管对玻璃纤维复合材料高周疲劳寿命的延长.docx》由会员分享,可在线阅读,更多相关《碳纳米管对玻璃纤维复合材料高周疲劳寿命的延长.docx(17页珍藏版)》请在冰豆网上搜索。
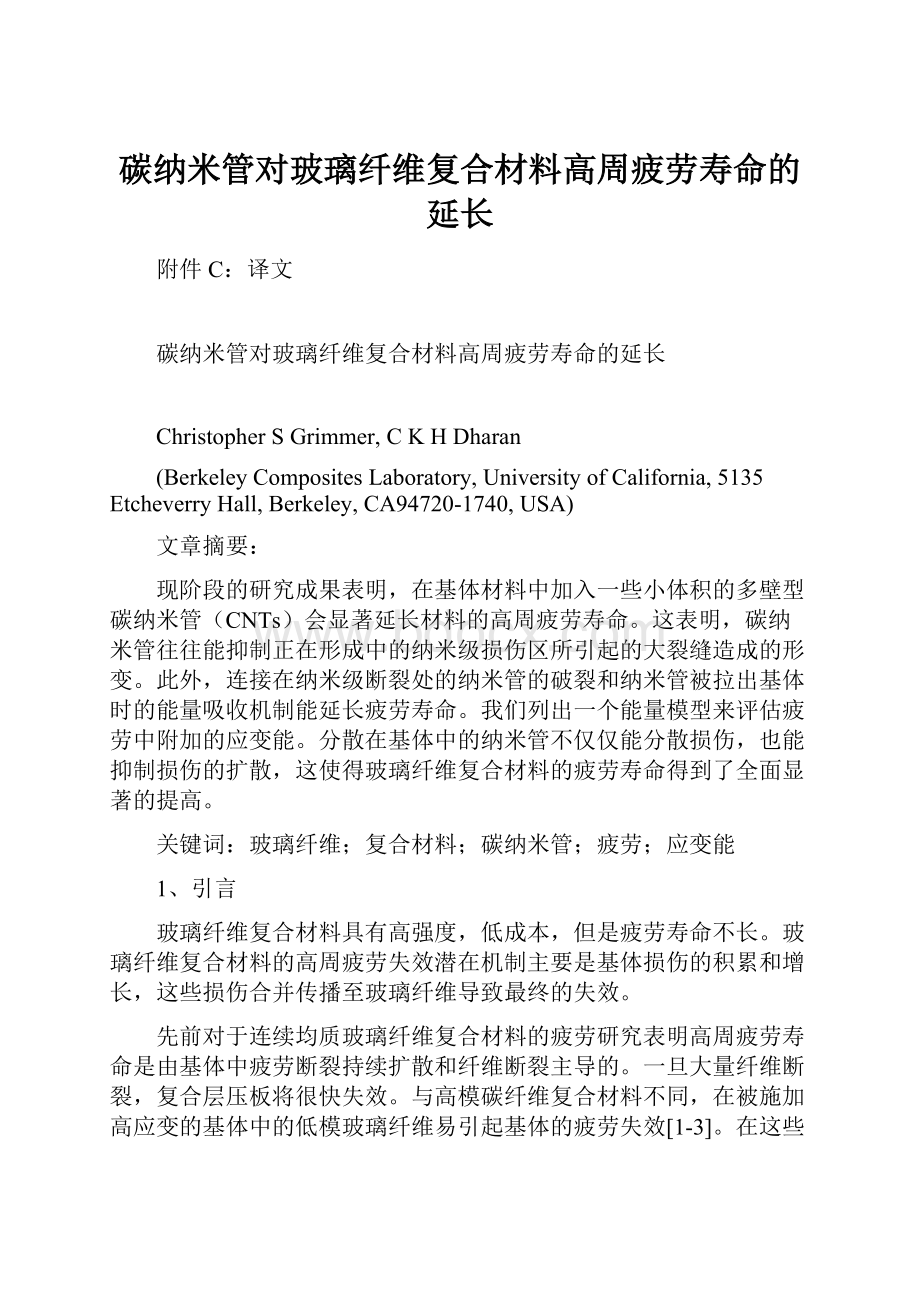
碳纳米管对玻璃纤维复合材料高周疲劳寿命的延长
附件C:
译文
碳纳米管对玻璃纤维复合材料高周疲劳寿命的延长
ChristopherSGrimmer,CKHDharan
(BerkeleyCompositesLaboratory,UniversityofCalifornia,5135EtcheverryHall,Berkeley,CA94720-1740,USA)
文章摘要:
现阶段的研究成果表明,在基体材料中加入一些小体积的多壁型碳纳米管(CNTs)会显著延长材料的高周疲劳寿命。
这表明,碳纳米管往往能抑制正在形成中的纳米级损伤区所引起的大裂缝造成的形变。
此外,连接在纳米级断裂处的纳米管的破裂和纳米管被拉出基体时的能量吸收机制能延长疲劳寿命。
我们列出一个能量模型来评估疲劳中附加的应变能。
分散在基体中的纳米管不仅仅能分散损伤,也能抑制损伤的扩散,这使得玻璃纤维复合材料的疲劳寿命得到了全面显著的提高。
关键词:
玻璃纤维;复合材料;碳纳米管;疲劳;应变能
1、引言
玻璃纤维复合材料具有高强度,低成本,但是疲劳寿命不长。
玻璃纤维复合材料的高周疲劳失效潜在机制主要是基体损伤的积累和增长,这些损伤合并传播至玻璃纤维导致最终的失效。
先前对于连续均质玻璃纤维复合材料的疲劳研究表明高周疲劳寿命是由基体中疲劳断裂持续扩散和纤维断裂主导的。
一旦大量纤维断裂,复合层压板将很快失效。
与高模碳纤维复合材料不同,在被施加高应变的基体中的低模玻璃纤维易引起基体的疲劳失效[1-3]。
在这些研究中,失效被定义为一个工作循环次数,当达到这个循环次数时刚度达到规定的损失。
近期失效理论的评论会被列在参考文献中[4]。
刚度的降低作为复合材料的损伤指标,已经被广泛研究的理论和实践所采纳。
然而,裂纹扩展和由此产生的刚度降低只是复合材料损伤的一个综合指标。
损伤可以在微观水平裂纹的萌生和微裂纹发生聚并前产生。
其他的研究都集中在测量复合材料中裂纹扩散引起的断裂能量,特别是在一种被称为层间断裂的常见的失效模型中[5]。
这些研究表明,一个单一的在复合材料基体或者在基体和纤维界面处的扩散的裂纹,将会伴随低能量级的断裂能的吸收。
在典型的复合材料层合板设计中,板材将被设计成能承受循环条件下的结构载荷,碳纤维复合材料和玻璃纤维复合材料相比,承受的负载循环时失效的情况会少一些。
对于碳纤维复合材料有较少的失效率的解释是:
高模量的碳纤维使得基体上的受到相对较低水准的循环应变。
在基体上临界基体疲劳应变的相应复合应力被定义为复合材料的疲劳失效的临界参数[2]。
在玻璃纤维复合材料中,在基体上许用循环应变要超过纯树脂材料相应的疲劳应变,然而一些高模复合材料,如,碳纤维复合材料,基体的许用循环应变要比这个临界值低。
因此,碳纤维复合材料不常在循环作业中出现性能降低的情况,被公认为具有良好的疲劳强度。
这解释了最近的研究中导向绳状纳米管增强环氧树脂复合材料具有高模量的原因[6]。
