烧结机改造项目可行性研究报告.docx
《烧结机改造项目可行性研究报告.docx》由会员分享,可在线阅读,更多相关《烧结机改造项目可行性研究报告.docx(34页珍藏版)》请在冰豆网上搜索。
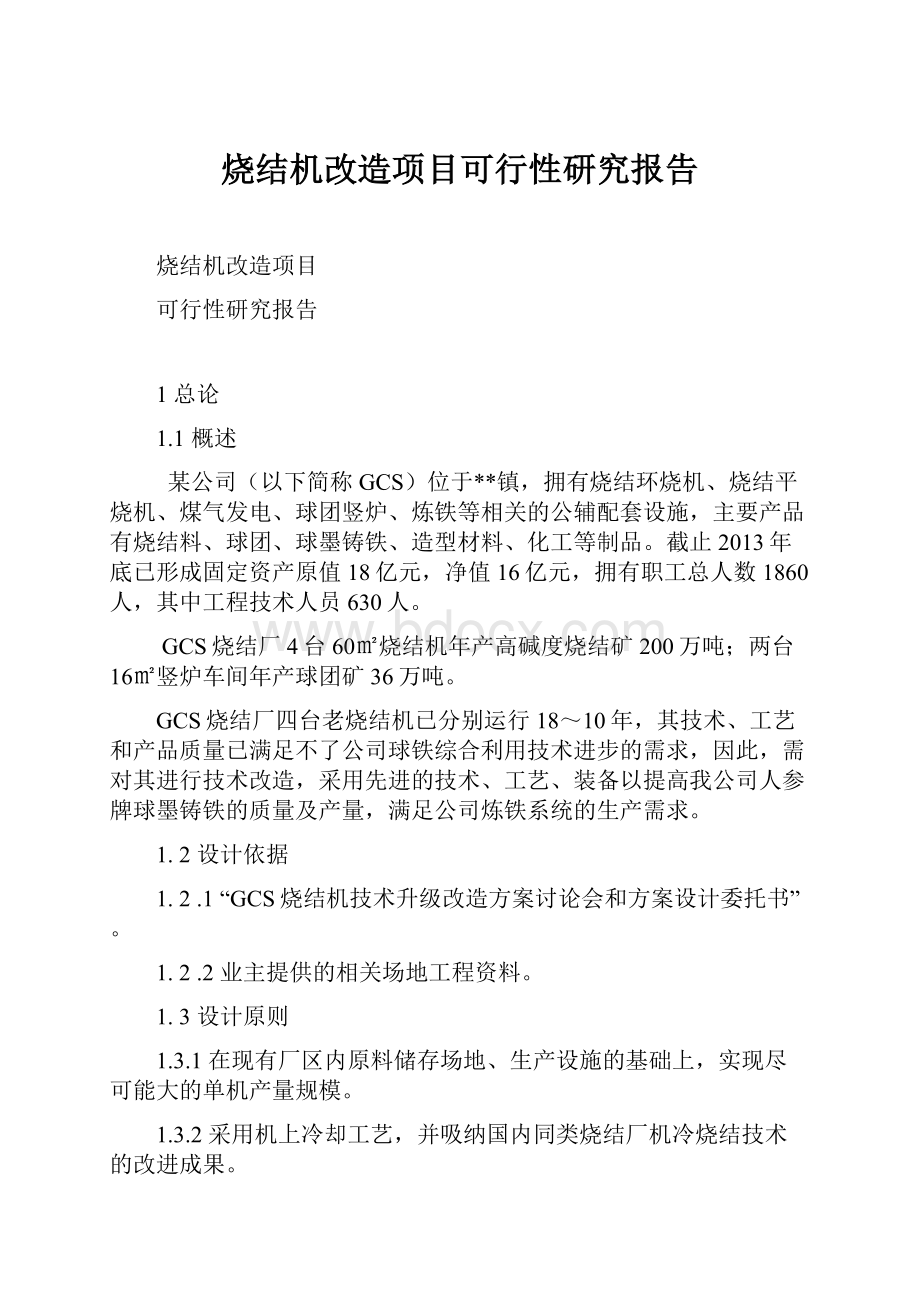
烧结机改造项目可行性研究报告
烧结机改造项目
可行性研究报告
1总论
1.1概述
某公司(以下简称GCS)位于**镇,拥有烧结环烧机、烧结平烧机、煤气发电、球团竖炉、炼铁等相关的公辅配套设施,主要产品有烧结料、球团、球墨铸铁、造型材料、化工等制品。
截止2013年底已形成固定资产原值18亿元,净值16亿元,拥有职工总人数1860人,其中工程技术人员630人。
GCS烧结厂4台60㎡烧结机年产高碱度烧结矿200万吨;两台16㎡竖炉车间年产球团矿36万吨。
GCS烧结厂四台老烧结机已分别运行18~10年,其技术、工艺和产品质量已满足不了公司球铁综合利用技术进步的需求,因此,需对其进行技术改造,采用先进的技术、工艺、装备以提高我公司人参牌球墨铸铁的质量及产量,满足公司炼铁系统的生产需求。
1.2设计依据
1.2.1“GCS烧结机技术升级改造方案讨论会和方案设计委托书”。
1.2.2业主提供的相关场地工程资料。
1.3设计原则
1.3.1在现有厂区内原料储存场地、生产设施的基础上,实现尽可能大的单机产量规模。
1.3.2采用机上冷却工艺,并吸纳国内同类烧结厂机冷烧结技术的改进成果。
1.3.3主体工艺生产流程实现PLC系统集中控制。
1.3.4除主体工艺设备必须更换,相关部分土建厂房、基础改造扩建外,其它电气、自动化仪表、通风除尘、给排水和燃气等专业设施立足于用旧。
1.3.5统筹考虑原有烧结机公辅设施利旧的可行性。
1.3.6工艺流程布置顺畅、简洁;总图布局紧凑、合理,节省工程投资,技术装备达到国内先进水平。
1.3.7严格遵守国家有关能源、环保、工业卫生与安全、消防等有关法令法规,强化“三废”治理,有效地保护厂址区域环境和生产岗位环境;采用节能的新工艺设备,注重节能降耗。
1.4主要设计决定和工艺特点
1.4.1利用现有场地布置1台有效烧结面积180㎡烧结主厂房,其他车间及辅助设施作相应改造,形成一条年产180万吨成品烧结矿的生产线。
1.4.2在现有的原料库西侧扩建两个圆筒仓,以提高含铁原料的供料能力;同时延长现有的配料皮带。
1.4.3熔剂和燃料准备系统全部利旧,生石灰使用粒度为0~3mm。
1.4.4采用三段式混合和燃料分加工艺,一、二次圆筒混合机均放置在地面,传动方式采用刚性齿轮传动;三混设在烧结主厂房,胶轮传动。
1.4.5采用梭式布料器+圆辊给料机+多辊布料器的形式。
1.4.6烧结机点火采用高效节能点火器,火焰集中,节省能耗;燃料为高炉煤气。
1.4.7成品筛分采用一级高效椭圆等后冷矿筛,根据机上冷却的技术特点,不设铺底料系统。
1.4.8烧结段大烟道除尘采用电除尘器,冷却段大烟道除尘采用多管除尘器。
1.4.9在烧结机冷却段大烟道上设置翅片管换热器,回收热废气的余热,生产低压蒸汽,用于混合料预热。
1.4.10烧结机大烟道卸灰系统采用电液动双层卸灰阀+皮带机的干式密封输灰方式,稳定烧结混合料的水分,并有效改善车间环境。
