Mastercam9线割编程说明书精.docx
《Mastercam9线割编程说明书精.docx》由会员分享,可在线阅读,更多相关《Mastercam9线割编程说明书精.docx(70页珍藏版)》请在冰豆网上搜索。
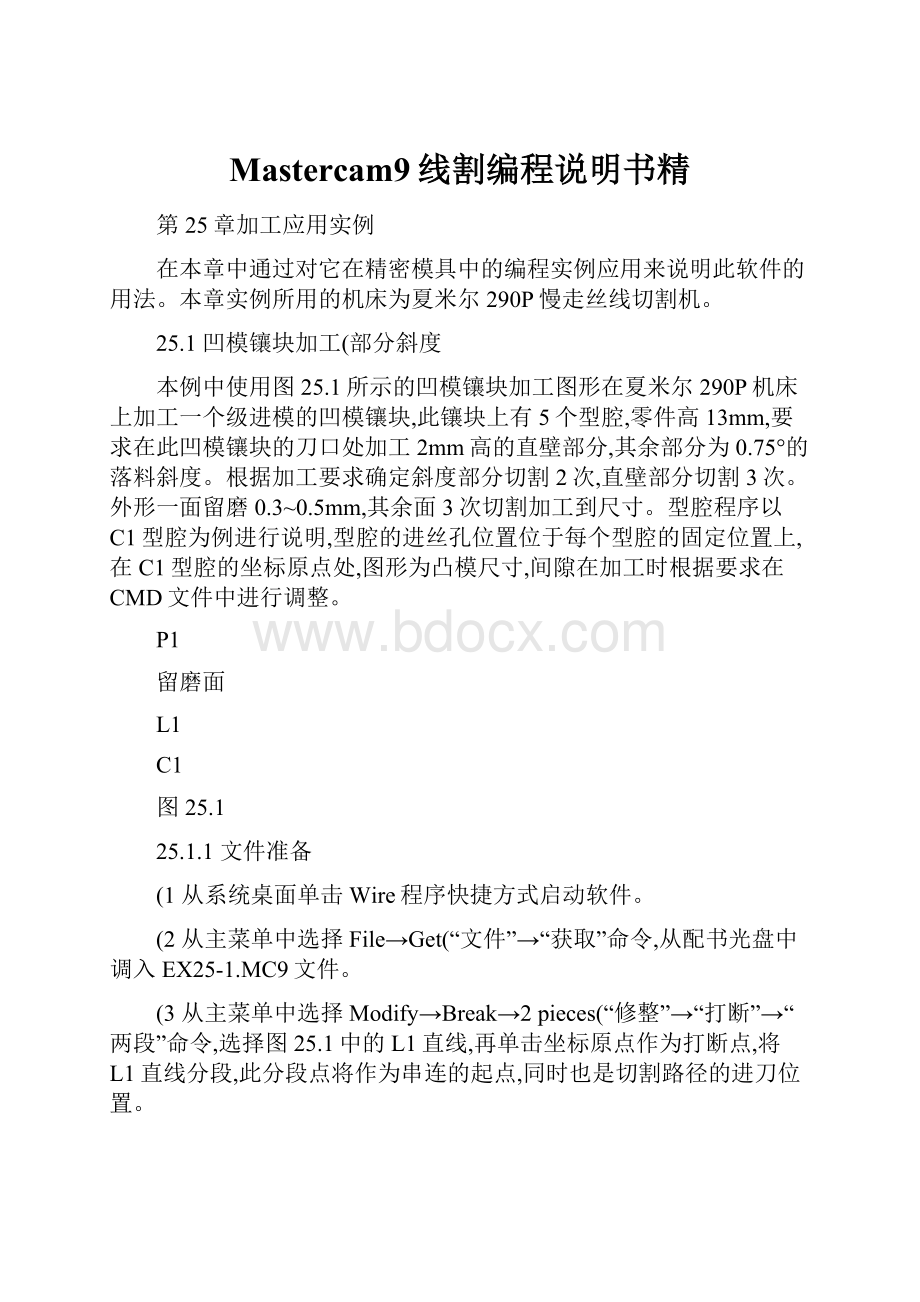
Mastercam9线割编程说明书精
第25章加工应用实例
在本章中通过对它在精密模具中的编程实例应用来说明此软件的用法。
本章实例所用的机床为夏米尔290P慢走丝线切割机。
25.1凹模镶块加工(部分斜度
本例中使用图25.1所示的凹模镶块加工图形在夏米尔290P机床上加工一个级进模的凹模镶块,此镶块上有5个型腔,零件高13mm,要求在此凹模镶块的刀口处加工2mm高的直壁部分,其余部分为0.75°的落料斜度。
根据加工要求确定斜度部分切割2次,直壁部分切割3次。
外形一面留磨0.3~0.5mm,其余面3次切割加工到尺寸。
型腔程序以C1型腔为例进行说明,型腔的进丝孔位置位于每个型腔的固定位置上,在C1型腔的坐标原点处,图形为凸模尺寸,间隙在加工时根据要求在CMD文件中进行调整。
P1
留磨面
L1
C1
图25.1
25.1.1文件准备
(1从系统桌面单击Wire程序快捷方式启动软件。
(2从主菜单中选择File→Get(“文件”→“获取”命令,从配书光盘中调入EX25-1.MC9文件。
(3从主菜单中选择Modify→Break→2pieces(“修整”→“打断”→“两段”命令,选择图25.1中的L1直线,再单击坐标原点作为打断点,将L1直线分段,此分段点将作为串连的起点,同时也是切割路径的进刀位置。
(4从主菜单中选择NCutils→PostProc→Change(“NC实用”→“后处理”→“改变”命令,弹出SpecifyFileNametoRead(读取特定的文件名称对话框,在其中选择MPWROBO.PST后处理程序,如图25.2所示,单击“打开”按钮返回,再单击MAINMENU(主菜单命令返回主菜单。
数控电火花线切割编程应用技术·432·
·432
·
图25.2
