凸轮板.docx
《凸轮板.docx》由会员分享,可在线阅读,更多相关《凸轮板.docx(21页珍藏版)》请在冰豆网上搜索。
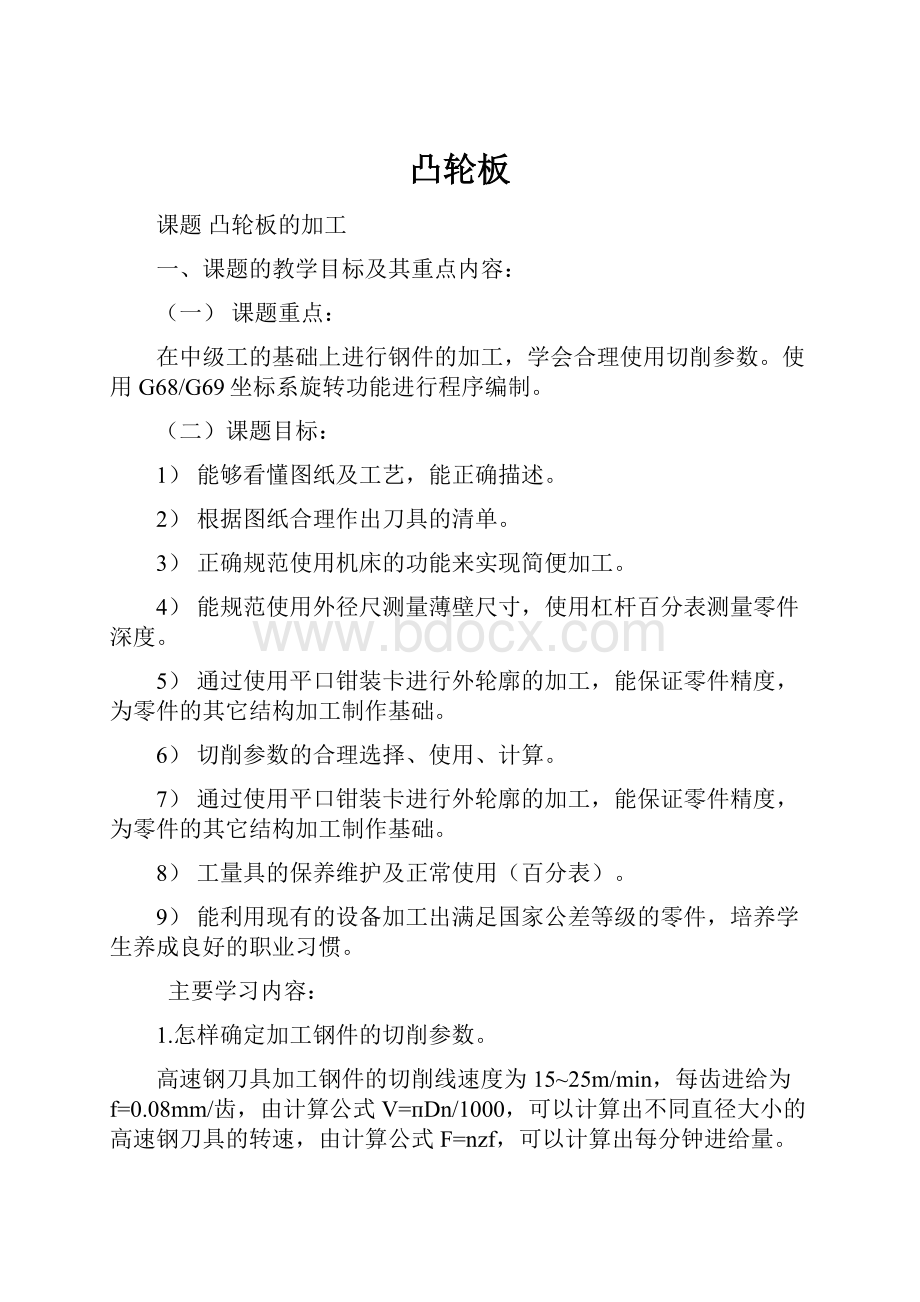
凸轮板
课题凸轮板的加工
一、课题的教学目标及其重点内容:
(一)课题重点:
在中级工的基础上进行钢件的加工,学会合理使用切削参数。
使用G68/G69坐标系旋转功能进行程序编制。
(二)课题目标:
1)能够看懂图纸及工艺,能正确描述。
2)根据图纸合理作出刀具的清单。
3)正确规范使用机床的功能来实现简便加工。
4)能规范使用外径尺测量薄壁尺寸,使用杠杆百分表测量零件深度。
5)通过使用平口钳装卡进行外轮廓的加工,能保证零件精度,为零件的其它结构加工制作基础。
6)切削参数的合理选择、使用、计算。
7)通过使用平口钳装卡进行外轮廓的加工,能保证零件精度,为零件的其它结构加工制作基础。
8)工量具的保养维护及正常使用(百分表)。
9)能利用现有的设备加工出满足国家公差等级的零件,培养学生养成良好的职业习惯。
主要学习内容:
1.怎样确定加工钢件的切削参数。
高速钢刀具加工钢件的切削线速度为15~25m/min,每齿进给为f=0.08mm/齿,由计算公式V=пDn/1000,可以计算出不同直径大小的高速钢刀具的转速,由计算公式F=nzf,可以计算出每分钟进给量。
2.坐标旋转指令(旋转非连续切削)的编制的问题主要有
(1)第一段原始的刀具路径的终点应该是旋转一次坐标后的下一段刀具路径的起始点;而第一段原始的刀具路径的起始点应该是最后一次旋转坐标后刀具路径的终点坐标。
旋转非连续切削时,第一次的刀具路径最好是起始点和终点在同一位置。
(2)使用旋转指令在G17平面非连续切削时,G68坐标旋转指令后一定要写入X,Y平面的刀具路径指令,如G68坐标旋转指令后写入的是Z轴坐标移动指令,刀具将移动到切削平面再进行旋转,会出现过切现象。
(3)顺逆时针旋转切削,分清此时刀具路径是顺铣还是逆铣,使用正确的刀补G41\G42指令。
(4)使用旋转指令时注意有的机床不允许包含倒角指令,所以尽量直接使用直线、圆弧插补指令。
三、实训资源:
资源序号
资源名称
备注
1
数控铣床XD40
系统FANUC0I、SIEMENS、华中
2
精密平口钳
高60mm
3
虎钳扳手
内六角
4
内六角扳手
安装虎钳压板用
5
各类刀具
根据加工的需要选择
13
等高垫铁
45X15/38X15(各一对)
14
百分表
0-1
15
图纸(含评分标准)
16
游标卡尺
0-150
17
内测千分尺
5-30
18
油石
19
材料(45#)
毛坯100X100X22
四、注意事项:
1、数控机床属于精密设备,未经许可严禁进行尝试性操作,观察操作时必须戴护目眼睛且站在安全位置并关闭防护挡板。
2、工件必须装夹稳固。
3.刀具必须装夹稳固方可进行加工。
4.FANUC系统机床锁闭空运行后必须重新返回参考点。
5.SIEMENS系统机床锁闭空运行后必须取消空运行。
6.切削加工中禁止用手触摸工件。
7.粗精加工必须使用不同刀具。
8.★更换刀具时必须重新对刀,再切削时注意刀具与工件之间的距离。
五、评分标准与图纸:
