压力容器制造工艺指导书.docx
《压力容器制造工艺指导书.docx》由会员分享,可在线阅读,更多相关《压力容器制造工艺指导书.docx(18页珍藏版)》请在冰豆网上搜索。
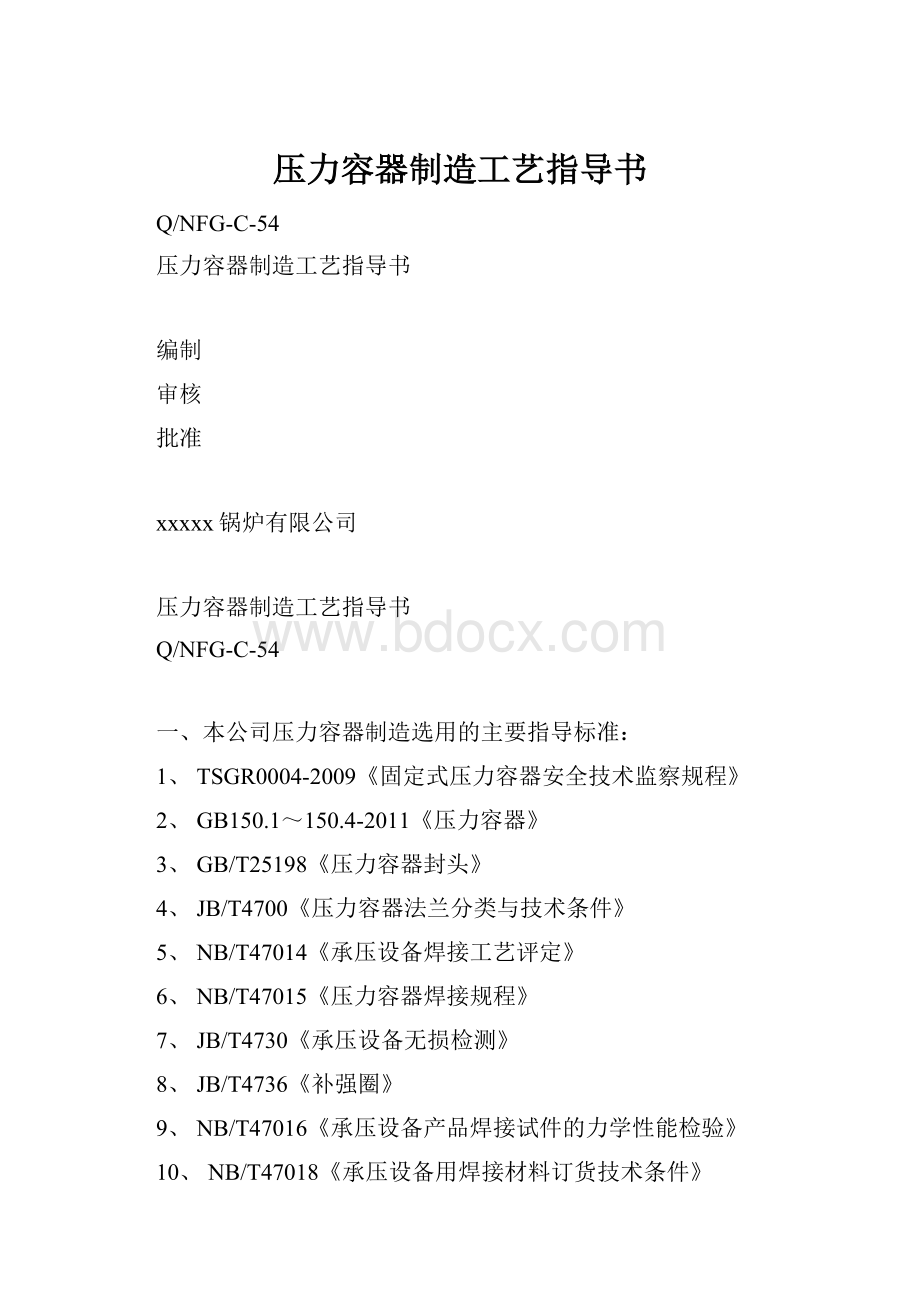
压力容器制造工艺指导书
Q/NFG-C-54
压力容器制造工艺指导书
编制
审核
批准
xxxxx锅炉有限公司
压力容器制造工艺指导书
Q/NFG-C-54
一、本公司压力容器制造选用的主要指导标准:
1、TSGR0004-2009《固定式压力容器安全技术监察规程》
2、GB150.1~150.4-2011《压力容器》
3、GB/T25198《压力容器封头》
4、JB/T4700《压力容器法兰分类与技术条件》
5、NB/T47014《承压设备焊接工艺评定》
6、NB/T47015《压力容器焊接规程》
7、JB/T4730《承压设备无损检测》
8、JB/T4736《补强圈》
9、NB/T47016《承压设备产品焊接试件的力学性能检验》
10、NB/T47018《承压设备用焊接材料订货技术条件》
11、JB/T4711《压力容器涂覆与运输包装》
二、压力容器制造工艺程序:
材料(包括受压原件)检验→筒节下料→筒节卷制→筒节纵缝组对、焊接→筒节纵缝检验→人孔短节与法兰组对、焊接→接管与法兰组对、焊接→制作支座(腿)、补强圈→筒体组对、焊接→筒体环缝检验→筒体开接管口→筒体装配接管、人孔、支座(腿)、补强圈等→补强圈泄露实验→筒体外观、管口方位尺寸检验→容器最终外观检验→水压试验→油漆。
三、压力容器制造工艺项目具体内容:
1、材料检验:
压力容器所用原材料主要是钢板,其检验主要是通过核查材料质证书、外观检查和几何尺寸检验三个方面进行。
1.1查阅材料质证书:
核实材料牌号、规格是否与图纸相同;核实材料质检标准是否与图纸指定标准相同;核实材料力学性能、化学性能和工艺性能是否符合图纸所指定标准的要求。
若有缺项和不祥的公司还要做复验。
1.2外观检验:
用目视检验钢板外表,是否有裂纹、结疤、气泡、折叠、夹层、分层等缺陷。
1.3几何尺寸件检验:
检验钢板厚度、宽度和长度尺寸,主要核实钢板厚尺寸是否在标准要求的正负偏差之内。
2、受压原件(封头、设备法兰、管法兰)检验:
2.1封头检验:
压力容器用封头,一般形状是椭圆形、蝶形、平底形和锥形4种,检验内容主要有5个方面,即封头成形后外周长或内直径、封头的直边倾斜度、凸形封头内表面形状尺寸、封头的直边部分有无纵向皱折、蝶形、锥形和平底形封头过渡段转角半径。
2.1.1封头外周长或内直径检验:
用卷尺量封头外端口尺寸,然后对照该标准要求尺寸公差,确定此项是否合格;用板尺或卷尺从不同的4个方向量封头端口内直径,然后对照该标准要求尺寸公差,确定此项是否合格。
2.1.2封头直边倾斜度检验:
在封头端面直径方向拉一根钢丝或放一直尺,用直角尺的一直角边与拉紧的钢丝或直尺重合,另一直角边与封头接触,在直边部位测量直角尺与封头间的最大距离即为封头的直边倾斜度,然后对照该标准要求尺寸,确定此项是否合格。
2.1.3凸形封头内表面形状尺寸:
用封头轮廓样板从封头内侧,样板垂直于待测表面,测量样板与封头内表面间的最大间隙;标准要求外凸不得大于1.25%Di;内凹不得大于0.625%Di。