1.4.11烧结机机尾、成筛分以及各转运扬尘点的除尘,利用现有的2台40㎡电除尘器进行除尘。
1.4.12成品烧结矿经皮带机直接转运到高炉矿槽。
1.4.13烧结机主生产流程设备全部采用PLC系统集中联锁控制,利用现有的主控室及控制设施。
1.5烧结机主要技术经济指标见表1-1。
新烧结机技术经济指标表1-1
序号
项目
单位
指标
备注
1
烧结矿产量
104t/a
180
出厂烧结矿
2
烧结机总有效面积
㎡
180
有效烧结面积
㎡
180
有效冷却面积
㎡
216
利用系数
t/(㎡.h)
1.3
年作业时间
h
7920
3
烧结矿质量
TFe
%
56.0
FeO
%
10
R(Ca/SiO2)
2.0
转鼓指数(T)+6.3mm
%
≥72.0
4
原料消耗(干)
(估算)
铁精矿单耗
Kg/t结矿
670
白云石单耗
Kg/t结矿
60
生石灰单耗
Kg/t结矿
90
焦粉单耗
Kg/t结矿
56
高炉返矿单耗
Kg/t结矿
150
5
动力消耗
电
Kwh/t结矿
45
水
m³/t结矿
1.1
其中新水
m³/t结矿
0.35
压缩空气
m³/t结矿
6.0
蒸汽
m³/t结矿
35
混合煤气
GJ/t结矿
0.10
6
设备总重
t
3665
7
装机总容量
Kw
11300
高压8460KW
8
劳动定员
人
160
2烧结工艺
2.1设计规模、工作制度及产品方案
2.1.1设计规模
依据GCS公司的改造预期目标,采用机上冷却烧结工艺,主体设备为有效烧结面积180㎡的一台带式烧结机,有效冷却面积216㎡的环冷机,年产成品烧结矿180万t。
2.1.2工作制度
烧结机为连续工作制,四班三运转,每班工作8h;主机年工作时间7920h,日历作业率90.4%,单位产量为195t/h。
2.1.3产品方案
烧结机产品为经过筛分的冷烧结矿,粒度5-150㎜,温度≤150℃;烧结矿主要化学成分指标:
TFe=56%,R=2.0。
2.2主要设计条件
2.2.1原、燃料的来源
烧结机使用的含铁原料主要是普通精矿,由料场采用皮带机运入配料仓。
燃料以焦粉为主,熔剂为生石灰和轻烧白云石。
燃料和轻烧白云石由皮带机运输,生石灰采用罐车运输。
2.2.2原、燃料的主要化学成分略。
2.2.3含铁原料、熔剂及燃料的需要量
原、燃料消耗量表表2.1
物料
单耗
干耗量
名称
结矿
小时耗量
日耗量
年耗量
kg/t
t/h
t/d
104t/a
铁矿粉
670
130.65
3135.6
103.47
白云石
60
11.7
280.8
9.27
焦粉
56
10.92
262.08
8.65
生石灰
90
17.55
421.2
13.90
高炉返矿
150
29.25
702
23.17
合计
1026
200.07
4801.68
158.46
2.4烧结机系统工艺流程见图-1。
2.5主要工艺技术特点和装备水平
2.5.1除主体生产设备外,相关辅助设施尽量利用。
2.5.2配料设备采用变频调速圆盘给料机和电子皮带秤,PLC系统自动控制配料过程。
2.5.3采用小球烧结工艺,配备三次混合机,有效保证实现小球烧结;同时采用燃料两次分加技术,在提高产量的条件下节能降耗。
