硅单晶成长.docx
《硅单晶成长.docx》由会员分享,可在线阅读,更多相关《硅单晶成长.docx(25页珍藏版)》请在冰豆网上搜索。
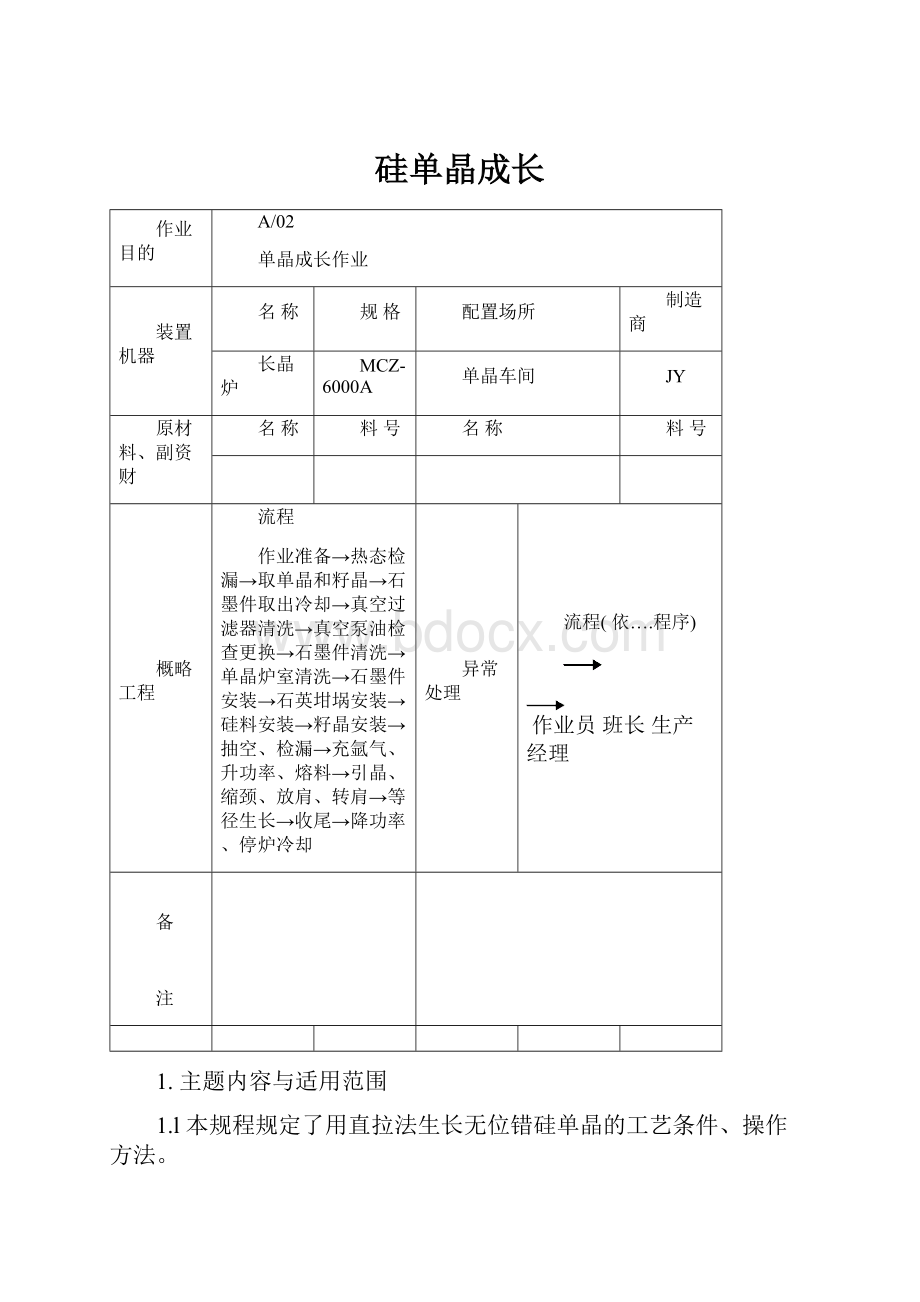
硅单晶成长
作业目的
A/02
单晶成长作业
装置机器
名称
规格
配置场所
制造商
长晶炉
MCZ-6000A
单晶车间
JY
原材料、副资财
名称
料号
名称
料号
概略工程
流程
作业准备→热态检漏→取单晶和籽晶→石墨件取出冷却→真空过滤器清洗→真空泵油检查更换→石墨件清洗→单晶炉室清洗→石墨件安装→石英坩埚安装→硅料安装→籽晶安装→抽空、检漏→充氩气、升功率、熔料→引晶、缩颈、放肩、转肩→等径生长→收尾→降功率、停炉冷却
异常处理
流程(依….程序)
作业员班长生产经理
备
注
1.主题内容与适用范围
1.l本规程规定了用直拉法生长无位错硅单晶的工艺条件、操作方法。
1.2本规程适用于MCZ-6000A单晶炉生长Φ158mm硅单晶。
2.实施
若无技术部门的变动文件,任何人不得违背本规程。
3.引用文件
4.述语(略)
5.人员
操作本设备的人员必须经过三个月以上严格培训,经考核合格,持有上岗证后方可独立操作。
6.安全防范措施
6.l进入工作区必须穿好工作服、鞋、戴好工作帽。
6.2拿取炉内热的单晶或部件必须戴好绝热手套。
6.3开炉前必须检查设备电机的完好情况,发现问题应立即向设备主管报告。
6.4未经安全教育的人员或非本岗位人员禁止操作本设备。
6.5禁止往电气设备上冲水。
6.6禁止用湿手操作本设备。
7.器材
7.1工具
25mm、30turn活络扳手、一字螺丝刀、十字螺丝刀、手电筒、钢丝钳剪刀、手推车、毛刷、真空吸尘管、钢丝刷、500mm游标卡尺、拿石墨托身专用工具、内六角一套、天平、摄子、测径仪。
7.2材料
分析醇酒精、分析纯丙酮、丝光毛巾、砂皮、掺杂剂、钢丝、定性滤纸、清洁塑料袋、一次性卫生手套、石墨器件、石英器材、多晶硅、碳毡、碳箔。
8.设备
8.1MCZ-6000A单晶炉
8.2配套主室真空泵
8.3配套副室真空泵
9.操作开关与控制(见附录1)
10.设施要求
10.l炉子电源
10.1.l加热功率:
最大值150kw
IO.1.2加热电压:
0-6OV
IO.1.3加热电流:
最大值2500A
10.2循环冷却水
10.2.1温度:
20-30℃
10.2.3冷却进水口压力:
0.15Mpa-0.4Mpa
10.3压缩空气压力:
0.5Mpa~0.9Mpa
1O.4氩气进口处绝对压力:
最大值0.4Mpa
11.操作工艺流程
作业准备→热态检漏→取单晶和籽晶→石墨件取出冷却→真空过滤器清洗→真空泵油检查更换→石墨件清洗→单晶炉室清洗→石墨件安装→石英坩埚安装→硅料安装→籽晶安装→抽空、检漏→充氩气、升功率、熔料→引晶、缩颈、放肩、转肩→等径生长→收尾→降功率、停炉冷却
