机械常识问.docx
《机械常识问.docx》由会员分享,可在线阅读,更多相关《机械常识问.docx(93页珍藏版)》请在冰豆网上搜索。
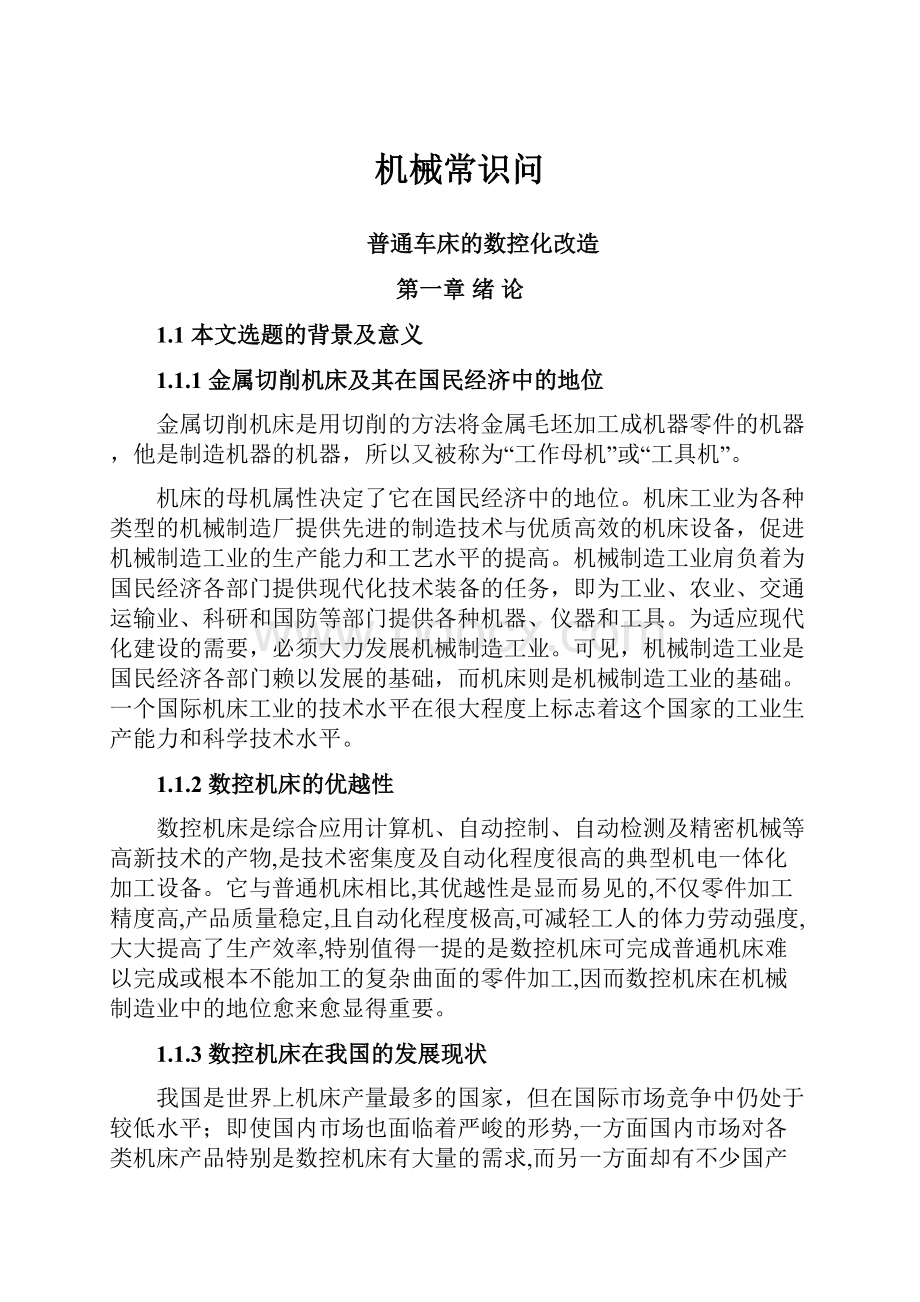
机械常识问
普通车床的数控化改造
第一章绪论
1.1本文选题的背景及意义
1.1.1金属切削机床及其在国民经济中的地位
金属切削机床是用切削的方法将金属毛坯加工成机器零件的机器,他是制造机器的机器,所以又被称为“工作母机”或“工具机”。
机床的母机属性决定了它在国民经济中的地位。
机床工业为各种类型的机械制造厂提供先进的制造技术与优质高效的机床设备,促进机械制造工业的生产能力和工艺水平的提高。
机械制造工业肩负着为国民经济各部门提供现代化技术装备的任务,即为工业、农业、交通运输业、科研和国防等部门提供各种机器、仪器和工具。
为适应现代化建设的需要,必须大力发展机械制造工业。
可见,机械制造工业是国民经济各部门赖以发展的基础,而机床则是机械制造工业的基础。
一个国际机床工业的技术水平在很大程度上标志着这个国家的工业生产能力和科学技术水平。
1.1.2数控机床的优越性
数控机床是综合应用计算机、自动控制、自动检测及精密机械等高新技术的产物,是技术密集度及自动化程度很高的典型机电一体化加工设备。
它与普通机床相比,其优越性是显而易见的,不仅零件加工精度高,产品质量稳定,且自动化程度极高,可减轻工人的体力劳动强度,大大提高了生产效率,特别值得一提的是数控机床可完成普通机床难以完成或根本不能加工的复杂曲面的零件加工,因而数控机床在机械制造业中的地位愈来愈显得重要。
1.1.3数控机床在我国的发展现状
我国是世界上机床产量最多的国家,但在国际市场竞争中仍处于较低水平;即使国内市场也面临着严峻的形势,一方面国内市场对各类机床产品特别是数控机床有大量的需求,而另一方面却有不少国产机床滞销积压,国外机床产品充斥市场。
90年国外数控机床在我国市场的占有率仅达15%左右,而95年已达77%。
严重影响我国数控机床自主发展的势头。
这种现象的出现,除了有经营上、产品制造质量上和促销手段上等原因外,一个主要的原因是我国生产的数控机床品种、性能和结构不够先进,新产品(包括基型、变型和专用机床)的开发周期长,从而不能及时针对用户的需求提供满意的产品。
具体地说,这个问题反映在下列五个方面:
(1)我国机床厂目前开发基型产品的周期约为15~18个月,其中设计时间约为5~8个月,占总周期的40%左右。
而国外一些先进机床厂同类基型产品的开发周期为6~9个月,其中设计约1.5~2个月,只占25%。
因此无论是产品开发的总周期还是设计所占的时间比例均与国外先进水平有很大的差距。
(2)我国工厂由于缺乏设计的科学分析工具(如分析和评价软件、整机结构有限元分析方法以及机床性能测试装置等),自行开发的新产品大多基于直观经验和类比设计,使设计一次成功的把握性降低,往往需要反复试制才能定型,从而可能错过新产品推向市场的良机。