2.5.4二次圆筒混合机内采用雾化水和特制逆流分级复合衬板,提高烧结机的制粒效果。
2.5.5混合料采用蒸汽预热技术,提高料温,增强料层的透气性。
蒸汽为余热回收蒸汽。
2.5.6采用机上冷却工艺,混合料的烧结和烧结饼的冷却过程都在同一台烧结机上完成,物化反应充分,可显著提高烧结矿质量;取消热矿筛分工序,改善车间环境。
2.5.7采用大风量、低碳厚料层(料厚600-650㎜)生产工艺,强化料层的蓄热作用,有效降低燃料消耗,降低烧结矿中FeO含量,提高其还原性。
2.5.8烧结机采用高效节能型点火器,使用混合煤气点火,点火能耗0.10GJ/t-s。
2.5.9烧结机采用旋转散料收集装置,半悬挂柔性传动和尾部移动架等先进结构形式,设备运行平稳可靠。
2.5.10烧结机头尾采用全金属结构密封,台车采用弹簧滑道密封技术,有效降低漏风率,并设有台车篦条清扫器。
2.5.11烧结机采用圆辊给料机、辊式布料器和可调松料器技术,具有对小球破坏少,料面平整,混合料粒度偏析适宜的特点,保证料层具有较好的透气性。
2.5.12对扬尘设备严格密封,烧结机、原料和成品系统均采用静电除尘器集中除尘以保护劳动环境,使烟尘排放浓度≤100mg/Nm3。
2.6烧结工艺生产系统
烧结机工艺生产系统主要包括以下车间:
配料室、一次混合室、二次混合室、烧结主厂房、烧结风机房、冷却风机房、转运站及皮带机通廊等设施。
新1#烧结机的生产系统平断面布置详见附图。
2.6.1配料室
配料室设在原料仓库的西侧,增建2个圆筒仓,形成两列共计12个仓的配料系统,东侧6个仓作为铁精矿的配料仓,通过皮带上料;精矿仓下采用PZ20圆盘给料机和电子皮带秤配料,增加2套配料设施;现有2个白云石仓、2个燃料仓和2个生石灰仓的配料设施全部利旧。
配料设备全部由PLC系统实现闭环自动控制调节。
配料室±0.00米地坪的配-2、配-3皮带机尾部延长6米;检修设备利旧。
2.6.2一次混合室
一次混合室内设1台Ø3.0×13.0m圆筒混合机,刚性齿轮传动;设备安装基本参数如下:
安装角度2.5°,转速7.0r/min,填充率15.08%,混合时间为2.8min。
一次混合机设备、厂房和检修设施全部利旧改造,Ø3.0×13.0m圆筒混合机是利用现在使用的二混制粒机。
2.6.3二次混合室
二次混合室内设1台Ø3.5×16m大型圆筒混合机,强化混合料造球,采用刚性齿轮配液压马达传动,转速可调;设备基本参数如下:
筒体转速6.4r/min,安装角度1.5°,填充率13.5%,混合时间为5min。
二次混合室混合机设备新上,厂房改造,检修设施全部利旧。
2.6.4熔、燃破碎间和二次配煤仓
烧结机熔剂和燃料来自现有烧结厂的熔燃制备系统,熔剂和燃料的上料系统和准备设施全部利旧。
二次配煤仓及二次配煤设施全部利旧。
2.6.5烧结主厂房
烧结机主厂房沿老厂房向西延长布置,新主厂房总成116.5米,宽12米,主要包括三次混合机、布料系统、点火、烧结、冷却、破碎和冷矿筛分工序,在标高16.90m平台设有中央计算机控制室(利旧),各作业工序设计如下:
(1)三次混合
三次混合机设在主厂房标高22.50平台,规格Ø2.8×7m,对二次燃料和混合料进一步造球,使燃料外裹在小球表面,提高垂直烧结速度,提高产量,并降低燃耗。