12.操作内容
12.1作业准备
1)进入单晶车间须穿戴好洁净工作服、鞋。
2)开炉前,按工艺要求检查水、电、气,确认无误后方能开炉。
3)准备好一次性洁净手套、耐高温手套、毛巾、纸巾、研磨布、酒精、吸尘刷、吸尘管、防尘口罩。
4)准备好钳子、扳手和各类装拆炉专用工具。
5)取单晶的架子、装石墨件的不锈钢小车、装埚底料的不锈钢筒和装硅料的不锈钢小车,并处理干净。
6)用毛巾将炉体从上到下一遍,擦洗时注意不要将所有控制接线及开关碰断或碰坏,并把炉子周围清扫干净。
12.2热态检漏
7)检查上一炉功率关闭时间,在单晶冷却4.5~5.0小时后,关闭氩气开始抽高真空,并作时间记录。
8)待炉内压力到达极限(要求达到2Pa以下)后,先关闭主室球阀而后关闭真空泵电源进行检漏,并作相应时间记录,若0.5小时内抽不到2Pa以下时,交有关维修人员处理,在此期间须配合有关维修人员进行装拆炉,并作相关记录。
9)检漏要求5分钟,漏气率<0.6Pa/min为正常,同时作好漏气率记录,若漏气率>0.6Pa/min时,交有关维修人员处理,在此期间须配合有关维修人员进行装拆炉,并作相关记录。
12.3取单晶和籽晶
10)热态检漏后,充氩气至常压,关闭氩气。
11)提升单晶至付室,从付室窗口内确认单晶升至所需高度,若无异常,盖住翻板阀,打开液压泵,升起付室。
12)把安全接盘移到炉筒口处,缓慢转动付室至侧面。
13)把取单晶的架子放在付室炉筒正下方,准备接单晶。
14)稳定单晶,移开安全接盘,按下籽晶快降,将单晶降入架子内。
15)确认单晶完全入架子内后,按住籽晶,用钳子将籽晶从细径处钳断,钳断籽晶后,应稳定重锤,防止重锤快速转动,损坏钢丝绳。
16)将籽晶从重锤上取下,放在指定场所,再将重锤升至付室内适当位置。
17)将单晶移到中转区,及时、准确的将单晶编号写在单晶上,待自然冷却后送至检查部门进行检测入库。
12.4石墨件取出冷却
18)石墨小件取出
a)打开液压泵电源,按炉盖升按钮上升炉盖。
炉盖上升到位后,再旋转炉盖到侧面。
b)戴好耐高温手套按顺序取出导流筒及保温盖放在装石墨件的不锈钢小车上,注意要拿稳并轻放。
c)戴好耐高温手套用钳子夹住石英坩埚的上端部分提起,使其松动,将石英坩埚取出。
若石英坩埚能将埚底料全部带出直接放入不锈钢盘;若不能则将先取出石英坩埚,剩下的埚底料随三瓣埚一并取出后,再将埚底料放入不锈钢盘内。
若出现闷炉等意外情况则用钳子像装料一样一块块取出,直至彻底取出。
最后将不锈钢盘移到指定地方,自然冷却。
冷却后对埚底料进行重量检测并作好记录。
d)戴好耐高温手套依次取出三瓣埚、埚底放在装石墨件的不锈钢小车上,放上后要注意放稳当。
e)用埚杆板手从埚杆中央孔的位置拧下不锈钢螺丝,取出埚杆板手,再将埚杆连不锈钢螺丝放在不锈钢小车上,注意堆放稳当。
