白车身零件工装供应商标准通则.docx
《白车身零件工装供应商标准通则.docx》由会员分享,可在线阅读,更多相关《白车身零件工装供应商标准通则.docx(15页珍藏版)》请在冰豆网上搜索。
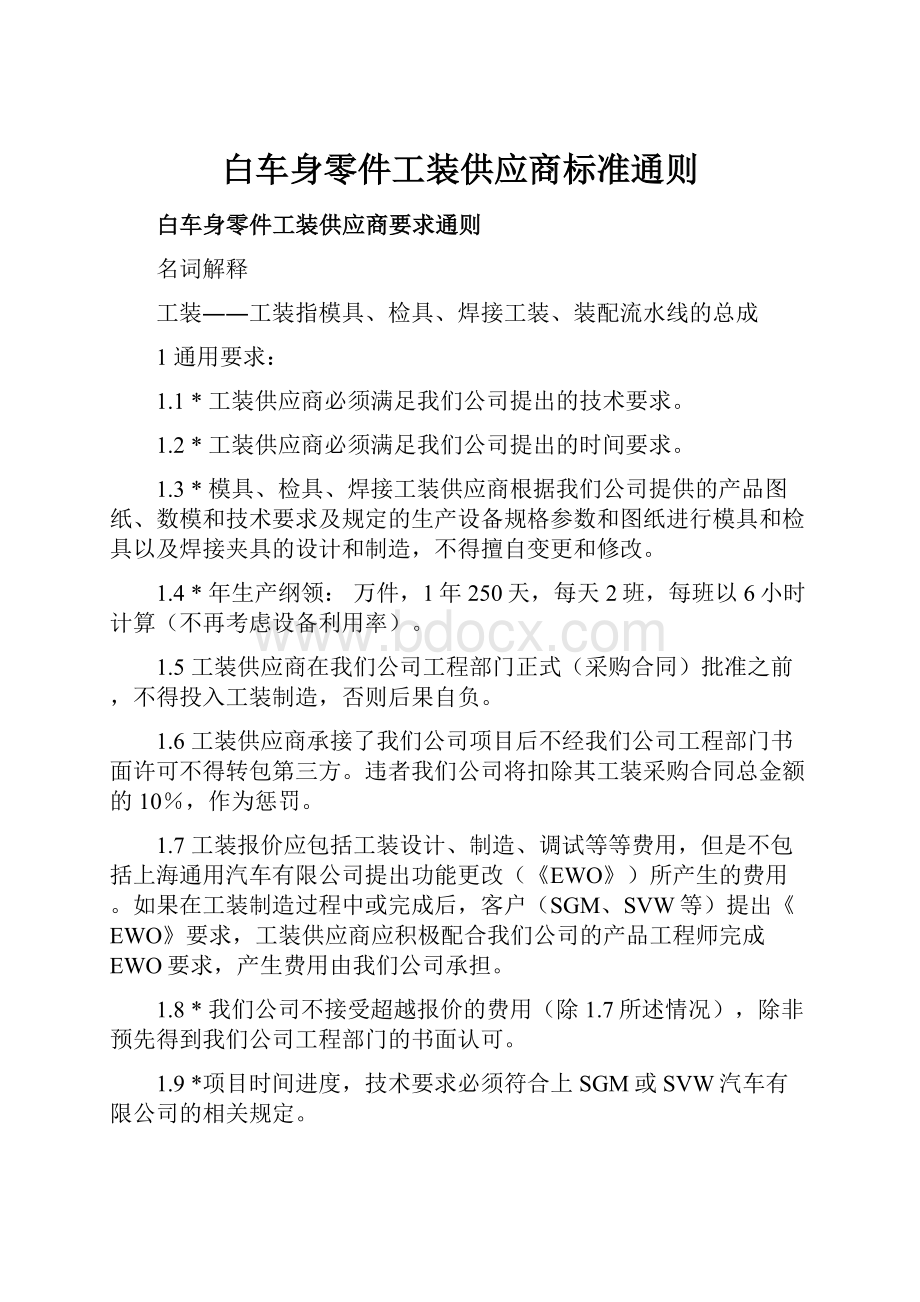
白车身零件工装供应商标准通则
白车身零件工装供应商要求通则
名词解释
工装――工装指模具、检具、焊接工装、装配流水线的总成
1通用要求:
1.1*工装供应商必须满足我们公司提出的技术要求。
1.2*工装供应商必须满足我们公司提出的时间要求。
1.3*模具、检具、焊接工装供应商根据我们公司提供的产品图纸、数模和技术要求及规定的生产设备规格参数和图纸进行模具和检具以及焊接夹具的设计和制造,不得擅自变更和修改。
1.4*年生产纲领:
万件,1年250天,每天2班,每班以6小时计算(不再考虑设备利用率)。
1.5工装供应商在我们公司工程部门正式(采购合同)批准之前,不得投入工装制造,否则后果自负。
1.6工装供应商承接了我们公司项目后不经我们公司工程部门书面许可不得转包第三方。
违者我们公司将扣除其工装采购合同总金额的10%,作为惩罚。
1.7工装报价应包括工装设计、制造、调试等等费用,但是不包括上海通用汽车有限公司提出功能更改(《EWO》)所产生的费用。
如果在工装制造过程中或完成后,客户(SGM、SVW等)提出《EWO》要求,工装供应商应积极配合我们公司的产品工程师完成EWO要求,产生费用由我们公司承担。
1.8*我们公司不接受超越报价的费用(除1.7所述情况),除非预先得到我们公司工程部门的书面认可。
1.9*项目时间进度,技术要求必须符合上SGM或SVW汽车有限公司的相关规定。
1.10我们公司提供零件的数据信息、技术标准、冲压设备、焊接设备技术资料。
我们公司提供的工艺流程图、检具GD&T仅供工装供应商参考。
1.11*工装供应商承担工艺设计、工装设计、制造、调试、培训及售后服务的全部责任。
1.12*工装供应商负责相关的零件认可,直至通过客户(SGM、SVW等)的PPAP(生产件批准程序)认可,并正式生产一年后结束。
1.13*我们公司工装的付款方式为,采购合同确立10工作日内预付10%合同款,设计会签后5工作日预付20%,客户的功能匹配或预验收认可后付30%合同款,最终验收后付30%合同款,PPAP认可后正式生产一年后付清全部合同款。
1.14工装供应商须明确固定的项目联系人与我们公司联系,并提供有效的联系方式。
同时,工装供应商须明确我们公司相关的联系人员及联系方式。
我们公司的联系人通常是相关的产品工程师或项目负责工程师。
1.15工装供应商提供给我们公司的技术资料须用公制描述。
1.16*我们公司要求的工装寿命为30万台套。
1.17我们公司提供的技术资料未经我们公司工程部书面许可,不得传于第三方。
2模具供应商要求概述:
2.1*模具供应商承担相关零件的制造工艺、工艺方案图、模具设计、制造、调试、培训及售后服务的全部责任及费用。
2.2我们公司提供相关零件的图纸、数模、涉及产品的技术标准以及冲压设备的技术资料,并对这些资料的有效性承担责任。
其他资料仅供供应商参考。
2.3*合同确立后,模具供应商每周五向我们公司项目工程师汇报项目进度,进度报告使用清晰的照片或数码照片结合文字说明的方式。