设备采用胶轮传动,安装角度2.0°,填充率17.9%,混合时间为1.76min。
三次混合设备利旧改造,基础提高1.50米,传动装置与26.40米土建梁碰,设备做相应修改。
(2)点火系统
烧结机使用混合煤气为点火燃料,点火温度要求1100±50℃,点火时间为1-2min,点火燃耗为0.10GJ/t烧结矿。
点火设备包括1台幕帘式点火器和2台高压鼓风机。
(3)烧结机及配套设施
烧结机设计有效抽风面积为275㎡,安装在烧结主厂房标高12.90m平台,台车宽度为3.2m,总有效长度为86m,其中有效烧结面积183.6㎡,有效冷却面积121.6㎡。
烧结机基本结构主要有烧结台车、头部骨架、中部骨架、尾部骨架、尾部移动架、风箱、灰箱、头部星轮、尾部星轮、滑道、头尾弯道、传动装置等主题设施以及混合料斗、圆辊给料机、多辊布料器、台车篦条自动清理装置等辅助设施组成。
下面简述其主要设计特点。
烧结机台车本体材质采用低硫球墨铸铁(球化率≥85%);篦条为生产中易损件,采用材质为高铬铸铁。
台车设计为整体防漏风结构,主梁与篦条之间设隔热垫;台车两侧下部采用弹簧弹压式密封装置;拦板为上下两节式。
烧结机头部设有混合料斗、圆辊给料机和辊筛式布料器。
混合料斗通过侧重传感器安装于头部骨架,料斗上设置可调给料闸门,内部设防粘耐磨衬;圆辊给料机采用交流变频调速装置,辊筛式布料器安装角度较小,强化混合料在烧结台车上的偏析分布,使混合料中的大颗粒尽量布在台车底部,提高料层透气性;料层厚度为650-700㎜。
头部下方还设有台车篦条自动清扫装置。
烧结机头部传动为半悬挂柔性传动,采用交流变频调速装置,并配带光电码测速仪,可根据生产情况与圆辊给料机一起通过计算机进行同步调速。
烧结机下部设有风箱、风箱立管和大烟道。
烧结机风箱共60个,风箱设有防上浮装置;点火器下3个风箱设有风量调节阀,采用电液动执行机构,机旁操作。
烧结机头尾密封采用全金属结构,密封性能良好,可降低烧结机漏风率。
烧结机润滑系统考虑如下,头部传动采用稀油润滑,中部滑道采用干油集中润滑,台车车轮为定期注油。
烧结机头部布料、点火和结尾单辊破碎均设有工业电视监视系统,用于辅助操作;烧结终点位置和温度有仪表检测,计算机进行运算处理,在CRT画面上显示。
在主厂房标高12.25m平台设有小格拉链机,收集并运输烧结机散料,通过斜溜槽将散料送入烧结矿皮带。
(4)单辊破碎机
从烧结机上卸下的烧结矿饼经单辊破碎机破碎到150mm以下,单辊破碎机设计规格为ø1.7×3.53m,破碎齿为可更换式,锤头表面堆焊耐热耐磨硬质合金钢。
单辊破碎机安装在主厂房伟跨标高13.05m平台。
(5)冷矿筛分
在烧结主厂房尾跨标高4.60m平台配备1台TDLS2575型椭圆等厚筛,对破碎后的烧结矿进行分级,筛出返矿(<5mm)和成品。
烧结返矿经灰-2皮带机、改混-1#皮带机送入一次混合机参加混合。
成品矿经一冷-5#皮带机等现有皮带机系统直接运至高炉矿槽。
2.6.6烧结风机房及机头电除尘器
烧结烟气经大烟道、电除尘器、烧结风机、烟囱,最后排入大气。
大烟道内径4960mm,中心标高8.00mm,设计烟气流速15.0m/s,烟气温度80--120℃,粗颗粒粉尘在此进行一次降尘。