f)取出的石墨件一并放在不锈钢车上,自然冷却。
19)石墨大件的取出(一般5炉做一次,须作好大清记录)
a)取出上保温罩放在不锈钢小车上。
b)取下炉筒侧面欧抗,将其及对应的密封及玻璃放到适当的位置以放损坏丢失。
c)打开油泵开关,按住炉筒升按纽,升起炉筒至限位,旋转炉筒,并降至适当位置。
d)取出中保温罩放在不锈钢小车上。
e)先取下加热器螺丝盖,再用专用工具取下加热器螺丝后,取下加热器螺丝和加热器放在不锈钢小车上。
f)依次取出电极护套、电极石英环、埚杆护套、炉底压片、石墨碳毡、排气套管、下保温罩、炉底碳毡、石墨电极等放在不锈钢小车上自然冷却。
12.5真空过滤器清洗
20)准备好吸尘刷、吸尘管、酒精、丝光毛巾、扳手,带好手套、防尘口罩。
21)用扳手打开真空过滤器盖螺丝,取出过滤网。
22)用吸尘刷仔细清洗过滤网及过滤器内的挥发物。
23)将清洗后的过滤网缓慢放进过滤器内。
24)用吸尘刷清洗过滤器盖,用沾酒精的丝光毛巾擦净密封圈,并检查密封圈是否完全就位,防止出现脱落或出槽影响抽空。
25)盖好过滤器盖并用扳手上好过滤器盖螺丝。
12.6真空泵油检查更换
26)确认关闭主泵球阀和真空泵,在放油单晶炉上挂检修牌,将废油桶置于真空泵放油口下方,打开上下腔放油开关,放完油后关闭上下腔放油阀,废油倒入指定油桶。
27)清洗真空泵(每5炉清洗一次),用扳手打开真空泵侧盖,置于适当位置,用毛巾彻底清理真空泵腔、侧盖和下腔滤油网的油污,清洗完毕后,安装好滤网,安装好侧盖。
侧盖在打开、安装时小心操作,防止损坏侧盖及油封而漏油。
泵腔内禁止遗留纸屑或其它异物,不然会造成油路的堵塞导致真空泵卡死。
清理真空泵的废弃物放入指定垃圾桶。
28)打开真空泵注油口,将真空泵油注入真空泵注油孔,观察真空泵油位至油位观察窗1/2位置,停止注油,打开泵侧的油路管道阀门向下腔放油,关闭油口。
29)启动真空泵工作5min后关闭泵侧的油路管道阀门,察看油位是否处于油位观察窗1/3----1/2位置,关闭真空泵,在放油单晶炉上移去检修牌。
若低于下限重复28)、29)操作。
12.7石墨件清洗
30)石墨件清洗
a)准备好清洗用品(吸尘刷、丝光毛巾、吸尘管、砂纸、菜瓜布等)戴好手套、口罩。
清洗好清洗台及周围环境。
b)依次用吸尘刷清洗各类石墨件直至确认无污物,沟槽及接口等吸附挥发物较多的部位要用砂纸认真打磨后再吸尘清洗。
c)清洗时注意检查各石墨件是否有损坏及粘硅,有损坏及粘硅要及时更换和处理。
d)操作时要轻拿轻放以免造成石墨件的损坏。
e)清理完毕的石墨件放到事先准备好的洁净不锈钢小车上。
禁止叠加,移动不锈钢小车要稳当。
f)清洗后垃圾放入垃圾指定处,清洗好清洗台及周围环境。
31)石墨大件炉内清洗(适用于每炉小清,石墨大件未取出时在炉内清洗)。