其他一些碳纳米管对于聚合物基体断裂影响的研究中表明,添加少量(0.1wt%~0.2wt%)的碳纳米管使聚合物的断裂韧性增加40%。
微观形貌观察显示,位于基体的高密度纳米级断裂是由基体断裂韧性的改善引起的。
在这项工作中,碳纳米管在静态和循环荷载作用进行了研究,提出了一个观察到的行为机制作用下结构复合材料的寿命的影响。
在传统的复合材料层合板的损伤机制,包括形成在基体微裂纹的启动和循环荷载作用下的传播,最终导致纤维失效和断裂的复合。
碳纳米管的加入可降低损伤机制的大小导致在吸收应变能通过大量的细小纳米尺度裂缝的产生增加几个数量级的规模。
此外,纤维桥接在纳米尺度的增加能量吸收通过纳米管在断裂过程中的参与。
这个效果应该提高了复合材料的损伤容限和使它更耐循环荷载作用下的损伤增长。
一种基于能量的模型被提出,试图描述碳纳米管/玻璃纤维混杂复合材料的疲劳行为。
我们已经将热固性树脂(环氧树脂)含有均匀分布的纳米纤维聚合物(CNTs)为常规的玻璃纤维聚合物复合材料。
我们最近的研究已经确定,这些树脂具有相对均匀的纤维分布在聚合物与小团聚合物[8]。
含有碳纳米管的复合系统,静态和循环荷载下,通过扫描电子显微镜显示相应的断裂表面失效模式表明,这里提出的失效机理研究。
2、实验过程
2.1材料准备
环氧树脂和固化剂分别为826和Epikure3234,都产自Hexion化工集团有限公司(Houston,Texas,USA)。
混入1wt%多壁碳纳米管的EPON826树脂由Nanoledge公司(clapiers,France)提供。
1wt%目前碳纳米管负载水平被选定为足以改变复合材料的力学行为的指标[7,9],同时不会由于聚合物的粘度增加降低可塑性[10]。
7500型,0.28毫米厚平纹织玻璃纤维由Hexcel公司(Fullerton,CAUSA)提供。
2.2样品制备
CNT和非碳纳米管[0/90]纤维增强复合材料是由湿铺在平板热压机生产,以0.56的纤维体积分数在80℃和580kPa一小时进行固化。
对齐24×200毫米拉伸试样切取固化片。
以直径6.4毫米的中心孔钻在每个试样的损伤定位。
铝片粘结到试样的端部,以方便夹紧。
标本在测试前25℃的室温下熟化处理。
2.3试验方法
样品进行失效测试时使用MTS(EdenPrairie,Minnesota,USA)100kN伺服液压试验机加装由INSTRON(Norwood,MAUSA)labtronic8400控制器数字控制可变流量液压供应。
使用美国国家仪器公司(Austin,TXUSA)LabVIEWV7命令控制器进行数据采集。
在疲劳试验之前,可以获取两种碳纳米管和非碳纳米管复合试样的拉伸强度。
这两种材料在应力比(R)0.15时进行拉-拉疲劳应力峰值在70,60,45和加载其百分之30的恒力。
加载频率为3Hz来消除样品预热。
选取具有代表性的失效标本并将其断口进行切除并使用BALTEC(Balzers,Liechtenstein)Med020涂布机溅射涂覆一层2.5nm的铂。
采用日立(东京,日本)S-5000冷场发射扫描电镜,以加速电压10kV进行样品成像。
3、结果和讨论
3.1拉伸试验