1.图纸:
见下页
2.评分标准
序号
项目及技术要求
配分
评分标准
检测结果
实得分
1
尺
寸
公
差
8
超差全扣
2
8
超差全扣
3
9
超差全扣
4
16H7
10
超差全扣
5
30H7
10
超差全扣
6
9
超差全扣
7
5
超差全扣
8
6-R20
5
超差全扣
9
6-R6
5
超差全扣
10
形
位
公
差
平行度0.04(A)
8
超差全扣
11
对称度0.04(A)
8
超差全扣
12
其
它
表面粗糙度3.2
5处
超差面扣分
13
棱边倒钝
2
超差全扣
14
文明生产
8
违规操作全扣
15
工时
每超15分钟扣5分
六、加工流程
在制订机械加工工艺规程时,正确选择合适的毛坯,对零件的加工质量、材料消耗和加工工时都有很大的影响。
显然毛坯的尺寸和形状越接近成品零件,机械加工的劳动量就越少,但是毛坯的制造成本就越高,所以应根据生产纲领,综合考虑毛坯制造和机械加工的费用来确定毛坯,以求得最好的经济效益。
1.工艺安排:
以下图形为加工的工序图样示意:
(1)加工原点设定。
图1
图1
(2)工序1:
加工外凸轮。
图2
图2
工序2:
粗加工圆台。
图3
图3
工序3:
加工凸台轮廓。
图4
图4
工序4:
加工凸台上的槽。
图5
图5
刀具卡片与工艺卡片的制作:
加工刀具卡片
零件名称
加工令号
零件图号
序号
刀具号
刀具规格名称
(尺寸单位㎜)
数量
加工表面
(尺寸单位㎜)
备注
1
T01
Φ3定心钻
1
中心孔孔定心
2
T02
Φ8立铣刀
1
外轮廓
3
T03
Φ16立铣刀
1
凸外圆
4
T04
Φ8钻头
1
中心孔
6
T06
Φ12立铣刀
1
中心孔
8
T08
Φ8键槽刀
1
铣孔
9
T09
10
T10
11
T11
12
T12
13
T13
14
T14
15
T15
16
T16
17
T17
18
T18
编制
审核
批准
共页
第页
数控加工工艺卡片
单位名称
北京市工业技师学院
零件名称
加工令号
零件图号
圆台列阵孔件
001
工序号
程序编号
夹具名称
使用设备
车间
一
一号
平口钳
数控铣床XD40
数控铣厂房
工步号
工步内容
(尺寸单位㎜)
刀具号
刀具规格
(尺寸单位㎜)
主轴转速
rad/min
进给速度
背吃刀量
mm
备注
1
粗加工底座外轮廓
2
Φ16立铣刀
375
84
5
3
粗加工大凸外圆至尺寸Φ60
3
4
粗加工小凸外圆至尺寸Φ50
5
粗加工上台阶至尺寸44
5
Φ8立铣刀
750
120
2
6
精加工上台阶至尺寸43.8
5
7
粗加工下台阶外轮廓
5
8
精加工下台阶外轮廓
9
中心孔定位
1
Φ3中心钻
3000
100
2
10
钻中心孔
4
Φ8钻头
800
80
Φ14钻头
350
60
11
铣孔
6
Φ8键槽刀
750
80
5
12
Φ8球头刀
倒圆角
2700
600
13
编制
审核
批准
年月日
共页
第页
操作要点:
1.加工准备
(1)详阅零件图X10-1,并按坯料图X10-2检查坯料的尺寸;
(2)编制加工程序,输入程序并选择该程序;
(3)用平口虎钳装夹工件,伸出钳口10mm左右,用百分表校正;
(4)安装寻边器,确定工件零点为坯料上表面的中心,设定零点偏置;
