单晶硅.docx
《单晶硅.docx》由会员分享,可在线阅读,更多相关《单晶硅.docx(10页珍藏版)》请在冰豆网上搜索。
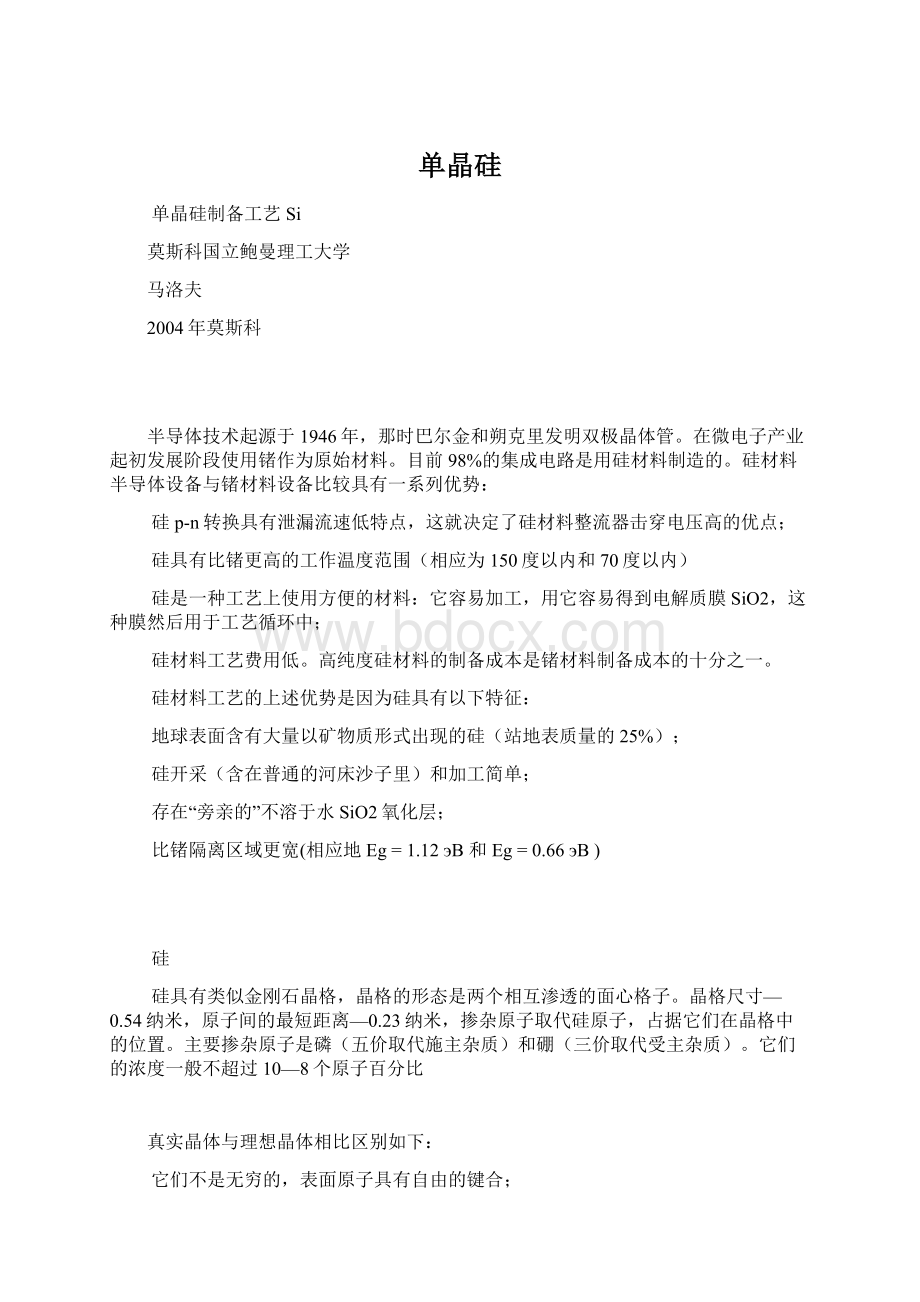
单晶硅
单晶硅制备工艺Si
莫斯科国立鲍曼理工大学
马洛夫
2004年莫斯科
半导体技术起源于1946年,那时巴尔金和朔克里发明双极晶体管。
在微电子产业起初发展阶段使用锗作为原始材料。
目前98%的集成电路是用硅材料制造的。
硅材料半导体设备与锗材料设备比较具有一系列优势:
硅p-n转换具有泄漏流速低特点,这就决定了硅材料整流器击穿电压高的优点;
硅具有比锗更高的工作温度范围(相应为150度以内和70度以内)
硅是一种工艺上使用方便的材料:
它容易加工,用它容易得到电解质膜SiO2,这种膜然后用于工艺循环中;
硅材料工艺费用低。
高纯度硅材料的制备成本是锗材料制备成本的十分之一。
硅材料工艺的上述优势是因为硅具有以下特征:
地球表面含有大量以矿物质形式出现的硅(站地表质量的25%);
硅开采(含在普通的河床沙子里)和加工简单;
存在“旁亲的”不溶于水SiO2氧化层;
比锗隔离区域更宽(相应地Eg=1.12эВ和Eg=0.66эВ)
硅
硅具有类似金刚石晶格,晶格的形态是两个相互渗透的面心格子。
晶格尺寸—0.54纳米,原子间的最短距离—0.23纳米,掺杂原子取代硅原子,占据它们在晶格中的位置。
主要掺杂原子是磷(五价取代施主杂质)和硼(三价取代受主杂质)。
它们的浓度一般不超过10—8个原子百分比
真实晶体与理想晶体相比区别如下:
它们不是无穷的,表面原子具有自由的键合;
因为热震荡原子在晶格中能位移到相对理想的状态。
真实晶体包含缺陷。
从三维角度看真实晶体缺陷分为下列类型:
点缺陷
点状缺陷包括:
--萧特基Schottky缺陷
--富兰克Frenkel缺陷
--取代位置的杂质原子;
--接点间的杂质原子。
萧特基Schottky缺陷是晶格中的空位。
空位通常在晶体的表面。
原子要么离开晶格,要么与其键合。
接下来空位依靠晶体热能进入其体内。
在热动力平衡的条件下集中这些缺陷NШ得到如下等式:
NШ=C*exp(-W/kT)
其中,C-是常数;
W—形成这种空位的能量;
对于硅来讲,W=2,6эВ.
[pic]
富兰克缺陷是一个空位,是一个间隙原子。
这些缺陷的密度也可以按照上述公式计算,但是,间歇原子形成的能量值很大W=4,5эВ.空位和间隙原子依靠热能在晶格里相互移动。
可以向晶格中输入杂质原子。
同时,位于取代位置的杂质原子在半导体禁止区域创造能级。
位于接点间的杂质原子不会创造这些能级,但是不会影响半导体的机械性能。
线缺陷:
线缺陷包括:
边缘差排和螺旋差排。
边缘差排产生原因同一平面的原子沿着差排可能平行移动的方向位移同样距离b。