2.1.4封头的直边部分有无纵向皱折:
用目视观察即可,标准要求不得有皱折。
2.1.5蝶形、锥形和平底形封头过渡段转角半径检验:
根据图纸尺寸预制弧形板,再用弧形板实测,确定是否合格。
2.2设备法兰检验:
用标准或图纸对照实物测量各尺寸,核实材质。
名义尺寸照图,需要相互配合公差尺寸,参照标准GB/T1801-1999选用;不是配合,不需公差尺寸,参照GB/T1804-1992选用;通过测量,参照标准有关数据,确定是否合格。
2.3管法兰检验:
用标准或图纸对照实物测量各尺寸,核实材质。
名义尺寸照图,尺寸公差照标准规定。
通过测量,参照标准有关数据,确定是否合格。
3、下料:
3.1材料标记移植:
需下料的钢板带有标记,在下料划线前操作人员必须按《产品钢印及标记移植工艺守则》在钢板余料上进行钢印(或标记)移植,无标记移植或标记不完整的不得流入下道工序。
3.2划线:
3.2.1钢材若存在影响划线的弯曲、凹凸不平时,应先进性矫正;划线前,钢材表面必需清理干净,去掉锈蚀、油污等;应按设计图样,工艺文件在钢板上以1:
1实样进行划线,划线时应留出适当的切割余量。
3.2.2筒节下料的展开长度依据来源图纸和相接封头实测值确定。
名义尺寸:
D筒中经×3.14±公差
实测尺寸1:
量相接封头端口外圆-封头壁厚×3.14±公差
实测尺寸2:
(量相接封头内径+封头壁厚)×3.14±公差
3.2.3钢板划线的尺寸偏差值应不大于尺寸公差值得三分之一,如果下料后为方形或矩形板时,则划线时对角线长度差应不大于板材下料时对角线长度差的三分之一。
3.2.4、筒体等重要工件划线应进行100%检验,其他工件则应做好首检和抽检工作,抽检的数量按工件的情况和相关规定。
3.3下料:
3.3.1下料有机械下料和火焰气割下料,根据公司目前条件,仅采用火焰气割下料。
3.3.2提供切割的工件表面应平整、干净、如果表面凹凸不平或有严重油垢、锈蚀等不得进行切割。
3.3.3为减少工件变形和利于气割排渣,工件应垫平或选放好支点,且工件下面留出一定高度的空间。
3.3.4切割工件时,应选择在余料较大部分结束切割,防止工件受热变形而是工件移动,影响工件尺寸,在切割细长条工件时应采用断续切割或双边同时切割。
3.3.5切割之前,应预先根据切割件的厚度配置相应的割嘴型号,同时调整好与板厚相应的切割氧压力和可燃气体的压力。
3.3.6应根据可燃气体性质,对割件切口处采用中性焰预热至切口处的氧流中燃烧的温度,即可行走切割(割件越厚,预热时间越长)。
3.3.7切割速度与切割厚度、切割氧纯度与压力,割嘴的氧流孔道形状等有关,切割速度正确与否,主要根据割纹的后拖量大小来判断,氧气纯度为99.8%,机械直线切割时割速与后拖量的关系见下表:
切割厚度(mm)
5
10
15
20
25
割速(mm/min)
500~800
400~600
400~550
300~500
200~400
后拖量(mm)
1~2.6
1.4~2.8
3~9
2~10
1~15
3.3.8割嘴倾角直接影响切割速度和拖量,直线切割时,割嘴倾角见下表,曲线切割时,割嘴应垂直于工件。
割嘴类型
割件厚度(mm)
割嘴倾角
普通割嘴
<6
后倾5°~10°