(3)用户根据使用需要,在订货时往往提出一些特殊要求,甚至在产品即将投产时有的用户临时提出一些要求,这就需要迅速变型设计和修改相应的图纸及技术文件。
在国外,这项修改工作在计算机的辅助下一般仅需数天至一周,而在我国机床厂用手工操作就至少需1~2个月,且由于这些图纸和文件涉及多个部门,常会出现漏改和失误的现象,影响了产品的质量和交货期。
(4)现在我国工厂设计和工艺人员中青年占多数,他们的专业知识和实际经验不足,又担负着开发的重任。
(5)由于长期以来形成的设计、工艺和制造部门分立,缺乏有效的协同开发的模式,不能从制订方案开始就融入各方面的正确意见,容易造成产品的反复修改,延长了开发的周期。
为解决这些问题,必须对产品开发的整个过程综合应用计算机技术,发展优化和仿真技术,提高产品结构性能,并建立起基于并行工程(ConcurrentEngineering)的使设计、工艺和制造人员协同工作和知识共享的产品虚拟开发环境,使用相应的产品虚拟开发软件,这样才能有效地解决产品开发的落后局面,使企业取得良好的经济效益。
1.1.4机床数控化改造的必要性
我国目前机床总量380余万台,而其中数控机床总数只有11.34万台,即我国机床数控化率不到3%。
近10年来,我国数控机床年产量约为0.6~0.8万台,年产值约为18亿元。
机床的年产量数控化率为6%。
我国机床役龄10年以上的占60%以上;10年以下的机床中,自动/半自动机床不到20%,FMC/FMS等自动化生产线更屈指可数(美国和日本自动和半自动机床占60%以上)。
可见我们的大多数制造行业和企业的生产、加工装备绝大数是传统的机床,而且半数以上是役龄在10年以上的旧机床。
用这种装备加工出来的产品普遍存在质量差、品种少、档次低、成本高、供货期长,从而在国际、国内市场上缺乏竞争力,直接影响一个企业的产品、市场、效益,影响企业的生存和发展。
所以必须大力提高机床的数控化率。
经过大量实践证明普通机床数控化改造具有一定经济性、实用性和稳定性。
所以很多企业纷纷将现有机床改造成经济型数控机床,这种做法具有投资少、见效快的特点。
事实证明:
用较少的资金,将普通机床改造升级为数控机床,可以为企业带来可观的经济效益。
1.2机床数控技术的基本概念
1.2.1概述
数控技术,简称数控(NumericalControl)。
它是利用数字化的信息对机床运动及加工过程进行控制的一种方法。
用数控技术实施加工控制的机床,或者说装备了数控系统的机床称为数控机床。
数控系统包括:
数控装置、可编程序控制器、主轴驱动及进给装置等部分。
要实现对机床的控制,需要用几何信息描述刀具和工件间的相对运动以及用工艺信息来描述机床加工必须具备的一些工艺参数,如:
进给速度、主轴转速、主轴正反转、换刀、冷却液的开关等。
这些信息按一定的格式形成加工程序,通过数控系统的译码,从而使机床准确地动作和加工出优质的零件。