25.1.2生成切割路径
(1从主菜单中选择Wirepaths→Contour(“线切割路径”→“轮廓”命令,进入切割路径的串连选择菜单中,从图25.1中单击L1直线的下半部分,串连方向按顺时针方向,完成图形串连,如图25.3所示。
图25.3
(2然后在提示选择第二串连时选择菜单中的Done(执行命令,完成切割路径的选择,同时弹出切割设置的对话框,如图25.4所示。
(3由于采用机床控制器方式进行切割路径的偏置计算,电极丝的大小对切割路径的生成没有影响,为观察方便,在图25.4中的电极丝参数设置对话框中,取消对AssociatetoLibrary(关联到库复选框的选择,然后设置电极线直径为0.5mm,如图25.4所示(由于起割点位于图形的坐标原点上,加工的STCW(位置点默认即是在坐标原点,因此不需要再进行设置。
(4单击Contour(轮廓标签进入轮廓设置选项卡中,在其中选择锥度的形式,锥度角度值0.75°,同时设置UV平面及UV修剪面的高度值为(13-2,在补偿设置中设置控制器补偿方式,补偿方向为右偏移,如图25.5所示。
错误!
使用“开始”选项卡将标题1,章标题,部分标题1,章,章节应用于要在此处显示的文字。
·433·
·433·
图25.4
图25.5注意:
此处的高度设臵也可以在后臵生成的NC文件中直接进行修改,因为熟练应用后对
编程的处理也可以简化,直接修改NC文件更为方便。
(5单击Leadin/out(导入/导出标签进入导入/导出设置选项卡中,设置进入方式为直
线圆弧,圆弧半径为0.4mm,扫描角度为45°,退出方式为直线,导入/导出设置如图25.6所示。
数控电火花线切割编程应用技术·434·
·434·
图25.6
提示:
设臵导入/导出圆弧及过切值时需要根据加工零件的型腔大小来确定,读者可在实际切割编程时根据情况设臵这些值。
(6单击Cuts(切割标签进入切割方式设置选项卡,选中Performrough
cut(进行粗加
工复选框,然后设置精加工次数为两次,这时在右下角会看到一次粗加工、两次精加工的加工方法,切割次数设置如图25.7所示。
图25.7
错误!