a)用吸尘刷吸净炉筒、保温罩和加热器上沿拆炉时掉落的残渣。
b)用吸尘刷仔细用力清洗保温罩,加热器所能触及到的部位。
c)取出加热器螺丝盖,检查电极螺丝是否松动、胶落或粘硅。
有松动须拧紧,有胶落或粘硅须更换。
再盖好加热器螺丝盖。
d)如果在拆炉时不小心引起热场移动或转动一定要检查热场是否对称,测温孔要重新校正。
如果侧温孔有偏离会影响测光信号,导致欧陆表数值过小,无法对炉内温度进行自动控制无法成晶。
e)用吸尘刷吸净炉底上压片、炉底波纹管、排气孔内的附尘及残渣。
f)用沾有酒精的丝光毛巾清理炉壁上部。
12.8单晶炉室清洗
32)付室的清洗安装
a)准备好清洗棒、丝光毛巾、酒精。
b)在清洗棒上缠上沾有酒精的丝光毛巾,清洗付室内部至上部,直至确认无污物。
c)快速降下籽晶夹头,用沾有酒精的丝光毛巾认真擦洗重锤及钼夹头。
需要时要将重锤摘下用研磨布认真打磨,并清洗干净。
摘下重锤时要慎重作业,防止钢丝绳上弹造成钢丝绳出槽。
清洗钢丝绳时要检查其接头部位是否老化或损坏,若有应截去一截钢丝绳,防止在拉晶过程中单晶掉下。
清洗好上升重锤到一定位置,升重锤时,不要使重锤晃动,防止重锤挂住付室下沿,拉断钢丝绳。
33)炉盖清洗
a)先用丝光毛巾擦洗内壁(氧化物过多先用吸尘刷清理)。
b)小孔部位、观察窗部位、伊尔根部位、阀口部位等各处的接口及焊接口等不易清洗的部位要用沾有酒精的丝光毛巾认真擦洗,直至确认无污物。
c)硅粉强力附着时或炉盖局部发黑、发白时要用研磨布认真研磨直至炉盖整个内壁出现光亮无污物。
d)观察窗、伊尔根窗口要认真清理,同时把所有小孔的位置清理干净。
34)炉筒清洗
a)先用沾有酒精的丝光毛巾擦洗内壁(氧化物过多先用吸尘刷清理)。
b)取光孔部位要用沾有酒精的丝光毛巾认真擦洗,直至确认无污染。
c)硅粉强力附着时或炉筒局部发黑、发白时要用研磨布认真研磨直至炉筒整个内壁出现光亮无污物。
35)抽气管道清洗。
a)用扳手打开抽气管道上的封盖螺丝,取下封盖和密封圈。
b)用一头缠钢丝球的长棒伸入管道抽动,另一头用吸尘刷吸除抽气管道内的挥发物。
c)用沾有酒精的丝光毛巾认真擦洗封盖和密封圈,再安装好。
12.9石墨件安装
36)清洗后的石墨大件安装(一般5炉做一次)。
a)依次装好石墨电极、炉底碳毡、下保温罩,两侧排气管、炉底压片、埚杆护套、电极护套、石英电极环。
安装电极时检查接触面是否平整,上下接触面要放一层石墨纸,防止热场打火。
b)将清洗后的加热器装好,拧上石墨螺丝,要拧紧,不然要引起热场打火,并盖上石墨螺丝盖。
c)将清洗后的中保温罩装好,卡口接到位。
并校正与加热器的间距,要均匀一致,否则需调整好。
d)炉筒复位,打开液压泵,升起炉筒至上限,用沾有酒精的纸巾擦洗下炉筒上部的结合部和炉筒下部的结合部,同时转动炉筒到适当位置。