1.2.2数控机床的工作流程
数控机床工作时根据所输入的数控加工程序,由数控装里控制机床部件的运动零件加工轮廓,从而满足零件形状的要求。
数控加工程序的编制:
在零件加工前,首先根据被加工零件图样所规定的零件形状、尺寸、材料及技术要求等,确定零件的工艺过程、工艺参数、几何参数以及切削用量等,然后根据数控机床编程手册规定的代码和程序格式编写零件加工程序。
对于比较简单的零件,通常采用手工编程;对于形状复杂的零件,则在编程机上进行自动编程,或者在计算机上用CAD/CAM软件自动生成零件加工程序。
译码:
数控装置接受程序,译码程序按照一定的语法规则将信息解释成计算机能够识别的数据形式。
刀具补偿:
零件加工程序通常是按零件轮廓轨迹编制的。
刀具补偿的作用是把零件轮廓轨迹转换成刀具中心轨迹运动加工出所要求的零件轮廓。
插补:
插补的目的是控制加工运动,使刀具相对于工件作出符合零件轮廓轨迹的相对运动。
位置控制和机床加工:
位置控制的任务是在每个采样周期内,将插补计算出的指令位置与实际反馈位置相比较,用其差值去控制伺服电机,电动机使机床的运动部件带动刀具相对于工件按规定的轨迹和速度进行加工。
1.3数控机床的组成和分类
1.3.1数控机床的组成
数控机床一般由输入输出设备、数控装置、伺服系统、测量反馈装置和机床本体组成,见图1-1:
图1-1数控机床的组成
(1)输入输出设备
输入输出设备主要实现程序编制、程序和数据的输入以及显示、存储和打印。
(2)数控装置
数控装置是数控机床的核心。
它接受来自输入设备的程序和数据,并按输入信息的要求完成数值计算、逻辑判断和输入输出控制等功能。
(3)伺服系统
伺服系统是接受数控装置的指令,驱动机床执行机构运动的驭动部件。
它包括伺服电路和伺服电机组成。
一般来说,数控机床的伺服驱动要求有好的快速响应性能,能灵敏而准确地跟踪由数控装置发出的指令信号。
(4)测量反馈装置
该装置由测量部件和响应的测量电路组成,其作用是检测速度和位移,并将信息反馈给数控装置,构成闭环控制系统。
(5)机床本体
机床本体是数控机床的主体,是用于完成各种切削加工的机械部分。
1.3.2数控机床的分类
按伺服系统的控制原理可分为:
开环控制的数控机床、半闭环控制的数控机床和闭环控制的数控机床。
(1)开环控制的数控机床
这类数控机床不带有位置检测装置,数控装置将零件程序处理后,输出数字信号给伺服系统.驱动机床运动。
指令信号的流程是单向的。
如图1-2所示。
图1-2开环控制的数控机床
(2)闭环控制的数控机床
这类机床带有检测装置。
它随时接受在工作台端测得的实际位置反馈信号,将其与数控装置发来的指令位置信号相比较,由其差值控制进给轴运动,直到差值为零,进给轴停止运动。
如图1-3。
图1-3闭环控制的数控机床
闭环控制可以消除包括工作台传动链带在内的误差,从而定位精度高、速度调节快,但由于工作台惯量大,给系统的设计和调整带来很大的困难,主要是系统的稳定性受到不利影响。
