复合材料实训报告.docx
《复合材料实训报告.docx》由会员分享,可在线阅读,更多相关《复合材料实训报告.docx(9页珍藏版)》请在冰豆网上搜索。
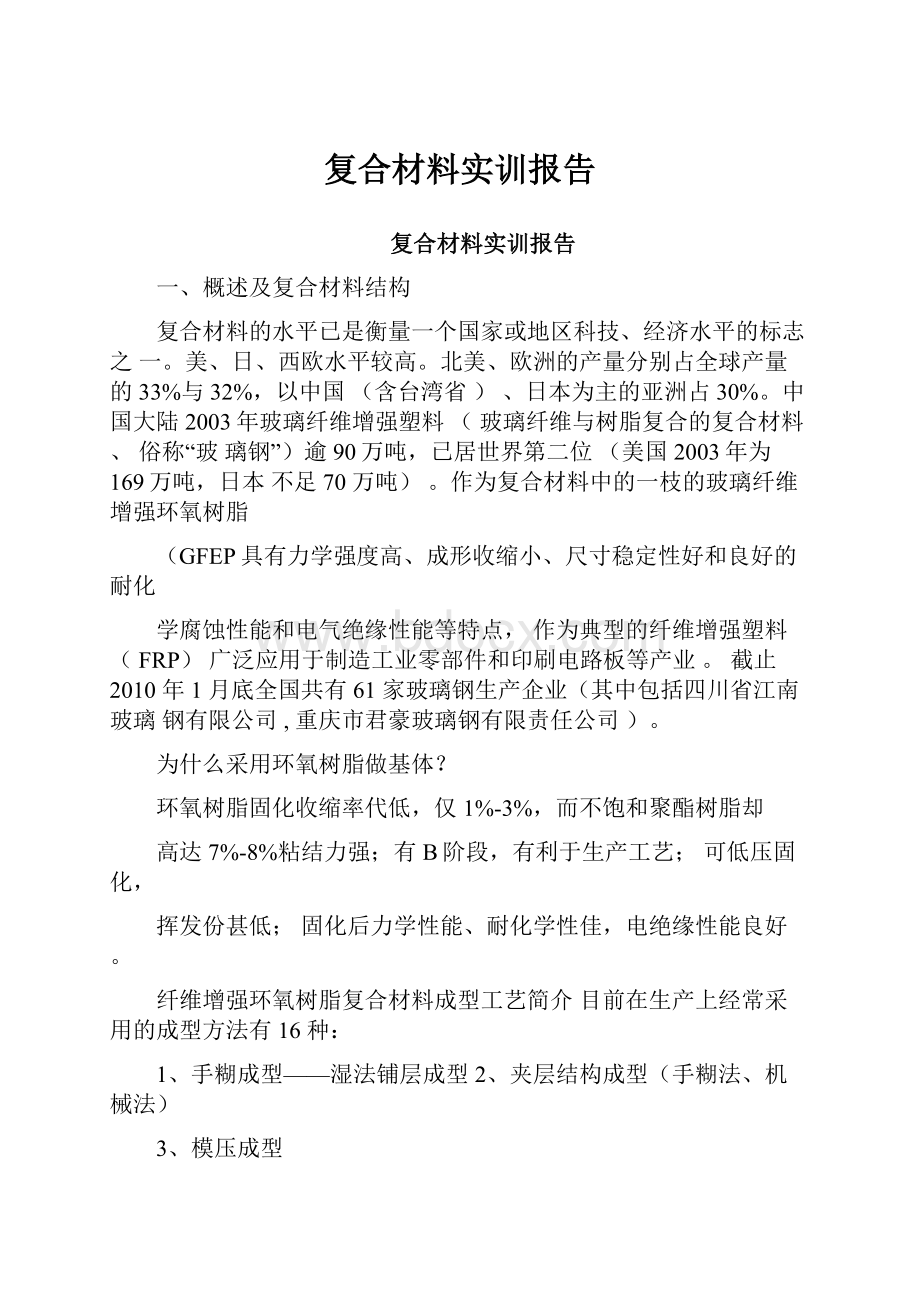
复合材料实训报告
复合材料实训报告
一、概述及复合材料结构
复合材料的水平已是衡量一个国家或地区科技、经济水平的标志之一。
美、日、西欧水平较高。
北美、欧洲的产量分别占全球产量的33%与32%,以中国(含台湾省)、日本为主的亚洲占30%。
中国大陆2003年玻璃纤维增强塑料(玻璃纤维与树脂复合的复合材料、俗称“玻璃钢”)逾90万吨,已居世界第二位(美国2003年为169万吨,日本不足70万吨)。
作为复合材料中的一枝的玻璃纤维增强环氧树脂
(GFEP具有力学强度高、成形收缩小、尺寸稳定性好和良好的耐化
学腐蚀性能和电气绝缘性能等特点,作为典型的纤维增强塑料(FRP)广泛应用于制造工业零部件和印刷电路板等产业。
截止2010年1月底全国共有61家玻璃钢生产企业(其中包括四川省江南玻璃钢有限公司,重庆市君豪玻璃钢有限责任公司)。
为什么采用环氧树脂做基体?