e)按炉筒降,炉筒降到位后,校对测温孔,防止测光信号过小无法温度自控。
f)安装偶抗,将其及对应的密封及玻璃按原次序装好。
g)将清洗后的上保温罩装好,并卡口接到位。
37)清洗后石墨小件安装。
a)用专用工具装好埚杆。
一定要拧紧埚杆螺丝,防止因松动造成液面晃动
b)依次装好埚底、三瓣埚。
安装时要确认埚杆、埚底、三瓣埚是否吻合,要认真、细心,防止碰坏保温材料或加热器。
c)装好后要打开埚转旋转一下,以检验三瓣埚与加热器间距上否一致。
若不一致,需及时调整。
12.10石英坩埚安装
38)炉筒、炉盖的外侧及周遍,用沾有酒精的丝光毛巾擦洗平干净,炉体周围地面认真打扫。
39)带好防尘口罩、装料用的洁净手套,取出石英坩埚。
40)检查石英坩埚包装上标识与配料单上否一致,打开石英坩埚包装,对光确认有无裂纹、污物、气泡。
若有异常及时处理并报告班长或车间经理。
41)在炉内的石墨三瓣埚内装好石英坩埚,注意四周间隙一致。
42)在操作记录上记好所用石英坩埚的生产厂家,同时把石英坩埚标签贴入操作记录的背面。
12.11硅料安装
43)取来装料不锈钢车和硅料,仔细核对配料单的各项内容是否与单晶炉号、配料实物一致,若有异常及时处理并报告班长或部门经理。
44)更换装料用的手套,如有母合金先放入石英坩埚。
再将碎料、小料平铺在埚底。
45)将大块料放置中央,用中型料放于大料四周上方左右予以固定,间隙中放入小硅料。
装料时要慎重作业,轻拿轻放,防止碰撞石英坩埚,不要使料掉在保温罩的缝隙,以免造成打火。
46)装料时注意不要使料探出石英坩埚,否则会在熔料过程中引起硅液流下,损坏石墨件,甚至焖炉。
47)装料完成后打开埚转旋转一下,确认四周间隙一致,再快速将埚降至下限。
停止旋转。
48)埚上部、加热器上部、保温罩上部再用干净吸尘刷吸净浮尘及硅渣。
49)依次装好保温盖、导流筒。
安装保温罩、导流时要相互吻合,安装导流筒时要慎重作业,如果与硅料发生接触时要调整硅料的摆放,防止在化料过程中发生沾硅。
12.12籽晶安装
50)用沾有酒精的丝光毛巾擦洗炉盖和炉筒接合部的密封圈,再将炉盖旋转至炉筒上部。
51)打开液压泵电源,按炉盖降按钮降下炉盖。
炉盖降到位后确认炉盖是否合好,防止漏气。
52)用沾有酒精的丝光毛巾擦洗付室下部的接合部和炉盖上部的接合部,转动付室,降下与炉盖合炉。
要缓慢转动付室,防止重锤与付室内壁碰撞。
53)从指定的场所将腐蚀好的籽晶取来,用沾有酒精的纸巾认真擦洗籽晶。
注意不要直接用手接触籽晶,防止汗渍污染籽晶。
54)下降籽晶夹头到付室下面,把籽晶装在夹头上,装好钼销。
用力向下拉一下籽晶使其牢固,稳定好籽晶后按晶快升使其上升至适当位置。
55)用沾有酒精的丝光毛巾擦洗付室接合部的密封圈。
12.13抽空、检漏
56)打开真空泵电源。
57)缓慢打开主室球阀。