(5)安装ø20mm粗立铣刀并对刀,设定刀具参数,选择自动加工方式。
2。
粗铣凸轮轮廓
粗铣凸轮轮廓,留0.50mm单边余量,如图6所示。
3.铣槽轮外圆轮廓
(1)选择程序,粗铣槽轮外圆轮廓,留0.50mm单边余量;
(2)安装ø20mm精立铣刀并对刀,设定刀具参数,半精铣槽轮外圆轮廓,留0.10mm单边余量;
(3)测量外圆直径,调整刀具参数,精铣槽轮外圆轮廓至要求尺寸,如图7所示。
(4)选择凸轮加工程序,设定刀具参数,半精铣凸轮轮廓,留0.10mm单边余量;
(5)测量凸轮尺寸,调整刀具参数,精铣凸轮轮廓至要求尺寸。
图6粗铣凸轮轮廓图7铣外圆轮廓
4.铣6-R15圆弧
(1)选择加工程序,调整刀具参数,粗铣6-R15圆弧,留0.50mm单边余量;
(2)调整刀具参数,半精铣6-R15圆弧,留0.10mm单边余量;
(3)测量工件尺寸,调整刀具参数,精铣6—R15圆弧至要求尺寸,如图8所示。
图8铣6-R15圆弧图9铣6-12槽
5.铣6-12槽
(1)安装ø10mm粗立铣刀并对刀,设定刀具参数,选择程序,粗铣各槽,留0.50mm单边余量;
(2)安装ø10mm精立铣刀并对刀,设定刀具参数,半精铣各槽,留0.10mm单边余量;
(3)测量各槽尺寸,调整刀具参数,精铣各槽至要求尺寸,如图9所示。
三、注意事项
(1)使用寻边器确定工件零点时应采用碰双边法;
(2)精铣时采用顺铣法,以提高尺寸精度和表面质量;
(3)立铣刀垂直方向进刀时,铣刀中心不能直接铣削工件。
注:
(1)在加工槽形轮廓时须考虑工件与刀具的变形情况,故在加工时应注意切削参数的选择,切削时采用顺铣,以减小加工时过切现象的发生。
(2)由于图纸给出的尺寸
方法
(第四步)程序的编制:
分析图纸确定加工部位编程所需运动指令:
G01直线插补
G02顺圆弧插补
G03逆圆弧插补
G81点孔钻
G83深孔钻
O1;(程序名)铣凸轮外轮廓
行号
主程序O1
解释
N1
G90G54G00Z100
定位起始高度
N2
X0Y0
定位起始点
N3
S375M03
主轴正转启转
N4
X70
N5
Z10
N6
M08
冷却液开
N7
G01Z-2.0F80
N8
M98P2
调用2号子程序
N9
G00Z100
抬到安全高度
N10
M05
主轴停转
N11
M30
程序结束并返回的开始
N12
%2
子程序
N13
G90G41G01X42Y0D1
刀具路径
N14
G03X44.381Y-10.462R20
N15
G02X41.951Y-25.32R20
N16
G02X0Y-49R49
N17
G02X-49Y0R49
N18
G02X-31.719Y37.348R49
N19
G02X-7.201Y43.923R30
N20
G01X-7.307Y41.360
N21
G02X42Y0R42
N22
G40G01X70Y0
N23
M99
返回到主程序
O2;(程序名)铣6-R15圆弧
行号
主程序O1
解释
N24
G90G54G00Z100
定位起始高度
N25
X0Y0
定位起始点
N26
S750M03
主轴正转启转
N27
Y-52
N28
Z10
N29
M08
冷却液开
N30