(3)半闭环控制的数控机床
半闭环控制的数控机床与闭环控制得到数控机床的区别在于检测反馈信号不是来自工作台。
而是来自电动机端或丝杠端连接的测量元件。
如图1-4。
图1-4半闭环控制的数控机床
实际位置的反馈是通过间接测得的伺服电动机的角位移算出来的,因而控制精度没有闭环高,但机床工作的稳定性却由于大惯盆工作台被排除在控制环外,调试方便,因而广泛用于数控机床中。
1.4数控机床的特点
(1)加工零件的适应性强,灵活性好。
(2)加工精度高,产品质皿稳定。
(3)生产率高。
(4)减少工人的劳动强度。
(5)生产管理水平高。
1.5CA6140车床数控改造技术参数
最大工件直径/mm400
最大工件长度/mm1500
溜板及刀架重力/N纵向(z轴)800;横向(x轴)600
刀架快速移动速度/m/min纵向2.4;横向1.2
最大进给速度/m/min纵向0.6;横向0.3
定位精度/mm±0.015
主电动机功率/kw7.5
启动加速时间/ms30
第二章车床的总体改造和设计
2.1CA6140车床改造的总休方案
图2-1数控系统的总体框架
总体框架说明:
(1)PC机:
可采用工控PC机,可满足该控制系统的控制要求。
(2)运动控制卡:
采用PCL运动控制卡,该卡是一种高速三轴步进电机运动控制卡,它有16位的数字输入、输出口,可实现三轴联动。
因此,它可以满足车床X、Z轴联动,实现直线,圆弧插补。
(3)光电耦合电路的作用是能够隔离外部干扰信号对运动控制卡的信号冲击,提高系统的稳定性。
(4)机床本体是由CA6140改造而来,拆除原来的丝杆,溜板箱,变速箱等。
(5)步进电机及其驱动器要能够达到0.005mm的加工精度要求。
(6)各种限位开关:
减速开关,回零开关均安装在机床本体上,限位开关起着硬件硬限位的作用,当车床加工工件超出加工范围时,车床自动停止加工。
减速开关的作用是当车床刀架回零并走到车床零点附近时,减速开关被开启并通知车床减速走到零位置。
2.2进给系统的设计
考虑到该数控系统是开环控制,没有位置反馈,故进给系统尽可能的要减少中间传动环节。
本车床的X、Z两轴进给系统去掉了原来的进给系统的中间传动环节,直接采用了步进电机+刚性联轴器+滚珠丝杆的传动方案。
拆除原来的丝杆,增加少量的机械附件,就可安装步进电机及滚珠丝杆螺母副。
2.3控制系统的软件部分
该车床控制系统采用GSK980T系统。
其功能主要有读取零件的加工G代码,编辑和编译G代码,仿真加工(包括加工前仿真和与加工同步仿真),回参考点,手工对刀,加工中断,超程软限位等功能。
它可处理进给速度,主轴速度及转速方向,刀具信息,M功能等多种加工信息。
加工过程中,软件界面的状态栏还可以显示出刀具当前的坐标,加工状态,加工时间等信息。
2.4改造后机床的特点
(1)具有与原机床一致的刚度与强度.