使用“开始”选项卡将标题1,章标题,部分标题1,章,章节应用于要在此处显示的文字。
·435··435·(7单击General(通用标签进入通用功能设置选项卡,设置切割方向为单一方向,保
持其他设置不变,如图25.8所示,单击“确定”按钮结束设置。
(8系统将所有的端点显示出来,提示进行参数变更,选择菜单区中的Done(执行命
令,完成切割路径的创建,绘图区中的路径上出现切割路径的显示,如图25.9
所示,从图中可以清楚地看到斜度产生的上下两条切割路径及圆弧进入、直线退出的情况。
图25.8图25.925.1.3实体模拟加工
(1从主菜单中选择Wirepaths→Jobsetup(“线切割路径”→“工件设置”命令,进
入毛坯工件的设置对话框中,毛坯设定如图25.10所示,单击Selectcorners(选择拐点按钮返回到绘图区中,在生成切割路径的图形左上和右下任意选取两点作为毛坯的边界,此两点数据返回到设置区中,在Z高度设置和毛坯原点的Z值设置框中均输入数值“11”,选中Displaystock(显示毛坯选项,单击OK按钮确定。
(2在绘图区中以线框方式显示出毛坯的外形,如图25.11所示。
(3从主菜单中选择Wirepaths→Operations(“线切割路径”→“操作”命令,进入图25.12(a所示的操作管理对话框中,单击Verify(校验按钮,进入实体切削模拟对话框,同时弹出实体模拟工具栏,如图25.12(b所示。
(4单击工具栏中的(切削设置按钮,进入切削设置对话框中,选中UseJobSetup
values(使用工件设置的值选项,设置毛坯使用JobSetup(工件设置中的设置大小,同时打开UseTrueSolid(使用真实实体及Removechips(除去片方式,实体模拟设置如图25.13所示(本章实例均使用这样的设置。
·436·
图25.10
图25.11
(a
(b
图25.12
图25.13
的文字。
·437·
(5单击工具栏中的(开始按钮,开始实体模拟,实体模拟结果如图25.14所示,同时菜单区出现图
25.15
所示的废料显示子菜单,用于对切割后的废料进行去除以方便观察。
图25.14
图25.15
(6单击图25.15所示菜单中的Pickachip(选择片,在绘图区中单击型腔中间产生的废料,得到如图
25.16所示的型腔实体模型。
图25.16
注意:
此处的Pickachip操作需要执行两次,因为除型腔中间的整体废料外,在圆弧进入
和直线退出中间还有一段小的废料也需要进行这种操作来去除显示,才能最终得到图25.15所示的效果。
通常先去除进刀圆弧产生的小废料的显示,再去除型腔中大废料的显示。
最终的模拟图形模拟的是不带刀具补偿的切割路径,因为在切割参数设臵中我们选择的是控制器补偿方式,读者需要注意这一点。
(7选择菜单区中的Done(执行命令退出,再单击实体切割工具栏右上角的按钮退出实体切削模拟对话框,返回到图25.12所示的操作管理对话框中。
25.1.4后置处理生成程序
(1从操作管理对话框中单击Post(后置按钮,进入后处理设置界面中,确认当前的后处理程序为MWPROBO,保持其他设置值不变,如图25.17所示,单击OK按钮。
(2在弹出的文件写入对话框中输入产生的程序名称,单击“保存”按钮。
系统创建并在程序文件编辑器中自动调出CMD文件,如图25.18所示,其中所用的ISO文件同时被创建。
图25.17图25.18
注意:
在图25.18所示的CMD文件中,GOH值的高度与工件高度HPA一样,通常在加工时上机头的高度根据实际工件高度及装夹情况来直接调整,因此这里不需要GOH值,应该将其去掉。
但是读者要清楚这里的值是由图25.5所示对话框中的UV高度和UV修剪面高度来确定的。
(3删除GOH代码行,根据零件的配合间隙加入CLE指令设定所需的偏移,将文件保存,CMD文件创建成功。
技巧:
保存前,在REXE502代码行前加入一行指令“OSP,0”;它的含义为取消选项停止功能,这样在NC文件中就可以设臵选择性停点,使切割加工在第一次完成时暂停以便取废料,在第二、三次切割中忽略停点。
(4在程序编辑器中调入创建的NC代码文件,如下所示:
%(EX25-1x
N100G92G60X0.Y0.W0.H11.R11.
N102M20
N104M06
N106G29
N108G01X.94284Y.28284
N110G42D0
N112G28
N114G02X1.06Y0.I.66J0.A.75
N116G01Y-1.06
N118G02X.94Y-1.18I.94J-1.06
N120G01X-.94
N122G02X-1.06Y-1.06I-.94J-1.06
N124G01Y.82
N126G02X-.935Y.9399I-.94J.82
·438·
的文字。
N128G03X-.81Y1.05979I-.93J1.05979
N130G01Y4.2
N132G02X-.69Y4.32I-.69J4.2
N134G01X.69
N136G02X.81Y4.2I.69J4.2
N138G01Y1.05979
N140G03X.935Y.9399I.93J1.05979
N142G02X1.06Y.82I.94J.82
N144G01Y0.