6~30
垂直于工件表面
>30
始割前倾5°~10°,割穿后,垂直割近终点时前倾5°~10°
快速割嘴
10~16
后倾20°~25°
17~22
后倾5°~15°
23~30
后倾15°~25°
3.3.9根据割件厚度选好割嘴及规范参数后,即可点火调整预热火焰,并试开切割氧,检查切割氧是否挺直清晰,符合切割要求。
3.3.10用预热火焰将切口始端预热到金属的燃点(呈亮红色),燃后打开切割氧,待切口始端被割穿后,即移动割矩进入正常切割。
氧─乙炔手工气割
割件厚度(mm)
割距及割嘴号
氧气压力(MPa)
乙炔压力(MPa)
切割速度(㎜/min)
3~12
G01-30
1~2
0.4~0.5
0.01~0.12
400~550
13~30
2~3
0.5~0.7
300~400
32~50
G01-100
1~2
0.5~0.7
250~300
52~100
2~3
0.6~0.8
200~250
3.3.11采用等离子弧切割下料时,应选择与切割板厚相匹配的割炬(抢)或喷嘴,气路和水路系统畅通,电极完好,气体的压力在切割过程中应保持在0.4~0.55MPa,等离子切割不锈钢时的工艺参数见下表:
等离子弧切割不锈钢
厚度(mm)
电弧电压(V)
电弧电流(A)
切割速度(m/h)
12
16
20
25
30
40
60
70
80
100
110~140
130~140
130~140
130~140
140~150
140~150
140~150
140~150
145~150
150~160
150~160
200~210
200~210
240~250
270~280
320~340
370~380
390~400
400~420
500~600
100~130
85~95
70~80
45~55
30~35
25~30
13~15
10~12
8~9
9~12
3.3.12除图样标有明确的尺寸偏差以外,下料长度尺寸偏差、截面垂直度、对角线长度差应符合下表:
下料方式
下料长度
长度偏差(±)与截面垂直度
截面垂线度
对角线长度差
板厚t
t<12
12<t<20
20<t<30
t>30
气割
L≤500
1.5
1
2
1.5
2.5
2
3
2.5
不大于下料长度的2%,且最大不超过2.5
3
500<L<1500
2
2.5
3
3.5
1500<L<2500
2.5
3
3.5
4
4
2500<L<4000
3
3.5
4
4.5
4000<L<6000
3.5
4
4.5
5
L>6000
4
4.5
5
5.5
4、筒节卷制:
4.1卷制前准备:
4.1.1卷制前操作者应熟悉有关图样和工艺文件。
4.1.2卷制前操作者应了解《压力容器制造通用工艺守则下料》中的有关要求并对钢板坯料进项检查,材质标记应放在外侧。
4.1.3筒节的下料长度尺寸一般应与之相配的管板、法兰或封头冲压成形的尺寸相适应,以保证筒体和管板、法兰、或封头环缝对接质量。
4.1.4钢板卷制前,应保证钢板的长、宽尺寸偏差和对角线长度之差,且符合图样或《压力容器制造通用工艺守则下料》中的有关规定,检验合格后方可转入冷卷工序。
4.1.5被卷钢板必须清除气割毛刺及金属飞溅物,钢板表面及边缘必须光洁、平整,对接口(或坡口)端面及两侧不小于20mm范围内必须清除油污、铁锈、氧化皮等。