(2)具有与原机床一致的加工范围。
(3)纵向进给直线度与原机床一样,其运动精度则有数控系统和纵向电机、滚珠丝杠的精度保证。
(4)横向进给的直线度和运动精度全部有改造部分的制造和装配精度保证。
(5)可充分利用机床床身部分的已加工表面作为改造部分的定位和测量基准。
(6)改造后的机床外型将类似于国产经济型数控车床,整体较美观、大方。
第三章机床的电气改造
3.1数控系统的选择
机床数控系统(CNC系统)是数控机床的控制核心,随着机床数控技术的不断发展与进步,提高了数控机床的整体性能,尤其是它的加工精度和生产效率提高得更为显著,现在,数控机床已在机械工业生产中得到广泛应用。
目前市场上流行的数控系统,如FANUC、西门子、GSK980TD等都配置有车床数控系统,能够胜任车、削加工的大部分工作,并具有价格低廉、可靠性强、功能强大等特点。
在对多家数控系统进行比较后!
我们选择了GSK980TD型数控系统。
数控机床应能长期连续加工,其数控系统必须能够长期无故降连续运行。
为保证机床长期可靠地运行,数控系统必须有抵抗恶劣环境的高可靠运行特性。
常年的工作考脸证明GSK980TD系统是最可靠的数控系统之一,它能在一般车间环境下运行。
其工作场地的室温为0-45℃,相对湿度75%短时可达95%,抗震为0.5g,电网电压波动为10%-15%,经对使用中系统的实际统计,GSK980TD系统的故障率为0.008,比较好地满足了我国市场的要求。
GSK980TD系统之所以有非常高的可靠性,主要源自以下因素:
(1)可靠的高质量的元器件及良好的老化筛选工艺。
(2)大规模及超大规模的专用集成电路芯片:
GSK980TD系统采用了许多由富士通公司制造的高度集成的专用功能芯片。
(3)全自动化工厂生产制造:
多层印刷板的制板、元件的插装、焊接、印刷板的检查、系统的组装、电机投料、冲片、精铸、机械加工、装配、成品的包装出厂全部为自动化,这就使得在生产过程中避免了外界(人)的不稳定因素的干预。
所以产品的一致性好,增加了可靠性。
(4)良好的控制软件设计:
GSK980TD系统经过在国内各地数年的运行,积累了丰富的数据,因此在软件设计时考虑了可能出现的各种故障情况,加入了许多保护和提高可靠性的措施,如开机和状态切换时的层层检侧、过压、过流、反馈断线等报警,使得机床运行中出现故障时,系统能及时处理,从而进免了元部件的损坏。
(5)数字式进给伺服和数字式主轴驱动:
数字控制、数据的串行传输大大提高了运行的可靠性。
主轴控制信号的传送使用光缆,使信号免受外界干扰。
3.1.1硬件结构
采用CISC(超大规模集成电路)技术的GSP主板,主板上连接可插接(分离的)小模板。
对于数控系统,由于其是弱电电路,如果采用十24VDC为电源输入,可以大大降低其热源和不稳定因素。
用户可以把+24V稳压电源放在电气柜内,从而大大提高了整个数控系统的可命性能。
GSK980TD系统的可靠性好,性能/价格比高,在全国各地己销售10余万台。
随着大规棋集成电路芯片的发展,GSK980TD系统的破件结构已经改进过多次。
目前销售的TA和TD,其硬件结构基本一样,只是控制轴数不同,所配置的进给轴驱动电机不同。
GSK980TD系统的CNC单元为大板结构。
基本配置有主板、存储器板、I/O板、伺服轴控制板和电源。
各板插在主板上,与CPU的总线相连。
(1)主板
主CPU在该板上。
主CPU用于系统主控,原来用80386,从1998年起改用80486/DX2。
此外,显示的CRT控制也在该板上。
(2)存储器板
该板上有:
①系统的控制软件ROM(共5片)。
GSK980TD系统可控制车床。
不同类型的机床控制软件不同;②伺服控制软件ROMI片;③PMC-L的ROM芯片2片,用于存储机床的强电控制逻辑程序;④RAM芯片,用于寄存CPU的中间运算数据,根据需安装;⑤COMSRAM,用于存储系统和机床参数、零件加工程序,根据用户要求配置,最大可为128K字节。