N146G40
N148G27
N150X0.A0.
N152/M12
N154M02
在N100行中的3个参数含义如下。
●W:
参考面到工件底面的高度,通常指编程平面到零平面的高度。
●H:
切割高度,通常指工件厚度。
●R:
参考面和第二平面的距离。
提示:
在锥度切割中,通常在XY平面进行绘图,通过在NC代码修改W的高度来设臵程序平面的高度。
在本例中由于工件高度为13mm,同时要求的直壁部分为2mm,因此我们的程序平面高度为11。
在有些后处理器生成的程序中会在第1行出现G70代码,这是代表英制单位。
如果有这类代码出现在机床上,做加工前绘图检查时就会产生错误,需要将其删除。
技巧:
在N144的代码行后加入选择性暂停指令M01,可配合CMD文件中的OSP设臵功能实现停点,在第一次切割时有效以便移除废料。
(5将NC文件的第一行代码改为:
N100G92G60X0.Y0.W11
在第N144代码行后加入:
N145M01
删除N152代码行(此代码为剪丝指令,在型腔切割中不需要。
将修改后的NC文件保存。
至此斜度程序编制完毕。
(6直壁部分的切割按上述步骤进行,请读者自行编制,注意以下几点:
●在Contour选项卡中不再设置锥度切割。
●在Cuts选项中修改切割次数为所需的次数。
提示:
直壁部分的切割可以不考虑编程平面的高度设臵,加工厚度有关的工艺文件在机床
·439·
·440·
中生成。
按照本例中斜度的切割方法生成程序并修改,完成直壁部分的切割。
这样通过两个程序完成了对凹模型腔直壁和斜度部分的加工。
提示:
在实际工作中,由于斜度和直壁部分的ISO代码中切割路径一样,区别仅在于高度
和斜度的设臵,因此通过在斜度加工的程序代码中取消锥度设臵,即可将锥度加工的ISO文件作为直壁加工的ISO程序,从而得到简化程序编制过程的效果。
读者可自行对这种方法进行验证。
至此本实例的型腔程序完成,可依次使用其对5个型腔进行加工,型腔的斜度加工读者可参考配套光盘中的EX25-1X.mc9文件。
25.1.5外形切割的程序编制
(1从操作管理对话框中右击型腔切割路径,按图25.19所示的菜单将切割路径的显示关闭,再返回到主菜单中。
图25.19
(2选择辅助菜单中的STCW命令,将Startposition、Threadposition、Cutposition的位置设置到图25.1中的P1点上,STCW位置点设置对话框如图25.20所示,单击OK按钮确定。
(3从主菜单中选择Modify→Break→2pieces(“修整”→“打断”→“两段”命令,选择图25.1中指示的留磨面的直线,再单击P1点作为打断点,将此直线在P1点处分为两段,此分段点将作为外形串连的起点,同时也是外形切割路径的进刀位置。
(4从主菜单中选择Wirepaths→Contour(“线切割”→“轮廓”命令,进入切割路径的串连选择菜单中,从图25.3中单击分段直线在P1点右侧的部分,串连方向按顺时针方向,完成图形串连,如图25.21所示。
的文字。
图25.20
图25.21
(5然后在提示选择第二串连时单击主菜单中的Done(执行命令,完成切割路径的选择,同时弹出切割设置的对话框,如图25.22所示。
图25.22
为方便观察,将电极丝直径设置为0.5mm。
(6单击Contour标签进入轮廓设置选项卡中,同时设置UV平面及UV修剪面的高度值为13.0mm,在补偿设置中设置控制器补偿方式,补偿方向为左偏移,如图25.23所示。
图25.23
(7单击Leadin/out(导入/导出标签进入导入/导出设置选项卡中,设置进入退出方式均为直线,如图25.24所示。
图25.24
的文字。
(8单击Cuts标签进入切割方式设置选项卡,选中Performroughcut(进行粗加工复选框,然后设置精加工次数为两次。
接着选中Tab(分离复选框,设置分离段宽度值为25.0mm,切割次数为一次,这时在右下角会看到一次粗加工、两次精加工的加工方法以及分离段的分离切割。
精加工设置如图25.25所示。
图25.25
(9单击General标签进入通用功能设置选项卡,设置切割方向为Reverse正逆切割,保持其他设置不变,如图25.26所示,单击“确定”按钮结束设置。
图25.26