图1表明单调拉伸试验中纯树脂混合碳纳米管以及不混合碳纳米管时应力-应变曲线的对比。
但是观察到其对弹性模量的影响不显著。
然而,与未改性树脂相比,高含CNT树脂样品与相应的极限拉伸强度的最大的失效应变值稍低。
对于含有碳纳米管的纯树脂,这些变化会在材料的机械行为中导致韧性增加,或提供断裂能量。
图2和图3显示了扫描电子显微镜(SEMs)下两种材料的断裂表面。
含碳纳米管的树脂材料有一个粗糙的断裂面,这与上面讨论的断裂能增加表现一致。
图1
图2
图3
图4显示了含碳纳米管的纯树脂恒力拉伸断口表面。
在树脂中的碳纳米管均匀分布的普遍存在,同时观察表明一些随机分布的碳纳米管群(见图4)也是存在的,这些聚集的碳纳米管簇是有害的强度以及疲劳寿命的[11]。
图4
图5显示了混合碳纳米管复合材料呈现出的纳米管从基体中拉拔而出的断裂表面(图中的小孔和大凸管)。
在显微镜看到的小的突起部分可能表明纳米管与基质一同裂缝。
单孔(白色箭头所指)是一个纳米管从该表面拉出所留下的。
正是这一过程的纳米管和纳米管断裂有助于提高混合碳纳米管的复合材料抗断裂性能以及显著提高疲劳寿命(见下文)。
图5
3.2疲劳试验
添加和不添加1wt%碳纳米管的玻璃纤维环氧树脂复合材料的疲劳寿命数据(每点三个样本)如图6所示。
对于含有碳纳米管的样品,观察到在每个样品加载至失效情况下荷载循环次数显着增加。
所观察到的延长后寿命一般在大于104次的循环后。
在这个高周循环下,多大的负载周期中会产生裂纹成核和微裂纹的生长[1,2]。
表1比较了混合碳纳米管和不含碳纳米管的玻璃纤维复合材料的疲劳寿命。
延长疲劳寿命的碳纳米管加入量减少了循环应力的作用,使效果最明显在循环高周期。
在循环应力为44MPa,加入1wt%碳纳米管的复合材料结果几乎增加了3倍的疲劳寿命。
在含有碳纳米管的复合材料中,碳纳米管的存在导致大量开始成核的裂纹生长点。
此外,对于给定的应变能,大密度的纳米级裂纹增长将比不含碳纳米管复合材料微裂纹的密度较低,而且增长速度更慢。
结果是在裂纹在生长和聚结期,高周疲劳寿命所需循坏周期数增加。
此外,纳米级裂纹桥接的碳纳米管会在被拉出表面的过程中增加纤维断裂参与度,并提高裂纹扩展所需的断裂能,进一步延迟失效。
3.2.1断裂表面分析
含有碳纳米管的玻璃纤维复合材料试样的断裂表面高分辨率电子显微照片如图7所示。
这两个照片都是从相同的位置拍摄的;右边的照片是碳纳米管簇,与之相对的,左侧图片是断裂的玻璃纤维。
在复合材料中被拉拔出的碳纳米管的断裂类似于在纯树脂混合碳纳米管断裂表面观察到的机制(图5)。
此外,图7显示碳纳米管具有穿透玻璃纤维间的能力,进一步验证了碳纳米管是适当分散在聚合物之中[12]。
图6
图7
表1加入碳纳米管(CNTs)对玻璃纤维复合材料疲劳寿命的比较
循环应力幅值/ MPa
玻璃纤维复合材料的疲劳寿命/周期
CNTs/玻璃纤维复合材料的疲劳寿命/周期
寿命改善系数
98.0
1473
2091
1.4
85.0
3238
3813
1.2
65.0
11488
18517
1.6
44.0
109055
316227
2.9
3.3微分能量模型