CMOSRAM与4.5V电池相连,关机时保存信息。
(3)I/O板
该板是CNC单元与机床强电柜的接口,接收或输出24V直流信号,由PMC实施输入/输出控制,I/O点数可根据机床的复杂程度选择,标准配置为104个输入点,72个输出点。
(4)进给伺服控制板
GSK980TD系统全部用数字式交流伺服控制。
其控制板装在CNC单元内,插在主板上,即CNC单元与进给伺服为一体化设计。
伺服板上有2个CPU(TMS320),用于伺服的数字控制。
每个CPU控制2个轴,一块板可控制4个轴。
该板接受主CPU分配的伺服控制指令,输出6个相位各差60°的脉宽调制信号(每轴),加于各轴的伺服驱动的功率放大器上。
TD系统为4轴(最大配里)控制,2轴联动,只用一块伺服板。
(5)电源
主要有5V直流电,用于各板的供电。
24V直流电,用于单元内各继电器控制。
除上述这些板外,还有图形控制板、PMC-M板、远程缓冲器(REMOTEBUFFER)板,这些板用户可根据自身要求选订。
(6)PLC功能的内部集成
PLC功能的内部集成化,提高了PLC和CNC的内部通讯能力,增强了机床的逻辑控制,PLC的32输入和24输出模块,阳M的32输入和24输出模块,可以和外围的电路相连接,而这种模块,通过阳M提供的电缆和刚M数控系统连接。
这就提高了整个机床的可靠性。
同时又提高了数控系统的保护(如果有间题,只能损坏这种模块,不会对数控系统造成破坏)。
光纤技术的通讯,可以扩展PLC输入输出点,通过光纤进行连接,简化和线路的连接。
(7)轴转接模块
GSK980TD提供了轴转接模块,机床的编码器和到伺服的线路可以直接联到此模块,通过它再和数控系统的轴板进行连接。
提高了数控系统的可靠性,如果机床的轴有问题,可以直接把轴模块上的插头相对换,就能很快的查出问皿所在(系统内部或外部)。
3.1.2软件功能
(1)CNC功能
系统软件的开放性和友好界面,帮助性的编程方式。
定义的固定循环并使用户很方便地根据其加工特性进行编写自己的固定循环,用户集成的G代码功能。
M功能和PLC功能的调用子程序,E参数(用户可以通过E参数来读取或改变CNC的数值)。
强大的通讯功能(RS232IRS4221RS485),边加工边传输功能。
提高了计算机的CAD/CAM程序的加工能力。
完善的丝杠螺距补偿。
FANUC的螺距补偿为线性补偿,补偿中仅把相应的拐点坐标值输入即可。
并且没有固定的距离和补偿值的限制。
(2)PLC功能
梯形图的PLC程序,多任务的PLC程序的编程结构,提高了PLC程序的编写和可读性。
梯形图PLC程序在屏幕上的动态显示,方便了最终用户的维修。
丰富的PLC和CNC交换信息量,PLC图形界面的管理。
(3)强大的编程软件
GSKCC软件。
Windows环境下并运行在PC计算机上,PLC程序的编写工具,方便的机床程序管理。
简便的通讯能力(PCIONC间为主从关系,所有操作均在PC侧完成),动态的PLC程序显示(PC侧)。
GSKCC软件Windows环境并运行在PC计算机。
调整NC的机床参数和伺服系统,图形的动态响应,强大的优化功能,方便地调整系统参数。
3.1.3显示
GSK980TD系统的显示器320×240点阵,用单色液晶显示器(LCD),标准为5.7″,也可配彩色显示器。
GSK980TD系统有图形显示功能:
①对编制的加工程序进行加工前的图形模拟,模拟刀尖的轨迹或加工件的三维实体形状:
②在加工过程中显示刀尖的轨迹,使操作员能够监视切削过程。
图形可局部放大,以便观察细部。
显示图形必须用图形控制板,该板为专用微机,CPU用80186。
3.1.4PMC控制
PMC就是可编程序机床控制器,是专门用于控制机床的PLC。
GSK980TD系统的PMC只有47条指令〔基本指令有12条,功能指令有35条)。
基本指令为2进制位的逻辑运算,功能指令主要有数据定义、数据变换、译码和代数运算。
GSK980TD系统用梯形图编制PMC顺序逻辑程序。