螺旋差排也产生于原子面的移位,但是原子沿着差排垂直移动方向位移不同的距离。
两种类型的缺陷都产生于晶体内的机械应力,并受制于温度等级或者杂质原子的过高浓度。
IC产业中使用的晶体内通常没有边缘差排。
面缺陷
面缺陷包括:
n晶粒边界
n双晶边界–沿着某些双晶面BC(见图1)改变晶体的取向。
这些缺陷产生于硅生长过程中晶锭的确定部分。
IC产业不使用这种晶体,它们只能作废处理。
硅内体缺陷
晶格内三维破坏的表现形式之一是微型缺陷和沉淀物(相位,如果物质内溶解度过高,在同等温度下相位内就会释放杂质原子)
在硅晶体生长中,如果位错密度很低,就会产生这样的缺陷,这种缺陷主要是针对半导体级硅晶体,目前正在努力研究。
因为尺寸小它们被称为微型缺陷。
晶体横截面上微型缺陷分散图具有螺旋状的形状,所以又称为“螺旋图”。
螺旋图在直拉法和区熔法制备的晶体中都有发现,并不取决于结晶取向。
这种缺陷首先在局部腐蚀无错位硅片过程中发现的。
硅片内发现的缺陷,区别于位错、包装缺陷、孪晶、沉淀物和粒间界面。
这种缺陷给出了腐蚀图像,称为“非结晶”或者“空的”腐蚀坑。
相对于晶体,非结晶腐蚀坑没有特定取向。
它们具有平底,相应地受制于局部的接近球面缺陷的腐蚀,并在腐蚀过程中在表面出口位置留下“很深”的坑。
借助x光地形测量法和局部腐蚀法,在研究晶体过程中识别出两类微型缺陷,大尺寸的缺陷称为缺陷-A,主要位于离晶体表面和硅片边缘较远的区域。
小尺寸的微型缺陷(缺陷-B)出现在晶体体内,直到晶体侧表面。
硅材料生产阶段
制备半导体级单晶硅的工艺包括下列工序:
1.制备工业硅;
2.把硅转化为易挥发性化合物,这种化合物提纯后容易还原;
3.提纯和还原化合物,得到棒状多晶硅;
4.用结晶法彻底提纯硅材料;
5.生长掺杂单晶硅。
硅材料生产主要阶段
制备工业硅
大多数微电子产品的原材料是电子级硅。
生产电子级硅的第一阶段是制作称为工业硅(冶金硅)这种原料。
这一工艺阶段采用装有电级的电弧炉。
炉内装入硅石和煤、木屑、焦炭等碳物质。
反应温度Т=18000С,能耗W=13千瓦/小时。
炉内会发生一系列中间反应。
最终反应式如下:
SiC(固体)+SiO2(固体)>Si(固体)+SiO2(气体)+CO(气体)
(1)
这种方法得到的工业硅,硅含量98—99%,Fe,Аu,В,Р,Са,Cr,Cu,Mg,Mn,Ni,Ti,V,Zn等等含量1—2%
制备三氯氢硅
多晶硅的现代制备工艺基于三氯氢硅氢还原、用锌还原四氯化硅和硅烷高温分解,大部分硅(约80%)的制备方法是三氯氢硅氢还原法。
本法的优势:
制备三氯氢硅简便和经济,三氯氢硅提纯效率高,硅回收率大和硅沉积速度快(硅的回收率,使用四氯化硅时为15%,而使用三氯氢硅时不少于30%),产品成本低。
三氯氢硅通常采用工业硅氢氯化法制得:
工业硅与氯化氢或者含有氯化氢的混合物相互反应,反应温度260—400°С。
伴随三氯氢硅合成会发生一些副反应,并生成四氯化硅和其他氯硅烷,以及金属卤化物,如АlСl3,ВСl3,FeCl3等等。
制备氯硅烷的反应是可逆的和放热的过程。
Si(T)+ЗНСl(Г)>SiHCl3(Г)+H2(Г)
(2)
Si(T)+4НСl(Г)>SiCl4(Г)+2Н2(Г)(3)
当温度超过300°С时三氯氢硅在反应产物中几乎不存在。
如果因提高三氯氢硅产出率而降低反应温度,就会大大减缓(3)反应速度。
为了加快
(2)反应速度是用了催化剂(铜、铁、铝等等)。
例如,如果原始硅中加入5%的铜,反应产物中三氯氢硅的含量在265°С温度条件下达到95%。
三氯氢硅的合成在反应炉沸腾层上进行,向炉顶不断输入颗粒0.01—1毫米的工业硅粉。
厚度200—600毫米颗粒流化层会引起氯化氢的逆流,这些氯化氢以每秒1—8厘米速度进入炉底。
这就能保证异质化学-工艺流程从扩散区域转变到运动区域。
因为流程是放热的过程,为了在规定温度范围内稳定反应流程需要加快排放热量,仔细检测流化层不同液位上的温度。
除了温度,还要控制氯化氢流量和炉内压力。
原料中水份和氧的存在会大大影响三氯氢硅的产出率。
这些杂质,通过氧化硅粉,在其表面产生一层稠密的SiO2,阻碍硅与氯化氢相互反应,相应地就会降低三氯氢硅的产出率。
因为当氯化氢中水份含量从0.3%增加到0.4%时三氯氢硅的产出率就会从90%降到65%。
鉴于此,氯化氢,甚至硅粉在三氯氢硅合成前需要经过仔细干燥和脱氧处理。
三氯氢硅合成过程中产生的汽气混合物进入冷却区域,这里它们被快速冷却到40—130°С,最终以灰尘形式排出固体杂质颗粒(铁、铝及其他的氯化物),这些杂质与没有参与反应的硅颗粒和聚氯化物(SinCl2n+2)颗粒通过过滤器进行分离。
除尘之后(硅尘是易爆物质)汽气混合物进入冷凝工序,冷凝温度—70°С。
三氯氢硅和四氯化硅(沸点相应为SiHCl3和SiCl4)与氢气和氯化氢(沸点为84°С)进行分离。
冷凝后得到的混合物主要由三氯氢硅(达90—95%)组成,其他成分---四氯化硅可以通过精馏得到分离,分离得到的四氯化硅接下来可以用于硅酸盐、石英玻璃的生产,以及使用催化剂通过补充氢化方式制备三氯氢硅。
三氯氢硅提纯
获得的三氯氢硅含有大量杂质,清除这些杂质是一项很复杂的课题。
最有效的提纯法是精馏法。
但是,仅凭精馏法要全部深入地清除具有不同物理-化学属性的各类杂质是很难的。
对此,为了提高对一系列杂质的清除深度需要运用补充措施。
例如,针对很难用结晶法清除的杂质(硼、磷、碳)必须采用三氯氢硅更深程度的提纯。
所以,为了提高提纯效率都把这些杂质转化为非挥发性的化合物或者络合物。
