精密与特种加工简答综合10修改解答.docx
《精密与特种加工简答综合10修改解答.docx》由会员分享,可在线阅读,更多相关《精密与特种加工简答综合10修改解答.docx(19页珍藏版)》请在冰豆网上搜索。
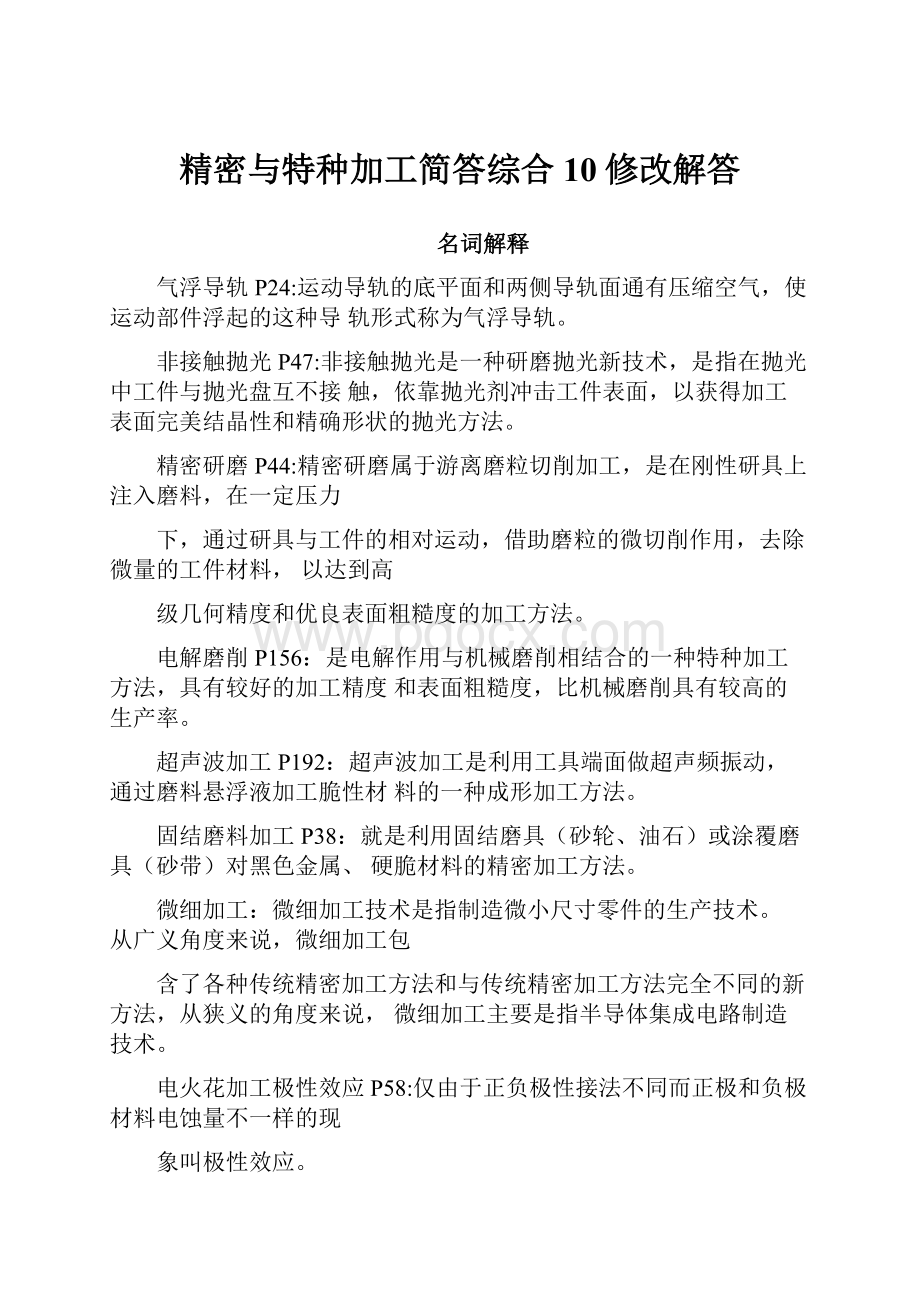
精密与特种加工简答综合10修改解答
名词解释
气浮导轨P24:
运动导轨的底平面和两侧导轨面通有压缩空气,使运动部件浮起的这种导轨形式称为气浮导轨。
非接触抛光P47:
非接触抛光是一种研磨抛光新技术,是指在抛光中工件与抛光盘互不接触,依靠抛光剂冲击工件表面,以获得加工表面完美结晶性和精确形状的抛光方法。
精密研磨P44:
精密研磨属于游离磨粒切削加工,是在刚性研具上注入磨料,在一定压力
下,通过研具与工件的相对运动,借助磨粒的微切削作用,去除微量的工件材料,以达到高
级几何精度和优良表面粗糙度的加工方法。
电解磨削P156:
是电解作用与机械磨削相结合的一种特种加工方法,具有较好的加工精度和表面粗糙度,比机械磨削具有较高的生产率。
超声波加工P192:
超声波加工是利用工具端面做超声频振动,通过磨料悬浮液加工脆性材料的一种成形加工方法。
固结磨料加工P38:
就是利用固结磨具(砂轮、油石)或涂覆磨具(砂带)对黑色金属、硬脆材料的精密加工方法。
微细加工:
微细加工技术是指制造微小尺寸零件的生产技术。
从广义角度来说,微细加工包
含了各种传统精密加工方法和与传统精密加工方法完全不同的新方法,从狭义的角度来说,微细加工主要是指半导体集成电路制造技术。
电火花加工极性效应P58:
仅由于正负极性接法不同而正极和负极材料电蚀量不一样的现
象叫极性效应。
激光焊接P186:
焊接过程属传导焊接,即激光辐照加热工件表面,产生的热量通过热传导向内部传递。
在工件上形成一定深度的熔池,冷却凝固以后就将工件焊接完成。
离子镀膜P213:
是在真空条件下,利用气体放电使气体或被蒸发物质部分离化,在气体离
子或被蒸发物质离子轰击作用的同时把蒸发物或者反应物沉积在基片上成膜。
镜面磨削P41:
镜面磨削是指加工表面粗糙度达到Ra0.02〜0.01Am、表面光泽如镜的磨削
方法。
空气静压轴承P19:
在转轴和轴承瓦之间,通入压缩空气,将轴承和转轴分开,以压缩空气承受径向载荷的一种轴承形式。
等脉冲电源P72:
是指每个脉冲在介质击穿后所释放的单个脉冲能量相等。
电刷镀P166:
又称涂镀或无槽镀,是在金属工件表面局部快速电化学沉积金属的新技术,主要用于增大尺寸、修复零件、改善表面性能等。
电子束曝光P209:
是先利用低功率密度的电子束照射称为电致抗蚀剂的高分子材料,由入射电子与高分子相碰撞,使分子链被切断或重新聚合而引起分子量的变化,这一步骤也称为
电子束光刻。
浮动抛光P48:
浮动抛光是一种平面度极高的非接触超精密抛光方法。
抛光时抛光盘及工
件高速回转,在二者之间的抛光液呈动压流体状态,并形成一层液膜,从而使工件在浮起状
态下进行抛光。
砂轮修整P43:
就是用修整工具将砂轮修整成形或修去磨钝的表层,以恢复工作面的磨削
性能和正确的几何形状的操作过程。
砂轮修整是整形和修锐的总称。
整形是为了获得理想的
砂轮几何形状,修锐是为了提高磨削性能。
金刚石晶面磨削率P31:
它是指单位载荷和单位线速度下的磨削体积。
电镀P162:
利用电解液中的金属正离子在外电场的作用下沉积到阴极的过程对工件进行加工的方法,主要用于表面装饰、防锈。
液体静压轴承P18:
靠外部供给压力油、在轴承内建立静压承载油膜以实现液体润滑的滑
动轴承。
修光刃P34:
金刚石刀具刀头在主切削刃和副切削刃之间加过渡刃,对加工表面起修光作用,获得好的加工表面质量。
光刻加工P240:
光刻加工技术是用照相复印的方法将光刻掩模上的图形印制在涂有光致抗蚀剂的薄膜或基材表面,然后进行选择性腐蚀,刻蚀出规定的图形。
光管效应P180:
激光打孔采用多次照射加工,孔深可以大大增加,锥度可以减小,孔径几乎不变的现象。
简答题
1、简述精密磨削加工机理P38-39
低,处于钝化状态而受到钝化膜的保护就可以减少杂散腐蚀,提高加工精度;加工型孔时,
咼。
3、简述电铸方法基本原理P163
用可导电的原模作为阴极,电铸材料作为阳极,电铸材料的金属盐溶液做电铸液,在直
流电源的作用下,溶液中金属离子在阴极上获得电子成为金属原子而沉积镀覆在阴极原模表
)加工后零件无毛刺和残余应力,粗糙度好,精度差)与其它加工方法相比,生产率最高)加工过程中工具电极(阴极)基本不损耗
4
的气体对环境有一定的污染
7、简述超声加工原理及应用P192-193201-203
局限性:
1)加工精度一般不如电火花和超声波加工高)加工复杂型腔和型面时,工具的制造费用较高)电解加工设备占地面积大、附属设备多,初期投资较大)电解液的处理和回收油一定难度,而且对设备有一定的腐蚀作用,加工过程中产生
原理:
超声波加工是利用工具端面作超声频振动,通过磨料悬浮液加工脆性材料的一种
成形加工方法。
超声波发生器产生1.6万Hz以上高频交流电源,输送给超声换能器,产生
超声波振动,并借助变幅杆将振幅放大到0.05〜0.1mm左右,使变幅杆下端的工具产生强烈
振动。
磨料在工具的超声振荡作用下,以极高的速度不断地撞击工件表面,使工件材料在瞬间高压下产生局部破碎。
