年产5万吨12淡色啤酒工厂工艺设计毕业论文最终.docx
《年产5万吨12淡色啤酒工厂工艺设计毕业论文最终.docx》由会员分享,可在线阅读,更多相关《年产5万吨12淡色啤酒工厂工艺设计毕业论文最终.docx(34页珍藏版)》请在冰豆网上搜索。
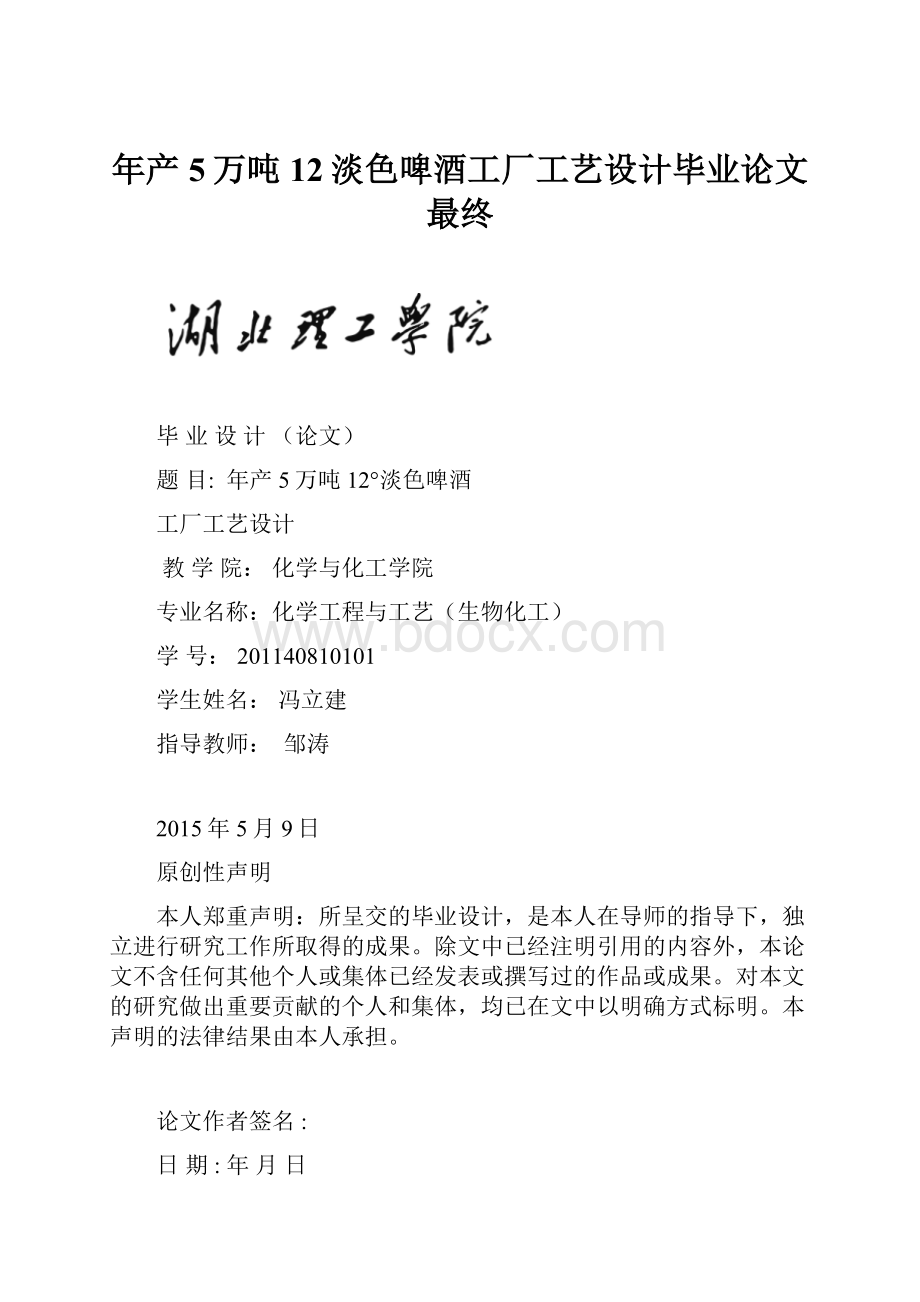
年产5万吨12淡色啤酒工厂工艺设计毕业论文最终
毕业设计(论文)
题目:
年产5万吨12°淡色啤酒
工厂工艺设计
教学院:
化学与化工学院
专业名称:
化学工程与工艺(生物化工)
学号:
201140810101
学生姓名:
冯立建
指导教师:
邹涛
2015年5月9日
原创性声明
本人郑重声明:
所呈交的毕业设计,是本人在导师的指导下,独立进行研究工作所取得的成果。
除文中已经注明引用的内容外,本论文不含任何其他个人或集体已经发表或撰写过的作品或成果。
对本文的研究做出重要贡献的个人和集体,均已在文中以明确方式标明。
本声明的法律结果由本人承担。
论文作者签名:
日期:
年月日
摘要
本设计是以生产苯丙乳液为主要目的的,简明的介绍了苯丙乳液的研究现状。
并且由各种合成工艺路线的综合评价以及分析比较之后,选取最为合理的生产工艺流程。
通过对每一批物料的进料量和反应热的相关计算,进而选取最佳的换热方式以及相关设备。
按照测得的物料粘度选取最佳的搅拌器,确定其搅拌功率,这样才能最终按照50000吨/年苯丙乳液的设计目的要求来设计出主要设备——聚合釜,与此同时能对其工艺来进行设计,绘制出最佳的工艺流程图。
关键词:
苯丙乳液;搅拌装置;聚合釜
ABSTRACT
Thispaperproductionstyrene-acryliclatexforthepurpose,expoundsthepresentsituationofthestudystyrene-acryliclatex,throughvarioussynthesisprocessroutecomprehensiveevaluation,theanalysisandcomparison,thechoiceofreasonableproductionprocess,determinetheeconomicandreasonableprocessflow.Calculatedeachbatchofmaterialfeedrate,reactionheat,tochooseasuitableheattransfermethodsandequipment.Accordingtothemeasurementofmaterialviscositychooseappropriatemixerandmixingpower,andintheendto40000tons/yearstyrene-acryliclatexdesignspecificationsofthemainequipment-polymerizationkettle,anditstechnologicalengineeringdesign,drawreasonableprocessflowdiagram.
Keyword:
Styrene-acrylicemulsion;theproductionprocess;stirringdevice;polymerizer.
第一章概述
1.1苯丙乳液
苯乙烯以及丙烯酸酯共聚物乳液涂料同时又被称作为苯-丙乳液涂料,是一种用苯乙烯改性的丙烯酸酯系共聚物乳液涂料,笨丙乳液是采用苯乙烯部分或者是全部代替纯丙乳液中的甲基丙烯酸甲酯。
因为是在共聚物中引入了一部分的苯乙烯链段,能有效的提高其作为涂膜的耐水性、耐碱性、硬度、抗污性以及抗粉化性。
苯丙乳液为乳白色液体,液体是带有蓝光。
固体含量是40~45%,粘度是80~1500mPa·s,单体残留量为0.5%,pH值一般在8~9左右。
苯丙乳液的附着力相当好,而且胶膜十分透明,耐水、耐油、耐热、耐老化性能都非常良好,不仅可以用来作为纸品胶粘剂,还可以与淀粉、聚乙烯醇、羧甲基纤维素钠等胶粘剂一起配合来使用。
此物一般贮存于5~30℃的库房内,贮存期一般不会超过1年。
该涂料的保光性、保色性、户外耐久性、抗污性不错,还有对填料粘结强度相当高;同时还可以用来配制高光泽乳液涂料;考虑到经济原因,其成本比纯丙乳液涂料低上不少。
这种涂料不仅仅能供水泥沙浆、灰泥沙浆、木材、混凝土底材的涂装,还能有效的配制沙浆喷涂漆和水泥系涂料,当然也可以大量地用来作为外墙的涂料。
这类涂料用途十分广泛,在乳液涂料总产量中占有一席之地,是一类非常具有发展前途的乳液涂料。
1.2苯丙乳液发展简介
乳化剂体系的研究进展主要是由50-60年代开始,在当时,人们研究比较多的是表面活性引发剂和表面活性链转移剂;苯丙乳液的研究热潮是出现在20世纪末和21世纪初,随着可聚合乳化剂的优异性能慢慢被人们所发现,研究也就越来越集中在可聚合乳化剂上面了。
极具有代表性的研究是由欧盟资助、GuyotA[3]等领导的由8个学术和5个工业实验室联合进行的系统性研究。
这些实验室系统性地研究了可以影响可聚合乳化剂应用性能的诸多影响因素,与此还探讨了怎么做才能使可聚合乳化剂达到他们所预期的最佳使用效果。
从那以后的系统研究逐渐减少,人们开始热衷于进行新结构反应型乳化剂的合成与性能的研究,期望着可以找到性能更加优异的品种和开拓其应用领域市场等。
另一方面,近些年来,研究相对多的是将可聚合乳化剂应用到微乳聚合中得以来制备无机或者是有机纳米粒子。
我国国内有关反应型乳化剂的研究是近几年才开始兴起,就眼前而言,较为热门的几种可聚合乳化剂有阴离子型、阳离子型马来酸酯类的和丙烯酰胺可聚合乳化剂等。
这几年,在乳液聚合理论和技术发展的基础上,发现了有机-无机纳米复合高分子乳液,材料的复合也已经开始从单纯的机械共混逐步扩大发展到了亚微观的有机复合[21]。
纳米复合高分子乳液中一相为有机聚合物相,另一相为无机相合物相,该类型的复合材料与常规的聚合物/无机填料复合体系不同,不仅仅在于有机相与无机相的简单混合,而更为重要的是两相在纳米尺寸范围内可以复合而成的。
有机-无机复合乳液聚合是把有机物和无机物的长处结合起来的一种新型乳液聚合技术。
无机材料具有硬度高、耐老化、耐溶剂、价廉等长处,与此同时有机材料具有成膜性好、柔韧性好、可选择性强等优点。
用有机-无机复合乳液聚合所得来的高分子乳液具有着与生俱来的强大优势,比如说附着性能好、耐水性好、透气透湿性高、抗粘连性、力学性能好等优点,在化工、电子学、光学、机械、生物学等领域展现出广阔的应用前景,市场前景无比灿烂。