4.1.6钢板卷制前开动卷板机进行空车运转检查,各转动部分运转正常,方可进行卷制。
4.2卷制过程:
4.2.1在三辊卷板机上卷制时,钢板两端一般应预弯,预弯长度应大于三辊卷板机两个下辊中心距尺寸的二分之一,在预弯长度内,预弯圆弧与检查样板(检查样板曲率半径的公称尺寸应比图样名义尺寸小0.5~1mm)间隙h≤1.0mm。
4.2.2预弯时应随时用样板检查预弯圆弧,局部有凸起或凹进的地方,可用钢板条作衬垫来校正。
用卷板机预弯时,可分两次完成,第一次卷弯时,可使圆弧曲率半径约大于要求值得10%,第二次卷弯时应达到要求值。
4.2.3被卷钢板应放在轴辊长度方向的中间位置,并对钢板位置进行校正,使钢板接口边缘与轴辊中心线平行。
4.2.4卷制时应使钢板起始卷制段逐渐弯曲卷制至适宜曲率半径,之后再连续卷制成筒状。
4.2.5用三辊卷板机时,应多次调整上辊向下移动,使钢板弯曲,卷制成筒体,上辊每下降一次开动卷板机,使工件在卷板机上往返卷一至二次,对不同直径的工件,卷板机上轴辊下降参照下表:
设备能力
筒体内径
800
900
1000
1200
1400
1600
1800
20×2000
31
28
26
22
19
17
15
30×2500
78
72
66
57
49
44
41
注:
以上数值表未考虑钢板本身的弹性回量。
4.2.6在每一次调整三辊卷板机上轴辊下移后卷弯时,都需用样板检查钢板圆弧曲率大小,直至完全符合样板为止。
4.2.7在卷制过程中,应使钢板两侧边缘与轴辊中心垂直,应经常进行检查以防跑偏造成端面错口。
4.2.8在卷制过程中,应调整卷板机的轴辊使其互相保持平行,以避免卷制出的筒体出现锥形。
4.2.9在卷制过程中,钢板必须随卷板机轴辊同时滚动,不应有滑动现象。
如出现滑动应立即排出。
4.2.10筒体卷制成形后用专用纵缝对接装置将纵缝对接口对平,两端面对齐,对接口间隙应符合图样和焊接工艺的要求,a=1~2㎜。
4.2.11定位焊接完成后,必须有检验人员对筒体对接边缘偏差和端面纵向错口按《钢制压力容器》的要求重点检查,对口错边量≤1/4δ,合格后方可转入焊接工序。
4.2.12应用气割方法切除引、收弧及焊接试板(不允许用锤击方法去除),气割部位必须用砂轮修磨平整。
5、筒节纵缝焊接:
5.1焊前准备:
焊钳焊工应阅读和熟练公司下达的该产品焊接工艺规程,领取相关的焊接材料,准备制备焊接坡口和配合铆工进行定位焊。
5.1.1焊工根据焊接工艺规程指定的焊材品种、规格,统计数量申请和领取相应的焊接材料,然后送入烘干室烘干待用。
5.1.2焊工根据焊接工艺规程指定的破口形状与尺寸制备焊缝坡口(筒节卷焊前进行)。
5.1.3待筒节卷制好纵缝组对完毕时,焊工应配合铆工定位焊接。
5.2焊接
5.2.1工艺人员应根据焊件设计文件、服役要求和制造现场条件,依据评定合格的焊接工艺,从实际出发,按每个焊接接头编制焊接工艺规程。
5.2.2焊工应按图样,工艺规程和技术标准施焊。
5.2.3焊接环境:
焊接环境出现下列任一情况时,应采取有效防护措施,否则禁止施焊:
a)风速:
气体保护焊大于2m/s,其他焊接方法大于10m/s;
b)相对湿度大于90%;
