带侧孔塑料盖注射模设计.docx
《带侧孔塑料盖注射模设计.docx》由会员分享,可在线阅读,更多相关《带侧孔塑料盖注射模设计.docx(25页珍藏版)》请在冰豆网上搜索。
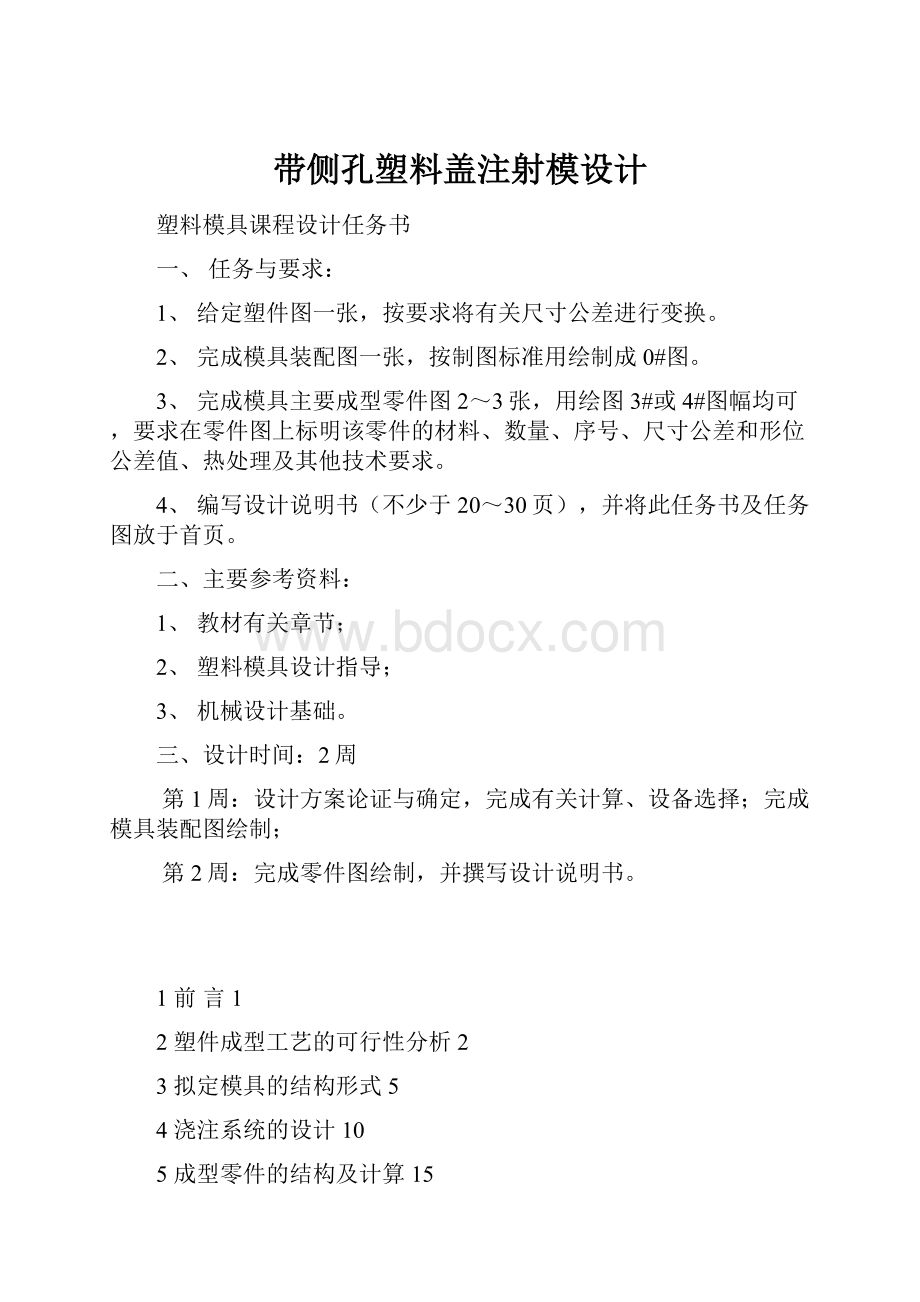
带侧孔塑料盖注射模设计
塑料模具课程设计任务书
一、任务与要求:
1、给定塑件图一张,按要求将有关尺寸公差进行变换。
2、完成模具装配图一张,按制图标准用绘制成0#图。
3、完成模具主要成型零件图2~3张,用绘图3#或4#图幅均可,要求在零件图上标明该零件的材料、数量、序号、尺寸公差和形位公差值、热处理及其他技术要求。
4、编写设计说明书(不少于20~30页),并将此任务书及任务图放于首页。
二、主要参考资料:
1、教材有关章节;
2、塑料模具设计指导;
3、机械设计基础。
三、设计时间:
2周
第1周:
设计方案论证与确定,完成有关计算、设备选择;完成模具装配图绘制;
第2周:
完成零件图绘制,并撰写设计说明书。
1前言1
2塑件成型工艺的可行性分析2
3拟定模具的结构形式5
4浇注系统的设计10
5成型零件的结构及计算15
6脱模推出机构的设计20
7侧向分型与抽芯机构的设计23
8模架的确定28
9排气槽的设计29
10冷却系统的设计30
11导向与定位机构的设计32
参考文献33
致谢34
1前言
塑料产业是如今世界上增长速度最快的产业之一,然而注塑模具是其最重要的组成部分,也是其中发展较快的类型。
由于塑料成型技术的不断发展,塑料制品因为重量轻、价格不贵、生产方式简单方便的好处已经进入到了人们日常生活中的每个角落现在,除了几种塑料制品,塑料注塑成型方法是相当好的选择。
更据科学统计,注射产品的数量大约占全部塑料产品总产量的30%,每年全世界生产的注射模数量大约是全部塑料成型模具数量的50%。
早期的注射成型方法主要是用在生产热塑性塑料产品,由于塑料工业的极速发展和塑料产品的推广应用范围在不断地扩大,现在的注射成形方法已经开始应用到了热固性塑料制品和一些塑料复合材料制品的生产中。
注射成型方法不仅广泛应用于通用塑料产品生产,而且就工程塑料而言,它也是一种极重要的成型方法。
根据科学统计,就目前的工程塑料产品而言,使用注射成型的生产方法就已经达到了80%。
我国塑料模具工业从开始进入我们的生活到现在,已经多达了50年之久,并且取得了一定程度的成就,注塑模的设计与制造水平也有了相当大的提高。
在模具市场中的总体趋势呈现稳步向上,模具市场在不久的将来,塑料模具的增长速度将高于其它模具,它占据在模具行业的比例也将逐渐增加。
然而,我国在此方面基础相对薄弱,对引进技术的同化、把握,尚有一段距离,而且发展不稳定。
因此,中国整体的注塑模具及相关国家的水平采用先进的技术在世界上是有显著的差距。
现今技术在塑料模的设计制造领域上应用已经越来越普遍,特别是技术的应用已经相当广泛,并取得了明显的成绩。
因为电子信息工程技术的发展更深一步提高了塑料模的制造设计和制造水平,这不但减少了生产前的准备时间,而且还为扩大模具出口创造了条件,从而达到减少模具的设计和制造周期。
2塑件成型工艺的可行性分析