电子邮件的方式传递。
模具供应商进度延误造成我们公司整体国产化计划延误,每延误5个工作日我们公司将扣除合同总金额的5‰。
2.4我们公司与模具供应商的相关要求须3个工作日内答复,未能答复要互相告知理由。
2.5零件制造工艺设计及模具设计要求:
2.5.1模具供应商在合同确立前须提供相关零件的工艺流程方案。
我们公司工作人员未经供应商许可,不得将工艺流程方案提供给第三方。
2.5.2相关零件的工艺流程应该考虑到我们公司的利益。
2.5.3模具供应商须提供相关零件的过程失效模式分析(PFMEA)。
分析结果按规定格式要求输出。
2.5.4模具供应商须提供模具设计制造的设计失效模式分析(DFMEA)。
分析结果按规定格式要求输出。
DFMEA可分为模具设计阶段、制造阶段、调试阶段分别分析并提供文件输出。
2.5.5模具设计阶段,我们公司建议模具供应商进行有限元模拟分析,降低模具制造风险。
有限元分模拟分析的结果提供给我们公司工程部。
我们公司会优先选择具有有限元模拟分析的模具供应商。
2.5.6模具设计标准采用汽模标准或经过业主方签字认可后的投标方所提供的标准。
根据冲压零件形状尺寸优先采用铸模。
2.5.7*模具供应商在工艺流程方案中须提供零件制造的材料利用率,材料利用率如果达不到60%,供应商须在设计阶段得到产品工程师书面认可。
否则,不能交付。
2.5.8模具设计时须考虑是否便于操作以及日常维修,须考虑操作、维修、放置运输时的安全性。
模具设计前须及时提供有限元模拟分析资料及DL图及排样图会审。
2.5.9模具设计须符合我们公司提供冲压设备的技术资料。
单付模具冲压中心须符合机床的压力中心。
2.5.10模具设计时尽可能采用冲压机床的气垫。
2.5.11组合安装的模具,设计时须考虑整体的冲压中心与机床压力中心一致,还须考虑机床气垫受力的平衡。
2.5.12模具设计时,冲压最大负荷力应≯选用压机许用负荷的80%。
2.5.13模具设计时,单付模具上模重量不得超过10吨,整体重量不得超过20吨。
2.5.14模具设计时须考虑材料送进和取出的方式,便于工人操作;废料须排出模具,废料长度不得超过300mm。
2.5.15模具设计时须保证同一零件的模具闭合高度一致,允许高度差为±2.5mm。
2.5.16模具设计时须考虑模具与机床之间的安装V型定位槽,定位方式为定位销定位。
我们公司提供定位销的尺寸。
2.5.17*模具设计应采用标准件,供应商须提供每套模具选用所有标准件规格的技术资料清单,建议标准件采用盘起(PUNCH)标准件,每套模具不同规格尺寸的冲头、凹模及特殊刀口镶块易损件需各提供5件备件。
2.5.18模具设计时须考虑零件定位的合理性、可靠性,并且模具应具备防错功能。
2.5.19*模具寿命为30万台套。
除特别要求外。
2.5.20*模具材料允许使用GM241、GM190、SKD11、ICD5、HMD5或GB/T14662表1、表2上规定的材料。
供应商必须提供使用材料的化学成分、机械性能、热处理硬度范围。
铸件必须留出样棒供验证材质性能。
2.5.21模具设计及零件制造工艺设计须得到我们公司产品工程师及模具工程师的书面(会签)认可。
2.6模具制造要求
2.6.1模具机加工、装配、研磨须以模架为基准。