机头除尘配备1台260m2三电场电除尘器,采用先进顶部振打结构形式,维护量小;设计进口粉尘浓度5g/m3,出口粉尘浓度100mg/m3。
除尘器下部输灰设备采用刮板输送机和加湿机进行输灰。
烧结风机房配备1台风量17000m3/min、升压17KPa的离心抽风机,检修设备采用1台Q=25/5t双钩桥式起重机。
烧结风机进口设有风量调节门,采用电动执行机构控制;进出风口均设有非金属膨胀节,避免进出风管对风机壳体的挤压。
烧结风机润滑系统由主油泵、油站及高位油箱等组成。
主油泵2台,一备一用性质;润滑点包括风机轴承、电机轴承、齿式联轴器等5个点,润滑油采用20#或30#汽轮机油,油过滤精度≤30
。
风机电机选用T5300-6/1730型同步电机,功率:
5300KW,电压:
6KV;防护等级为IP44。
烧结烟囱采用钢筋混凝土结构,设计高度100m,上口内径4.3m,烟尘排放浓度100mg/Nm3。
烧结风机和电除尘器的控制系统设在烧结风机房值班室内,控制室厂房、检测仪表和控制设施利旧。
2.6.7冷却风机房及多管除尘器
冷却风机房配备1台风量:
15000m3/min、升压:
8KPa的离心抽风机,检修设备是1台Q=20/5t双钩桥式起重机。
冷却段大烟道内径4660mm,中心标高8.88m,配备一台1200管除尘器进行烟气除尘。
冷却风机排放烟囱采用砖混结构,设计高度50m,上口内径4.3m,烟尘排放浓度100mg/Nm3。
2.6.8灰处理
烧结机大烟道、机头260m2电除尘器、1200管除尘器收集的烧结灰,加湿处理后经改混-1#皮带机送入一次混合机参加混合。
2.6.9余热回收系统
烧结机冷却段烟气平均温度在350℃以上,含有大量废热,采用换热器回收部分余热,生产低压蒸汽,再用来加热烧结混合料,可有效降低生产能耗。
改造方案在1200管除尘器后的大烟道上安装1台翅片管式换热装置,该设备具有热交换效率高、适应温度范围宽的特点,设计蒸汽产量6.0t/h,压力0.3-0.5MPa,完全满足混合料预热要求。
该套系统主要包括软水箱、变频供水和换热器三部分设施。
3总图
3.1气象条件
年平均温度8.9℃
极端最高温度41.5℃
极端最低温-23.1℃
年平均无霜期158天
平均风速1.4m/s
年最大降水量835.9mm
最大冻土深度1260mm
3.2总平面布置
3.2.1主要设施组成:
略,详见“GCS公司1#烧结机改造工程方案设计总平面布置图”。
3.3竖向布置及雨排水
3.3.1根据老厂区地形现状,竖向布置形式采用单向斜面型平坡式。
3.3.2依托现有的排水系统,改造部分场地排水采用盖板排水沟与厂区现有排水设施衔接,布置在厂区内道路一侧。
3.4道路布置
为满足厂内运输和消防要求,在有条件的地方设计道路及场地,新铺砼道路总长度约320.00m,路面宽度:
主干道8.00m,次干道6.00m。
道路型式采用郊区型,不设人行步道,最小转弯半径6.00m,最小纵坡小于3%,路面载荷为汽-20级。
3.5消防
本改造工程不考虑设置消防站,有关消防事宜依托GCS公司现有消防系统。
3.6拆迁
本工程需拆除原烧结厂部分设施及相应地上、地下管线。
4土建