2.1塑件的分析
(1)外形与尺寸
该塑件测壁的厚度为2.5~3,外形尺寸不是很大,塑件材料为,即聚乙烯,具有相对较好的流动性与热塑性,适合注射成型。
(2)精度等级
由图可知,该塑件的各部分精度等级不一,除了部分公差尺寸是给定的,其余未标注的尺寸取公差等级均取5级。
(3)脱模斜度
材质有很好的成形性能,比较大的成型收缩,查参考文献可选择塑件型芯与凹模的统一脱模角度为40’。
2.2材料工程塑料的性能分析
材料的基本性能:
(聚乙烯)化学性能比较好,耐水性好,但是却以强氧化剂发生反应。
高密度聚乙烯()强度、刚性、硬度和熔点较高,吸水性相对较小,电气性能和耐辐射性良好。
低密度聚乙烯()材质较软、伸长率、冲击韧性和透明性相对较好。
2.3材料的注射成型过程和工艺参数
(1)注射成型过程
1)成型前准备。
检查材料的粒度、色泽和均匀度,并对材料进行干燥,处理温度不能高于55℃,干燥约2h。
2)注射过程。
注射过程是由塑料转变为塑件的重要阶段,分为加料、塑化、注射、保压、冷却、脱模六个过程。
3)塑件的成型后处理。
塑件注射成型之后,需除去浇口凝料,打磨毛刺,并进行调试处理和退火处理。
退火处理的方法为放入热水中浸泡,处理时间为24h。
3拟定模具的结构形式
3.1分型面位置的确定
根据分型面选择的原则,并通过对该塑件的结构形式进行分析,分型面应该选在端盖截面积最大并且利于开模去除塑件的底平面上,如图2所示。
图1分型面的选择
3.2型腔数量和排位方式的确定
(1)型腔数量的确定
该塑件的精度不高,并且塑件尺寸较小,为大批量生产,所以可采用一模多腔的结构形式。
同时,考虑到经济成本和模具尺寸的问题,以及该塑件有两个对称的侧孔问题,初步定为一模两腔的结构形式。
(2)型腔的排列形式
该模具确定为一模两腔的形式,则使用如图3排列形式。
图2型腔数量的排列布置
(3)模具结构形式的初步确定
从上面的分析结果得出,模具设计可以设为一模两腔,分析塑件的基本结构和形状,可以确定推出机构可以选择推板推出或者推杆形式推出。
浇注系统的设计,取对称平衡的流道形式,采用侧浇口并且设在分型面。
开模具方向与孔不一致,故采用侧向分型抽芯机构,方便侧孔的成型与脱模。
从上面的综合分析初步可确定为单分型面的注射模并采用带推件板的。
3.3注射机型号的确定
(1)注射量的计算
分析利用三维建模可以得出塑件质量属性如图3所示。
图3塑料盖的质量属性
塑件体积:
=11.067
塑件质量:
=11.067
0.95=10.514
,式中
据参考文献取0.95
。
(2)浇注系统凝料体积的初步计算
在设计之前浇注系统凝料无法确定其确切数值,但按照塑件的体积为0.2倍~1倍估算经验的基础上进行加工。
因为这个流道的设计不是很长,较为简单,所以用0.3倍的浇注系统凝料来计算塑件的体积。
所以得出塑料熔体一次性注入模具型腔的总体积是:
=1.3x2x10.514=27.300
(3)注射机的选择
根据以上计算得出,注入型腔内的塑料熔体总体积约为27.3
,由参考文献得:
27.3/0.8=34.2
由以上计算分析,可选用公称注射量为60
,注射机型号为60注射机,其主要技术参数如表2。