随着悬浮液的循环流动,使磨料不断得到更新,同时带走被粉碎下来的材料微粒。
工具连续进给,工具的形状便被复制到工件上。
P201
超声波加工的应用:
成形加工、切割加工、复合加工、超声波焊接、超声波清洗。
8、电化学阳极钝化现象是优势还是缺点,为什么?
P131
电极钝化现象的存在,使电解加工阳极溶解速度下降甚至停顿。
从生产率的角度出发人们不希望选用能产生钝化现象的钝化型电解液。
但是,当采用NaCl等非钝化型电解液工作时,虽然生产率很高,但因为杂散腐蚀严重,成形精度较差,严重影响了电解加工的应用。
而当采用钝化型电解液加工时,尽管电极工具的非工作面没有绝缘,但当加工间隙达到一定尺寸后,对应的工件表面就会产生钝化膜,可以避免产生杂散腐蚀,提高加工精度,促进电解加工的推广应用。
9、简述超精密加工的实现条件P15
P31
超精密加工的实现条件包括以下几个方面:
①超精密加工的机理与工艺方法;②超精密加工工艺装备;③超精密加工工具;④超精密加工中的工件材料;⑤精密测量及误差补偿技术;⑥超精密加工工作环境、条件等。
在超精密加工的实施过程中,必须综合考虑以上因素才能取得令人满意的效果。
10、为什么要进行金刚石晶体的定向?
有几种方法?
金刚石晶体属于平面立方晶系,由于每个晶面上原子排列形式和原子密度的不同以及晶
(100)、
面之间距离的不同,造成天然金刚石晶体的各向异性,天然金刚石晶体三个主要晶面
(110)、(111),各晶面硬度和耐磨性的程度不同,其中(110)晶面硬度和耐磨性最低,(111)
晶面硬度和耐磨性最高。
因此,在制造刀具时,如果晶向选择不当,即使晶面选择正确,刃磨效率也会大大降低,所以金刚石刀具制造前.对金刚石天然晶体的准确定向.是合理选择晶面的基础技术,是制造性能优良刀具的必要条件。
X射线晶体定向,激光晶体定向。
金刚石晶体的定向有三种方法:
人工目测定向,
涂镀加
11、简述涂镀加工原理与应用。
P166
涂镀又称刷镀或无槽镀,是在金属工作表面局部快速电化学沉积金属的新技术。
工时,工件接电源的负极,镀笔接电源的正极。
浸满镀液的镀笔在工件表面上以一定的相对运动速度进行刷抹而使工件获得镀层。
在阴极工件上,镀液中的金属离子在电场作用下与电子结合,还原为金属原子而沉积形成镀层。
应用:
(1)修复失效的零部件表面,恢复尺寸和几何形状,设施超差品补救。
柱塞、密封部件、模具型腔、印刷辊及吸墨鼓、造纸辗光辊及烘缸等的修补。
(3)大型、复杂、单件小批量工件的表面局部刷镀镍、铜、锌、镉、钨、金、银等防护层,改善表面性能。
12、电解加工及电火花加工过程中,电极与工件能否出现短路,为什么?