c)焊件温度低于-20℃;
5.2.4当焊件温度为-20℃~0℃时,应在施焊处100mm范围内预热到15℃以上。
5.2.5纵焊缝应在引弧板上引弧,弧坑应填满,禁止在非焊接部位引弧。
5.2.6防止底线、电缆线、焊钳等于焊件打弧。
5.2.7多层焊时,应注意层件清理,将焊缝表面熔渣,有害氧化物、油脂锈迹等清楚干净后再继续施焊。
5.2.8双面焊须清理焊根,显露出正面打底的焊缝金属。
5.2.9接弧处应保证焊缝与融合。
5.2.10施焊过程中应控制焊道温度不超过规定的范围。
5.2.11焊工施焊完毕,在焊缝要求位置打好焊工标识。
5.3焊接返修:
5.3.1返修前应将缺陷清除干净。
5.3.2待返修部位应制备坡口,坡口形状与尺寸要防止产生焊接缺陷且便于焊工操作。
5.3.3返修焊缝性能和质量要求应与原焊缝相同。
5.4焊接工艺:
本公司所制造的压力容器材质分三类,即低碳钢、低合金钢和奥氏体不锈钢。
常用的焊接方法有焊条电弧焊、埋弧自动焊、钨极氩弧焊及熔化极气体保护焊。
采用的具体焊接方法是根据待制造压力容器的直径选择的。
≤DN800的容器采用单面焊双面成型技术,其方法一,氩弧焊打底,焊条电弧焊盖面;方法二,焊条电弧焊打底,埋弧自动焊盖面。
>DN800的容器采用双面埋弧自动焊。
这些方法都有各自的焊接工艺,所有的焊接工艺都有焊接工艺评定合格的工艺支持。
若需要请参阅公司压力容器制造通用工艺规程─焊接工艺规程。
6、筒节校圆:
6.1筒节纵焊缝焊接完毕经检验合格后,拿到卷板机上校圆,校圆应随时用样板检查,要求圆弧曲率尽量均匀,使D─D(圆度)和棱角度ΔC符合《压力容器的规定》。
6.2质量检验:
按产品图样及《压力容器》的规定,对卷制的筒体进行检查。
6.2.1筒节圆度检查:
用卷尺或板尺量筒体同一断面上最大内经与最小内径之差,应不大于该断面内径Di的1%,且不大于25mm。
6.2.2筒节环向棱角度ΔC检查:
用弦长等于Di/6,且不小于300mm的内样板(或外样板)和直尺检查棱角度ΔC值不得大于(δs/10+2)mm,且不大于5mm。
7、人孔短节与法兰组对、焊接
7.1人孔短节与法兰组对
组对时法兰面应垂直筒节轴线,其偏差值≤3mm。
7.2人孔短节与法兰焊接
人孔短节与法兰焊接,根据容器受力不同,分平焊与对接焊。
平焊:
人孔短节伸入法兰内孔一定深度,短节上口和法兰内孔角焊,法兰下口内径与短节外壁角焊。
对接焊:
人孔短节与法兰下口对接焊(应控制组对间隙0~1mm,错边量≤1/4δs)。
8、接管与法兰组对、焊接
8.1接管与法兰组对
组对时法兰面应垂直接管轴线,其偏差值≤2mm。
8.2接管与法兰焊接
接管与法兰焊接,根据容器受力不同,分平焊与对接焊。
平焊:
接管伸入法兰内孔一定深度,接管上口和法兰内孔角焊,法兰下口内径与接管外壁角焊。
对接焊:
接管与法兰下口对接焊(应控制组对间隙0~1mm,错边量≤1/4δs)。
9、制作制造(鞍座)
9.1支座筋板、腹板、底板等按图尺寸下料,然后去除毛刺。
9.1腹板按图纸要求的弧度卷弧,一般是120°。
9.3支座组对,要求筋板与底板垂直,组对时用直角尺协助,组对好后焊工点固焊定位。
9.4组对的焊缝由焊工施焊,基本都是角焊缝。
10、筒体组对、焊接
10.1筒体组对:
组对分筒节与筒节组对和上下封头与筒节组对,应内壁平齐,要求⑴对口间隙a=1~2mm;⑵对口错边量≤1/4δ;⑶棱角度≤δ/10+2,组对好后固定焊。
10.2筒体焊接(环缝焊)
10.2.1焊前准备:
焊钳焊工应阅读和熟练公司下达的该产品焊接工艺规程,领取相关的焊接材料,准备制备焊接坡口和配合铆工进行定位焊。
10.2.1.1焊工根据焊接工艺规程指定的焊材品种、规格,统计数量申请和领取相应的焊接材料,然后送入烘干室烘干待用。
10.2.1.2焊工根据焊接工艺规程指定的坡口形状与尺寸制备焊缝坡口(筒节卷焊前进行)。
10.2.1.3待筒节卷制好纵缝组对完毕时,焊工应配合铆工定位焊接。
10.2.2焊接
10.2.2.1工艺人员应根据焊件设计文件、服役要求和制造现场条件,依据评定合格的焊接工艺,从实际出发,按每个焊接接头编制焊接工艺规程。
10.2.2.2焊工应按图样,工艺规程和技术标准施焊。
10.2.2.3焊接环境:
焊接环境出现下列任一情况时,应采取有效防护措施,否则禁止施焊:
d)风速:
气体保护焊大于2m/s,其他焊接方法大于10m/s;
e)相对湿度大于90%;
f)焊件温度低于-20℃;
10.2.2.4当焊件温度为-20℃~0℃时,应在施焊处100mm范围内预热到15℃以上。
10.2.2.5环焊缝应在引弧板上引弧,弧坑应填满,禁止在非焊接部位引弧。
10.2.2.6防止底线、电缆线、焊钳等于焊件打弧。
10.2.2.7多层焊时,应注意层件清理,将焊缝表面熔渣,有害氧化物、油脂锈迹等清楚干净后再继续施焊。
10.2.2.8双面焊须清理焊根,显露出正面打底的焊缝金属。
10.2.2.9接弧处应保证焊缝与融合。
10.2.2.10施焊过程中应控制焊道温度不超过规定的范围。
10.2.2.11焊工施焊完毕,在焊缝要求位置打好焊工标识。
10.2.3焊接返修:
10.2.3.1返修前应将缺陷清除干净。
10.2.3.2待返修部位应制备坡口,坡口形状与尺寸要防止产生焊接缺陷且便于焊工操作。
10.2.3.3返修焊缝性能和质量要求应与原焊缝相同。
10.2.4焊接工艺:
本公司所制造的压力容器材质分三类,即低碳钢、低合金钢和奥氏体不锈钢。
常用的焊接方法有焊条电弧焊、埋弧自动焊、钨极氩弧焊及熔化极气体保护焊。
采用的具体焊接方法是根据待制造压力容器的直径选择的。
≤DN800的容器采用单面焊双面成型技术,其方法一,氩弧焊打底,焊条电弧焊盖面;方法二,焊条电弧焊打底,埋弧自动焊盖面。
>DN800的容器采用双面埋弧自动焊。
这些方法都有各自的焊接工艺,所有的焊接工艺都有焊接工艺评定合格的工艺支持。
若需要请参阅公司压力容器制造通用工艺规程─焊接工艺规程。
11、筒体焊缝检验
11.1焊缝外观检查,不得有气孔、夹渣、裂纹,焊缝余高在要求范围。
11.2焊缝进行RT无损检测,根据图样和B/T4730-2005规定要求确定合格等级。
12、筒体开接管孔
12.1按图纸及管口方位图划出各接管、人孔位置及孔径大小;
12.2按图纸及管口方位图检查容器划线开孔位置尺寸准确性,确定是否开孔。
12.3按划线尺寸和《产品焊接工艺规程》气割开孔并修磨坡口。
13、筒体装配接管、人孔、支座
13.1将事先预制好的接管和法兰装配于筒体。