环氧树脂固化收缩率代低,仅1%-3%,而不饱和聚酯树脂却
高达7%-8%粘结力强;有B阶段,有利于生产工艺;可低压固化,
挥发份甚低;固化后力学性能、耐化学性佳,电绝缘性能良好。
纤维增强环氧树脂复合材料成型工艺简介目前在生产上经常采用的成型方法有16种:
1、手糊成型——湿法铺层成型2、夹层结构成型(手糊法、机械法)
3、模压成型
4、层压成型
5、缠绕成型
6、拉挤成型
7、注射成型
8、喷射成型
9、真空袋压力成型
10、压力袋成型
11、树脂注射和树脂传递RTM模塑成型
12、卷制成型
13、真空辅助注射成型
14、离心浇铸成型
15、片状smc(团状bmC模塑成型
16、连续板材成型
目前我国还是以手糊成型为主,在树脂基复合材料中约占80%。
(一)、手糊成型(handlayup)
概要
1.定义:
玻璃钢成型加工成型工艺,以手工方式或简单工具辅助铺放增强材料浸渍树脂成型玻璃钢制品的一种工艺方法。
2.玻璃钢成型工艺:
手糊为最基础的成型工艺,此外据我了解有RTM模压、层压、
SMCBMC拉挤、喷射等。
⑴手糊成型工艺特点:
1低压接触成型。
人工成本低,手糊在我国所占的市场份额较发达国家高。
(2)主要原材料:
①树脂:
a.不饱和聚酯树脂(UP)196#(通用牌号)
191#195#(透明制品)
33#34#(胶衣树脂,耐热)b.环氧树脂E42E44616618c.乙烯基树脂d.酚醛树脂由于对生产者身体伤害较大,一般不用于手糊。
2增强材料:
玻璃纤维主要选用无碱及中碱玻纤,高模及高强玻纤也有选用。
水泥基复合材料一般用高碱玻纤。
织物形态:
玻璃布、表面毡、针织毡、复合毡。
3助剂:
用量少,但有重要作用。
a.固化剂:
过氧化物,如过氧化甲乙酮、过氧化二苯甲酰。
b.促进剂:
促进反应,如萘酸钻(环烷酸钻)、环己酮。
例如不饱和
聚酯与苯乙烯单体加入过氧化甲乙酮促使反应发生,使反应物由液态变为固态。
4添加剂:
a.填料:
降低成本,降低树脂固化收缩,改善树脂性能。
b.触变剂:
利用分子间粘合力。
c.增稠剂:
增加树脂粘度,利于固化。
d.增韧剂:
增加树脂韧性,降低脆性。
e.抗紫外线添加剂
f.低收缩添加剂:
降低树脂收缩率。
(3)手糊成型玻璃钢过程:
总体过程:
原材料准备、模具加工制作、产品成型、后处理③工艺条件:
a.铺层
b.根据树脂固化配方,控制凝胶时间。
最佳凝胶时间:
成型操作后30min左右。
控制方法:
调整固化剂、促进剂用量。
c.对环境要求:
温度》15C,湿度w75%
d.后处理(后固化处理为主):
80士5C,处理8小时。
II、参观手糊成型车间:
1.手糊车间:
⑴模具制作:
①打磨:
在模具基本成型后,要对其表面进行打磨处理(阴模打磨
内表面,则相应产品外表面光洁度高;阳模打磨外表面,则产品内表面光洁度高)。
一般采用人工打磨,用砂纸对表面进行处理。
砂纸选用顺序由粗到细,以逐步提高表面光洁度,如可用200—400—600—800目的顺序,2000目以上即可进行抛光处理。
2表面毡:
薄,约30~50g/mA2.