2.6.2凹、凸模间隙合理。
凹、凸模研磨着色面≮85%
2.6.3*模具表面质量:
2.6.3.1拉伸/成型模表面硬度达到HRC56~62,钼铬铸铁拉伸/成型模表面硬度达到HRC50~55,凸模表面粗糙度0.8、压料圈表面粗糙度0.8。
2.6.3.2冲裁类模具刃口表面硬度达到HRC56~62。
2.6.3.3翻边类模刃口圆角表面硬度达到HRC58~64,表面粗糙度达到0.8。
2.6.4模具上须清楚表明正、反方向、送料方向以及模具编号。
模具编号由我们公司提供。
2.6.5模具上须有铭牌,铭牌清晰上记录模具编号、冲压吨位、模具在机床上的位置、模具闭合高度、气垫顶杆位置、顶杆高度、气垫压力。
2.6.6冲裁类模具刃口镶块间隙小于0.15mm。
2.6.7模具中超过20KG的部件必须有起吊装置。
2.6.8模具模架涂色按照《技术协议》的相关规定、起重装置和安全部件整体涂成红色或作明显得红色标记、定距块、废料槽、送料架等其他部件表面涂成黄色。
2.6.9*试模及FE3前交样的材料费用由供应商负责,可向我公司购买规定牌号的材料。
2.6.10*试模时,零件材料不能用拉伸油或其他润滑手段。
2.6.11*高强度板零件,的拉延模、成形模、整形模、折边模的主体模心要采用合金钢材料。
2.6.12*在我们公司JH36-250冲床上使用的拉延模、成形模需要用氮气缸提供反向力。
2.7模具相关文件的要求:
2.7.1模具供应商在确立采购合同前提供模具的报价单、零件制造的初步工艺流程图、模具制造的时间进度。
2.7.2模具设计和零件制造工艺流程审核时模具供应商须提供相关零件的制造工艺流程图、零件制造过程的PFMEA、模具设计的DFMEA。
2.7.3合同确立后,模具供应商须每周五下午,向我们公司产品工程师汇报合同进度,使用清晰的照片或数码照片结合文字说明的方式。
电子邮件的方式传递。
2.7.4模具交付时模具供应商须提供模具结构图纸或电子文档(两套)、自制零部件图纸或电子文档(两套)。
选用标准件的规格清单、模具选用材料的化学成分和机械性能及热处理检测报告。
上述资料未经双方同意,不得转给第三方。
2.7.5模具设计的最终数学模型(CAD)、所有模具加工的NC数据、所有有限元模拟分析的数据、所有选用标准件的数学模型归模具供应商与我们公司共有。
模具供应商须提供给我们公司。
上述资料未经双方同意,不得转给第三方。
2.7.6我们公司提供的关于零件的技术资料所有权归上海通用汽车有限公司。
模具供应商在模具交付时,须将这些资料交还给我们公司。
2.7.7模具发运前两周,模具供应商必须提供《模具维修保养手册》和《模具使用培训手册》及其电子文档。
2.7.8*模具供应商在开发过程中提供的样件必须附有CMM测量报告,划线样件必须符合客户的划线要求。
2.8模具验收原则:
2.8.1零件尺寸验收以检具为验收标准。
2.8.2模具发运至我们公司生产现场前,须进行模具的预验收。
2.8.3预验收包括静态验收和动态验收两部分。
2.8.4模具供应商须满足标书中对模具供应商的要求以及经济合同中对供应商的要求,模具才能最终验收。
2.8.5*最终验收须在我们公司的生产现场完成。
最终验收须冲压不少于300件零件。
2.8.6最终验收通过要求,零件须满足我们公司提供的技术图纸、数模,零件的Cpk值≮1.33。