(10绘图区中出现设置完成的切割路径,如图25.27所示,从中可以明显地看到在正逆切割中电极丝的偏移方向是否正确,可以使用操作管理对话框中的Backplot功能对运动情况进行模拟。
图25.27
25.1.6实体模拟加工
(1接着进行实体切削模拟,这时需要重新设置毛坯的大小。
从主菜单中选择Wirepaths→Jobsetup(“线切割路径”→“工件设置”命令,进入图25.13所示毛坯工件的设置对话框中,单击Selectcorners按钮返回到绘图区中,在生成切割路径的图形左上和右下任意选取两点作为毛坯的边界,此两点数据返回到设置区中,在Z高度设置和毛坯原点的Z值文本框中均输入数值13,选中Displaystock选项,单击OK按钮确定,毛坯显示如图25.28所示。
(2从主菜单中选择Wirepaths→Operations(“线切割”→“操作”命令进入图25.12所示的操作管理对话框中,单击SelectAll按钮将型腔的斜度切割一起选择,然后单击Verify(校验按钮,进入实体切削模拟对话框,同时弹出实体模拟工具栏。
单击工具栏中的
按钮,进入切削设置界面中,按照步骤(前面所示的方法进行设置。
在模拟工具栏中单击(开始按钮,开始实体模拟,同时菜单区出现图25.15所示的子菜单,将型腔和外形废料去除后得到模拟结果,如图25.29所示。
图25.28图25.29
的文字。
25.1.7后置处理生成程序
(1从操作管理对话框中选择外形切割程序,然后单击Post(后处理按钮,系统出现图25.30所示的提示信息,指出后处理不是对所有切割路径进行的,单击“否”按钮继续,仅对外形切割进行后处理操作,进入后处理设置选项卡中,确认当前的后处理程序为MWPROBO,保持其他设置值不变,如图25.17所示,单击OK按钮。
图25.30
(2生成的CMD程序如图25.31所示。
图25.31
(3现在对程序进行检查修改,在CMD程序中可以看出使用了3个ISO代码程序,分别如下:
外形正切割:
EX25-1x.iso
外形逆切割:
EX25-1xAA.iso
分离段切割:
EX25-1xAB.iso
其中在CMD文件中将GOH命令行取消,在ISO文件中将“G70,M12”代码取消,即完成程序编制。
切割时执行过程为:
先调用EX25-1x.iso程序进行第一次粗加工,偏移方向为左侧,然后使用EX25-1xAA.iso程序以右侧偏移反向加工回起点,再以EX25-1x.iso程序进行一次正向加工,然后以EX25-1xAB.iso程序将分离段切除。
注意:
分离段的偏移值需要根据零件加工的留磨情况进行设臵,具体方法为:
在CMD文件中的分离切割前加入CLE命令行指定一个偏移值。
生成的CMD中的程序名称和ISO代码的名称根据绘图时的文件名而自动给定,因
此读者在练习过程中,文件名可能会与图示中不一致,但是命名规律是一致的,即按照第一次正向加工为文件名,逆向加工加上后缀AA,分离段切割加上后缀AB。
技巧:
为了尽量减小无用的加工路径,提高效率,可以采用以下方法对程序进行一些改进:
①在本例中可以看到,起始点与外形间的距离值为2mm,在CMD文件中对正向的
切割路径使用一个ISO代码程序,然后将ISO代码中正向切割的退出点设臵到距离外形路径0.3mm处,将逆向切割的起始点也设臵到距离外形切割0.3mm处的同一点上,可以最大程度地提高效率,减少无用加工。
②将CMD文件中的分离切割取消,在第三次切割完成后,直接用粗加工工艺参数
以手工方式加工到外形路径的起始位臵,以达到切断并留磨的目的,可以提高一定的生产效率。
外形加工的程序读者可参考配书光盘中的EX25-1W.MC9文件。
25.2凸模加工(留料策略
本实例是由一个级进模中的凸模改编而成的,对其进行切割编程,主要是继续学习分离段在加工中的使用方法,根据图形形状,将分离段部分设置在图形上部,对图形进行往返5次切割,最后的分离段一次切下,再使用后续加工方法对其进行加工,由于图形较小,为观察方便设其高度为1mm。
本节详细介绍分离段在异形凸模零件切割中的编程方法。
在图25.32中L1直线为留磨边。
L1
图25.32
25.2.1文件准备
(1从系统桌面双击Wire程序快捷方式启动软件。
(2从主菜单中选择File→Get(“文件”→“获取”命令,调入EX25-2.MC9文件。