58)抽空后炉内压力达到<20Pa时,进行反复充氩气使炉内压力<2Pa。
59)待炉内压力<2Pa后,关闭主室球阀而后关闭真空泵电源之后进行测漏,要求炉子漏气速率<0.6Pa/min,检漏时间5分钟。
检漏合格进入加热熔料工序。
60)若炉子漏气速率>0.6Pa/min,则需重复56)、57)、58)、59)步进行抽空检漏,若仍不合格报告维修人员处理。
并进行相应记录。
12.14充氩气、升功率、熔料
61)抽空检漏合格后,再打开真空泵电源。
62)缓慢打开球阀。
63)打开氩气充气系统,调节付室氩气流量在20~30slpm,使炉内压力稳定在1000~1500Pa。
64)打开加热开关。
65)根据下表通过欧陆表分步增加功率。
每次加温均作相应记录。
对欧陆表的使用应小心操作,防止功率迅速增大,瞬时造成变压器负荷过大,或对整个加热回路造成瞬间电流过大而打火或损坏。
应严格按照加热顺序进行加热,否则可能会温度突然上升造成石英坩埚破裂、漏硅。
时间
功率
0min
50KW
30min
70KW
60min
<100KW
66)熔料过程中时刻注意观察炉内的情况,若无异常塌料后给定埚转2rpm,上升适当埚位。
升埚时注意不要使硅液面触到导流筒下沿。
升完埚后通过对埚位标尺的确认埚无动作,方可完成,否则会使导流筒粘硅,发生跳硅。
67)料熔完时,降低加热功率至引晶温度(与上炉对应)。
给定埚转到5~7rpm,并进行相应记录。
68)欧陆表值降至引晶温度对应的数值时切入温度自动,将埚升至引晶埚位稳定即导流筒至液面距离为15mm左右。
引晶埚位也可在上炉装料基础上根据投料量增加/减少量,来确定本次引晶埚位,具体可参照附录15.1引晶位置变化参考表。
并进行相应记录。
12.15引晶、缩颈、放肩、转肩
69)测电阻率取样
a)温度切入自动后,按籽晶快降,将籽晶降至从主观察窗刚能看到的位置,并打开晶转电源,给定晶转10~12rpm。
b)20分钟后,降籽晶使之与液面接触,通过欧陆表调整温度开始放肩。
c)将肩放至直径50~60mm提离液面上升到至付室,关闭翻板阀,打开主炉室氩气,调节流量到炉压和原来一致。
d)缓慢调节晶转为0rpm,关晶转
e)增大付室氩气流量。
等付炉室炉压表指示到0时,关闭氩气后升起付室。
并右转至极限位置,用钳子取出籽晶下放肩部位,取籽晶时要慎重作业,不可用手直接接触籽晶,防止烫伤。
等冷却后去测电阻率。
f)等籽晶冷却后用沾有酒精的丝光毛巾擦洗干净,然后装上籽晶,合闭付室。
70)付泵抽空作业
a)合闭好付室炉筒后打开付泵电源。
b)慢慢打开后面的付室抽气球阀,直至全开。
c)付室压力表抽至-0.05~-0.1Mpa时打开付室氩气阀,同时关闭付泵球阀。
d)付室压力表充至0~-0.05Mpa时关闭付室氩气阀,同时打开付泵球阀。
e)步骤c)和步骤d)反复操作三次.