断裂表面的电子显微镜研究表明,从机械的角度来分析断面,传统的玻璃纤维复合材料和碳纳米管/玻璃纤维混杂复合材料的断裂行为的主要差异是破碎的纳米管分布和从断裂面内的混合环氧树脂基体中拔出碳纳米管。
这些均匀分布混杂在复合材料纳米尺度的断裂过程,吸收应变能并阻碍基体微裂纹生长使得疲劳寿命增长。
在该模型中,碳纳米管个体被假定为在环氧树脂基体中均匀分布、随机取向的三个维度。
这种假设有利于建立微米尺度的统计代表性体积单元。
碳纳米管和周围的环氧树脂基体由专门的范德瓦尔斯力[13-15]作为连接纽带。
由于碳纳米管较低的热膨胀系数(CTE)与聚合物基体的热膨胀系数不匹配[16],需要在升高的温度下施加径向压缩预应力对碳纳米管进行室温固化。
这就产生一个摩擦剪应力,τP会抑制管被拉拔出表面。
碳纳米管与基体之间一定程度的互锁可能有助于τP[11]。
除非碳纳米管与断裂平面之间的夹角达到临界角φ时,会被认定为从基体拉出,否则会使得管断裂而不是被拉出。
将纳米管的力学行为由被拉出转变为断裂的角度,φC,与载荷循环下两个相对的断面分离速率有关。
图8将表示这一概念。
图8
3.3.1基体断裂能量关系
传统的对复合材料弹塑性基体的潜在能量的损失关系的描述是建立在传统复合材料和碳纳米管混合复合材料都使用的方法,即由Budiansky[17]提出的评估增强陶瓷断裂的方法。
在传统的复合材料中,这些损失是由于基体裂缝产生的。
同样,在混合复合材料中,这些损失也是由基体裂缝、碳纳米管和碳纳米管/基体界面拉拔过程中的摩擦滑动和碳纳米管的断裂造成的。
这两种情况下的能量关系的增加同水平增进,直到其材料到达对应的摩擦滑动和碳纳米管的断裂。
在推导式中,将对应传统复合材料的符号设为(X,Y),而对应混合复合材料的符号设为(
)。
图9中展示了这两种情况下三种状态的关系。
图9
状态(0)对应于一个不受任何外部负载自由体的体积V和表面ST,这个自由体也并没有位移或应变,但包含内应力σ0。
状态
(1)对应于相同的自由体,但被施加的牵引力T,并有应力σ1,产生位移U1,和相应的应变ε1。
在没有表面牵引力的情况下,状态
(2)发生了一些内部开裂导致表面SC产生裂纹,和新的应力分布σ2,位移U2,应变ε2。
同样地,对于混合复合材料基体,状态(
)对应于一个不受任何外部负载自由体,体积
和表面
T,没有位移和应变,内应力
。
状态(
)对应于相同的个体,但其被施加牵引力
,产生应力
1,位移
1和应变
1.在表面牵引力
没有改变下相应的状态(
),内部裂纹产生了新裂纹表面
,由于新的碳纳米管/基体界面的表面
上的拉拔产生了摩擦滑动,由于碳纳米管的断裂产生了新的碳纳米管表面
,和新的应力
2,位移
2和应变
2。
本构关系中在两种情况下的应变及应力的关系有:
对于传统的玻璃纤维复合材料有:
对于碳纳米管/玻璃纤维混合复合材料,其中
和
是两种情况下的弹性柔量。
对于传统复合材料,在三个状态分别的势能可以被描述为[17]:
以上式中的体积积分表示了弹性存储能,表面积分表示个体的表面收到牵引力的功。
其中的柔度是常量。
由于内部开裂而引起的势能变化是:
将对象在外部受到的牵引力T所做的功与位移U1-U2相应内部应力的虚功等值化处理,使得σ2超过应变M(σ1-σ2),我们将得到:
联立式
(1),(6)和(7)得到从状态
(1)到状态
(2)由于基体开裂造成的潜在量损失的一般形式:
在我们设定的情况下,由于纳米管的拔出和碳纳米管的断裂,在含滑动摩擦的弹性体和纤维断裂的情况下,潜在的能量损失与所推导的一样多,直到加入虚功的计算。
为了保证数据完整性,第二种情况的潜在能量方程将采用更精确的形式,以式(6)作为基础,但与原式相比更接近实际情况:
在混合基体中能量关系推导的差异是两个额外对应摩擦滑移和纤维断裂的内部虚拟工作条件造成的。
摩擦滑动条件可表示为:
式中,τP是剪应力,产生于碳纳米管的聚合物基体在拉拔过程中的滑动距离δ。
注意到摩擦剪切力意味着牵引总是会沿着滑动相反的方向进行的性质,我们可以移除点乘积,简化式(10):
纤维断裂内部虚功可表示为:
式中,ψ(L)是两个纳米管单位的管横截面之间的原子间作用力,L是两个面之间的距离,L0是碳-碳键的长度。
重写式(7),加入附加条件,并与式(11)和(12)联立,得到混合复合材料的新的虚功表示方式:
联立式
(2),(9)和(13)可得到由于基体开裂,摩擦滑动和纳米管断裂而造成的潜在能量损失的最终形式:
下一节将把这两式(8)和(14),在传统的玻璃纤维复合材料和碳纳米管/玻璃纤维混合复合材料中,以基于能够预测潜在的能量损失的变化的这两个模型做出直接的比较,从而得出在类似的条件下纤维混合复合材料的微分能量模型。
3.3.2能量关系的比较
在这一小节中,将对先前得到的两个潜在能量损失方程进行直接比较,或更具体地说,比较状态
(2)和状态(
)的潜在能量差。
虽然这两种模型,传统的复合材料情况下的式(8),和混合复合材料情况下式(14),都有一个相似点,但是他们表示两个不同的材料,因此,在之后的步骤进行之前采取直接比较是很有必要的。
这个必要的一步是要认识到,虽然这两种材料是不同的,但是宏观的弹性力学行为在此是等价的。
回到图2,我们可以看到,对应于各自的聚合物复合材料,加入碳纳米管或不加入碳纳米管的环氧试样的屈服强度和弹性模量的差异是很小的。
由于在碳纳米管/环氧树脂体系内应变失效的改变与这种由低应变聚合物作为基体的复合材料并不相关,鉴于材料对称性可得:
可知状态
(1)和状态(
)能量等效,即π1=
1,使外部牵引力
和
,以及内应力相等,并利用式(15),可以发现式(14)和(8)的差异如下:
式(16)表示在两个微元在达到损坏状态
(2)和(
)时所需要损失的潜在能量差。
更简单地说,式(16)右边所代表的应变能,是在混合复合材料的两个伤害吸收过程中,基体裂纹的形成过程中形成的。
正是这种吸收在不促进增长和基体微裂纹,使得混合复合材料能够在疲劳作业时聚结应变能的能力显著优于传统的复合材料。
4、结论
加入1wt%碳纳米管的玻璃纤维/环氧聚合物基的复合材料会显著改善其高周疲劳寿命。
在纯树脂的拉伸试验(不包括玻璃纤维)中,当加入碳纳米管后并没有影响样本的弹性模量。
然而,未改性树脂中更高的韧性会导致失效应变略微增加。
使用高分辨率的扫描电子显微镜观察纯树脂试样拉伸断裂后,发现在碳纳米管较多致使树脂改性的表面粗糙度较高。
对于复合材料试样在疲劳检测中的结果表明,碳纳米管被拉出树脂基体的断裂,造成能量吸收,可能是增加疲劳寿命的机制。