例如,为了清除硼,在120°С温度下三氯氢硅蒸汽通过铝屑。
通过吸收硼,铝屑就可以彻底把它从三氯氢硅中清除。
产生的副产品铝的氯化物在220—250°С温度下进行蒸发,然后通过分馏冷凝进行分离。
除了铝外,还可以使用银、铜或者锑。
向铝中添加铜可以同时清除三氯氢硅中砷和锑杂质。
向三氯氢硅中加入磷的五氯化物或者磷的氯氧化物可以提高硼杂质清除的效率。
同时产生了磷与硼非挥发络合物,组分为РСl5·ВСl3或者РОС13·ВСl3,然后通过精馏分离。
把硼转化为非挥发化合物的方法还有向三氯氢硅中添加三苯甲氯(或者三甲胺、乙腈、氨基酸、酮等等),可以与硼一起生成型号为(С6Н5)3С·ВСl3络合物,然后通过精馏清除。
清除含硼杂质还可以在注入铝胶或者其他胶体(TiO2,Fe2O3,Mg(OH)2)的反应炉内吸收完成,然后对三氯氢硅进行精馏。
为了清除三氯氢硅中的磷杂质注入氯气,把磷的三氯化物转化为五氯化物。
在溶液中添加铝的氯化物条件下会产生非挥发性的化合物РСl5·АlСl3,然后通过精馏清除。
检测提纯得到三氯氢硅的纯度采用红外线光谱仪、色层谱仪,甚至测量三氯氢硅氧本制备的样硅导电类型和导电值。
样检有两种方法。
按照第一种方法,在实验室装置里通过气相沉积方法获得多晶硅棒,直径10---20毫米。
然后用无坩埚区熔法把多晶硅棒拉制成检测用单晶硅,根据单晶硅导电类型和比电阻判定三氯氢硅的纯度。
为了确定施主浓度需要在氩气或者真空里进行一次区熔,得到n型单晶硅,根据单晶硅的比电阻施主方面纯度(施主方面比电阻);为了确定硼的浓度需要在真空里进行5—15次区熔,得到p型单晶硅,根据单晶硅的比电阻判定硼方面的纯度(硼方面的比电阻)。
按照第二种样测方法在微型石英炉内直接在单晶硅棒上从气态生长单晶硅,然后测量该单晶硅的比电阻。
提纯后三氯氢硅内微型杂质的余量不应该超过:
质量%,硼--3·10-8,磷--1·10-7,砷--5·10-10,碳(碳氢化合物形式)--5·10-7。
根据样品的电性测量施主杂质余量应该能保证n型硅的比电阻不小于5000Ом·厘米,而根据受主杂质含量p型硅的比电阻应不小于8000Ом·厘米。
制备硅其他化合物的其他方法
与上述方法比较经济技术更具竞争力的方法是通过分解高纯硅烷SiH4制备多晶硅,其制备流程如下:
在温度下在氢气中熔化工业硅和锰,得到硅化锰Mg2Si,然后在液氨介质中在30°С温度下用氯化铵对硅化锰按照下列反应式进行分解:
Mg2Si+4NH4Cl>SiH4+2MgCl2++4NH3(4)。
分离出的硅烷进入精馏提纯工序,提纯后杂质含量降到10-8—10-7%水平以下。
众所周知,还有制备挥发性的硅化合物的其他方法---工业硅氯化或者碘化,反应产物是四氯化硅或者四碘化硅。
还原提纯的三氯氢硅
还原提纯的三氯氢硅和由此制备出多晶硅在氢气介质中完成,反应式为:
SiHCl3(Г)+H2(Г)>Si(T)+3HCl(Г)(5)
反应位置:
加热硅棒表面,硅棒直径4---8毫米(有时达30毫米,硅棒是通过直拉法得到的。
在某些工艺里不用圆柱形硅棒,而用薄片状硅棒(厚度1—5毫米,宽度30—100毫米),具有更大的沉积面积。
拉制硅棒的材料是高质量的多晶硅。
硅基棒的表面经过超音速提纯、混合酸液(例如,HF++HNO3)中酸洗、清洗和干燥。
为了获得高质量的多晶硅对硅棒在纯度方面提出了很高的要求。
硅棒应该具有比电阻:
施主方面>700Ом·厘米和受主方面>5000Ом·厘米。
用硅棒制成电发热体(例如,П状形式),采用通电流方式加热。
伴随硅棒直径的生长逐渐加大电流强度。
选择三氯氢硅氢还原反应条件应该基于流程下列参数最佳相互作用:
--三氯氢硅与硅的转化率平稳,获得硅棒晶体结构平稳;
--反应温度;
--能耗;
--Н2:
SiHCl3摩尔比;
--硅沉积速度。
还原反应最佳条件为:
温度1100—1150°С,Н2:
SiHCl3摩尔比在5—15范围内,三氯氢硅输送密度0,004摩尔/(小时·см2)。
如果硅棒温度低于最佳值三氯氢硅与四氯化硅的转化率提高,硅的产出率降低。
温度过高会大大增加能源消耗。
在Н2:
SiHCl3最佳摩尔比=5—15条件下,硅棒具有稠密的微型晶体结构和相对平滑的表面。
如果不在这个比例之内会形成不平整的表面,硅棒结构是大型晶体的,并夹杂气孔,这些气孔在接下来为生长单晶硅融化多晶硅过程中造成熔化液沸腾和飞溅。
安装在不同工业炉内的硅棒数量在2---16根之间,每根长度为2米,最终直径为150—250毫米。
凭借硅棒相互加热硅沉积速度在多硅棒炉内要比双硅棒炉内快。
硅棒直径生长速度达到0.5毫米/小时,能耗为3000千瓦.小时/公斤。
为了提高硅成品的纯度需要进行认真提纯氢气,反应炉要用特殊钢制造,并且为了保护炉面不与气体介质相互反应,需要加盖追加的石英罩(硅制罩),该罩把反应空间与炉壁分离。
涂上保护膜,例如聚氯硅烷,是对炉壁很好的保护。
用硅烷SiH4制备多晶硅
在1000°С温度下通过高温分解硅烷SiH4方式可以制备多晶硅。
反应式为SiH4(Г)->Si(T)+2Н2(Г),在分解中产生的氢气具有很高纯度,并运用到同步的生产中。
根据这个工艺获得的多晶硅具有比三氯氢硅还原法制备的多晶硅更高的纯度。
从四氯化硅和四碘化硅回收硅的方法是用锌还原四氯化硅或者高温离解四碘化硅。
得到的多晶硅棒在用于直拉法生长单晶硅之前打成便于装入坩埚的块状或者按照标准毛坯进行切割。
针对无坩埚区熔法硅棒需要进行抛光处理,获得需要的尺寸。
此外,消除富含杂质和气体的表面层可以预防硅从熔融区域飞溅。
多晶硅制备现代工艺包括再生工序、重复使用各种组分和还原(高温分解)反应产物,这有利于改善流程的经济技术指标,降低硅成品的成本,使流程更加清洁安全。