由于有功能指令,使得PMC程序编制非常容易,简捷。
梯形图可用下述两种方法编制:
①用专用的编辑卡利用LCD液晶显示画面在系统上现场编制。
②在计算机上装入专用软件用计算机编制,然后经RS-232C口将梯形图程序传送到数控系统。
调试好的程序要用写入器写入EPROM。
GSK980TD系统PMC控制有FMC-L和PMC-M2种。
PMC-L的处理机与主机共用,其处理时间为6/步,最大步数为5000步。
PMC-M为专用处理机,徽处理器为80186,专用一块板,插在主板上,处理时间为2us步,最大步数为8000步。
2种PMC的扫描周期均为I6ms。
3.1.5进给伺服驱动
GSK980TD系统进给轴的驱动使用交流同步电动机,目前为a系列。
根据其负载特性和快速性分为:
a(标准型)、am(高加速特性)、ac(经济型)和aL(低惯量型)。
最大力矩为400N'm。
0-C配a型。
0-D配置ac型。
am加速特性好,从0至最高转速的启动过程为24ms,故用于高速加工。
电机轴上装有脉冲编码器,每转发出65536个脉冲(经电路倍频),用做位置反馈和速度反馈。
这种位置反馈,是间接测量工作台的直线位移,所以称为半闭环伺服系统。
但是,只要设定相应的参数GSK980TD系统可以使用直线光栅尺,使系统接成全闭环。
除此之外,还可接成双位置反馈,即同时具有上述2个闭环。
这样,既可以提高系统的稳定性,还可以提高系统的快逮性和加工精度。
进给伺服单元的控制用前述的轴控制板,该板输出控制指令信号到功率放大器。
功率放大器为模块化结构,分为整流模块和逆变模块,使用IPM元件。
LSI是专用位置控制大规模集成电路芯片。
ROM中存储的控制程序主要有同步电机的快速响应矢量控制、IP调节器、速度和位里的反馈控制、前馈和提前前馈控制和状态观测器。
此外,还有许多非线性补偿与控制,如单脉冲抑制、超调抑制、反向间隙加速补偿、机床的速度反馈等。
还有运行过程的监测及保护。
由于有这些控制,使GSK980TD系统运行可靠、快速、平稳、精度高。
3.1.6主轴驱动
GSK980TD系统可以同时控制2个主轴电动机,可以是2个数字式控制的电机,也可以一个为数字式,另一个为模拟式控制电机。
模拟控制指令是0-10V的直流电压。
该系统的主轴电机为异步电机,目前为a系列。
有以下品种。
a:
标准型,恒功率调速范围4:
1。
aP:
恒功率宽调速范围型(8:
1)。
aC经济型。
aT:
与主轴直连型。
主轴电机的最大功率为37kW,最高转速可达15000r/min,用数字式矢量控制。
主轴驱动有速度控制和位置控制2种工作方式,普通加工为速度控制。
主轴电机轴上装有圆型的磁性传感器,用做速度反馈。
位置控制用于主轴同步、主轴定向、刚性攻丝、Cs轴轮廓控制。
因此需要控制主轴的转角或转位,轮廓控制时要与其它轴插补。
此时需在机床的主轴上装位置编码器,位置编码器有光电式和磁性传感器。
普通为每转发出1024个脉冲,高精度的发出360000个脉冲/转。
主轴控制用单独的CPU控制,处理器为TMS-320。
从CNC单元输出的控制指令用一条光缆送到主轴的控制单元,数据为串行传送,因此可靠性比较高。
3.1.7RS-232C口及数据通讯
GSK980TD系统有2个串口(RS-232C),分4个通道,用于系统与外部设备的数据交换。
交换的数据包括:
系统及机床的设定参数、PMC参数、零件加工程序、刀具补偿值、设定的工件坐标系、丝杠的螺补值等。
与计算机相连时,计算机内必须装有数据传送软件。
最快的传送速率为9600bps。
除上述的信息交换外,利用串行通讯还可实现下列方式的在线加工与机床的DNC管理:
(1)纸带方式的加工:
加工复杂零件时,加工程序非常长,CNC的内存容量不够用,可将程序存于外设,如计算机的软盘。
用电缆将PC机与CNC经串口连接后,启动自动加工,CNC预读15个程序段,开始加工。
此后加工一段读入一段