同时模具也须满足双方签订的《技术协议》。
2.8.7模具最终验收通过之日起,发生模具损坏,由双方共同鉴定,若属模具制造问题,由投标方无条件提供修理;若属使用保养问题,由双方协商解决。
2.9*培训
2.9.1模具供应商必须对我们公司操作工人进行培训。
2.9.2培训在我们公司的正式生产厂地上进行。
2.9.3培训时间和最终调试验收同时进行,具体时间日程安排由双方协商决定。
2.9.4模具发运前两周,模具供应商须提供《模具维修保养手册》和《模具使用培训手册》及其电子文档。
经我们公司认可。
2.9.5《模具维修保养手册》必须包括(不局限于以下内容):
2.9.5.1模具结构图纸。
2.9.5.2模具维修保养的要求。
2.9.5.3模具零部件拆装的要求。
2.9.5.4模具液压部件和机械结构的功能,拆解的方法。
2.9.5.5模具中须定期清洁、保养的部分及清洁、保养的方法。
2.9.5.6模具中须定期给油的部分及给油的标准。
2.9.5.7模具所有选用材料的清单以及相对应焊接焊条的标准(焊条必须选用国家标准焊条,特殊焊条必须提供焊条标准和供应厂商)。
2.9.5.8所有模具材料的焊接要求。
2.9.5.9维修技能的要求。
如小修应该掌握的技术、焊接应该达到的要求。
2.9.6《模具使用培训手册》必须包括(不局限于以下内容):
2.9.6.1《模具安装指导书》包括模具安装的要求、模具的编号、模具在机床上的安装位置图、顶杆安装位置图、模具闭合高度、模具冲压吨位、气垫压力、顶杆高度等(这些数据须是在我们公司最终调试的结果)。
2.9.6.2生产中,零件或材料定位位置略图。
2.9.6.3安全部件的说明。
2.9.6.4维修技能的培训计划。
3检具供应商的要求:
3.1*所有检具的所有权归上海通用汽车有限公司所有。
检具的设计和制造必须符合客户(SGM、SVW等)的《FIXTURESTANDARDS》(检具标准)。
客户(SGM、SVW等)检具工程师提出的要求必须得到满足。
3.2*检具供应商承担检具设计、制造、调试、培训及售后服务的全部责任及费用。
检具供应商所选用的制造材料须得到我们公司检具工程师的认可,检具型面可采用“汽巴图5166”工程塑料,钢制底板及铝合金均要求时效处理,并提供相关的材质报告(必须时提供材料样件)。
检具使用寿命应与模具等同。
3.3我们公司提供相关零件的图纸、数模、所有客户(SGM、SVW等)提供的技术资料,并对这些资料的有效性承担责任。
其他资料仅供供应商参考。
3.4*合同确立后,检具供应商须每周五向我们公司检具工程师汇报合同进度,。
进度报告使用清晰的照片或数码照片结合文字说明的方式。
报告通过信件或电子邮件的方式传递。
检具必须在FE3之前完成制造验收,检具供应商进度延误造成我们公司整体国产化计划延误,每延误5个工作日我们公司将扣除合同总金额的5‰。
3.5我们公司与检具供应商的相关要求须3个工作日内答复,未能答复要互相告知理由。
3.6检具相关的文件要求:
3.6.1*检具设计前必须提供设计草图,在设计草图获得我们公司检具工程师审核后,才能进行检具设计。
3.6.2*检具设计完成后,设计图必须通过我们公司检具工程师和客户(SGM、SVW等)检具工程师的审核,并由客户(SGM、SVW等)检具工程师签署A表(检具设计检查表),认可后才能进行检具制造。