上述多晶硅沉积方法还用于在碳心棒上制备多晶硅管。
凭借纯度高和强度大这种管道可以代替石英管运用在高温炉内(超过1200°С),以便制造半导体和微电子设备。
在使用的几年里硅管不会下陷或者其他变形,尽管温度会在900和1250°С之间循环。
那时石英管在这种流程下使用期是有限的。
为了得到高纯度的硅多晶硅棒需要在真空里用区熔法进行结晶提纯处理。
同时,除了用结晶法清除硅中非挥发性杂质(主要是受主杂质)以外,还要用熔融区域蒸发方式根本清除硅中挥发性的施主杂质。
这样,经过15次区熔,速度3毫米/分钟,得到p导电型的单晶硅,剩余杂质浓度小于1013см-3,比电阻(硼)大于104Ом*厘米。
单晶硅生产
单晶硅生产主要采用直拉法(占整个电子产业消耗量的80—90%),另外还使用无坩埚区熔法。
直拉法
单晶硅直拉生产法是指单晶硅的生长依靠原子在界面上从液相或者气相跃迁为固相。
用在硅生产上这个方法可以看成是液体-固体单组分生长系统。
生长速度V取决于生长中的硅表面连接来自液相原子的位置数和界面上跃迁的特征。
单晶硅生长设备
设备包括下列部件:
--反应炉,包括坩埚(8),支撑坩埚的坩埚杆(14),发热体(15),电源(12)高温区域室(6)和绝热层(3,16);
--晶体拉直工具,包括籽晶棒(5),籽晶旋转工具
(1)和籽晶夹具,坩埚旋转和起降装置(11);
--介质组分控制装置(4—气体入口,9—排气口,10—真空泵)
--控制单元,包括微处理器、硅锭生长的直径和温度传感器(13,19)和输入设备;
补充设备:
视窗—17,外罩—2。
工艺流程
高质量籽晶硅放入硅熔融物中,同时转动籽晶硅。
在坩埚内熔化多晶硅,在惰性气体环境下(氩气,真空度约为104Па),反应温度稍高于硅的熔点Т=1415°С。
坩埚顺着与籽晶棒相反的方向旋转,以便拌匀熔融物,使温度分配不均匀性降到最低。
硅真空下生长可以通过真空蒸发法部分清除硅熔物中挥发性杂质,也可以减少炉内表面一氧化硅颗粒附着数量,这些颗粒会使晶体内形成瑕疵,破坏单晶硅的生长。
在单晶硅生长初期需要把部分籽晶硅熔化,以便消除其机械张力高密度区域和瑕疵区域。
然后逐渐从硅熔物中拉直单晶硅。
为了用直拉法制备单晶硅开发和广泛使用高效的自动化的设备,能够重复生产无位错单晶硅,直径达200—300毫米。
但是,在大质量熔融物中(60—120公斤)对流特性更加复杂,这就为保障硅材料所需特性制造额外的困难。
此外,在大质量的熔融物下成本降低不明显,因为石英坩埚造价高,由于很难排出结晶潜热而使硅生长速度减缓。
鉴于此,为了进一步提高生产效率,减少拉直单晶硅的硅熔液体积,半连续性生长设备得到长足的发展。