4.1主要设计参数
基本风压值:
0.4KN/m2
本地区地震基本烈度<7度
4.2工程地质情况
第一层杂填土
第二层粉质粘土
第三层非自重湿陷性粉质粘土
第四层粉质粘土
第五层粉质粘土
第六层细砂
第七层粉质粘土
第八层卵石
4.3建筑结构形式
4.3.1烧结主厂房
烧结主厂房内共设有6层平台,烧结机基础平台标高为12.90m和12.25m,其中12.90m平台利旧改造,12.25m平台新建,三次混合机及上料系统的22.50m及26.40m平台利旧改造。
烧结主厂房设有3台检修吊车,其中2台吊车利旧,新上1台Q=20/5t,LK=18m吊车,检修烧结机尾设备,轨顶标高为25.70m。
新扩建厂房为钢筋砼框架结构,屋面采用现浇钢筋砼板,卷材防水;吊车梁为钢吊车梁或混凝土吊车梁,烟道及卸灰斗采用钢结构;基础为桩基础;地面采用砼地面;外墙封闭为空心砖或加气砼块填充墙,普通钢门窗。
现有厂房根据现场实际情况及工艺要求改造加固。
4.3.2配料室
在现有原料库4个铁料仓的东侧增建2个含铁原料仓,柱距6.0m,结构形式为现浇钢筋砼结构,料仓为钢结构,钢筋砼独立柱基。
4.3.3烧结风机房
烧结风机房土建厂房利旧改造,风机基础及烟道等相关设施基础新建。
260m2电除尘支架采用钢筋砼框架结构,100m烟囱为钢筋砼结构,上口内径4.30m。
4.3.4转运站及皮带通廊
1#烧结机改造涉及4#、9#和10#转运站及相应的通廊,转运站的各层平台及连接通廊全部利旧,只对通廊内皮带机的基础修改,传动基础通过设备底座调整。
4.3.51200管除尘器
结构形式为钢筋混凝土框架结构,柱下独立基础,顶标高约4.50m,地面为混凝土,围护墙采用砖砌体,普通钢门窗。
4.3.6冷却风机房
新建厂房建筑面积288m2,结构形式为排架结构,预应力混凝土屋面梁、板,柱下独立基础,设有20/5t天车一台,砖砌体围护,地面为混凝土,柱牛腿标高约14.00m,柱顶标高约18.00m。
冷却风机烟囱为砖混结构,高50m,上口内径4.30m。
4.3.7一次混合室、二次混合室
一次混合室厂房利旧,设备基础根据工艺要求适当改造;二次混合室厂房利旧改造,现有厂房向西延长3米,新建厂房结构形式为钢筋混凝土框架结构,现浇钢筋混凝土屋面,柱下独立基础,砖砌体围护,混凝土地面,柱顶标高约14.00m。
设备基础新建。
5电气
5.1电压等级及负荷
5.1.1电压等级
交流:
6KV;380V;220V;36V
直流:
220V
电源频率:
50Hz
5.1.2计算负荷
全厂装机总容量约11300KW,其中高压电机4台,装机容量8460KW,最大电机5300KW。
无功补偿采用同步电机进行补偿。
全厂总计算负荷如下:
有功功率Pjs=7731KW
无功功率Qjs=5687KW
视在功率Sjs=8590KVA
功率因数COSø=0.90
年耗电量Wh=46.5×106kWh
5.1.3负荷类别
烧结机、冷却风机、烧结抽风机等重要用电设备为一类负荷;配料系统、混料系统、成品系统、除尘系统等用电设备为二类负荷;其它附属设施为三类负荷。
5.2供配电系统
烧结机改造供电系统利用在建的35KV变电站,两路6KV电源引自上级高压配电室不同段母线,每路6KV电源均能负荷本工程100%的用电负荷。