3.6.3*检具制造完成后,必须提交检具的CMM合格检测报告(包括所有通止规、位置规和卡板)。
3.6.4*检具交付前必须提交检具的所有图纸包括数学模型、所有通止规、位置规和卡板的图纸包括数学模型。
3.6.5检具若带有FE匹配功能,须提供所有有关图纸包括数学模型。
3.6.6*检具交付前必须提交检具的《操作指导书》电子文档,指导书的格式由双方协商决定。
检具的《操作指导书》应缩封后固定与检具上。
各检测芯棒须敲钢印和色别标识。
3.7检具验收原则:
3.7.1*检具功能验收按照客户(SGM、SVW等)的《FIXTURESTANDARDS》(检具标准)。
3.7.2检具尺寸验收原则上以供应商提供的CMM检测报告为准,我们公司只对报告进行复测认可。
3.7.3检具发运前,我们公司须进行预验收。
3.7.4*检具必须通过客户(SGM、SVW等)要求的GR&R评估(要求参见AIAGMSA手册)。
3.7.5*检具的最终验收必须在我们公司的生产场地上进行,并通过我们公司检具工程师和客户(SGM、SVW等)检具工程师的审核,由客户(SGM、SVW等)检具工程师签署B表(检具制造检查表)。
3.7.6*检具车身尺寸线须清晰无误,坐标孔及平面须用防护装置以免损坏。
3.8*培训:
3.8.1检具供应商必须对我们公司操作工人进行培训。
3.8.2培训在我们公司的正式生产厂地上进行。
3.8.3培训时间和最终调试验收同时进行,具体时间日程安排由双方协商决定。
3.8.4检具发运前两周,检具供应商必须提供《检具使用维护手册》《操作指导书》及其电子文档。
经我们公司认可。
3.8.5《检具使用维护手册》必须包括(不局限于以下内容):
3.8.5.1《操作指导书》。
3.8.5.2使用维护要求。
3.8.5.3CMM测量报告。
3.8.5.4通止规、位置规理论值和实测值的清单
4焊接工装供应商的要求
4.1*焊接工装供应商承担相关焊接工装设计、制造、调试、培训及售后服务的全部责任及费用。
4.2我们公司提供相关零件的图纸、数模、技术资料以及生产设备的技术资料,并对这些资料的有效性承担责任。
其他资料仅供供应商参考。
4.3*合同确立后,焊接供应商须每周五向我们公司指定工程师汇报合同进度,。
进度报告使用清晰的照片或数码照片结合文字说明的方式。
报告通过信件或电子邮件的方式传递。
工装供应商进度延误造成我们公司整体国产化计划延误,每延误5个工作日我们公司将扣除合同总金额的5‰。
4.4我们公司与焊接工装供应商的相关要求须3个工作日内答复,未能答复要互相告知理由。
4.5焊接工装设计要求:
4.5.1焊接工装设计的要求焊接工装供应商在合同确立前须提供相关的工艺方案。
我们公司工作人员未经供应商许可,不得将工艺方案提供给第三方。
4.5.2相关工艺方案应该考虑到我们公司的利益。
4.5.3焊接工装供应商必须提供工装设计制造的设计失效模式分析(DFMEA)。
DFMEA可分为设计阶段、制造阶段、调试阶段分别分析并提供文件输出,分析结果按SGM要求输出。
4.5.4焊接工装供应商应具备读取客户提供数模的能力。
焊接工装设计阶段,如有必要我们公司建议工装供应商进行仿真模拟分析,降低工装制造风险。