在这样的设备里硅材料额外不间断或者周期的装入坩埚,不用冷炉,例如用另一个坩埚的液相补充硅熔物,那个坩埚也可以周期或者不间断的得到固相补充。
这种完善的直拉法可以把单晶硅生产成本降低数十个百分点。
此外,可以在常态不大容积的硅熔物中拉直单晶硅。
这就容易调节和优化硅熔物内的对流,消除因硅生长中熔融物体积的改变而引起的晶体偏析不均匀性。
掺杂
为了制备具有所需比电阻的n型或者p型单晶硅需要对原始多晶硅或者硅熔液进行掺杂处理。
向装入的多晶硅输入相应元素(Р,В,As,Sb等等)或者它们与硅的合金,这样就能保证掺杂的精度。
硅材料的彻底处理
从生产设备取出硅锭,直径20—50厘米,长度达3米。
为了把硅锭制成规定取向、厚度为几十毫米的硅片需要进行下列工艺程序:
1硅锭机械处理
--分离硅锭的颈尾部分;
--研磨侧表面至需要的厚度;
--磨削一个或者多个基本切面(便于工艺设备下一步的取向和确定结晶取向);
--用金刚石锯把硅锭切成硅片(100)--平面精确(111)--偏向误差几度;
2酸洗。
使用磨料SiC或者Al2O3消除高度超过10微米的损伤。
然后,使用氟酸、硝酸和醋酸按照1:
4:
3的比例配置的混合溶液或者苛性钠溶液酸洗硅的表面。
3抛光—得到镜面般平整的表面。
使用抛光悬浮液(规格为10纳米的SiO2颗粒胶体溶液)和水的混合物。
最终,硅材料具有片状,直径15—40厘米,厚度0.5—0.65毫米,一侧表面如镜平滑。
不同表面取向和导电类型的硅片种类在本文附表中给出。
直拉法生产的单晶硅主要用于制造集成电路,少量部分(约2%)用于制造太阳能电池。
该方法最适合制造的设备,不需要很高的比电阻(25Ом·厘米以内),因为受到氧气和坩埚材料其他杂质的污染。
无坩埚区熔法
无坩埚区熔法生长单晶硅基于单匝感应线圈(《针眼型》),其内径小于原始多晶硅棒的直径。
在所有现代区熔系统中都使用固定位置的感应线圈,而移动多晶硅棒和生长的单晶硅。
与直拉法比较,无坩埚区熔法晶体生长速度要快一倍,因为区熔法温度梯度更大。
受到技术限制,无坩埚区熔法生长的硅晶体(其直径达150毫米)在直径方面要比直拉法得到的硅晶体逊色。
在无坩埚区熔过程中为了对生长中的晶体掺杂,通常在气态下向气体载体(氩气)输入掺杂杂质气态化合物。
同时晶体比电阻变化范围广,达到200Ом·厘米。
在真空下生长得到的单晶硅具有很高的比电阻—达到3·104Ом·厘米。
在制备硅材料中为了防止污染不对多晶硅棒进行切削和研磨处理。
通过真空下五次区熔提纯,消除硅棒中的余下施主杂质、氧、碳和重金属。
无坩埚区熔法的缺点是硅成品比电阻分配很不均匀(20—30%),通过质变掺杂方式可以降低这个缺陷。
无坩埚区熔法制备的单晶硅约占整个单晶硅总产量的10%,主要用来制造数字设备,特别是大功率可控硅整流器。
单晶硅的缺陷