3腻子:
填料加固化剂组成。
⑵手糊产品生产:
在模具表面涂脱模剂后涂刷树脂铺放玻璃布,再涂刷树脂浸渍玻璃布,如此反复,直至需要厚度。
固化后脱模,对产品进行机加工至所需要求。
学习及参观感受:
深入了解了手糊的工艺过程。
手糊成型生产效率低,劳动强度大,成型周期长,且树脂中有害成分挥发使操作间内气味较大,对工人身体造成伤害。
但由于我国劳动力成本低,因此手糊成型在我国复合材料制造中占有很大比重。
随着技术发展,相信我国的复合材料及相关产业会加大科技含量,改善目前状况。
依次在模具表面上施加脱模剂、胶衣一层粘度为0.3-0.4PaS的中等活性液体热固性树脂(须待胶衣凝结后)一层纤维增强材料,纤维增强材料有表面毡、无捻粗纱布(方格布)等几种。
以手持辊子或刷子使树脂浸渍纤维增强材料,并驱除气泡,压实基层。
铺层操作反复多次,直到达到制品的设计厚度。
树脂因聚合反应,常温固化。
可加热加
速固化2、手糊成型工艺的优点:
1)、不受尺寸、形状的限制;
2)、设备简单、投资少;
3)、工艺简单;
4)、可在任意部位增补增强材料,易满足产品设计要求;
5)、产品树脂含量高,耐腐蚀性能好。
3、手糊成型工艺的缺点
1)、生产效率低,劳动强度大,卫生条件差;
2)、产品性能稳定性差;有些树脂有害健康
3)、产品力学性能较低。
4、手糊制品为什么要在表面覆盖聚酯薄膜?
自由基与苯乙烯的反应速度比自由基与02的反应速度慢104倍,一般聚酯树脂制品固化时,表面应覆盖聚酯薄膜。
若不用薄膜覆盖,也应使成型表面形成与空气隔离的物质如蜡类,否则自由基与周围空气中的02、H20反应,耗去大部分自由基,造成表面固化不完全而发粘
5、手糊成型易发生的缺陷及防止措施
1)、制品表面发粘
原因1:
空气湿度太大,水对树脂起阻聚作用
解决办法:
(1)在树脂中加入0.02%左右的液体石蜡;
2)在树脂中掺加5%的异腈酸酯
3)制品表面覆盖薄膜隔绝空气;
原因2:
引发剂、促进剂的比例弄错或失效,更换引发剂、促进剂。
2)、制品内气泡太多
原因1:
用量过多树脂解决办法:
1、控制胶含量2、注意拌合方式原因2:
树脂粘度过大解决办法:
1、适当增加稀释剂2、提高环境温度
原因3:
增强材料选择不当解决办法:
选用浸透性好的无捻玻璃布
3)、流胶
树脂粘度太小,可加入2〜3%的活性氧化硅。
配料不均匀,充分搅拌。
固化剂用量不足,适当调整固化剂用量。
二、复合材料的模压成型:
1.特点:
操作方便,容易成型,通过改变原料配比改变产品性能。
成型性好,成型后不需后序加工。
2.SMC片材成型原材料:
⑴树脂:
不饱和聚酯,苯乙烯稀释。
若用于食品制品(如水箱),苯乙烯含量要低,粘度要低(易于浸渍树脂),增稠快(不易粘手,易于进行下一道工序),活性高(快速固化),耐高温(成型温度高),耐水性好(易于增稠),储存稳定性好。
⑵引发剂:
模压成型过程中使树脂、苯乙烯聚合成型。
要求:
储存性好;根据温度不同选择引发剂,如手糊选用低温引发剂,模压选择高温引发剂;模具中流动性好;反应性高(模压过程中迅速与树脂反应)。
⑶填料:
一般为粉末状,如CaCO、3Al(OH)3、高岭土、玻璃珠等,可降低产品成本。
若用于阻燃,可选Al(OH)3(高温时生成水);填料若吸油值高,对树脂需求量大,且较稠,不易浸渍树脂;提高耐磨性、导电性可加入较硬填料(硅粉)或金属粉末、导电剂(如铝粉);若减轻重量,可加空心微珠;若要提高流动性,可加高龄土。
⑷低收缩添加剂:
防止制品收缩变形大、翘曲(树脂一般为热固性,变形大,加入低收缩添加剂—热塑性树脂,可使树脂变形小,且使制品易着色,改善制品外观)。
⑸化学增稠剂:
浸渍过程增稠慢,一般不起作用,当加热至35〜40C时,需很快增稠至模压需要粘度,一般选用CaMg的氧化物、氢氧化物。
⑹内脱模剂:
防止粘模,避免每次模压时涂外脱模剂。
需低于模压
温度熔化析至产品表面,一般选熔点120〜130C(模压温度140〜150C)的硬脂酸盐类(如硬脂酸锌);若产品较厚,可选熔点70〜80C(硬脂酸)。
⑺着色剂:
色浆,饱和聚酯树脂(防止凝固)。
颜料需耐高温,无毒性,耐晒,着色力强。
若不加,则制品显示填料颜色。
若产品颜色
不均,加入润饰剂(防花剂);部分颜料导电(如炭黑),在制作绝缘产品时避免使用。
⑻增强材料:
主要为纤维,对树脂糊浸渍性好,切割性好。
⑼阻聚剂:
在使用黑色色浆时,需加入(黑色吸热,温度高,易自聚),氢醌类。
⑽降粘剂:
润滑分散剂。
根据对产品要求的不同,表面经过不同处理(喷漆前需打磨,否则表面光滑易掉漆)。
⑵模压过程:
1加料:
加在薄膜中间,给片材流动的空间,一般加料量二体积X1.8(片材大致比重,在1.6〜2.0之间适当增减)。
2成型时模具温度要求:
取决于固化体系的情况(引发剂作用时温度高低、产品薄厚)。
3成型压力:
简单制品压力可适当减小,易充模,制品可达到要求;复杂制品需较大压力充模。
4保温时间(固化时间):
按固化体系、制品薄厚确定。
一般薄制品30〜40s/mm。
5后处理:
磨边、打孔等,对不影响制品的缺陷(针眼、气孔)进行修补。
对气孔的处理:
注射器注入树脂,固化后用细砂纸(800〜1200目)打磨。
室温固化
学习参观感受;各种不同的成型工艺需要有不同的原料配制。
模压成型温度高,成型周期短,但车间的溶剂挥发对工人身体造成伤害,可从改善通风设备及研究无毒溶剂入手进行解决。
拉挤车间通风较差,不过味道相对较小,生产出的格栅(工字钢+玻璃钢棒)强度比预想的要强得多,可见复合材料强度不可小看。
但切割及钻孔时粉尘很大,应研究湿法切割。
总体来讲,设备自动化程度不算高,有改进空间。
一周的复合材料实训很快就过去了。
实习时间虽然短暂,学到的专业知识和技能也是沧海一粟,但认真总结反思,收获也不少,主要内容见实习过程。
在这周中我们先做了环氧树脂加强玻璃纤维的复合材料板,随后自己制作模型,本来是做个漏斗,但是因为锥形不好铺制玻璃纤维,同时还得在锥形顶端开口而宣告失败。
我们将这个作品改为了一个草帽,实验结果还不错。
通过这周的实训我觉得自己主要有两大心得体会。
第一,一个人要活到老、学到老。
知识海洋无止境,创新风光无限。
实习期间给我们讲解的老师对自己的专业精通,讲解流利且带有幽默。
厂里的优秀员工是我们的榜样,他们兢兢业业,在工作中善于发现问题并努力解决问题。
我们毕业生无论以后读研深造还是走上工作岗位,都要谦虚好学,努力掌握专业技能,不断追求进步!
只有这样,我们才能不断提高自己,做一个有为之人!
第二,第二,学以致用、造福人民。
我们学到的课本知识仅仅是理论
知识,有时并不符合实际,需要实践来检验。
通过两者的有效结合,我们方能把学到的知识应用于实际生产应用。
在实习期
间,每次走进大门时,“航空报国、强军富民”的八个大字引入眼帘,震撼心灵。
一个人如果紧紧为了自己的利益而努力,很难有大作为。
把造福人民作为自己内心最崇高的追求,作为自己不断前进的最根本动力。
今后两三年,我应该会在南京
航空航天大学读研,目前在准备复试。
读研也是提高自己本领的途径,为以后走向工作打下良好的基础