就现在而言,有机-无机复合乳液聚合最关键的技术是要解决有机、无机两种材料的界面亲和性,高性能有机硅-丙烯酸酯复合乳液是有机-无机复合乳液聚合最典型的代表[22]。
1.3研究目的和步骤
本课题是以生产苯丙乳液为目的,通过研究合成工艺路线的差异,来选择最佳的且经济合理的工艺流程,设计的装置中的主要设备——聚合釜。
由于设计需要每一批的进料量、反应时所放出热量的速率、以及物料的粘度、密度和比热等数据,因此本设计工作主要分为两步来进行:
1、资料收集:
通过查阅有关资料来确定物料的进料比、反应时间、反应温度等相关的操作条件,通过生产需求来确定实际生产的进料量,可以为工艺设计提供极其重要的计算数据,测产品的粘度密度等都要作为设计依据。
2、设计计算:
知道生产的进料量,进行物料衡算、热量衡算;根据相关工艺操作要求,设计出合适高效的操作方式和生产工艺;再就是设备的选型问题、计算得出聚合釜的主体尺寸;绘制出工艺流程图以及聚合釜总装图。
第二章厂址选择及工厂总平面设计
2.1厂址选择
2.1.1厂址选择的原则
1、符合当地城镇总体发展规划的要求,并尽量与附近企业相配合。
2、面积和外形要满足啤酒生产工艺的要求,并留有适当的扩建余地。
3、厂址地形宜平坦,地面倾斜坡度最好不超过3%,便于厂区运输线路布置。
2.1.2厂址选择从投资和经济效益考虑
1、较方便的运输条件,距离公路或专用铁路最短为好,以节省投资。
2、有一定供电条件,满足生产需要。
3、所选厂址附近不仅有充足的水源,而且水质应较好。
2.1.3厂址选择结果
本设计综合以上各种因素,经过半个月的探访和实地考察,由于上窑发展较早,厂房建设较为密集,、金属等重污染行业,有完善的污水处理系统,及消防系统,利于工厂进驻。
所以初步选择了黄石市上窑作为工厂的厂址。
2.2总平面设计
2.2.1总平面的设计的原则和要求
总平面设计必须符合国家各项方针的前体下,符合防火,卫生规范,尽可能节约用地,不占或少占农田,少劳动强度,节约建筑材料[3]。
厂区占地面积包括厂区建筑物,露天原料,产品堆场,道路管廊,绿化用地等。
第三章工艺流程设计
3.1工艺方案的确定
传统乳液聚合方法得到的苯丙乳液。
最低成膜温度(MFT)比较高,常温下不能成膜,大大限制了它的应用范围。
靠传统的聚合方法是不能解决这一问题的。
核壳乳液聚合生成具有异相结构的胶粒,能很好地解决这一问题。
制备核壳乳液最常用的方法就是种子聚合。
乳液聚合是制造合成聚合物的主要实施方法之一。
目前在世界范围内的乳液聚合法用来大量的制备各种类型乳液聚合物和聚合物乳液,其产品已广泛的应用于各个技术领域中,成为不可缺少的材料或工作物质。
由于乳液聚合体系粘度低,反应中心乳胶粒直径小,故容易散热;乳液聚合反应即可具有高的聚合反应速率,又可获得高分子量的聚合物,再者进行乳液聚合所用设备简单,工艺流程较短,不要求高温高压的反应条件,操作方便,技术容易掌握,生产灵活性大。
同时聚合物乳液以水为介质,便宜,易得,不污染环境,不会对从事聚合物乳液生产和应用的操作人员造成人体伤害,且聚合物乳液可以直接用作涂料、粘合剂等性能优良的材料或工作物质,所以,许多年来乳液聚合科学与技术一直保持长盛不衰,乳液聚合理论、聚合物乳液和乳液聚合物的工业化生产和应用技术都得到了快速的发展。