这包括在环氧树脂基体的疲劳裂纹萌生点,产生尽可能好的裂缝桥接的更大密度的碳纳米管。
这两种机制可以导致疲劳裂纹萌生过程中,当添加碳纳米管时,生成,聚集和传播裂纹的能量吸收显着增加,导致疲劳寿命显著增加。
基于能量的模型利用在聚合物基体中的均匀分布和碳纳米管的大量随机取向,以此作为建立均质材料性能假设,并以微米尺度的代表性体积单元反映其包含整个材料的机械行为的基础。
能量关系在这种同质化的碳纳米管/环氧树脂体系中平行展开,在纯环氧树脂基体内裂纹的形成和扩展上建立能量的差异,或差分能量的模型。
研究结果表明,在涉及高周疲劳应用时,为制造更高性能的玻璃纤维复合材料,在玻璃纤维复合材料加入小部分的碳纳米管可以使其疲劳寿命显著增加。
参考文献
[1]DharanCKH.FatigueFailureMechanismsinaUnidirectionallyReinforcedCompositeMaterial[M].ASTMSpec.Tech.Publ.,1975,569:
171
[2]DharanCKH.FatigueFailureinGraphiteFibreandGlassFibre-polymerComposites[J].J.Mater.Sci.,1975,10:
1655
[3]HahnHT,KimRY.FatigueBehaviorofCompositeLaminate[J].J.Compos.Mater.,1976,10:
156
[4]DegrieckJ,VanPaepegemW.FatigueDamageModelingofFibre-reinforcedCompositeMaterials:
Review[J].Appl.Mech.Rev.,2001,54(4):
279
[5]SaghizadehH,DharanCKH.DelaminationFractureToughnessofGraphiteandAramid-epoxyComposites[J].J.Eng.Mater.Tech.:
Trans.ASME,1986,108(4):
290
[6]RenY,LilF,ChengHM,etal.FatigueBehaviourofUnidirectionalSingle-walledCarbonNanotubeReinforcedEpoxyCompositeunderTensileLoad[J].Adv.Compos.Lett.,2003,12
(1):
19
[7]GanguliS,AglanH.EffectofLoadingandSurfaceModificationofMWCNTsontheFractureBehaviorofEpoxyNanocomposites[J].J.Reinforc.Plast.Compos.,2006,25
(2):
175
[8]GrimmerCS,DharanCKH.High-cycleFatigueofHybridCarbonNanotube/GlassFiber/PolymerComposites[J].J.Mater.Sci.,2008,43:
4487