M98P2L6
调用2号子程序
N31
G90G00Z100
N32
M05
N33
M30
N34
%2
2号子程序
N35
G90G01Z-2.0
N36
M98P3
调用3号子程序
N37
G91G68X0Y060
N38
G90G01X0Y-52
N39
G00Z10
N40
M99
N41
%3
3号子程序
N42
G90G41X15Y-52D2
N43
G03X-15Y-52R15
N44
G40G01XOY-52
N45
M99
返回到主程序
O2;(程序名)铣6-12沟槽
行号
主程序O1
解释
N46
G90G54G00Z100
定位起始高度
N47
X0Y0
定位起始点
N48
S750M03
主轴正转启转
N49
X60
N50
Z10
N51
M08
冷却液开
N52
M98P2L6
调用2号子程序
N53
G90G00Z100
N54
M05
N55
M30
N56
%2
2号子程序
N57
G90G01Z-2.0
N58
M98P3
调用3号子程序
N59
G91G68X0Y060
N60
G90G01X60Y0
N61
G00Z10
N62
M99
N63
%3
3号子程序
N64
G90G41X60Y6D2
N65
G01X30Y6
N66
G03X30Y-6R6
N67
G01X60Y-6
N68
G40G01X6OY0
N69
M99
返回到主程序
旋转指令格式复习
坐标系旋转(G68,G69)
编程形状可以被旋转。
例如,在机床上,当工件的加工位置由编程的位置旋转相同的角度,使用旋转指令修改一个程序。
更进一步,如果工件的形状由许多相同的图形组成,则可将图形单元编成子程序,然后用主程序的旋转调用。
这样可简化程序,省时,省存储空间。
图8
格式
G17
G18G68α_β_R_;坐标系旋转开始
G19
:
坐标系旋转模式
:
(坐标系被旋转)
G69;坐标系旋转取消模式
指令含义
G17(G18或G19):
选择包含有被旋转图形的平面
α_β_:
对应当前平面指令(G17,G18或G19)中的两个轴的绝对指令。
此指令指定了G68后面指定旋转中心的坐标。
R_:
正值为逆时针方向的角度位移。
参数5400Bit0指定角度位移是绝对值位移或者由G码(G90或G91)来决定绝对值或相对值。
最小输入增量:
0.001度
有效数据范围:
-360.000~360.000
图9
注意:
当使小数指定角度位移时(R_),数字1代表度单位。
宏程序的应用
理解和正确应用宏程序的代码和条件、跳转及其它的语句。
注意:
条件语句中的DO1不要写成D01。
[说明]
G码选择平面:
G17,G18,或G19
选择平面的G码(G17,G18,或G19)可以在包含有坐标系旋转的G码(G68)的单节前指定。
G17,G18,或G19不能在坐标系旋转模式下指定。
作为增量位置指令在G68单节和绝对指令之间指定;它被认为是指定G68旋转中心的位置。
当省略α_和β_时,指定G68时的位置被设定为旋转中心。
当省略旋转角度时,设定在参数5410的值被认为是旋转角度。
旋转坐标系取消使用G69。
G69可以指定在其它指令的同一单节中,刀具偏置,例如刀具半径补正,刀长补正或刀具偏置在旋转后的坐标系中执行。