仿真模拟析的结果提供给我们公司工程部。
我们公司会优先选择具有仿真模拟分析的工装供应商。
4.5.5工装设计标准采用客户(SGM、SVW等)标准或经过业主方签字认可后的投标方所提供的标准。
4.5.6工装设计时须考虑是否便于操作以及日常维修,必须考虑操作、维修、放置运输时的安全性。
4.5.7工装设计须符合我们公司提供设备的技术资料。
4.5.8*工装设计尽可能采用标准件,气动元件(缸、阀、分离器)应采用SMC牌号元件,气管采用二层防焊接飞溅气管。
供应商须提供选用所有标准件清单。
4.5.9焊接工装设计必须考虑CMM测量机(三座标测量机)的安装位置、CMM测量机的测量范围。
4.5.10焊接工装设计须考虑焊接变形对零件的影响,预留焊接工装三维调整的余地。
焊接工装设计须考虑零件装夹的稳定性,零件定位孔与零件基准孔保持一致。
4.5.11工装设计时须考虑零件定位的合理性、可靠性。
4.5.12焊接工装制造工艺设计须得到我们公司产品工程师的书面认可。
4.6焊接工装制造的要求
4.6.1焊装夹具要求发黑或其他防锈处理,外购零件保持其本色。
其它部位颜色,由供应商按照国标或行业标准自行对应,并得到我们公司产品工程师的书面认可。
4.6.2定位销、定位块调质处理,表面硬度达到HRC42~45。
4.6.3焊接件须时效后再进行下一步加工。
4.6.4夹紧装置尽可能采用气动夹紧,夹紧器间隙小于0.1mm。
4.6.5焊接定位间隙小于0.05mm,夹紧配合面间隙小于0.1mm。
4.6.6*焊接夹具底板必须有测量基准,建议选用不锈钢的基准套,标定相对车身位置尺寸指示牌。
夹具每一个定位或夹紧面都必须三向可调±3MM。
4.6.7*焊后必须满足图纸关于焊接质量、焊接变形、总成各零件相对位置精度、尺寸精度的要求。
4.6.8夹具应操作简便、夹紧力充分、动作可靠。
4.6.9如工装超过20KG的部分须有起吊装置。
4.6.10工装调试所用零件由我们公司提供。
4.7焊接工装相关文件的要求
4.7.1焊接工装供应商在确立采购合同前提供焊接工装的报价单、零件制造的初步工艺流程图、焊接工装制造的时间进度。
4.7.2焊接工装设计和零件制造工艺流程审核时焊接工装供应商须提供相关总成零件的制造工艺流程图、零件制造过程的PFMEA、焊接工装设计的DFMEA。
4.7.3合同确立后,焊接工装供应商须每隔两周向我们公司焊接工装工程师汇报合同进展进度,每个时间节点前3天须焊接工装供应商也须向我们公司焊接工装工程师汇报合同进展。
进度报告使用清晰的照片或数码照片结合文字说明的方式。
报告通过信件或电子邮件的方式传递。
4.7.4焊接工装交付时焊接工装供应商须提供焊接工装结构图纸(两套)、自制零部件图纸(两套)、选用标准件的图纸资料或标准件手册(两套)、选用标准件的制造厂商清单、焊接工装选用材料的化学成分和机械性能报告及热处理报告。
上述资料未经双方同意,不得转给第三方。
4.7.5焊接工装设计的最终数学模型(CAD)、所有焊接工装加工的NC数据、所有选用标准件的数学模型归焊接工装供应商与我们公司共有。
焊接工装供应商必须提供给我们公司。
上述资料未经双方同意,不得转给第三方。
4.7.6我们公司提供的关于零件的技术资料所有权归上海通用汽车有限公司。