接管轴线与筒体轴线相垂直,装时用直角尺协助确定方向,插入合适的高度和方向摆正后,由焊工定位焊固定。
13.2将事先预制好的人孔短节和法兰装配于筒体。
人孔短节轴线与筒体轴线相垂直,装时用直角尺协助确定方向,插入合适的高度和方向摆正后,由焊工定位焊固定,然后进行焊接,最后将人孔盖装入,固定螺栓,螺母拧紧。
13.3将事先预制好的支座装配于筒体。
装配时主要控制两支座中心线位置,特别是两支座底板上孔眼的距离。
另外支座的中心线应与设备中心线重合,支座两底板平行并设备中心线垂直。
14、补强圈泄露实验
在补强圈检查孔上接空气管,然后通过空气管向补强圈与壳体间注入空气,注入的空气压力达到设计压力时开始保压,保压期间用肥皂水刷补强圈内圈、外圈的角焊缝和壳体内侧短节与壳体相焊焊缝,检查是否泄露,若经检查不漏并保压认为合格。
15、容器最终检查
15.1容器内、外表面检查。
检查容器在再造中表面是否有机械损伤,对于尖锐伤痕以及不锈钢容器内腐蚀表面的局部伤痕、刻槽等缺陷应预以修磨,修磨斜度最大为1:
3.修磨的深度应不大于该部位钢材厚度的δ0的5%,且不大于2mm,否则应予补焊。
15.2所有接管质量检查,检查接管的垂直度,伸长尺寸,方位尺寸,法兰密封面是否有划伤、飞溅物、接管焊缝外观有无气孔、夹渣,焊角高度是否符合要求。
15.3人孔组装质量检验,检查人孔方位尺寸、检查人孔短节与筒体、与人孔法兰垂直成度,检查人孔盖与法兰开合是否自如,检查人孔所有焊缝外观是否符合要求,检查补强圈是否已做泄露实验。
15.4实测筒体的几何尺寸与垂直度,并做好记录。
15.5检查筒体所有焊缝外观,是否有气孔、夹渣等缺陷,余高是否都在要求范围。
15.6实测两支座中心线距离和底板的孔距,看是否符合图纸要求,并检查两支座外观与焊缝。
16、水压试验、气密性试验
16.1压力容器的水压试验,应在容器本体全部组装完毕,一切受压原件的焊接和热处理完毕,无损探伤及有关检查项目合格后进行。
16.2制造完毕的压力容器应按设计文件规定进行水压试验。
16.3水压试验时,如采用压力表测量试验压力,则应使用两个量程相同的,并经鉴定合格的压力表。
压力表的量程应为1.5~3倍的试验压力,宜为试验压力的2倍。
压力表的精度不得低于1.6级,表盘直径不得小于100mm。
16.4水压试验的试验压力应按图纸要求。
16.5水压试验前,容器各连接部位的紧固件应装配齐全,并紧固妥当;为进行水压试验而装配的临时受压元件,应采取适当的措施,保证其安全性。
16.6试验用压力表应安装在被试验容器安放位置的顶部;
16.7水压试验保压期间不得采用连续加压以维持试验压力不变,实验过程中不得带压拧紧紧固件或对受压原件施加外力。
16.8带套容器应先进行内筒水压试验,合格后再焊夹套,然后再进行夹套的水压试验。
16.9水压试验合格后应立即将水排净吹干;无法完全排净吹干时,对奥氏体不锈钢容器,应控制水的氯离子含量不超过25mg/L。
16.10试验温度:
Q345R、Q370R、07MnMoVR容器进行水压试验时,水温度不得低于5℃,其他碳素钢和低合金钢制容器进行水压试验时,水温度不得低于15℃。
16.11试验程序和步骤:
a、试验容器内的气体应当排净并充满水,试验过程中,应保持容器观察表面