在短
电解加工电流极大,电流是几千安培甚至上万安培,由于没有安装限流电阻,短路就会烧伤工件,所以不能短路。
电火花加工中安装了限流电阻,而且有伺服自动进给系统,路时,自动进给调节系统将自动调节,使其迅速退回,消除短路,短路时不会烧伤工件。
13、简述精密加工技术难点。
P12
工精度影响大;③工具和工件表面微观变形随机,精度难控制。
超微量加工时,工具和工件表面微观的弹性变形和塑性变形是随机的,精度难以控制;工艺系统的刚度和热变形对加工精度有很大影响;去除层越薄,被加工表面所受的切应力越大,材料就越不易被去除。
14、为什么单晶金刚石被认为是理想、不能代替的超精密切削刀具材料?
P31
是因为它有着一系列优异的特性,如硬度极高,耐磨性和强度高,导热性能好,和有色
金属摩擦系数小,能磨出极锋利的刀刃等。
而且单晶金刚石可以研磨达到极锋利的刃口,没有其他材料可以磨到这样锋锐并且能长期切削而磨损很小。
因此金刚石是理想的、不能代替
的超精密切削的刀具材料。
15、电铸为什么能达到很高的尺寸精度和很小的表面粗糙度?
P163-164
(1)高复制精度。
电铸件是靠在原膜表面沉积金属离子而成,由于电铸件与模具表面不存在间隙,所以可准确复制原模的表面细节。
(2)原模可永久性重复使用。
电铸加工过程对原模无任何损伤,所以原模可永久性重复使用,而同一原模生产的电铸件重复精度极高,尺寸误差可在微米数量级。
(3)借助石膏、石蜡、环氧树脂等作为原模材料,可把复杂零件的内表面复制为外表面,或外表面复制为内表面,然后再电铸复制。
超声波加工机床是由超声波电源(超声发生器)、超声振动系统、超声加工机床本体、磨料悬浮液冷却及循环系统四部分组成。
其各部分作用为:
超声波发生器:
其作用是将50Hz的交流电转变为一定功率的超声频电信号,以提供工具端面往复振动和去除被加工材料的能量。
超声振动系统:
是将高频电能转变为机械能,使工具端面作高频率小振幅的振动,并将振幅扩大到一定范围(0.01~0.15mm)以进行加工。
磨料工作液及冷却循环系统:
更换和输送磨粒悬浮液,以及冷却换能器
机床本体:
超声波加工机床一般比较简单,机床本体就是把超声波发生器、超声波振动
还包括支撑
系统、磨料工作液及其循环系统、工具及工件按照所需要位置和运动组成一体。
声学部件的机架及工作台、使工具以一定压力作用在工件上的进给机构及床体等部分。
17、举例说明精密与特种加工技术对材料科加工性和结构工艺性的影响。
P3-4
特种加工方法对材料的可加工性,不再受其硬度、强度、韧性、脆性等影响,容易加工传统方法难加工的金刚石、硬质合金、淬火钢、半导体、玻璃等材料,提高了材料的可加工性。
特种加工方法对过去因刀刃不能达到的圆角过渡、因大而复杂只能是镶拼的模具结构等都得
以改进,使传统方法难于加工的异形孔、微孔、弯孔、斜孔、窄缝等得以实现,对各种复杂型面、低刚度零件、精微零件等加工发挥了重要作用。
18、分析超硬磨料砂轮修整的机理与特点。
P43
砂轮修整时,修整器应安装在低于砂轮中心0.5〜1.5mn处并向上倾斜10。
〜15°。
修