本实验采用种子乳液聚合法。
3.1.1反应时间的选择[25]
固定乳化剂质量分数为3%,引发剂用量质量分数0.4%,反应温度80℃时,温度对黏度的影响,由图3-1可知,选择反应时间为3小时比较合适。
3.1.2产品主要技术性能指标
外观:
带有蓝色荧光的白色乳液
固含量:
(40±2)%
pH值:
7~8
粘度:
80~1500mPa·s
最低成膜温度:
15℃
图3-1乳化剂质量分数对粘度影响
3.2工艺原理
乳液聚合是以水为连续相(分散剂),在表面活性剂(乳化剂)存在下,使聚合反应发生在由乳化剂形成的乳胶粒内部(即表面活性剂形成的胶束作为微反应器),制备高分子材料的一种方法。
乳液聚合技术较本体聚合、溶液聚合、悬浮聚合相比较,有许多重要特点、优点,既可制备高分子量的聚合物,又有高的聚合反应速率。
反应体系易散热,有利于聚合反应的控制。
生产设备和工艺简单,操作方便,灵活性大,代表了环境保护技术的发展方向,很多场合下,聚合物乳液可直接利用。
因此,近年来乳液聚合技术发展很快,特别是在聚合技术上派生、发展了多种新技术、新方法。
乳液聚合体系主要有四大组分:
单体、分散介层(水)、乳化剂、引发剂,其次还有用了pH调节并改善乳液流动性的电解层,pH调节用的中和剂等。
依据反应单体与反应性质,来选用不同的乳化剂。
乳化剂是决定乳液稳定性的最主要因素,对反应速率、乳液粘度、胶粒尺寸等也有很主要的作用。
乳化剂的选择除单体要求的种类外,一般以体系要求的HLB值决定其配比和用量,而且多以非离子型与离子型乳化剂复配,常用的乳化剂如下:
用于乳液聚合的引发剂主要是以过氧化氢为母体的衍生物,如过硫酸铵(NH4)2S2O8、过硫酸钾K2S2O8、有机过氧化氢,对某些体系,还可采用其他热分解引发剂如芳基偶氮氨基化合物等。
经典的乳液聚合物工艺的定性理论(用以描述乳液聚合体系中各种物料所处的状态及它们之间的相互影响、相互作用和相互转化规律)将乳液聚合过程分为四个阶段:
分散阶段:
乳化剂在分散相(水)中形成胶束:
加入部分单体后,在搅拌作用下,部分形成单体珠滴、部分增溶在乳化剂形成的胶束中或溶解在水相中。
乳化剂、单体化水相、单体珠滴和胶束之间建立动态平衡。
阶段Ⅰ(成核阶段):
水溶性引发剂加入到体系中后,在反应温度下引发剂在水相中开始分解出初始自由基,或扩散到胶束中或在水相引发聚合,或扩散到单体珠滴中。
无论那种情况都可引发单体聚合形成乳胶粒。
阶段Ⅱ(乳胶粒长大阶段):
聚合反应发生在乳胶粒中,逐渐加入的单体形成单体珠滴,单体由单体珠滴通过水相扩散到乳胶粒中,在其中进行聚合反应,使乳胶粒长大,此时,乳化剂和导体在乳胶粒、水相和单体珠滴间建立动态平衡。
单体珠滴消失。
标志阶段Ⅱ结束。
阶段Ⅲ(聚合反应完成阶段):
在该阶段,胶束和单体珠滴都不见了。
绝大多数未反应的单体集中在乳胶粒内部,只有极少数的单体溶解在水相中,单体和乳化剂在水相和乳胶粒之间建立动态平衡。
水相中的引发剂分解出自由基,扩散到乳胶粒中,在乳胶粒中引发聚合,使乳胶粒中的单体逐渐降低。
使单体转化率达到最大至反应结束。
3.3设计原则,依据和指导思想
3.2.1设计原则