表2注射机主要技术参数
技术参数
指标
技术参数
指标
理论注射量/
60
拉杆空间
190x300
螺杆柱塞直径
38
移模行程
180
注射压力
122
最大模具厚度
200
注射时间
1.2
最小模具厚度
70
塑化能力·h
5.6
锁模形式
液压-机械
注射方式
柱塞式
锁模定位孔直径
55
锁模力
500
喷嘴球半径
12
喷嘴孔直径
4
(4)注射机的相关参数的校核
注射压力校核。
查阅参考文献可以知道,材料所需要的注射压力一般为70100,这次可以取
=80。
由上述表可以知道,注射机的公称注射压力值
=122,注射压力的安全系数1.25~1.4,我们取1.3,则注射压力:
=1.3x80=104<
=122
所以,我们所选的注射机注射压力可以满足要求。
4浇注系统的设计
4.1主流道设计
一般地,我们选择主流道为垂直式主流道。
主流道是指连接注射剂喷嘴与分流道的塑料熔体通道,是熔体注入模具最先经过的一段流道,其形状、大小会直接影响到熔体的流动速度和注射时间。
(1)主流道尺寸
1)主流道的长度:
一般地,主流道的长度由模具的结构而确定,而本次设计的模具为小型的模具,其主流道长度取82。
2)主流道小端直径:
注射剂喷嘴尺寸+(0.5~1)4.5
3)主流道大端直径:
,式中,
。
4)主流道球面半径:
注射机喷嘴球头半径+(1~2)12+2=14
5)球面的配合高度:
球面的配合高度这里取3。
(2)主流道衬套的形式
注射机的喷嘴会与主流道的小端入口处反复接触产生摩擦,容易损坏,因此,其对材料选定要求相对比较严格,因而模具的主流道部分一般要求设计成可以拆卸方便更换的衬套形式,这样可以有效的选用优质的材料进行单独的加工与热处理。
主流道浇口套的结构形式如图4。
图4主流道交口套结构形式
(3)主流道当量半径
4.2分流道的设计
(1)分流道的形状及布置
此次设计的塑件含有侧孔,需要在对开方向进行侧向抽芯。
由上面可初步选定分流道的结构形式及布置如图5。
图5分流道布置形式
(2)分流道的长度
根据分流道设计原则,以及本设计的一模两腔结构设计,分流道的长度应该尽可能短,这里取长度为10。
(3)分流道的当量直径
流过分流道塑料的质量为
该塑件的壁厚在2.53之间,根据参考文献可查得
=4.6,再根据单向分流道长度20,查参考文献得修正系数为
,则修正后分流道直径为:
(4)分流道的截面形状及尺寸
一般来说分流道应采用梯形截面,因其加工工艺性好,流动阻力不大。
设梯形的上帝宽度为6,地面圆角半径1,梯形下底宽度为b,梯形高度为23=4,则提醒关系式如下。
带人各值进入计算,可得2.67,由于考虑到梯形底部圆弧对面积的减小以及脱模斜度的影响,取4,如图6所示。
图6分流道的截面形状和尺寸
(5)分流道的表面粗糙度和脱模斜度
分流道的表面粗糙度要求相对较高,一般选取
,此次设计中,取
。
另外,其脱模斜度一般在
之间,这里我们取脱模斜度为
,脱模斜度足够。
4.3浇口的设计
浇口同时也叫作进料口,是分流道和型腔之间的相连的通道,除了直接浇口外,浇口的形尺寸、状和位置对塑件性能与质量的有着很大的影响。