f)最后根据压力表指针确认付室与主室气压达到一致,关闭付室球阀,然后关闭付泵电源。
g)缓慢打开挡板阀。
h)打开付室氩气阀至正常流量,关闭主室氩气阀。
71)补掺母合金
a)若电阻率测试结果在目标范围时,可进行下一步预热接触引晶;若有偏离,须补掺母合金,由班长根据电阻率测试结果和投料量计算出补掺母合金的类型和数量,并去取出称量,进行补掺,作好相应记录。
b)补掺过程同69)测电阻率取样一样,只是放肩放到100~150mm,尽量放平肩。
c)打开付炉室门后,不取下籽晶,而将已称量的母合金放在平肩上。
放母合金时要慎重作业,不可用手直接接触籽晶,防止烫伤。
d)再按70)付泵抽空作业后,适当调节熔硅温度,把籽晶和母合金降到液面中,使其熔化掺入。
e)再重复69)测电阻率取样,70)付泵抽空作业,71)补掺母合金,直到电阻率测试合格进入下一工序。
72)预热接触
a)电阻率合格后按籽晶快降,将籽晶降至从主观察窗刚能看到的位置,并打开晶转电源,给定晶转10~12rpm。
b)20分钟后,按籽晶快降按钮将籽晶降至距硅液面10mm处预热20分钟。
必须预热,不然会由于籽晶由低温区到高温区、由固定到液态转变时,温差太大造成籽晶产生位错。
c)籽晶快速上升或下降的位置必须给予确定,升降操作方可完成,否则会溶掉籽晶甚至重锤,升至上限时会导致重锤掉下进入溶硅内,造成漏硅或整炉料彻底报废,无法再次利用。
d)降籽晶使之与硅液面接触,浸润20分钟,熔去籽晶较细的部分,根据接触光圈的形状,确定引晶温度是否合适,若合适开始引晶;若不合适,通过欧陆表调整温度20分钟后开始引晶,温度不宜偏低。
73)引晶
a)打开晶升电源,计长归0。
作好相应记录。
b)缓慢提升拉速至1.5mm/min左右先提拉籽晶约10mm后,再提升拉速让拉速保持在1.5mm/min~6mm/min之间,引晶直径控制在3mm左右,长度不低于150mm。
c)引晶过程中若温度不适可适当进行温度的调整,但不宜过大。
引晶开始时,应先引10mm左右直径较粗的细颈,可作为下次接触使用,这样避免籽晶的浪费。
d)引晶过程中若籽晶熔断,则重新进行欧陆表温度的调整,籽晶插入液面,重新进行引晶。
作好相应记录。
74)放肩
a)引晶达到预定的长度后,缓慢降低拉速直至0.3~0.5mm/min进行放肩。
b)放肩时要时刻观察肩的形状,放肩过快过慢时应及时进行适当地温度调整。
c)放肩坏时,则重新进行温度的调整,插入液面,熔去放肩和引晶部位,再引晶。
d)若料较脏时,将肩放至直径150~160mm提离液面上升到付室,打开主室氩气阀后合闭挡板阀。
e)增大付室氩气流量,到达常压后关闭付室氩气阀。
f)打开付室后,取出不成晶品放到适当位置待其冷却后做好标识放入指定场所。
75)转肩