注意:
如果与G69一起指定了一个移动指令,随后的增量指令不能按指定的值执行。
坐标点提示:
七、平行度测量方法
1、找到被测要素所选基准,以所选基准为定位基准利用杠杆百分表检测平行度,使设计基准面与测量基准重合进行测量。
2、测量步骤及过程
(1)如图10所示在工件上确定九个虚拟的测量点,用来测量,测量点的选择和设立应符合设计基准的要求,并应计算出轮廓的真实尺寸,避免基准转换造成测量误差,测量者应具有使用杠杆百分表的能力。
图10
(2)将杠杆表表针压在斜轮廓1点将杠杆表表盘数值压为零,或确定为一整数值,并将当前机床Z轴机械坐标值记下,对于有相对坐标值清零功能的机床可直接将Z轴相对坐标值清零,然后摇动手轮将Z轴抬起,使杠杆表表针远离工件表面10-50mm,再次摇动手轮到达3点,(注意在此过程中不可以转动百分表)与1点操作方法相同,将百分表表针读数压到1点相同值,然后看机床3相对坐标值与在1点压表相对坐标值的差值,记录下差值后在对4—6/7—9几个测量点进行1—2同样的测量,然后将所有记录所得的数值得最大值和最小值相减,所得两数之差为加工所得的被测面与基准面之间的平行度。
3、平行度保证方法
(1)基准的选择和夹紧定位
对于该工件来说设计基准是被测要素的底面,根据定为基准的选择原则,应达到基准重合基准统一,即设计基准要与定为基准相重合,以减小基准不重合造成加工误差,在实际加工时装夹工件要以工件设计基准,即图中所标出的基准A为定位基准,限制与平行度有关的三个自由度,然后用钳口加紧,限制工件的另外两个自由度,此时工件处于不完全定位但可以进行加工。
(2)装夹的过程及注意事项
由于要保证工件尺寸精度和工件的形状位置精度,在确定了装夹方式后因保证工件的定为基准面与机床的工作台面平行,从而保证加工后的被测面与基准面同样平行。
八、对称度的测量方法
由于图示工件对称度的测量基准为工件的中心线,而中心线为虚拟基准不可测,故选择与中心线有平行关系的面为间接测量基准,用杠杆百分表对被测面进行检测。
1、测量步骤及过程
(1)如图11所示在工件上确定4个虚拟的测量点,用来测量,测量点的选择和设立应符合设计基准的要求,并应计算出轮廓的真实尺寸,避免基准转换造成测量误差,测量者应具有使用杠杆百分表的能力。
图11
(2)将杠杆表表针压在工件底座B点处将杠杆表表盘数值压为零,或确定为一整数值,机床相对坐标值清零,在将百分表提起,离开工件表面5—10mm然后摇动手轮到达A点处,(注意在此过程中不可以转动百分表),进行B点处相同的操作,看机床从B点处移动到A点处的距离记录当前相对坐标值,然后在对C—D两个测量点进行A—B同样的测量,然后将记录的两组相对坐标值的绝对值相减,所得两数之差再除以二为加工所得的被测面与基准面之间的对称度。
2、对称度保证方法
(1)基准的选择和夹紧定位
由于图示工件对称度的测量基准为工件的中心线,所以在建立工件坐标系时保证建立的工件坐标系与工件实际对称中点重合,以此保证轮廓的对称度。
(2)装夹的过程及注意事项
由于要保证工件尺寸精度和工件的形状位置精度,在确定了装夹方式后因保证工件的定为基准面与机床的工作台面平行,从而保证加工后的被测面与基准面同样
教学后记