其作用是说从分流道过来的熔体会以很快的速度充满整个型腔,待型腔充满之后,浇口可以迅速冷却并封闭,从而避免塑料熔体的回流。
(1)侧浇口尺寸的确定
1)侧浇口的深度计算。
根据参考文献,可知侧浇口的深度h的计算公式为:
式中n为塑料成型系数,选取0.6;t为塑件壁厚,此塑件绝大部分壁厚是2.5。
根据参考文献列出的侧浇口基本尺寸,其中材料为0.5~0.7,因此,这里取0.6。
2)侧浇口的宽度计算。
可知侧浇口的宽度b的计算公式为:
式中n为塑料成型系数,材料的成型系数为0.6;A为模具凹模的内表面面积(由于塑件表面有小凸台和侧孔,此两项计算比较复杂,并且凸台和侧孔比较小,因此计算面积时忽略此两项,视为可抵消)。
3)侧浇口的长度计算。
根据参考文献,可选取侧浇口的长度
4.4冷料穴的设计及计算
冷料穴在主流道相对的动模板上,主要是用来储存熔体前锋的冷料,达到防止冷料进入模具型腔会影响制品的表面质量的目的。
本设计中因为分流道相对较短,可以不需要设置分流道冷料穴,因此只有主流道才有冷料穴。
因为该塑件表面质量要求,采用推杆推出塑件,故采用半球形拉料杆匹配的冷料穴。
开模时,利用凝料对半球形拉料杆的包紧力使凝料从主流道衬套中脱出。
5成型零件的结构及计算
5.1成型零件的结构设计
(1)凹模的结构设计
凹模又叫作阴模,它是用于成型塑件外表面的成型零件。
按照凹模的形式不同,可以将凹模分为整体嵌入式、镶拼式、组合式和整体式四种形式。
根据塑件的结构和型腔的数量以及排列形式的不同,本设计中适合采用整体嵌入式的凹模,如图7所示。
图7凹模嵌件结构
(2)凸模的结构设计
凸模又叫做型芯,它是成型制件内表面的成型零件。
凸模一般分为整体式和组合式两种。
本次设计中的塑件结构较为简单,因此采用整体式凸模,如图8所示。
图8凸模结构
5.2成型零件钢材的选用
根据对塑件的具体分析,构成型腔的整体嵌入式凹模选用P20。
凸模在脱模时也常与塑件进行摩擦,所以型芯材料选用P20钢材,进行渗氮处理。
5.3成型零件工作尺寸的计算
(1)凹模径向尺寸的计算
,相应的塑件制造公差
;
,相应的塑件制造公差
;
,相应的塑件制造公差
。
式中
为塑件的平均收缩率,根据表可知,材料的收缩率在1.5%~3.0%之间,则取其平均收缩率
取
6(下同)。
(2)凸模径向尺寸计算
,相应的塑件制造公差
。
式中
是模具尺寸修正系数,根据参考文献可知,
=0.58。
6脱模推出机构的设计
6.1脱模力的计算
由于
,所以此处可视为薄壁圆通塑件,则根据参考文献可知脱模力为:
6.2推出方式的确定
(1)采用推杆推出
1)推杆推出时推出面积。
设6的圆锥杆设置4根,那么推出面积为:
2)推杆推出应力。
根据参考文献,可取许用应力
,则
通过以上计算发现,应力偏大,推出时有顶破或者顶白的可能,为安全起见,在此不采用推杆推出。
(2)采用推杆改良杆推出
1)推杆改良杆推出时与工件接触的面积。
设10的推杆一根,推杆顶端设有一20的圆盘,那么推出面积为:
2)推杆改良杆推出应力。
根据参考文献,可取许用应力
,则:
所以,用此方法推出合格。
由于推杆改良杆两端都有端盖头,为了能使推杆改良杆能放入模具中,讲推杆分为上、下两部分,用螺钉连接紧固。