[9]GojnyFH,WichmannMHG,FiedlerB,etal.InfluenceofNano-modificationontheMechanicalandElectricalPropertiesofConventionalFibre-reinforcedComposites[J].Compos.A,2005,36:
1525
[10]KimJA,SeongDG,KangTJ,etal.EffectsofSurfaceModificationonRheologicalandMechanicalPropertiesofCNT/EpoxyComposites[J].Carbon,2006,44:
1898
[11]WongM,ParamsothyM,XuXJ,etal.PhysicalInteractionsatCarbonNanotube-polymerInterface[J].Polym.,2003,44(25):
7757
[12]FanZ,HsiaoKT,AdvaniSG.ExperimentalInvestigationofDispersionduringFlowofMulti-walledCarbonNanotube/PolymerSuspensioninFibrousPorousMedia[J].Carbon,2004,42:
871
[13]SchadlerLS,GiannarisSC,AjayanPM.LoadTransferinCarbonNanotubeEpoxyComposites[J].Appl.Phys.Lett.,1998,73:
3842
[14]WagnerHD,LourieO,FeldmanY,etal.Stress-inducedFragmentationofMultiwallCarbonNanotubesinaPolymerMatrix[J].Appl.Phys.Lett.,1998,72:
188
[15]LordiV,YaoN.MolecularMechanicsofBindinginCarbon-nanotube-polymerComposites[J].J.Mater.Res.,2000,15:
2770
[16]JiangH,LiuB,HuangY,etal.ThermalExpansionofSingleWallCarbonNanotubes[J].J.Eng.Mater.Technol.,2004,126:
265
[17]BudianskyB,HutchinsonJW,EvansAG.MatrixFractureinFiber-reinforcedCeramics[J].J.Mech.Phys.Solids,1986,34:
167
译文出处:
ChristopherSGrimmer,CKHDharan.High-cycleFatigueLifeExtensionofGlassFiber/PolymerCompositeswithCarbonNanotubes[J].JournalofWuhanUniversityofTechnology(MaterialsScienceEdition),2009,02:
167-173.