a)将肩放到合适直径(6英寸单晶为150mm左右)时,将拉速缓慢提高2~4mm/min,进行转肩。
b)密切关注单晶的生长速度,调整拉速。
c)待单晶生长到目标直径时缓慢降低拉速同时适当给定埚跟随动。
埚跟随动设定可参照附录15.2埚跟比参考表。
d)转肩过后计长清零,观察单晶生长情况待其生长稳定后,调整伊尔根使其压单晶光圈1/3~1/2之间位置。
e)调整好拉速到1.2~1.3mm/min和直径信号为500左右时,将计算机切入自动控制拉晶状态。
f)一定要注意单晶生长稳定后方可切入自动,否则会造单晶生长失控。
12.16等径生长
76)正常等径控制
a)计算机切入自动控制后认真做好各项记录。
b)等径过程中应时常观察炉内单晶生长情况,每隔10分钟对炉内巡视1次,确认有无异常,每隔1小时对炉内晶体测量一次直径。
等径过程中每1个小时做1次拉晶记录。
c)根据情况的不同,等径至硅料液面下降到石英坩埚内径变小处时,应该适当增大埚升随动。
77)等径断棱时回熔
a)在200mm以内断棱时,进行回熔处理。
作好相应记录。
b)将欧陆表设置为OP值,晶转设定为5转,埚转为1转。
c)功率调整到熔料功率的90%。
d)观察炉内状态,慢慢下降晶体进行回熔,晶体过长需要熔化一段后,经确认经已熔化后,再慢慢下降一段晶体进行回熔,直到全部回熔。
.
e)回熔完成后重新开始引晶操作。
78)等径断棱时晶体收尾提出
a)晶体等径在200mm以上断棱时,且估计本次晶体提前收尾并提出后还能正常等径200mm或以上时应将单晶提前收尾并提出。
收尾过程见12.17收尾工序。
b)提前收尾要求收尾长度在80~100mm。
收尾长度计算是从实际晶体断棱处到收小后晶体提出处的距离。
c)收好尾后先下降坩埚液面30mm,缓慢调节晶转为5rpm,再给定拉速4.0mm/min上升1小时,作好相应记录。
而后上升到付室炉筒内挡板阀上,再等1小时后打开主室氩气流量,合闭挡板阀。
d)合闭挡板阀后,增大付室氩气流量,到达常压后关闭付室氩气升起付室炉筒并转到右侧面,取出断棱单晶。
作好相应记录。
e)对炉筒及小付室进行清洗。
f)进行二次作业,重新开始引晶操作。
79)等径断棱时晶体收尾停炉
a)晶体等径在200mm以上断棱时,且估计本次晶体提前收尾并提出后已不能再正常等径200mm时,可进行提前收尾停炉。
收尾过程见12.17收尾工序。
b)提前收尾要求收尾长度在80~100mm。
收尾长度计算是从实际晶体断棱处到收小后晶体提出处的距离。
c)收好后转入12.18降功率、停炉冷却工序。
12.17收尾
80)当晶体长度达到预定长度(根据埚内实际剩料多少计算,可参照附录15.3晶体收尾长度参考表)时,或断棱需要收尾时,退自控,缓慢停止埚升进行收尾。
并做好相应记录。
81)要经常查看收尾情况,对拉速和温度做适当调整。
82)正常收尾长度应为晶体等径直径的大