推杆改良杆和型芯及动模的形式如图9所示。
图9型芯和推杆改良杆
7侧向分型与抽芯机构的设计
7.1侧向分型与抽芯机构类型的确定
本设计中的塑件结构较为简单,则采用有机动侧向分型与抽芯机构的模具,其驱动方式通过斜导柱完成侧抽芯。
7.2斜导柱的设计
(1)斜导柱弯曲力计算
本次设计中模具侧型芯的抽拔方向和开模方向相对垂直,滑块的受力如图10所示。
图10滑块受力图
(2)斜导柱截面尺寸的确定
在斜导柱的截面形状一般采用矩形和圆形。
圆形不仅装配简单,容易制造,并且被广泛使用;矩形截面制造稍显不便,但高强度,可以承受较大的作用力。
本设计中,我们采用圆形界面的斜导柱,其直径为:
根据参考文献可选得标准导柱尺寸12.5,斜导柱台阶孔
=17。
(3)斜导柱与滑块斜孔的配合
为了保证在开模的那一刻能够有一段小空程使塑件在活动型芯未抽出之前从型腔内或型芯上获得松动,并能够使楔紧块先脱出开滑块,以避免干涉抽芯动作,斜导柱与滑块孔之间配合的单边间隙应有0.250.5。
7.3滑块、导滑槽及定位装置的设计
(1)滑块的设计
本设计中的塑件有两个很整齐的侧孔,侧型芯的仅是很小的突起,加工方便,故这里采用整体式滑块。
(2)滑块的导滑形式
滑块在滑槽内活动必须是稳定和流畅的,卡滞、跳动是不应该发生的现象。
经分析,该设计可以采用T型导轨槽实现。
如图11所示。
图11滑块的导滑槽形式
(3)滑块的导滑长度
滑块的导滑长度L至少大于滑块的宽度B的1.5倍,滑块在完成侧向抽芯后应该继续停留在导滑槽内,而且需要确保在导滑槽内的长度L不小于滑块全长的2/3。
本设计中,滑块的长度55,滑块的宽度128,而导滑槽长79.5,抽芯需要5,在抽芯复位的过程中滑块全部位于导滑槽内,所以运行平稳。
(4)滑块的定位装置
以确保斜导柱突出端能准确地进入滑块的斜孔,因此,需要定位抽芯终止后滑块的位置。
为了方便起见,采用了传统的定位弹簧,螺钉和挡板模具的设计。
其结构形式如图12所示。
图12滑块的定位装置与滑块锁紧形式
7.5楔紧块的设计
为了防止活动型芯和滑块接触时产生移动的现象,往往需要采用滑块楔紧块结构。
因为适合精密塑料零件的精度为5,整体式的楔形块可以满足设计要求。
如图12所示。
8模架的确定
根据本设计中凹模嵌件所占的面积通过模具型腔的数目与布置的中心长度以及凹模嵌件的大小可以算出约为118
42,凹模的最小壁厚和向抽芯以及导柱导套的布置侧等因素需要考虑,根据参考文献,即:
,
;
再根据参考文献,可以选定模架为200
200及各板的厚度尺寸;再根据参考文献可确定选用A2型模架。
(1)定模型腔板(A板)尺寸。
本设计中塑件的高度为30,考虑到需要在模板上创建冷却槽,你需要预留一定的距离,这里定模型腔板厚度取50。
(2)型芯固定板(B板)尺寸。
根据标准模架型芯固定板的板厚度取40。
(3)垫块(C板)尺寸。
垫块的厚度等于推出行程加推板厚度加推杆固定板厚度+(5~10)(30+20+16+5~10)71~76
这里确定垫块厚度为80。
经过以上的计算,模架的尺寸基本确定,板面尺寸为200
200,其外形尺寸如图13所示。