(3从主菜单中选择NCutils→PostProc→Change(“NC实用”→“后处理”→“改变”命令,弹出SpecifyFileNametoRead对话框,在其中选择MPWROBO.PST后处理程序,如图25.2所示,单击“打开”按钮返回,再单击MAINMENU(主菜单命令返回主菜单。
(4从主菜单中选择Create→Point→Position→Relative(“创建”→“点”→“位置”·446·
的文字。
·447·
→“相对点”命令,出现参考点的点输入菜单,从中以自动捕捉方式选择图形左上角的参考点,出现相对点的两种创建方法:
直角坐标方式和极坐标方式,选择Rectang(直角坐标命令,在弹出的坐标文本框中输入相对坐标值(0.5,1.5,创建P1点,位置点标识如图25.33所示。
P1L1
参考点
图25.33
(5从主菜单中选择Modify→Break→2pieces(“修整”→“打断”→“两段”命令,选择图25.33中的L1直线,再单击刚创建的P1点将其作为打断点,将L1直线打断成两段,此分段点将作为串连的起点,同时也是切割路径的进刀位置。
25.2.2生成切割路径
(1选择辅助菜单中的STCW命令,弹出如图25.20所示的STCWParameters参数设置对话框,从中单击SelectStart/Thread/Cut按钮,选取图25.33中的P1点,设置它同时作为起始点、穿丝点及剪丝点,STCW位置点设置如图25.34所示,单击OK按钮确定。
(2从主菜单中选择Wirepaths→Contour(“线切割路径”→“轮廓”命令,进入切割路径的串连选择菜单中,单击绘图区中图25.33所示的图形中L1
直线打断的左侧部分,按逆时针方向进行串连,结束后在图中出现代表串连的箭头标志,串连切割路径如图
25.35所示。
图25.34图25.35
(3在系统提示选择第2个串连路径时,选择菜单区的Done(执行命令,进入切割设
置对话框中。
按照25.1.2节中步骤(6的方法设置电极丝直径为0.05mm,保持Leadin/out选项卡中的设置值不变,在Contour选项卡中将UVTrimPlane和UVHeight的值设为5mm以便利于观察,如图25.36所示。
(4单击Cuts标签进入切割方法设置选项卡中,打开Performroughcut(进行粗加工选项,并设置精加工次数为4次。
选中Tab(分离复选框,在Tabwidth(分离宽度文本框中设置分离段的宽度为1.8mm,设置Numberoftabcuts(分离切割次数为1次,并确保在分离段加工时会输出停点选项,如图25.37所示。
图25.36
·448·
的文字。
·449·
图25.37
(5单击General标签进入通用参数设置选项卡,在切割方式中设置反向切割Reverse选项有效,保持其他设置值不变,如图25.38所示。
(6单击对话框下方的“确定”按钮,系统退出设置,提示对切割路径上的点进行修改,直接选择菜单区的Done(执行按钮,完成编程,生成的路径如图25.39所示。
图25.38图25.39
25.2.3实体模拟加工
(1从主菜单中选择Wirepaths→Jobsetup(“线切割路径”→“工件设置”命令,进入如图25.10所示的毛坯工件的设置对话框中,单击Selectcorners按钮返回到绘图区中,在图形的左上和右下任意选取两点作为毛坯的边界,此两点数据返回到设置区中,在Z高度设置和毛坯原点的Z值文本框中均输入数值5,选中Displaystock复选框,单击OK按钮确定,如图25.40所示。
图25.40
(2从主菜单中选择Wirepaths→Operations(“线切割路径”→“操作”命令,进入操作管理对话框中,单击其中的切割路径,然后再单击Verify(校验按钮,进入实体切割模拟
·450·
的文字。
环境中。
(3直接单击实体切割模拟工具栏中的(开始按钮,开始实体模拟,如图25.41所示,同时菜单区出现图25.15所示的子菜单,用于对切割后的废料进行去除以方便观察。
(4单击图25.15中的Pickachip(选择片命令,选取图24.41中的废料(注意是外面的部分,完成后实体模拟的结果如图24.42所示。
图25.41图25.42
(5选择菜单区中的Done(执行按钮,再关闭实体切割模拟工具,返回到操作管理对话框中。
25.2.4后置处理生成程序
(