针对固体电子,直拉法和无坩埚区熔法制备的硅晶体绝大多数是无位错的,其内部的主要结构缺陷为微型缺陷,尺寸从几分之一纳米到几个微米,浓度107см-3及更大。
主要分为三类微型缺陷:
受杂质稳定的位错环及其聚集(A缺陷);球面延长或者平面的杂质附着物和稠密硅相位颗粒(B缺陷)和空位聚集(Д缺陷)。
可以设想,微观缺陷可能直接产生于结晶过程中,也可能产生于晶体处理(热处理、辐射处理、机械处理等等),以及半导体仪表运行中。
甚至,在硅生长过程中硅棒截获杂质络合物和富含杂质的粒子、点滴熔化物,以及硅原子附聚物,其结果都可能产生微观缺陷。
在生长后阶段微型杂质产生的主要原因是:
在异质中心或者晶体生长中形成的原始微型缺陷中分解杂质固溶体或者分解硅内自身的点缺陷。
单晶硅中主要背景杂质是氧、碳、氮、重金属易扩散杂质。
单晶硅中含有的氧气,视其浓度、存在形式和分配方式,对硅的结构性能和电性能既可产生正面的影响,也可产生负面的影响。
从石英坩埚中用直拉法生产的单晶硅内氧的浓度取决于下列因素:
坩埚溶解程度和氧气从生长室环境进入熔化物的数量。
直拉法生产硅的氧的浓度大小取决于熔化物的黏度、熔化物内对流特性和晶体生长速度,该浓度在5"1017至2"1018厘米-3范围内变化。
氧在单晶硅中极限溶解度为1,8"1018.氧气的溶解度随着温度的降低而急剧下降。
为了控制和降低氧气在直拉法制备的单晶硅中的浓度,可以不使用石英坩埚,而使用亚硝酸硅制成的坩埚,仔细清除炉内环境(氩气)中含氧杂质。
区熔法制备的单晶硅中氧气的浓度通常为2"1015—2"1016厘米-3.
碳是硅中最有害的背景杂质之一,它与氧气一起严重影响硅材料的电性能和结构特性。
在直拉法和区熔法制备的单晶硅中碳的含量为5"1016—5*1017厘米-3.在熔点下碳的溶解度在硅熔化物中等于(2-4)"1018厘米-3,在晶体中等于6"1017厘米-3.在硅中碳的有效分配系数为0.07。
单晶硅中碳的主要来源是:
一氧化碳和二氧化碳,以及原始多晶硅。
碳氧化物产生于一氧化硅和发热体高温元件的石墨材料以及设备内拉制单晶硅用坩埚支架的石墨材料相互反应,石英坩埚和石墨支架相互反应,氧气氧化石墨元件。
为了降低碳在硅中的浓度,就要减少其在主要来源物中的含量,减少硅生长室内石墨元件和含碳元件的数量,或者在它们表面涂上保护层。
在直拉法和区熔法制备的单晶硅中氮的残余浓度不超过1012厘米-3。
在熔点下氮在固体硅中的溶解度为4,5"1015厘米-3。
熔化平均的系数为0.05。
氮的主要来源是:
气体环境、石墨的释放、亚硝酸硅坩埚。
作为施主杂质,氮气还会导致硅内移位临界应力值的提高。
在直拉法和无坩埚区熔法生产的硅单晶中易扩散重金属杂质(Fe,Сu,Аu,Сr,Zn等等.)的浓度不超过5-Ю13,而在多次区熔得到的超纯硅晶体中浓度为5·1011см-3.