图13模具尺寸
9排气槽的设计
本设计中的塑件采用的是侧浇口进料,熔体由塑件下方的台阶以及中间的肋板充满型腔,而型芯的顶部有推杆,侧部有侧抽芯,气体会顺着其配合间隙、分型面和型芯之间的间隙排出去。
排气系统结构如图15所示。
图15排气形式
10冷却系统的设计
10.1冷却介质
聚乙烯()具有较好的流动性,成型温度为150~250℃,模具温度为50~70℃,所以初步选定模具温度为60℃,用常温水对模具进行冷却。
10.2冷却系统的简单设计
(1)单位时间内注入模具中的塑料熔体的总质量W
1)塑料熔体体积
2)塑料制品的质量
3)塑料熔体单位小时内注入模具的总体积为
(2)确定单位质量的塑件在凝固时所放出的热量Q
根据参考文献可知熔体的单位热流量为:
,这里取750。
(3)冷却水通道的导热总面积A以及冷却水管总长L
由以上计算结果可知,使模具得到充分冷却1根冷却水道就可以了。
11导向与定位机构的设计
导柱导向的作用是在定模和动模有相互运动的时候,为动模导向,使动模能准确的与定模进行合模而不发生偏差。
在模具工作时,导向机构可以使动模按照顺序准确合模,防止型芯在合模的时候受到损坏。
本设计中,塑件较为简单,为了方便起见,可采用模架本身自带的定位结构进行定位。
如图16所示。
图16导柱与导套定位机构
参考文献
[1]叶久新、王群主编.塑料成型工艺与模具设计.北京:
机械工业出版社,2007.11
[2]黄毅宏、李明辉主编模具制造工艺.北京:
机械工业出版社,1999.6
[3]《塑料模设计手册》编写组编著.塑料模设计手册.北京:
机械工业出版社,2002.7
[4]李绍林,马长福主编.实用模具技术手册.上海:
上海科学技术文献出版社,2000.6
[5]许发樾主编.实用模具设计与制造手册.北京:
机械工业出版社,2000.10
[6]李绍林主编.塑料·橡胶成型模具设计手册.北京:
机械工业出版社,2000.9
[7]章飞主编、陈国平副主编。
型腔模具设计与制造北京:
化学工业出版社,2003
[8]李建军,李德群主编.模具设计基础及模具[M].机械工业出版社,2005.
[9]中国塑料机械信息网首页,行业咨询,2006-4-19.
[10]中国模具工业协会标准件委员会编.中国模具标准件手册[M].上海科学普及出版社.
[11]马树奇、金燕编著.4野火4.0从入门到精通.电子工业出版社.
致谢
经过本次对带侧孔塑料盖进行的模具设计,我得到了用于设计注塑模具模具在成型过程中更深层次理解,能够独自对塑件进行分析与计算,对独立设计模具有了全新的认识。
此次论文的完成,指导老师蒋冬青教授对我的耐心指导和室友们对我的无私帮助将会是我受用一生的财富,并在此提出感谢。
本次带侧孔塑料盖的模具设计采用测浇浇注系统,既保证了塑件的精度要求,同时也达到了表面粗糙度要求。
由于塑件有对开的侧孔,为了方便起见,本设计中采用一模两腔的结构形式,对开侧抽芯。
在与塑件有接触并且极易磨损的地方,利用高性能的模具材料,提高模具的使用寿命,同时也可提高模具的精度。
在脱模的设计中使用在推杆顶端加圆盘的推杆改良杆进行推出,大大的减小了推出应力,并且简化了模具的结构。