5.3配电室设置及供电范围
5.3.1配料变配电室
利旧改造现有的配料变配电室,增加的主要供电设备有:
配料室圆盘给料机、皮带机、电子皮带秤及振动器等设施。
5.3.2混合变配电室
1、二次混合室配电室均利用现有的配电室,配电室内各设1台630KVA,6/0.4KV变压器。
两路电源引自6KV高压配电室,各设1个MCC,其主要供电范围有:
一次混合室、二次混合室、皮带机、除尘器等工艺设备及附属设施。
5.3.3烧结主厂房变配电室扩建改造
烧结主厂房变配电室扩建改造,内设两台1000KVA,6/0.4KV变压器。
两路电源引自6KV高压配电室,下设1个MCC,其主要供电范围:
烧结主厂房设备、260m2电除尘器、皮带机等工艺设备及附属设施。
低压变配电室母线采用单母线分段运行方式,两段母线之间设置分段母联开关,手动投入。
5.4电气传动系统的控制及操作方式
烧结机改造工程的混料系统、配料系统、烧结系统、成品系统、熔燃破碎系统、输灰系统等工艺设备均采用PLC可编程控制器控制。
配料室圆盘给料机、烧结系统烧结机、布料设备等设备采用变频调速。
各车间设备的操作方式为机旁手动操作和集中连锁操作两种方式。
5.5主要电气设备及材料的选型
5.5.16KV高压开关柜
型式:
封闭铠装中置式手车柜,真空断路器采用弹簧储能操作机构。
额定电流:
1250A(1600A,进线柜)
额定电压:
6KV
防护等级:
IP30
开断电流:
31.5KA
5.5.2直流电源装置
输入电压:
三相四线380±10%
频率:
50Hz±10%
输出电压:
DC220V
控制系统:
微机监控,汉化显示,IGBT
防护等级:
IP20
5.5.3电力变压器
型式:
油浸式自冷节能型变压器
接线组别:
D,yn-10
一次电压:
6KV±10%
二次电压:
0.4KV
阻抗电压:
4¥或4.5%
5.5.4低压配电屏
型式:
GGD固定式
防护等级:
IP30
主要设备:
低压断路器(开断电流35KA)、交流接触器、热继电器等设备选用国产或合资厂的产品。
5.5.5交流变频器:
采用西门子变频器,采用网络控制方式
5.5.6电缆
高压电力电缆采用YJV-10KV型,低压电力电缆采用YJV-1KV型,控制电缆采用KYKV-500V型,回收区域采用防腐电缆,局部高温区域采用ZR-YJV-1KV型。
5.6电缆敷设
电缆采用沿电缆沟、电缆槽及电缆桥架敷设方式,局部电缆穿镀锌钢管明配或穿钢管埋地敷设。
5.7接地系统
本工程接地系统采用TN-C-S系统,接地电阻不大于1欧姆,设置防雷接地及静电接地,接地电阻不大于10欧姆和30欧姆。
5.8照明
配电室、控制室、操作室均采用荧光灯照明。
车间各层平台的照明采用高效节能型工厂灯,煤气净化区域采用防爆灯,并在重要场所设置应急照明。
5.9防火措施
高、低压配电室均应设置手持式灭火装置,并设有自动火灾报警装置(见通信专业说明书)。
电缆须刷防火涂料,电缆进出配电室孔洞须用防火堵料封堵,电气设备的施工及安装均按有关规程规范进行设计。
6自动化仪表
6.1控制水平
自动化主要对设计范围的工艺过程进行检测及控制。
其中主工艺流程采用计算机控制,辅工艺流程