(1)本设计每一环节都遵循国家政策、法律、法令及行业规范;
(2)在结合国情的前提下,采用世界先进生产工艺,合理的控制生产开销、坚决保证生产的安全以及对三废的严格处理。
(3)采用国内现有生产的成套设备;
(4)成品标准按国家标准、行业标准执行。
3.3.2设计依据
(1)依据学校下达的毕业设计任务书;
(2)依据实习公司的有关资料;
(3)依据图书馆及网上查询的有关资料。
3.3.3指导思想
(1)为了保证产品的高质量和生产过程的安全,采用悬浮聚合工艺;
(2)生产过程采用自动化控制,机械化操作;
(3)对于可能出现的危险,安装报警消防设施;
(4)为达到环保要求采用技术成熟的溶液聚合方法,并对生产过程中排放出来的废物进行处理;
(5)为保证生产正常的进展和操作便利以及工作人员的安全,厂房、车间、设备的布局一定要严格执行土建标准。
第四章原料,配方设计及选型依据
4.1原料的用量
4.1.1单体用量[23]
不同的单体具有不同的性能,一种单体均聚物一般不具备全面的性能(表4-1),需选用多种单体进行共聚合成。
丙烯酸丁酯玻璃化温度较低,是一种软单体。
如其含量较高,则产品强度低,但成膜性好。
苯乙烯玻璃化温度较高,是一种硬单体,如其含量较高,则产品强度高,但成膜性差。
故二者共用,通过调整比例,可使乳液性能较为理想。
表4-1 不同单体的性能
性能
成膜性
硬度
拉伸强度
附着力
耐湿性
耐热性
耐紫外线
丙烯酸丁酯
有
很软
很低
良好
一般
良好
良好
苯乙烯
无
硬
高
良好
优
优
一般
4.1.2 乳化剂的选择和用量[23]
在乳液聚合中,乳化剂的性能影响聚合反应的速度、相对分子质量大小及分布、乳胶粘度和稳定性。
阴离子乳化剂赋予乳液较好的机械稳性;非离子乳化剂赋予乳液较好的化学稳定性。
经实践对比,选用阴离子型乳化剂十二烷基硫酸钠与非离子型乳化剂op-10组成复合体系,可提高乳液的稳定性,解决胶体易破乳问题,同时根据乳化剂对粘度的影响,其最佳用量:
十二烷基硫酸钠为0.6%,op-10为0.3%。
图1乳化剂质量分数对粘度影响
4.1.3引发剂的用量[23]
引发剂是聚合反应的触媒。
用量少则反应不完全,用量大则反应剧烈甚至爆聚。
因此适当的用量不仅可使聚合过程稳定,而且也可使聚合反应完全。
一般引发剂用量占单体量的0.2%~0.7%之间[24],经实验,一般选择过硫酸铵为引发剂,用量为0.4%。
4.2选型依据
4.2.1总体概述
为反应温度分布均匀,需使用搅拌反应釜。
典型的搅拌反应器如图4所示,它主要由搅拌罐、搅拌装置和轴封三大部分组成。
搅拌罐包括罐体、加热装置及附件。
罐体为一个提供化学反应空间的容器。
由于化学反应一般都要吸收和放出热量,因此在容器的内部或外部设置加热或者冷却装置。
例如在容器外部设置夹套,或者在容器内部设置蛇管;为了与减速机和轴封相连接,顶盖上要焊装底座;为了便于检修内件及加料和排料,需要装焊人孔,手孔和各种管件;为了在操作过程中有效地监视和控制物料的温度,压力和
料面高度,则需要安装温度计,压力图4
表,液面计,视镜和安全泄放装置;有是为了改变物料流型,增强搅拌强度,强化传质和传热,还要在罐体的内部焊装挡板和导流筒。
另外,在罐体上还需设置工艺接管等附件,但是随着附件的增加,往往会给设备的制造和维修带来很多麻烦,增加设备制造和维修费用。