焊接工装供应商在焊接工装交付时,必须将这些资料交还给我们公司。
4.7.7焊接工装发运前两周,焊接工装供应商须提供《焊接工装维修保养手册》和《焊接工装使用培训手册》及其电子文档。
4.7.8焊接工装制造完成后,焊接工装供应商须提供焊接工装的CMM检测报告。
4.8焊接工装验收的原则
4.8.1零件尺寸验收以检具为验收标准。
4.8.2焊接工装发运至我们公司生产现场前,须进行焊接工装的预验收。
4.8.3预验收包括静态验收和动态验收两部分。
4.8.4焊接工装供应商须满足标书中对焊接工装供应商的要求以及经济合同中对焊接工装供应商的要求,焊接工装才能最终验收。
4.8.5*最终验收必须在我们公司的生产现场完成。
最终验收须生产不少于300件零件。
4.8.6最终验收通过要求,零件须满足我们公司提供的技术图纸、数模,零件的Cpk值≮1.33。
同时焊接工装也须满足双方签订的《技术协议》。
4.8.7自焊接工装最终验收通过之日起,发生焊接工装损坏,由双方共同鉴定,若属焊接工装制造问题,由投标方无条件提供修理;若属使用保养问题,由双方协商解决。
4.9培训
4.9.1焊接工装供应商必须对我们公司操作工人进行培训。
4.9.2培训在我们公司的正式生产厂地上进行。
4.9.3培训时间和最终调试验收同时进行,具体时间日程安排由双方协商决定。
4.9.4焊接工装发运至我们公司前两周,焊接工装供应商须提供《焊接工装维修保养手册》和《焊接工装使用培训手册》及其电子文档。
经我们公司认可。
4.9.5《焊接工装维修保养手册》须包括(不局限于以下内容):
4.9.5.1焊接工装结构图纸。
4.9.5.2焊接工装维修保养的要求。
4.9.5.3焊接工装零部件拆装的要求。
4.9.5.4焊接工装气压部件和机械结构的功能,拆解的方法。
4.9.5.5焊接工装中须定期清洁、保养的部分及清洁、保养的方法。
4.9.5.6焊接工装中须定期给油的部分及给油的标准。
4.9.5.7焊接工装所有选用材料的清单以及相对应焊接焊条的标准(焊条必须选用国家标准焊条,特殊焊条必须提供焊条标准和供应厂商)。
4.9.5.8所有焊接工装材料的焊接要求。
4.9.5.9维修技能的要求。
如小修应该掌握的技术、焊接应该达到的要求。
4.9.6《焊接工装使用培训手册》须包括(不局限于以下内容):
4.9.6.1《焊接工装操作指导书》
4.9.6.2生产中,零件定位位置略图。
4.9.6.3安全部件的说明。
4.9.6.4维修技能的培训计划。
5FE匹配承接商的要求
5.1*FE匹配承接商与我们公司的产品工程师共同负责相关零件上海通用汽车有限公司的FE匹配工作,并使零件通过客户(SGM、SVW等)的技术要求。
5.2*FE匹配承接商负责相关零件总成匹配工作,并使我们公司能够稳定生产该零件总成。
5.3我们公司提供相关零件的图纸、数模、技术资料以及生产设备的技术资料,并对这些资料的有效性承担责任。
其他资料仅供供应商参考。
5.4*FE匹配承接商在开发过程中提供的样件必须附有CMM测量报告,划线样件必须符合客户(SGM、SVW等)的划线要求。
5.5FE匹配承接商相关文件的要求
5.5.1FE匹配承接商在匹配过程中有权提出分零件的更改申请,更改申请须以书面形式提出。
表式由我们公司提供。
5.5.2我们公司相关产品工程师和工装工程