整包括整形和修锐,整形是使砂轮达到一定精度要求的几何形状;修锐是去除磨粒间的结合
剂,使磨粒突出结合剂一定高度。
普通砂轮的整形和修锐一般是合为一步进行,而超硬磨料
砂轮的整形和修锐一般是分为先后两步进行的。
特点:
1)磨削能力强,耐磨性好,耐用度高,易于控制加工及实现自动化2)磨削力
小,温度低,加工质量好,不烧伤,裂纹和组织变化3)磨削率高,4)加工成本低
19、简述实现电火花加工的必要条件。
P51
1)电极之间始终保持确定的距离;
2)放电点的局部区域达到足够高的电流密度;
3)必须是脉冲性的放电(高频脉冲);
4)及时排除电极间的电蚀产物,以确保电极间介电性能的稳定。
20、简述超精密切削加工对刀具的要求。
P27
1)极高的硬度、极高的耐磨性和极高的弹性模量,以保证刀具有很高的尺寸耐用度。
2)刃口能磨得极其锋锐,即刃口半径P值很小,以实现超薄切削。
3)刀刃无缺陷,切削时刃形将复制在被加工表面上,从而得到超光滑的镜面。
4)与工件材料的抗粘结性好、化学亲和性小、摩擦因数低,以得到极好的加工表面完整性。
21、精密磨削砂轮为何要修整?
如何修整?
P43
修整是整形和修锐的总称。
整形是为了获得理想的砂轮几何形状,修锐是为了提高磨削性
能。
修整方法:
1)车削法2)磨削法3)滚压挤轧法4)喷射法5)电加工法6)超声波振动修整法
综合题
P127+129
1试述电解加工平衡间隙的影响因素,说明平衡间隙理论有何应用。
*■
电解加工电极间隙△
根据上式可知,平衡间隙与电流效率、电化学当量、电导率、电解液的欧姆压降成正比;
与加工速度成反比。
当加工条件确定后,电流效率、电化学当量、电导率基本不变,平衡间
隙主要由选用的电压和进给速度所决定。
平衡间隙理论可以应用在NaCI电解液加工中,计算加工中端面、斜面、侧面的电极间隙;设计电极尺寸和修正量;分析加工精度;选择加工参数,如电源电压、进给速度、电解液的浓度和温度等等。
略去切入、切出程序)
但特特种加工工艺但不可能取代和排斥应用各种复合加工技术。
序号
线段
B
X
B
Y
B
J
G
Z
1
直线AB
B
40000
B
0
B
40000
G
L1
2
斜线BC
B
17000
B
10000
B
17000
G
12
3
圆弧CD
B
3000
B
4000
B
6000
G
NR
4
斜线DA
B
17000
B
10000
B
17000
G
13
3、精密与特种加工技术能否取代传统机械切削加工?
为什么?
P5
精密与特种加工技术不能取代传统机械切削加工。
因为传统加工是指切削加工和磨料加工,是行之有效的实用加工方法,是主要加工手段,今后仍将占主导地位,应重视进一步发展。
随着难加工的新材料、复杂表面和有特殊要求的零件越来越多,传统加工工艺必然难以适应。
种加工扩大了加工范围,提高了加工精度、表面质量和加工效率,具很大潜力。
是传统加工工艺的补充和发展,可在特定条件下取代一部分传统加工工艺,
主流的传统加工工艺。
应发挥各自所长,并将各种加工方法融合在一起,丿
4、电火花加工与电解加工在自动进给系统、所用电源及工作液等方面有何不同?