所以在确定搅拌罐结构的时候应全面综合考虑,使设备满足生产工艺要求有做到经济合理,实现最佳化设计[26]。
4.2.2罐体的长径比
选择罐体的长径比应考虑的主要因素有3个方面,即长径比对搅拌功率的影响,对传热的影响以及物料搅拌反应特性对长径比的要求。
·罐体长径比对搅拌功率的影响
一定结构型式搅拌器的桨叶直径同与其装配的搅拌罐罐体内径通常有一定的比例范围。
随着罐体长径比的减小,即高度减小而直径放大,搅拌器桨叶直径也相应放大。
在固定的搅拌轴转数下,搅拌器功率与搅拌器桨叶直径的5次方成正比。
所以,随着罐体直径的放大,搅拌器功率增加很多,这对于需要较大搅拌作业功率的搅拌过程是适宜的,否则减小长径比只能无谓地消耗一些搅拌器功率,长径比则可以考虑选得大一些。
·罐体长径比对传热的影响
套传热有显著影响。
容器一定时长径比越大则罐体盛料部分表面积越大,夹套的传热面积也就越大。
同时长径比越大,则传热表面距离罐体中心越近,物料的温度梯度就越小,有利于提高传热效果。
因此单从夹套传热角度考虑,一般希望长径比取得大一些。
·物料特性对罐体长径比的要求
某些物料的搅拌反应过程对罐体长径比有着特殊要求,例如发酵罐之类,为了使通入罐内的空气与发酵液有充分的接触时间,需要有足够的液位高度,希望长径比取得大一些。
根据实践经验,几种搅拌罐的长径比大致如表4-2。
表4-2几种搅拌罐的长径比
种类
设备内物料类型
H/D
一般搅拌器
液-固相或液-液相物料
1~1.5
气-液相物料
1~2
发酵罐类
1.7~2.5
4.2.3装料系数[26]
选择了罐体长径比之后,还要根据搅拌罐操作时所允许的装满程度考虑选择装料系数η,然后经过初步计算,数值圆整及核算,最终确定筒体直径和高度。
反应液体积VR与反应器实际体积VT有如下关系:
VR=VTη(m3)(1—1)
设计时应合理地选用装填系数η值,尽量提高设备利用率。
通常η可取0.6~0.85。
如果物料在反应过程中起泡沫或呈沸腾状态,η应取低值,约0.6~0.7;如果物料反应平稳,η取0.8~0.85(物料黏度较大可取大值)。
4.2.4确定筒体直径和高度[27]
知道了筒体的长径比和装填系数之后,还不能直接算出筒体直径和高度,因为当筒体直径不知道时封头的容积就不知道,罐体全容积也不能最后知道。
查表【7】标准椭圆封头的体积为0.131D3、h封=D/4。
令:
h为釜体直边高、H为反应器釜体总高度,则:
H=h+2h封=h+D/2=1.5D
若取H/D=1.5,则有:
h=D
VT=πD2h/4+0.262D3=πD3/4+0.262D3=1.047D3(1—2)
所以D=
(1—3)
圆整后查表【7】选取公称直径。
所以,釜直边高
h=(VT-2×V封)/0.785D2(1—4)
再重新计算H及新的长径比,大致符合要求便可。
4.3搅拌设备的传热
4.3.1传热方式
反应器的加热和冷却有多种方式。
可在容器的外部或内部设置供加热或冷却的换热装置,例如在容器外部设置夹套,在容器内部设置蛇管换热器等,一般用的最普遍的采用夹套传热的方式。
4.3.2夹套传热
传热夹套一般由普通碳钢制成,它是一个套在反应器筒体外面能形成密封空间的容器,既简单又方便(如图6)。