一般电解加工自动进给系统主要是控制均匀等速的进给速度,它的大小是事先设定好的。
进
给速度的大小与端面平衡间隙有直接关系(双曲线关系),而端面平衡间隙又直接影响到阴极的
形状。
在正常电解加工时,主要依照电流的大小来进行控制,但在电极开始进入或即将退出工件
时,由于加工面积的变化,则不能依照电流的大小来控制。
电火花加工自动进给控制系统的目的是保证某一设定加工间隙的稳定,它是按照电极间隙蚀
除特性曲线来工作的,它的进给速度不是均匀等速的。
之所以形成这种不同的进给特性,主要是
电解加工中存在平衡间隙,进给速度大,平衡间隙越小,工件的蚀除速度越高,在进给方向、端面上一般不宜短路;而电火花加工中不存在平衡间隙,进给速度稍大于蚀除速度,极易引起短路,
所以必须调节进给速度以保证放电间隙。
电火花所用电源是脉冲电源,电解加工所用电源是直流电源。
电火花所用工作液是机油、煤油,电解加工工作液是电解质,如NaCL
5、用固定式阴极及NaCI电解液对碳钢零件进行电解扩孔加工,已知初始单边间隙
io=0.15mm,电压Ur=12V电导率=0.0力/过渡公式:
«=2.22rmm^/(A,m电n流效率=98%。
(已知侧面间
也=(2n⑴'"URt+i。
)
要求:
(1)画出加工示意图;
(2)求解初始蚀除速度;
(3)求解间隙由0.20mm扩大到0.50mm所需的时间;
(4)侧面间隙理论上能扩大到多大?
解:
(1)加工示意图所右图所示。
(2)初始蚀除速度
耳皿=他嘗=98%心mm/min
(3)间隙由0.20mm扩大到0.50mm所需的时间
(4)侧面间隙理论上能扩大到无穷大。
NaCI电解液是线性电解液,几乎不产生纯化膜,速度与电流密度是一条过原点的直线,
所以侧面间隙理论上能扩大到无穷大。
但随着加工间隙的增大,电流密度会减小,加工的速
度减小。
6、根据超硬磨料(金刚石、立方氮化硼)的特点,说明为什么超硬磨料磨具在精密加工和超精密加工中得到广泛应用?
P43
组织变化。
④磨削效率高,在加工硬质合金及非金属硬脆材料时,金刚石砂轮的金属切除
率优于立方氮化硼砂轮,但在加工耐热钢、钛合金、模具钢等时,立方氮化硼砂轮远高于金
刚石砂轮。
⑤综合成本低。
所以说超硬磨料磨具在精密加工和超精密加工中得到广泛应用。
7、试比较电火花加工、电解加工在进给系统、电源、工作液、生产率、加工精度及表层质
量方面异同。
10年试卷
隙又直接影响到阴极的形状。
在正常电解加工时,主要依照电流的大小来进行控制,但在电
极开始进入或即将退出工件时,由于加工面积的变化,则不能依照电流的大小来控制。
隙蚀除特性曲线来工作的,它的进给速度不是均匀等速的。
之所以形成这种不同的进给特性,
给方向、端面上一般不宜短路;而电火花加工中不存在平衡间隙,进给速度稍大于蚀除速度,
极易引起短路,所以必须调节进给速度以保证放电间隙。
两种加工的加工精度都不高,但其影响因素不同。
(电火花
加工存在电极损耗和二次放电,电极损耗多集中在尖角或底面,最近的机床产品已能将电极相对损耗比降至0.1mm甚至更小,电蚀产物在排除过程中与工具电极距离太小时会引起二次
放电,形成加工斜度影响成型精度。
但加工时不产生毛刺和刀痕沟纹等缺陷。
而电解加工的加工精度取决于阴极的精度和加工间隙的控制。
而阴极的设计、制造和修正都比较困难,
阴极的精度难以保证。
此外影响电解加工间隙的因素很多,且规律难以掌握,加工间隙的
控制比较困难。
)电火花加工依靠火花放电产生的高温熔化、气化工件材料,工件表面存在
好于电火花加工。
8、用NaNO3电解液电解加工一批零件,要求在50mm厚的低碳钢钢板上加工直径为*50mm
的通孔,已知中空电极圆孔内径为忆5mm低碳钢电化学当量:
W=2.22mm3/(Amin),
NaNO3电解液电流效率n=60%,要求:
(1)画出加工示意图;
(2)如果加工限时50min,需要的电解电流为多大?
(3)如果电解电流为1000A,则需用加工时间为多少?
解:
(1)加工示意图所右图所示。
■1
J
I
1
1
、5
*5D
(2)如果加工限时50min,需要的电解电流先求出所溶解金属的体积:
V=(兀^50―兀^35)x50=5004375mm3
44
根据公式V=wt得
=50043.75=751.4A
(3)如果电解电流为1000A,则需用加工时间
60%X2.22x50
根据公式V=Wt得
t=「50043.75=37.5min
n©|60%X2.22x1000
9、电铸加工能达到很高尺寸精度和很小表面粗糙度,其根本原因是什么?
工艺上还必须采取哪些措施?
P163-164复P6
由于电铸件与模具表面不
(1)高复制精度。
电铸件是靠在原膜表面沉积金属离子而成,
存在间隙,所以可准确复制原模的表面细节。
(2)原模可永久性重复使用。
电铸加工过程对原模无任何损伤,所以原模可永久性重复使用,而同一原模生产的电铸件重复精度极高,尺寸误差可在微米数量级。
(3)借助石膏、石蜡、环氧树脂等作为原模材料,可把复杂零件的内表面复制为外表面,
或外表面复制为内表面,然后再电铸复制。
采取的措施:
溶液必须连续过滤,以除上电解质水解或硬水足成的沉淀、阳极夹杂物和尘土等固休悬浮物+防止电铸件产生针孑Lr疏松、瘤斑和凹坑尊缺陷,
匂必须搅样电铸镀液,降低浓差极化,以增大电流密度,缩短电铸时问。
3)电铸件凸岀部分电场强.镀层厚,凹入部分电场弱,俶层薄.为了便片薄均匀,凸出部分应加屏蔽,凹入部览要拥装辅助阳扱,
⑷要严格控制钱液成分.敞度、酸碱麼、温麼电流密度等.以免舞件内应力过人导致变形,起皱、开裂或剥落,通常开始时电流宜稍小,以1^^逐渐增加.中途不宜停电*^^1纯分层。
P41
10、试从系统工程的角度分析超精密磨削能达到高精度的原因。
影响超精密磨削的因素很多,(超精密磨削的加工精度受到许多因素的影响,如超精密磨削机理、被加工材料、砂轮及其修整、超精密磨床、工件的定位夹紧、检测及误差补偿、工作环境、操作水平等。
)各因素之间又相互关联,缺一不可。
这些条件共同构成一个系统。
超精密磨削需要一个高稳定性的工艺系统,对热、力、振动、材料组织、工作环境温度和净
有了高稳定性,才
化等都有稳定性要求,并有较强的抗击来自系统内外的各种干扰的能力,能保证加工质量的要求。
所以超精密磨削是一个高精度、高稳定性的系统。
11.电解加工的间隙蚀除特性曲线与电火花加工时的间隙蚀除特性曲线各有何特点?
有何不同?
复P7
电解加工时,电极间隙蚀除特性曲线是一条双曲线,即
Ua也二C(常数)如a,而电火
花加工的蚀除特性曲线则是一条蚀除速度在起点和终点都为零的上凸二次曲线,如图
电解加工电极间隙△
电火花放电间隙^
电解加工时,只要电极不发生短路,电极间隙愈小,阳极工件的蚀除速度就愈高,
生产
率就愈高;反之,当电极间隙变大时,蚀除速度将下降。
电火花加工时,当放电间隙为零时,蚀除速度也为零。
其实,当放电间隙很小时,排屑
困难,短路率增加,蚀除速度将大大下降,甚至无法正常加工;而当放电间隙过大时,间隙
无法击穿,蚀除速度也为零(相当于非线性电解液中电解加工时有一一“断电间隙”
12、为什么说电化学加工在机理上有发展成为“纳米级加工”或“原子级加工”技术的可能性?
真正实现要采取哪些措施?
P6
由于电化学加工从机理上看,是通过电极表面逐层地原子或分子的电子交换,
使之在电
解液中“阳极溶解”而被去除来实现加工的,可以控制微量、极薄层“切削”去除。
因此,
电化学加工有可能发展成为纳米级加工或原子级的精密、
微细加工。
但是真的要实现它,从
技术上讲还有相当难度。
主要是由于电化学加工的实质是实现选择性阳极溶解或选择性阴极
沉积,只要能把这种溶解或沉积的大小、方向控制到原子级上就可以了。
但是由于它们的影
响因素太多,如温度、成分、浓度、材料性能、电流、电压等,故综合控制起来还是很不容
易。