夹套上设有水蒸汽、冷却水或其他加热、冷却介质的进出口。
如果加热介质是水蒸气,则进口管应靠近夹套上端,冷凝液从底部排除;如果传热介质是液体,则进口管应安置在底部,液体从地步进入,上部流出,使介质能充满整个夹套的空间。
有时,对于较大型容器,为了得到较好的传热效果,在夹套空间装设螺旋导流板,以缩小夹套中的流体的流通面积,提高流体的流动速度和不避短路,但结构较为复杂一些。
夹套的高度决定于传热面积F,而传热面积F是由工艺要求确定。
但须注意的是夹套高度一般应不低于料液的高度,应该比器内液面高出50~100mm左右,以保证充分传热。
根据装料系数η,则物料容积V·η,因此,夹套高度H夹可由下式来估算:
H夹≥(V·η-V封)/f(1—5)
f=πD2/4(1—6)
式中:
f——筒体横截面积(m2);
D——容积内直径(m);
η——装料系数;
V——容器容积(m3);
V封——封头容积(m3)
4.3.3蛇管传热
当需要的传热面积较大、而夹套传热在允许的反应时间内不能满足要求时,或是壳体内衬有橡胶、耐火砖等隔热材料而不能采用夹套时,可采用蛇管传热,蛇管的管长与管径之比见表4-3。
表4-3管长与管径之比值表
蒸汽压力(kgf/cm2)
0.45
1.25
2
3
5
管长与管径最大比l/d
100
150
200
225
275
4.3.4内传热挡板和夹套
随着反应器容积的增大,传热问题显得突出起来,光靠夹套已很不够,常常要在反应器内附加传热挡板。
传热挡板既可以增加传热面积,移走热量,又可以强化搅拌效果,起破坏涡流控制流型效果。
4.4确定传热方式
反应釜一般需采用夹套,而夹套又有多种类型各种类型夹套的适用范围见表4-4。
表4-4各种类型夹套的使用范围
夹套形式
温度(℃)
压力(kgf/cm2)
整体夹套
350
300
6
16
半圆管夹套
280
10~64
型钢夹套
225
6~25
蜂窝夹套
250
25~40
4.4.1整体夹套的结构类型
按照对罐体的包覆程度,夹套可分为4种类型。
第一种仅圆筒的一部分有夹套,用在需要加热面积不大的场合。
第二种为圆筒的一部分和下风头包有夹套。
这种夹套是常用的类型结构。
第三种是为减小罐体的外压计算长度L,或者为了实现在罐体的轴线方向分段地控制温度、进行加热和冷却而采用的分段夹套,各段之间设置加强圈或采用能够起到加强圈作用的夹套封口件。
这种结构适用于罐体细长的场合。
第四种为全包覆式夹套。
4.4.2整体夹套夹套的尺寸及连接型式
整体夹套和罐体有2种连接型式,即不可拆卸式和可拆卸式。
不可拆卸式夹套的结构简单,密封可靠,主要适用于碳钢制的搅拌设备。
可拆卸式夹套的连接结构,用在操作条件较差,以及要求定期检查罐体外部表面或者要求定期清洗夹套内污垢的场合。
夹套直径确定见表5。
表5整体夹套直径的确定
Dg
500~600
700~1800
2000~3000
Dj
Dg+50
Dg+100
Dg+200
4.5搅拌器
4.5.1搅拌器分类及参数[28]
搅拌器是搅拌槽的核心设备,一般是根据不同的应甩条件和不同的工艺要求而设计的,其主要在于搅拌叶轮的型拭和传动装置有区别。
(一)依据叶轮的形状来分有:
1桨式——有分平桨和折桨两种。
其桨宽和叶径